Основные свойства рабочих сред.
Введение Ректификация - массообменный процесс, который осуществляется в большинстве случаев в противоточных колонных аппаратах с контактными элементами (насадки, тарелки), аналогичными используемыми в процессе абсорбции. Поэтому методы подхода к расчету и проектированию ректификационных и абсорбционных установок имеют много общего. Тем не менее ряд особенностей процесса ректификации (различное соотношение нагрузок по жидкости и пару в нижней и верхней частях колонны, переменные по высоте колонны физические свойства фаз и коэффициент распределения, совместное протекание процессов массо- и теплопереноса) осложняет его расчет. Одна из сложностей заключается в отсутствии обобщенных закономерностей для расчета кинетических коэффициентов процесса ректификации. В наибольшей степени это относится к колоннам диаметром более 800 мм с насадками и тарелками, широко применяемым в химических производствах. Большинство рекомендаций сводится к использованию для расчета ректификационных колон кинетических зависимостей, получаемых при исследовании абсорбционных процессов. Большое разнообразие тарельчатых контактных устройств затрудняет выбор оптимальной конструкции тарелки. При этом наряду с общими требованиями (высокая интенсивность единицы объема аппарата, его стоимость и др.) ряд требований может определяться спецификой производства: большим интервалом устойчивой работы при изменении нагрузок по фазам, способность тарелок работать в среде загрязненных жидкостей, возможностью защиты от коррозии и т.п. Зачастую эти качества становятся превалирующими, определяющими пригодность той или иной конструкции для использования в каждом конкретном процессе. Размеры тарельчатой колонны (диаметр и высота) обусловлены нагрузками по пару и жидкости, типом контактного устройства (тарелки), физическими свойствами взаимодействующих фаз. Ректификацию жидкостей, не содержащих взвешенные частицы и не инструктирующих, при атмосферном давлении в аппаратах большой производительности часто осуществляют на ситчатых переточных тарелках.
|
|
Описание технологической схемы установки.
1- емкость для исходной смеси; 2, 9 – насосы; 3 – теплообменник-подогреватель; 4 – кипятильник; 5 – ректификационная колонна; 6 – дефлегматор; 7 – холодильник дистиллята; 8 – емкость для сбора дистиллята; 10 – холодильник кубовой жидкости; 11 – емкость для кубовой жидкости
Рис. 1. Принципиальная схема ректификационной установки.
Принципиальная схема ректификационной установки представлена на рис.1. Исходную смесь из промежуточной емкости 1 центробежным
|
|
насосом 2 подают в теплообменник 3, где она подогревается до температуры кипения 53,7ºС. Нагретая смесь поступает на разделение в ректификационную колонну 5 на тарелку питания, где состав жидкости равен составу исходной смеси xp.
Стекая вниз по колонне, жидкость взаимодействует с
поднимающимся вверх паром t=143ºC, образующимся при кипении в кубовой жидкости в кипятильнике 4. Начальный состав пара примерно равен составу кубового остатка xw, т.е. обеднен легколетучим компонентом и включает труднолетучий компонент - четыреххлористый углерод. В результате массообмена с жидкостью пар обогащается легколетучим компонентом. Для более полного обогащения верхнюю часть колонны орошают в соответствии с заданным флегмовым числом (это отношение количества флегмы к количеству дистиллята) R=1,47 жидкостью (флегмой) состава xp, получаемой в дефлегматоре 6 путем конденсации пара, выходящего из колонны. Часть конденсата выводится из дефлегматора в виде готового продукта разделения – дистиллята, который охлаждается в теплообменнике 7 и направляется в промежуточную емкость 8.
Из кубовой части колонны насосом 9 непрерывно выводится кубовая жидкость – продукт обогащенный труднолетучим компонентом, который охлаждается в теплообменнике 10 тип кожухотрубчатый и направляется в емкость для сбора 11, выполненной из стали марки ОХ17Т обладающей повышенной сопротивляемостью межкристаллической коррозии.
|
|
Таким образом, в ректификационной колонне осуществляется непрерывный неравновесный процесс разделения исходной бинарной смеси на дистиллят (с высоким содержанием легколетучего компонента) и кубовый остаток (обогащенный труднолетучим компонентом).
Основные свойства рабочих сред.
Разделяемая смесь состоит из сероуглерода и тетрахлорид углерода.
Сероуглерод CS2 — соединение серы с углеродом, бесцветная жидкость с неприятным запахом, под действием света разлагается, tпл—112,1°С. Пары при 236°С воспламеняются. В промышленности сероуглерод получают ректификацией с СН4 [2]. Четыреххлористый углерод, тетрахлорметан, CCl4, бесцветная со сладковатым запахом жидкость, tпл —22,9 °С. Практически нерастворим в воде, смешивается со многими органическими растворителями.
Температуры кипения и молекулярные массы разделяемых компонентов:
tк, °С | Мr, кг/кмоль | |
сероуглерод | 46.24 | 76 |
тетрахлорид углерода | 76.7 | 154 |
|
|
Следовательно, сероуглерод является низкокипящим компонентом, а тетрахлорид углерода - высококипящим.
х | 0 | 5 | 10 | 20 | 30 | 40 | 50 | 60 | 70 | 80 | 90 | 100 |
y t | 0 76,7 | 13,2 73,7 | 24,0 71,0 | 42,3 66,0 | 54,4 62,3 | 64,5 59,0 | 72,6 56,1 | 79,1 53,7 | 84,8 51,6 | 90,1 49,6 | 95,0 47,9 | 100,0 46,3 |
Таблица 1.- Равновесные составы жидкости и пара (y – x, % мол.) и температуры кипения смеси (°С) для некоторых бинарных систем при P = 760 мм рт. ст.
Технологические расчеты.
Материальный баланс колонны
Мольные доли исходной смеси, дистиллята и кубового остатка:
= (0,40/76)/[(0,40/76)+(0,60/154)]=0,6 (1.1)
= (0,95/76)/[(0,95/76)+(0,05/154)]=0,98
= (0,05/76)/[(0,05/76)+(0,95/154)]=0,097
Уравнение материального баланса
F = D + W; (1.2)
F
F = D
+ W
,
где F,
,
– массовые концентрации н.к.к.,
F = 2,0 кг/с – расход исходной смеси или производительность,
D – расход дистиллята,
W – расход кубового остатка,
отсюда находим:
W = F( –
)/(
–
) = 2×(0,95 – 0,40)/(0,95 – 0,05) = 1,2 кг/с
D = F – W = 2 – 1,2 = 0,8 кг/с.
3.2 Определение рабочего флегмового числа
Рис. 2. Диаграмма равновесия между паром и жидкостью в координатах
Y-X.
Из диаграммы получим
0,8 кмоль/кмоль смеси.
Нагрузки ректификационной колонны по пару и жидкости определяются рабочим флегмовым числом R; его оптимальное значение Rопт можно найти путем технико-экономического расчета. Ввиду отсутствия надежной методики оценки Rопт используют приближенные вычисления, основанные на определении коэффициента избытка флегмы (орошения): b = R/ Rmin , где Rmin — минимальное флегмовое число:
(1.3)
При этом коэффициент избытка флегмы будет равен:
Построение рабочих линий
Уравнения рабочих линий:
верхняя часть: Y = [R/(R+1)]x + XD / (R+1)
Y = 0,595x + 0,397
нижняя часть: Y = [(R+f)/(R+1)]x – [(f – 1)/(R + 1)]XW
Y= 1,607x – 0,059
f = F / D = 2,0/0,8 = 2,5
![]() |
Дата добавления: 2018-10-27; просмотров: 376; Мы поможем в написании вашей работы! |
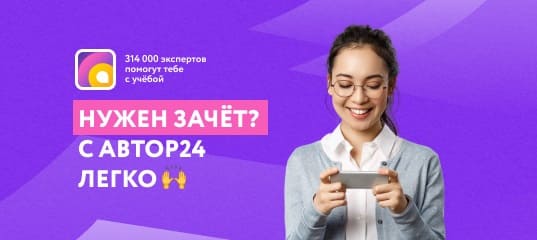
Мы поможем в написании ваших работ!