Влияние условий кристаллизации на свойства кристаллов
КРИСТАЛИЗАЦИЯ
Общие сведения
Кристаллизацией называют выделение твердой фазы в виде кристаллов главным образом из растворов и расплавов. Кристаллы представляют собой однородные твердые тела различной геометрической формы, ограниченные плоскими гранями. Каждому химическому соединению обычно соответствует одна или несколько кристаллических форм, отличающихся положением и числом осей симметрии. Явление образования нескольких кристаллических форм у данного химического соединения носит название полиморфизма. Кристаллы, включающие молекулы воды, называют кристаллогидратами, причем в зависимости от условий проведения процесса кристаллизации одно и то же вещество может кристаллизоваться с разным числом молекул воды.
В химической технологии процессы кристаллизации широко используют для получения в чистом виде различных веществ. Осуществляемое в промышленном масштабе одновременное получение большого числа кристаллов носит название массовой кристаллизации.
Массовую кристаллизацию обычно проводят из водных растворов, по нижая растворимость кристаллизуемого вещества за счет изменения температуры раствора или удаления части растворителя. В ряде случаев кристаллизацию ведут из растворов органических веществ (спиртов, эфиров, углеводородов и др.).
Кристаллизацию из расплавов осуществляют путем их охлаждения.
|
|
Кристаллы можно получать также возгонкой и последующим охлаждением образующегося пара при температуре ниже температуры «тройной» точки*.
В производственных условиях процесс кристаллизации состоит из следующих операций: собственно кристаллизации, отделения кристаллов от маточных растворов**, перекристаллизации (в случае необходимости), промывки и сушки кристаллов.
2. Равновесие при кристаллизации
Рассмотрим условия равновесия между твердой фазой (кристаллом) и жидкой фазой (растворителем).
Для большинства веществ с повышением температуры растворимость увеличивается. Эти вещества обладают «положительной» растворимостью Растворимость некоторых веществ «отрицательна», т. е. снижается с повышением температуры раствора. Как известно, раствор, находящийся в равновесии с твердой фазой при данной температуре, называют н а с ы-
-----------------------------
* На диаграмме состояний «тройная точка» характеризует одновременно- существование вещества в трех состояниях: твердом, жидком и парообразном.
** Маточным раствором называют раствор, оставшийся после выпадения из него кристаллов.
щенным. В насыщенных растворах между кристаллами и раствором возникает подвижное равновесие, при котором количество растворяющихся из кристалла частиц и вновь кристаллизующихся частиц одинаково в единицу времени.
|
|
|
При некоторых условиях концентрация растворенного вещества может быть больше его растворимости. Такие растворы, называемые п е р е–
сыщенными, нестабильны и легко переходят в состояние насыщения. При этом из них выпадает часть твердой фазы.
На рис. XVI-1 показаны кривые растворимости водных растворов различных солей в зависимости от температуры. Как видно из рисунка, наиболее резко возрастающей положительной растворимостью обладает азотнокислый калий (линия 1—1), меньше изменяется с повышением температуры растворимость хлористого калия (линия 2—2) и почти не изменяется растворимость хлористого натрия (линия 3—3). Характер изменения растворимости сульфата натрия зависит от присутствия в молекуле соли кристаллизационной воды: в отличие от водного сульфата натрия (Na2SO4-10H2O), обладающего положительной растворимостью (участок 4а—4), растворимость безводного Na2S04 снижается с возрастанием температуры (участок 4—4б).
Пользуясь диаграммами состояния растворов (рис. XVI–2), можно выяснить поведение раствора при его кристаллизации и получить данные для выбора наибо лее эффективного способа проведения процесса кристаллизации. На рис. XVI-2 изображены диаграммы состояний для трех бинарных систем. В каждой системе ниже линии 1—1 (линии растворимости) находится область ненасыщенных растворов (область В). Пунктирная линия 2—2 условно делит область пересыщенных растворов на две части. Между линиями 1—1 и 2—2 расположена относительно устойчивая, или м е т а с т а б и л ь н а я, область Б и над линией 2—2 неустойчивая, или лабильная, область А.
|
|
Пересыщенные растворы с концентрациями, соответствующими лабильной области, кристаллизуются мгновенно, в метастабильной же области эти растворы то или иное время остаются без изменения.
Границы метастабильной области зависят от большого числа факторов: температуры раствора, скорости его охлаждения или испарения, перемешивания и др. Так, у соединений с резко возрастающей кривой растворимости (рис. XVI-2, а), при относительно небольшом снижении температуры насыщенного раствора от t 2 до t 1 состояние раствора отвечает сначала метастабильной области (на небольшом участке от с0 до сх), а затем — области пересыщенных
растворов, где происходит выделение твердой фазы. При этом раствор снова становится насыщенным и его концентрация значительно уменьшается (от с0 до с´х ).
|
|
Кристаллизацию подобных растворов, близких к насыщению, целесообразно вести путем их охлаждения, осуществляя быстрый переход в благоприятную для кристаллизации метастабильную область.
Для соединений, растворимость которых более медленно возрастает с увеличением температуры (рис. XVI-2, б), переход в область пересыщенных растворов (из точки с0 до сх) происходит лишь при значительном снижении температуры. При этом количество выпавшей из раствора твердой фазы невелико (оно пропорционально изменению концентраций от сх до с'0). Как видно из рисунка, состояние раствора, соответствующее области его пересыщения, может быть быстро достигнуто и при постоянной температуре (вертикальный участок от точки с0 до точки с"х). Это указывает на возможность кристаллизации раствора и путем удаления части раство рителя. Для таких растворов вопрос о выборе оптимального способа кристаллизации можно решить только технико-экономическим расчетом .
На рис. XVI-2, в рассмотрен случай, когда растворимость кристаллизуемого вещества почти не изменяется в широком диапазоне температур. При этом целесообразно осуществлять кристаллизацию путем выпаривания.
При сильном пересыщении растворов образуется много зародышей, поэтому во всех случаях степень пересыщения должна быть такой, чтобы количество возникающих зародышей было наименьшим а кристаллы росли достаточно быстро. Поэтому кристаллизацию нужно вести из растворов с умеренным пересыщением из метастабильной области (точка с'х).
Скорость кристаллизации
На скорость кристаллизации оказывает влияние ряд факторов: степень пересыщения раствора, его температура, образование зародышей кристаллов, интенсивность перемешивания, наличие примесей и др.
При массовой кристаллизации из растворов возникновение кристаллических зародышей и рост из них кристаллов протекают одновременно, что затрудняет изучение кинетики процесса.
Образование зародышей. Зародыши, или центры кристаллизации, образуются в пересыщенных или переохлажденных растворах самопроизвольно. По современным воззрениям, зародыши возникают за счет образования ассоциаций частиц при столкновении в растворе отдельных ионов (молекул) растворенного вещества и постепенно достигают субмикроскопических размеров. Зародыши находятся в подвижном равновесии с раствором и видимой кристаллизации не происходит. Такой скрытый период начала кристаллизации называют индукционн ы м.
В зависимости от природы растворенного вещества и растворителя, степени пересыщения, наличия примесей индукционный период может продолжаться от нескольких секунд до нескольких месяцев Его можно сократить путем внесения в пересыщенный раствор кристалликов растворенного вещества — «затравки». Начало массовой видимой кристаллизации соответствует моменту нарушения подвижного устойчивого равновесия между зародышем и раствором.
Скорость образования зародышей может быть увеличена путем повы шения температуры, перемешивания раствора, внешних механических воздействий (встряхивание, удары, трение и др.). Большое влияние на процесс образования зародышей могут также оказывать шероховатость стенок кристаллизатора, материал мешалки, присутствие в растворе твердых тел с большой поверхностью (ленты, нити и др.). Закономерности процесса образования зародышей при промышленной кристаллизации устанавливают по практическим данным.
Рост кристаллов. Кристалл растет на сформировавшемся, достигшем критической величины зародыше. Он обладает большой поверхностной энергией, за счет которой адсорбируются все новые частицы растворенного вещества. Адсорбировать частицы из раствора могут также твердые частицы другого обладающего соответствующей поверхностной энергией вещества. Они становятся, таким образом, центрами кристаллизации. В последнем случае процесс носит название кристаллизации на подложке.
Рост кристаллов происходит одновременно по всем его граням, однако при различных линейных скоростях роста отдельных граней. Одни из них исчезают, другие — развиваются, что приводит к изменению внешнего вида кристалла.
Предложено несколько теорий роста кристаллов, но ни одна из них не получила всеобщего признания.
По диффузионной теории, например, растворенное вещество первоначально диффундирует из глубины раствора через ламинарный пограничный подслой у поверхности кристалла, затем подведенное вещество как бы встраивается в тело кристалла.
Толщина ламинарного подслоя вблизи поверхности кристалла зависит от интенсивности
перемешивания раствора. На неподвижных кристаллах в неподвижном растворе толщина ламинарного подслоя δ равна 20 — 150 мкм, в сильно перемешиваемых растворах δ → 0.
При большой скорости процесса встраивания кристаллизуемого вещества рост кристалла будет определяться молекулярной диффузией вещества через пленку раствора у поверхности кристалла; напротив, при низкой скорости встраивания решающей будет скорость встраивания
Диффузионная теория роста кристаллов не объясняет ряд явлений, происходящих при кристаллизации (различная скорость роста граней, дефекты, слоистость и пр.). Согласно этой теории, процессы растворения и кристаллизации обратимы, однако доказано, что это не так. Часто при одинаковых значениях движущей силы (разности концентраций) рост кристаллов протекает гораздо медленнее, чем растворение
Скорость кристаллизации не является постоянной. Она изменяется во времени в зависимости от условий кристаллизации в широких пределах. Вначале скорость равна нулю (период индукции), потом достигает "кратковременного максимума и снова уменьшается до нуля (рис. XVI-3). При
сравнительно большой степени пересыщения раствора наблюдается резкий максимум скорости (кривая 1). При малой степени пересыщения или наличии тормозящих кристаллизацию примесей период индукции достаточно велик и на кривой 2 наблюдается горизонтальный участок τ2 — τ3, т. е. максимальная скорость в течение некоторого времени имеет постоянное значение.
|
Температура кристаллизации в общем оказывает положительное влияние на скорость роста кристаллов. При более высокой температуре снижается вязкость раствора и, следовательно, облегчается диффузия. Однако в большей степени влияние температуры отражается на увеличении числа зародышей, что, как известно, приводит к образованию более мелких кристаллов. При положительной растворимости с повышением температуры кристаллизации уменьшается степень пересыщения раствора, что, в свою очередь, вызывает снижение движущей силы процесса.
Влияние условий кристаллизации на свойства кристаллов
Рассмотрим основные факторы, влияющие на свойства кристаллов:
1. Форма кристаллов. Форма кристаллов определяется природой кристаллизуемого вещества и зависит также от наличия примесей в растворе. Например, хлористый калий из чистого водного раствора кристаллизуется в виде кубов, в присутствии кармамид (мочевины) — в виде кубооктаэдров. Более правильной формы, с хорошо развитыми гранями получаются кристаллы при свободном их обтекании раствором (например, при кристаллизации во взвешенном слое). Слишком большая скорость движения суспензии приводит к сглаживанию ребер кристалла и их истиранию за счет энергичных соударений и трения о стенки аппарата и насоса.
2. Размер кристаллов. Более крупные кристаллы получаются при медленном их росте и небольших степенях пересыщения раствора. Существенное влияние на размер кристаллов оказывает перемешивание раствора. С одной стороны, интенсивное движение раствора облегчает дифффузионный перенос вещества к граням кристаллов, способствуя их росту, с другой стороны, вызывает образование зародышей, т. е. накопление мелких кристаллов. Таким образом, перемешивание раствора порождает два противоположных явления. Нахождение оптимальной скорости движения раствора, определяющей желаемое соотношение между производительностью кристаллизатора и требуемыми размерами кристаллов, является одной из важнейших задач рациональной организации процесса массовой кристаллизации. Для ряда кристаллизуемых веществ эти соотношения найдены экспериментально.
На размерах кристаллов сказывается наличие примесей. Присутствие поверхностно-активных веществ в растворе даже в очень небольших количествах может резко влиять как на форму, так и на размеры кристаллов. Некоторые из этих веществ при известных условиях, даже при больших степенях пересыщения, могут приостановить рост крупных кристаллов или, наоборот, способствовать ему.
Один из основных практических способов снижения скорости процесса и получения крупных кристаллов — введение в раствор затравочных кристаллов и вывод из зоны кристаллизации наиболее мелких фракций
Пои массовой кристаллизации размер товарных кристаллов различных веществ колеблется от сотых долей миллиметра до 10—12 мм
3. Фракционный состав. Изменение гранулометрического состава, главным образом за счет уменьшения количества мелких фракций, достигается сужением пределов температур и концентраций раствора, а также последующей классификацией кристаллов.
4. Степень чистоты продукта. Кристаллизация — один из распространенных и наиболее эффективных методов получения веществ в чистом виде. Допустимая величина примесей определяется назначением продукта. Степень его чистоты зависит как от условий самой кристаллизации, так и от дальнейших технологических операций (фильтрование, промывка и др.). Основные загрязнения кристаллов обусловлены наличием в исходном растворе нежелательных примесей. Они могут попасть внутрь кристалла с маточным раствором в виде включений (в трещинах, дефектных полостях и др.) или адсорбироваться гранями кристалла. Изоморфные* примеси могут образовывать смешанные кристаллы. Борьбу с загрязнениями кристаллов ведут механической (отстаивание, фильтрование) и химической обработкой исходного раствора, например, осаждают растворенные соли железа, сернистые соединения, хлориды и пр.
Пересыщение раствора иногда приводит к снижению растворимости примесей и их выпадению из раствора. Чем меньше размеры кристалла, тем больше на его поверхности остается маточного раствора, менее чистого, чем сам кристалл. Степень чистоты кристаллов повышается при промывке. Для получения особо чистых кристаллов их подвергают перекристаллизации.
Остатки влаги обычно удаляют из кристаллов путем сушки, доводя их влажность до состояния, близкого к равновесному.
Способы кристаллизации
Известны следующие способы кристаллизации: кристаллизация с удалением части растворителя, кристаллизация с охлаждением или нагреванием раствора, комбинированные способы.
Кристаллизация с удалением части растворителя. Частичное удаление растворителя производят или его испарением, или вымораживанием. Наибольшее распространение получило испарение. Растворитель ( испаряют) в выпарных аппаратах (см. главу IX), подводя к нему тепло извне, через стенку. После достижения нужной степени пересыщения, как правило, в тех же аппаратах осуществляют и кристаллизацию. Этот способ кристаллизации называют изотермическим.
Общий недостаток процесса кристаллизации при выпаривании — это отложение кристаллов (инкрустация) на теплопередающих поверхностях; одновременно концентрируются примеси, имевшиеся в исходном растворе. Для уменьшения количества твердых отложений повышают скорость циркуляции раствора и вводят в аппарат вещества, препятствующие образованию накипи.
Отделение от маточного раствора и промывку кристаллов производят вне аппарата — на фильтрах или центрифугах. Маточные растворы и промывные воды, если они не содержат
большого количества нежелательных примесей, возвращают для дальнейшего концентрирования
--------------------------------
* Изоморфные вещества — это вещества, образующие с другими веществами кристаллы одинаковой формы
Кристаллизация с изменением температуры раствора. Такой способ называют изогидрическим, так как он осуществляется при постоянном содержании в растворе растворителя. Незначительные потери растворителя за счет его испарения в окружающую среду в открытых кристаллизаторах (см. ниже) в этом случае можно не учитывать. В химической промышленности наибольшее распространение имеет кристаллизация солей с положительной растворимостью. Пересыщение растворов таких солей достигается охлаждением раствора. Процесс ведут как в аппаратах периодического, так и непрерывного действия, одиночных или многокорпусных, располагаемых ступенчато (каскадом). В качестве охлаждающей среды применяют главным образом воду. При охлаждении воздухом процесс протекает гораздо медленнее, но кристаллы получаются более крупными и однородными. Реже в качестве охлаждающей среды используют холодильные рассолы. Для кристаллизации солей с отри цательной растворимостью применяют нагревание.
Комбинированные способы. К ним относятся: вакуум-кристаллизация, кристаллизация с испарением части растворителя в токе носителя и дробная кристаллизация.
Вакуум-кристаллизация. При вакуум-кристаллизации испарение растворителя происходит не путем подвода тепла через стенку, а за счет отдачи раствором своего физического тепла, которое расходуется на испарение части растворителя (приблизительно 10 вес. %). Пары откачиваются вакуум-насосом. Температура поступающего горячего насыщенного раствора снижается до температуры кипения раствора, соответствующей давлению в аппарате. Процесс протекает адиабатически. Пересыщение раствора достигается в основном его охлаждением, так как концентрация при этом изменяется незначительно. Растворитель может испаряться не только за счет физического тепла раствора, но и за счет выделяющейся теплоты кристаллизации. Испарение с одновременным охлаждением раствора и кристаллизацией происходит во всем объеме раствора. Это значительно уменьшает отложение кристаллов на стенках аппарата, сокращая непроизводительные затраты времени на его очистку.
Кристаллизация с испарением части растворителя в токе носителя (воздуха). При этом способе часть растворителя испаряется в движущийся непосредственно над раствором воздух. Одновременно раствор охлаждается.
Дробная, или фракционированная, кристаллизация. При наличии в растворе одновременно нескольких подлежащих извлечению веществ его подвергают дробной, или фракционированной, кристаллизации, создавая условия для последовательного осаждения этих веществ путем изменения температуры и концентрации раствора.17.04.12
Устройство кристаллизаторов
По принципу действия различают следующие типы промышленных кристаллизаторов: 1) кристаллизаторы с удалением части растворителя; 2) кристаллизаторы с охлаждением раствора; 3) вакуум-кристаллизаторы; 4) кристаллизаторы с псевдоожиженным слоем.
Кристаллизаторы с удалением части растворителя. Как было указано, наиболее распространенным способом удаления части растворителя является выпаривание. Появление в растворе кристаллов и создание условий для их роста требуют внесения некоторых изменений в конструкцию обычных выпарных аппаратов.
На рис. XVI-4 изображен выпарной аппарат-кристаллизатор с подвесной нагревательной камерой и двумя работающими поочередно нутч-фильтрами для отделения кристаллов от маточного раствора.
Выпарной аппарат-кристаллизатор с выносной нагревательной камерой и сборником кристаллов показан на рис. XVI-5.
Наиболее производительны и надежны в эксплуатации выпарные аппараты-кристаллизаторы с принудительной циркуляцией раствора и выносной нагревательной камерой (аналогичный аппарат см. главу IX, рис. IX-17). Содержание кристаллов в циркулирующей суспензии составляет 10—20 вес. %. Скорость раствора в трубках нагревательной камеры не должна превышать 3 м/сек. При больших скоростях наблюдается исти рание кристаллов. Процесс кристаллизации легко подвергается регулированию. Продукт получается сравнительно
крупнокристаллическим и однородным. Такие аппараты применяют для кристаллизации солей как с положительной, так и с отрицательной растворимостью
Для снижения расхода тепла процесс осуществляют в многокорпусных установках. При выпаривании с одновременной кристаллизацией удобнее использовать параллельное питание исходным раствором с выводом суспензии из каждого корпуса (рис. IX-4). При этом отсутствуют переточные трубопроводы из корпуса в корпус, и устраняется возможность их засорения кристаллами.
Прямоточная схема многокорпусного выпаривания для кристаллизации растворов нежелательна, так как постепенное снижение температуры раствора при переходе из корпуса в корпус может вызвать преждевременную кристаллизацию и засорение трубопроводов.
Противоток применяют в случае, если раствор, поступает на выпаривание, сильно разбавлен. В первых корпусах по ходу раствора его выпаривают и только в последнем корпусе, обогреваемом первичным паром с наиболее высокой температурой, кристаллизуют. Особенно рекомендуется такая схема при переработке солей с отрицательной растворимостью. Высокая температура раствора в последнем по ходу раствора корпусе способствует более полному осаждению кристаллов .
Кристаллизаторы с охлаждением раствора. Простейшие кристаллизаторы периодического действия с охлаждением раствора представляют собой цилиндрические вертикальные аппараты с охлаждающими змеевиками (или рубашками) и механическими мешалками для перемешивания раствора. С целью увеличения времени пребывания раствора в установке эти аппараты часто соединяют последовательно, располагая каскадом.
Качающиеся кристаллизаторы (рис. XVI-6). Такой кристаллизатор представляет собой длинное неглубокое открытое корыто 1, укрепленное на круглых бандажах 2, которые опираются на ролики 3. Корыто установлено с небольшим наклоном вдоль его продольной оси. Посредством
специального привода (на рисунке не показан) корыто может медленно качаться на опорных роликах.
Раствор подают в корыто вблизи его верхнего конца; медленно протекая по корыту, он охлаждается вследствие потери тепла в окружающую среду и частичного испарения. При медленном движении и охлаждении раствора скорость образования зародышей снижается Кристаллы растут медленно, получаются крупными, размером от 3—5 до 10—25 мм . Механическое истирание кристаллов при перемешивании почти устранено; стенки аппарата не инкрустируются. Выгрузка кристаллов и маточного раствора производится в нижнем конце корыта. Длина применяемых аппаратов — до 15 м ширина — до 1,5 м .
Более энергичное перемешивание раствора и поддержание кристаллов во взвешенном состоянии достигается в кристаллизаторах шнекового типа.
Шнекавые кристаллизаторы . Кристаллизатор шнекового типа — это горизонтальное неподвижное закрытое корыто с водяной рубашкой, внутри которого вращается ленточная или шнековая мешалка. Она не только перемещает образующиеся кристаллы к месту выгрузки, но и поддерживает их во взвешенном состоянии, что способствует свободному и равно мерному росту кристаллов.
На рис. XVI-7 показан кристаллизатор с ленточной мешалкой. В корыте 1 с водяной рубашкой 2 медленно вращается спиралевидная мешалка 3 из металлических полос. Охлаждающая вода в рубашке движется противотоком к раствору.
В отличие от ленточных собственно шнековые кристаллизаторы имеют мешалку в виде бесконечного винта — шнека. Средний размер кристаллов не превышает 0,5—0,6 мм. Для получения более крупных кристаллов иногда применяют воздушное охлаждение. В данном случае аппараты выполняют без рубашек – открытыми. Однако это сильно снижает их производительность.
Недостатки кристаллизаторов шнекового типа: наличие движущихся частей; возможность заклинивания мешалки; нежелательное перемешивание раствора вдоль оси аппарата. Эти кристаллизаторы довольно широко распространены вследствие простоты устройства и обслуживания, а также надежности в работе. Для экономии производственных площадей их устанавливают друг над другом, соединяя последовательно.
Барабанные кристаллизаторы. Эти кристаллизаторы имеют воздушное или водяное охлаждение.
Кристаллизаторы с воздушным охлаждением (рис. XV1-8).
Основная часть аппарата — слегка наклонная, вращающаяся от привода труба 1, заключенная в кожух 2. Раствор поступает с верхнего конца трубы, а кристаллы выгружаются из ее нижнего конца. Воздух, подаваемый вентилятором 3, движется над раствором противотоком к направлению движения раствора. При вращении трубы раствор смачивает стенки аппарата, что увеличивает поверхность испарения. При воздушном охлаждении тепло от раствора отнимается довольно медленно, и кристаллы получаются более крупными, чем при водяном охлаждении, но при этом снижается производительность аппарата. Для предотвращения образования кристаллов на стенках барабана его покрывают снаружи тепловой изоляцией или помещают в обогреваемый кожух (трубы для обогрева 4). Средний расход воздуха составляет приблизительно 20 м3 на 1 кг кристаллов.
Кристаллизаторы с водяным охлаждением. По своей конструкции эти аппараты аналогичны барабанным кристаллизаторам с воздушным охлаждением. Раствор охлаждают через рубашку водой значительно быстрее, чем воздухом. Расход воды составляет 3-5 м3 на 1- м3 охлаждаемого раствора.
«Вальцовые» кристаллизаторы. Аппарат представляет собой горизонтальный вращающийся охлаждаемый изнутри металлический барабан 1 (рис. XVI-9). Он частично погружен в корыто 2 с кристаллизуемым раствором. Во избежание преждевременной кристаллизации корыто обогревается. Через полые валы 3, которые вращаются вместе с барабаном, внутрь последнего поступает и удаляется с противоположного конца охлаждающая вода, иногда холодильные рассолы. Валы соединены с неподвижными трубопроводами при помощи сальниковых уплотнений. За один оборот барабана и его поверхности образуется плотный тонкий слой кристаллов, которые снимаются с барабана ножом 4.
Вальцовые кристаллизаторы применяют главным образом для кристаллизации из расплавов или растворов, содержащих небольшие количества маточного раствора.
Помимо свойств кристаллизуемого материала и скорости охлаждения производительность «вальцовых» кристаллизаторов зависит от времени прохождения барабана через раствор, что, в свою очередь, определяется скоростью вращения и величиной погружения барабана. Скорость вращения барабана колеблется от 0,1 до 1 м/сек.
В вальцовых кристаллизаторах продукт из-за быстрого охлаждения получается мелкокристаллическим. Кроме того, кристаллы, образующиеся из расплавов, содержат все примеси, находящиеся в исходном расплаве. Это ограничивает область применения вальцовых кристаллизаторов.
Вакуум-кристаллизаторы. Эти кристаллизаторы не имеют охлаждающих устройств. Поэтому их можно изготовлять из коррозионностойких материалов с низкой теплопроводностью (например, из керамики, кислотоупорного чугуна и др.).
Однокорпусные вакуум-кристаллизаторы обычно представляют собой вертикальные аппараты цилиндрической формы с рамной или якорной мешалкой. Перемешивание раствора препятствует отложению кристаллов на стенках аппарата и ускоряет снижение концентрации раствора.
Отсасывание и конденсация паров растворителя осуществляются с помощью конденсатора или пароструйного насоса, присоединенного к верхней части аппарата.
Значительно более экономичны многоступенчатые вакуум-выпарные аппараты, состоящие обычно из 3—4 ступеней. Наибольшее разрежение поддерживают в последней ступени. Вследствие меньшего разрежения в остальных ступенях в них снижаются скорости испарения
растворителя и роста кристаллов; вместе с тем увеличиваются размеры кристаллов.
На рис. XVI-10 показана схема многокорпусной вакуум-кристаллизационной установки, в которой раствор из каждого нижерасположенного корпуса под действием разрежения засасывается в вышерасположенный корпус. Каждый корпус имеет поверхностный конденсатор и пароструйный насос. Разрежение в последнем корпусе создается с помощью барометрического конденсатора, а неконденсируемые газы удаляются посредством эжектора. Поверхностные конденсаторы охлаждаются вместо воды исходным раствором; одновременно они служат подогревателями исходного раствора. Выгрузку суспензии производят из последнего корпуса.
Вакуум-кристаллизаторы имеют большую производительность и широко используются в крупнотоннажных производствах.
При вакуум-кристаллизации обычно образуются мелкие кристаллы (со средним размером не более 0,1—0,15 мм). Применение вакуум-кристаллизаторов с принудительной циркуляцией и проведение процесса в псевдоожиженном слое дает возможность получать более крупные кристаллы.
Кристаллизаторы с псевдоожиженным слоем. Кристаллизация в псевдоожиженном слое помимо увеличения скорости процесса, способствует получению однородных правильной формы кристаллов размером 1—3 мм.
Интенсивное перемешивание в условиях псевдоожижения увеличивает скорость подачи материала путем диффузии его к граням растущих кристаллов, что ускоряет их рост. При этом быстро уменьшается степень пересыщения раствора. При больших скоростях раствора, как известно, увеличивается скорость образования зародышей это может привести к снижению
размеров кристаллов. При одинаковых температурах и гидродинамических условиях с уменьшением степени пересыщения скорость роста кристаллов возрастает в большей степени, чем
|
скорость образования зародышей. Обычно таким способом осуществляют кристаллизацию относительно слабо пересыщенных растворов вблизи нижней границы метастабильной области, регулируя степень пересыщения, температуру, соотношение количеств кристаллов и раствора, а также время пребывания кристаллов в аппарате. Крупные кристаллы осаждаются на дно, а более мелкие кристаллы продолжают расти в псевдоожиженном слое. Часть мелких кристаллов и зародышей потоком раствора выносится из аппарата. Это увеличивает средний размер получаемых кристаллов.
Кристаллизация в псевдоожиженном слое проводится или с удалением части растворителя испарением или с охлаждением раствора до его пересыщения.
Выпарной аппарат-кристаллизатор с псевдоожиженным слоем показан на рис . XVI-11. Исходный раствор смешивается с поступающим по трубе 7 маточным раствором, насосом 4 прокачивается через нагревательную камеру 1 и по трубе 5 поступает в расширяющуюся кверху трубу вскипания 8. После энергичного парообразования пересыщенный раствор по трубе 6 опускается в нижнюю часть корпуса кристаллизатора. Здесь происходят (во взвешенном состоянии) образование и рост кристаллов Более крупные кристаллы оседают на дно и отводятся снизу аппарата, а мелкие кристаллы удаляются через сборник 9. Во избежание накопления загрязнений часть маточного раствора удаляют из аппарата через фонарь 10.
В этих аппаратах кристаллизации подвергают растворы с небольшой степенью пересыщения, поэтому производительность кристаллизаторов такого типа невелика. Основное их
достоинство — получение крупных (не более 2 мм ) кристаллов веществ с отрицательной растворимостью.
Кристаллизаторы с охлаждением раствора аналогичны выпарным аппаратам-кристаллизаторам с псевдоожиженным слоем, в них по межтрубному пространству камеры 1 движется охлаждающая вода.√√√
16.5.6. Противоточная кристаллизация (В.Г.Айнштейш. Общий курс ПАХТ, 2003, ч.2)
Противоточная непрерывная фракционная кристаллизация является одним из наиболее перспективных методов разделения и очистки веществ*. Она позволяет достигать высоких степеней разделения при значительной производительности. В настоящее время данный метод успешно используется, в частности, для промышленного разделения ряда углеводородных смесей.
Создать противоток при кристаллизации значительно труднее, чем в других процессах разделения (ректификации, абсорбции) — вследствие малой разности плотностей кристаллической и жидкой фаз: обычно их плотности различаются менее чем в 1,1—1,3 раза. Поэтому противоток фаз в кристаллизаторах чаще всего осуществляют принудительно — с помощью различных механических устройств (шнеков, поршней, скребков, вращающихся барабанов и др.) или путем использования центробежных сил.
По принципу действия противоточные кристаллизаторы можно разделить на две группы — со ступенчатым и непрерывным контактом фаз (массообменом).
Особенностью ступенчатых кристаллизаторов является отсутствие четко выраженных секций (зон) охлаждения и разделения. В таких аппаратах в каждой ступени происходит плавление кристаллической фазы, поступающей с предыдущей ступени, и образование новой кристаллической фазы с более высокой концентрацией высокоплавкого компонента. Ступенчатые противоточные кристаллизаторы по принципу работы аналогичны другим ступенчатым массообменным аппаратам. Примером является многоступенчатый барабанный кристаллизатор**. Каждая ступень такого аппарата снабжена охлаждающим барабаном и обогреваемой ванной. Образующиеся на барабанах кристаллические слои снимаются ножами и поступают в ванну последующей ступени, где полностью расплавляются. Между ваннами имеются переточные трубки. При этом расплав перетекает из ванны в ванну противотоком относительно движения кристаллической фазы.
Для глубокой очистки небольших количеств вещества от примесей часто используют различные шнековые кристаллизаторы периодического и непрерывного действия.
_______________________________
* Более подробные сведения см. [5, 6].
** Подробнее конструкции противоточных кристаллизаторов см. [5, 6].
Гельперин Н.И., Носов Г.А.Основы техники кристаллизации растворов. М. : Химия, 1975. 352 с.
Гельперин Н.И., Носов Г.А. Основы техники фракционной кристаллизации. М.: Химия, 1986. 303 с.
На рис. 16.34,а показана схема непрерывного шнекового кристаллизатора с центральным питанием. В верхней части аппарата расположена секция (зона) охлаждения 2, где происходит образование кристаллической фазы (охлаждение производится хладагентом Gx). Транспортировка кристаллов в аппарате осуществляется шнеком 4. Внизу колонны (в плавителе 3) кристаллы расплавляются. Часть получаемого расплава отбирается в виде высокоплавкого продукта П, а другая часть возвращается в зону разделения, где движется противотоком к опускающимся кристаллам. Низкоплавкий продукт W выводится из верхней части колонны.
В противоточных кристаллизаторах поршневого типа (рис. 16.34,6) исходный расплав F подается первоначально в секцию охлаждения 2. Из нее образовавшаяся кристаллическая суспензия поступает в секцию разделения 1, где кристаллическая фаза перемещается к плавителю 3 с помощью поршня 5. Высокоплавкий продукт П выводится из зоны плавления 3, а низкоплавкий W — через фильтр 6, расположенный в верхней части секции разделения 1.
В кристаллизаторах пульсационного типа (рис. 16.34,в) противоток фаз осуществляется благодаря пульсатору. С этой целью на линиях подвода исходной смеси и отбора продуктов разделения установлены обратные клапаны.
Поршневые и пульсационные кристаллизаторы обладают значительной производительностью (до нескольких тонн разделяемой смеси в час) и используются в промышленности для разделения углеводородных смесей (в частности, для выделения 99,9% и-ксилола из его смеси с другими изомерами). Диаметр таких аппаратов достигает 1000 мм, а высота секции противоточного массообмена — 2—6 м.
Схема потоков фаз в многоступенчатом кристаллизаторе показана на рис. 16.35,а. Весь аппарат можно разбить по длине на четыре характерные секции: низкоплавкого продукта 1, питания 2, высокоплавкого продукта 3 и плавления 4.
Исходный расплав F с концентрацией высокоплавкого компонента х F подают в секцию питания, являющуюся одной из промежуточных ступеней аппарата. Обедненный высокоплавким компонентом продукт W с концентрацией х W выводят из первой секции в расплавленном виде. Обогащенная высокоплавким компонентом кристаллическая фаза К по выходе из третьей секции поступает в четвертую, где полностью расплавляется. При этом часть полученного расплава отбирается в виде конечного высокоплавкого продукта П с концентрацией хП, а другая часть — М — возвращается в секцию 3 в качестве флегмы.
Рассмотрим расчет многоступенчатых противоточных кристаллизаторов применительно к разделению бинарной смеси, образующей непрерывный ряд твердых растворов (рис. 16.35,6). Запишем уравнения материального баланса для всего аппарата в целом:
для потоков фаз
F = П+ W, (щ)
для потоков высокоплавкого компонента
FxP = Пхп + Wxw. (э)
При совместном решении уравнений (щ) и (э) получим выход высокоплавкого продукта:
(16.47)
Уравнения рабочих линий, представляющих собой геометрическое место точек сопряженных концентраций кристаллической (xк) и жидкой (хм) фаз, как и для других противоточньгх процессов, можно получить из уравнений материального баланса соответствующих секций.
Для контура K1 с потоками К, П и М (см. рис. 16.35,а) уравнение материального баланса высокоплавкого компонента имеет вид
Кхк = Пхп + Мхм ,
откуда получаем:
(16.48)
Уравнение (16.48) описывает рабочую линию секции высокоплавкого продукта.
Рассматривая контур к2 с потоками М', К' и W (см. рис. 16.35,а), имеем;
М'хм = К'хк + Wxw, откуда
(16.49)
Зависимость (16.49) представляет собой уравнение рабочей линии секции низкоплавкого продукта. При этом К' и М' — потоки кристаллической и жидкой фаз в данной секции.
Заметим, что ход рабочих линий зависит от соотношения потоков фаз в отдельных ступенях и эффекта продольного перемешивания. Если массовые потоки фаз одинаковы во всех ступенях и исключено продольное перемешивание между ступенями, то рабочие линии являются прямыми.
Необходимое число ступеней разделения здесь определяется теми же методами, что и для ректификации, абсорбции и жидкостной экстракции. Проводя графические построения в диаграмме хк — хм (см. рис. 16.35,6), определяют необходимое число теоретических ступеней для достижения заданных концентраций продуктов разделения хП, и хW. Зная найденные из опыта коэффициенты эффективности разделения (КПД ступеней), находят число реальных ступеней разделения.
Противоточные кристаллизаторы с непрерывным массообменом (шнековые, поршневые, пульсационные) по принципу действия и в расчетном плане аналогичны насадочным и пленочным абсорбционным и ректификационным колоннам. Состав фаз по длине таких аппаратов изменяется плавно. Исходная смесь может подаваться, как в центральную, так и в торцевую часть кристаллизатора.
Расчеты кристаллизаторов
Материальный баланс кристаллизации
Кристаллизация с удалением части растворителя. Обозначим:
Gp, Gкр, Gм — количества исходного раствора, полученных кристаллов и маточного раствора, кг;
Bp , b м — концентрации исходного и маточного растворов, вес. доли;
а = М/Мкр — отношение молекулярных весов абсолютно сухого растворенного вещества и кристаллосольвата (для водного раствора кристаллогидрата); при кристаллизации без присоединения молекул растворителя М = Мкр и а = 1;
W — количество удаленного растворителя, кг.
Тогда общий баланс будет:
Gр = Gкр + Gм + W (XVI, 1)
Баланс по абсолютно сухому растворенному веществу:
Gр bр = Gкр a + G м bм (XVI, 2)
Весовое количество полученных кристаллов определяется совместным решением уравнений (XVI, 1) и (XVI, 2). Обычно Gpbp, buи а известны; W вычисляют при помощи уравнения (IX, 9) по заданным Gp, bpи bM . Величина G кр составляет:
Gккр= ( XVI, 3)
При а = 1 имеем
(XVI, 4)
Кристаллизация без удаления растворителя (W=0). Количество полученных кристаллов
(XVI. 5)
При а = 1 находим
(XVI, 6)
При испарении растворителя в газ (воздух) расход газа (в кг) определяется из уравнения
(XVI, 7)
где L — расход сухого газа (воздуха), кг; х1 х2 — начальное и конечное влагосодержание газа (воздуха), кг влаги/кг сухого газа
Тепловой баланс непрерывной кристаллизации
При растворении твердого кристаллического вещества происходит поглощение тепла q к p для разрушения кристаллической решетки (теплота плавления) и выделение тепла при химическом взаимодействии вещества с растворителем qp (образование гидратов). В зависимости от величин q к p и qp тепловой эффект кристаллизации будет положительным или отрицательным.
Помимо принятых в материальном балансе введем следующие обозначения: iр, iкр, iм — энтальпия раствора, кристаллов и маточного раствора, кдж/кг; iт1, iт2 — начальная и конечная энтальпия теплоносителя, кдж/кг; i 01 , io 2 — начальная и конечная энтальпия охлаждающей среды, кдж/кг; I — энтальпия парообразного растворителя, кдж/кг; r — теплота образования кристаллической решетки (теплота затвердевания), кдж/кг кристаллов; Δq— тепловой эффект концентрирования раствора при изменении его концентрации от b р до b м кдж; GT, G0 — количество теплоносителя или охлаждающей среды, кг/сек.
В общем случае будем иметь:
Приход тепла | Расход тепла | ||
С раствором | G р i р = Q 1 | С кристаллами | G кр i кр = Q 5 |
Теплота кристаллизации | G кр r = Q 2 | С маточным раствором | Gм iм = Q 6 |
Теплота дегидратации | ±ΔqG м b м = Q 3 | С парами растворителя | WI = Q7 |
Получено от теплоносителя | Gт (iт1 – iт2 )= Q 4 | С охлаждающим агентом Потери в окружающую среду | Go(i02- i01) = Q8 Q9 |
Тогда можно записать:
Q1 + Q2 + Q3 + Q4 = Q5 + Q6 + Q6 + Q7 ± Q9
При кристаллизации с охлаждением Q4 = 0 и Q7 = 0; при кристаллизации с испарением части растворителя Q 8 == 0; при вакуум-кристаллизации Q4 = 0 и Q 8 = 0.
Для теплоносителя — насыщенного водяного пара (в кдж)
Q 4 = D (ID – iконд)
где ID , iконд — энтальпии пара и конденсата, кдж/кг; D —расход пара, кг/сек.
Для охлаждающей среды — воздуха (в кдж/сек)
Q 8 = L (12 — I 1)
где L — расход сухого воздуха, кг/сек; I 1, 12 — его начальная и конечная энтальпии. кдж/ кг
В зависимости от температурных условий потери тепла Q9 могут быть положительны или отрицательны.
Энтальпии i р, iкр, iмрассчитывают (в кдж/кг) по уравнению общего вида
i = с(t2 — t1)
в котором с — средняя теплоемкость, кдж/(кг-град); ( t 2 — tt ) — перепад температур (конечной и начальной).
Напряженность поверхности по испаренной влаге в воздушных кристаллизаторах в среднем можно принять 0,042 кг/(м2ч). Расчет размеров поверхности охлаждения или нагревания производится по общим правилам расчета теплообменных поверхностей (см. главу VII). Более подробные расчеты процессов кристаллизации из растворов приведены в специальной литературе*.
-----------------------------
* См., например: Л. Н М а т у с е в и ч, Кристаллизация из растворов в химической промышленности, Изд. «Химия», 1968
Дата добавления: 2018-10-27; просмотров: 2863; Мы поможем в написании вашей работы! |
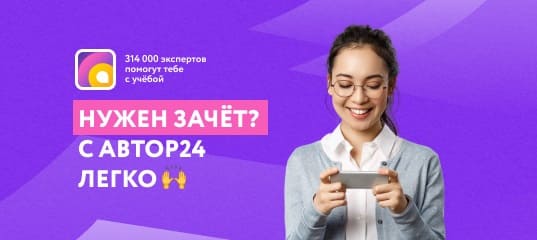
Мы поможем в написании ваших работ!