Процессы, происходящие в металлах и сплавах при нагревании. Динамика изменения механических и теплофизических свойств.
Опасные факторы пожара и свойства строительных материалов, влияющие на их образование. Поведение строительных материалов в условиях пожара и определяющие это поведение факторы.
Любой пожар сопровождается проявлением опасных факторов пожара. Опасный фактор пожара (ОФП) – фактор пожара, воздействие которого приводит к травме, отравлению или гибели человека, а также к материальному ущербу.
Опасными факторами пожара (ОФП), воздействующими на людей и материальные ценности, являются:
- пламя и искры;
- повышенная температура окружающей среды;
- токсичные продукты горения и термического разложения;
- снижение видимости в дыму;
- пониженная концентрация кислорода.
К вторичным проявлениям опасных факторов пожара относятся:
- осколки, части разрушившихся аппаратов, агрегатов, установок, конструкций;
- радиоактивные и токсичные вещества и материалы из разрушенных аппаратов и установок;
- электрический ток, возникший в результате выноса высокого напряжения на токопроводящие части конструкций, аппаратов, агрегатов;
- опасные факторы взрыва, произошедшего в результате пожара;
- воздействие огнетушащие вещества.
Под поведением строительных материалов в условиях пожара понимается комплекс физико-химических превращений, приводящих к изменению состояния и свойств материалов под влиянием интенсивного высокотемпературного нагрева.
Основные виды металлов и сплавов. Строение, механические и теплофизические свойства.
|
|
К металлам относятся вещества, обладающие высокими теплопроводностью и электрической проводимостью, ковкостью, блеском и другими характерными свойствами, которые обусловлены наличием в их кристаллической решетке большого числа свободных электронов.
Единственными объективными критериями, позволяющими отнести материал к металлам, считаются наличие электропроводности при Т = 0 К и положительный температурный коэффициент удельного сопротивления. Указанными выше свойствами обладают свыше 80 простых веществ (элементов) и множество металлических сплавов.
Все металлы и сплавы делят на черные (к ним относят железо и сплавы на его основе; на их долю приходится около 95 % производимой в мире металлопродукции) и цветные или, точнее, нежелезные (все остальные металлы и сплавы). По физическим и химическим свойствам и характеру залегания в земной коре нежелезные металлы делят на следующие группы: легкие – алюминий, магний, титан, бериллий, литий, натрий, калий, стронций, барий и др.; тяжелые – медь, никель, кобальт, свинец, олово, цинк, кадмий, сурьма, висмут, ртуть и др.; тугоплавкие – вольфрам, молибден, ниобий, тантал, ванадий, хром, цирконий и др.; благородные – золото, серебро, платина и платиноиды (рутений, родий, палладий, осмий, иридий); рассеянные – галлий, индий, таллий; редкоземельные – скандий, иттрий, лантан и все лантаноиды; радиоактивные – технеций, франций, радий, полоний, актиний, торий, уран и трансурановые элементы.
|
|
Приведенная классификация условна: многие металлы могут быть отнесены одновременно к разным группам. Например, легкий металл титан является также тугоплавким; тугоплавкий металл рений – типичный рассеянный элемент и т.д.
Металлы играют огромную роль в современной технике. Обычно металлы применяют не в чистом виде, а в виде сплавов, количество которых превышает 10 тысяч.
Металлы получают из руд, а также путем вторичной переработки материалов. Рудами называют горные породы, которые технически возможно и экономически целесообразно перерабатывать для извлечения содержащихся в них металлов. К основным процессам металлургического процесса относятся: обработка руд с целью их подготовки к извлечению металлов (дробление, обогащение, окускование и пр.); извлечение металлов из руд и других материалов; очистка металлов от нежелательных примесей; производство металлов и сплавов; термическая, химико-термическая и термомеханическая обработка; формообразование давлением и литьем; покрытие в декоративных или защитных целях поверхности изделий из металла слоями другого металла.
|
|
К основным свойствам металлов и сплавов относятся физические (в том числе механические), химические, технологические и функциональные. К физическим свойствам относятся: температура плавления, цвет, плотность, магнитная восприимчивость, электропроводность, теплоемкость и др. Особую группу составляют механические свойства: прочность, пластичность, твердость, ударная вязкость и др.
Химические свойства металлов определяются способностью их атомов легко отдавать валентные электроны и переходить в состояние положительно заряженных ионов. Указанное определяет особенности химического взаимодействия металлов и сплавов с агрессивными средами.
К технологическим свойствам металлов и сплавов относится их способность к формоизменению (ковкость, свариваемость и т.д.). Важное значение имеет жидкотекучесть – свойство расплавленного металла заполнять и точно воспроизводить литейную форму.
Функциональные или эксплуатационные свойства включают в себя хладостойкость, жаропрочность, жаростойкость, антифрикционность и другие характеристики материалов, определяемые условиями их работы.
|
|
Металлы и сплавы в твердом состоянии имеют поликристаллическую структуру, состоящую из отдельных зерен – монокристаллических областей, ориентированных относительно друг друга под различными углами. На границе между зернами атомы имеют менее правильное расположение, чем в объеме зерна. Линейный размер зерен составляет 1–104 мкм.
С помощью рентгеноструктурного анализа установлено, что кристаллическое строение твердых тел, состоящих из различных атомов, описывается 14 различными типами пространственных элементарных ячеек.
Наиболее широко применяются металлы и сплавы, образованные одним из 3-х типов пространственных решеток, определяемых отдельно взятой элементарной ячейкой: кубической объемно центрированной ОЦК (a–Fe, b–Fe, d–Fe, Cr, W, Mo, V и др.); кубической гранецентрированной ГЦК (g–Fe, Cu, Al, Ni, Pb и др.); гексагональной плотноупакованной ГПУ (Ti, Mg, Zn, Be и др.) (рис. 3.1).
Переход металла из жидкого состояния в твердое (кристаллическое) называется кристаллизацией. Подвижность атомов при снижении температуры уменьшается, устанавливается определенный порядок в их расположении с образованием отдельных групп атомов, близких к элементарным ячейкам, имеющимся в твердом металле. Возникают центры кристаллизации – зародыши, вокруг которых постепенно образуется твердая фаза. Кристаллизация происходит вследствие перехода к более устойчивому состоянию с меньшей свободной энергией.
Чистые металлы в большинстве случаев не обеспечивают необходимого комплекса механических, технологических и функциональных свойств и поэтому применяются редко. В большинстве случаев в технике используют сплавы.
Металлическим сплавом называют материал, состоящий из двух или более компонентов и обладающий свойствами, характерными для металлов. Сплавы создаются в результате расплавления, спекания исходных компонентов и другими методами [7]. Необходимым процессом получения сплава является диффузия элементов в твердом, жидком или газообразном состоянии. Диффузия осуществляется путем взаимного проникновения частиц каждого из компонентов сплава с образованием новых однородных тел, называемых фазами.
Для описания свойств сплавов в металловедении используют понятия: система, фаза, компонент.
Системой называют совокупность фаз, находящихся в равновесии при определенных внешних условиях (температуре, давлении).
Фазой называют однородную по химическому составу, кристаллическому строению и свойствам часть системы, отделенную от ее других частей поверхностью раздела. Однофазной системой являются, например, однородная жидкость, твердый чистый металл; двухфазной – механическая смесь двух видов кристаллических веществ.
Компонентами называют вещества, образующие систему. Компонентами могут быть элементы (металлы и неметаллы), а также химические соединения. По числу компонентов различают двойные, тройные и многокомпонентные сплавы. Компонент сплавов может быть основным, легирующим или случайным.
Сплавы, находящиеся в твердом состоянии, делят по составу на 3 группы: твердый раствор, химическое соединение, механическая смесь компонентов.
Твердый раствор. В жидком состоянии большинство металлических сплавов представляет собой однородные жидкости, т.е. жидкие растворы. При переходе в твердое состояние во многих таких сплавах однородность, а следовательно и растворимость, сохраняется. Твердый раствор, как и металл, имеет одну кристаллическую решетку, соответствующую типу кристаллической решетки основного компонента сплава (растворителя). Различие состоит в том, что в кристаллической решетке металла размещаются атомы одного элемента, а в твердом растворе – атомы различных элементов, образующих этот твердый раствор.
Процессы, происходящие в металлах и сплавах при нагревании. Динамика изменения механических и теплофизических свойств.
При нагреве металла происходит изменение его энтальпии, а поскольку в большинстве случаев подвод тепла производится к поверхности слитков и заготовок, то их наружная температура выше температуры внутренних слоев. В результате термического расширения разных частей твердого тела на разную величину возникают напряжения, получившие название термических.
Другая группа явлений связана с химическими процессами на поверхности металла при нагреве. Поверхность металла, находящаяся при высокой температуре, вступает во взаимодействие с окружающей средой (т. е. с продуктами сгорания или с воздухом), в результате чего на ней образуется слой оксидов. В случае, если какие-либо элементы сплава взаимодействуют с окружающей металл средой с образованием газовой фазы, то происходит обеднение поверхности этими элементами. Например, окисление углерода стали при ее нагреве в печах, вызывает поверхностное обезуглероживание.
Термические напряжения
Как отмечено выше, в сечении слитков и заготовок при их нагреве возникает неравномерное распределение температур и, следовательно, разные части тела стремятся изменить свой размер в разной степени. Так как в твердом теле существуют связи между всеми отдельными его частями, то они не могут независимо деформироваться в соответствии с теми температурами, до которых они нагреты. В результате возникают термические напряжения, обусловленные разностью температур. Наружные, более нагретые слои, стремятся расшириться и находятся, поэтому в сжатом состоянии. Внутренние, более холодные слои, подвержены при этом растягивающим усилиям. Если эти напряжения не превосходят предела упругости нагреваемого металла, то с выравниванием температуры по сечению термические напряжения исчезают.
Все металлы и сплавы обладают упругими свойствами до определенной температуры (например, большинство марок стали до 450—500 °С). Выше этой определенной температуры металлы переходят в пластическое состояние и возникшие в них термические напряжения вызывают пластическую деформацию и исчезают. Следовательно, температурные напряжения должны учитываться при нагреве и охлаждении стали только в интервале температур от комнатной до точки перехода данного металла или сплава из упругого состояния в пластическое. Такие напряжения называются исчезающими, или временными.
Кроме временных, существуют остаточные температурные напряжения, увеличивающие опасность разрушения при нагреве. Эти напряжения возникают в случае, если слиток или заготовка ранее подвергались нагреву и охлаждению. При охлаждении наружные слои металла (более холодные) раньше достигают температуры перехода из пластического в упругое состояние. По мере дальнейшего охлаждения внутренние слои оказываются под воздействием растягивающих усилий, которые не исчезают вследствие малой пластичности холодного металла. Если этот слиток или заготовка будут снова нагреты, то возникающие в них временные напряжения наложатся с тем же самым знаком на остаточные, что усугубит опасность возникновения трещин и разрывов.
Помимо временных и остаточных температурных напряжений при нагреве и охлаждении сплавов возникают также напряжения, вызванные структурными изменениями объема. Но так как эти явления имеют место обычно при температурах, превышающих границу перехода из упругого состояния в пластическое, то структурные напряжения рассеиваются в связи с пластическим состоянием металла.
Нагрев металлов и сплавов производят либо для уменьшения их сопротивления пластической деформации (т. е. перед ковкой или прокаткой), либо для изменения кристаллической структуры происходящего под воздействием высоких температур (термообработка). В каждом из этих случаев условия протекания процесса нагрева оказывают существенное влияние на качество конечного продукта.
Решаемые задачи предопределяют основные характеристики процесса нагрева: температуру, равномерность и продолжительность.
Температурой нагрева обычно называют конечную температуру поверхности металла, при которой он в соответствии с требованиями технологии может быть выдан из печи. Значение температуры нагрева зависит от химического состава (марки) сплава и от цели нагрева.
При нагреве перед обработкой давлением температура выдачи заготовок из печи должна быть достаточно высокой, так как это способствует уменьшению сопротивления пластической деформации и приводит к сокращению расхода электроэнергии на обработку, повышению производительности прокатного и кузнечного оборудования, а также увеличению срока его службы.
Однако существует верхний предел температуры нагрева, поскольку она лимитируется ростом зерна, явлениями перегрева и пережога, а также ускорением окисления металла. В процессе нагрева большинства сплавов при достижении точки, лежащей на 30-100°С ниже линии солидус на их диаграмме состояния, благодаря ликвации и неметаллическим включениям, на границах зерен появляется жидкая фаза; это приводит к ослаблению механической связи между зернами, интенсивному окислению на их границах; такой металл теряет прочность и разрушается при обработке давлением. Это явление, называемое пережогом, лимитирует максимальную температуру нагрева. Пережженный металл не может быть исправлен никакой последующей термической обработкой и пригоден только для переплавки.
Перегрев металла приводит к чрезмерному росту зерна, в результате чего ухудшаются механические свойства. Поэтому прокатка должна завершаться при температуре более низкой, чем температура перегрева. Перегретый металл можно исправить посредством отжига или нормализации.
Низший предел температуры нагрева устанавливают исходя из допускаемой температуры в конце обработки давлением с учетом всех потерь тепла от заготовки в окружающую среду и выделения тепла в ней самой за счет пластической деформации. Следовательно, для каждого сплава и для каждого вида обработки давлением существует определенный диапазон температур, выше и ниже которого не следует нагревать заготовку. Эти сведения приведены в соответствующих справочниках.
Дата добавления: 2018-10-27; просмотров: 2187; Мы поможем в написании вашей работы! |
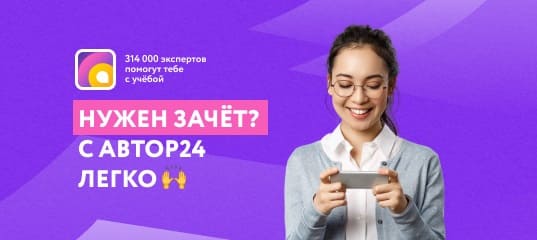
Мы поможем в написании ваших работ!