Продукты доменного производства
Основным продуктом доменного производства является чугун. В чугуне углерод может содержаться в виде механической примеси (свободного графита) и химического соединения — карбида железа (Fe3C), называемого цементитом.
Чугуны, содержащие свободный графит, имеют в изломе серый цвет и крупнозернистое строение. Эти чугуны применяются для получения отливок, так как хорошо заполняют литейные формы и достаточно легко поддаются обработке режущим инструментом. Такой чугун называют серым или литейным чугуном. Характерным для него является повышенное содержание кремния и пониженное — серы.
Чугуны, содержащие углерод в виде химического соединения с железом (Fe3C), имеют белый излом. Для отливок они малопригодны и трудно обрабатываются режущим инструментом. Эти чугуны преимущественно перерабатываются на сталь, они имеют пониженное содержание кремния и называются белыми или передельными чугунами.
Кроме литейных и передельных чугунов в доменных печах получают специальные чугуны, или ферросплавы. Ферросплавы имеют повышенное (более 10%) содержание некоторых элементов, например кремния, марганца. Применяются ферросплавы в качестве специальных присадок при выплавке стали.
Кроме чугуна в доменном .производстве получают доменный газ и шлак.
Доменный газ и шлак представляют собой побочные продукты плавки.
Доменный газ используется в качестве топлива. Он улавливается в области колошника и подвергается очистке. Около 25% доменного газа используется непосредственно в доменном процессе, остальные 75% идут для сжигания на ТЭЦ.
|
|
Шлак идет для производства строительных материалов
32. Технология производства стали в кислородных конвертерах
33. Технология производства стали в мартеновских печах
34. Технология производства стали а электрических печах
Металлургия стали
Значительную часть стали получают из передельного чугуна. Сущность процесса заключается в уменьшении в чугуне содержания углерода и примесей (серы, фосфора, кремния и марганца) путем их окисления. Кроме чугуна в состав шихты могут входить металлический лом, железная руда, флюсы. Сталь выплавляют в кислородных конверторах, мартеновских и электрических печах.
Выплавка стали в кислородных конвертерах
Сущность процесса заключается в том, что через расплавленный чугун и небольшое количество металлического лома черных металлов, загруженных в конвертор, продувается кислород, образуется оксид железа FО, который, взаимодействуя с углеродом и примесями чугуна, окисляет и обращает их в газ и шлак. Реакции окисления идут с выделением тепла. Чугун при этом превращается в сталь. Конвертер с кислородным дутьем (рис. 2) состоит из стального корпуса, футерованного огнеупорным кирпичом. Конвертер имеет поворотное устройство, с помощью которого может устанавливаться в наклонном положении. В таком положении его заливают жидким чугуном, затем устанавливают вертикально и через фурму производят продувку кислородом. По окончании процесса конвертер вновь наклоняют и выпускают сталь и шлак.
|
|
Емкость современных конвертеров составляет 300— 350 т. Продолжительность плавки 30—40 минут. Температура, развиваемая в плавильном пространстве, достигает 1800 °С. Высокая производительность агрегата, простота конструкции и обслуживания, отсутствие потребности в топливе обеспечивают невысокую себестоимость конверторной стали.
К недостаткам работы конверторов относятся невозможность переработки значительного количества металлического лома, значительный угар металла (5—10%), повышенное содержание вредных примесей в получаемой стали.
Конвертерная сталь относится к стали обыкновенного качества. Такая сталь идет для получения проката различного профиля — листов, прутков, трубного проката, уголков и т. д. Кислородное конвертирование — перспективный процесс, поскольку с его помощью в последние годы освоено получение качественной стали.
|
|
Выплавка стали в мартеновских печах
Процесс выплавки разработан французскими металлургами Э. и П. Мартенами. Он отличается более высокой по сравнению с конвертированием температурой, развиваемой в плавильном пространстве печи, — 1800—1900 °С, что позволяет перерабатывать чугун в твердом, жидком состоянии, стальные отходы металлургического и машиностроительного производства. В состав шихты могут входить железная руда, флюсы, марганец. В качестве топлива в мартеновском процессе используется природный газ.
Мартеновская печь (рис. 3) работает следующим образом.
Шихта через загрузочные окна 1 загружается в плавильное пространство 2, выложенное огнеупорным кирпичом. Природный газ и воздух, образующие факел для расплавления шихты, поступают по каналам сначала справа, а продукты горения отводятся слева через регенератор 3, отдавая свое тепло кирпичной кладке регенератора. Через каждые 10—15 минут направления потоков газов изменяются на обратные. Природный газ и воздух, проходя через регенератор, утилизируют тепло отходящих газов. Из регенератора после очистки продукты горения отводятся.
|
|
Готовая сталь выпускается через отверстие — летку, расположенную в задней стенке печи.
Различают два варианта мартеновского процесса: скрап-процесс и скрап-рудный процесс.
При скрап-процессе шихта на 60—80% состоит из стального лома и на 20—40% — из чушкового чугуна. Такой процесс используется на металлургических заводах, где нет доменных печей. Скрап-процесс позволяет вводить в состав стали легирующие добавки (марганец, хром, ванадий и др.), улучшающие качество стали.
При скрап-рудном процессе шихта состоит на 60—75% из жидкого чугуна, небольшого количества железной руды и металлического лома. Этот процесс используется на металлургических заводах, имеющих доменные печи. Скрап-рудный процесс — наиболее распространенный процесс плавки.
Емкость мартеновских печей достигает 900 т. Время плавки составляет 3—6 часов. Достоинством мартеновского способа является возможность широкого использования в составе шихты металлического лома и получения качественной стали. Основными недостатками мартеновского процесса следует считать значительную продолжительность плавки и большой расход топлива.
Выплавка стали в электрических печах
Электросталеплавильный процесс, появившийся в конце XIX в., благодаря поддержанию в плавильном пространстве повышенной температуры (порядка 2000 °С и выше), обеспечивает получение стали более высокого качества по сравнению с конверторным и мартеновским процессами. Высокая температура дает возможность полнее удалять примеси, вводить в состав стали тугоплавкие легирующие металлы, значительно повышающие ее прочность, твердость и коррозийную стойкость.
Электрические плавильные печи разделяются на дуговые и индукционные.
Дуговая электрическая печь (рис. 4) состоит из стального кожуха, футерованного огнеупорным кирпичом. Сверху через отверстия в своде печи введены угольные электроды. Шихта загружается через загрузочное окно 1. Шихта плавится под воздействием высокой температуры, создаваемой электрической дугой, возникающей при прохождении электрического тока между электродами 2 и шихтой 3. Готовую сталь выпускают по желобу летки 4 при наклоне печи, осуществляемом с помощью поворотного механизма 5.
Емкость дуговых печей колеблется от 0,5 до 400 т, длительность плавки составляет 3-6 часов.
В индукционной печи (рис. 5) плавка осуществляется в тигле из огнеупорного материала 1. Вокруг тигля располагается спиральный индуктор 2, изготовленный из медной трубки, в которой циркулирует охлаждающая вода.
При прохождении тока через индуктор в шихте 4 наводятся мощные вихревые токи, которые обеспечивают плавление шихты. Шихтовые материалы загружаются сверху. Для выпуска готовой стали тигель наклоняют в сторону сливного желоба 3.
В индукционных печах выплавляют особо высококачественные стали. Вместимость печей составляет от десятков килограммов до 2—5 т металла. Продолжительность одной плавки составляет от 0,5 до 2,5 часов.
Электрометаллургический процесс — основной способ производства высококачественных и особо высококачественных сталей. Вместе с тем, себестоимость электростали значительно выше конверторной и мартеновской стали. Недостатком электрических печей является относительно малая вместимость, сложность и высокая стоимость электрооборудования, низкая стойкость электродов и тиглей, необходимость использования чистых шихтовых материалов.
Разливка стали
Разливка стали имеет важное значение в, металлургии и позволяет придать полученной стали первичную форму — форму слитка.
Применяют два способа разливки: разливка в изложницы и непрерывная разливка стали (рис. 6).
Разливка в изложницы подразделяется на разливку сверху и сифонную разливку.
Разливка сверху используется для получения крупных слитков (десятки тонн). Преимуществом разливки является простое разливочное оборудование, а недостатками — малая производительность и повышенные потери материала за счет усадочной раковины, образующейся в слитке при затвердевании стали.
Сифонный способ разливки (разливка снизу) позволяет получать небольшие слитки (тонны). Производительность процесса выше разливки сверху, поскольку заполняется одновременно несколько изложниц, потери материала меньше. Недостаток способа — сложное разливочное оборудование.
Непрерывная разливка стали — наиболее производительный и экономичный способ разливки. Из ковша 1 через разливочное устройство расплавленная сталь поступает в охлаждаемый водой кристаллизатор 2. В кристаллизаторе сталь затвердевает и в виде слитка 3 непрерывно вытягивается вращающимися роликами 4. Нужной длины слитки отрезаются ацетилено-кислородной горелкой 5.
Преимуществом непрерывной разливки является высокая производительность процесса, возможность получения необходимой формы сочетания слитки, что позволяет направить их непосредственно на обработку резанием и прокатку. При непрерывной разливке до пяти раз сокращаются отходы материалы по сравнению с разливкой в изложницы.
Недостатком способа является сложность разливочного оборудования. Однако применение непрерывной разливки стали в мире быстро увеличивается. Перспективной является организация единого технологического процесса: непрерывная разливка — прокатка стали.
Прогрессивные способы получения стали
Бездоменная металлургия. Прогрессивным способом является получение стали прямым восстановлением из руд, минуя доменный процесс. Железистый концентрат поступает по пульпопроводу прямо на завод, где вавтоматических шахтных печах при температуре 1000 0С получают металлизированные окатыши. Окатыши в качестве шихты поступают в электропечи. Полученный материал после непрерывной разливки сразу идет на прокатку.
Способ весьма экономичен. Отпадают затраты на коксохимическое производство, качество полученной стали высокое, поскольку в рудах Курской магнитной аномалии практически отсутствуют фосфор и сера. Производительность бездоменного процесса заметно выше традиционных способов выплавки стали.
Электрошлаковый переплав (ЭШП). Данным способом получают особо высококачественные легированные стали. Для этого сталь обыкновенного качества подается в установку ЭШП в виде прутков-электродов. Вследствие сопротивления электрода проходящему току выделяется большое количество теплоты, отчего электрод плавится. Расплавленный металл электрода проходит через слой специального жидкого шлака и очищается от вредных примесей и газов. Аналогичный способ — плазменно-дуговой переплав (ПДП). Источником тепла здесь служит плазменная дуга с температурой до 10000 0С. Используется также электронно-лучевой переплав (ЭЛП). Плавление происходит под действием потока электронов, излучаемых высоковольтной кобальтовой пушкой с созданием в плавильном пространстве глубокого вакуума.
Достоинствами перечисленных способов является возможность получения стали и сплавов очень высокой чистоты, применение которых облегчает массу конструкций, увеличивает надежность и долговечность машин и механизмов. Такая сталь необходима для атомной, реактивной и космической техники.
35. Технология получения алюминия
Производство алюминия
Алюминий — металл серебристо-белого цвета, температура его плавления 660 0С, плотность 2,7 т/м3. Алюминий обладает высокой электро- и теплопроводностью, уступая по этим свойствам серебру и меди, пластичностью и малой окисляемостью. Прочность и твердость алюминия невысокие.
Наибольшее применение алюминий получил в электротехнической промышленности для изготовления проводов и кабелей. Сплавы алюминия широко применяются в авиации, машиностроении, пищевой промышленности.
Получают алюминий из руд с высоким содержанием глинозема: бокситов, нефелинов, алунитов и коалинов. Основным сырьем для получения алюминия являются бокситы (50-60% глинозема).
Процесс получения алюминия состоит из двух стадий: получение глинозема (Аl203) из руды и производство алюминия из глинозема. В зависимости от состава и свойств исходного сырья применяют различные способы получения глинозема. Наиболее эффективным из них является щелочной способ. Выход глинозема из руды при этом способе составляет около 87%.
Глинозем представляет собой прочное химическое соединение, температура его плавления — 2050 0С. В этих условиях восстановление алюминия из глинозема весьма затруднительно. Поэтому алюминий получают электролизом из глинозема, растворённого в расплавленном криолите (3NaFuAlF3). Процесс проходит в электролизных ваннах (электролизерах). Ванна (рис. 8) представляет собой металлический корпус, футерованный углеродистыми блоками. В них вставляются медные катодные шины. Сверху в ванну опускается угольный электрод, представляющий собой анод.
В результате электролиза на дне ванны собирается жидкий алюминий, который периодически откачивается с помощью вакуумного насоса.
Для увеличения степени чистоты алюминия его рафинируют. С этой целью алюминий в ковшах при температуре 650-770 0С подвергают продувке хлором в течении 10-15 минут. Из алюминия удаляются примеси глинозема, криолита и газы. Готовый алюминий разливают в изложницы.
Алюминий высокой чистоты получают электролитическим рафинированием. Анодом в этом случае служит подлежащий очистке алюминий, катодом — пластины из чистого алюминия. Расплавы хлористых и фтористых солей используются в качестве электролита.
36. Технология получения меди
Металлургия цветных металлов
Широкое применение цветных металлов объясняется их специфическими свойствами: высокими электро- и теплопроводностью, коррозийной стойкостью, жаропрочностью. Кроме того, цветные металлы способны образовывать сплавы друг с другом и с черными металлами.
Цветные металлы классифицируют на четыре группы:
тяжелые — медь, никель, свинец, цинк, олово;
легкие — алюминий, магний, титан, кальций и др.;
благородные — золото, серебро, платина;
редкие — молибден, вольфрам, ванадий, уран и др.
Производство меди
Медь имеет красный цвет, температура ее плавления 1083 °С, плотность 8,96 т/м3. Медь хорошо проводит электричество и тепло, отличается малой прочностью, высокой пластичностью. Медь используется в электро- и радиопромышленности, значительная часть ее идет на получение сплавов.
Около 80% меди выплавляют из сульфидных руд. Основными медными рудами являются медный колчедан (CuFeS2) и медный блеск (Cu,S).
Медные руды относительно бедны (содержание меди — не более 5%), поэтому их подвергают обогащению. С этой целью используют метод флотации, основанный на способности тонко измельченных рудных минералов смачиваться некоторыми реагентами. Смесь измельченной руды, воды и реагентов помещается в специальной ванне, через которую пропускается воздух. Благодаря пузырькам воздуха на поверхность ванны поднимаются частицы рудных минералов, а пустая порода осаждается и удаляется. Содержание меди в полученном концентрате достигает до 30%.
Медный концентрат после обогащения содержит сернистые соединения. Для снижения содержания серы концентрат подвергают обжигу, который ведут в специальных печах при температуре 700—800 0С.
В результате обжига получают так называемый огарок и сернистый газ S02. Огарок направляется на плавку. Сернистый газ используется для получения серной кислоты.
Плавка огарка производится в отражательных печах, по устройству сходных с мартеновскими. В них одновременно может плавиться более 100 т огарка.
В конце плавки в печи образуется полупродукт — штейн (Cu2S4FeS), содержащий до 50% меди, а также железо, серу, кислород и включающий небольшое количество золота, серебра, свинца и других металлов. Штейн сливают и направляют в конверторы для получения черновой меди.
Конвертор представляет собой футерованный изнутри металлический сосуд, установленный на опорных роликах и поворачивающийся вокруг горизонтальной оси (рис. 7). Масса плавки составляет до 1000 т. Воздушное дутье подается через фурмы, расположенные вдоль конверторов. Затем в конвертор подается кварцевый флюс. Продувка длится до 30 часов. В результате получают черновую медь.
Черновая медь содержит примеси железа, серы, мышьяка, кислорода.
Примеси ухудшают свойства меди, поэтому черновую медь подвергают рафинированию. Рафинирование меди производится огневым и электролитическим способами. Огневое рафинирование осуществляется в пламенных печах и производится в том случае, когда пренебрегают небольшим количеством благородных металлов, содержащихся в черновой меди. Окисление примесей в печи происходит за счет кислорода воздуха, который подается в жидкий металл. Готовую медь разливают на слитки или анодные пластины.
Для получения высококачественной меди и выделения из нее благородных металлов производят электролитическое рафинирование. Для этого черновую медь в виде пластин (анодов) погружают в ванну с водным раствором медного купороса в серной кислоте. Параллельно анодам подвешивают тонкие листы чистой меди (катоды). При прохождении постоянного тока аноды растворяются в воде и медь осаждается на катодах. За 10—12 суток на катодной пластине отлагается около 100 кг меди. Катоды затем переплавляют и разливают в слитки.
В зависимости от степени чистоты различают ряд марок меди (М00, МО, Ml, М2, МЗ, М4) с содержанием меди от 99,0 до 99,95%.
37. Обработка металлов давлением
Обработка металлов давлением
Сущность и значение процессов обработки металлов давлением
Способность металлов принимать пластическую деформацию в горячем и холодном состоянии широко используется в технике. При этом изменение формы осуществляется преимущественно с помощью давящего на металл инструмента, поэтому получение изделий таким способом называется обработкой металла давлением, или пластической обработкой.
Обработка металла давлением представляет собой важный технологический процесс. При этом обеспечивается не только придание слитку или заготовке необходимой формы и размеров, но совместно с другими видами обработки существенно улучшаются механические и другие свойства металлов.
Обработка металлов давлением основана на использовании пластичности металлов, способности твердого тела под действием внешних сил необратимо изменять форму без разрушения.
Процессы обработки давлением отличаются высокой производительностью. Так, при прокатке скорость выпуска готовой продукции составляет до 20-30 м/с, при горячей объемной штамповке за одну минуту на штамповочном молоте или прессе изготавливают 2—3 поковки, при холодной листовой штамповке на одном прессе-автомате в одну минуту изготовляют до 1500 мелких деталей.
Основные виды обработки металлов давлением
Процессы обработки металлов давлением включают прокатку, волочение, прессование, объемную ковку и листовую штамповку.
Прокатка — процесс, при котором заготовка под действием сил трения втягивается в зазор между вращающимися валками и пластически деформируется ими (рис. 14).
Волочение — процесс протягивания катанного или прессованного прутка (или трубы) через постепенно сужающееся отверстие в инструменте, называемом волочильной матрицей.
Прессование — процесс выдавливания металла из замкнутой полости контейнера через матрицу, площадь отверстия которой меньше площади поперечного сечения исходной заготовки.
Ковка — процесс горячей обработки металлов давлением при помощи бойков или универсального подкладного инструмента. При ковке металл заготовки пластически деформируется, постепенно приобретая заданную форму, размеры и свойства.
Объемная штамповка — придание заготовке заданной формы и размеров путем принудительного заполнения материалом рабочей полости штампа. В отличие от ковки пластическое течение при штамповке ограничивается стенками матрицы.
Различают горячую и холодную объемную листовую штамповку.
Вовлечение
Обработка металла волочением, т. е. протягивание прутка через отверстие, выходные размеры которого меньше, чем исходное сечение прутка, находит широкое применение в металлургической, кабельной и машиностроительной промышленности. Волочением получают проволоку с минимальным диаметром 0,002 мм, прутки диаметром до 100 мм, причем не только круглого сечения, трубы, главным образом небольшого диаметра с тонкой стенкой.
В результате волочения поперечное сечение заготовки уменьшается, а длина увеличивается.
Волочением обрабатывают стали разнообразного химического состава, а также практически все цветные металлы и их сплавы.
Волочение выгодно отличается от механической обработки металла резанием, так как при этом отсутствуют отходы металла в виде стружки, а сам процесс производительнее и менее трудоемок.
Технологический процесс волочения состоит из трех основных стадий: подготовка металла (очистка от окалины, нанесение смазки, заделка концов), волочение по определенному режиму и отделка (удаление дефектов, правка, резка на мерные длины, маркировка, консервационная смазка и пр.).
Ковка и штамповка металла
Ковкой и штамповкой изготовляют металлические изделия — поковки, из которых затем получают детали, идущие на сборку машин, приборов, агрегатов и т. д. В ряде случаев штамповкой получают непосредственно готовые детали.
Поковки отличаются от детали припуском — определенным слоем металла поковки, снимаемом при последующей механической обработке,
Ковку и штамповку применяют почти во всех отраслях промышленности и особенно в машиностроении. Процессы штамповки имеют также важное значение при производстве неметаллических изделий.
38. Обработка металлов резанием
Резание металлов – это обработка металлов снятием стружки для придания изделию заданной формы, размеров и обеспечения определенного технологического качества поверхности. Резание металлов осуществляется на металлорежущих станках или вручную с помощью металлорежущего инструмента.
На машиностроительных заводах до 40–60 % деталей машин получают в результате обработки заготовок на металлорежущих станках.
В процессе обработки исходная заготовка и режущий инструмент получают рабочее движение от механизмов металлорежущих станков и перемещаются относительно друг друга. Для осуществления обработки резанием необходимо сочетание двух видов движения: главного движения резания и движения подачи.
Наиболее распространенными видами обработки металлов резанием явл-ся: точение, сверление, фрезерование, строгание, шлифование.
Обработку металлов резанием производят на металлорежущих станках при помощи режущего инструмента – однолезвийного (резцы) и многолезвийного с двумя и более режущими кромками (сверла, зенкеры, развертки и др.). Инструменты, изготовленные из абразивных материалов (например, шлифовальные круги), обеспечивают высокую точность обработки и относятся к многолезвийным, так как они имеют множество острых режущих кромок.
Точение (токарная обработка) – обработка наружных и внутренних поверхностей тел вращения резанием – характеризуется вращательным движением заготовки и поступательным движением режущего инструмента – резца. Разновидности точения: обтачивание, растачивание, подрезание, разрезание. При точении заготовке сообщается главное движение резания, а инструменту – движение подачи.
Сверление – широко распространенный метод получения отверстий резанием. Главное движение при сверлении – вращательное, а движение подачи – поступательное. Оба движения при сверлении отверстий на сверлильных станках сообщаются инструменту – сверлу. При сверлении отверстие получается небольшой точности, с шероховатой поверхностью, поэтому предварительно просверленные отверстия обрабатывают зенкером (зенкерование) и разверткой (развертывание).
Фрезерование – процесс обработки изделий многолезвийным режущим инструментом – фрезой. По сравнению с процессом точения, при фрезеровании в работе одновременно участвует несколько лезвий, поэтому фрезерование является более производительным способом обработки, чем точение. Каждый зуб фрезы работает периодически, а корпус – ее большей частью.
Строгание – предназначенодля обработки длинных плоских поверхностей. Оно выполняется при прямолинейном возвратно-поступательном движении резца или заготовки – это движение является главным. После каждого двойного хода заготовка или резец перемещаются в поперечном направлении, совершая тем самым движение поперечной подачи.
Шлифование – процесс обработки заготовок резанием при помощи шлифовального круга-инструмента, имеющего форму тела вращения и состоящего из абразивных зерен и связующего их материала. При вращении круга наиболее выступающие из связки зерна, контактируя с заготовкой, снимают с ее поверхности тонкие стружки. Большинство из них, сгорая, образуют пучок искр. Обработка шлифованием в большинстве случаев является чистовой и отделочной операцией, обеспечивающей высокое качество обработанной поверхности и точность обработки. В некоторых случаях шлифование применяется для предварительной обработки заготовок, обдирки при снятии слоя до 6 мм.
39. Технология получения разъемных и не разъемных соединений
Разъёмные соединения.
При сборке изделий применяют разъемные соединения. Они допускают разборку без повреждения сопрягаемых деталей. К ним относятся: резьбовые, клиновые, штифтовые, шлицевые, шпоночные и профильные соединения, а также соединения с помощью упругих элементов.
Резьбовые соединения весьма распространены в машиностроении. Их выполняет, применяя крепежные детали (болты, винты, шурупы, гайки, резьбовые шпильки); иногда резьбу выполняют непосредственно на самой детали. Болтовое и винтовое соединение, особенного часто применяется при массовом и крупносерийном пр-ве, т.к. возможно эффективно использовать современные ср-ва механизации и автоматизации.
Штифтовые соединения применяют для точной фиксации сопрягаемых деталей между собой, а иногда и для передачи сдвигающих сил перпендикулярно их оси. Шпоночные и шлицевые соединения используют для передачи крутящего момента. Шлицевые соединения целесообразно применять в массовом пр-ве, они более надежны и с их помощью можно передавать большие крутящие моменты. Профильные соединения имеют преимущества по сравнению со шпиночным: они имеют хорошее центрирование деталей, не имеют острых углов и резких переходов сечения, что желательно при термообработке
Дата добавления: 2018-10-26; просмотров: 315; Мы поможем в написании вашей работы! |
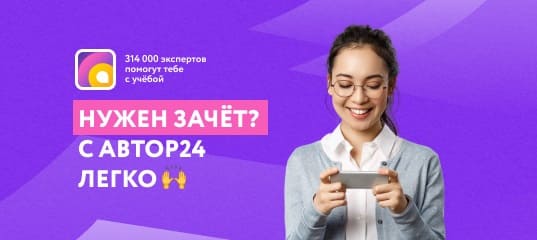
Мы поможем в написании ваших работ!