Требования к монтажу, ремонту и реконструкции (модернизации) оборудования
106. Монтаж, ремонт и реконструкция (модернизация) оборудования под давлением с применением сварки и термической обработки должны быть проведены по технологии и рабочим чертежам, разработанным до начала производства работ специализированной организацией, выполняющей соответствующие работы.
Все положения принятой технологии должны быть отражены в технологической документации, регламентирующей содержание и порядок выполнения всех технологических и контрольных операций.
107. При монтаже, ремонте и реконструкции (модернизации) с применением сварки и термической обработки должна быть применена установленная распорядительными документами специализированной организации система контроля качества (входной, операционный, приемочный), обеспечивающая выполнение работ в соответствии с настоящими ФНП и технологической документацией.
108. Текущий профилактический ремонт и техническое обслуживание оборудования, не требующие применения сварки и термической обработки, выполняют работники (ремонтный персонал) эксплуатирующей или специализированной организации. Порядок выполнения, объем и периодичность выполнения работ определяют утвержденные в эксплуатирующей организации производственные и технологические инструкции, разработанные с учетом требований руководств (инструкций) по эксплуатации и фактического состояния оборудования.
|
|
Резка и деформирование полуфабрикатов
109. Резка листов, труб и других полуфабрикатов, а также вырезка отверстий могут быть произведены любым способом (механическим, газопламенным, электродуговым, плазменным). Конкретный способ и технологию резки устанавливает технологическая документация в зависимости от классов сталей (характеристик материала).
110. Применяемая технология термической резки материалов, чувствительных к местному нагреву и охлаждению, должна исключать образование трещин на кромках и ухудшение свойств металла в зоне термического влияния. В необходимых случаях, предусмотренных технологической документацией, следует предусматривать предварительный подогрев и последующую механическую обработку кромок для удаления слоя металла с ухудшенными в процессе резки свойствами.
111. Гибку труб допускается производить любым освоенным специализированной организацией способом, обеспечивающим получение качества гиба, соответствующего требованиям технологической документации.
112. Для обеспечения сопряжения поперечных стыков труб допускается расточка, раздача или обжатие концов труб. Значения расточки, деформация раздачи или обжатия принимаются в пределах, установленных технологической документацией.
|
|
113. Холодный натяг трубопроводов, если он предусмотрен проектом, может быть произведен лишь после выполнения всех сварных соединений, за исключением замыкающего, окончательного закрепления неподвижных опор на концах участка, подлежащего холодному натягу, а также после термической обработки (при необходимости ее проведения) и контроля качества сварных соединений, расположенных по всей длине участка, на котором необходимо произвести холодный натяг.
Сварка
114. При выполнении сварочных работ следует руководствоваться Федеральными нормами и правилами в области промышленной безопасности "Требования к производству сварочных работ на опасных производственных объектах" , утвержденными приказом Федеральной службы по экологическому, технологическому и атомному надзору от 14 марта 2014 г. N 102 (зарегистрировано Министерством юстиции Российской Федерации 16 мая 2014 г., регистрационный N 32308).
(Пункт в редакции, введенной в действие с 26 июня 2018 года приказом Ростехнадзора от 12 декабря 2017 года N 539 . - См. предыдущую редакцию )
115. Пункт утратил силу с 26 июня 2018 года - приказ Ростехнадзора от 12 декабря 2017 года N 539 . - См. предыдущую редакцию .
|
|
116. Пункт утратил силу с 26 июня 2018 года - приказ Ростехнадзора от 12 декабря 2017 года N 539 . - См. предыдущую редакцию .
117. Пункт утратил силу с 26 июня 2018 года - приказ Ростехнадзора от 12 декабря 2017 года N 539 . - См. предыдущую редакцию .
118. Пункт утратил силу с 26 июня 2018 года - приказ Ростехнадзора от 12 декабря 2017 года N 539 . - См. предыдущую редакцию .
119. Перед началом сварки должно быть проверено качество сборки соединяемых элементов, а также состояние стыкуемых кромок и прилегающих к ним поверхностей. При сборке не допускается подгонка кромок ударным способом или местным нагревом.
120. Подготовка кромок и поверхностей под сварку должна быть выполнена механической обработкой либо путем термической резки или строжки (кислородной, воздушно-дуговой, плазменно-дуговой) с последующей механической обработкой (резцом, фрезой, абразивным инструментом). Глубина механической обработки после термической резки (строжки) должна быть указана в технологической документации в зависимости от восприимчивости конкретной марки стали к термическому циклу резки (строжки).
121. При сборке стыковых соединений труб с односторонней разделкой кромок и свариваемых без подкладных колец и подварки корня шва смещение (несовпадение) внутренних кромок не должно превышать значений, установленных в технологической документации.
|
|
122. Кромки деталей, подлежащих сварке, и прилегающие к ним участки должны быть очищены от окалины, краски, масла и других загрязнений в соответствии с требованиями технологической документации.
123. Приварка и удаление вспомогательных элементов (сборочных устройств, временных креплений) должны быть произведены в соответствии с указаниями чертежей и технологической документации по технологии, исключающей образование трещин и закалочных зон в металле оборудования под давлением. Приварку этих элементов должен выполнять сварщик, допущенный к проведению сварочных работ на данном оборудовании под давлением.
124. Прихватка собранных под сварку элементов должна быть выполнена с использованием тех же сварочных материалов, которые будут применены (или допускаются к применению) для сварки данного соединения.
Прихватки при дальнейшем проведении сварочных работ удаляют или переплавляют основным швом.
125. Пункт утратил силу с 26 июня 2018 года - приказ Ростехнадзора от 12 декабря 2017 года N 539 . - См. предыдущую редакцию .
126. Пункт утратил силу с 26 июня 2018 года - приказ Ростехнадзора от 12 декабря 2017 года N 539 . - См. предыдущую редакцию .
127. Пункт утратил силу с 26 июня 2018 года - приказ Ростехнадзора от 12 декабря 2017 года N 539 . - См. предыдущую редакцию .
128. Пункт утратил силу с 26 июня 2018 года - приказ Ростехнадзора от 12 декабря 2017 года N 539 . - См. предыдущую редакцию .
129. Пункт утратил силу с 26 июня 2018 года - приказ Ростехнадзора от 12 декабря 2017 года N 539 . - См. предыдущую редакцию .
130. Сварочные материалы должны быть проконтролированы:
а) на наличие соответствующей сопроводительной документации;
б) каждая партия электродов - на сварочно-технологические свойства, а также на соответствие содержания легирующих элементов нормированному составу путем стилоскопирования (или другим спектральным методом, обеспечивающим подтверждение наличия в металле легирующих элементов) наплавленного металла, выполненного легированными электродами;
в) каждая партия порошковой проволоки - на сварочно-технологические свойства;
г) каждая бухта (моток, катушка) легированной сварочной проволоки - на наличие основных легирующих элементов путем стилоскопирования или другим спектральным методом, обеспечивающим подтверждение наличия в металле легирующих элементов;
д) каждая партия проволоки с каждой партией флюса, которые будут использованы совместно для автоматической сварки под флюсом, - на механические свойства металла шва.
131. Технология сварки при монтаже, ремонте, реконструкции (модернизации) оборудования под давлением допускается к применению при условии подтверждения ее технологичности на реальных изделиях, проверки всего комплекса требуемых свойств сварных соединений и освоения эффективных методов контроля их качества. Применяемая технология сварки должна быть аттестована в соответствии с установленными требованиями.
(Пункт в редакции, введенной в действие с 26 июня 2018 года приказом Ростехнадзора от 12 декабря 2017 года N 539 . - См. предыдущую редакцию )
132. Аттестацию технологии сварки подразделяют на исследовательскую и производственную.
Исследовательскую аттестацию проводят при подготовке к внедрению новой, ранее не регламентированной нормативными документами технологии сварки.
Производственную аттестацию технологии сварки осуществляют до начала ее применения в рамках проверки готовности организаций к выполнению сварочных работ в условиях конкретного производства с учетом требований нормативных документов.
(Пункт в редакции, введенной в действие с 26 июня 2018 года приказом Ростехнадзора от 12 декабря 2017 года N 539 . - См. предыдущую редакцию )
133. Исследовательскую аттестацию технологии сварки проводят в целях определения характеристик сварных соединений, необходимых для расчетов при проектировании и выдаче технологических рекомендаций (область применения технологии, сварочные материалы, режимы подогрева, сварки и термической обработки, гарантируемые показатели приемосдаточных характеристик сварного соединения, методы контроля).
Характеристики сварных соединений, определяемые при исследовательской аттестации, выбирают в зависимости от вида и назначения основного металла и следующих условий эксплуатации сварных соединений:
а) механические свойства при нормальной (20±10°С) и рабочей температуре, в том числе временное сопротивление разрыву, предел текучести, относительное удлинение и относительное сужение металла шва, ударная вязкость металла шва и зоны термического влияния сварки, временное сопротивление разрыву и угол изгиба сварного соединения;
б) длительная прочность, пластичность и ползучесть;
в) циклическая прочность;
г) критическая температура хрупкости металла шва и зоны термического влияния сварки;
д) стабильность свойств сварных соединений после термического старения при рабочей температуре;
е) интенсивность окисления в рабочей среде;
ж) отсутствие недопустимых дефектов;
з) стойкость против межкристаллитной коррозии (для сварных соединений элементов из сталей аустенитного класса);
и) характеристики, специфические для выполняемых сварных соединений, устанавливаемые организацией, проводящей их исследовательскую аттестацию.
По результатам исследовательской аттестации организацией, проводившей ее, должны быть выданы рекомендации, необходимые для ее практического применения.
134. Производственная аттестация технологии сварки должна осуществляться с целью подтверждения того, что организация, занимающаяся монтажом, ремонтом, реконструкцией (модернизацией) оборудования под давлением, обладает техническими, организационными возможностями и квалифицированными кадрами для производства сварки по аттестуемым технологиям, а также проверки того, что сварные соединения (наплавки), выполненные в условиях конкретного производства по аттестуемой технологии, обеспечивают соответствие требованиям настоящих ФНП, нормативных документов и технологической документации по сварке.
После получения положительных результатов проверки наличия технических, кадровых и организационных возможностей организации необходимо выполнить сварку контрольных сварных соединений с применением конкретной технологии в условиях производства, на котором осуществляются сварочные работы в процессе строительства, монтажа ремонта, изготовления объекта, либо на организованной на время строительства, монтажа, ремонта или на постоянной основе промышленной базе для выполнения работ, включающих сборку и сварку производственных сварных соединений.
(Пункт в редакции, введенной в действие с 26 июня 2018 года приказом Ростехнадзора от 12 декабря 2017 года N 539 . - См. предыдущую редакцию )
135. Производственную аттестацию проводит аттестационная комиссия, созданная в специализированной организации в соответствии с программой, разработанной этой организацией и утвержденной председателем комиссии.
Программа должна предусматривать проведение неразрушающего и разрушающего контроля сварных соединений, оценку качества сварки по результатам контроля и оформление итогового документа по результатам производственной аттестации.
Порядок проведения производственной аттестации определяет технологическая документация.
Если при производственной аттестации технологии сварки получены неудовлетворительные результаты по какому-либо виду испытаний, аттестационная комиссия должна принять меры по выяснению причин несоответствия полученных результатов установленным требованиям и решить, следует ли провести повторные испытания или данная технология не может быть использована для сварки производственных соединений и нуждается в доработке.
136. В случае ухудшения свойств или качества сварных соединений по отношению к уровню, установленному производственной аттестацией, организация должна приостановить применение технологии сварки, установить и устранить причины, вызвавшие их ухудшение, и провести повторную производственную аттестацию, а при необходимости - и исследовательскую аттестацию.
(Пункт в редакции, введенной в действие с 26 июня 2018 года приказом Ростехнадзора от 12 декабря 2017 года N 539 . - См. предыдущую редакцию )
137. При монтаже, ремонте, реконструкции (модернизации) оборудования под давлением применяются аттестованные технологии сварки, предусмотренные проектно-конструкторской, технической и технологической документацией и обеспечивающие качество выполнения работ с учетом примененных в конструкции оборудования материалов.
(Абзац в редакции, введенной в действие с 26 июня 2018 года приказом Ростехнадзора от 12 декабря 2017 года N 539 . - См. предыдущую редакцию )
Не допускается применение газовой сварки для деталей из аустенитных сталей и высокохромистых сталей мартенситного и мартенситно-ферритного класса.
138. Сварка элементов, работающих под избыточным давлением, как правило, должна проводиться при положительной температуре окружающего воздуха. Допускается выполнять сварку в условиях отрицательной температуры при соблюдении требований технологической документации и создании необходимых условий для защиты места сварки и сварщика от воздействий ветра и атмосферных осадков. При отрицательной температуре окружающего воздуха металл в районе сварного соединения перед сваркой должен быть просушен и прогрет с доведением температуры до положительного значения.
139. Необходимость и режим предварительного и сопутствующих подогревов свариваемых деталей определяются технологией сварки и должны быть указаны в технологической документации. При отрицательной температуре окружающего воздуха подогрев производят в тех же случаях, что и при положительной, при этом температура подогрева должна быть выше на 50°С.
140. После сварки шов и прилегающие участки должны быть очищены от шлака, брызг металла и других загрязнений.
Внутренний грат в стыках труб, выполненных контактной сваркой, должен быть удален для обеспечения заданного проходного сечения.
141. Термическая обработка элементов оборудования при монтаже, ремонте, реконструкции (модернизации) проводится в случаях, установленных технологической документацией с учетом рекомендаций изготовителя, указанных в руководстве (инструкции) по эксплуатации.
Дата добавления: 2018-09-23; просмотров: 327; Мы поможем в написании вашей работы! |
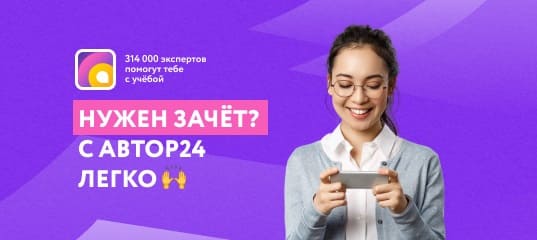
Мы поможем в написании ваших работ!