Изменения микроструктуры материалов после их длительного отжига в среде аргона и воздуха
Предпосылкой ко всем металлографическим исследованиям является получение гладкой и блестящей поверхности, которая заключается в шлифовке и полировке образца. Для удобства обработки поверхности образцы фиксировались в металлической обойме. Приготовленные таким образом образцы механически шлифовали и полировали на шлифовальном станке. Окончательная механическая полировка проводится алмазной пастой с размером абразивных частиц до 1 мкм.
Для удаления наклепа и получения гладкой поверхности шлифы были подвергнут электролитическому полированию. Полировку проводили в электролите состоящем из 4 частей уксусной кислоты, 1 части хлорной кислоты, при напряжение 12,5 В и плотности тока 0,3 А/см2. Время полировки составила около 40 с. Материал катода нержавеющая сталь.
Выявление микроструктуры проводили методом электролитического травления в растворе 1 части хромового ангидрида в 5 части дистиллированной воды. При напряжение 6 В плотность тока составила 0,1 А/см2. Время травления 5 минут. Материал катода нержавеющая сталь
Результаты металлографических исследований облученных образцов чехла ТВС показывают, что после отжига микроструктура образцов характеризуется полосами скольжения на которых наблюдаются выделения вторичных фаз. На рисунке ‑ 9 представлена микроструктура торцевой поверхности образца вырезанного из грани чехла отработавшей ТВС ЦЦ‑19 реактора БН‑350 с отметки «-275 мм» от ЦАЗ (испытания при температуре 550 °С в среде аргон).
|
|
Рисунок ‑ 9 – Микроструктура облученного образца стали 12Х18Н10Т после длительного отжига при 550 ˚С в течение 2600 часов.
Из рисунка видно, что структура образца однородна, имеет полиэдральное строение аустенита. В теле зерна облученного образца имеется большое количество мелких дисперсных карбидов.
|
Для определения временного интервала интенсивного старения был проведен кратковременный отжиг облученного образца чехла ТВС из отметки +165 мм от ЦАЗ в течение одного часа при температуре 450 °С.
Микроструктура образца с отметки «+160», выявленная методами металлографии, характеризуется отчетливо видимыми полосами скольжения, на которых в отдельных местах наблюдаются выделения карбидных частиц (вероятно, М23С6) размером 2-3 мкм (Рисунок ‑ 10а).
![]() | ![]() |
Рисунок ‑ 10 - Микроструктура стали 12Х18Н10Т: а – после облучения нейтронами при 370 °С до 53,4 сна; б – после облучения и отжига при температуре 450 °С, 1 ч. |
В металлографической структуре стали после отжига выявилось множество полос скольжения, декорированных карбидными частицами. Отдельные выделения наблюдали также на границах зерен (рисунок ‑ 10 б). Образование большого числа обособленных карбидных фаз приводит к уменьшению микротвердости и изменению плотности материала
|
|
Наряду с тем были проведены исследования изменения микроструктуры двух необлученных образцов стали 12Х18Н10Т, после коррозионных испытаний при температурах 550 ˚С и 600 ˚С. Эти исследования проводились с использованием растрового электронного микроскопа JSM‑6390LV. Предельный вакуум в камере электронной пушки составлял 1 мПа, при уровне вакуума в камере образцов 27 Па. Юстировка электронной пушки, контрастность и яркость изображения, фокусировка и астигматизм устанавливались автоматически. Изображения получали в режиме отраженных электронов. Поверхность образца сканировалась первичным электронным пучком при рабочем расстоянии 10 мм и ускоряющем напряжении 30 кВ.
Исследовали торцевую поверхность образцов, то есть изучали различие микроструктуры по толщине стенки чехла ТВС. С этой целью были приготовлены шлифы методом механической полировки. На рисунок ‑ 11 показана микроструктура образца после коррозионных испытаний при температуре 550 ˚С в среде аргона в течение 7000 ч. снятая в отраженных электронах с контрастом по элементному составу. На изображении можно видеть темные включения правильной формы, размером ~ 6 мкм. Следует обратить внимание, что крупные образования вторичных фаз наблюдались, в основном, в середине стенки, тогда как по внешним ее краям преобладали более мелкие включения. По‑видимому, это обстоятельство связано с особенностями изготовления шестигранной трубы.
|
|
Рисунок ‑ 11– Поверхность образца стали 12Х18Н10Т в режиме фазового контраста.
На основании анализа электронного изображения можно предположить, что выделения вторичных фаз состоят из легких элементов, скорее всего титана и азота. Об этом свидетельствуют данные локального химического анализа образца стали 12Х18Н10Т представленного в Таблица 2.
Таблица 2. Результаты локального химического анализа поверхности
стали 12Х18Н10Т после длительного отжига.
C, % | N, % | Ti, % | Cr, % | Fe, % | Ni, % | |
Спектр 1 | 2,69 | 0 | 0 | 18,16 | 69,60 | 9,55 |
Спектр 2 | 2.88 | 21.55 | 73.45 | 0.77 | 1.35 | 0 |
3.2 Изменение плотности высоко облученных образцов стали 12Х18Н10Т в результате долговременных отжигов.
Предполагалось, что долговременное термическое воздействие при отсутствии нейтронных потоков приведет к эволюции сформировавшейся под облучением структуры. Распад твердого раствора либо эволюция карбидной компоненты могут повлечь за собой изменение плотности и, как следствие, изменение линейных размеров объекта с возникновением дополнительных механических напряжений. В Таблице 3 ‑ приведены данные по плотности облученной стали, полученные методом гидростатического взвешивания.
|
|
Таблица 3 ‑ Плотность образцов стали 12Х18Н10Т, облученной в реакторе БН‑350 и подвергнутых долговременному отжигу.
Образец | Параметры облучения | Параметры отжига | Плотность, г/см3. | |||
Отметка | Доза, сна | Темп-ра облучения | Темп-ра отжига, °С | Длитель-ность, часы | ||
Облучение без отжига | -160 | 55 | 305 | – | – | 7,87±0,01 |
3.1 | -275 | 50 | 310 | 300 | 2600 | 7,39±0,01 |
3.3 | -275 | 50 | 310 | 300 | 7200 | 7,38±0,01 |
2.1 | -275 | 50 | 310 | 550 | 2600 | 7,44±0,01 |
Действительно, как следует из Таблица 3, долговременный отжиг при 300 °С привел к уменьшению плотности материала по сравнению со значением для облученного материала до отжига. Отметим, что плотность значительно изменилась уже после 2600 часов выдержки и ее значение практически не менялось с ростом времени отжига. То есть, можно ожидать, что после первоначального изменения плотности материала (и соответственно – геометрии объекта), его геометрическая стабильность будет достаточно высокой в течение последующего долговременного хранения.
Отжиг при 550 °С в течение 2600 часов привел к несколько большим значениям плотности (7.44), что тем не менее ниже этой величины для исходной стали (7.86). Поскольку плотность облученного материала даже после долговременного отжига при 550 °С остается ниже, чем у исходной стали, при более высоких температурах, сопоставимых с температурой рекристаллизации, следует ожидать возврата плотности и соответствующего изменения линейных размеров объектов.
3.3 Эволюция микротвердости высокооблученной стали при длительном термическом воздействии.
Результаты, полученные при измерениях микротвердости, сведены в Таблица .
Таблица 4 ‑ Микротвердость высокооблученной стали 12Х18Н10Т до и после долговременного термического воздействия
Образец | Параметры облучения | Параметры отжига | Микротвер дость, кг/см2. | |||
Отметка | Доза, сна | Темп-ра облучения | Темп-ра отжига, °С | Длительность, часы | ||
Необлученная сталь | – | – | – | – | – | 240-260 |
Облучение без отжига | -160 | 55 | 310 | – | – | 365 |
3.1 | -275 | 50 | 310 | 300 | 2600 | 311 |
2.1 | -275 | 50 | 310 | 550 | 2600 | 234 |
Облучение без отжига | +160 | 55 | 370 | – | – | 385 |
3.2 | +175 | 55 | 375 | 300 | 7000 | 385 |
Как следует из Таблица 4, микротвердость стали 12Х18Н10Т в результате облучения до 50 - 55 сна повышается до значений 365-385 кг/мм2 (строки 2, 5) по сравнению с 240 ‑ 260 кг/мм2 для образцов необлученной стали из аналогичного чехла новой тепловыделяющей сборки.
В ходе долговременного отжига при температуре, равной или превосходящей температуру облучения, микротвердость материала снижается тем сильнее, чем выше температура отжига. Это можно объяснить снижением плотности дефектов, которые достаточно подвижны при температуре более 300 °С.
В то же время отжиг при температуре ниже температуры облучения (см. Таблица 4, строки 5, 6) не приводит к существенному изменению микротвердости. Видимо, структура, полученная облучением при 375 °С, достаточно равновесна и устойчива при 300 °С даже в отсутствие нейтронных потоков.
Дата добавления: 2018-09-20; просмотров: 304; Мы поможем в написании вашей работы! |
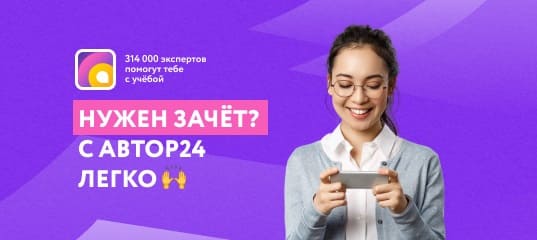
Мы поможем в написании ваших работ!