Неразрушающие методы контроля прочности конструкционных материалов. Классификация неразрушающих методов.
Методы местных разрушений:
Это самые точные из методов неразрушающего контроля прочности, поскольку для них допускается использовать универсальную градуировочную зависимость, в которой изменяются всего два параметра: 1) крупность заполнителя, которую принимают равной 1,0 при крупности менее 50 мм и 1,1 при крупности более 50 мм; 2) тип бетона – тяжелый либо легкий. Метод отрыва со скалыванием и скалывания ребра конструкции заключаются в регистрации усилия, необходимого для скалывания участка бетона на ребре конструкции, либо местного разрушения бетона при вырыве из него анкерного устройства. Метод отрыва со скалыванием является единственным неразрушающим методом контроля прочности, для которого в стандартах прописаны градуировочные зависимости. Метод отрыва стальных дисков заключается в регистрации напряжения, необходимого для местного разрушения бетона при отрыве от него металлического диска, равного усилию отрыва, деленному на площадь проекции поверхности отрыва бетона на плоскость диска. В настоящее время метод используется крайне редко.
Недостатки методов местных разрушений: повышенная трудоемкость; необходимость определения оси арматуры и глубины ее залегания; невозможность использования в густоармированных участках; частично повреждает поверхность конструкции. Методы местных разрушений - самые точные из методов неразрушающего контроля. Приборы, основанные на методах местных разрушений, применяются в основном в монолитном домостроении и при обследовании конструкций зданий и сооружений.
|
|
Методы ударного воздействия на бетон:
Самый распространенный метод контроля прочности бетона из всех неразрушающих - метод ударного импульса. Метод ударного импульса заключается в регистрации энергии удара, возникающей в момент соударения бойка с поверхностью бетона. Приборы, использующие данный метод, отличаются небольшим весом и компактностью, а определение прочности бетона методом ударного импульса является достаточно простой операцией. Результаты измерений выдаются в единицах измерения прочности на сжатие. После соответствующей настройки данные приборы можно использовать для работы с различными строительными материалами. Также с их помощью можно определять класс бетона, производить измерение прочности под различными углами к поверхности объекта, переносить накопленные данные на компьютер.
Метод упругого отскока заключается в измерении величины обратного отскока ударника при соударении с поверхностью бетона. Типичным представителем приборов для испытаний по этому методу является склерометр Шмидта и его многочисленные аналоги. Метод упругого отскока, каки метод пластической деформации, основан на измерении поверхностной твердости бетона.
|
|
Метод пластической деформации основан на измерении размеров отпечатка, который остался на поверхности бетона после соударения с ней стального шарика. Метод устаревший, но до сих пор его используют из-за дешевизны оборудования. Наиболее широко для таких испытаний используют молоток Кашкарова. Принцип действия - в молоток вставляется металлический стержень определенной прочности, после чего прибором наносят удар по поверхности бетона. С помощью углового масштаба измеряют размеры отпечатков, получившихся на бетоне и стержне. Прочность бетона определяется из соотношения размеров отпечатков (прочность стержня известна).
Ультразвуковой метод:
Ультразвуковой метод заключается в регистрации скорости прохождения ультразвуковых волн. По технике проведения испытаний можно выделить сквозное ультразвуковых прозвучивание, когда датчики располагают с разных сторон тестируемого образца, и поверхностное прозвучивание, когда датчики расположены с одной стороны. Метод сквозного ультразвукового прозвучивания позволяет, в отличие от всех остальных методов неразрушающего контроля прочности, контролировать прочность не только в приповерхностных слоях бетона, но и прочность тела бетона конструкции. Ультразвуковые приборы могут использоваться не только для контроля прочности бетона, но и для дефектоскопии, контроля качества бетонирования, определения глубины. Недостатки: нельзя ультразвуковые приборы использовать для контроля качества высокопрочных бетонов.
|
|
Оценка прочности металла
Выбор характеристик для оценки конструкционной прочности металла в пластической области зависит от характера нагружения и вида нарушения прочности данной конструкции. Нарушение прочности может происходить как вследствие наступления чрезмерной пластической деформации (текучесть, ползучесть), так и в следствие разрушения (статическое путем отрыва или среза, усталостное, статическое длительное или замедленное), а также особые случаи – потеря устойчивости и износ.Одним из существенных признаков правильно выбранного критерия оценки конструкционной прочности металла при лабораторных испытаниях является сходство изломов, полученных при испытаниях и в условиях эксплуатации.
|
|
Наибольшее применение в строительной практике для оценки прочности металла имеетприбор Польди ударного действия.Наконечником прибора является шарик 2 диаметром 10 мм из твердой закаленной стали, дающий при ударе отпечаток одновременно на исследуемом металле 1 и на стальном эталонном бруске 3, твердость которого должна быть заранее определена. Для получения отпечатков ударяют молотком по верхнему торцу стержня 4.
Рис. 1. Схема прибора Польди:
1 - исследуемый материал;
2-стальной шарик;
3- эталонный брусок;
4- ударный стержень;
5- обойма прибор
Определение прочности и марки металла производятся с помощью соответствующих таблиц. Для термически обработанных легированных сталей вводится поправочный коэффициент.
С помощью прибора Польди можно получать, однако, лишь ориентировочные характеристики. Но и с учетом этого применение прибора практически полезно, в особенности в следующих случаях:
· для ускоренной проверки однородности материала в различных элементах освидетельствуемых конструкций;
· при отбраковке (проверке марок металла) поступающих заготовок.
Известен способ определения прочности металла, определяемого методом царапания, заключающийся в том, что на поверхности металла элемента наносится царапина при постоянной силе давления от индентора, автономно измеряется ширина царапины микроскопом и твердость находится по формуле, а по твердости определяется предел прочности материала.
Недостатком этого способа является низкая точность результатов измерений ширины царапины из-за влияния навалов на границах царапания, необходимость непосредственного контакта микроскопа с металлом в конструкции, что не всегда возможно, например, в углах конструкций; отсутствие автоматического регистрирования всей ширины царапины, а лишь точечное (дискретное) ее измерение на длине царапины; влияние на значение ширины царапины в местах измерения возможного наличия более твердых частиц металла.
Дата добавления: 2018-08-06; просмотров: 651; Мы поможем в написании вашей работы! |
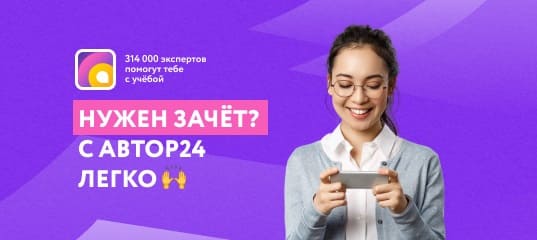
Мы поможем в написании ваших работ!