Характеристика технологической схемы производства листового полированного стекла
Листовое стекло является базовым продуктом стекольной промышленности. Это бесцветное, прозрачное натрий-кальций-силикатное стекло, изготавливаемое флоатспособом без какой-либо дополнительной обработки поверхностей.
Современные технологии и оборудование позволяют получать из листового стекла множество видов стекла с различными свойствами, например:
- теплосберегающее (низкоэмиссионное) стекло, применение которого в остеклении зданий позволяет сократить потребление теплоэнергии на 30-50%;
- закаленное стекло (сталинит), имеющее в пять раз большую, чем обычное стекло, прочность, в т.ч. термическую. При разрушении закаленного стекла образуются мелкие осколки с тупыми краями, что позволяет значительно сократить риск травмирования людей;
- многослойное стекло (в том числе строительный и автомобильный триплекс), при разбивании которого осколки не разлетаются, а остаются скрепленными вместе полимерной композицией, т.е. безосколочное стекло;
- зеркальное полотно - стекло, способное отражать окружающие предметы и визуально увеличивать пространство;
- тонированное стекло, ограничивающее пропускание солнечного света и ультрафиолетового излучения, и многие другие виды стекла и его произ-водные.
Выпускаемое ОАО «Гомельстекло» листовое стекло успешно реализуется на территории Республики Беларусь и в десятках стран мира. Самый крупный потребитель - Центральная Европа. На экспорт ежемесячно уходит 70% изготав-ливаемого стекла. Товар задерживается на складе не более 2÷3 часов.
|
|
Ассортимент выпускаемого листового полированного стекла - разнообразнейший: от 2,5 до 19 миллиметров по толщине.
В настоящее время объемы производства листового стекла на существующей технологической линии составляют:
- суточный - 800 т/сутки;
- годовой - 273 750 т/год.
В конце 50-х годов английской фирмой «Пилкингтон бразерс Лимитед» был разработан способ получения полированного стекла методом формования лен-ты стекла на расплаве олова, получивший название флоат-процесса.
Принцип формования заключается в том, что строго дозируется количество стекломассы из выработанной части стекловаренной печи по сливному лотку сте-кает на зеркальную поверхность расплавленного олова и, растекаясь по нему, превращается в ленту равновесной толщины. Сформированная лента стекла далее продвигается по поверхности олова, постепенно охлаждается и передается в печь отжига.
В ванну расплава подается защитная атмосфера, состоящая из азота водорода, предупреждающая окисление олова. Полученная лента стекла раскра-ивается на заданные форматы и упаковывается в тару. Часть стекла направляется на промышленную переработку.
|
|
1 Характеристика и расход исходных материалов
Исходным сырьем для производства листового стекла являются стеклянный бой и шихта в соотношении:
- стеклянный бой −24%;
- шихта−76%.
Шихта −это смесь сырьевых материалов для стекловарения.
Сырьевые материалы для стекловарения условно делятся на основные и вспомогательные.
В состав главного сырья входят основные и кислотные оксиды (основа стекол).
Вспомогательные сырьевые материалы представляют собой вещества, которые вводятся в его состав для изменения характеристик стекла или ускорения стекловарения (красители, восстановители, окислители, ускорители, глушители).
К основным сырьевым материалам в производстве листового стекла относятся:
- песок - SiO2;
- полевой шпат – Na2О*К2О*А12О3*6SiO2;
- кальцинированная сода - Nа2СО3;
- доломит - СаСО3*МgСО3;
- мел - СаСОз.
К вспомогательным сырьевым материалам в производстве листового стекла относятся:
- сульфат натрия - Nа2SО4 (осветлитель);
- уголь - С (сильнейший восстановитель).
Расчеты расхода шихты и исходных сырьевых материалов для выполнения запланированной суточной и годовой программы по производству листового стекла выполнены в соответствии с технологическими нормами и приведены в таблицах 1-2.
|
|
Требования, предъявляемые к шихте: шихта, загружаемая в ванную стек-ловаренную печь, должна быть однородна, не комковаться, т. е. соотношение мате-риалов в каждом участке шихты должно быть одинаковым и строго соответство-вать заданному рецепту.
На однородность стекольной шихты влияет гранулометрический состав сырьевых материалов, их химический состав, влажность, качество и продолжи-тельность перемешивания в смесителе, а также способ транспортирования.
Нарушение однородности шихты приводит к изменению условий варки, фо-рмования, плохому отжигу, повышенной хрупкости, пониженной термостойкости и прочности стекла.
Влажность шихты допускается (4,5±0,5) %. Увлажняют шихту подачей воды непосредственно в смеситель с помощью форсунок после того, как отвес предва-рительно перемешан всухую. Определенное количество влаги препятствует рас-слоению и пылению шихты. Кроме того, увлажненная шихта обладает повы-шенной теплопроводностью и реакционной способностью, быстрее прогре-вается и переходит в расплав, чем сухая шихта.
Температура увлажненной шихты должна быть не ниже 40 °C.Температура сырьевых материалов на весах при дозировании должна быть не более:
|
|
- песок кварцевый - 90°С;
- полевой шпат - 40 ºС
Контроль температуры шихты и песка кварцевого производит ПЛ.
При транспортировании отвешенных компонентов от весовых дозаторов к смесителю должны полностью исключаться потери материалов.
Для предупреждения расслаивания готовой шихты при ее транспортиро-вании от смесителей до бункеров загрузчиков ванной печи, а также при хранении шихты нельзя допускать резких сотрясений и падения с большой высоты.
Требования предъявляемые к стекольному бою: химический состав об-ратного стеклобоя должен соответствовать составу вырабатываемого стекла.
Обратный бой должен быть тщательно отсортирован. Все посторонние при-меси, куски боя с оловом, огнеупорным камнем выбрасываются в отвал.
Количество вводимого в стекловаренную печь обратного боя должно быть (15-30)% и устанавливается главным технологом.
Таблица1.
Заданный химический состав стекла
Наименование оксидов | Содержание оксидов, % | Отклонения, ±% | Примечание |
SiO2 | 72,7 | 0,3 | в т.ч. Fe2O3 до 0,13% |
R2O7 | 1,2 | 0,2 | |
CaO | 8,6 | 0,2 | |
MgO | 3,6 | 0,2 | |
Na2O | 13,4 | 0,2 | |
SO3 | не более 0,5 |
Таблица 2. Расчет годовой потребности в шихте для производства листового стекла
с учетом введения обратного боя в количестве 24%.
№ п/п
| Наименование материала
| Расход материала, с учетом производственных потерь | ||||||
на 1 тонну листового стекла, кг/т
| суточный расход, т/сутки | годовой расход, т/год | ||||||
сущ. технол. линия 800 т/сутки | проект. технол. линия 780 т/сутки | на две линии 1580 т/сутки | сущ. технол. линия 273750 т/год | проект, технол. линия 255500 т/год | на две линии 529250 т/год | |||
1 | Песок | 504,36 | 403,488 | 393,401 | 796,889 | 138068,55 | 128863,98 | 266932,53 |
2 | Полевой шпат | 66,96 | 53,568 | 52,229 | 105,797 | 18330,3 | 17108,28 | 35438,58 |
3 | Доломит | 140,73 | 112,584 | 109,769 | 222,353 | 38524,838 | 35956,515 | 74481,353 |
4 | Мел | 38,86 | 31,088 | 30,311 | 61,399 | 10637,925 | 9928,73 | 20566,655 |
5 | Сульфат натрия | 11,99 | 9,592 | 9,352 | 18,944 | 3282,263 | 3063,445 | 6345,708 |
6 | Сода кальцинированная | 165,45 | 132,36 | 129,051 | 261,411 | 45291,938 | 42272,475 | 87564,413 |
7 | Уголь | 0,7 | 0,56 | 0,546 | 1,106 | 191,625 | 178,85 | 370,475 |
Всего: | 929,050 | 743,240 | 724,659 | 1467,899 | 254327,439 | 237372,275 | 491699,714 |
Таблица 3.Расчет годовой потребности в сырьевых материалах для производства листового стекла
№ п/п
| Наименование материала
| Расход материала, с учетом производственных потерь | ||||||
на 1 тонну листового стекла, кг/т
| суточный расход, т/сутки | годовой расход, т/год | ||||||
сущ. технол. линия 800 т/сутки | проект. техн.. линия 780 т/сутки | на две линии 1580 т/сутки | сущ. тех- нол. линия 273750 т/год | проект. технол. линия 255500 т/год | на две линии 529250 т/год | |||
1 | Песок | 592,98 | 474,384 | 462,524 | 936,908 | 162328,275 | 151506,39 | 313834,665 |
2 | Полевой шпат | 67,31 | 53,848 | 52,502 | 106,35 | 18426,113 | 17197,705 | 35623,818 |
3 | Доломит | 156,84 | 125,472 | 122,335 | 247,807 | 42934,95 | 40072,62 | 83007,57 |
4 | Мел | 46,75 | 37,4 | 36,465 | 73,865 | 12797,813 | 11944,625 | 24742,438 |
5 | Сульфат натрия | 12,11 | 9,688 | 9,446 | 19,134 | 3315,113 | 3094,105 | 6409,218 |
6 | Сода кальцинирован. | 166,29 | 133,032 | 129,706 | 262,738 | 45521,888 | 42487,095 | 88008,983 |
7 | Уголь | 0,78 | 0,624 | 0,608 | 1,232 | 213,525 | 199,29 | 412,815 |
8 | Стеклобой | 240 | 192 | 187,2 | 379,2 | 65700 | 61320 | 127020 |
Всего: | 1283,060 | 1026,448 | 1000,786 | 2027,234 | 351237,677 | 327821,830 | 679059,507 |
Описание технологического процесса
В настоящее время основными производственными участками, задействованными в производстве листового стекла, являются:
- открытый склад песка;
- составной цех с силосными складами соды и доломита;
- цех производства полированного стекла способом термического формования;
- открытый склад готовой продукции.
Составной цех предназначен для получения шихты, являющейся полуфабрикатом для варки листового стекла (подробнее составной цех будет рассмотрен ниже).
В составе составного цеха предусмотрены следующие производственные участки:
- закрытый склад сырьевых материалов;
- силосный склад соды;
- силосный склад доломита;
- отделение обработки;
- дозировочно-смесительное отделение.
Открытый склад песка является промежуточным складом для приема и хранения песка. Доставка песка на склад осуществляется железнодорожным транспортом. Площадь склада − 8000 м2 . С открытого склада песок транспортными средствами перевозится в закрытый склад составного цеха и загружается в отсеки на хранение.
Доставка всех сырьевых материалов осуществляется железнодорожным транспортом:
Хранение сырьевых материалов предусмотрено:
- доломита и соды - в силосных банках;
- сульфата натрия, угля, полевого шпата - в отдельных отсеках закрытого склада составного цеха;
- мел хранится затаренным в бумажных мешках.
Обработка сырья для приготовления шихты в настоящее время осуществляется по следующей схеме:
- песок - сушка, просев;
- сода- просев;
- полевой шпат - сушка, просев;
- мел - дробление, просев;
- сульфат натрия - просев;
- доломит - дробление, помол, просев;
- уголь - помол, просев.
В качестве технологического оборудования для обработки исходного сырья используются сушильные барабаны, работающие на природном газе, вибросита, сито-бураты, элеваторы, дробилки.
Хранение обработанного сырья предусмотрено в отдельных расходных бункерах.
Производство шихты в составном цехе осуществляется на дозировочно-смесительной линии, которая состоит из автоматических весовых дозаторов, сборного конвейера и двух смесителей.
Обработанные компоненты шихты из расходных бункеров взвешиваются на весах-дозаторах и по транспортерной ленте подаются в смесители, где тщательно перемешиваются.
Далее подготовленная шихта по ленточному транспортеру из составного цеха поступает в цех производства полированного стекла способом термического формования и подается в бункер над загрузчиком шихты в печь ЛТФ. Сюда же по другому транспортеру подается стеклянный бой, компоненты перемешиваются.
Загрузка сырья из бункера в загрузочные карманы стекловаренной печи, осуществляется посредством механических толкателей.
В качестве топлива в существующей стекловаренной печи используется природный газ.
Процесс варки стекла постепенно продвигается в центр печи и температура расплава повышается до 1560°С. При варке стекла происходит химическая реакция между компонентами шихты: разложение солей, образование двойного карбоната, силикатов натрия и кальция, сернистого натрия и т.д.
Сваренная стекломасса поступает в ванну расплава на жидкий слой олова, в которую, для предотвращения окисления металла, подается газообразные азот и водород. В ванне расплава формуется лента стекла. К ванне примыкает шлаковая камера. Для защиты нижней поверхности стеклоленты от налипания олова, для упрочнения ленты стекла, повышения его химической стойкости в шлаковую камеру вводится сернистый ангидрид.
Полированное стекло на ленточных транспортерах нарезается в размер, упаковывается и отправляется на склад готовой продукции, расположенный на открытой территории предприятия, в непосредственной близости от здания цеха.
Таким образом производство листового полированного стекла можно представить в виде схем:
Технологическая схема производства
![]() |
Загрузка шихты и стеклобоя в ванную стекловаренную печь |
![]() |
![]() ![]() |
Отжиг
![]() |
Программная резка ленты стекла
![]() |
Резка стекла на резных столах |
Технологическая схема производства с расстановкой технологического оборудования
Бункер готовой шихты | |||
![]() | |||
| |||
![]() | ![]() | ![]() | Система равномерного распределения шихты и стеклобоя над бункерами загрузчиков |
![]() | |||
Загрузчики стольного типа | |||
![]() | |||
![]() | |||
![]() | |||
Печь отжига | |||
![]() |
| ![]() | |
Аварийная резка стекла | |||
![]() | |||
![]() | |||
![]() |
| ||
Программная резка стекла | |||
![]() | |||
Продольная резка стекла | |||
![]() | |||
Отломка листов стекла | |||
![]() |
| ![]() | |
![]() | |||
![]() |
| ||
![]() |
| ||
![]() | Бункера стеклобоя у резных столов | Раскрой и разломка листов стекла на резных столах | |
![]() | |||
![]() |
| ||
Упаковка стекла | |||
![]() |
| ![]() | |
Склад стекла |
Выбросы загрязняющих веществ в атмосферный воздух от источников их выделения, расположенных в цеху полированного стекла представлены в таблице 4.
Таблица 4.
№ источника выбросов* | Источник выделения | Определяемое вещество | ППериодичность контроля | Норматив допустимых выбросов | Лаборатория, осуществляющая контроль | ||
класс опасности | наименование | г/с | мг/м3 при н.у. | ||||
201 | Печь ЛТФ | 2 | Азота диоксид | 1раз в месяц | 67,3977 | 22,94 | Производственная лаборатория предприятия |
3 | Азота оксид | 1раз в месяц | 10,9587 | 373 | |||
3 | Ангидрид сернистый | 1раз в месяц | 15,6008 | 531 | |||
4 | Углерода оксид | 1раз в месяц | 15,6302 | 640 | |||
3 | Пыль неорганич. <70% SiO2 | 1раз в месяц | 5,1121 | 174 | |||
202 | Вытяжка из шлаковой камеры | 3 | Ангидрид сернистый | 2 раза в год | 0,0115 | 8,58 | |
4 | Углерода оксид | 2 раза в год | 0,302 | 22,5 | |||
2 | Азота диоксид | 2 раза в год | 0,0051 | 3,84 | |||
203 | Транспортер боя | 3 | Пыль неорганич. <70% SiO2 | 2 раза в год | 0,0407 | 94,6 | |
204 | Лента загрузки шихты | 2 | Азота диоксид | 2 раза в год | 0,0016 | 2,05 | |
4 | Углерода оксид | 2 раза в год | 0,0615 | 0,003 | |||
3 | Пыль неорганич. <70% SiO2 | 2 раза в год | 0,0362 | 45,3 | |||
205 | Вытяжка от загрузочного кармана | 2 | Азота диоксид | 2 раза в год | 0,0983 | 56,8 | |
3 | Ангидрид сернистый | 2 раза в год | 0,0049 | 2,86 | |||
4 | Углерода оксид | 2 раза в год | 0,0238 | 13,75 | |||
3 | Пыль неорганич. <70% SiO2 | 2 раза в год | 0,21197 | 127 | |||
3 | Азота оксид | 2 раза в год | 0,016 | 9,23 | |||
206 | Вытяжка от загрузочного кармана | 2 | Азота диоксид | 2 раза в год | 0,1939 | 131 | |
3 | Азота оксид | 2 раза в год | 0,0315 | 21,3 | |||
3 | Ангидрид сернистый | 2 раза в год | 0,0042 | 2,86 | |||
4 | Углерода оксид | 2 раза в год | 0,0148 | 10 | |||
3 | Пыль неорганич. <70% SiO2 | 2 раза в год | 0,225 | 153 | |||
335 | Камера дожига | 4 | Углерода оксид | 2 раза в год | 0,006 | 8,75 |
|
Дата добавления: 2018-08-06; просмотров: 801; Мы поможем в написании вашей работы! |
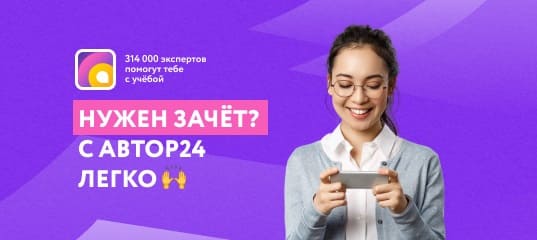
Мы поможем в написании ваших работ!