Процессы расширения и выпуска
Для определения параметров процесса расширения примем показатель политропы расширения
Определим давление :
Определим температуру:
Проверка ранее принятой температуры остаточных газов:
Погрешность составляет:
Таблица 5 - Результаты процесса расширения и выпуска
Параметры | Значения |
Pb | 0,5232 |
Tb | 1723 |
Индикаторные параметры рабочего цикла
Рабочий цикл двигателя внутреннего сгорания характеризуется индикаторными показателями:
Среднее индикаторное давление теоретическое:
Среднее индикаторное давление действительное:
Примем , получим
Определим индикаторный КПД:
где плотность воздуха на впуске двигателя.
Удельный расход топлива
Таблица 6 - Индикаторные параметры рабочего цикла
Параметры | Значения |
Pi’, МПа | 1,476 |
Pi, МПа | 1,4473 |
ηi | 0,4354 |
gi, г/кВт*ч | 188 |
φ | 0,98 |
Эффективные показатели двигателя
Эффективное давление определяется:
,
Где - среднее давление механических потерь. Для инжекторного двигателя составляет
.
Механический КПД:
Эффективный КПД двигателя:
Определим эффективный удельный расход топлива:
Таблица 7 - Эффективные показатели двигателя
Параметры | Значения |
∆P, МПа | 0,0784 |
Pe, МПа | 1,3689 |
ηм | 0,9458 |
ηe | 0,4118 |
ge, г/кВт*ч | 199 |
|
|
Основные параметры цилиндра и двигателя
Литраж двигателя:
Литраж одного цилиндра:
Примем соотношение хода поршня к диаметру и определим диаметр цилиндра.
Округлим до 82мм.
Примем ход поршня.
Определим основные параметры двигателя для полученных значений S и D.
Литраж двигателя:
Номинальная эффективная мощность
Номинальный крутящий момент
Часовой расход топлива
Таблица 8 - Основные параметры цилиндра и двигателя
Параметры | Значения |
D, мм | 82 |
S,мм | 75,6 |
Vл, л | 1,6 |
Ne,кВт | 72,8 |
Me, Н·м | 173,8 |
Gт, кг/ч | 14,5 |
1.3 Посторенние индикаторной диаграммы
Индикаторная диаграмма ДВС строится с использованием данных теплового расчета, в выбранных масштабах. В начале построения на оси абсцисс откладываем отрезок AB, соответствующий рабочему объему цилиндра, а по величине равный ходу поршня в масштабе MS.
Масштабы диаграммы: масштаб хода поршня МS=0,1мм в мм и масштаб давления МР=0,05 МПа в мм.
Величины в приведенном масштабе, соответствующему рабочему объему цилиндра и объему камеры сгорания.
Максимальная высота диаграммы (точка Z)
Ординаты характерных точек:
;
;
;
;
Построение политроп сжатия и расширения производится аналитическим или графическим методом. Построение политроп выполняем аналитическим методом, вычисляя 9 точек для промежуточных объемов, расположенных между Vc и Va и между Vz и Vb по уравнению политропы . Для политропы сжатия
, откуда
|
|
где Pxи Vx – давление и объем в искомой точке процесса сжатия.
Отношение Va/Vx изменяется от 1 до . Для политропы расширения
а) политропа сжатия
Отсюда
где
б) политропа расширения
Отсюда
,
Результаты расчета точек представлены в таблице 9
Таблица 9 - Результаты расчета точек
№ точек | OX, мм | OB/OX | Политропа сжатия | Политропа расширения | ||||
![]() | ![]() | ![]() | ![]() | ![]() | ![]() | |||
1 2 3 4 5 6 7 8 | 7,6 17,6 28,2 39,2 50,2 61,2 72,6 83,2 | 10,94 4,72 2,95 2,12 1,65 1,35 1,14 1 | 26,8 8,44 4,42 2,81 1,99 1,5 1,2 1 | 20,8 9 5,6 4 3 2,6 2 1,912 | 1,04 0,45 0,28 0,2 0,15 0,13 0,1 0,0956 | 19,8 6,9 3,8 2,5 1,86 1,45 1,17 1 | 207 72 39,6 26 19,4 15 12,2 10,5 | 10,35 3,6 1,98 1,3 0,97 0,75 0,61 0,5232 |
Действительная или скругленная индикаторная диаграмма отличатся от расчетной за счет опережения зажигания или впрыска (т. с´), повышение давления в конце сжатия (т. c˝). Кроме того на рабочий процесс оказывает влияние период открытия и закрытия клапанов газораспределения (т. a´ a˝ b´ и r´).Для определения местоположения точек c´, b´, r´, a´ и a˝ следует задаться фазами газораспределения и углом опережения зажигания (впрыска), а также соотношение радиуса кривошипа R к длине шатуна Lш. значение данного соотношения. Примем .
|
|
В соответствии с принятыми фазами газораспределением и углом опережения зажигания (впрыска) определяют положение точек r´, a´, a˝, c´ и b´ по формуле:
Результаты расчетов приводим в таблице 10
Таблица 10 - Результаты расчета точек
Обозначение точек | Положение точек | φ° | ![]() | Расстояние точек от ВМТ (AX) мм. |
r´ | 25° до ВМТ | 25 | 0,1226 | 4,7 |
a´ | 30° после ВМТ | 30 | 0,1690 | 6,5 |
a˝ | 70° после НМТ | 110 | 1,4656 | 56,4 |
c´ | 40° до ВМТ | 40 | 0,2918 | 11,12 |
b´ | 60° до ВМТ | 120 | 1,6050 | 61,8 |
ʄ | 33 ![]() | 33 | 0,0584 | 2,25 |
Положение точки с"определяется из выражения
Тепловой баланс
Тепло, выделяющееся при сгорании топлива в цилиндрах двигателя, не может быть полностью преобразовано в полезную механическую работу. В реальном двигателе потери тепла возрастают из-за трения, теплообмена, неполноты сгорания и других причин. В связи с эти эффективный КПД цикла имеет меньшее значение по сравнению с термическим КПД, который всегда остается меньше единицы вследствие передачи части тепла холодному источнику.
|
|
Распределение тепловой энергии топлива, сгорающего в двигателе, наглядно иллюстрируется составляющими внешнего теплового баланса, которые определяются при установившемся тепловом состоянии двигателя в процессе его испытаний. Приближенно составляющие теплового баланса можно найти аналитически по данным теплового расчета двигателя.
Тепловой баланс позволяет определить тепло, превращенное в полезную эффективную работу, т.е. установить степень достигнутого совершенства теплоиспользования и наметить пути уменьшения имевшихся потерь. Знание отдельных составляющих теплового баланса позволяет судить о теплонапряженности деталей двигателя, рассчитать схему охлаждения, выяснить возможность использования теплоты отработавших газов и т.д.
Тепловой баланс двигателя характеризует распределение тепловой энергии сгоревшего топлива. Приближенно, составляющие теплового баланса можно определить аналитически по данным теплового расчета двигателя.
Уравнение теплового баланса:
Qo= Qe+ Qг + Qв + Qн.с.+ Qост.
где Qo – теплота, введенная в цилиндры двигателя с топливом при режиме номинальной нагрузки:
Qe – теплота, превращенная в полезную (эффективную) работу
Qг – теплота, потерянная с отработавшими газами,
где ,
– молярные теплоемкости продуктов сгорания и свежего заряда, кДж/(кмоль·град.),
tг , to – температура отработавших газов и свежего заряда, для расчета примем:
кДж/(кмоль·град),
кДж/(кмоль·град);
Qв – теплота, передаваемая охлаждающей среде:
, Дж/с ,
где – коэффициент пропорциональности для 4-х тактных двигателей,
– эмпирический коэффициент, примем m=0,6
– число цилиндров,
Qост – неучтенные потери теплоты:
Представим тепловой баланс в относительных единицах.
Знание абсолютных значений составляющих теплового баланса позволяет осуществить количественную оценку распределения теплоты в двигателе.
Величины отдельных составляющих теплового баланса двигателя не являются постоянными, а изменяются в процессе его работы в зависимости от нагрузки, быстроходности и других факторов.
Характер распределения теплоты, подводимой в цилиндр с топливом, в процессе превращения в полезную эффективную работу наглядно может быть представлен в виде кривых теплового баланса. Графические зависимости строятся на основании определения каждой составляющей в зависимости от частоты вращения, нагрузки, качества смеси и т.д.
Тепловой баланс
1.5 Выбор турбокомпрессора для двигателя ВАЗ 21126
В моей дипломной работе приведен пример расчета турбокомпрессора с целью выбора прототипа турбокомпрессора, для подачи воздуха в цилиндры двигателя внутреннего сгорания под избыточным давлением.
Таблица 11 – Исходные данные для расчёта турбокомпрессора низкой ступени
Параметр | Обозначение | Величина | Размерность |
Мощность | ![]() | ![]() | ![]() |
Частота вращения | ![]() | ![]() | ![]() |
Литраж | ![]() | ![]() | ![]() |
Удельный расход топлива | ![]() | ![]() | ![]() |
Коэффициент избытка воздуха | ![]() | ![]() | – |
Коэффициент наполнения | ![]() | ![]() | – |
Коэффициент продувки | ![]() | ![]() | – |
Сопротивление воздухоочистителя | ![]() | ![]() | ![]() |
Сопротивление на выпуске | ![]() | ![]() | ![]() |
Температура отработавших газов | ![]() | ![]() | ![]() |
Давление окружающей среды | ![]() | ![]() | ![]() |
Температура окружающей среды | ![]() | ![]() | ![]() |
По исходным данным определяем секундный расход воздуха
где – количество воздуха, необходимого для сгорания 1 кг топлива. Для расчёта принимаем
.
Секундный расход газов через турбину
Плотность воздуха на выходе из воздухоочистителя
где – универсальная газовая постоянная для воздуха.
Плотность воздуха на входе в двигатель
Давление воздуха на выходе из компрессора. Для системы наддува без промежуточного охлаждения наддувочного воздуха:
где – показатель политропы сжатия в компрессоре,
Степень повышения давления в компрессоре
Зная, все исходные данные мы теперь можем, подбирая давление наддува видеть, как меняется мощность.
Берем давление наддува 0,5-0,7 бар
Бар
Преобразуем формулу Рк / Ро так, чтобы мы могли найти Рк:
Находим путем преобразования формулы:
Рк= (0,15 – 0,18)Ре
Подставляя это значение Ре в формулу мы можем найти мощность при наддуве в 0,7 Бар:
Умножив, полученные киловатты на 1,36 мы получим мощность в лошадиных силах:
По результатам расчёта с использованием данных по полям расхода базовых моделей турбокомпрессоров, выбираем типоразмер турбокомпрессора. Выбранный типоразмер определяет диаметр колеса компрессора и турбины
. В нашем случае это ТКР 7Н-1.
1.6 Построение внешней скоростной характеристики двигателя
Внешняя скоростная характеристика позволяет провести анализ и дать оценку мощностных, экономических и эксплуатационных показателей при работе двигателя с полной нагрузкой.
При построение внешней скоростной характеристики двигателя используют результаты испытаний двигателя на специальных стендах, а на стадии проектирования двигателя можно использовать результаты теплового расчета.
В дипломном проекте внешнюю скоростную характеристику двигателя строим по результатам теплового расчета и выбора турбокомпрессора для режима номинальной нагрузки с использованием эмпирических зависимостей.
Построение кривых скоростей характеристики ведется в интервале от 1000 до 6300мин-1
Расчетные точки кривой эффективной мощности определяются по следующим эмпирическим зависимостям через каждые 1000 мин-1:
Где, Ne и nN – номинальная эффективная мощность (кВт) и частота вращения коленчатого вала (мин-1) при этой мощности
Nex и nx – эффективная мощность (кВт) и частота вращения коленчатого вала (мин-1) в искомой точке на кривой скоростной характеристики двигателя.
Для рассмотрения произведём расчёт только для одной точки х=1( ), а результаты расчёта для других точек занесём в табл.11.
Мощность в расчётных точках, кВт:
По рассчитанным точкам в масштабе MN строится кривая эффективной мощности.
Точки кривой эффективного крутящего момента (Н·м) определяются по формуле:
Расчетные точки кривой удельного эффективного расхода топлива qe , г/(кВт·ч) определяются:
- для бензиновых двигателей:
где qeN – удельный эффективный расход топлива при номинальной мощности принимается из теплового расчета, г/(кВт·ч).
Часовой расход топлива для расчетных точек, кг/ч:
;
Значение параметров скоростной характеристики рассчитываем по приведенным выше формулам и заносим в таблицу 12.
Таблица 12 - Значения параметров скоростной характеристики
Частота вращения коленчатого вала, мин-1 | Параметры внешней скоростной характеристики | |||
Nex, кВт | Mex, Н·м | qex , г/(кВт·ч) | GT, кг/ч | |
1000 | 11,61 | 110,87 | 214,124 | 2,48 |
2000 | 24,87 | 118,75 | 194,8 | 4,84 |
3000 | 38,73 | 123,3 | 183,3 | 7,1 |
4000 | 51,65 | 123,31 | 177,1 | 9,14 |
5000 | 62,54 | 119,45 | 181,1 | 11,32 |
5600 | 67,37 | 115 | 181,5 | 12,2 |
6000 | 69,7 | 110,9 | 183,1 | 12,76 |
7000 | 72,6 | 99 | 199 | 14,45 |
2 Организационно - технологическая часть
2.1 Выбор типа производства
Тип производства – это классификация категории производства, выделяемая по признакам широты номенклатуры, регулярности, стабильности и объема выпуска изделия.
Различают три типа производства: единичное, серийное, массовое.
Тип производства можно выбрать по заданной годовой программе и массе собираемой детали, с помощью таблице №13.
Таблица 13 - Типы производства
Тип производства | Количество выпускаемых деталей в зависимости от их веса. | ||
До 30кг | 30…500кг | Свыше 500кг | |
Единичное Серийное Массовое | До 100 шт 100…50000 шт Свыше 50000 шт | До 10 шт 10…5000шт Свыше 5000 шт | До 5 шт 5…1000 шт Свыше 1000 шт |
На основании таблице и задания выбираем серийное производство с программой выпуска деталей 1000 шт с весом до 500 кг.
При серийном производстве выпуск готовой продукции происходит по сериям, которые повторяются через определенный промежуток времени.
После выбора серийного типа производства рассчитывают такт выпуска изделия.
tВ= , шт/мин (87)
где FД- действительный годовой фонд времени
FД=QР FC
Кn, час (88)
где QР- количество рабочих дней
FC- продолжительность смены, FC=8 (час)
S- количество смен, S=1
Кn- коэффициент невыходов, Кn=0,89.
FД=267 =234,96 час
N- программа выпуска, N=1000 шт.
tВ= =14,1 шт/мин.
Зная такт выпуска, определяют коэффициент загрузки:
КЗ= (89)
где Тшт.ср. – среднее штучное время по типовому или базовому варианту технологического процесса.
Тшт.ср.=2,8 мин/взят с базового варианта технологического процесса.
КЗ= =5,03.
2.2 Выбор формы и метода сборки
В зависимости от конструкции, размеров и массы собираемого объекта производства, а также трудоемкости, масштаба, выпуска и степени расчлененности изделия различают две организационные формы сборки: стационарная и подвижная.
Стационарная сборка характеризуется тем, что весь процесс сборки выполняется на одном неподвижном рабочем месте, к которому подводится все детали и узлы. Эта форма сборки может выполняться по принципу концентрации и дифференциации операций технологического процесса сборки.
При концентрационном методе сборка изделий производится от начала до конца одной бригадой. Этот метод сборки применяется в единичном и мелкосерийном производстве. При этой форме сборки требуется большая площадь, высокая квалификация сборщиков, большие затраты, отсутствует специализация рабочих и цикл сборки больше. Поэтому эта форма сборки в современном машиностроение не применяется.
При дифференциальном процессе сборки стационарная сборка может быть поточной. Здесь технологический процесс сборки разделяется на операции и рабочие передают узел с одного рабочего места на другое, после выполнения своей операции с соблюдением определенного режима. Эта форма сборки применяется в серийном производстве.
Поточно-подвижная сборка более совершенная форма сборки и осуществляется при перемещении собираемого объекта по рабочим местам. Она применяется в серийном и массовом производстве. Подвижная сборка может осуществляться в свободном или принудительном перемещении собираемого объекта. При свободном перемещении собираемый объект перемещается вручную от одной операции к другой в тележках и т.п. сборка с принудительным перемещением изделия осуществляется непосредственно на конвейере, на котором неподвижно закрепляется стенд сборки собираемого изделия. В этом случае процесс сборки проектируется таким образом, чтобы длительность всех операций была равной или кратной. Это необходимо для непрерывности процесса сборки и для равномерной загрузки сборщиков.
Методы сборки в зависимости от требуемой точности сборочных соединений разделяются на пять методов:
- сборка методом полной взаимозаменяемости;
- сборка с подбором деталей (неполной взаимозаменяемостью);
- сборка с сортировкой деталей по группам (групповая взаимозаменяемость);
- сборка с применением компенсаторов (регулируемая);
- сборка с индивидуальной пригонкой.
На основании годового выпуска и типа производства принимаю стационарную форму сборки с дифференциальным процессом сборки, а вследствие того, что установка турбокомпрессора требует особой точности для обеспечения создания необходимого давления в системе выбираю метод сборки с индивидуальной пригонкой.
2.3 Разработка технологической схемы сборки
Построение процессов общей и узловой сборки наглядно представлено при помощи технологической схемы. Эта схема отражает структуру и последовательность комплектования изделий и узлов. Технологические схемы упрощают проектирование процессов сборки, вносят определенную стройность в их выполнение, позволяют оценить конструкцию изделия с технологической точки зрения дают хорошую наглядность сборки. Составление технологической схемы сборки общей и узловой на одно и тоже изделие возможно в нескольких вариантах, отличающихся как по структуре, так и по последовательности комплектования сборочных элементов. Выбор варианта производится с учетом производительности, рентабельности и удобства выполнения процессов сборки.
Рисунок 3 - Технологическая схема сборки клапана
2.4 Маршрутная технология сборки
Автотракторная техника - сложные много детальные изделия и для рационального построения технологического процесса их сборки необходимо, прежде всего, тщательно изучить конструкцию изделия и его частей.
Для выполнения данных задач, увеличение производительности сборочных работ и обеспечения должного качества сборки следует предусматривать целесообразную механизацию сборочных работ за счет применения механизированного инструмента.
Таблица 14 – Маршрутная карта на технологический процесс сборки
№ операции | № перехода | Наименование и содержание операции | Оборудование | Приспособление | Инструмент |
1 | 2 | 3 | 4 | 5 | 6 |
1 | 000 | Транспортировка на сборочный участок | Авто кар | Тара | |
2 | 005 | Установить и подсоединить интеркулер | Вручную | Пневмотрещетка | |
3 | 010 | Установить на выпускной коллектор турбокомпрессор. Убедиться, что прокладка правильно прижата. | Вручную | Ключ с трещеткой | |
4 | 015 | Установить маслосливную трубку | Вручную | Ключ | |
5 | 020 | Заполнить турбокомпрессор чистым маслом через маслоподводящее отверстие, медленно проворачивая вал рукой | Вручную | масленка | |
6 | 025 | Установить маслоподводящую трубку | Вручную | Ключ | |
7 | 030 | Установить воздушный фильтр | Вручную | ||
8 | 035 | Установить и подсоединить воздушные патрубки. Убедиться в плотности прилегания и затяжки | Вручную | Трещетка | |
9 | 040 | Установить и подсоединить выпускной патрубок. Убедиться в плотности прилегания и затяжки | Вручную | Трещетка | |
10 | 045 | Провернуть двигатель, не заводя его, чтобы создать давление в турбокомпрессоре и масляной системе в целом | Вручную | ||
11 | 050 | Завести двигатель на холостых оборотах (на 5/10 мин) и прогреть до рабочей температуры, постепенно увеличивая нагрузку | Вручную | ||
12 | 055 | Проверить отсутствие подтекания масла, утечек воздуха и горячих газов, нехарактерных шумов. (Для обнаружения утечек воздуха и газов используйте мыльный раствор) | Вручную | Мыльный раствор | |
13 | 060 | Совершить пробную поездку с постепенным увеличением нагрузки | Вручную | ||
14 | 065 | Еще раз проверить отсутствие подтекания масла, утечек воздуха и горячих газов, нехарактерных шумов | Вручную |
2.5 Расчёт технической нормы времени на сборку
Определение штучного времени на выполнение одной операции сборки узла
Тшт=Топ+Тобс+Тот ,мин (90)
где Топ-оперативное время
Топ=Тосн+Твсп , мин (91)
Топ=3,7 мин
Тосн- основное время;
Твсп- вспомогательное время;
Тобс- время на обслуживание рабочего места.
Тобс= Топ 2,5% , мин (92)
Тобс=3,7 2,5%=0,0925 мин.
Тот- время на отдых
Тот= 4%Топ ,мин (93)
Тот=4% 3,7=0,04
3,7=0,148(мин)
Тшт=3,7+0,0925+0,148=3,94(мин)
Общее время на сборку всего узла
Тшт.общ= шт, мин (94)
где m- количество операций
Тшт.общ= шт=55,2 мин.
Общая годовая трудоемкость узла
Тобщ= Тшт.общN , мин (95)
где N- программа выпуска, N=1000шт.
Тобщ=Тшт.общN=55,2 1000=55200 мин=920 ч.
Определение норм выработки
Нвб= , мин (96)
где Тсм- продолжительность смены, Тсм=480 мин.
Нвб= =8,7
2.6 Определение количество рабочих мест
Обработка технологического процесса сборки сборочной единицы сопровождается соответствующими расчетами, количества оборудования, рабочих сил их производительности, количества рабочих мест (сборочных стендов, постов) производится по формуле:
n= , мест (97)
где R – такт поточной линии (равен 12,29 мин/шт).
n= =4,49 мест. = 5 мест.
При получении дробного количества рабочих мест (стендов), принимается ближайшее целое количество рабочих мест с округлением в большую сторону.
Таким образом, принимаю 5 рабочих мест.
Коэффициент загрузки при серийном производстве равен
𝖞з= 100% (98)
Коэффициент загрузки не должен превышать 105%
𝖞з= 100=50%
Часовая производительность стендов
Р= , узла/ч (99)
Р= =11 узла/ч.
Количество рабочих сборщиков для стационарной сборки определяется по формуле:
А1= , чел (100)
где Тк- штучное калькуляционное время на общую сборку сборочной единицы в часах.
Fq- действительный годовой фонд времени, Fq=3574,24 ч.
А1= =3,9 чел.
Принимаю количество рабочих мест равное 4.
2.7 Определение площади участка
Расположение рабочих мест для различных видов работ сборочного цеха должно соответствовать последовательности прохождения деталей по стадиям сборки. Такое расположение дает возможность достигнуть наименьшего пути движения деталей и получить постоянное общее направление грузопотоков.
Размер устройств и оборудования для сборки зависят от размеров собираемых деталей, узлов и машин. В случае необходимости движения транспорта по проходу ширина его принимается в зависимости от принимаемого транспорта.
Площадь участка рассчитывается по следующей формуле:
Sуч=АВ , м2 (1)
где А- ширина участка, принимаю А=12 м2.
В- длина участка, принимаю В=14 м2.
Sуч=12 14=168 м2.
По полученной общей производственной площади участка рассчитывается удельная площадь ,то есть площадь приходящееся на одного производственного рабочего.
Sуд= ,м2/чел. (102)
где - число работающих.
Sуд= =42 м2/чел.
В состав вспомогательных отделений входят участки технического контроля, кладовая инструментальные и приспособлений, склады готовых деталей и узлов, склад попутных изделий.
Транспортирование изделий с одной операции на другую или на склад можно осуществлять различными способами:
По транспортному конвейеру – для транспортирования деталей и узлов, предназначенных для сборки изделий, а также готовой продукции на испытательные станции или на окраску.
Сборочные стенды – предназначены для машин и крупных узлов, их конструкция зависит от формы, веса и размеров изделия, а также от организации производства.
Ленточные конвейеры – применяют при сборке мелких узлов и деталей.
Сборочные тележки – применяются при поточной сборки, на них часто закрепляются собираемые изделия.
Рольганги-собираемые узлы или детали либо опираются на роликовую поверхность рольгангов непосредственно, либо устанавливаются на деревянные или металлические поддоны соответствующей формы.
Часто механизация сборочных процессов осуществляется на многих предприятиях машиностроения, является базой для решения задач по повышения производительности труда сборки.
Для увеличения выпуска изделий необходимо повысит производительность и ускорить выполнение работ на всех или большинстве операций процесса сборки. Это можно осуществить только на основании комплексной механизации. Комплексная механизация-эта главное направление в совершенствовании технологии сборки.
Решение проблемы завершения комплексной механизации является базой для перехода на новую, высококачественную ступень механизации-автоматическую сборку с широким внедрением в технологический процесс машин автоматов, выполняемые сборочные операции без непосредственного участия рабочих.
В данном проекте применена поточная сборка, сборка ведется на сборочных стендах. Транспортировка деталей и узлов на складские помещения и на контроль ведется на транспортном конвейере. Для механизации сборочных процессов при сборке возможны применения различных приспособлений такие, как: электро- пневмо- гайковерты, специальные пресс машины.
2.8 Охрана труда и техника безопасности на сборочном участке
С настоящей инструкцией должны быть ознакомлены:
-руководящий линейный производственный персонал (мастера, начальники участков и т.д.) цехов, в которых выполняются слесарно-сборочные работы;
-рабочие (слесари-сборщики), выполняющие слесарно-сборочные работы или если в технологическом процессе (операции) на выполняемые ими работы дача ссылка на настоящую инструкцию.
Общие положения.
Слесарю-сборщику необходимо твердо знать правило техники безопасности применительно к своим обязанностям по работе, знать особенности безопасного труда на всех рабочих местах, на которых ему по роду выполнения своих обязанностей приходится работать, четко знать технологический процесс сборки на выполняемых операциях и неукоснительно выполнять его требование о порядке и методах работы и применяемом оборудовании, технологической оснастке, приемах и средствах безопасного ведения работал. В связи с этим слесарь-сборщик обязан:
В соответствии с установленным на заводе порядком получать инструктаж по технике безопасности.
Изучить требования и положения инструкций по технике безопасности, указанных в технологическом процессе, соблюдать все требования и положения, требовать ознакомления с ними.
Заботиться о выполнении правил безопасного труда на закрепленных рабочих местах, требовать соблюдения правил техники безопасности в своей бригаде, на своем участке.
Пользоваться предохранительными приспособлениями и инструментом, предназначенными для обеспечения безопасности труда согласно технологическим процессам, инструкциям по технике безопасности, приказам и распоряжениям.
Своевременно производить уборку и очистку своего рабочего места, не допускать его захламленности и загромождения, наличия на полу масла, деталей, неисправности полового покрытия и т.д. Следить за состоянием рабочего места, которое должно полностью соответствовать находящейся на участке карте чистоты и порядка, требованиям технологического процесса. Помнить, что высокая культура производства является одним из важнейшим условий безопасности труда.
Обращаться к администрации (мастер, бригадир и т.д.) за разъяснением, если что-нибудь непонятно.
Выполнять только ту работу, которая поручена администрацией (мастер, начальник участка и т.п.)
Быть внимательным и аккуратным во время работы. Не отвлекаться самому и не отвлекать других посторонними разговорами и действиями.
Пользоваться только установленными переходами и проходами при передвижении (переходе) обращать внимание на предупредительные таблички, указатели, сигналы.
Не перелезать через рольганги, детали, узлы, и т.п. не перебегать путь перед близко идущим транспортом. Повышенное внимание близко работающему транспорту, уступать место идущему транспорту своевременно отходить в сторону.
При выявлении нарушений настоящей инструкции правил техники безопасности немедленно заявить об этом мастеру общественному инспектору по охране труда, инженеру по технике безопасности. Нарушение безопасности со стороны слесаря-сборщика в каждого завода рассматривается как нарушение производственной дисциплины и правил внутреннего распорядка с соответствующими выводами.
Знать, где находиться первичные средства пожаротушения, сигнальные устройства для оповещения о загорании, уметь пользоваться ими в случае загораний.
Не работать и не находиться под транспортируем грузом.
Детали, поступающие на сборку, узлы складировать предусмотренным техпроцессом или картой чистоты и порядком методом, укладывать устойчиво, следить, чтобы стопки деталей не разваливались.
Не сдувать с деталей стружку и металлическую пыль ртом, не применять сжатый воздух вне специально предусмотренных обдувочных камер, не использовать сжатый воздух не по назначению.
При совместной работе согласовывать свои действии с товарищами по работе.
Строго соблюдать производственную дисциплину.
Соблюдать правило личной гигиены:
Не мыть руки в масле, эмульсии, топливе и т.п., не вытирать их ветошью, салфетками, загрязненными стружкой.
Не принимать пищи на рабочем месте, грязными руками.
Изучить и запомнить правило оказания первой помощи при поражении электротоком.
При использовании на рабочем месте пневмоинструмента, соблюдать правило техники безопасности согласно инструкции.
За невыполнением требований инструкции по технике безопасности виновные привлекаются к ответственности согласно действующему законодательству.
3 Экономическая часть
3.1 Расчет экономического эффекта проекта
Расчёт фонда заработной платы основных рабочих
Основные рабочие оплачиваются по сдельной форме. Расценки (R) рассчитываются на каждую операцию по формуле:
![]() ![]() | (9) |
где Тст – тарифная ставка, руб./час;
Тшт – норма времени на обработку продукции на операцию, мин.
Расчёт расценок сводится в таблицу 4.
Таблица 15 – Расчёт сдельных расценок по операциям
Наименование операции | Разряд | Тст | Тшт | Сдельная расценка |
Сборочная | 6 | 169 | 55,2 | 155,5 |
Основная заработная плата рабочих рассчитывается по формуле:
![]() ![]() ![]() | (10) |
где Кр – (районный) коэффициент (15%);
Кпр – премиальный коэффициент (45%).
Дополнительная заработная плата принимается в размере 10% от основной заработной платы по формуле:
![]() ![]() | (11) |
Отчисления на социальные нужды принимаются в размере 30% от суммы основной и дополнительной заработных плат, так как в 2018 году страховые взносы необходимо уплачивать по следующим тарифам и определяется по формуле:
- Пенсионный Фонд России (ПФР) – 22 %,
- Фонд обязательного медицинского страхования (ФОМС) – 5,1 %,
- Фонд социального страхования (ФСС) – 2,9%.
![]() ![]() | (12) |
Годовой фонд заработной платы рассчитывается как сумма фондов основной и дополнительной заработных плат.
Средняя заработная плата рассчитывается по всем рабочим вместе по формуле:
![]() ![]() | (14) |
где ЗПг.о. – годовой фонд заработной платы основных рабочих;
Расчёт заработной платы сводится в таблицу 5.
Таблица 16 – Сводная ведомость заработной платы рабочих участка.
Категория рабочих | Основная заработная плата | Дополнительная заработная плата | Отчисления на социальные нужды | Итого |
Основные рабочие | 1037185 | 103718,5 | 342271,1 | 1483174,6 |
Расчёт трудовых затрат
Трудовые затраты в калькуляции складываются из основной заработной платы, дополнительной заработной платы и отчислений на социальные нужды.
Чтобы получить эти данные на одно изделие необходимо разделить соответствующие числа на величину годового выпуска деталей.
Расчёт стоимости накладных расходов
Накладные расходы на уровне цеха складываются из расходов на содержание и эксплуатацию оборудования (РСЭО) и общепроизводственных (цеховых) расходов.
РСЭО определяются как 130% от основной заработной платы основных рабочих.
Для того, чтобы рассчитать амортизационные отчисления, необходимо знать первоначальную стоимость оборудования. Эти данные возьмём из таблицы 17. Средняя норма амортизации оборудования – 15%.
Таблица 17 – Первоначальная стоимость оборудования
Наименование и модель инструмента | Количество инструмента | Цена инструмента, руб. | Балансовая цена станков |
Универсальный набор Licota | 4 | 21000 | 84000 |
Гайковерт Licota | 4 | 7800 | 31200 |
Динамометрический ключ | 4 | 2300 | 9200 |
Итого | 11 | - | 124400 |
![]() ![]() |
где ОПФпер – первоначальная стоимость основных производственных фондов, руб.;
НА – средняя норма амортизации оборудования в год – 15%.
Общепроизводственные расходы принимаются в размере 120% от основной заработной платы основных производственных рабочих.
Внепроизводственные расходы принимаются 40% от производственной себестоимости.
Все расчёты сводятся в таблицу 18.
Таблица 18 – Расчёт себестоимости изделия
Наименование статьи | Сумма, руб. | % к полной стоимости |
1. Основные материалы | 70000 | 12,7 |
2. Основная заработная плата | 1037 | 16,5 |
3. Дополнительная заработная плата | 103,7 | 1,7 |
4. Отчисления на социальные нужды | 342,3 | 5,5 |
5. РСЭО | 1348,3 | 16,4 |
6. Амортизация | 18,7 | 3,6 |
7. Общепроизводственные расходы | 1244,6 | 15,2 |
8. Стоимость двигателя | 84000 | |
8. Производственная себестоимость | 158094,6 | 71,5 |
9. Внепроизводственные расходы | 63237,8 | 28,5 |
10. Полная себестоимость | 221332,4 | 100 |
Вывод: Путем внедрения системы турбонаддува стоимость двигателя увеличилась на 137332,4 рублей. Чтобы снизить стоимость модернизированного двигателя можно уменьшить внепроизводственные расходы на 10%, а также РСЭО на 20% и выбрать более дешевые компоненты для модернизации двигателя. Примем РСЭО 110%, внепроизводственные расходы 30% и стоимость компонетов 50000 рублей. Сведем в таблицу 19.
3.2 Анализ себестоимости продукции
Методика анализа себестоимости продукции:
- на основании произведённых расчётов, заполняется таблица 19
- методом сравнения выявляется абсолютное отклонение по всем показателям;
- по результатам анализа исчисленных показателей, предлагаются мероприятия по снижению производственной себестоимости.
К приоритетным направлениям снижения себестоимости можно отнести:
- внедрение новой, прогрессивной техники и энергосберегающих технологий производства, механизацию и автоматизацию производственных процессов;
- улучшение использования и применение новых видов сырья и материалов;
- изменение конструкции и технических характеристик товаров;
- совершенствование системы управления производством и труда;
- улучшение материально-технического снабжения; сокращение транспортных расходов.
Таблица 19 - Динамика затрат на единицу продукции по экономическим элементам
Элементы затрат | Сумма тыс. руб. | ||
Факт | План | Абсолют. откл.(+;-) | |
1 | 2 | 3 | 4 |
Оплата труда | 1140,7 | 1140,7 | 0 |
Отчисления на социальные нужды | 342,3 | 342,3 | 0 |
Материальные затраты | 70000 | 50000 | 20000 |
РСЭО | 1348,3 | 1140,9 | 207,4 |
Амортизация | 18,7 | 18,7 | 0 |
Общепроизводственные расходы | 1244,6 | 1244,6 | 0 |
Стоимость двигателя | 84000 | 84000 | 0 |
Производственная себестоимость | 158094,6 | 137887,2 | 20207,4 |
Вывод: Путем снижения РСЭО и стоимости комплектующих мы снизили стоимость нового двигателя на 20207,4 рублей. В итоге получаем 179253,4 рублей за новый двигатель, себестоимость снижается на 12,8%
3.3 Расчёт розничной цены изделия
Расчёт производится по условию, что рентабельность изделия (R) составляет 24%, торговая надбавка (наценка) (Тнад.) – 25%, тарифная ставка по налогу на добавленную стоимость (ТСНДС) – 18%. Расчёт сводится в таблицу 20
Таблица 20 – Расчёт розничной цены изделия
Наименование статьи | Обоснование расчёта | Сумма, руб. | % к полной стоимости |
1. Себестоимость изделия (С/с) | 179253,4 | 54,7ь | |
2. Прибыль (П) | П = R · С/с : 100% | 43020,8 | 13,12 |
3. НДС | НДС = ТСНДС · (С/с + П) | 40009,4 | 12,2 |
4. Отпускная цена | Цотп = С/с + П + НДС | 262283,6 | 80 |
5. Торговая надбавка | ТН = Тнад. · Цотп : 100% | 65570,9 | 20 |
6. Розничная цена | Цр = Цотп + ТН | 327854,5 | 100 |
По результатам расчётов таблицы 20 строится диаграмма «Структура розничной цены изделия».
Рисунок 4 – Структура розничной цены изделия
3.4 Расчёт изменения затрат на рубль товарной продукции
Методика расчёта изменения затрат на рубль товарной продукции:
По условию на будущий год предприятие планирует заменить часть оборудования на более современное. При этом себестоимость продукции снизится на 12,8%.
Себестоимость продукции в будущем году (С/С2 ) рассчитывается по формуле:
![]() ![]() |
где С/С1 – базовая себестоимость (таблица 19);
ПС% - процент снижения себестоимости.
Снижение затрат на рубль товарной продукции (ΔЗ1р) рассчитывается по формуле:
![]() ![]() |
где З1,З2 – затраты на рубль товарной продукции в базовом и будущем периодах.
Затраты на один рублю товарной продукции рассчитывается по формуле :
![]() ![]() ![]() | (24) |
где Ц – отпускная цена изделия.
3.5 Расчёт эффективности мероприятий по снижению себестоимости изделия
Методика расчёта изменения затрат на рубль товарной продукции:
Расчёт эффективности капитальных вложений производят на основе балансовой стоимости станков и стоимости арендованных производственных площадей.
Прежде всего необходимо рассчитать годовую экономию текущих затрат , которая показывает какую сумму экономит предприятие за счёт снижения себестоимости изделия:
![]() ![]() | (25) |
Далее считают годовой экономический эффект, который показывает насколько рублей годовая экономия текущих затрат превышает нормативную сумму эффективности капитальных вложений:
![]() ![]() | (26) |
где Ен – нормативный коэффициент эффективности капитальных вложений (Ен = 0,15);
К – капитальные вложения (балансовая стоимость оборудования )
Затем рассчитывают срок окупаемости капитальных вложений по формуле:
![]() ![]() | (27) |
Тн = 6,67 года – нормативный срок окупаемости капитальных вложений по отрасли.
Далее считают коэффициент эффективности капитальных вложений по формуле:
![]() ![]() | (28) |
Дата добавления: 2018-08-06; просмотров: 477; Мы поможем в написании вашей работы! |
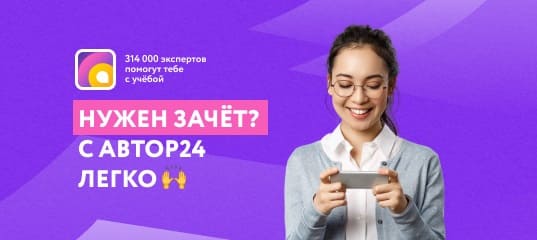
Мы поможем в написании ваших работ!