Удельные расходы тепла на образование силикатов
Силикаты | Расход тепла, кДж/кг оксида, при температуре, °С | |||||
1 000 | 1 100 | 1 200 | 1 300 | 1 400 | 1 500 | |
Al2O3∙ SiO2 BaO∙2SiO2 CaO∙SiO2 K2O∙4SiO2 (из поташа) K2O∙4SiO2 (из селитры) МgO∙SiO2 Na2O∙3SiO2 PbO∙SiO2 SiO2 (нагрев) | 1 664,7 2 073,6 4 423,8 5 668,2 10 701,7 5 201,0 7 055,5 556,4 1 305,2 | 1 866,2 2 235,8 4 656,3 6 166,8 11 271,5 5 525,8 7 658,1 615,1 1 425,4 | 2 068,2 2 397,9 4 954,7 6 665,5 11 840,9 5 850,1 8 261,0 673,3 1 546,1 | 2 269,7 2 560,1 5 193,9 7 164,1 12 410,4 6 174,8 8 863,5 731,6 1 668,9 | 2 471,3 2 722,2 5 432,8 7 662,7 12 979,8 6 499,1 9 466,9 790,2 1 787,0 | 2 673,2 2 884,4 5 672,0 8 161,3 13 549,2 6 823,8 10 069,0 848,5 1 907,7 |
Пример.Необходимо рассчитать расход тепла на образование силикатов при 1200°С для стекла следующего химического состава, мас.%: 72 SiO2; 2 Al2O3; 4 MgO; 8 CaO; 14 Na2O.
Расчет ведут на 100 кг стекла. Выражают заданный состав стекла в мольных долях путем деления массовой концентрации оксидов на молекулярную массу:
SiO2 72/60 = 1,20;
Al2O3 2/102= 0,02;
MgO 4/40 = 0,10;
CaO 8/56 = 0,14;
Na2O 14/62 = 0,23.
Составляют стехиометрические уравнения силикатообразования и определяют силикатный состав стекла, выраженный в мольных долях:
0,02 (Al2O3 + SiO2) = 0,02 Al2O3∙SiO2
0,10 (MgO + SiO2) = 0,01 MgO∙SiO2
0,14 (CaO + SiO2) = 0,14 CaO∙SiO2
0,23 (Na2CO3 + 3. SiO2) = 0,23 (Na2O∙3SiO2) + 0,23 CO2
Σ SiO2 = 0,86
Таким образом, в силикатах связано 0,86 моля SiO2, что составляет общего содержания SiO2. Свободного кремнезема в состав стекла вошло (1,20 – 0,86) = 0,34 моля (28,3 мол. %), что составляет 0,34∙60 = 20,4 кг.
|
|
Расчет расхода тепла на образование силикатов сводят в табл. 2.3.
Таблица 2.3
Расход тепла на образование силикатов
Силикат | Удельный расход тепла, кДж/кг | Расчет | Расход тепла, кДж |
Al2O3∙SiO2 MgO∙SiO2 CaO∙SiO2 Na2O∙3SiO2 SiO2 (нагрев) | 2 068,2 5 850,1 4 954,7 8 261,0 1 546,1 | 2 068,2×2 5 850,1×4 4 954,7×8 8 261,0×14 1 549,1×20,4 | 4 136,4 23 400,4 39 637,6 115 654,0 31 601,4 |
Итого: на 100 кг стекломассы на 1 кг >> | 214 429,8 2 144,3 |
Стеклообразование
После того как силикатообразование закончилось, в первичном силикатном расплаве остаются зерна песка, не вошедшего в состав образовавшихся силикатов. Первичный расплав содержит больше щелочных, щелочноземельных и других компонентов, чем готовое стекло заданного химического состава. Содержание нерастворившегося избыточного SiO2 при проваре шихты обычных промышленных стекол составляет порядка 25 % по массе от его содержания в шихте.
Растворение остаточного кварца (стеклообразование) протекает медленнее, чем силикатообразование, занимая 60–70 % общего времени варки промышленных стекол. Этот процесс имеет двойную природу – химическую и физико-химическую. Остаточные зерна кварца вступают с окружающим расплавом в химические реакции, образуя силикаты натрия с постепенно возрастающим содержанием SiO2. Чтобы реакции могли пройти до конца, необходимо, чтобы продукты реакций непрерывно отводились от поверхности зерен, заменяясь свежим реагентом – расплавом. Однако вследствие высокой вязкости силикатных расплавов этот обмен происходит медленно, продукты реакции накапливаются вокруг зерен и образуют пленки, в которых содержание SiO2 становится настолько высоким, что песок перестает растворяться.
|
|
Главную роль в отводе продуктов реакции играет диффузия, скорость которой зависит, помимо вязкости диффузионной среды, от разности концентраций растворяющегося вещества в объемах расплава, между которыми происходит диффузия. С уменьшением этой разности диффузия, а следовательно, и растворение замедляются, что и происходит при накоплении SiO2 у поверхности зерен песка.
Растворение идет не только по периферии зерен, но и внутри трещин, образовавшихся в зернах при их нагревании и полиморфных превращениях. Проникновение расплава в трещины вызывает в конечном итоге разрушение зерен, которые распадаются на блоки размером до десятка микрометров; эти блоки растворяются в стекломассе длительное время. Малая скорость растворения блоков отчасти вызвана тем, что при высокой температуре и в присутствии щелочных силикатов кварц превращается с поверхности в кристобалит, скорость растворения которого в силикатном расплаве меньше, чем α-кварца.
|
|
Скорость стеклообразования как химического процесса зависит от тех же факторов, что и скорость силикатообразования, а именно: от состава стекла и шихты, реакционной поверхности зерен в расплаве и температурных условий процесса. Вместе с тем скорость стеклообразования зависит от физических свойств и особенностей растворяющихся зерен, от свойств растворителя – расплава и от скорости его обмена на контакте с растворяющимся веществом.
Скорость стеклообразования зависит от вязкости и поверхностного натяжения расплава. Высокая вязкость затрудняет диффузию, а при повышенном поверхностном натяжении расплава, ухудшается смачивание им зерен песка, они флотируются на поверхность расплава и скапливаются, образуя агломераты, которые растворяются с трудом. Так как вязкость зависит от состава стекла, то и время стеклообразования различно для стекол различного состава.
|
|
Введение в состав шихты веществ, понижающих поверхностное натяжение, например сульфата натрия или сульфидов щелочных и щелочноземельных металлов, ускоряет растворение кварцевых зерен.
Время стеклообразования тем меньше, чем меньше зерна песка; для песков с одним размером зерен (монофракционных) оно обратно пропорционально их удельной поверхности. Неоднородность песков по зерновому составу, то есть одновременное присутствие крупных и пылевидных зерен, увеличивает время растворения песка. Пылевидные частицы растворяются первыми, вследствие чего вязкость расплава быстро возрастает и растворение более крупных зерен задерживается. На скорость растворения влияют также форма и чистота зерен кварца, а главное – разновидность строения SiO2 – его кристаллическое или аморфное состояние. Угловатые зерна с инородными включениями (оксидами железа, карбонатами и др.) растворяются быстрее округлых, чистых зерен. Особенно велика разница в скоростях растворения у кристаллической и аморфной разновидностей кремнезема: аморфный SiO2, взаимодействуя с растворами щелочей, способен образовывать щелочные силикаты уже при 180–200°С.
На скорость растворения кварцевых зерен сильное влияние оказывает температура расплава. Стеклообразование промышленных силикатных стекол ускоряется больше всего в интервале температур расплава 1550–1600°С, так как при этих температурах кремнезем переходит в неустойчивое аморфное состояние. В этом интервале повышение температуры на 10°С увеличивает скорость растворения SiO2 на 10–15%, а при температуре ниже 1550°С и выше 1600°С – на 5–7 %.
Вследствие диффузионного характера стеклообразования его скорость зависит от интенсивности обмена расплава на контакте с зернами SiО2 в такой же степени, как и от температуры. Движущаяся стекломасса удаляет с поверхности кварцевых зерен защитную кремнеземистую пленку, что дает импульс к новой активизации их растворения. Условия интенсивного обмена стекломассы могут создаваться, например, при бурном перемешивании ее газами или при сообщении расплаву вращательного движения с большой скоростью.
Для обычных стекол стеклообразование завершается при 1200°С.
Дата добавления: 2018-08-06; просмотров: 446; Мы поможем в написании вашей работы! |
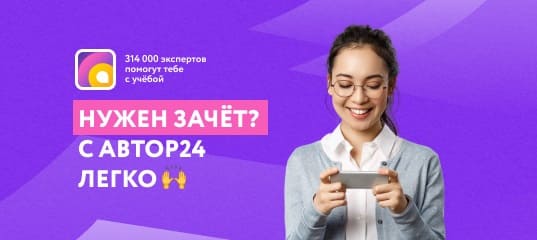
Мы поможем в написании ваших работ!