Получение изделий методом обработки металлов давлением
МЕТОДЫ получения и обработки материалов и изделий
Получение изделий методом литья
Литьё − это способ изготовления заготовки или изделия заполнением полости заданной конфигурации жидким металлом с последующим его затвердеванием. Различают слитки и отливки. Для литья слитков используют деформируемые сплавы, а для литья отливок - литейные.
Слитки, как правило, изготавливаются круглыми или плоскими. Они имеют большую массу и значительные габаритные размеры. Слитки используют для получения деталей машин и другой металлической продукции методами пластического деформирования (рис. 1).
![]() | ![]() ![]() |
Рис. 1 - Слитки, полученные методом литья |
Исходная заготовка - слиток (схема А) - в процессе изготовления конкретных деталей многократно подвергается нагреву до довольно высоких температур (до tнагр=0,7tпл) с одновременным силовым воздействием на металл, которое последовательно изменяет форму исходной заготовки, приближая ее к конфигурации требуемой детали (фасонная заготовка).
В результате теплового и силового воздействия структура металла претерпевает существенные изменения, часть литейных дефектов исчезает, механические свойства металла существенно повышаются.
![]() |
Схема А: кузнечно-штамповочное производство (из слитков) |
Отливки получают методами фасонного литья. Конфигурация отливок максимально приближена к размерам и конфигурации готовой детали. Методами фасонного литья можно изготовить детали практически любого веса (от несколько грамм до сотен тонн), любого размера (от миллиметров до нескольких метров), любой сложной конфигурации (рис. 2).
|
|
![]() | ![]() |
Рис. 2 - Отливки, полученные методом литья |
Исходная заготовка -отливка (схема Б) механические свойства металла могут быть улучшены только термической обработкой, что не позволяет устранить многие литейные дефекты.
Изменения в структуре литого металла не так глобальны, как при обработке давлением. К тому же, ряд сплавов вообще не упрочняется термической обработкой. В связи с этим к качеству литой структуры отливок предъявляются особо жесткие требования, т.к. она всецело определяет свойства металла в готовой детали.
![]() |
Схема Б: литейное производство (из отливок) |
Литейная форма представляет собой систему элементов, образующих рабочую полость с внешними контурами получаемой отливки.
· Разовая форма - получения отливки разрушают. Форма изготовляются путем уплотнения формовочных смесей, основой которых является кварцевый песок.
· Постоянная форма - пригодная для многократного применения.
|
|
Выбор способа литья определяется:
· служебным назначением детали,
· производственной программой
· требуемой точностью и качеством поверхности отливки.
Виды литья подразделяют на (рис. 3):
· литьём в песчаные формы | Распространенный метод литья |
· ![]() | Специальные виды литья, когда качество отливки не удовлетворяет предъявляемым требованиям − высокая точность, − лучшее качество поверхности, − меньшие величины припусков |
а) Литьё в песчаные формы | ![]() |
![]() | |
Рис. 3. Виды литья |
Эффективность литья может быть оценена через коэффициент использования металла (КИМ) - отношение масс детали и заготовки.
КИМ | ||
Виды литья | Литье под давлением | 0,95 |
Литье в кокиль | 0,75 | |
Литье в песчаные формы | 0,70 | |
Виды деформированного полуфабриката | Штамповка (горячая) | 0,45 |
Прокатка | 0,60 | |
Свободная ковка | 0,30 |
Требования к литейным материалам:
- хорошая жидкотекучесть,
- малая усадка,
- хорошая трещиностойкость,
|
|
- отсутствие различного рода дефектов (трещины, спаи, пригары, заливы)
Жидкотекучесть − это способность металлов и сплавов занимать литейную форму. Чистые металлы и сплавы эвтектического состава обладают лучшей жидкотеучесть, чем сплавы-твёрдые растворы, доэвтектические и заэвтектические сплавы.
Раковинывнутренние или наружныепустоты в теле отливки. Они могут быть пустыми или заполнены формовочным материалом, шлаком. С гладкой или шероховатой поверхностью. По природе происхождения различают: усадочные, газовые, шлаковые, песчаные.
Дефекты литья(пригары, спаи, заливы) - образуются в результате нарушения технологических параметров литья
![]() | ![]() |
а) жидкотекучесть | б) усадочная раковина |
![]() |
![]() |
в) горячая трещина | г) поры в слитке |
Рис. 4 - Дефекты литья |
Пластическая деформация (ПД)
Характерной особенностью металлов и сплавов является способность непрерывно деформироваться вплоть до разрушения под воздействием внешних сил, приложенных к металлу. Процесс деформации складывается из упругой и пластической деформаций и завершается разрушением.
Упругая (обратимая)деформация - это деформация, которая полностью исчезает после снятия нагрузки.
|
|
Пластическая (необратимая)деформация характеризуется остаточной деформацией в металле после снятия нагрузки. Кроме упругих напряжений она вызывает и остаточные, а также изменения в структуре металла, которые увеличиваются с ростом нагрузки вплоть до разрушения.
При пластической деформации происходит движение имеющихся дислокаций и образование огромного количества новых дислокаций в различных кристаллографических плоскостях и направлениях В недеформированном кристалле плотность дислокаций достигает 106 см-2, а в сильно деформированном металле порядка 1012 см-2. Если на пути движения дислокаций встречается препятствие в виде другой дислокации или дефектов другого рода, то процесс движения дислокаций тормозится и необходимы более высокие внешние напряжения, чтобы продеформировать материал, т. е. происходит деформационное упрочнение (наклеп, нагартовка, упрочнение – слова синонимы). Оно проявляется в процессе деформации и сохраняется по окончании деформирования.
Таким образом, увеличение количества (плотности) дислокаций в структуре деформированного металла в процессе пластической деформации ведет к повышению прочности
Например, путем ХПД; легированием; термической обработки (создаётся структура металла, с минимальной подвижностью дислокаций).
В процессе пластической деформации изменяется структура, а следовательно, все свойства металлов и сплавов. При высоких степенях деформации в деформированных полуфабрикатах возникает волокнистая структура с определенной кристаллографической ориентировкой, называемой текстурой деформации. Возникновение волокнистой текстурованной структуры в процессе деформирования вызывает анизотропию свойств деформированного полуфабриката, что обуславливает различное поведение листового материала при глубокой вытяжке (рис. 5а). При деформировании увеличиваются прочностные характеристики (твердость, sв, s0,2) и понижаются пластичность (s, y) и ударная вязкость (КСU) (рис. 5б)
![]() | ![]() |
Рис. 5. Изменение микроструктуры (а) и механических свойств (б) металла от степени деформации |
Получение изделий методом обработки металлов давлением
Обработки металлов давлением (ОМД) - это придание металлу требуемой формы, размеров и физико-механических свойств без нарушения его сплошности путем пластической деформации. ОМД подразделяется на горячую пластическую деформацию (ГПД) и холодную пластическую деформацию (ХПД).
При обработке металлов давлением на металл действуют внешние силы (удары молота, давление пресса), вызывающие в нем напряжения, превышающие предел упругости. В результате изменяется форма исходного металла, а объем его остается постоянным (не считая потерь на отходы и угар).в процессах ОМД упругая и пластическая деформация сопутствуют друг другу. При пластической деформации происходит изменение исходной структуры с резким повышением механических свойств металла.
В зависимости от температуры деформации различают холодную и горячую пластическую деформацию
Холодная пластическая деформация | Горячая пластическая деформация |
- проводят при температурах ниже tрек - приводит к наклепу металла или сплава - обработка давлением (ОД) ниже tрек называется холодной обработкой давлением | - проводят при температурах выше tрек - сопровождается рекристаллизацией Þ наклеп устраняется - обработка давлением (ОД) выше tрек называется горячей обработкой давлением |
ß Таким образом, границей между холодной и горячей обработкой давлением является температура рекристаллизации материала. |
Холодной обработке давлением поддаются только ковкие металлы, обладающие достаточной пластичностью Например: Свинец (Pb), Олово (Sn), Алюминий (Al), Медь (Cu), Цинк (Zn).
Хрупкие металлы и сплавы обработке давлением не обрабатываются. (Например: Магний (Mg), чугун, твердые сплавы.
Металлы и их сплавы, обладающие недостаточной пластичностью, обрабатывают в горячем состоянии. Например: Титан (Ti), Стали.
Металл | tпл,°С | tрек | Вывод |
свинец (Pb) | 327° | -30 | Обработка давлением при tкомн. является горячей ОД |
олово (Sn) | 232° | -70 | |
вольфрам (W) | 3380° | 1200° | Обработка давлением при 1000–1100°С является холодной ОД |
Алюминий (Al) | 660 | 100° | Для большинства металлов обработка давлением при комнатной температуре является холодной ОД |
к процессам горячей деформации относят процессы, протекающие при температуре выше температуры рекристаллизации. Для проведения процессов ГПД металл необходимо нагреть выше
tнагр ³0,7×Тпл для обеспечения полного протекания разупрочняющих процессов.
Достоинства горячей пластической обработки | Недостатки горячей пластической обработки |
Нагрев металла выше tрекр приводит Þ 1. Увеличивается способность к ПД 2. Уменьшается сопротивление деформации 3. ГОД менее трудоёмкая и энергоёмкая | Наличие окалины на поверхности детали Þ 1. Хуже качество поверхности. 2. Меньшая точность геометрических размеров |
Для обработки металлом давлением важно строгое соблюдение режима нагрева, так как он оказывает влияние на качество и точность геометрических размеров полуфабриката, состояние оборудования и технико-экономические показатели производства. В процессе нагрева возникает перепад температур между внутренними и наружными зонами заготовки, которые сопровождаются возникновением термических напряжений. Они при недостаточной пластичности металла или сплава могут привести к возникновению и развитию трещин в нагреваемом полуфабриката
Процессы обработки металлов давлением по назначению подразделяют на два вида:
1. Для получения заготовок постоянного поперечного сечения по длине -прутки, проволока, листы (рис. 3 а, б, в). Разновидностями ОМД являются прокатка, прессование и волочение;
2.Для получения деталей или полуфабрикатов, имеющих приближённо формы и размеры готовых деталей (рис. 3 г,д). Разновидностями ОМД являются ковка и штамповка.
![]() | | ![]() | |
а) прутки | б) листы | в) проволока | |
|
| ||
г) штампованные изделия | д) кованое изделие | ||
Рис. 3 - Полуфабрикаты полученные методами пластической деформацией | |||
Прокатка - процесс обжатия металла между вращающимися валками стана (рис. 4 а).
Волочение -состоит в деформации металла путем протягивания через сужающийся по длине канал круглого, квадратного или более сложного профиля. Получаемые заготовки - проволоки, прутка или трубы (рис. 4 б).
Прессование - процесс выдавливания (экструзии) находящегося в полости контейнера металла через выходное отверстие - очко матрицы (рис. 4 в).
Ковка - процесс свободного течения металла под воздействием периодических ударов или статических воздействий инструмента (необходимое изменение формы заготовки) (рис. 4 г).
Штамповка - способ изготовления фасонных заготовок пластической деформацией с помощью специального инструмента (штампов), рабочая полость которых определяет конфигурацию конечной штамповки (изделия) (рис. 4 д).
Прокатка − из плиты толщиной H получается лист толщиной h
![]() | Волочение − из прутка диаметром D получается проволока диаметром d
![]() | Прессование − из слитка получается длинномерный профиль (прутки)
![]() |
Ковка − из заготовки произвольной формы получается кованое изделие (подкова)
![]() | Штамповка − из заготовки в виде листа (пунктирные линии) получается фигурный профиль
![]() | Рис. 4. Виды обработки металлов давлением |
Оценка обрабатываемости давлением необходима при разработке новых деформируемых сплавов и при совершенствовании технологии производства и корректировки состава существующих сплавов. Обрабатываемость давлением включает сочетание оценок податливости материала и его технологической пластичности.
Податливость материала − это силовая характеристика сопротивления деформации. В случае повышенного сопротивления для обработки данного металла требуется более мощное оборудование.
Технологическая пластичность − это характеристика предельной степени деформации, после которой либо происходит локализация деформации, либо наступает разрушение металла во время обработки металла давлением в производственных условиях.
Дата добавления: 2018-08-06; просмотров: 2020; Мы поможем в написании вашей работы! |
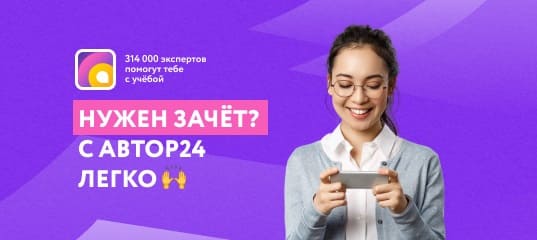
Мы поможем в написании ваших работ!