Границы и область применения.
Содержание.
1.Введение. 2
2.Виды сварки и их классификация. 4
3.Термитная сварка. 6
3.1.Принцип сварки. 6
3.2.Границы и область применения. 9
3.3.Выбор основных и присадочных материалов. 13
3.4.Техника сварки. 14
3.5.Основные элементы устройств для термитной сварки. 17
5. Лазерная сварка. 18
5.1.Сущность и основные преимущества сварки лазерным лучом. 18
5.2.Технологические особенности процесса лазерной сварки. 22
5.3.Качество и свойства лазерной сварки. 31
6.Заключение. 33
7.Список литературы. 34
Введение.
Сварочная металлургия отличается от других металлургических процессов высокими температурами термического цикла и малым временем существования сварочной ванны в жидком состоянии, т.е. в состоянии, доступном для металлургической обработки металла сварного шва. Кроме того, специфичны процессы кристаллизации сварочной ванны, начинающиеся от границы сплавления, и образования изменённого по своим свойствам металла зоны термического влияния.
В своей работе я отразил сущность лишь основных и наиболее общих процессов сварки, хотя постарался изложить их как можно подробней и интересней.
Сварка сопровождается комплексом одновременно протекающих процессов, основными из которых являются: тепловое воздействие на металл в зоне термического влияния, термодеформационные плавления, металлургической обработки и кристаллизации металла в объёме сварочной ванны.
|
|
Физическая свариваемость характеризует принципиальную возможность получения монолитных сварных соединений и главным образом относится к разнородным металлам.
В процессе сварки имеет место непрерывное охлаждение. Характер структурных превращений при изотермической выдержке. При непрерывном охлаждении, значение инкубационного периода в 1.5 раза больше, чем при изотермическом. С увеличением скорости охлаждения получаемая структура в зоне изотермического влияния измельчается, твёрдость её повышается. Если скорость охлаждения превышает критическую скорость, образование структур закалки неизбежно.
Закалённые структуры в аппаратостроении являются крайне нежелательными: отличаются высокой твёрдостью, хрупкостью, плохо обрабатываются, склонны к образованию трещин.
Если скорость охлаждения ниже критической скорости, образование закалочных структур исключается. В зоне термического влияния наиболее желательными являются пластичные, хорошо обрабатываемые структуры типа перлита или сорбита. Поэтому получение качественных соединений непременно связано с достижением желаемых структур в основном регулированием скорости охлаждения.
Подогрев способствует перлитному превращению и является действенным средством исключения закалочных структур. Поэтому он служит в качестве предварительной термической обработки сварных соединений (нагрев до сварки и в процессе её). Меняя скорость охлаждения, можно получить желаемую твёрдость в зоне термического влияния.
|
|
В некоторых случаях появляется необходимость увеличения скорости охлаждения. Путём ускоренного охлаждения удаётся измельчить зерно, повысить прочностные свойства и ударную вязкость в зоне термического влияния. С этой целью находит применение метод сопутствующего охлаждения. Сварное соединение в процессе сварки с обратной стороны дуги охлаждается водой или воздушной смесью, что способствует получению крутой ветви скорости охлаждения.
Виды сварки и их классификация.
Сварка - технологический процесс соединения твёрдых материалов в результате действия межатомных сил, которое происходит при местном сплавлении или совместном пластическом деформировании свариваемых частей.
Сваркой получают изделия из металла и неметаллических материалов (стекла, керамики, пластмасс и др.). Изменяя режимы сварки, можно наплавлять слои металла различной толщины и различного состава. На специальном оборудовании в определенных условиях можно осуществлять процессы, противоположные по своей сущности процессу соединения, например огневую, или термическую, резку металлов.
|
|
Современные способы сварки металлов можно разделить на две большие группы: сварка плавлением, или сварка в жидкой фазе, и сварка давлением, или сварка в твёрдой фазе. При сварке плавлением расплавленный металл соединяемых частей самопроизвольно, без приложения внешних сил соединяется в одно целое в результате расплавления и смачивания в зоне сварки и взаимного растворения материала. При сварке давлением для соединения частей без расплавления необходимо значительное давление. Граница между этими группами не всегда достаточно чёткая, например возможна сварка с частичным оплавлением деталей и последующим сдавливанием их (контактная электросварка). В предлагаемой классификации в каждую группу входит несколько способов. К сварке плавлением относятся: дуговая, плазменная, электрошлаковая, газовая, лучевая и др.; к сварке давлением - горновая, холодная, ультразвуковая, трением, взрывом и др. В основу классификации может быть положен и какой-либо др. признак. Например, по роду энергии могут быть выделены следующие виды сварки электрическая (дуговая, контактная, электрошлаковая, плазменная, индукционная и т. д.), механическая (трением, холодная, ультразвуковая и т. п.), химическая (газовая, термитная), лучевая (фотонная, электронная, лазерная).
|
|
Термитная сварка.
Принцип сварки.
Термитами называются порошкообразные горючие смеси металлов с окислами металлов, способные сгорать с выделением значительного количества тепла и развивать при этом весьма высокую температуру. Термиты изобретены в конце позапрошлого столетия. Они применяются для производства некоторых металлов и сплавов.
Важной областью применения термитов является сварка металлов. Горючими металлами в термитных смесях могут служить металлы с большой теплотой образования окислов, например алюминий, магний, кремний (в особенности аморфный). Источником кислорода в термитных смесях являются окислы металлов со сравнительно небольшой теплотой образования, например, окислы железа, марганца, никеля, меди и т. п. В качестве источника кислорода в сварочных термитах обычно применяется железная окалина, примерно отвечающая по составу магнитной окиси-закиси железа Fe304, содержащей 27,6% кислорода и 72,4% железа.
Наиболее важным для сварки является алюминиевый термит, который состоит из металлического алюминия в форме грубозернистого порошка или крупы, обычно с величиной зерна около 1 мм, и из железной окалины примерно с той же величиной зерна. По внешнему виду алюминиевый термит представляет собой сыпучую грубозернистую смесь из белых зерен (алюминий) и черных зерен (железная окалина). Для зажигания термита его необходимо нагреть хотя бы в одной точке до температуры порядка 1000° С. Начавшееся горение протекает весьма бурно, быстро распространяется на весь объем термитной смеси и проходит по реакции:
3Fe2О4 + 8Al = 4Al2О3+9Fe (1)
Термит сгорает полностью за 20—30 сек. Время горения зависит от грануляции, т. е. размеров зерен смеси: чем мельче зерно, тем быстрее заканчивается процесс горения. Экзотермическая реакция сгорания 1 кг алюминиевой термитной смеси развивает около 750 ккал.
Из приведенной выше реакции сгорания термита легко рассчитать, что на 1 кг термитной смеси необходимо 237 г алюминия и 763 г железной окалины. Этот расчет относится к химически чистым компонентам. В действительности термитную смесь изготовляют из возможно более дешевых материалов: из технического алюминия низших марок или алюминиевого лома с содержанием алюминия 88—98%. Железную окалину берут обычно из цехов горячей прокатки стали, в которых она является отбросом производства. Такая окалина может содержать различное количество кислорода. Поэтому действительный состав термитных смесей может меняться в довольно широких пределах в зависимости от химического состава применяемых материалов, который следует проверять химическим анализом. Наиболее распространенный состав термитной смеси для материалов среднего качества: 23% алюминия и 77% железной окалины.
Несмотря на то, что алюминиевый термит выделяет сравнительно небольшое количество тепла, в среднем 750 ккал на 1 кг смеси (1 кг хорошего каменного угля дает 7000 ккал), термитная смесь развивает при сгорании весьма высокую температуру. Это объясняется тем, что сгорание термита идет исключительно за счет вещества самой смеси и 1 кг термита при сгорании дает столько же, т. е. 1 кг продуктов сгорания. Уголь же сгорает за счет кислорода воздуха, и при сжигании 1 кг угля в воздухе получается около 14 кг продуктов сгорания. По теоретическому расчету реакции сгорания термита с учетом теплоемкости продуктов сгорания обеспечивается температура ~ 3000°С; такую же температуру показывают и непосредственные измерения. Поэтому продукты сгорания термита — железо (температура плавления около 1500°С) и окись алюминия А12O3 (температура плавления 2050°С) получаются в расплавленном, жидком и сильно перегретом виде.
Если сжечь термит в огнеупорном тигле, то по окончании реакции горения продукты реакции — жидкая сталь и шлак, состоящий главным образом из окиси алюминия, быстро разделятся на два слоя: металл — шлак в соответствии с удельным весом продуктов реакции; из 1 кг термитной смеси образуется 550 г расплавленной стали и 450 г шлака — расплавленной окиси алюминия. В сварочные термитные смеси, помимо алюминия и железной окалины, обычно вносят различные добавки с целью улучшить состав и повысить прочность термитного металла, увеличить общий выход металла при сжигании смеси, несколько понизить температуру термитной реакции.
Для раскисления термитного металла, улучшения его химического состава и повышения механической прочности в термитные смеси обычно вводят ферросплавы, главным образом ферросилиций и ферромарганец. Меняя количество этих присадок, можно изменять в широких пределах химический состав и механические свойства термитного металла, например предел прочности можно изменять от 40 до 75 кг/мм2. Для увеличения выхода термитного металла и некоторого снижения температуры термитной реакции в термитную смесь для сварки обычно добавляют технически чистое железо в мелких кусочках в количестве 10—15% веса термитной смеси. Для этой цели чаще всего применяют обсечку — отход при производстве проволочных гвоздей. Окончательный состав термитной сварочной смеси определяют расчетом в зависимости от характера работы и состава металла, подлежащего сварке.
Границы и область применения.
Рассмотрим применение и области использования термитной сварки на примере сварки рельсового стыка — самом обычном применении термитной сварки. При сварке давлением жидкие продукты выливают через край тигля (рисунок 1, а); при этом место сварки сначала заливается жидким шлаком, смачивающим металл и дающим на его поверхности тонкую пленку, препятствующую прилипанию термитного металла к основному. Жидкий металл поступает в форму вслед за шлаком, но не сваривается с основным металлом и может быть удален по окончании сварки. Жидкий металл используется лишь как носитель тепла для разогрева места сварки. После того как жидкая смесь выпущена в форму и стык достаточно разогрет, приступают к осадке. Для этой цели применяют стяжные прессы, приводимые вручную рычажными ключами. При повороте ключей приходят в действие винтовые стяжки, создающие давление и производящие осадку разогретых деталей. Стяжной пресс (рисунок 2) надевают на место сварки до выпуска расплавленной смеси.
Поверхность сварного стыка должна быть защищена от попадания термитного шлака, для чего соединяемые поверхности тщательно пригоняют, отшлифовывают и перед сваркой стягивают со значительным давлением посредством стяжного пресса. Так как рельсовая сталь обладает ограниченной свариваемостью в пластическом состоянии, то в стык перед сваркой закладывают пластинку по профилю рельса из мягкой низкоуглеродистой стали с тщательно зачищенными и отшлифованными поверхностями. При разогреве стыка термитом усиливают давление, поворачивая стяжные гайки пресса, и производят осадку.
Способ термитной сварки давлением в том виде, как он описан выше, в настоящее время почти не применяется, так как этот способ сложен, кропотлив, требует очень тщательной пригонки свариваемых поверхностей и дает значительный разброс результатов в отношении прочности стыка. Также трудоемка операция осадки и установки стяжного процесса.
Значительно дешевле и удобнее сварка плавлением, так называемый способ промежуточного литья (рисунок 1, б). В этом случае рельсы заформовывают со значительным зазором (10—12 мм) в стыке, поэтому особенно тщательной пригонки и шлифования соединяемых поверхностей не требуется. Расплавленную смесь выпускают через дно тигля. Поступающий в форму перегретый расплавленный металл оплавляет основной металл у сварного стыка и сплавляется с ним в одно целое. Термитный шлак, поступающий в форму вслед за металлом, служит лишь для дополнительного подогрева сварного стыка и замедления его охлаждения по окончании сварки. Осадочного давления и применения стяжного пресса не требуется, рельсы остаются неподвижными в процессе сварки. Поэтому возможно, например, сваривать рельсы, уложенные в пути, без расшивки, что позволяет сваривать плети неограниченной длины, вваривать куски рельсов в местах вырезки поврежденных стыков и т. п.
Рисунок 1. - Схемы термитной сварки рельсового стыка
а — давлением; б — плавлением (промежуточное литье); в — комбинированный способ.
Недостатки способа промежуточного литья:
1) несколько увеличенный расход термита;
2) образование литой структуры металла в сварном стыке, не уплотняемого осадочным давлением и поэтому склонного к образованию пор и раковин;
3) все сечение стыка для надлежащего разогрева получает значительный облив, удаление которого вызывает известные затруднения. Приходится обрубать и шлифовать поверхность катания и боковые грани головки рельса.
При комбинированном способе металл выпускают через дно тигля, заливку жидким металлом ведут лишь до нижней грани головки рельса (рисунок 1, в), а отшлифованные торцы головок собирают со вкладной пластинкой низкоуглеродистой стали. При выпуске жидкой смеси головку заливают шлаком и сваривают давлением при последующей осадке стяжным прессом, в то время как шейка и подошва рельса оказываются сваренными плавлением по способу промежуточного литья. Комбинированный способ является наилучшим и в настоящее время находит преобладающее применение. Результаты термитной сварки рельсовых стыков достаточно удовлетворительны. Сварку легко вести в полевых условиях. Несмотря на это, термитная сварка рельсовых стыков на железных дорогах применяется в ограниченных размерах и в настоящее время почти вытеснена контактной сваркой. Причиной служит довольно высокая стоимость термитной смеси, дефицитность металлического алюминия, низкая производительность термитной сварки. Этот вид сварки сохранил свое значение для рельсовых стыков трамвайных путей, так как в условиях города другие методы сварки рельсовых стыков трудноприменимы.
Рисунок 2. - Стяжной пресс для рельсового стыка
1 — стяжная штанга; 2 — стяжная гайка; 3 — зажимная гайка; 4 — термитный тигель; 5 — крышка тигля.
Термитную сварку можно использовать для ремонта крупных стальных и чугунных деталей. При сварке чугуна применяют специальный термит со значительным содержанием ферросилиция. Посредством термитной сварки можно приливать отломанные части стальных деталей, например зубья крупных шестерен, наплавлять поверхности и т. п. Термитная сварка позволяет изготовлять стальные отливки, на месте в любых, даже полевых условиях, что в ряде случаев может представлять практический интерес.
Дата добавления: 2018-08-06; просмотров: 246; Мы поможем в написании вашей работы! |
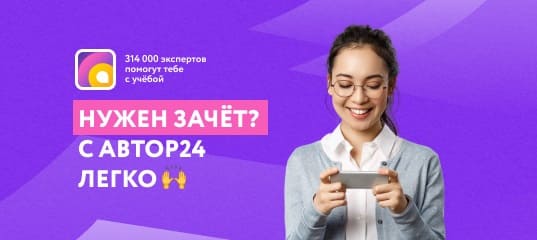
Мы поможем в написании ваших работ!