Выбор способа производства и анализ типовых технологических линий.
При проектировании производства необходимо выбрать наиболее рациональный способ производства изделий, технологич. схему процесса, оборудование, режимы формования, оптимал. режим ТО. Выбор технол. пр-ва зависит от наменклатуры изделий, объемы вып. изд., осбенностей армирования и т.д. Выбор осущ. сравнением нескольких вариантов. Приемлемый - способ с наим. кап. затратами при наименьшей себестоимости продукции. Для выбора необход. сгрупир. изд. по однородным технол. и конструктивн. признакам, опред. баз. изд. по каждойц группе. ЗА базовый приним. наиболее массовый тип изд. Для базового выбир. и обоснов. способ пр-ва, составл. технол. схема пр-ва и расчет произв. мощностей.
Агрег-пот. Изгод. изд.: панели перекрытий, многопуст. панели, колонны, сваи, , трубы; осн. обор. – бетоноукл., виброплощ., пригр. щит.
Конв. способ. период. действ. Изг. изд.: много- и односл. панели, внутр. стен панели, перкрытия, лестн. марши; осн. обор. – бетоноукл., выбропл., заглаж. устр.
Конв. способ. непрер. формов. Изг. изд.: нар. стен. панели, перекрытия, трат. плитка и т.д.; осн. обор. – двухяр. стан, вибропрот. устр.
Стендов. способ: фермы, подкр. бакли, сваи, ригели и т.д. Оборуд.: бетоноукл., навесн. вибраторы.
Обоснование и составление схемы технологического процесса
Проектирование предприятия начинается с построения технологической схемы. Последняя устанавливает состав процессов и порядок выполнения, а также дает возможность установить вид необходимого теплотехнического и транспортного оборудования и условия их компоновки, дает наглядное представление о составе производственных операций и их взаимосвязи.
|
|
Технологическая схема сопровождается пояснительной запиской, в которой приводятся описание технологических и других процессов, характеристика исходного сырья, необходимая рецептура изготавлеваемого материала, условия хранения сырья и готовности продукции, а также технические характеристики выбранного оборудования.
Схемы бывают: условные, фигурноконтурные и фигурно-пространственные. На условных схемах отдельные операции с учетом их функционального назначения выделяют с помощью спец. символов. Линии, соедин. символы, показывают направление основных потоков и поставки материалов и полуфабрикатов.
В Фигурно-контурных схемах вместо символов показывают контуры используемого оборудования.
Расчет расходов сырья, топливных и энергетических ресурсов.
Потребное колич. мат. необход. знать при проектир. складов цем., зап., арм. и БСЦ.
Исходн. данными служат год. мощность предприятия, номенклатура и чертежи изд., способ формования изделий. Потребность в колич. матер. опред. по видам изделий и бетона с учетом потерь.
|
|
При привязке типовых складов уем. БСЦ, составлений обоснований и инвестиций, потебное колич. мат. опред. по нормам технологич. проектирования предприятий СЖБ и СНИП 5.01.23-83. Предвар. необходимо выбрать способ пр-ва, технологическую схему и формуемость бет. смеси. Согласно снипу для неармир. бет изд. составляет 200 кг, для армир. – 220, максимально – 600кг/м3. Для расчета вместимости складов и бункеров допускается принимать укрупненные расходы цем. и зап. (см. табл. 2-4 ОНТП), расход матер. различн. видов отделки (по табл. 6 ОНТП). Расход воды для всех расчетов приним. 200л. Расход хим. доб. по СНиП 3.09.01-85.
Расчет энергетических рес. производтся исходя из того, что расходуются они на: электроэнергии на освещение исходя из норм для внутреннего освещения, на технологические нужды (электродвигателей различного оборудования исходя из расхода в паспортных данных и их работы в течении года).
Проектирование склада цемента
Хранение цем-та должно производ-ся в стационарных или инвентарных силосных складах :
- прирельсовые (привязаны к железной дороге);
- притрассовые (расположены вдоль автодороги).
Транспортный поток на складе цемента происходит в трех направлениях:
|
|
• разгрузка вагонов и загрузка силосов;
• подача цемента из силосов в расходные бункера БСЦ;
• разгрузка бункеров и подача в бетоносмесители.
Способы разгрузки цемента зависят от вида транспортных средств, в которых он поставляется.
Разгрузку цем-та из вагонов-цементовозов типа Хоппер, контейнеров с открывающимся днищем осущ-т гравитац спос-м в приемные бункера, а затем подают на склад пневмотранспортом.
Разгрузку автоцементовозов и вагонов-цементовозов (цистерн), оснащенных пневматическими установками, производят пневматическим способом.
Для транспортирования цемента со склада в расходные бункера БСЦ применяют пневмовинтовые, камерные или струйные насосы. Выбор вида насоса зависит от производительности этих агрегатов (от 25 до 140 т/ч).
Производительность насоса должна быть больше часового расхода цемента на предприятии для изготовления изделий:
где Кчн - часовой коэффициент неравномерности выдачи бетонной смеси: для товарной смеси К^ = 0,8, при выдаче в цех - 0,5... 0,8;
nсм и Vсм - соответственно число и объем смесителей;
βб - коэффициент выхода бетона;
nз - нормативное число замесов в час;
|
|
Ц - расход цемента на 1 м3.
Склады цемента предприятий сборного железобетона должны обладать следующими конструктивными особенностями:
• надежно защищать цемент от увлажнения;
• обеспечивать раздельное хранение цементов не менее трех видов и марок;
• обеспечивать периодическое рыхление цемента при хранении;
• допускать возможность выдачи цемента в автоцементовозы.
При хранении цемента в силосах он слеживается, т.е. теряет сыпучесть. На слеживаемость сильно влияет влажность (должна быть не более 1 %). Для предотвращения слеживаемости в силосах необходимо периодическое аэрационно-пневматическое разрыхление и перекачивание цемента не реже 1 раза в 15 суток.
Большинство предприятий оснащено силосными складами цемента вместимостью 240, 360,480, 720, 1100, 1700,2500 и 4000 тонн. По ОНТП 07-85 требуются:
• запас цемента на складе (в расходных рабочих сутках) при поступлении железнодорожным транспортом - 7-10 сут, автотранспортом - 5-7 сут;
• запас декоративного цемента - 30 сут;
• число емкостей для хранения: на заводах при Пг < 100 тыс. м3/год не менее 4; при Пг > 100 тыс. м3/год не менее 6;
• коэффициент заполнения емкостей склада не менее 0,9;
• средняя плотность цемента - минимальная расчетная в разрыхленном состоянии -1 т/м3.
Технологические расчеты сводятся к опред-нию вместимости склада цемента по массе, кг:
где nсм и Vсм - соответственно число и объем смесителей;
tсм и Nсм - соответственно длительность смены, ч, и число смен;
Зсц - запас цемента на складе, сут;
и вместимости склада цемента по объему
где ρцн, - минимальная расчетная плотность цемента, кг/м3;
Кемк - коэффициент заполнения емкости склада, равный 0,9.
Склад цемента следует размещать вблизи бетоносмесительного цеха с наветренной стороны от главного производственного и административного корпусов.
20.Утилизация некондиционных железобетонных изделий.
В результате технологических правил произ-ва при приготовлении б/с , ТО, транспортировании или складировании образуется некондиционные конструкции, которые необходимо подвергнуть утилизации.
Процесс переработки НК делят на 2 этапа: 1) предварительное разрушение с отделением ар-ры 2) дробление бетона до требуемых размеров фракций
Предварительное разрушение может производиться механическим, гидродинамическим, взрывным или электро-импульсным способами, обеспечивающими отделение бетона от ар-ры до 90 %/.
Дробление бетона осуществляют в щековых, конусных и других дробилках.
При механическом разрушении используется установка для разрушения изделий и отделения ар-ры типа УПН-24. Для этого изделие поднимают и устанавливают на колосниковый стол, а затем разрушают посредством бруса ножа пресса.
Щебень из дробленого бетона можно применять в качестве крупного заполнителя для бетонов марок М50-М200.
Бетоны на этом щебне хар-ся повышенным водопоглащением, меньшей прочностью, меньшим модулем упругости, по сравнению с бетоном на природном заполнителе.
Дата добавления: 2018-08-06; просмотров: 236; Мы поможем в написании вашей работы! |
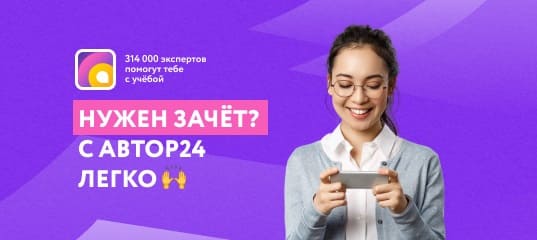
Мы поможем в написании ваших работ!