Назначение установки и сведения о технологическом процессе
Nbsp;
РЕФЕРАТ
Выпускная квалификационная работа 138 л., 11 рис., 38 табл., 32 источников, 2 прил.
ОСНОВНОЕ ОБОРУДОВАНИЕ БЛОКА РЕКТИФИКАЦИИ НИЗКОКИПЯЩИХ УГЛЕВОДОРОДОВ АБСОРБЦИОННО-ГАЗОФРАКЦИОНИРУЮЩЕЙ УСТАНОВКИ
Объектом исследования является основное оборудование технологической установки абсорбционно-газофакционирующей установки низкокипящих углеводородов.
В процессе исследования были рассмотрены технологический процесс каталитического риформинга бензиновых фракций, технические разработки и решения для повышения качества процесса, основное технологическое оборудование.
Цель работы – проектирование и подбор колонного, теплообменного и емкостного оборудования.
В результате исследования проделанной работы обоснована необходимость качественного проектирования оборудования для надежной и эффективной работы.
В результате исследования проведен расчет на прочность и устойчивость колонного аппарата, подбор и расчет на прочность теплообменного аппарата и емкости.
Введение
Процессы разделения углеводородных фракций на индивидуальные углеводороды или узкие технические фракции, таких как конденсация, компрессия, абсорбция, ректификация получили широкое распространение на нефте- и газоперерабатывающих заводах.
Известно, что ректификация является завершающей стадией процесса разделения углеводородов. Особенностью ректификации сжиженных газов по сравнению с ректификацией нефтяных фракций является четкость разделения очень близких по температуре кипения компонентов или фракций, которую приходится проводить при повышенном давлении в колоннах, по причине необходимости создания жидкостного орошения и сконденсировать верхние продукты колонн в обычных воздушных в водяных холодильниках, не прибегая к искусственному холоду.
|
|
На НПЗ для этих целей применяются преимущественно два типа газофракционирующих установок, в каждый из которых входят блоки компрессии и конденсации: ректификационный ‒ сокращенно ГФУ и абсорбционно–ректификационный ‒ АГФУ.
Литературный обзор
Теоретические основы процесса ректификации
В зависимости от происхождения нефтяные газы делятся на природные, попутные и искусственные [1,2]. Природные газы добываются из самостоятельных месторождений, попутные — совместно с нефтью.
Искусственные газы образуются при переработке нефти каталитическими и термическими методами. Составы газов, получаемых при различных процессах, очень заметно отличаются. Газы термических процессов и каталитического крекинга в значительном количестве содержат непредельные углеводороды, а в газах каталитического риформинга, гидроочистки, гидрокрекинга их вообще нет.
|
|
На многих современных технологических установках имеются блоки первичной обработки газа. На этих блоках проводится очистка газа от сероводорода, а также выделение из газа углеводородов С3 и С4 в виде жидкой углеводородной фракции.
Однако разделение газа на отдельные индивидуальные углеводороды и узкие углеводородные фракции осуществляется на специально сооружаемых газофракционирующих установках (ГФУ). На нефтеперерабатывающем заводе обычно имеется не менее двух ГФУ, одна из которых предназначена для переработки предельных углеводородов, другая — непредельных [2,3].
При переработке предельных углеводородов получаются следующие продукты, которые используются для различных целей:
1) этановая фракция — сырье пиролиза, хладагент на установках депарафинизации масел и др.;
2) пропановая фракция — сырье пиролиза, хладагент для многих технологических установок, бытовой сжиженный газ;
3) изобутановая фракция — сырье для производства синтетического каучука (изопренового и бутилкаучука), используется на установках алкилирования;
4) бутановая фракция — сырье для получения бутадиена в производстве синтетического каучука, сырье пиролиза и компонент сжиженного бытового газа, добавка к автомобильному бензину для придания ему требуемого давления паров;'
|
|
5) изопентановая фракция — сырье для производства изопренового каучука, компонент в высокооктановых сортах бензинов;
6) пентановая фракция — сырье для процессов изомеризации и пиролиза, в производстве амилового спирта.
На ГФУ непредельных углеводородов из олефинсодержащих потоков выделяются следующие фракции:
1) пропан-пропиленовая — сырье для производства полимер-бензина, фенола и ацетона, синтетических моющих средств, бутиловых спиртов, может быть использована как сырье установок алкилирования;
2) бутан-бутиленовая — сырье установок алкилирования и полимеризации, присадки к маслам, в производстве синтетических каучуков.
Очистка и осушка газов предшествуют их фракционированию и дальнейшей переработке.
Очистка газов. Нефтезаводские газы, полученные при переработке сернистых нефтей, всегда содержат сероводород и некоторые другие сернистые соединения. Особенно много сероводорода в газах установок, перерабатывающих тяжелое сырье: мазут, вакуумные дистилляты, гудрон.
|
|
Сероводород ухудшает работу катализаторов тех каталитических процессов, которые используют в качестве сырья сжиженные газы, его присутствие совершенно недопустимо в бытовом сжиженном газе. Наличие активных сернистых соединений вредно влияет на оборудование газоперерабатывающих установок, вызывает активную коррозию аппаратов и трубопроводов.
Поэтому углеводородные газы, содержащие сероводород и такие активные сернистые соединения, как низшие меркаптаны, перед подачей на ГФУ подвергают очистке. В некоторых случаях газы нефтепереработки очищают также от окиси и двуокиси углерода.
При очистке газа от сероводорода чаще всего используется процесс абсорбции. Абсорбентами для избирательного извлечения сероводорода из газов служат растворы трикалийфосфата, фенолята натрия, этаноламинов.
Наиболее распространена на НПЗ очистка при помощи раствора моноэтаноламина (МЭА).
1.1.1 Способы разделения газовых смесей.
Для разделения смеси газов на индивидуальные компоненты или пригодные для дальнейшей переработки технические фракции применяются следующие процессы: конденсация, компрессия, абсорбция, ректификация, адсорбция. На ГФУ эти процессы комбинируются в различных сочетаниях.
Конденсация — первая стадия разделения газов. С помощью конденсации газ превращается в двухфазную систему жидкость — газ, которую затем механически разделяют на газ и жидкость. В качестве хладагента при конденсации прежде всего используют воду или воздух. В этом случае температура конденсации составляет 35-40°С. Чтобы увеличить число конденсирующихся компонентов, необходимо понизить температуру конденсации, используя в качестве хладагента испаряющийся аммиак, фреон или углеводородные газы — пропан и этан [2,3,4].
Компрессия применяется в схемах разделения газов совместно с конденсацией. При повышении давления газов создаются наиболее благоприятные условия конденсации углеводородов.
Абсорбция — это процесс поглощения отдельных компонентов газа жидкостью (абсорбентом), вступающей с ним в контакт.
При повышении температуры растворимость газа в жидкости уменьшается, абсорбция замедляется и может совсем прекратиться. На технологических установках при извлечении из газа пропана и бутана, поддерживается температура не выше 35 °С. Выбор абсорбента зависит от свойств абсорбируемого газа. Углеводородные газы наилучшим образом извлекаются близкими им по строению и молекулярной массе жидкими углеводородами легкого бензина.
Обычно на абсорбционных установках применяют двухступенчатую абсорбцию: основным абсорбентом служит бензиновая фракция, а затем выходящий из абсорбера газ промывается жидкостью тяжелого фракционного состава, например керосиногазойлевой фракцией, для извлечения из газа унесенного бензина.
Поглощение газа жидкостью сопровождается выделением тепла. Чтобы при этом не ухудшались условия абсорбции, на технологических установках применяют ряд специальных приемов. Одним из эффективных способов повышения степени извлечения целевых компонентов является охлаждение абсорбента и газа перед подачей их в абсорбер до температуры ниже рабочей. Съем тепла абсорбции осуществляется в промежуточных выносных холодильниках. Насыщенный абсорбент, взятый с вышележащей тарелки, пропускается самотеком или прокачивается насосом через холодильники, а затем возвращается на нижележащую тарелку. Для охлаждения сырья и циркулирующего абсорбента применяют не только воду, но и искусственные хладагенты: пропан, аммиак.
Поглощенный при абсорбции газ отделяется от абсорбента в отпарной колонне-десорбере. Для десорбции необходимы условия, противоположные тем, при которых следует проводить абсорбцию, т. е. повышенная температура и низкое давление.
Адсорбционный метод разделения газов мало распространен в промышленности. Он основан на способности некоторых твердых веществ с развитой поверхностью (активированного угля, силикагеля и др.) избирательно поглощать различные компоненты газа. Подобно жидким поглотителям (абсорбентам) твердые адсорбенты более интенсивно поглощают тяжелые углеводороды. Подобрав определенный режим адсорбции, можно получить достаточно сухой газ. Адсорбцию применяют для извлечения целевых компонентов из смесей, в которых содержание извлекаемых углеводородов не превышает 50 мг/м3, а также из газов, содержащих воздух.
Ректификация является завершающей стадией разделения газовых смесей. Она применяется для получения индивидуальных углеводородов высокой чистоты. Поскольку разделение на компоненты смеси газов проводить затруднительно, при существующих схемах газоразделения на ректификацию подают жидкость, выделенную из газа конденсационно-компрессионным или абсорбционным методом. Особенность ректификации сжиженных газов по сравнению с ректификацией нефтяных фракций — необходимость разделения очень близких по температуре кипения продуктов и получения товарных продуктов высокой степени чистоты. Ректификация сжиженных газов отличается также повышенным давлением в колоннах, поскольку для создания орошения необходимо сконденсировать верхние продукты ректификационных колонн в обычных воздушных и водяных холодильниках, не прибегая к искусственному холоду.
Схема ректификационной установки и последовательность выделения отдельных компонентов зависят от состава исходной смеси, требуемой чистоты продуктов и количества получаемых фракций.
Установки АГФУ
Абсорбция и десорбция — массообменные процессы, составляющие основу абсорбционного разделения нефтяных и природных газов. Абсорбционный метод разделения углеводородных газов применяется в промышленности для извлечения газового бензина и жидких газов (пролан-бутановая смесь).
Физическая сущность абсорбции и десорбции заключается в достижении равновесия между взаимодействующими потоками газа и жидкости. Достижение состояния равновесия в системе «газ - жидкость» зависит от диффузии (переноса) вещества из одной фазы в другую. Движущая сила диффузии определяется разностью парциальных давлений извлекаемого компонента в газовой и жидкой фазах. Если парциальное давление компонента в газовой фазе выше, чем в жидкой, то происходит процесс абсорбции (поглощение газа жидкостью) и наоборот, если парциальное давление извлекаемого компонента в газовой фазе ниже, чем в жидкой, то происходит десорбция (выделение газа из жидкости).
При десорбции многокомпонентных смесей жидкость и газ в аппарате (по крайней мере на теоретической тарелке) находятся в состоянии фазового равновесия— в том смысле, что жидкость кипит, а пар является насыщенным. При этом температура жидкости на каждой тарелке или в каждой точке аппарата определяется давлением и составом [3,4].
При абсорбции этого нет: температура от давления не зависит и может быть выбрана в некоторых пределах.
На газоперерабатывающих заводах абсорбцию и десорбцию проводят в аппаратах тарельчатого и насадочного типов. При наличии технологического контура «абсорбер — десорбер» поглощение из газа соответствующих компонентов происходит в абсорбере, а выделение их — в десорбере. Извлеченные из насыщенного абсорбента углеводороды получают из верхней части десорбера, а регенерированный абсорбент отводят из его нижней части и подают в абсорбер для повторного использования.
Процесс абсорбции углеводородных газов сопровождается выделением тепла, поэтому температура в нижней части абсорбера несколько выше, чем в верхней. При абсорбции природного газа (с содержанием метана 85-95%) разница между температурами верха и низа абсорбера составляет 5-8 °С. При абсорбции заводских газов эта разница увеличивается в несколько раз.
Регенерация абсорбента в десорбере сопровождается подводом тепла в аппарат, поэтому разница между температурой верха и низа десорбера составляет несколько десятков градусов.
Назначение установки и сведения о технологическом процессе
Полное наименование производственного объекта - абсорбционно-газофракционирующая установка (АГФУ-1) - предназначена для сбора, компремирования жирных газов, стабилизации рефлюксов и бензинов термических крекингов, бензинов с установок 21-10, ЛЧ-24-7, факельных конденсатов, конденсата прямогонного газа.
Производительность АГФУ-1 составляет 350 тыс.т/год по газу.
Номинальная производительность блока ректификации по сырью составляет 690 тыс.т/год
В состав установки входят следующие блоки:
‒ блок сбора и компремирования жирных газов;
‒ блок ректификации бензинов термических крекингов, бензинов с установок 21-10, ЛЧ-24-7, рефлюксов с установок ТК-2,3, 22-4, Л-35-11/1000, «Жекса», ОАО «УНПЗ», факельных конденсатов, конденсата прямогонного газа;
‒ блок теплоносителя – дизельное топливо;
‒ блок сбора и компремирования прямогонного и углеводородных газов;
‒ блок фракционирования фракции нк-80°с (ДИП);
‒ блок деизогексанизации (ДИГ);
‒ блок теплоносителя АМТ-300.
Продуктами установки являются [1]:
– рефлюкс стабилизации;
– пропан–пропиленовая фракция;
– фракция широкая легких углеводородов (при простое ГФУ);
– бутан–бутиленовая фракция;
– газовый бензин;
– сухой газ.
Рефлюкс стабилизации используется в качестве сырья на ГФУ для дальнейшего фракционирования. Пропан–пропиленовая фракция используется в качестве сырья объекта 1/1.
При остановке на ремонт ГФУ на блоке №1 вырабатывается широкая фракция легких углеводородов, которая направляется в качестве сырья на другие нефтеперерабатывающие предприятия.
Газовый бензин, вырабатываемый на блоках №1 и №2 используется в качестве компонентов автомобильного бензина, либо в качестве сырья производства ароматических углеводородов. Сухой газ после очистки от сероводорода на установке замедленного коксования используется на заводе в качестве топливного газа, ББФ используется в качестве сырья установки 29/3.
На рисунке 1.1 приведена принципиальная схема АГФУ для фракционирования жирного газа и стабилизации бензина каталитического крекинга (на схеме не показаны блоки сероочистки, осушки, компрессии и конденсации) [1].
Для деэтанизации газов каталитического крекинга на установках АГФУ используется фракционирующий абсорбер 1. Он представляет собой комбинирован-ную колонну абсорбер–десорбер. В верхней части фракционирующего абсорбера происходит абсорбция, т. е. поглощение из газов целевых компонентов (Сз и выше), а в нижней – частичная регенерация абсорбента за счет подводимого тепла. В качестве основного абсорбента на АГФУ используется нестабильный бензин каталитического крекинга. Для доабсорбции унесенных сухим газом бензиновых фракций в верхнюю часть фракционирующего абсорбера подают стабилизирован-ный (в колонне 4) бензин. Абсорбер оборудован системой циркуляционных орошений для съема тепла абсорбции (на рисунке 1 не показана). Тепло в низ абсорбера подают с помощью "горячей струи". С верха фракционирующего абсорбера 1 выводят сухой газ (C1–С2), а с низа вместе с тощим абсорбентом выводят углеводороды Сзи выше.
1 – фракционирующий абсорбер; 2 – стабилизационная колонна; 3 –пропановая колонна; 4 – бутановая колонна; I – очищенный жирный газ; II – нестабильный бензин; III – сухой газ; IV– пропан–пропиленовая фракция; V– бутан – бутиленовая фракция; VI– стабильный бензин
Рисунок 1.1 – Принципиальная схема абсорбционно–газофракционирующей установки (АГФУ)
Деэтанизированный бензин, насыщенный углеводородами Сз и выше, после подогрева в теплообменнике направляют в стабилизационную колонну 2, нижним продуктом которой является стабильный бензин, а верхним – головка стабилизации. Из нее (иногда после сероочистки) в пропановой колонне 3 выделяют пропан–пропиленовую фракцию. Кубовый продукт пропановой колонны разделяют в бутановой колонне 4 на бутан–бутиленовую фракцию и остаток (Сз и выше), который объединяют со стабильным бензином. Газофракционирование – процесс разделения смеси углеводородных газов на составляющие компоненты путем ректификации [1,2]. Сырье, перерабатываемое на газофракционирующих установ-ках, различается по химическому составу и агрегатному состоянию [1.2]. Углеводородный состав сырья и содержание в нем примесей зависят от его происхождения и способа получения [2].
Патентная проработка
Cтабилизация бензина путем удаления из него газов путем фракционирования [7]. Изобретение касается способа переработки бензиновых фракций, включающего подачу нестабильных бензиновых фракций в колонну стабилизации бензина, разделение их на фракции -головку стабилизации и остаток стабилизации, подачу головки стабилизации на газофракционирующую установку с получением газовых компонентов.
Рисунок 1.3 – Схема абсорбционно-газофракционирующей установки
Насыщенный абсорбент из нижней части абсорбционной колонны подают в блок стабилизации бензина, куда также поступают бензиновые фракции, при этом углеводородные газы из блока стабилизации бензиновых фракций и насыщенного абсорбента отводят в абсорбционную колонну, перед подачей в колонну стабилизации бензина бензиновые фракции в смеси с насыщенным абсорбентом нагревают за счет передачи тепла от остатка стабилизации, отводимого с колонны стабилизации в качестве товарного бензина, часть остатка стабилизации направляют в абсорбционную колонну для поглощения пропан-бутановой фракции из углеводородных газов низкого давления с последующей подачей насыщенного абсорбента в колонну стабилизации бензина, а другую часть остатка стабилизации отводят в качестве товарного бензина. Технический результат - обеспечение требуемой степени стабилизации бензина, уменьшение энергопотребления, снижение потери бензиновых фракций и сжиженного газа.
По патенту РФ 2275223 [7] получение пропана за счет разделения нестабильного углеводородного конденсата, получаемого при переработке углеводородных газов, с выходом в качестве конечных продуктов широкой фракции легких углеводородов (ШФЛУ) и пропановой фракции, и может быть использовано на предприятиях газовой и нефтяной промышленности.
Рисунок 1.4 – Схема разделения нестабильного углеводородного конденсата
Установка включает колонну-деэтанизатор с подогревателем низа и узлом орошения верха, отводами газа деэтанизации в верхней части и стабилизированного конденсата в нижней части. Средняя часть укрепляющей секции колонны-деэтанизатора снабжена отводом жидкости с тарелки, соответствующей требуемой концентрации пропановой фракции, который соединен с верхней частью колонны получения пропана. Колонна получения пропана представляет собой стриппинг-колонну с подогревателем низа колонны, отводом пропана в нижней части и отводом паров углеводородов с верха колонны, который соединен с верхней частью колонны-деэтанизатора. Установка позволяет снизить капитальные затраты за счет сокращения количества и размеров используемого оборудования и снизить энергозатраты [7].
Известно получение пропановой фракции с содержанием пропана не менее 96 мас. % на абсорбционно-газофракционирующей установке [31], на которой может перерабатываться жирный газ, поступающий с установок первичной переработки нефти AT и АВТ, гидрокрекинга, каталитического риформинга и некоторых других. Абсорбционно-газофракционирующая установка включает фракционирующий абсорбер, стабилизационную колонну с узлом орошения верха колонны и подводом тепла в низ колонны, верх которой подключен к колонне получения пропана с подогревателем низа и узлом орошения верха колонны, с верха которой выводится пропан. Сырьем для колонны получения пропана является сжиженный газ (пропан, бутан, пентан), выводимый с верха стабилизационной колонны.
Общими признаками данного технического решения и предлагаемой установки являются наличие колонны с подогревателем низа и узлом орошения верха, служащей для получения сырья для колонны получения пропана, и наличие непосредственно колонны получения пропана с подогревателем низа и отводом пропана.
Однако рассматриваемая установка не обладает высокой эффективностью с точки зрения получения пропана, т.к. не позволяет получать пропан высокой чистоты. Концентрация пропана в готовом продукте зависит от степени деэтанизации насыщенного абсорбента во фракционирующем абсорбере. При высокой степени деэтанизации в абсорбере значительно снижается извлечение ШФЛУ из газа, поэтому степень деэтанизации насыщенного абсорбента ограничивается определенными пределами (требованиями ТУ на ШФЛУ). Кроме того, к недостаткам такой установки получения пропана можно отнести ее сложность, использование полной ректификационной колонны получения пропана с подогревом низа и орошением верха колонны и связанные с этим высокие энергозатраты.
Обычно получение пропана на газоперерабатывающих заводах производится в минимальном количестве, достаточном для восполнения потерь в пропановой системе охлаждения и других собственных нужд завода, на отдельных установках получения пропана из ШФЛУ, вырабатываемой на основном производстве (чаще всего, на установках НТК - низкотемпературной конденсации газа) после деэтанизации нестабильного конденсата, полученного при переработке газа. Такой традиционной установкой, наиболее близкой к заявляемому решению, является установка получения пропана высокой чистоты из ШФЛУ [32], которая включает насадочную колонну-деэтанизатор с подогревом низа и узлом орошения верха колонны-деэтанизатора, отводом газа деэтанизации в верхней части и стабилизированного конденсата в нижней части, нижняя часть колонны-деэтанизатора подключена к ректификационной колонне получения пропана с подогревателем низа колонны и отводом пропана с верха колонны, а конденсата - с низа колонны для последующей подачи в поток ШФЛУ.
Общими признаками известного и предлагаемого решений являются наличие колонны-деэтанизатора с подогревателем низа и узлом орошения верха колонны-деэтанизатора, отводами газа деэтанизации в верхней части и стабилизированного конденсата в нижней части, а также колонны получения пропана с подогревателем низа колонны и отводом пропана.
Недостатком такой установки является сложность технологической схемы, обусловленная использованием полной ректификационной колонны получения пропана, снабженной узлом орошения верха колонны и подогревателем низа. Кроме того, сырьем установки служит ШФЛУ, а при использовании на такой установки в качестве сырья колонны-деэтанизатора нестабильного конденсата увеличиваются энергетические затраты, поскольку в колонне-деэтанизаторе придется отпаривать больше легких углеводородов (метана и этана) из большего количества нестабильного конденсата, чем ШФЛУ. Увеличатся в этом случае и габариты колонны-деэтанизатора, узла орошения и подогревателя низа колонны-деэтанизатора, а следовательно, и капитальные затраты.
Техническая задача достигается тем, что в установке получения пропана из углеводородного конденсата, включающей колонну-деэтанизатор с подогревателем низа и узлом орошения верха колонны-деэтанизатора, отводами газа деэтанизации в верхней части и стабилизированного конденсата в нижней части и колонну получения пропана с подогревателем низа колонны и отводом пропана, средняя часть укрепляющей секции колонны-деэтанизатора снабжена отводом жидкости с тарелки, соответствующей требуемой концентрации пропановой фракции, который соединен с верхней частью колонны получения пропана, представляющей собой стриппинг-колонну с отводом пропана в нижней части и отводом паров углеводородов с верха колонны, который соединен с верхней частью колонны-деэтанизатора.
Наличие в средней части укрепляющей секции колонны-деэтанизатора отвода жидкости с тарелки, соответствующей требуемой концентрации получаемой пропановой фракции, позволяет подать в колонну получения пропана этан-пропан-бутановую смесь требуемой концентрации, которую необходимо отпарить только от лишнего этана. В процессе деэтанизации конденсата в жидкости на тарелках укрепляющей секции колонны-деэтанизатора растет содержание этана и резко снижается содержание бутанов и более тяжелых углеводородов, вплоть до почти полного их отсутствия. При этом в этой жидкости всегда имеется пропан, содержание которого зависит от температуры орошения и давления в колонне. При выведении этой жидкости из колонны-деэтанизатора и отпарке в стриппинг-колонне от лишнего этана получают пропановую фракцию высокой концентрации. В зависимости от тарелки отбора жидкости из колонны-деэтанизатора можно регулировать в пропановой фракции содержание бутанов, т.е. получать пропановую фракцию различной концентрации.
Соединение отвода жидкости с тарелки колонны-деэтанизатора, соответствующей требуемой концентрации получаемой пропановой фракции, с верхней частью колонны получения пропана и соединение отвода паров углеводородов из колонны получения пропана с верхней частью колонны-деэтанизатора позволяет направить для получения пропана сырье с требуемым содержанием бутанов и избежать использования полной ректификационной колонны получения пропана, в результате чего сокращается набор используемого оборудования. Это позволяет использовать небольшую по размерам и простую по оснащенности стриппинг-колонну с отводом пропана в нижней части и отводом паров углеводородов с верха колонны, который соединяют с верхней частью колонны-деэтанизатора для получения заданного количества пропана с необходимой чистотой (до 99% массовых).
Таким образом, заявляемая конструкция установки получения пропана из углеводородного конденсата позволяет добиться получения заданного количества пропана требуемой чистоты при упрощении конструкции, сокращении количества оборудования и его габаритов. Кроме того, для получения пропана наряду с ШФЛУ может использоваться нестабильный углеводородный конденсат с большим содержанием легких углеводородов (метана, этана), чем в ШФЛУ.
Обоснование выбора темы
Объектом исследования выпускной квалификационной работы является абсорбционно-газофракционирующая установка выделения бутан–бутиленовой фракции блока ректификации низкокипящих углеводородов. Во введение и литературном обзоре показано, что схема ректификационной установки и последовательность выделения отдельных компонентов зависят от состава исходной смеси, требуемой чистоты продуктов и количества получаемых фракций.
Нефтехимическая промышленность большое значение предает получению таких многотоннажных промышленных продуктов как бензин, легкие и ароматические углеводороды, применяемые в качестве сырья на нефтеперерабатывающих предприятиях, топливный газ, ББФ и т.д. Процесс получения данных продуктов проходит при большом разнообразии рабочих условий, температур, давлений, сред. Сосуды и аппараты работают в тяжелых условиях (под избыточным давлением).
Производительность установки во многом зависит от правильно подобранного оборудования и его компановки. Грамотный расчет, точное проектирование оказывают большое влияние на экономическую эффективность процесса и стоимость и готовой продукции.
Основной целью выпускной квалификационной работы является проектирование колонного и теплообменного оборудования, на которое возлагается одна из основных ролей процесса.
В связи с этим была поставлена задача провести технологический анализ теплообменного оборудования и колонных аппаратов, выполнить необходимые прочностные расчеты, рассмотреть безопасность и экологичность проекта абсорбционно-газофракционирующей установки выделения бутан–бутиленовой фракции блока ректификации низкокипящих углеводородов.
Технологический раздел
Дата добавления: 2018-06-27; просмотров: 1959; Мы поможем в написании вашей работы! |
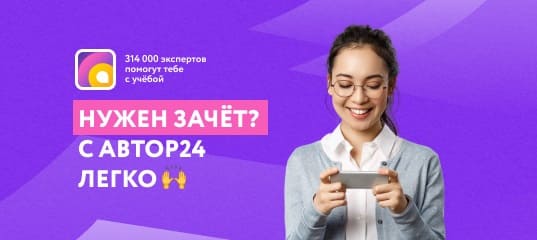
Мы поможем в написании ваших работ!