Упрочнение при холодной деформации
Одним из наиболее распространенных методов получения изделий с высокой (более 1600 – 2000 МПа) прочностью является холодное волочение проволоки с содержанием 0,8 – 0,9 % С. При этом для получения больших степеней обжатия структура стали должна представлять феррито – карбидную смесь тонкопластинчатого строения. Такая структура может быть получена при помощи патентирования или термообработки.
Холоднодеформированная патентированная проволока широко используется для изготовления пружин, в которых применяют деформационное старение для повышения предела текучести и релаксационной стойкости.
Проволока особо высокой прочности (более 3500 МПа) применяется для изготовления тросов, прядей и других изделий, работающих в основном при осевых нагрузках.
Прочность холоднодеформированной проволоки со структурой тонкопластинчатого сорбита определяется содержанием углерода и азота, а также степенью деформации при волочении.
Существует формула, связывающая временное сопротивление проволоки с содержанием углерода, азота и степенью деформации:
sв = 315 + 720(С) + 17,68 ´ 103 (N) + 176 lne
Где:
e - истинная деформация проволоки при волочении.
Для получения проволоки сверхвысокой прочности необходимо применение при волочении очень больших деформаций (98 – 99 % и выше). Такая степень деформации может быть получена только на проволоке диаметром 0,1 мм и меньше.
Содержание углерода в сверхвысокопрочной проволоке должно быть максимально возможным, при этом в структуре не должно быть обрывов цементитной сетки. Таким образом, оптимальное содержание углерода в такой проволоке близко к эвтектоидному (0,80 – 0,95 %).
|
|
Для получения сверхвысокопрочной проволоки применяют особо чистые по неметаллическим включениям, примесям и газам стали, в том числе полученные вакуумным способом выплавки. Шихтовые материалы для производства подобного вида проволоки должны обладать повышенной чистотой. Также положительное влияние повышенной чистоты стали проявляется в возможности получения больших степеней обжатия при волочении и, соответственно более высокого временного сопротивления по сравнению со сталями обычного способа выплавки. Прирост временного сопротивления холоднотянутой проволоки из сталей повышенной чистоты по сравнению с обычными сталями может достигать 1000 МПа. На холоднотянутой проволоке из сталей повышенной чистоты на диаметре заготовки 0,08 – 0,10 мм достигнут sв = 4800 – 5000 МПа. При этом пластические свойства остаются на достаточно высоком уровне.
Дополнительное деформационное старение при 150 – 200 оС практически не изменяет временного сопротивления сверхвысокопрочной проволоки, но при этом повышается предел текучести и снижается пластичность.
|
|
Легирующие элементы, за исключением кобальта и никеля, понижают пластичность холоднотянутой патентированной проволоки и поэтому для ее производства нежелательны. Легирование кобальтом в количестве 2,0 – 4,0 % ускоряет распад переохлажденного аустенита при патентировании и увеличивает пластичность проволоки. Более высокие содержания кобальта могут вызывать графитизацию стали и падение прочностных свойств холоднотянутой проволоки.
Временное сопротивление холоднотянутой сверхпрочной проволоки снижается при дополнительной деформации другого вида (кручение, изгиб). При этом падение временного сопротивления может составлять от 5 до 20 %.
Получение тонкопластинчатой феррито – карбидной структуры возможно и при скоростном отпуске (электроотпуске) закаленной стали. При скоростном отпуске закаленной стали в интервале 500 – 650 оС можно получить пластинчатые выделения цементита, такая структура обладает хорошей пластичностью и значительно упрочняется при волочении. Достоинством такого метода является возможность получения высокопрочной проволоки из легированных сталей типа 30ХГСА, 38ХА, 15ХА. При этом проволока выдерживает высокие степени обжатия (более 80 %) и дает sВ > 2000 МПа на диаметре 1,2 мм при достаточно высокой пластичности.
|
|
Стали со сверхмелким зерном
Одним из способов значительного увеличения прочности является получение сверхмелкозернистых сталей (диаметр зерна порядка 10 мкм и меньше). Получение сверхмелкого аустенитного зерна, а при закалке резкое измельчение мартенситных пластин, можно осуществить при скоростной аустенитизации с применением специальных методов сверхскоростного нагрева и очень коротких выдержек при температурах, не намного превышающие критические. Достоинством подобной обработки является одновременное повышение вязкости разрушения и ударной вязкости при высокой прочности.
В высокопрочных сталях со структурой сверхмелкого мартенсита увеличение предела текучести может достигать 10 %. Такие стали характеризуются высокой конструктивной прочностью, т.е. сочетанием высокой прочности, вязкости разрушения и ударной вязкости. Кроме того, сверхмелкозернистая сталь имеет высокое сопротивление усталости.
К недостаткам таких сталей относится трудность, а иногда и невозможность, получения зерна путем сверхбыстрой аустенитизации и закалки в больших сечениях, а также склонность таких сталей к разупрочнению при нагреве.
|
|
В сверхмелкозернистых сталях и сплавах при определенных температурах и скоростях нагружения можно получить аномально высокие значения относительного удлинения.
ПНП – стали
Высокопрочные стали с пластичностью, наведенной превращением. Принцип их получения и способы упрочнения состоят в следующем.
Соответствующим подбором легирующих элементов снижают мартенситные точки Мн и МД ниже комнатной температуры. Таким образом, после закалки такие стали имеют аустенитную структуру. Для получения повышенных прочностных свойств стали подвергают пластической деформации в интервале температур 250 – 550 оС (ниже температуры рекристаллизации) с большими степенями обжатия (до 80 %). При этом мартенситные точки Мн и МД повышаются и точка МД становится выше комнатной температуры (точка Мн остается ниже комнатной температуры). Повышение мартенситной точки МД может быть усилено посредством легирования стали мартенситообразующими элементами, выделения карбидов при пластической деформации, изменения состава мартенсита и дополнительным повышением мартенситных точек Мн и МК . после охлаждения стали от температур теплого деформирования сталь сохраняет структуру деформированного аустенита, но этот аустенит становится метастабильным по отношению к пластической деформации при комнатной температуре. Деформация такого аустенита приводит к образованию мартенсита деформации, что сопровождается увеличением прочностных свойств и значительным ростом относительного удлинения.
ПНП – стали легируют такими элементами как марганец, кремний, молибден, хром, ванадий, вольфрам, никель. Содержание углерода в высокопрочных ПНП – сталях составляет 0,3 %.
Для получения повышенных прочностных свойств ПНП – стали подвергают дополнительной холодной пластической деформации с развитием g a - превращения в процессе деформации. При этом прочностные свойства стали продолжают расти, а пластичность уменьшается.
Для некоторых ПНП – сталей применяют дополнительное охлаждение и деформацию при низких температурах (до – 196 оС) с последующим отпуском при 350 – 400 оС, при этом частично получают мартенсит деформации. При такой обработки можно получить условный предел текучести более 2000 МПа и относительное удлинение 20 – 25 %.
Достоинством ПНП – сталей являются высокие значения вязкости разрушения, высокое сопротивление усталостному и коррозионному разрушению.
К недостаткам ПНП – сталей относятся значительные трудности, связанные с осуществлением большой пластической деформации при теплой деформации, трудность контроля состава, ограничения по сортаменту.
ПНП – стали используют для производства ответственных деталей, высокопрочных крепежных изделий, а также высокопрочной проволоки и тросов.
Дата добавления: 2018-06-27; просмотров: 426; Мы поможем в написании вашей работы! |
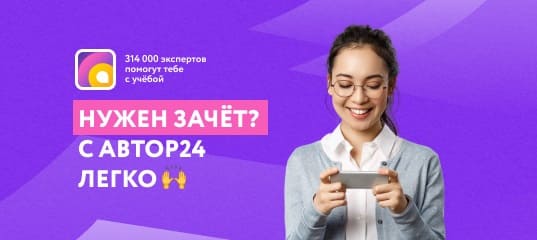
Мы поможем в написании ваших работ!