Металлы, обрабатываемые в кабельной промышленности
Министерство образования и науки Российской Федерации
Федеральное агентство по образованию
Пермский государственный технический университет
Т.В. КОСТЫГОВА
ТЕХНОЛОГИЯ ПРОИЗВОДСТВА ПРОВОДОВ
Утверждено Редакционно-издательским советом университета
в качестве конспекта лекций для студентов специальности 180300
«Электроизоляционная, кабельная и конденсаторная техника»
очной и заочной форм обучения
Пермь 2006
УДК 621.315
К72
Рецензенты:
доктор технических наук, профессор Пермского
государственного технического университета Л.А. Ковригин;
генеральный директор ОАО «Камкабель»
кандидат технических наук В.В. Смильгевич
Костыгова Т.В.
К72 Технология производства проводов: конспект лекций / Т.В. Костыгова; Перм. гос. техн. ун-т. – Пермь, 2006. – 96 с.
Рассмотрены особенности производства проволоки. Изложена теория производства эмалированных проводов и технология изготовления обмоточных проводов с другими видами изоляции.
УДК 625.768.5
Ó Пермский государственный
технический университет, 2006
ОГЛАВЛЕНИЕ
Введение….…………………………………..…………………..….. | 5 |
1. Производство проволоки ………………………………………... | 6 |
1.1. Металлы, обрабатываемые в кабельной промышленности .... | 6 |
1.2. Изготовление медной и алюминиевой катанки …..…………. | 10 |
1.3. Нагрев металла перед прокаткой ……………………………… | 13 |
1.4. Технология прокатки …………………………………………... | 15 |
1.4.1. Калибровка валков ...………………………………………. | 15 |
1.4.2. Рабочие клети прокатных станов ………………………… | 16 |
1.4.3. Прокатные станы …………………………………………... | 17 |
1.5. Метод непрерывного литья и прокатки ………………………. | 20 |
1.6. Метод «дип-форминг» …………………………………………. | 21 |
1.7. Травление катанки ……………………………………………... | 22 |
1.8. Скальпирование медной катанки ……………………………… | 25 |
1.9. Волочение проволоки ………………………………………….. | 27 |
1.10. Оборудование для волочения проволоки …………………… | 30 |
1.11. Волочильный инструмент ……………………………………. | 34 |
1.12. Отжиг медной и алюминиевой проволоки ………………….. | 36 |
1.13. Качество продукции и виды брака …………………………... | 38 |
2. Производство обмоточных проводов …………………………… | 39 |
2.1. Классификация обмоточных проводов ………………………. | 39 |
2.2. Проводниковые материалы, применяемые в производстве обмоточных проводов ………………………………………………… | 40 |
3. Производство эмалированных проводов ……………………….. | 42 |
3.1. Лаки для эмалирования проволоки …………………………… | 42 |
3.2. Способы наложения эмалевой изоляции …………………….. | 44 |
3.3. Удаление растворителя из эмаль-лака …………………….…. | 47 |
3.3.1. Расчет концентрации растворителя для случая, когда скорость процесса определяется диффузией растворителя внутри пленки (Bi > 1) ………………………………………………………… | 48 |
3.3.2. Расчет концентрации растворителя для случая, когда скорость процесса определяется внешним массообменом (Bi < 1) .. | 51 |
3.3.3. Условия образования газообразных включений на стадии удаления растворителя …………………………………………… | 54 |
3.4. Расчет процесса пленкообразования изоляции эмалированных проводов ………………………………………………………….. | 55 |
3.5. Условия возникновения газообразных включений на стадии пленкообразования ................................................................................. | 58 |
3.6. Расчет температуры эмалируемой проволоки ……………….. | 61 |
3.7. Агрегаты для эмалирования проволоки ………………………. | 65 |
3.7.1. Агрегаты для эмалирования проволоки диаметром 0,015–0,05 мм ………………………………………………………….. | 68 |
3.7.2. Агрегаты для эмалирования проволоки диаметром 0,05–0,45 мм …………………………………………………………………. | 70 |
3.7.3. Агрегаты для эмалирования проволоки диаметром 0,4–2,5 мм …………………………………………………………………… | 71 |
3.7.4. Устройство катализаторов ………………………………… | 73 |
3.8. Особенности эмалирования проводов из расплава смол ……. | 74 |
4. Производство обмоточных проводов…………………………… | 76 |
4.1. Обмоточные провода с волокнистой, бумажной и пленочной изоляцией ………………………………………………………………. | 76 |
4.1.1. Обмоточные машины для наложения изоляции из натуральных и синтетических волокон …………………………………… | 78 |
4.1.2. Обмоточные машины для наложения бумажной и пленочной изоляции ………………………………………………………. | 81 |
4.1.3. Обмоточные машины для наложения стекловолокнистой изоляции ……………………………………………………………….. | 84 |
4.2. Подразделенные и транспонированные обмоточные провода | 87 |
4.3. Обмоточные провода со спекаемой пленочной изоляцией …. | 89 |
4.4. Обмоточные провода с пластмассовой изоляцией ………….. | 90 |
4.5. Обмоточные провода со сплошной стеклянной изоляцией и оборудование для их производства …………………………………... | 92 |
4.6. Обмоточные провода с гибкой керамической изоляцией …… | 93 |
Список литературы …………………………………………………. | 95 |
|
|
|
|
|
|
ВВЕДЕНИЕ
|
|
Кабельная продукция используется во многих отраслях промышленности – в электроэнергетике, машиностроении, строительстве, сельском хозяйстве и на транспорте.
Характер использования этой продукции определяет номенклатуру кабельных изделий, которая очень обширна и включает в себя более 20 000 изделий.
Технологию изготовления кабельного изделия можно условно разделить на три основных процесса:
– получение токопроводящей жилы (ТПЖ), обычно в виде проволоки необходимого сечения с требуемыми свойствами;
– изготовление изоляции;
– изготовление собственно изделия (наложение изоляционных и различных защитных покрытий на ТПЖ и соответствующий монтаж изделия).
Производственный цикл современных кабельных заводов начинается с металлообрабатывающих цехов: прокатного и волочильного.
Основными исходными материалами кабельной промышленности являются металлические слитки (медь, алюминий, свинец, сплавы) или катанка, изоляционные материалы (лаки, бумага, пластмасса, каучук и др.) и защитные материалы (битум, мел, стальная лента и др.).
Слитки поступают в прокатный цех, нагреваются в специальных печах до необходимой температуры и прокатываются за несколько проходов на прокатном стане. Продукция прокатного цеха – медная или алюминиевая катанка, подкат или заготовка для шин и коллекторной меди – передается в волочильный цех.
В волочильных цехах из катанки получают проволоку. Часть продукции волочильных цехов является готовой кабельной продукцией: троллейные провода, шины, коллекторная медь. Остальная проволока передается в цеха, где производятся наложение изоляции, скрутка и наложение защитных покрытий [2]. Расширение производства электрических машин, аппаратов и приборов требует увеличения выпуска обмоточных проводов. Особое место занимает производство эмалированных проводов, в основном нагревостойких.
Одним из важных направлений в этой области является развитие производства тончайших проводов, что связано с микроминиатюризацией радиотехнической и электронной аппаратуры.
Особое внимание на кабельных заводах уделяется совершенствованию технологии производства, применяемого технологического оборудования, внедрению методов испытаний, позволяющих прогнозировать надежность выпускаемой продукции.
ПРОИЗВОДСТВО ПРОВОЛОКИ
Металлы, обрабатываемые в кабельной промышленности
Металлы подразделяются на черные и цветные. К первым относятся железо и его сплавы с углеродом – сталь, чугун. Все остальные металлы – медь, олово, свинец, алюминий и др. – цветные.
Свойства некоторых цветных металлов, применяемых в кабельной промышленности, приведены в табл. 1.1.
Таблица 1.1
Свойства цветных металлов
Свойства | Медь | Алюминий | Константан | Манганин |
Плотность, г/см3 | 8,9 | 2,7 | 8,9 | 8,4 |
Предел прочности при растяжении в мягком состоянии, кгс/мм2 | 22–24 | 8,0 | 40–50 | 50–55 |
Удельное электрическое сопротивление при 20 ºС, Ом·мм2 /м | 0,017 | 0,028 | 0,48 | 0,43 |
Температура плавления, ºС | 1083 | 658,7 | 1260 | 1010 |
Основной проводниковый материал – медь. По электропроводности она превосходит все другие металлы (за исключением серебра), что позволяет обеспечивать минимальные габариты обмоток электрических машин, аппаратов и приборов.
Чистота применяемой меди имеет большое значение. Различные примеси даже в ничтожных количествах резко снижают проводимость меди и ухудшают ее технологические свойства.
Кислород находится в меди в виде закиси Cu2O, которая снижает пластичность меди, создает хрупкость при перегибах и повышает предел прочности. Медь, содержащая больше 0,1 % кислорода, легко разрушается при горячей прокатке, плохо поддается пайке. При нагреве в восстановительной атмосфере медь, содержащая кислород, становится красноломкой, т.е. хрупкой, и растрескивается. Объясняется это «водородной болезнью» меди. При высокой температуре (800–970 ºС) водород, окись углерода и метан, которые входят в атмосферу печи, восстанавливают закись меди. Происходят реакции, при которых образуются водяные пары и углекислота:
Cu2O + H2 = 2Cu + H2O,
Cu2О + CO = 2Cu + CO2.
Эти газы выходят на поверхность слитка и образуют микроскопические трещины в поверхностном слое металла. Через трещины восстановительные газы постепенно проникают в более глубокие слои слитка. Это в конечном итоге может привести к разрушению слитков.
Одной из вреднейших примесей в меди является висмут. Он вызывает красноломкость и хладноломкость. Для горячей прокатки допускается медь с содержанием висмута не более 0,005 %. При содержании висмута 0,25 % медь крошится в порошок.
Фосфор присутствует в меди как остаток фосфористого раскислителя. Он обладает значительным химическим сродством к кислороду и поэтому добавляется в медь только в качестве специальной присадки для раскисления. При присадке фосфора к меди в количестве, большем, чем необходимо для связывания кислорода, избыток фосфора образует твердый раствор с медью, что снижает ее проводимость.
Свинец также является вредной примесью. Он вызывает разрушение меди при горячей обработке, его содержание не должно превышать 0,005 %.
Железо понижает электропроводимость меди, его содержание в меди должно быть не более 0,005 %. При содержании в меди 0,05 % железа проводимость ее уменьшается на 15 %. Под влиянием железа измельчается структура, задерживается рекристаллизация, повышается прочность и ухудшаются антикоррозийные свойства меди.
Резко снижает пластичность меди при горячей и холодной прокатке сера. В меди, идущей для кабельной продукции, серы содержится не более 0,002 %.
Примеси оказывают неблагоприятное влияние на механические и электрические свойства меди, поэтому медь с содержанием примесей более 0,1 % в кабельном производстве вообще не применяется.
Лучшими параметрами с точки зрения применения в производстве обмоточных, в первую очередь эмалированных, проводов обладает бескислородная медь. Она превосходит обычную медь по пластичности и обеспечивает получение проволоки с лучшим качеством поверхности.
В соответствии с ГОСТ 859–78 медь по химическому составу разделяется на несколько марок. В кабельной промышленности используется только медь повышенной чистоты марок не ниже М1, М00к, М0к, М0ку, М00б, М0б, М1к, М1б, М1у. Не применяется медь марки М1ф с повышенным содержанием фосфора (0,012–0,06 %), а также М1р (раскисленная фосфором и содержащая его в количестве 0,002–0,012 %).
Индексы при марках имеют следующие значения: к, ку – катодная медь; б – бескислородная медь; у – катодная переплавленная; р, ф – раскисленная.
Цифры 00, 0 и 1 определяют содержание меди. Наибольшее содержание меди (99,9–99,99 %) имеют марки М00к, М00б.
На кабельные заводы медь поступает в слитках (вайербарсах) трапецеидальной формы со скошенными концами, а бескислородная – в слитках прямоугольной формы с закруглениями на углах. Формы медных слитков показаны на рис. 1.1.
|
|

Рис. 1.1. Форма медных слитков (ГОСТ 193–79): типа СВ (а), CH и CC (б)
Трапецеидальные слитки отливаются в горизонтально расположенные изложницы, открытые сверху, так что поверхность меди не защищена сверху от окисления и контактирует с воздухом. В результате при кристаллизации поверхность слитка становится морщинистой, «рожистой». Это связано с тем, что насыщенный кислородом слой меди имеет большую усадку при остывании, чем основная масса слитка. Наличие «рожистой» поверхности затрудняет получение при последующих операциях прокатки и волочения медной проволоки с высококачественной поверхностью. Поэтому для получения эмалированных проводов используются строганные слитки, у которых верхний слой снимается на глубину 8–12 мм. По химическому составу медные слитки горизонтальной отливки должны соответствовать меди не ниже марки М1, причем содержание кислорода не должно превышать 0,06 %.
Бескислородная медь, поставляемая в слитках вертикального исполнения, не имеет сильно окисленной поверхности. По химическому составу она должна соответствовать меди не ниже марки М0б. Слитки вертикальной отливки более однородны по содержанию кислорода и пористости, по механическим свойствам.
В соответствии с ГОСТ 193–79 для кабельной промышленности выпускаются медные слитки следующих марок:
СВ – вертикальной непрерывной отливки;
СН – горизонтальной отливки, с неудаленной верхней поверхностью;
СС – горизонтальной отливки, с удаленной верхней поверхностью.
Размеры медных слитков приведены в табл. 1.2 [2].
Таблица 1.2
Размеры медных слитков, мм
Марка слитка | Длина L | Ширина В | Высота Н |
СН | 1372 | 98 | 92–102 |
СС | 1360 | 110 | 100 |
СВ-I | 1400 | 100 | 100 |
СВ | 2800 | 100 | 100 |
Вторым по значению металлом в производстве обмоточных и эмалированных проводов является алюминий.
Алюминий – металл серебристо-белого цвета, обладает низким удельным весом, высокой проводимостью. В чистом виде алюминий имеет очень хорошие пластические свойства. Отличительной особенностью алюминия является хорошая коррозионная стойкость. Тонкая окисная пленка защищает металл от дальнейшего окисления. Железо и кремний снижают пластичность и проводимость алюминия (железо делает его хрупким и снижает его химическую стойкость, кремний упрочняет его).
Для производства обмоточных проводов применяется алюминий технической чистоты марок А5Е и А7Е по ГОСТ 11069–74. В нем содержание марганца не более 0,01 %, магния не более 0,02 %, мышьяка не более 0,015 %. В алюминии марки А5Е допускается содержание кремния не более 0,12 % и других примесей (титан, ванадий, марганец, хром) не более 0,01 %.
Удельное электрическое сопротивление алюминия в 1,62 раза выше, чем меди. Поэтому сечение алюминиевой проволоки с электрическим сопротивлением, равным сопротивлению медной проволоки, должно быть в 1,62 раза больше, а диаметр в 1,27 раза больше, чем сечение и диаметр медной проволоки. При этом алюминиевая проволока будет в два раза легче медной [1].
Алюминий поставляется в слитках с примерными размерами 100´100´2700 мм, весом до 76 кг. Однако в настоящее время для производства проводов в основном используется катанка, получаемая непосредственно из жидкого металла методом непрерывного литья и прокатки. Катанка поставляется в больших бухтах весом до 1500 кг.
Низкое удельное сопротивление меди, ее высокие механические характеристики, хорошая свариваемость, возможность пайки, способность подвергаться лужению, возможность покрытия ее серебром ставят медь на первое место в ряду других материалов. Но содержание меди в земной коре – около 0,1 %, а алюминия – 7,5 %, поэтому в связи с дефицитностью меди широко применяется алюминий.
Мягкие отожженные медь и алюминий идут на изготовление проволоки; полутвердые – на изготовление продукции, для которой необходима определенная механическая прочность; твердотянутые – на изготовление изделий, которым приходится выдерживать высокие механические нагрузки и которые не допускают никаких деформаций.
В кабельной промышленности находят также применение сплавы меди с элементами, позволяющими улучшить механические характеристики меди, сохранив удельную проводимость, близкую к проводимости чистой меди.
Медь с серебром (до 0,14 % Ag) используется при изготовлении коллекторных полос, медь с кадмием (0,7–1 %) – при изготовлении контактных проводов железных дорог, троллейбусных линий и т.д. [2].
Дата добавления: 2018-06-01; просмотров: 1014; Мы поможем в написании вашей работы! |
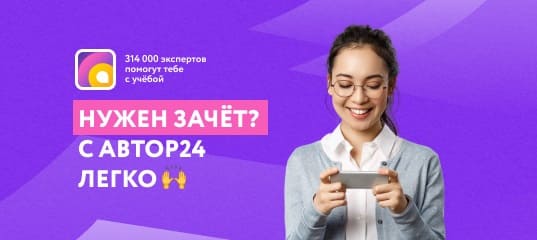
Мы поможем в написании ваших работ!