Технологическая схема производства латунированной проволоки.
Склад катанки>участок травления>грубое волочение>патентирование>среднее волочение>патентирование, латунирование>тонкое волочение
Со склада катанки заготовка поступает на участок травления. Травление может происходить несколькими способами: химически и механически. Затем проволока поступает на участок грубого волочения. Затем проволока идет на патентирование, где снимаются внутренние напряжения у улучшение структуры металла. Далее участок среднего волочения. Затем проволока идет на участок латунирования, где сначала происходит снятие внутренних напряжений, затем процесс нанесения тонкого слоя латуни. Латунный слой улучшает адгезию с резиной. Затем латунированная проволока идет на участок тонкого волочения, где проволока проходит последнее уменьшение диаметра. Продукция тонкого волочения может быть и готовым продуктом (проволока РМЛ), а также может и идти дальше на канатный участок, где происходит её свивка в металлокорд и канаты.
Для сокращения технологических операций в процессе производства проволоки применяют такой способ как объединение грубого волочения и среднего волочения в один процесс - грубо-среднее волочение. Это позволяет значительно экономить время при производстве проволоки, уменьшить затраты на оборудование тем самым снизить себестоймость продукции.
Латунированная проволока получила огромное распространение в различных областях. Эта проволока применяется для рукавов высокого давления, как заготовка для фибры. Также латунированная проволока идет на свивку металлокорда и канатов. Металлокорд применяется для армирования шин различных автомобилей. Начиная от шин легковых автомобилей и заканчивая крупногабаритными и сверхгабаритными шинами.
|
|
18. Дать определение понятию смазка. Перечислить виды смазки. Описать влияние смазки на процесс волочения. Проанализировать применение твердой смазки при производстве проволоки.
Смазка – это вещество, используемое для предотвращения задира, уменьшения и упорядочения износа взаимно перемещающихся поверхностей.
Технологическая смазка подразделяется на 3 вида: твёрдая смазка, жидкая смазка и консистентная смазка.
Твёрдая смазка – это мыло, представляющее собой соединение щелочных и щелочно- земельных металлов (Na,K) с жирными кислотами. Она применяется при сухом волочении проволоки грубого и среднего диаметра.
Жидкая смазка – это жидкое мыло. Наиболее часто используется при волочении тонкой, найтончайшей и микронной проволоки. Благодаря хорошей охлаждающей способности, эта смазка позволяет волочение на высоких скоростях.
|
|
Консистентная смазка изготавливается введением в животные, минеральные или растительные масла специальных загустителей.
Процесс волочения невозможен без применения смазочных материалов. Влияние смазки при волочении очень разнообразно, а конкретно: уменьшает внешнее трение, предотвращает прилипание металла к инструменту, препятствует контакту в местах отдельных неровностей, не только уменьшает внешнее трение, но и облегчает пластическую деформацию, рациональная смазка при волочении высоколегированной проволоки позволяет значительно увеличить суммарное обжатие и уменьшить число промежуточных термических обработок, обеспечивает однородность поперечного сечения металла на больших длинах, не допускается быстрая выработка канала волок, снижает температуру деформации, влияет на свойства деформированного металла, его характеристики, остаточные напряжения и коррозионные свойства.
Кроме сухого мыльного порошка, к твёрдым смазкам также относятся нефтяные продукты: парафин, воск. Смазкой такого типа обрабатывается проволока практически всех сталей. Парафин нашёл своё применение при волочении легированной стали. Также применяется пчелиный воск, который получил большее распространение при протяжке драгоценных металлов. Эти смазки наносятся путём погружения мотков в ванну с расплавом парафина или воска.
|
|
19. Дать определение понятию жидкая технологическая смазка при волочении. Перечислить способы нанесения жидкой смазки. Сравнить способы разбрызгивания и окунания. Проанализировать достоинства и недостатки жидкой смазки.
Жидкая смазка – это вещество (жидкое мыло), используемое для предотвращения задира, уменьшения и упорядочения износа взаимно перемещающихся поверхностей, наиболее часто используется при волочении тонкой, найтончайшей и микронной проволоки.
Существует два способа нанесения смазки на поверхность: окунанием и разбрызгиванием.
При окунании проволоки в ванну с жидкой смазкой обеспечивается тонкий ровный слой пленки на поверхности металла. В этом случае смазка проявляет свои объемные свойства. Для данного способа необходимо большое количество смазочной жидкости.
При разбрызгивании в узле машины создается смазочная атмосфера, путем ее разбрызгивания с помощью дождиков и движущихся частей машины. По сравнению с методом окунания требуется меньшее количество смазки. Смазка неравномерно распределяется по всему объему металла. Толщина в некоторых местах достигает лишь нескольких молекул. Из-за этого растет коэффициент трения, что приводит к росту напряжений в металле и износу обрабатывающего инструмента
|
|
Достоинствами жидкой сказки являются:
- значительное снижение коэффициента трения;
- улучшаются свойства охлаждения;
- увеличивает срок службы оборудования (уменьшая затраты на ремонт из-за износа)
Недостатки:
- низкая химическая стойкость;
- летучестью;
- возможностью загрязнения контактирующей с ними среды или рабочего пространства.
- необходимость применения герметичных корпусов для сохранности смазки;
- температурная нестабильность (из-за изменения вязкости).
20. Дать определение понятию волочильный инструмент. Перечислить виды волочильного инструмента. Охарактеризовать монолитные волоки в соответствии с рисунком. Проанализировать достоинства и недостатки данного вида волок.
Волочильный инструмент – инструмент служащий для протягивания металла (волочения), в процессе которого изменяется поперечное сечение исходной заготовки и увеличиваются линейные размеры готового изделия.
Виды волочильного инструмента: по конструктивному исполнению - твердосплавные волоки, сборные волоки, составные волоки, роликовые волоки, монолитные волоки, алмазные волоки, стальные волоки, дисковые волоки; по виду обработки – чистовые и черновые; по принципу действия – неподвижные и вращающиеся.
Геометрические параметры канала монолитной волоки с коническим профилем канала:
1)входная зона (форма входной зоны как правило двухконусная, с входным конусом 75-105° и вторым конусом 30-40°, как правило длина входной зоны составляют одну шестую длины канала волоки)
2)рабочая и смазочная зона (часть канала, предназначенная для захвата смазки проволокой в рабочую зону, а также для деформации проволоки, рабочая зона может быть конического или радиального исполнения)
3)калибрующая зона (в этой зоне размеры заготовки уменьшаются до размеров протянутого металла)
4)выходная зона (часть канала волоки, предназначенная для исключения возможности образования поверхностных повреждений: задиры, риски, царапины при выходе из волоки; конической формы).
Преимущества:
- простота конструкции волоки;
- высокие качества получаемого изделия.
Недостатки:
- во время волочения возникают значительные силы трения, на преодоление которых затрачивается большое количество энергии;
- относительно малая степень деформации (обжатия);
- низкая стойкость инструмента.
21. Дать определение понятию волока. Перечислить виды волок. Охарактеризовать твердосплавные волоки. Проанализировать достоинства и недостатки данного вида волок.
Волока– инструмент служащий для протягивания металла (волочения), в процессе которого изменяется поперечное сечение исходной заготовки и увеличиваются линейные размеры готового изделия.
Виды волок: твердосплавные волоки, сборные волоки, роликовые волоки, монолитные волоки, алмазные волоки, стальные волоки.
Технология изготовления твердосплавных вставок роликов включает три основных этапа:
- горячее прессование порошков;
- вакуумное спекание спрессованных заготовок;
- окончательное шлифование и калибровка.
Волоки с заготовками из твердых сплавов в десятки, а в некоторых случаях в сотни раз более стойкие, чем стальные волоки и во много раз дешевле алмазных волок. В эти волоки могут быть успешно и наиболее экономично протянуты проволока, прутки и трубы из всех черных и цветных металлов и их сплавов.
Преимущества:
- высокое качество поверхности получаемого изделия;
- низкая стоимость;
- высокая гибкость.
Недостатки:
- быстрая изнашиваемость;
- не могут использоваться для волочения тонкой проволоки.
22. Дать определение понятию роликовые волоки. Привести принцип действия роликовых волок. Охарактеризовать достоинства и недостатки данных волок. Привести пример применения роликовых волок при производстве проволоки и проволочных изделий.
Роликовая волока – инструмент для волочения металла с помощью деформирующих роликов, установленные посредством подшипников на неподвижных осях.
При волочение через роликовые волоки обрабатываемая проволока со стороны входа в волоку подается в волоку, состоящую из двух пар (вращающихся) роликов, расположенных перпендикулярно друг относительно друга, проволока проходя волоку обжимается, при этом максимальная степень обжатия составляет 55%.
Преимущества роликовых волок;
- малый расход электроэнергии;
- большая скорость;
- уменьшения количества Т/О;
- высокое качество получаемого изделия.
Недостатки:
- трудность настройки на размер;
- трудность придания необходимой жесткости;
- сложность конструкции;
В настоящее время роликовые волоки находят применение при производстве проволоки различного назначения в широком диапазоне профилеразмеров сечений, причем наибольшее распространение они получили при волочении прямоугольных, трапециевидных и круглых профилей.
23. Дать определение алмазным волокам. Перечислить операции при изготовлении данных волок. Описать Требования, предъявляемые к алмазным волокам. Привести пример применения алмазных волок.
Алмазные волоки – инструмент для волочения проволоки малого диаметра, а также проволоки, требующих превосходного качества поверхности.
Основными операция по изготовлению алмазных волок являются:
Огранка – проводится с целью придания алмазам правильной геометрической формы, для прочного закрепления их в обойме.
Центровка – заключается в определении середины заготовки на одной из торцевых поверхностей, после чего производят сверление конуса, производится с целью обеспечения правильного положения волочильного канала.
Алмаз используемый для изготовления волоки должен быть прозрачным, на свет должен просматриваться невооруженным глазом, не иметь рисок, пузырей и т.п. не алмазных включений. Ось волочильного канала должна быть перпендикулярной торцевой поверхности волоки. Все зоны канала волоки должны быть тщательно обработаны во избежание резких переходов от одной зоны к другой.
Алмазные волоки применяют для изготовления мягкой медной, алюминиевой, а также проволоки из нержавеющая стали, вольфрама и стальной проволоки с медным покрытием, стальной проволоки диаметром от нескольких микрон до 0,6 мм.
24. Дать определение понятию обоймы для волок. Перечислить виды обойм. Описать холодный и горячий способы закрепления волок в обоймы. Проанализировать достоинства и недостатки данных видов запрессовки.
Обоймы – вспомогательный инструмент для закрепления волоки для удобства ее установки при разработки канала и на волочильном стане в процессе волочения а также для уравновешивания силы возникающей под действием усилия волочения
Существует четыре способа закрепления волок в обойме:
А) Горячая запрессовка в цилиндрическое отверстие
Б) Холодная запрессовка в цилиндрическое отверстие
В) Холодная запрессовка в коническое отверстие
Г) Пайка
Горячая запрессовка в цилиндрическое отверстие осуществляется ручным или гидравлическим прессом сравнительно не большой мощности. Предварительный нагрев оправки 800-900С. После запрессовки медленное охлаждение обоймы с волокой в сухом песке.
Холодная запрессовка в цилиндрическое отверстие производится при помощи гидравлического пресса с усилием 2-4 тонны.
Холодная запрессовка в коническое отверстие производится при помощи гидравлического пресса с усилием.
При пайке волока помещается в отверстие оправки и помещается в печь до расплавления припоя, а затем медленно охлаждается
Достоинством горячей запрессовки в цилиндрическое отверстие является невысокое усилие запрессовки и ее высокая плотность, но исключается возможность повторного использования оправки. В отличии от горячей запрессовки холодная запрессовка в цилиндрические отверстия позволяет многократное использование оправок, но при данном виде запрессовки на всегда достигается нужная плотность закрепления.
При холодной запрессовке в цилиндрическое отверстие также возможно многоразовое использование оправок и достигается высокая плотность закрепления волоки, но для этого требуются большие усилия запрессовки.
25. Дать определение понятию притир. Перечислить виды обработки канала волок. Описать основные этапы обработки с помощью притира. Сравнить анодно-механическую и химико-механическую обработки.
Притир – инструмент предназначенный для переделке валок на больший размер или для изменения геометрической формы отверстия.
Виды обработки канала волок: 1) механическая обработка абразивами; 2) электроискровая обработка; 3) химико-механическая обработка; 4) анодно-механическая обработка.
Основные этапы обработки с помощью притира: шлифование, доводка, полирование и, если необходимо, сверление.
Шлифование осуществляют в определенной последовательности, зависящей от размера волок, условий обработки и других причин. Например, у волок средних диаметров первоначально шлифуют рабочую и смазочную зоны; затем выходную и калибрующую, а в конце операции осуществляют чистовое шлифование рабочей зоны. Доводка — это операция, при которой доводят до заданных размеров калибрующую и рабочую зоны, снимают резкие переходы от зоны к зоне и подготовляют поверхность очага деформации к полировке. Полирование рабочей и калибрующей зон проводят для придания их поверхности высокой степени чистоты — зеркального блеска, исключающего царапины, задиры и прочие дефекты. Из материалов для шлифования наиболее распространены карбид бора и карборунд. Карбид бора шлифует лучше, но уступает по шлифующей способности алмазной пудре.
Обработка отверстия волок химико-механическим методом. Этот метод обработки целесообразно применять для шлифования волок с диаметром отверстия более 15 мм. Шлифование отверстий химико-механическим методом производится аналогично обычной механической обработке отверстия волок с помощью абразивов, с применением соответствующих по форме и размерам притиров из красной меди. В качестве шлифующей смеси применяется абразивная суспензия, состоящая из водного раствора медного купороса и шлифовального порошка. Для повышения вязкости суспензии добавляется крахмал. Волоки после шлифования отверстия химико-механическим методом должны подвергаться обязательной доводке пастой из карбида бора.
Анодно-механический способ обработки отверстия волок. При данном способе обработки электрохимическое действие тока сочетается с механическим воздействием на поверхности отверстия волок. Поверхность отверстия из твердого сплава, являющаяся анодом, интенсивно разрушается в некоторых составах электролитов. Анодная пленка, образующаяся на твердом сплаве, представляет собой весьма хрупкое соединение компонентов сплава и электролита, легко удаляемое даже мягкими материалами. Катодом в данной установке является притир.
26. Описать процесс волочения. Перечислить способы волочения. Описать волочение с противонатяжением. Проанализировать достоинства и недостатки данного вида волочения.
Процесс волочения заключается в протягивании металла через волочильный инструмент (волока - фильера), в процессе которого изменяется поперечное сечение исходной заготовки и увеличиваются линейные размеры готового изделия. Различают следующие способы волочения со сниженным коэффициентом трения:
1. Волочение с противонатяжением
2. Ступенчатое волочение, при этом волока комплектуется из двух и более секций взамен одной
3. Волочение в роликовых волоках
4. Прокатка через многоволковые калибры
5. Безфильерное волочение
6. Вибрационное волочение
7. Волочение через вращающиеся волоки.
Если при обычном волочении упругие и пластические деформации сообщаются проволоке непосредственно в волоке, то при волочении с противонатяжением часть упругих напряжений проволоки создается еще до входа материала в волоку. В результате этого, в волоке давление металла на стенки канала снижается. Разогрев металла происходит при деформации, обеспечивая этим большую толщину и прочность смазочной пленки, снижается износ волок. На практике противонатяжение встречается часто. Это происходит следующим образом: торможение происходит на разматывающем устройстве либо торможение вытяжными шкивами при ступенчатом волочении через двойные волоки.
27. Дать определение понятию латунирование. Перечислить основные этапы данного процесса. Охарактеризовать процессы, проходящие при латунировании. Проанализировать использование латунированной проволоки в условиях БМЗ.
Латунирование - это электролитическое нанесение тонкого слоя латуни на проволоку.
Основные этапы латунирования проволоки:
Размотка » ванна промывки » печь патентирования » свинцовая ванна » ванна охлаждения » ванна травления в растворе серной кислоты » ванна промывки » ванна щелочного меднения » ванна промывки » ванна сернокислого меднения » ванна промывки » ванна цинкования » термодифузия » шкафы выдержки » ванна охлаждения » ванна фосфорного травления » камера сушки » намоточное устройство
Латунирование проволоки необходимо для облегчения дальнейшего волочения проволоки, она служит как подсмазочный слой при волочении. Также латунированная проволока обладает лучшей адгезией с резиной.
Латунированную проволоку на БМЗ используют в качестве заготовки для тонкого волочения. Там проволока в процессе волочения уменьшается в диаметре и отправляется на канатный участок, или на продажу(проволока РМЛ). Где она свивается в металлокорд различных конструкций. Который так необходим для армирования современных автомобильных шин.
28. Дать определение понятию окончательный брак. Перечислить виды брака при изготовлении проволоки. Описать характеристика брака по намоту. Проанализировать предупреждение производства брака в условиях БМЗ.
Окончательный брак — это продукция, которую экономически невыгодно или технически невозможно исправить и нельзя использовать по прямому назначению.
Получающийся при производстве проволоки калиброванного металла брак принято делить на исправимый и неисправимый.
Брак можно сгруппировать по следующим признакам: 1.Несоответствие геометрии: а)отклонения по размерам (диаметру) сечения; б)овальность, выходящая за пределы допуска; в)затяжки (местные утонения металла по его длине). 2.Поверхностные дефекты: а)дефекты, возникшие при металлургическом переделе (заусенцы, закаты, обезуглероживание); б)дефекты, возникшие при производстве проволоки (продольные и поперечные риски и трещины, раковины, рябизна, темные пятна, ржавая, темная и загрязненная поверхность). 3.Брак по механическим свойствам — это несоответствие требованиям стандарта по временному сопротивлению разрыву или твердости, числам перегибов и скручиваний, величине их относительного удлинения и сужения поперечного сечения, а также наличие в металле хрупких участков. 4.Несоответствие физических свойств (электросопротивления, электропроводности, коэффициента теплового расширения и др.).
Брак по намотке и массе мотка устраняется точной установкой отделочной волоки, тщательной регулировкой выпрямляющего (рихтовального) приспособления, созданием правильной конусности и хорошей полировкой чистового барабана и соблюдением у чистового барабана диаметра, соответствующего диаметру проволоки. Эти же причины приводят обычно к браку по "восьмеркам" (сворачиваниям мотков в виде цифры 8). Меры для их устранения те же. Несоответствие упаковки может произойти из-за применения не отвечающих требованию стандартов смазочных и оплеточных материалов, а также из-за недостаточной прочности, плохой герметизации и плохого внешнего оформления жесткой тары. Неясную и неполную маркировку улучшают повторным нанесением.
29. Технологическая схема производства металлокорда. Охарактеризовать операции при производстве данного вида продукции. Описать способы сокращения количества технологических операций при производстве металлокорда. Проанализировать область применения металлокорда.
проволока сердечник
+
прядь
= + оплетка
металлокорд
Основным способом сокращения технологических операций при производстве металлокорда является свивка металлокорда с сердечником в одну операцию (с помощью таких машин как RiR-15).
Применяется в качестве армирующего материала при производстве различных резинотехнических изделий: конвейерных лент, клиновидных ремней, рукавов высокого давления и т.д. Но самое широкое применение металлокорд нашел при производстве автомобильных и других резиновых шин.
30. Дать определение понятию сердечник. Перечислить виды сердечников. Охарактеризовать металлический сердечник. Проанализировать преимущества и недостатки металлических сердечников.
Сердечник – цилиндрическая часть каната, которая является опорой и амортизатором для прядей или канатов. Он должен противостоять радиальному давлению прядей или проволоки при нагруженном состоянии не допуская своей деформации.
Виды сердечника:
По типу материала изготовления: органические (волокна растений, хлопок, конопля, пенька) и неорганические (искусственных материалов( капрон, лавсан, полипропилен, полиэтилен) и металлические)
По типу свиваемой пряди:
- Однопрядные. Изготавливаются скручиванием с левым направлением из нескольких нитей.
- Трехпрядные. Сердечники изготавливаются скручиванием с направлением скрутки вправо, которые имеют скрутку влево(Z-левая, S-правая). Таким образом получают сердечник крестовой свивки.
Металлический сердечник предстовляет собой несколько свитых между собой металлических прядей. Металлический сердечник применяется тогда когда необходимо повысить структурную прочность каната, уменьшить конструктивное удлинение каната при растяжении, для увеличения продольной и поперечной жесткости и в условиях повышенной температуры.
Достоинствами стальных сердечников являются: стойкость при резко меняющейся нагрузке, работа при высоких температурах (оклоло 150°С) и под воздействием нагрузки от вышележащих витков канат не подвергается сплющиванию. К недостаткам металлических сердечников можно отнести малую гибкость, долговечность (из-за больших контактных напряжений межу проволоками пряди и сердечником) и полохое пропитывание смазкой в отличии от органических.
31. Дать определение понятию металлокорд. Перечислить виды контроля качества готовой продукции. Описать методики определения остаточного кручения и прямолинейности металлокорда. Привести пример регулировки канатной машины на заданные параметры кручения и прямолинейности.
Металлокорд - это стальной трос различных конструкций, свитый из высокопрочной тонкой латунированной проволоки.
Металлокорд состоит, как правило, из трёх элементов: проволок, прядей и оплёточной проволоки.
К видам контроля качества относятся остаточное кручение и прямолинейность. Остаточное кручение определяется путем отматывания с катушки металлокорда длиной 6 метров, загибается на конце под углом 90 градусов и смотрят, сколько оборотов сделает этот кончик. Кручение может быть положительным и отрицательным, положительное - это когда по часовой стрелке происходит кручение, отрицательное – против часовой стрелки.
Прямолинейность определяется путем отрезания металлокорда с катушки длиной 30-40 см, после чего этот кусок ложится на линейку со шкалой и определяется величина прямолинейности. На линейке 2 зоны: красная и желтая. Красная – брак, желтая – допустима. Остаточное кручение регулируется оборотами торсиона. Что бы изменить кручение на еденицу, необходимо изменить обороты торсиона на 20.
Прямолинейность регулируется с помощью рихтовки. Нужно смотреть, не вылетел ли какой-то ролик из рихтовки, зажата ли рихтовка. Попадет ли проволока в пазы роликов на рихтовке. Так же прямолинейность в какой-то мере зависит от правильного расположения проволок в подшипниках машины. Если она слетела с подшипников, то прямолинейность допустимой не будет.
32. Дать определение понятию канат. Перечислить виды канатов. Описать дефекты, возникающие в готовом изделии. Проанализировать область применения канатов.
Канат – это изделие которое применяется в грузоподъемных и транспортировочных устройствах, диаметр которого больше 4 мм.
Канаты классифицируются по конструктивному признаку: а) круглые канаты – одинарной свивки (спиральные, открытые, полузакрытые), двойной свивки (тросовые; однослойные; двухслойные; трехслойные из прядей круглого, трехгранного, овального и плоского сечения); б) некруглые – квадратные (одинарной и двойной свивки).
По типу касания проволок: точечные, точечно-линейные, линейные и линейно-точечные.
По направлению свивки: левые, правые, односторонние и крестовые.
По способу свивки: с одинарным кручением, с двойным кручением, с подкручиванием проволоки и сердечника.
По эксплуатационным характеристикам: нераскручивающиеся, обычные, некрутящиеся, нераскручивающиеся и некрутящиеся.
По назначению: металлургические, крановые, шахтные, подъемные, проходческие и откаточные.
Дефекты – несоответствие каких-либо показателей, механических свойств или геометрических размеров оговоренных в технологических инструкциях на данный вид продукции. Канат, прядь и проволока могут быть изготовлены без брака на всех стадиях производства, но быть забракованными на стадии контроля механических свойств как всего каната, так и прядей и проволоки. Канат может иметь исправимый и неисправимый брак. К исправимому относят: несоответствие прямолинейности, кручения или длинны полученного каната или пряди. К неисправимому – дефекты при свивке, несоответствие физико-химических и механических характеристик (разрыв, удлинение, вес, диаметр и т.д.)
Канаты широко используется во многих отраслях промышленности, сельского хозяйства:
- оснащение грузоподъемных устройств и механизмов, производство грузовых строп;
- оснастка судов морского и речного флота: швартовые, буксировочные и якорные канаты;
- в промышленном альпинизме - аварийно-спасательное, альпинистское, страховочное снаряжение;
- в коммунальном хозяйстве и сантехнических работах - уплотнение трубных соединений;
- в сельском хозяйстве, пищевой промышленности, торговле, почтовых учреждениях, в быту, на даче для упаковки, увязки, для хозяйственных и вспомогательных нужд и др.
33. Назвать основные отличия металлокорда от каната. Привести классификацию данных видов продукции. Описать особенности свивки канатов. Провести сравнительный анализ каната и металлокорда.
Основными отличиями металлокорда от каната являются диаметр и назначение.
Металлокорд бывает различных видов и конструкций. В зависимости от этого его применяют в различных типах шин:
· Металлокорд для легковых шин
· Металлокорд для легко-грузовых шин
· Металлокорд для грузовых шин
· Металлокорд для крупногабаритных и сверх крупногабаритных шин
Канаты классифицируются по следующим признакам:
1. Конструкция каната
Канаты одинарной свивки (спиральные) — состоящие из одного, двух или трех слоев проволоки, свитых в концентрические спирали.
Канаты двойной свивки — состоящие из шести и более прядей, свитых в один концентрический слой.
Канаты тройной свивки - состоящие из стренг, свитых по спирали в один концентрический слой.
2. Тип касания проволок между слоями
Пряди с точечным касание
Пряди с линейным касанием
Пряди с точечно-линейным касанием
Пряди с комбинированным линейно-точечным касанием
3. материал сердечника
Органический сердечник
Металлический сердечник
Канаты свиваются на канатных машинах из прядей - канатов одинарной или двойной свивки в зависимости от конструкции каната и его назначения. Канаты свиваются таким образом чтобы они могли гнуться, не раскручивались.
Металлокорд применяется для армирования различного вида шин. Канат же применяется для различного вида грузоподъемных механизмов, таких как: канаты для лифтов, канаты для различных грузоподъемных кранов, канаты для подвесных дорог, буксирные канаты.
Также металлокорд и канат отличаются диаметром. У каната он значительно больше.
34. Основные виды испытаний металлокорда. Сущность механических и химических испытаний. Описать метод определения массовой доли латунного покрытия. Сравнить методы определения массовых долей медного и латунного покрытий.
К основным видам испытания металлокорда относят химические и физико-механические испытания. Назначение технологических испытаний сводится к выявлению способности металла к восприятию предельных напряжений и деформаций. Назначение химических испытаний сводится к определелению характеристик пластичности, твердости и растяжения.
Для определения массовой доли латунного покрытия осуществляют следующую последовательность действий. Образцы расплетенного металлокорда в виде отрезков, взвешивают на аналитических весах. Образцы помещают в стакан, заливают раствором для снятия покрытия. Раствор сливают. Образец промывают водой, высушивают, и снова взвешивают на аналитических весах. Разность между двумя взвешиваниями составляет массу латунного покрытия.
Метод определения массовой доли меди заключается в взвешивании и стравливании поверхностного слоя металлокорда. Схема определения массовой доли меди : отбор образцов, взвешивание, стравливание образцов, промывки под струей воды, сушке и повторном взвешивании. Разница между двумя взвешиваниями и есть масса медного покрытия.
35. Дать определение понятию фибра. Перечислить типы фибры. Описать способы производства анкерной, волновой и микрофибры. Проанализировать область применения фибры.
Фибра - материал в виде волокон или узких полос, применяемый для дисперсного армирования бетонных конструкций. При этом повышается сопротивление растяжению, истиранию, ударным нагрузкам.
Типы фибры:
анкерная
волновая
![]() |

1. размотка
2. подвижный барабан
3. ножи для рубки фибры
4. приёмник для готового изделия
5. вибростол
С размотки (1) проволока по средствам вытяжного устройства поступает на линию и под воздействием ножей (3) расположенных на барабане (2) перерубается, в результате чего получается готовое изделие под названием фибра. Она попадает в приёмное устройство (4) – мешок, ящик, коробка, и с помощью вибростола (5) плотно утрамбовывается для последующей упаковки. Отличие в производстве анкерной фибры является то, что на барабан (2) и на ленте конвейера устанавливают специальные устройства, которые с помощью штамповки позволяет получить заданный профиль.
Стальная фибра улучшает характеристики бетона, после набора бетоном прочности выполняет силовые функции, стальная фибра будучи хорошо перемешанной представляет собой равномерно распределённую арматуру в теле бетонной плиты.
Стальная фибра по сравнению с арматурой является более экологическим материалом, её приминение позволяет уменьшить металлоёмкость конструкций и сократить вредное воздействие на окружающую среду.
Дата добавления: 2018-06-01; просмотров: 1227; Мы поможем в написании вашей работы! |
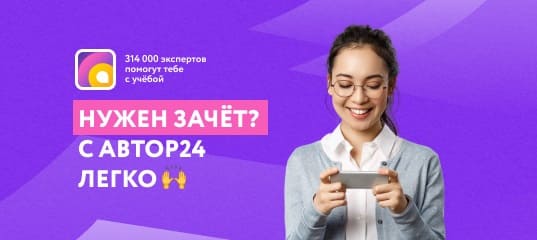
Мы поможем в написании ваших работ!