Особенности очистки газов от тонкой пыли. Способы очистки и снижения токсичности газовых выбросов.
Для тонкого пылеулавливания применяют фильтрующие аппараты и электрофильтры.
В основе работы пористых фильтров всех видов лежит фильтрация запыленного газа через пористую перегородку, в процессе которой частицы пыли, взвешенные в газе, задерживаются перегородкой, а газ беспрепятственно проходит сквозь неё.
Пористые фильтры могут весьма полно и эффективно задерживать, частицы пыли любых размеров и, как правило, отличаются высокой эффективностью.
скорость процесса фильтрации определяется перепадом давления на пористой перегородке, создаваемым вентилятором или другим побудителем тяги.
Применяемые пористые перегородки могут представлять собой зернистые слои, металлические сетки, керамику и металлокерамику, волокнистые материалы, бумагу, ткани.
Фильтрующие аппараты делят на волокнистые, тканевые и зернистые фильтры.
волокнистые фильтры применяют главным образом для фильтрации слабозапыленных потоков с концентрацией пыли не более 5 мг/м3. Волокнистые фильтры широко применяют для очистки атмосферного воздуха в системах приточной вентиляции, кондиционирования и воздушного отопления, а также в ряде установок специального назначения.
Для создания фильтрующих перегородок используют как естественные, так и специально изготовленные волокна толщиной 0,01-100мкм, например, отходы текстильного производства, шлаковую вату,целлюлозно-асбестовыеволокна, стекловолокно, волокна из кварца, базальта, графита, различных металлов, алюмоборсиликатов, полимеров и т. п.
|
|
Наиболее распространенным типом тканевого фильтра является рукавный фильтр, Главным элементом такого фильтра является рукав, изготовленный из фильтровальной ткани. Корпус фильтра разделен на несколько герметизированных камер, в каждой из которых размещено по нескольку рукавов. Газ, подлежащий очистке, подводится в нижнюю часть каждой камеры и поступает внутрь рукавов. Фильтруясь через ткань, газ проходит в камеру, откуда через открытый выпускной клапан поступает в газопровод чистого газа . Частицы пыли оседают на внутренней поверхности рукава.
По структуре фильтровальные материалы подразделяют на тканые и нетканые. Тканые материалы представляют собой переплетение нитей диаметром до 300-700мкм. Продольные нити называют основой, а поперечные утком. Характер переплетения может быть различным. В случае специальной обработки — ворсования на поверхности ткани образуется ворс из спутанных между собой волокон.
К нетканым материалам относятся фильтровальные войлоки и фетры, представляющие собой плотные слои беспорядочно перепутанных волокон, получаемые в основном на специальных иглопробивных машинах. Свойства фетров зависят от свойств волокон, из которых они изготовлены.
|
|
В условиях работы фильтров на металлургических предприятиях к тканям предъявляют следующие требования:
1)термостойкость, достаточная для работы в условиях температур отходящих газов металлургических агрегатов;
2)химическая стойкость по отношению к агрессивным компонентам, присутствующим в отходящих газах;
3)механическая прочность по отношению к истиранию и многократным изгибам во время регенерации тканей, а также стабильность размеров при рабочих условиях;
4)высокая пылеемкость при фильтрации и способность удерживать при регенерации часть пыли, что обеспечивает достаточно высокую эффективность после регенерации;
5)сохранение максимальной воздухопроницаемости в запыленном состоянии;
6)минимальное влагопоглощение и способность к легкому удалению накопленной влаги (малая гигроскопичность);
7)умеренная стоимость.
Выбор вида ткани определяется в основном температурой, а также влагосодержанием и агрессивными свойствами газового потока, сроками службы ткани в рабочих условиях и стоимостью ткани.
Наряду с тканями из натуральных волокон (хлопок, лен, шерсть) широко применяют ткани из синтетических волокон — капрон, нитрон, лавсан, а также стеклоткани. Используют и нетканые материалы: фетр и войлок.
|
|
В настоящее время чаще используют синтетические материалы. Наиболее распространены нитрон и лавсан, обладающие повышенной термостойкостью, достаточной химической стойкостью и механической прочностью наряду с хорошей фильтрующей способностью. Срок службы рукавов из этих тканей 6-12мес.
Фильтровальные материалы из стекловолокна характеризуются высокой термостойкостью и достаточной химической стойкостью. Главный недостаток стекловолокон - низкая изгибоустойчивость, вследствие чего рукава быстро выходят из строя. Для улучшения свойств стеклоткани ее обрабатывают кремний-органическимисоединениями. Получены стеклоткани, выдерживающие температуры до 500 °С.
В зернистых фильтрах фильтрация газа идет через слой зернистого материала – гравия, шлака, разных дробленных материалов, колец Рашига и т.п.
На металлургических заводах применяют зернистые фильтры кассетного типа для очистки воздуха перед доменными воздуходувками. Фильтр набирают из множества выдвижных кассет размером 0,5х0,5х0,1 м, наполненных насадкой, смоченной висциновым маслом.
|
|
Однако, вследствие низкой эффективности и большой затраты ручного труда при регенерации висциновые фильтры не удовлетворяют предъявляемым требованиям.
Стремление упростить процессы регенерации привело к созданию конструкций фильтров с движущимся зернистым слоем. Наиболее перспективны конструкции с вертикальным расположением слоя, при котором движение слоя осуществляется за счет силы тяжести . В таком фильтре при работе питателя загрязненные слои фильтра непрерывно выводятся из газохода и заменяются чистыми.
В металлургии особенно перспективно применение таких материалов, которые в дальнейшем могут быть использованы в технологическом процессе. Например, применяя в качестве фильтрующего материала чугунную дробь, железорудные концентраты, дробленную стружку и т.д., можно вообще отказаться от процесса регенерации и направлять отработавший фильтрующий материал вместе с уловленной пылью на аглофабрику или подавать его непосредственно в печь. Если жалюзийную решетку сделать водоохлаждаемой, то становится возможной очистка газов при высокой температуре, что особенно важно для металлургии.
Электрофильтры
Вэлектрофильтрах при пропускании запыленного газового потока через сильное электрическое поле частицы пыли получают электрический заряд и ускорение, заставляющее их двигаться вдоль силовых линий поля с последующим осаждением на электродах.
Вследствие того, что силы, вызывающие осаждение частиц пыли, приложены в этом случае только к самим частицам, а не ко всему потоку газа, расход энергии при электрической очистке значительно ниже, чем для большинства других пылеулавливающих аппаратов.
Электрофильтры по устройству сложнее и в эксплуатации дороже, но пригодны для улавливания частиц тоньше 1 мкм, составляющих возгоны.
Электрофильтры можно классифицировать по многим признакам.
По расположению зон зарядки и осаждения электрофильтры делят на однозонные и двухзонные. В однозонных электрофильтрах зоны зарядки и осаждения совмещены, а в двухзонных - коронирующие и осадительные электроды разделены и размещены в разных конструктивных зонах.
Всоответствии с направлением движения газового потока фильтры разделяют на горизонтальные и вертикальные.
По форме осадительных электродов различают электрофильтры пластинчатые, трубчатые и иногда шестигранные.
По числу последовательно расположенных полей электрофильтры бывают однопольными и многопольными, а по числу параллельно работающих секций – односекционными и многосекционными.
Вывод уловленной пыли может осуществляться в сухом виде посредством встряхивания электродов и в мокром виде смывом водой. В соответствии с этим различают сухие и мокрые электрофильтры
Рабочий элемент электрофильтра - пара металлических электродов: один с большой поверхностью - осадительный, другой с малой - коронирующий. Коронирующий электрод - вертикально подвешенная проволока с грузом на конце или стальной пруток. Осадительный - бывает в виде трубы (трубчатые электрофильтры) или пластин с двух сторон проволок (пластинчатые электрофильтры). Запыленный газ движется между ряда электродами вдоль проволок снизу вверх. Между электродами создается электрическое
поле постоянного тока напряжением 30-60тыс. В, в котором газ ионизируется и возникает свечение - «корона». Встречаясь с ионами, частицы пыли заряжаются одноименно с коронирующим электродом и отталкиваются от него. Притягиваясь к пластинам или трубе, они теряют заряд и оседают. Периодическими ударами механических молотов или иным способом пыль сбрасывается в бункер.
Сухие электрофильтры могут работать при температурах до 450 °С с коэффициентом полезного действия98-99%.Мокрые электрофильтры при температурах30-40°С удавливают из влажного газа особо тонкие возгоны и аэрозоли, они служат для газоочистки.
Конструкция инерционно-центробежного пылеуловителя включает корпус, внутри которого размещен завихритель, выполненный в виде полого диска, состоящего из верхней и нижней стенки. Внутри завихрителя расположены закручивающие лопатки. По оси корпуса проходит патрубок ввода запыленного газа, примыкающий к нижней стенке завихрителя. Концентрично снаружи патрубка ввода установлен патрубок вывода очищенного газа. По наружному нижнему краю диска завихрителя установлен экран в виде усеченного конуса. В нижней части корпуса расположен бункер для сбора пыли.
Пылеуловитель работает следующим образом. Запыленный газ через входной патрубок поступает в завихрительное устройство, в котором расположены лопатки, способствующие закручиванию пылегазового потока.
Отделение частиц пыли в закрученном потоке происходит под действием центробежных сил в пространстве между корпусом и экраном. Вихревой поток, опускаясь по спирали вниз, поворачивает на 180° и по внутренней спирали меньшего радиуса попадает под экран. Далее, снова изменив свое направление на 180°, уже очищенный газ поступает в патрубок вывода. Отделившаяся пыль по стенке корпуса под действием силы тяжести опускается в нижнюю часть корпуса и собирается в бункере.
Расположение входного патрубка по центру аппарата обеспечивает сохранение высокой скорости газа (до 20 м/с) в верхней части аппарата, в отличие от обычных циклонов, где в зоне ввода очищаемого потока скорость падает до 2-4м/с. Такое конструктивное решение существенно увеличивает центробежную силу и тем самым значительно повышает эффективность пылеулавливания.
При проведении промышленных испытаний аппарат показал высокую эффективность разделения пылевоздушной смеси – 98,6%.
В качестве основных методов очистки выбросов в атмосферу от токсичных газов используется абсорбция, адсорбция, каталитического и термического окисления.
Способ абсорбции основан на переходе газообразного вещества с поверхности абсорбента - вещества, применяемого для поглощения газов, паров и растворенных веществ в его объем с образованием раствора. Физическая сущность абсорбции заключается в следующем. Растворимый в жидкости компонент газовоздушной смеси проникает путем диффузии сначала через газовую пленку, затем сквозь жидкостную и поступает во внутренние слои абсорбента.
Абсорбция осуществляется в специальных аппаратах абсорберах. Принцип действия абсорберов заключается в том, что загрязненная газовая смесь двигается снизу вверх сквозь слой жидкого абсорбента, подаваемого сверху в виде капель. Скорость абсорбции зависит от поверхности соприкосновения жидкости с газом. С ее увеличением интенсивность абсорбция повышается.
Для удаления из промышленных выбросов аммиака, хлористого или фтористого водорода в качестве поглотительной жидкости применяют воду. Углеводороды по отношению к воде являются нейтральными и нерастворимыми, для их удаления применяют вязкие масла.
В зависимости от конструктивного исполнения абсорберы бывают пленочные, насадочные, трубчатые и др. В насадочные абсорберы по всей площади их поперечного сечения между двумя сетками помещают насадку. В качестве насадки, обеспечивающей значительную поверхность контакта газа с жидкостью, обычно используются кольца с перфорированными стенками или какой либо другой геометрической формы. Материалами для изготовления насадки могут быть керамика, фарфор, уголь, пластмассы, металлы, которые выбираются исходя из соображений антикоррозионной устойчивости. Орошение колец абсорбентом осуществляется при помощи разбрызгивателей.
Способ адсорбции основан на избирательном процессе поглощения веществ в газообразном или растворенном состоянии поверхностью твердых или жидких тел. Примером аппарата, работающего на этом принципе является противогаз. В адсорберах загрязненная смесь, из которой извлекают определенные вещества, проходит через смесь пористого адсорбента, с высоко энергетичной поверхностью, обеспечивающей адсорбцию. Эффективность адсорбции зависит от природы адсорбента и очищаемого газа, а также от свойств и концентрации адсорбированного вещества. При снижении температуры интенсивность поглощения увеличивается. Адсорбция - это физическое свойство веществ некоторых твердых тел с ультрамикроскопической структурой избирательно извлекать и концентрировать на поверхности компоненты из газовой смеси.
В качестве адсорбентов применяют активный уголь, активированный глинозем, активированный оксид алюминия, синтетические или природные цеолиты или молекулярные сита. Широкое распространение получили активированный уголь – мелкопористый продукт обугливания древесины и некоторых органических полимеров, обработанный водяным паром или углекислым газом. Активированный уголь применяется для очистки газов от органических паров, удаления неприятных запахов и газообразных примесей, содержащихся в выбросах.
Слой адсорбента высотой до 10 см обычно удерживается между двумя вертикальными пластинами, предпочтительно перфорированными металлическими листами, а газ проходит через него в горизонтальном направлении.
Гидравлическое сопротивление тонких слоев очень мало и необходимо следить за тем, чтобы толщина слоя была везде одинаковой и газ не мог проходить мимо адсорбента. Аппараты могут иметь плоскую, цилиндрическую или гофрированную форму. Промышленные цилиндрические аппараты имеют производительность около 0,012 м3/с, а большие гофрированные 0,35-0,50 м3/с. Адсорбционная емкость тонких слоев невелика и их целесообразнее всего использовать для обработки больших объемов газа с низким содержанием загрязнителей.
Дата добавления: 2018-06-01; просмотров: 503; Мы поможем в написании вашей работы! |
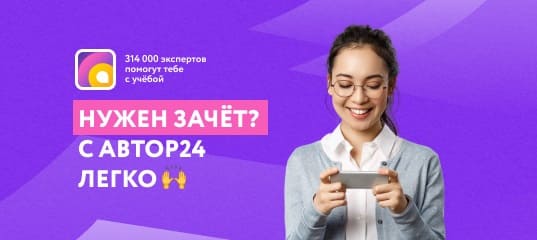
Мы поможем в написании ваших работ!