Общие требования, предъявляемые к материалам в зависимости от условий использования или эксплуатации.
Материаловедение — это вид научного обеспечения качества веществ и материалов.
Организационное обеспечение решается органами Госстандарта России, в задачи которого входит руководство такими органами, как, например, Государственная служба стандартных образцов состава и свойств веществ и материалов.
Стандартные образцы веществ и материалов — осязаемые объекты. Во многих случаях это прототипы либо образцы коммерческих материалов — керамики, стали, стекла — с аттестованным составом. Иногда это природные вещества, например горные породы, почва или ткани растений.
Изначально стандартные образцы веществ и материалов применялись для контроля качества в промышленности, особенно в отраслях, связанных с металлообработкой. В ряде случаев стандартные образцы веществ и материалов помогали заключению торговых сделок. Пример такого рода — продажа железной руды, количество которой исчисляется миллионами тонн, а цена прямо связана с содержанием железа. Отклонение концентрации железа в руде примерно на 0,1% увеличивает или уменьшает стоимость груза крупного рудовоза на тысячи условных единиц (у.е.).
Надежные измерения химического состава стандартных образцов веществ и материалов способствуют принятию важных решений в случае:
- определения пригодных материалов и готовой продукции для производств, где химический состав продукции регламентирован;
|
|
- контроля состояния здоровья и профилактики болезней, например при профессиональных заболеваниях;
- выявления возможности нарушения закона, например при анализе выхлопных газов автомобилей и сравнении результатов со стандартными образцами;
- установления совершения преступления при судебной экспертизе.
Для регистрации стандартных образцов состава и свойств веществ и материалов, типы которых признаны в качестве межгосударственного стандартного образца (МСО) стран СНГ, предназначен Реестр МСО. Он является источником официальной информации о результатах создания и признания типов МСО.
Создание стандартных образцов веществ и материалов — дело дорогостоящее и к тому же требует широких технических знаний и большого опыта. Разработка новых стандартных образцов веществ и материалов почти всецело определяется рыночным спросом.
В мире насчитывается 20 тыс. стандартных образцов веществ и материалов. Компьютерный банк данных «Кодекс образцовых веществ» (COMAR) содержит информацию о 12 тыс. таких образцов из 20 стран. В базу данных включены: название и общее описание вещества, название и адрес изготовителя, форма вещества, аттестованные свойства, их значения и область применения. Центры кодирования COMAR действуют в 14 странах. Необходимую информацию можно получить на Web-сайте и в центральном секретариате COMAR.
|
|
Нормативно-техническое и метрологическое обеспечение качества также решаются государственной системой стандартизации на основе систем стандартов, в число которых входят: государственная система стандартизации (ГСС); система показателей качества (СПК); государственная система обеспечения требуемой точности и единства измерений (ГСИ); государственная система стандартных справочных данных (ГСССД) и др.
ГСИ и ГС ССД широко используют образцовые вещества и химические эталоны, что формирует основу единства измерений и обеспечивает точность результатов, калибровку оборудования, мониторинг лабораторий и методов оценки, а также способствует сличению методов при использовании этих веществ в качестве эталонов сравнения. Они должны быть четко маркированы, что позволяет проводить их однозначную идентификацию со ссылкой на соответствующие сертификаты и другую документацию
Обязательные требования к качеству продукции, в том числе веществ и материалов, разрабатываются на основе показателей СПК. Они включены в государственные стандарты Российской Федерации - стандарты на продукцию.
|
|
На продукцию разрабатывают стандарты общих технических условий, которые содержат общие требования к группам однородной продукции, и технических условий, которые содержат требования к конкретной продукции.
Стандарт общих технических условий в общем случае содержит следующие разделы:
1) классификация, основные параметры и (или) размеры;
2) общие технические требования;
3) требования безопасности;
4) требования охраны окружающей среды;
5) методы контроля;
6) правила приемки;
7) транспортирование и хранение;
8) указания по эксплуатации (ремонту, утилизации);
9) гарантии изготовителя.
Номенклатуру, состав, содержание и наименование разделов (подразделов) определяют в соответствии с особенностями стандартизируемой продукции и характером предъявляемых к ней требований.
Стандарт технических условий устанавливает для одной или нескольких, например, марок, сортов, видов конкретной продукции всесторонние требования, соблюдение которых должно обеспечиваться при ее производстве, поставке, потреблении (эксплуатации), ремонте и утилизации.
Окончательная оценка пригодности тех или иных материалов для конкретного использования ведется на основании натурных испытаний, установленных требованиями государственных стандартов.
|
|
Задачи информационного обеспечения качества веществ и материалов решает Всероссийский научно-исследовательский центр стандартизации, информации и сертификации сырья, материалов и веществ Госстандарта России (ВНИЦ СМВ). Последний располагает информационным центром стандартов, который комплектуется таблицами рекомендуемых и стандартных данных по свойствам материалов и веществ, методикам ГС ССД, паспортами безопасности материалов и веществ, копиями аттестатов аккредитации органов по сертификации испытательных лабораторий (центров), государственными реестрами и копиями сертификатов соответствия (безопасности) на продукцию. Кроме того, в этом центре имеются авторские свидетельства об изобретении (разделы по материалам, веществам и методы их получения).
Правовое обеспечение качества гарантируется основными законами Российской Федерации, и в первую очередь Законом о защите прав потребителей.
Материально-техническое обеспечение качества определяется условиями производства и обращения материалов.
Классификация материалов.
Электротехнические материалы можно разбить на четыре группы: проводниковые, полупроводниковые, магнитные и диэлектрики.
Проводниковые материалы отличаются большой удельной электрической проводимостью и используются в электрических устройствах в качестве проводников электрического тока: всевозможные обмотки в машинах, аппаратах и приборах, контактные узлы, провода и кабели для передачи и распределения электрической энергии, в том числе и в линиях связи.
Полупроводники занимают по удельной проводимости промежуточное место между проводниками и диэлектриками. Особенности свойств полупроводников позволяют широко использовать их в различных отраслях электротехники: в техники связи в широком диапазоне частот, в различных устройствах радиоэлектроники и в технике сильного тока. Их применяют в выпрямителях, в усилителях, в фотодатчиках, в качестве специальных источников тока и т.п.
Магнитные материалы отличаются способностью усиливать магнитное поле, в которое их помещают, т.е. обладают большой магнитной проницаемостью. Они используются для изготовления магнитопроводов в электрических машинах и трансформаторах, для экранирования магнитного поля, а также в виде постоянных магнитов, создающих вокруг себя магнитное поле.
Диэлектрические материалы отличаются очень малой удельной электрической проводимостью. Количественно разница между проводимостью диэлектриков и проводников столь велика, что она обусловливает и качественную разницу между ними; в диэлектриках преобладают не электродинамические явления, характеризующиеся направленным движением огромного числа свободных зарядов (электронов и ионов), а электростатические, характеризующиеся наличием электрического поля. Реальные диэлектрики имеют некоторое (очень малое) количество свободных зарядов и как следствие отличающуюся от нуля проводимость. Электродинамические явления в нормальных условиях работы диэлектрических материалов выражены очень слабо. Диэлектрики служат для изоляции друг от друга различных токопроводящих деталей, находящихся под разными потенциалами, или для создания электрической емкости в конденсаторах.
Наиболее наглядно различие материалов по электрическим свойствам можно показать с помощью энергетических диаграмм зонной теории твердых тел.
Исследование спектров излучения различных веществ в газообразном состоянии, когда атомы расположены относительно друг друга на больших расстояниях, показывает, что для атомов каждого вещества характерны вполне определенные спектральные линии. Это говорит о наличии определенных энергетических состояний (уровней) для разных атомов.
Часть этих уровней (рис. 1.1) заполнена электронами в нормальном, невозбужденном состоянии атома, на других уровнях электроны могут находиться только после того, как атом испытает внешнее энергетическое воздействие; при этом он возбуждается. Стремясь прийти к устойчивому состоянию, атом излучает избыток энергии в момент возвращения электронов на уровни, при которых энергия атома минимальна. При переходе газообразного вещества в жидкость, а затем при образовании кристаллической решетки твердого тела все имеющиеся у данного типа атомов электронные уровни (как заполненные электронами, так и незаполненные) несколько смещаются вследствие действия соседних атомов друг на друга. Таким
образом, из отдельных энергетических уровней уединенных атомов в твердом теле образуется целая полоса - зона энергетических уровней.
Рис. 1.1. Схема расположения энергетических уровней уединенного атома (слева) и неметаллического твердого тела (справа)
1 – нормальный энергетический уровень атома; 2 – уровни возбужденного состояния атома; 3 – свободная зона; 4 – запрещенная зона; 5 – заполненная электронами зона
Энергетические диаграммы диэлектриков, полупроводников и проводников различны (рис. 1.2).
Диэлектриками будут такие материалы, у которых запрещенная зона настолько велика, что электронной электропроводности в обычных случаях не наблюдается.
Полупроводниками будут вещества с более узкой запрещенной зоной, которая может быть преодолена за счет внешних энергетических воздействий.
Проводниками будут материалы, у которых заполненная электронами зона вплотную прилегает к зоне свободных энергетических уровней или даже перекрывается ею. Вследствие этого электроны в металле свободны, т. е. могут переходить с уровней заполненной зоны на незанятые уровни свободной зоны под влиянием слабой напряженности приложенного к проводнику электрического поля.
Рис. 1.2. Энергетические диаграммы диэлектриков (а), полупроводников (б) и проводников (в) при нуле Кельвина в соответствии с зонной теорией твердого тела
1 – заполненная электронная зона; 2 – запрещенная зона; 3 – зона свободных энергетических уровней
При отсутствии в полупроводнике свободных электронов (при нуле Кельвина) приложенная к нему разность электрических потенциалов не вызовет тока. Если извне будет подведена энергия, достаточная для переброса электронов через запрещенную зону, то, став свободными, электроны смогут перемещаться под действием электрического поля, создавая электронную электропроводность полупроводника.
В заполненной зоне, откуда ушел электрон, образовалась «электронная дырка», а потому в полупроводнике начнется другое, «эстафетное», движение электронов, заполняющих образовавшуюся дырку, причем под воздействием электрического поля дырка будет двигаться в направлении поля, как эквивалентный положительный заряд. Процесс перехода электронов в свободное состояние сопровождается и обратным явлением, т. е. возвратом электронов в нормальное состояние. В результате в веществе наступает равновесие, т. е. число электронов, переходящих в свободную зону, становится равным числу электронов, возвращающихся обратно в заполненную зону.
С повышением температуры число свободных электронов в полупроводнике возрастает, а с понижением температуры до абсолютного нуля - убывает вплоть до нуля. Таким образом, электропроводность веществ, при различных температурах может быть существенно различной.
Энергию, необходимую для перехода электрона в свободное состояние или для образования дырки, может доставить не только тепловое движение, но и другие источники энергии, например свет, поток электронов и ядерных частиц, электрические и магнитные поля, механические воздействия и т.д.
Электрические свойства определяются условиями взаимодействия атомов вещества и не являются непременной особенностью данного атома. Например, углерод в виде алмаза является диэлектриком, а в виде графита обладает большой проводимостью.
Примеси и дефекты кристаллической решетки сильно влияют на
электрические свойства твердых тел.
По магнитным свойствам материалы подразделяются на слабомагнитные (диамагнетики и парамагнетики) и сильномагнитные (ферромагнетики и ферримагнетики).
Диамагнетиками являются вещества с магнитной проницаемостью mr < 1, значение которой не зависит от напряженности внешнего магнитного поля. К ним относятся водород, инертные газы, большинство органических соединений, каменная соль и некоторые металлы (медь, цинк, серебро, золото, ртуть), а также висмут, галлий, сурьма.
К парамагнетикам относятся вещества с магнитной проницаемостью mr > 1, также не зависящей от напряженности внешнего
магнитного поля. К ним относятся кислород, оксид азота, соли
железа, кобальта, никеля и редкоземельных элементов, щелочные металлы, алюминий, платина.
Диамагнетики и парамагнетики имеют магнитную проницаемость, близкую к единице, и по магнитным свойствам нашли себе ограниченное применение в технике.
У сильно магнитных материалов mr >> 1. К ним относятся железо, никель, кобальт и их сплавы.
Лекция 2
Особенности атомно-кристаллического строения металлов.
1. Металлы, особенности атомно-кристаллического строения.
2. Понятие об изотропии и анизотропии.
3. Аллотропия или полиморфные превращения.
4. Магнитные превращения.
Металлы, особенности атомно-кристаллического строения.
В огромном ряду материалов, с незапамятных времен известных человеку и широко используемых им в своей жизни и деятельности, металлы всегда занимали особое место.
Подтверждение этому: и в названиях эпох (золотой, серебряный, бронзовый, железный века), на которые греки делили историю человечества: и в археологических находках металлических изделий (кованые медные украшения, сельскохозяйственные орудия); и в повсеместном использовании металлов и сплавов в современной технике.
Причина этого - в особых свойствах металлов, выгодно отличающих их от других материалов и делающих во многих случаях незаменимыми.
Металлы – один из классов конструкционных материалов, характеризующийся определенным набором свойств:
- «металлический блеск» (хорошая отражательная способность);
- пластичность;
- высокая теплопроводность;
- высокая электропроводность.
Данные свойства обусловлены особенностями строения металлов. Согласно теории металлического состояния, металл представляет собой вещество, состоящее из положительных ядер, вокруг которых по орбитам вращаются электроны. На последнем уровне число электронов невелико и они слабо связаны с ядром. Эти электроны имеют возможность перемещаться по всему объему металла, т.е. принадлежать целой совокупности атомов.
Таким образом, пластичность, теплопроводность и электропроводность обеспечиваются наличием «электронного газа».
Все металлы, затвердевающие в нормальных условиях, представляют собой кристаллические вещества, то есть укладка атомов в них характеризуется определенным порядком – периодичностью, как по различным направлениям, так и по различным плоскостям. Этот порядок определяется понятием кристаллическая решетка.
Другими словами, кристаллическая решетка это воображаемая пространственная решетка, в узлах которой располагаются частицы, образующие твердое тело.
Элементарная ячейка – элемент объема из минимального числа атомов, многократным переносом которого в пространстве можно построить весь кристалл.
Элементарная ячейка характеризует особенности строения кристалла. Основными параметрами кристалла являются:
- размеры ребер элементарной ячейки. a, b, c – периоды решетки – расстояния между центрами ближайших атомов. В одном направлении выдерживаются строго определенными.
- углы между осями ( ).
- координационное число (К) указывает на число атомов, расположенных на ближайшем одинаковом расстоянии от любого атома в решетке.
- базис решетки количество атомов, приходящихся на одну элементарную ячейку решетки.
- плотность упаковки атомов в кристаллической решетке – объем, занятый атомами, которые условно рассматриваются как жесткие шары. Ее определяют как отношение объема, занятого атомами к объему ячейки (для объемно-центрированной кубической решетки – 0,68, для гранецентрированной кубической решетки – 0,74)
Рис.2.1. Схема кристаллической решетки
Классификация возможных видов кристаллических решеток была проведена французским ученым О. Браве, соответственно они получили название «решетки Браве». Всего для кристаллических тел существует четырнадцать видов решеток, разбитых на четыре типа;
- примитивный – узлы решетки совпадают с вершинами элементарных ячеек;
- базоцентрированный – атомы занимают вершины ячеек и два места в противоположных гранях;
- объемно-центрированный – атомы занимают вершины ячеек и ее центр;
- гранецентрированный – атомы занимают вершины ячейки и центры всех шести граней
Рис. 2.2. Основные типы кристаллических решеток: а – объемно-центрированная кубическая; б– гранецентрированная кубическая; в – гексагональная плотноупакованная
Основными типами кристаллических решеток являются:
1. Объемно - центрированная кубическая (ОЦК) (см. рис.2.2а), атомы располагаются в вершинах куба и в его центре (V, W, Ti, )
2. Гранецентрированная кубическая (ГЦК) (см. рис. 2.2б), атомы располагаются в вершинах куба и по центру каждой из 6 граней (Ag, Au, )
3. Гексагональная, в основании которой лежит шестиугольник:
- простая – атомы располагаются в вершинах ячейки и по центру 2 оснований (углерод в виде графита);
- плотноупакованная (ГПУ) – имеется 3 дополнительных атома в средней плоскости (цинк).
Понятие об изотропии и анизотропии.
Свойства тела зависят от природы атомов, из которых оно состоит, и от силы взаимодействия между этими атомами. Силы взаимодействия между атомами в значительной степени определяются расстояниями между ними. В аморфных телах с хаотическим расположением атомов в пространстве расстояния между атомами в различных направлениях равны, следовательно, свойства будут одинаковые, то есть аморфные тела изотропны.
В кристаллических телах атомы правильно располагаются в пространстве, причем по разным направлениям расстояния между атомами неодинаковы, что предопределяет существенные различия в силах взаимодействия между ними и, в конечном результате, разные свойства. Зависимость свойств от направления называется анизотропией.
Чтобы понять явление анизотропии необходимо выделить кристаллографические плоскости и кристаллографические направления в кристалле.
Плоскость, проходящая через узлы кристаллической решетки, называется кристаллографической плоскостью.
Прямая, проходящая через узлы кристаллической решетки, называется кристаллографическим направлением.
Для обозначения кристаллографических плоскостей и направлений пользуются индексами Миллера. Чтобы установить индексы Миллера, элементарную ячейку вписывают в пространственную систему координат (оси X,Y, Z – кристаллографические оси). За единицу измерения принимается период решетки.
Рис.2.3. Примеры обозначения кристаллографических плоскостей (а) и кристаллографических направлений (б)
Для определения индексов кристаллографической кристаллографической плоскости необходимо:
- установить координаты точек пересечения плоскости с осями координат в единицах периода решетки;
- взять обратные значения этих величин;
- привести их к наименьшему целому кратному, каждому из полученных чисел.
Полученные значения простых целых чисел, не имеющие общего множителя, являются индексами Миллера для плоскости, указываются в круглых скобках. Примеры обозначения кристаллографических плоскостей на рис.21.3 а.
Другими словами, индекс по оси показывает на сколько частей плоскость делит осевую единицу по данной оси. Плоскости, параллельные оси, имеют по ней индекс 0 (110)
Ориентация прямой определяется координатами двух точек. Для определения индексов кристаллографического направления необходимо:
- одну точку направления совместить с началом координат;
- установить координаты любой другой точки, лежащей на прямой, в единицах периода решетки
- привести отношение этих координат к отношению трех наименьших целых чисел.
Индексы кристаллографических направлений указываются в квадратных скобках [111].
В кубической решетке индексы направления, перпендикулярного плоскости (hkl) имеют те же индексы [hkl].
Аллотропия или полиморфные превращения.
Способность некоторых металлов существовать в различных кристаллических формах в зависимости от внешних условий (давление, температура) называется аллотропией или полиморфизмом.
Каждый вид решетки представляет собой аллотропическое видоизменение или модификацию.
Примером аллотропического видоизменения в зависимости от температуры является железо (Fe).
Fe: – ОЦК -
;
– ГЦК -
;
– ОЦК -
; (высокотемпературное
).
Превращение одной модификации в другую протекает при постоянной температуре и сопровождается тепловым эффектом. Видоизменения элемента обозначается буквами греческого алфавита в виде индекса у основного обозначения металла.
Примером аллотропического видоизменения, обусловленного изменением давления, является углерод: при низких давлениях образуется графит, а при высоких – алмаз.
Используя явление полиморфизма, можно упрочнять и разупрочнять сплавы при помощи термической обработки.
Магнитные превращения.
Некоторые металлы намагничиваются под действием магнитного поля. После удаления магнитного поля они обладают остаточным магнетизмом. Это явление впервые обнаружено на железе и получило название ферромагнетизма. К ферромагнетикам относятся железо, кобальт, никель и некоторые другие металлы.
При нагреве ферромагнитные свойства металла уменьшаются постепенно: вначале слабо, затем резко, и при определенной температуре (точка Кюри) исчезают (точка Кюри для железа – ). Выше этой температуры металлы становятся парамагнетиками. Магнитные превращения не связаны с изменением кристаллической решетки или микроструктуры, они обусловлены изменениями в характере межэлектронного взаимодействия.
Лекция 3
Строение реальных металлов. Дефекты кристаллического строения.
1. Точеные дефекты.
2. Линейные дефекты.
3. Простейшие виды дислокаций – краевые и винтовые.
Из жидкого расплава можно вырастить монокристалл. Их обычно используют в лабораториях для изучения свойств того или иного вещества.
Металлы и сплавы, полученные в обычных условиях, состоят из большого количества кристаллов, то есть, имеют поликристаллическое строение. Эти кристаллы называются зернами. Они имеют неправильную форму и различно ориентированы в пространстве. Каждое зерно имеет свою ориентировку кристаллической решетки, отличную от ориентировки соседних зерен, вследствие чего свойства реальных металлов усредняются, и явления анизотропии не наблюдается
В кристаллической решетке реальных металлов имеются различные дефекты (несовершенства), которые нарушают связи между атомами и оказывают влияние на свойства металлов. Различают следующие структурные несовершенства:
- точечные – малые во всех трех измерениях;
- линейные – малые в двух измерениях и сколь угодно протяженные в третьем;
- поверхностные – малые в одном измерении.
Точеные дефекты.
Одним из распространенных несовершенств кристаллического строения является наличие точечных дефектов: вакансий, дислоцированных атомов и примесей (рис. 3.).
Рис.3.1. Точечные дефекты
Вакансия – отсутствие атомов в узлах кристаллической решетки, «дырки», которые образовались в результате различных причин. Образуется при переходе атомов с поверхности в окружающую среду или из узлов решетки на поверхность (границы зерен, пустоты, трещины и т. д.), в результате пластической деформации, при бомбардировке тела атомами или частицами высоких энергий (облучение в циклотроне или нейтронной облучение в ядерном реакторе). Концентрация вакансий в значительной степени определяется температурой тела. Перемещаясь по кристаллу, одиночные вакансии могут встречаться. И объединяться в дивакансии. Скопление многих вакансий может привести к образованию пор и пустот.
Дислоцированный атом – это атом, вышедший из узла решетки и занявший место в междоузлие. Концентрация дислоцированных атомов значительно меньше, чем вакансий, так как для их образования требуются существенные затраты энергии. При этом на месте переместившегося атома образуется вакансия.
Примесные атомы всегда присутствуют в металле, так как практически невозможно выплавить химически чистый металл. Они могут иметь размеры больше или меньше размеров основных атомов и располагаются в узлах решетки или междоузлиях.
Точечные дефекты вызывают незначительные искажения решетки, что может привести к изменению свойств тела (электропроводность, магнитные свойства), их наличие способствует процессам диффузии и протеканию фазовых превращений в твердом состоянии. При перемещении по материалу дефекты могут взаимодействовать.
Линейные дефекты.
Основными линейными дефектами являются дислокации. Априорное представление о дислокациях впервые использовано в 1934 году Орованом и Тейлером при исследовании пластической деформации кристаллических материалов, для объяснения большой разницы между практической и теоретической прочностью металла.
Дислокация – это дефекты кристаллического строения, представляющие собой линии, вдоль и вблизи которых нарушено характерное для кристалла правильное расположение атомных плоскостей.
Простейшие виды дислокаций – краевые и винтовые.
Краевая дислокация представляет собой линию, вдоль которой обрывается внутри кристалла край “лишней“ полуплоскости (рис. 3.2).
а) б)
Рис. 3.2. Краевая дислокация (а) и механизм ее образования (б)
Неполная плоскость называется экстраплоскостью.
Большинство дислокаций образуются путем сдвигового механизма. Ее образование можно описать при помощи следующей операции. Надрезать кристалл по плоскости АВСD, сдвинуть нижнюю часть относительно верхней на один период решетки в направлении, перпендикулярном АВ, а затем вновь сблизить атомы на краях разреза внизу.
Наибольшие искажения в расположении атомов в кристалле имеют место вблизи нижнего края экстраплоскости. Вправо и влево от края экстраплоскости эти искажения малы (несколько периодов решетки), а вдоль края экстраплоскости искажения простираются через весь кристалл и могут быть очень велики (тысячи периодов решетки) (рис. 3.3).
Если экстраплоскость находится в верхней части кристалла, то краевая дислокация – положительная ( ), если в нижней, то – отрицательная (
). Дислокации одного знака отталкиваются, а противоположные притягиваются.
Рис. 3.3. Искажения в кристаллической решетке при наличии краевой дислокации
Другой тип дислокаций был описан Бюргерсом, и получил название винтовая дислокация.
Винтовая дислокация получена при помощи частичного сдвига по плоскости Q вокруг линии EF (рис. 3.4) На поверхности кристалла образуется ступенька, проходящая от точки Е до края кристалла. Такой частичный сдвиг нарушает параллельность атомных слоев, кристалл превращается в одну атомную плоскость, закрученную по винту в виде полого геликоида вокруг линии EF, которая представляет границу, отделяющую часть плоскости скольжения, где сдвиг уже произошел, от части, где сдвиг не начинался. Вдоль линии EF наблюдается макроскопический характер области несовершенства, в других направлениях ее размеры составляют несколько периодов.
Если переход от верхних горизонтов к нижним осуществляется поворотом по часовой стрелке, то дислокация правая, а если поворотом против часовой стрелки – левая.
Рис. 3.4. Механизм образования винтовой дислокации
Винтовая дислокация не связана с какой-либо плоскостью скольжения, она может перемещаться по любой плоскости, проходящей через линию дислокации. Вакансии и дислоцированные атомы к винтовой дислокации не стекают.
В процессе кристаллизации атомы вещества, выпадающие из пара или раствора, легко присоединяются к ступеньке, что приводит к спиральному механизму роста кристалла.
Линии дислокаций не могут обрываться внутри кристалла, они должны либо быть замкнутыми, образуя петлю, либо разветвляться на несколько дислокаций, либо выходить на поверхность кристалла.
Дислокационная структура материала характеризуется плотностью дислокаций.
Плотность дислокаций в кристалле определяется как среднее число линий дислокаций, пересекающих внутри тела площадку площадью 1 м2, или как суммарная длина линий дислокаций в объеме 1 м3
(см-2; м-2).
Плотность дислокаций изменяется в широких пределах и зависит от состояния материала. После тщательного отжига плотность дислокаций составляет 105…107 м-2, в кристаллах с сильно деформированной кристаллической решеткой плотность дислокаций достигает 1015…10 16 м –2.
Плотность дислокации в значительной мере определяет пластичность и прочность материала (рис. 3.5).
Рис. 3.5. Влияние плотности дислокаций на прочность
Минимальная прочность определяется критической плотностью дислокаций.
Если плотность меньше значения а, то сопротивление деформированию резко возрастает, а прочность приближается к теоретической. Повышение прочности достигается созданием металла с бездефектной структурой, а также повышением плотности дислокаций, затрудняющим их движение. В настоящее время созданы кристаллы без дефектов – нитевидные кристаллы длиной до 2 мм, толщиной 0,5…20 мкм - “усы“ с прочностью, близкой к теоретической: для железа = 13000 МПа, для меди
=30000 МПа. При упрочнении металлов увеличением плотности дислокаций, она не должна превышать значений 1015…10 16 м –2. В противном случае образуются трещины.
Дислокации влияют не только на прочность и пластичность, но и на другие свойства кристаллов. С увеличением плотности дислокаций возрастает внутреннее, изменяются оптические свойства, повышается электросопротивление металла. Дислокации увеличивают среднюю скорость диффузии в кристалле, ускоряют старение и другие процессы, уменьшают химическую стойкость, поэтому в результате обработки поверхности кристалла специальными веществами в местах выхода дислокаций образуются ямки.
Дислокации образуются при образовании кристаллов из расплава или газообразной фазы, при срастании блоков с малыми углами разориентировки. При перемещении вакансий внутри кристалла, они концентрируются, образуя полости в виде дисков. Если такие диски велики, то энергетически выгодно “захлопывание” их с образованием по краю диска краевой дислокации. Образуются дислокации при деформации, в процессе кристаллизации, при термической обработке.
Поверхностные дефекты– границы зерен, фрагментов и блоков (рис. 3.6).
Рис. 3.6. Разориентация зерен и блоков в металле
Размеры зерен составляют до 1000 мкм. Углы разориентации составляют до нескольких десятков градусов ( ).
Граница между зернами представляет собой тонкую в 5 – 10 атомных диаметров поверхностную зону с максимальным нарушением порядка в расположении атомов.
Строение переходного слоя способствует скоплению в нем дислокаций. На границах зерен повышена концентрация примесей, которые понижают поверхностную энергию. Однако и внутри зерна никогда не наблюдается идеального строения кристаллической решетки. Имеются участки, разориентированные один относительно другого на несколько градусов ( ). Эти участки называются фрагментами. Процесс деления зерен на фрагменты называется фрагментацией или полигонизацией.
В свою очередь каждый фрагмент состоит из блоков, размерами менее 10 мкм, разориентированных на угол менее одного градуса ( ). Такую структуру называют блочной или мозаичной.
Лекция 4
Общая теория сплавов. Строение, кристаллизация и свойства сплавов. Диаграмма состояния.
1. Понятие о сплавах и методах их получения.
2. Основные понятия в теории сплавов.
3. Особенности строения, кристаллизации и свойств сплавов: механических смесей, твердых растворов, химических соединений.
4. Классификация сплавов твердых растворов.
5. Кристаллизация сплавов.
6. Диаграмма состояния.
Понятие о сплавах и методах их получения.
Под сплавом понимают вещество, полученное сплавлением двух или более элементов. Возможны другие способы приготовления сплавов: спекания, электролиз, возгонка. В этом случае вещества называются псевдосплавами.
Сплав, приготовленный преимущественно из металлических элементов и обладающий металлическими свойствами, называется металлическим сплавом. Сплавы обладают более разнообразным комплексом свойств, которые изменяются в зависимости от состава и метода обработки.
Основные понятия в теории сплавов.
Система – группа тел выделяемых для наблюдения и изучения.
В металловедении системами являются металлы и металлические сплавы. Чистый металл является простой однокомпонентной системой, сплав – сложной системой, состоящей из двух и более компонентов.
Компоненты – вещества, образующие систему. В качестве компонентов выступают чистые вещества и химические соединения, если они не диссоциируют на составные части в исследуемом интервале температур.
Фаза – однородная часть системы, отделенная от других частей системы поверхностного раздела, при переходе через которую структура и свойства резко меняются.
Вариантность (C) (число степеней свободы) – это число внутренних и внешних факторов (температура, давление, концентрация), которые можно изменять без изменения количества фаз в системе.
Если вариантность C = 1 (моновариантная система), то возможно изменение одного из факторов в некоторых пределах, без изменения числа фаз.
Если вариантность C = 0 (нонвариантная cистема), то внешние факторы изменять нельзя без изменения числа фаз в системе.
Существует математическая связь между числом компонентов (К), числом фаз (Ф) и вариантностью системы ( С ). Это правило фаз или закон Гиббса
Если принять, что все превращения происходят при постоянном давлении, то число переменных уменьшится
где: С – число степеней свободы, К – число компонентов, Ф – число фаз, 1 – учитывает возможность изменения температуры.
Особенности строения, кристаллизации и свойств сплавов: механических смесей, твердых растворов, химических соединений.
Строение металлического сплава зависит от того, в какие взаимодействия вступают компоненты, составляющие сплав. Почти все металлы в жидком состоянии растворяются друг в друге в любых соотношениях. При образовании сплавов в процессе их затвердевании возможно различное взаимодействие компонентов.
В зависимости от характера взаимодействия компонентов различают сплавы:
1. механические смеси;
2. химические соединения;
3. твердые растворы.
Сплавы механические смеси образуются, когда компоненты не способны к взаимному растворению в твердом состоянии и не вступают в химическую реакцию с образованием соединения.
Образуются между элементами значительно различающимися по строению и свойствам, когда сила взаимодействия между однородными атомами больше чем между разнородными. Сплав состоит из кристаллов входящих в него компонентов (рис. 4.1). В сплавах сохраняются кристаллические решетки компонентов.
Рис. 4.1. Схема микроструктуры механической смеси
Сплавы химические соединения образуются между элементами, значительно различающимися по строению и свойствам, если сила взаимодействия между разнородными атомами больше, чем между однородными.
Особенности этих сплавов:
1. Постоянство состава, то есть сплав образуется при определенном соотношении компонентов, химическое соединение обозначается Аn Вm/.
2. Образуется специфическая, отличающаяся от решеток элементов, составляющих химическое соединение, кристаллическая решетка с правильным упорядоченным расположением атомов (рис. 4.2).
3. Ярко выраженные индивидуальные свойства.
4. Постоянство температуры кристаллизации, как у чистых компонентов.
Рис. 4.2. Кристаллическая решетка химического соединения
Сплавы твердые растворы – это твердые фазы, в которых соотношения между компонентов могут изменяться. Являются кристаллическими веществами.
Характерной особенностью твердых растворов является: наличие в их кристаллической решетке разнородных атомов, при сохранении типа решетки растворителя.
Твердый раствор состоит из однородных зерен (рис. 4.3).
Рис.4.3. Схема микроструктуры твердого раствора
Классификация сплавов твердых растворов.
По степеням растворимости компонентов различают твердые растворы:
· с неограниченной растворимостью компонентов;
· с ограниченной растворимостью компонентов.
При неограниченной растворимости компонентов кристаллическая решетка компонента растворителя по мере увеличения концентрации растворенного компонента плавно переходит в кристаллическую решетку растворенного компонента.
Для образования растворов с неограниченной растворимостью необходимы:
1. изоморфность (однотипность) кристаллических решеток компонентов;
2. близость атомных радиусов компонентов, которые не должны отличаться более чем на 8…13 %.
3. близость физико-химических свойств подобных по строение валентных оболочек атомов.
При ограниченной растворимости компонентов возможна концентрация растворенного вещества до определенного предела, При дальнейшем увеличении концентрации однородный твердый раствор распадается с образованием двухфазной смеси.
По характеру распределения атомов растворенного вещества в кристаллической решетке растворителя различают твердые растворы:
- замещения;
- внедрения;
- вычитания.
В растворах замещения в кристаллической решетке растворителя часть его атомов замещена атомами растворенного элемента (рис. 4.4 а). Замещение осуществляется в случайных местах, поэтому такие растворы называют неупорядоченными твердыми растворами.
Рис.4.4. Кристаллическая решетка твердых растворов замещения (а), внедрения (б)
При образовании растворов замещения периоды решетки изменяются в зависимости от разности атомных диаметров растворенного элемента и растворителя. Если атом растворенного элемента больше атома растворителя, то элементарные ячейки увеличиваются, если меньше – сокращаются. В первом приближении это изменение пропорционально концентрации растворенного компонента. Изменение параметров решетки при образовании твердых растворов – важный момент, определяющий изменение свойств. Уменьшение параметра ведет к большему упрочнению, чем его увеличение.
Твердые растворы внедрения образуются внедрением атомов растворенного компонента в поры кристаллической решетки растворителя (рис. 4.4 б).
Образование таких растворов, возможно, если атомы растворенного элемента имеют малые размеры. Такими являются элементы, находящиеся в начале периодической системы Менделеева, углерод, водород, азот, бор. Размеры атомов превышают размеры межатомных промежутков в кристаллической решетке металла, это вызывает искажение решетки и в ней возникают напряжения. Концентрация таких растворов не превышает 2-2.5%
Твердые растворы вычитания или растворы с дефектной решеткой. образуются на базе химических соединений, при этом возможна не только замена одних атомов в узлах кристаллической решетки другими, но и образование пустых, не занятых атомами, узлов в решетке.
К химическому соединению добавляют, один из входящих в формулу элементов, его атомы занимают нормальное положение в решетке соединения, а места атомов другого элемента остаются, незанятыми.
Кристаллизация сплавов.
Кристаллизация сплавов подчиняется тем же закономерностям, что и кристаллизация чистых металлов. Необходимым условием является стремление системы в состояние с минимумом свободной энергии.
Основным отличием является большая роль диффузионных процессов, между жидкостью и кристаллизующейся фазой. Эти процессы необходимы для перераспределения разнородных атомов, равномерно распределенных в жидкой фазе.
В сплавах в твердых состояниях, имеют место процессы перекристаллизации, обусловленные аллотропическими превращениями компонентов сплава, распадом твердых растворов, выделением из твердых растворов вторичных фаз, когда растворимость компонентов в твердом состоянии меняется с изменением температуры.
Эти превращения называют фазовыми превращениями в твердом состоянии.
При перекристаллизации в твердом состоянии образуются центры кристаллизации и происходит их рост.
Обычно центры кристаллизации возникают по границам зерен старой фазы, где решетка имеет наиболее дефектное строение, и где имеются примеси, которые могут стать центрами новых кристаллов. У старой и новой фазы, в течение некоторого времени, имеются общие плоскости. Такая связь решеток называется когерентной связью. В случае различия строения старой и новой фаз превращение протекает с образованием промежуточных фаз.
Нарушение когерентности и обособления кристаллов наступает, когда они приобретут определенные размеры.
Процессы кристаллизации сплавов изучаются по диаграммам состояния.
Диаграмма состояния.
Диаграмма состояния представляет собой графическое изображение состояния любого сплава изучаемой системы в зависимости от концентрации и температуры (рис. 4.5)
.
Рис. 4.5. Диаграмма состояния
Диаграммы состояния показывают устойчивые состояния, т.е. состояния, которые при данных условиях обладают минимумом свободной энергии, и поэтому ее также называют диаграммой равновесия, так как она показывает, какие при данных условиях существуют равновесные фазы.
Построение диаграмм состояния наиболее часто осуществляется при помощи термического анализа.
В результате получают серию кривых охлаждения, на которых при температурах фазовых превращений наблюдаются точки перегиба и температурные остановки.
Температуры, соответствующие фазовым превращениям, называют критическими точками. Некоторые критические точки имеют названия, например, точки отвечающие началу кристаллизации называют точками ликвидус, а концу кристаллизации – точками солидус.
По кривым охлаждения строят диаграмму состава в координатах: по оси абсцисс –концентрация компонентов, по оси ординат – температура.
Шкала концентраций показывает содержание компонента В. Основными линиями являются линии ликвидус (1) и солидус (2), а также линии соответствующие фазовым превращениям в твердом состоянии (3, 4).
По диаграмме состояния можно определить температуры фазовых превращений, изменение фазового состава, приблизительно, свойства сплава, виды обработки, которые можно применять для сплава.
Лекция 5
Диаграммы состояния двухкомпонентных сплавов.
1. Диаграмма состояния сплавов с неограниченной растворимостью компонентов в твердом состоянии (сплавы твердые растворы с неограниченной растворимостью)
2. Диаграмма состояния сплавов с отсутствием растворимости компонентов в компонентов в твердом состоянии (механические смеси)
3. Диаграмма состояния сплавов с ограниченной растворимостью компонентов в твердом состоянии
4. Диаграмма состояния сплавов, компоненты которых образуют химические соединения.
5. Диаграмма состояния сплавов, испытывающих фазовые превращения в твердом состоянии (переменная растворимость)
6. Связь между свойствами сплавов и типом диаграммы состояния
Диаграмма состояния сплавов с неограниченной растворимостью компонентов в твердом состоянии (сплавы твердые растворы с неограниченной растворимостью)
Диаграмма состояния и кривые охлаждения сплавов системы представлены на рис. 5.1.
Рис.5.1 Диаграмма состояния сплавов с неограниченной растворимостью компонентов в твердом состоянии (а); кривые охлаждения типичных сплавов (б)
Сначала получают термические кривые. Полученные точки переносят на диаграмму, соединив точки начала кристаллизации сплавов и точки конца кристаллизации, получают диаграмму состояния.
Проведем анализ полученной диаграммы.
1. Количество компонентов: К = 2 (компоненты А и В).
2. Число фаз: f = 2 (жидкая фаза L, кристаллы твердого раствора )
3. Основные линии диаграммы:
· acb – линия ликвидус, выше этой линии сплавы находятся в жидком состоянии;
· adb – линия солидус, ниже этой линии сплавы находятся в твердом состоянии.
4. Характерные сплавы системы:
Чистые компоненты А и В кристаллизуются при постоянной температуре, кривая охлаждения компонента В представлена на рис. 5.1,б.
Остальные сплавы кристаллизуются аналогично сплаву I, кривая охлаждения которого представлена на рис. 5.1, б.
Процесс кристаллизации сплава I: до точки 1 охлаждается сплав в жидком состоянии. При температуре, соответствующей точке 1, начинают образовываться центры кристаллизации твердого раствора . На кривой охлаждения отмечается перегиб (критическая точка), связанный с уменьшением скорости охлаждения вследствие выделения скрытой теплоты кристаллизации. На участке 1–2 идет процесс кристаллизации, протекающий при понижающейся температуре, так как согласно правилу фаз в двухкомпонентной системе при наличии двух фаз (жидкой и кристаллов твердого раствора
) число степеней свободы будет равно единице
. При достижении температуры соответствующей точке 2, сплав затвердевает, при дальнейшем понижении температуры охлаждается сплав в твердом состоянии, состоящий из однородных кристаллов твердого раствора
.
Схема микроструктуры сплава представлена на рис. 5.2.
Рис. 5.2. Схема микроструктуры сплава – однородного твердого раствора
5. Количественный структурно-фазовый анализ сплава.
Пользуясь диаграммой состояния можно для любого сплава при любой температуре определить не только число фаз, но и их состав и количественное соотношение. Для этого используется правило отрезков. Для проведения количественного структурно-фазового анализа через заданную точку проводят горизонталь (коноду) до пересечения с ближайшими линиями диаграммы (ликвидус, солидус или оси компонентов).
а). Определение состава фаз в точке m:
Для его определения через точку m проводят горизонталь до пересечения с ближайшими линиями диаграммы: ликвидус и солидус.
Состав жидкой фазы определяется проекцией точки пересечения горизонтали с линией ликвидус p на ось концентрации.
Состав твердой фазы определяется проекцией точки пересечения горизонтали с линией солидус q (или осью компонента) на ось концентрации.
Состав жидкой фазы изменяется по линии ликвидуса, а состав твердой фазы – по линии солидуса.
С понижением температуры состав фаз изменяется в сторону уменьшения содержания компонента В.
б). Определение количественного соотношения жидкой и твердой фазы при заданной температуре (в точке m):
Количественная масса фаз обратно пропорциональна отрезкам проведенной коноды.Рассмотрим проведенную через точку m коноду и ее отрезки.
Количество всего сплава (Qсп) определяется отрезком pq.
Отрезок, прилегающий к линии ликвидус pm, определяет количество твердой фазы.
Отрезок, прилегающий к линии солидус (или к оси компонента) mq, определяет количество жидкой фазы.
Диаграмма состояния сплавов с отсутствием растворимости компонентов в компонентов в твердом состоянии (механические смеси)
Диаграмма состояния и кривые охлаждения типичных сплавов системы представлены на рис. 5.3.
Рис. 5.3. Диаграмма состояния сплавов с отсутствием растворимости компонентов в твердом состоянии (а) и кривые охлаждения сплавов (б)
Проведем анализ диаграммы состояния.
1. Количество компонентов: К = 2 (компоненты А и В);
2. Число фаз: f = 3 (кристаллы компонента А, кристаллы компонента В, жидкая фаза).
3. Основные линии диаграммы:
линия ликвидус acb, состоит из двух ветвей, сходящихся в одной точке;
линия солидус ecf, параллельна оси концентраций стремится к осям компонентов, но не достигает их;
4. Типовые сплавы системы.
а) Чистые компоненты, кристаллизуются при постоянной температуре, на рис 5.3 б показана кривая охлаждения компонента А.
б). Эвтектический сплав – сплав, соответствующий концентрации компонентов в точке с (сплав I). Кривая охлаждения этого сплава, аналогична кривым охлаждения чистых металлов (рис. 5.3 б)
Эвтектика – мелкодисперсная механическая смесь разнородных кристаллов, кристаллизующихся одновременно при постоянной, самой низкой для рассматриваемой системы, температуре.
При образовании сплавов механических смесей эвтектика состоит из кристаллов компонентов А и В: Эвт. (кр. А + кр. В)
Процесс кристаллизации эвтектического сплава: до точки 1 охлаждается сплав в жидком состоянии. При температуре, соответствующей точке 1, начинается одновременная кристаллизация двух разнородных компонентов. На кривой охлаждения отмечается температурная остановка, т.е. процесс идет при постоянной температуре, так как согласно правилу фаз в двухкомпонентной системе при наличии трех фаз (жидкой и кристаллов компонентов А и В) число степеней свободы будет равно нулю . В точке 1/ процесс кристаллизации завершается. Ниже точки 1/ охлаждается сплав, состоящий из дисперсных разнородных кристаллов компонентов А и В.
в) Другие сплавы системы аналогичны сплаву II, кривую охлаждения сплава см на рис 5.3.б.
Процесс кристаллизации сплава II: до точки 1 охлаждается сплав в жидком состоянии. При температуре, соответствующей точке 1, начинают образовываться центры кристаллизации избыточного компонента В. На кривой охлаждения отмечается перегиб (критическая точка), связанный с уменьшением скорости охлаждения вследствие выделения скрытой теплоты кристаллизации. На участке 1–2 идет процесс кристаллизации, протекающий при понижающейся температуре, так как согласно правилу фаз в двухкомпонентной системе при наличии двух фаз (жидкой и кристаллов компонента В) число степеней свободы будет равно единице . При охлаждении состав жидкой фазы изменяется по линии ликвидус до эвтектического. На участке 2–2’ кристаллизуется эвтектика (см. кристаллизацию эвтектического сплава). Ниже точки 2’ охлаждается сплав, состоящий из кристаллов первоначально закристаллизовавшегося избыточного компонента В и эвтектики.
Схема микроструктуры сплава представлена на рис. 5.4.
Рис. 5.4. Схема микроструктур сплавов: а – доэвтектического, б – эвтектического, в – заэвтектического
5. При проведении количественного структурно-фазового анализа, конода, проведенная через заданную точку, пересекает линию ликвидус и оси компонентов, поэтому состав твердой фазы или 100 % компонента А, или 100 % компонента В.
Диаграмма состояния сплавов с ограниченной растворимостью компонентов в твердом состоянии
Диаграмма состояния и кривые охлаждения типичных сплавов системы представлены на рис.5.5.
1. Количество компонентов: К = 2 (компоненты А и В);
2. Число фаз: f = 3 (жидкая фаза и кристаллы твердых растворов (раствор компонента В в компоненте А) и
( раствор компонента А в компоненте В));
3. Основные линии диаграммы:
линия ликвидус acb, состоит из двух ветвей, сходящихся в одной точке;
линия солидус аdcfb, состоит из трех участков;
dm – линия предельной концентрации компонента В в компоненте А;
fn – линия предельной концентрации компонента А в компоненте В.
4. Типовые сплавы системы.
При концентрации компонентов, не превышающей предельных значений (на участках Аm и nВ), сплавы кристаллизуются аналогично сплавам твердым растворам с неограниченной растворимостью, см кривую охлаждения сплава I на рис. 5.5 б. При концентрации компонентов, превышающей предельные значения (на участке dcf), сплавы кристаллизуются аналогично сплавам механическим смесям, см. кривую охлаждения сплава II на рис. 5.5 б.
Рис. 5.5 Диаграмма состояния сплавов с ограниченной растворимостью компонентов в твердом состоянии (а) и кривые охлаждения типичных сплавов (б)
Сплав с концентрацией компонентов, соответствующей точке с, является эвтектическим сплавом. Сплав состоит из мелкодисперсных кристаллов твердых растворов и
, эвт. (кр. тв. р-ра
+ кр. тв. р-ра
)
Кристаллы компонентов в чистом виде ни в одном из сплавов не присутствуют.
Диаграмма состояния сплавов, компоненты которых образуют химические соединения.
Диаграмма состояния сплавов представлена на рис. 5.6.
Рис. 5.6. Диаграмма состояния сплавов, компоненты которых образуют химические соединения
Диаграмма состояния сложная, состоит из нескольких простых диаграмм. Число компонентов и количество диаграмм зависит от того, сколько химических соединений образуют основные компоненты системы.
Число фаз и вид простых диаграмм определяются характером взаимодействия между компонентами.
Эвт1 (кр. А + кр. AmBn);
Эвт2 (кр. B + кр. AmBn).
Диаграмма состояния сплавов, испытывающих фазовые превращения в твердом состоянии (переменная растворимость)
Диаграмма состояния представлена на рис. 5.7.
По внешнему виду диаграмма похожа на диаграмму состояния сплавов с ограниченной растворимостью компонентов в твердом состоянии. Отличие в том, что линии предельной растворимости компонентов не перпендикулярны оси концентрации. Появляются области, в которых из однородных твердых растворов при понижении температуры выделяются вторичные фазы.
На диаграмме:
df – линия переменной предельной растворимости компонента В в компоненте А;
ek – линия переменной предельной растворимости компонента А в компоненте В.
Кривая охлаждения сплава I представлена на рис. 5.7 б.
Рис. 5.7. Диаграмма состояния сплавов, испытывающих фазовые превращения в твердом состоянии (а) и кривая охлаждения сплава (б)
Процесс кристаллизации сплава I: до точки 1 охлаждается сплав в жидком состоянии. При температуре, соответствующей точке 1, начинают образовываться центры кристаллизации твердого раствора . На участке 1–2 идет процесс кристаллизации, протекающий при понижающейся температуре. При достижении температуры соответствующей точке 2, сплав затвердевает, при дальнейшем понижении температуры охлаждается сплав в твердом состоянии, состоящий из однородных кристаллов твердого раствора
. При достижении температуры, соответствующей точке 3, твердый раствор
оказывается насыщенным компонентом В, при более низких температурах растворимость второго компонента уменьшается, поэтому из
-раствора начинает выделяться избыточный компонент в виде кристаллов
. За точкой 3 сплав состоит из двух фаз: кристаллов твердого раствора
и вторичных кристаллов твердого раствора
.
Связь между свойствами сплавов и типом диаграммы состояния
Так как вид диаграммы, также как и свойства сплава, зависит от того, какие соединения или какие фазы образовали компоненты сплава, то между ними должна существовать определенная связь. Эта зависимость установлена Курнаковым, (см. рис. 5.8.).
Рис. 5.8. Связь между свойствами сплавов и типом диаграммы состояния
1. При образовании механических смесей свойства изменяются по линейному закону. Значения характеристик свойств сплава находятся в интервале между характеристиками чистых компонентов.
2. При образовании твердых растворов с неограниченной растворимостью свойства сплавов изменяются по криволинейной зависимости, причем некоторые свойства, например, электросопротивление, могут значительно отличаться от свойств компонентов.
3. При образовании твердых растворов с ограниченной растворимостью свойства в интервале концентраций, отвечающих однофазным твердым растворам, изменяются по криволинейному закону, а в двухфазной области – по линейному закону. Причем крайние точки на прямой являются свойствами чистых фаз, предельно насыщенных твердых растворов, образующих данную смесь.
4. При образовании химических соединений концентрация химического соединения отвечает максимуму на кривой. Эта точка перелома, соответствующая химическому соединению, называется сингулярной точкой.
Лекция 12
Виды термической обработки металлов. Основы теории термической обработки стали.
1. Виды термической обработки металлов.
2. Превращения, протекающие в структуре стали при нагреве и охлаждении
3. Механизм основных превращений
4. Превращение перлита в аустетит
5. Превращение аустенита в перлит при медленном охлаждении.
6. Закономерности превращения.
7. Промежуточное превращение
Виды термической обработки металлов.
Свойства сплава зависят от его структуры. Основным способом, позволяющим изменять структуру, а, следовательно, и свойства является термическая обработка.
Основы термической обработки разработал Чернов Д.К.. В дальнейшем они развивались в работах Бочвара А.А., Курдюмова Г.В., Гуляева А.П.
Термическая обработка представляет собой совокупность операций нагрева, выдержки и охлаждения, выполняемых в определенной последовательности при определенных режимах, с целью изменения внутреннего строения сплава и получения нужных свойств (представляется в виде графика в осях температура – время, см. рис. 12.1 ).
Рис.12.1. Графики различных видов термообработки: отжига (1, 1а), закалки (2, 2а), отпуска (3), нормализации (4)
Различают следующие виды термической обработки:
1. Отжиг 1 рода – возможен для любых металлов и сплавов.
Его проведение не обусловлено фазовыми превращениями в твердом состоянии.
Нагрев, при отжиге первого рода, повышая подвижность атомов, частично или полностью устраняет химическую неоднородность, уменьшает внутреннее напряжения.
Основное значение имеет температура нагрева и время выдержки. Характерным является медленное охлаждение
Разновидностями отжига первого рода являются:
· диффузионный;
· рекристаллизационный;
· отжиг для снятия напряжения после ковки, сварки, литья.
2. Отжиг II рода – отжиг металлов и сплавов, испытывающих фазовые превращения в твердом состоянии при нагреве и охлаждении.
Проводится для сплавов, в которых имеются полиморфные или эвтектоидные превращения, а также переменная растворимость компонентов в твердом состоянии.
Проводят отжиг второго рода с целью получения более равновесной структуры и подготовки ее к дальнейшей обработке. В результате отжига измельчается зерно, повышаются пластичность и вязкость, снижаются прочность и твердость, улучшается обрабатываемость резанием.
Характеризуется нагревом до температур выше критических и очень медленным охлаждением, как правило, вместе с печью (рис. 12.1 (1, 1а)).
3. Закалка – проводится для сплавов, испытывающих фазовые превращения в твердом состоянии при нагреве и охлаждении, с целью повышение твердости и прочности путем образования неравновесных структур (сорбит, троостит, мартенсит).
Характеризуется нагревом до температур выше критических и высокими скоростями охлаждения (рис. 12.1 (2, 2а)).
4. Отпуск – проводится с целью снятия внутренних напряжений, снижения твердости и увеличения пластичности и вязкости закаленных сталей.
Характеризуется нагревом до температуры ниже критической А (рис. 12.1 (3)). Скорость охлаждения роли не играет. Происходят превращения, уменьшающие степень неравновесности структуры закаленной стали.
Термическую обработку подразделяют на предварительную и окончательную.
Предварительная – применяется для подготовки структуры и свойств материала для последующих технологических операций (для обработки давлением, улучшения обрабатываемости резанием).
Окончательная – формирует свойство готового изделия.
Превращения, протекающие в структуре стали при нагреве и охлаждении
Любая разновидность термической обработки состоит из комбинации четырех основных превращений, в основе которых лежат стремления системы к минимуму свободной энергии (рис 12.2).
Рис. 12.2. Зависимость свободной энергии структурных составляющих сталей от температуры: аустенита (FA), мартенсита (FM), перлита (FП)
1. Превращение перлита в аустенит , происходит при нагреве выше критической температуры А1, минимальной свободной энергией обладает аустенит.
2. Превращение аустенита в перлит , происходит при охлаждении ниже А1, минимальной свободной энергией обладает перлит:
3. Превращение аустенита в мартенсит , происходит при быстром охлаждении ниже температуры нестабильного равновесия
4. Превращение мартенсита в перлит ; – происходит при любых температурах, т.к. свободная энергия мартенсита больше, чем свободная энергия перлита.
Механизм основных превращений
1. Превращение перлита в аустетит
Превращение основано на диффузии углерода, сопровождается полиморфным превращением , а так же растворением цементита в аустените.
Для исследования процессов строят диаграммы изотермического образования аустенита (рис.12.3). Для этого образцы нагревают до температуры выше и выдерживают, фиксируя начало и конец превращения.
Рис. 12.3. Диаграмма изотермического образования аустенита: 1 - начало образования аустенита; 2 - конец преобразования перлита в аустенит; 3 - полное растворение цементита.
С увеличением перегрева и скорости нагрева продолжительность превращения сокращается.
Механизм превращения представлен на рис.12.4.
Рис. 12.4. Механизм превращения перлита в аустенит.
Превращение начинаются с зарождения центров аустенитных зерен на поверхности раздела феррит – цементит, кристаллическая решетка перестраивается в решетку
.
Время превращения зависит от температуры, так как с увеличением степени перегрева уменьшается размер критического зародыша аустенита, увеличиваются скорость возникновения зародышей и скорость их роста
Образующиеся зерна аустенита имеют вначале такую же концентрацию углерода, как и феррит. Затем в аустените начинает растворяться вторая фаза перлита – цементит, следовательно, концентрация углерода увеличивается. Превращение в
идет быстрее. После того, как весь цементит растворится, аустенит неоднороден по химическому составу: там, где находились пластинки цементита концентрация углерода более высокая. Для завершения процесса перераспределения углерода в аустените требуется дополнительный нагрев или выдержка.
Величина образовавшегося зерна аустенита оказывает влмяние на свойства стали.
Рост зерна аустенита. Образующиеся зерна аустенита получаются мелкими (начальное зерно). При повышении температуры или выдержке происходит рост зерна аустенита. Движущей силой роста является разность свободных энергий мелкозернистой (большая энергия) и крупнозернистой (малая энергия) структуры аустенита.
Стали различают по склонности к росту зерна аустенита. Если зерно аустенита начинает быстро расти даже при незначительном нагреве выше температуры , то сталь наследственно крупнозернистая. Если зерно растет только при большом перегреве, то сталь наследственно мелкозернистая.
Склонность к росту аустенитного зерна является плавочной характеристикой. Стали одной марки, но разных плавок могут различаться, так как содержат неодинаковое количество неметаллических включений, которые затрудняют рост аустенитного зерна.
Ванадий, титан, молибден, вольфрам, алюминий – уменьшают склонность к росту зерна аустенита, а марганец и фосфор – увеличивают ее.
Заэвтектоидные стали менее склонны к росту зерна.
При последующем охлаждении зерна аустенита не измельчаются. Это следует учитывать при назначении режимов термической обработки, так как от размера зерна зависят механические свойства. Крупное зерно снижает сопротивление отрыву, ударную вязкость, повышает порог хладоломкости.
Различают величину зерна наследственного и действительного.
Для определения величины наследственного зерна, образцы нагревают до 930o С и затем определяют размер зерна.
Действительная величина зерна – размер зерна при обычных температурах. полученный после той или иной термической обработки.
Неправильный режим нагрева может привести либо к перегреву, либо к пережогу стали.
Перегрев. Нагрев доэвтектоидной стали значительно выше температуры приводит к интенсивному росту зерна аустенита. При охлаждении феррит выделяется в виде пластинчатых или игольчатых кристаллов. Такая структура называется видманштеттовая структура и характеризуется пониженными механическими свойствами. Перегрев можно исправить повторным нагревом до оптимальных температур с последующим медленным охлаждением.
Пережог имеет место, когда температура нагрева приближается к температуре плавления. При этом наблюдается окисление границ зерен, что резко снижает прочность стали. Излом такой стали камневидный. Пережог – неисправимый брак.
2. Превращение аустенита в перлит при медленном охлаждении.
Превращение связано с диффузией углерода, сопровождается полиморфным превращением , выделением углерода из аустенита в виде цементита, разрастанием образовавшегося цементита.
В зависимости от степени переохлаждения различают три области превращения. Вначале, с увеличением переохлаждения скорость превращения возрастает, а затем убывает. При температуре 727 oС и ниже 200o С скорость равна нулю. При температуре 200o С равна нулю скорость диффузии углерода.
Закономерности превращения.
Образцы нагревают до температуры, при которой структура состоит из однородного аустенита (7700 С). Затем переносят в термостаты с заданной температурой (интервал 25 – 500 С). Превращение аустенита можно легко обнаружить с помощью наблюдений за изменением магнитных характеристик, так как аустенит парамагнитен, а феррит и цементит обладают магнитными свойствами.
Получают серию кинетических кривых (рис. 12.5 а), которые показывают количество образовавшегося перлита в зависимости от времени, прошедшего с начала превращения.
Рис. 12.5. Кинетические кривые превращения аустенита при охлаждении (а); диаграмма изотермического превращения аустенита (б)
В начале наблюдается инкубационный подготовительный период, время, в течение которого сохраняется переохлажденный аустенит. Превращение протекает с различной скоростью и достигает максимума при образовании 50 % продуктов распада.
Затем скорость начинает уменьшаться и постепенно затухает. С увеличением степени переохлаждения устойчивость аустенита уменьшается, а затем увеличивается.
Горизонтальная линия Мн показывает температуру начала бездиффузного мартенситного превращения. Такие диаграммы называются диаграммами изотермического превращения аустенита (рис. 12.5 б).
При малых степенях переохлаждения, в области температур 727…550o С, сущность превращения заключается в том, что в результате превращения аустенита образуется механическая смесь феррита и цементита, состав которой отличается от состава исходного аустенита. Аустенит содержит 0,8 % углерода, а образующиеся фазы: феррит –0,02 %, цементит – 6,67 % углерола.
Время устойчивости аустенита и скорость его превращения зависят от степени переохлаждения.
Максимальная скорость превращения соответствует переохлаждению ниже температуры на 150…200o С, то есть соответствует минимальной устойчивости аустенита.
Механизм превращения представлен на рис. 12.6.
Рис. 12.6. Механизм превращения аустенита в перлит
При образовании перлита из аустенита ведущей фазой является цементит. Зарождение центров кристаллизации цементита облегчено на границе аустенитных зерен. Образовавшаяся пластинка цементита растет, удлиняется и обедняет соседние области углеродом. Рядом с ней образуются пластинки феррита. Эти пластинки растут как по толщине, так и по длине. Рост образовавшихся колоний перлита продолжается до столкновения с кристаллами перлита, растущими из других центров.
Свойства и строение продуктов превращения аустенита зависят от температуры, при которой происходит процесс его распада.
Толщина соседних пластинок феррита и цементита определяет дисперсность структуры и обозначается . Она зависит от температуры превращения. В зависимости от дисперсности продукты распада имеют различное название.
мм – перлит.
Образуется при переохлаждении до температуры Т = 650…700 oС, или при скорости охлаждения Vохл = 30…60 oС/ч. Твердость составляет 180…250 НВ.
мм – сорбит
Образуется при переохлаждении до температуры Т = 600…650 oС, или при скорости охлаждения Vохл = 60 oС/с. Твердость составляет 250…350 НВ. Структура характеризуется высоким пределом упругости, достаточной вязкостью и прочностью.
мм – троостит
Образуется при переохлаждении до температуры Т = 550…600 oС, или при скорости охлаждения Vохл = 150 oС/с. Твердость составляет 350…450 НВ. Структура характеризуется высоким пределом упругости, малой вязкостью и лпастичностью.
Твердость ферритно-цементитной смеси прямопропорциональна площади поверхности раздела между ферритом и цементитом..
Если температура нагрева незначительно превышала теипературу А и полученый аустенит неоднороден по составу, то при малой степени переохлаждения образуется зернистый леплит.
Промежуточное превращение
При температуре ниже 550 oС самодиффузия атомов железа практически не происходит, а атомы углерода обладают достаточной подвижностью.
Механизм превращения состоит в том, что внутри аустенита происходит перераспределение атомов углерода и участки аустенита, обогащенные углеродом превращаются в цементит.
Превращение обедненного углеродом аустенита в феррит происходит по сдвиговому механизму, путем возникновения и роста зародышей феррита. Образующиеся при этом кристаллы имеют игольчатую форму.
Такая структура, состоящая из цементита и феррита, называется бейнитом. Особенностью является повышенное содержание углерода в феррите (0.1…0.2 %).
Дисперсность кристаллов феррита и цементита зависят от температуры превращения.
При температуре мм – верхний бейнит. Структура характеризуется недостаточной прочностью, при низких относительном удлинении (
) и ударной вязкости (
).
При температуре 300oС – – нижний бейнит. Структура характеризуется высокой прочностью в сочетании с пластичностью и вязкостью.
Лекция 13
Основы теории термической обработки стали (продолжение)
Технологические особенности и возможности отжига и нормализации.
1. Превращение аустенита в мартенсит при высоких скоростях охлаждения
2. Превращение мартенсита в перлит.
3. Технологические возможности и особенности отжига, нормализации, закалки и отпуска
4. Отжиг и нормализация. Назначение и режимы
5. Отжиг первого рода.
3. Превращение аустенита в мартенсит при высоких скоростях охлаждения
Данное превращение имеет место при высоких скоростях охлаждения, когда диффузионные процессы подавляются. Солровождается полиморфным превращением в
При охлаждении стали со скоростью, большей критической (V > Vк), превращение начинается при температуре начала мартенситного превращения (Мн) и заканчивается при температуре окончания мартенситного превращения (Мк). В результате такого превращения аустенита образуется продукт закалки – мартенсит.
Минимальная скорость охлаждения Vк, при которой весь аустенит переохлаждается до температуры т.Мн и превращается, называется критической скоростью закалки.
Так как процесс диффузии не происходит, то весь углерод аустенита остается в решетке и располагается либо в ценрах тетраэдров, либо в середине длинных ребер (рис. 13.1).
Мартенсит – пересыщенный твердый раствор внедрения углерода в .
При образовании мартенсита кубическая решетка сильно искажается, превращаясь в тетрагональную (рис. 13.1 а). Искажение решетки характеризуется степенью тетрагональности: с/а > 1. Степень тетрагональности прямопролорциональна содержанию углерода в стали (рис. 13.1 б).
Рис. 13 1. Кристаллическая решетка мартенсита (а); влияние содержания углерода на параметры а и с решетки мартенсита (б)
Механизм мартенситного превращения имеет ряд особенностей.
1. Бездиффузионный характер.
Превращение осуществляется по сдвиговому механизму. В начале превращения имеется непрерывный переход от решетки аустенита к решетке мартенсита (когерентная связь). При превращении гранецентрированной кубической решетки в объемно-центрированную кубическую атомы смещаются на расстояния меньше межатомных, т.е. нет необходимости в самодиффузии атомов железа.
2. Ориентированность кристаллов мартенсита.
Кристаллы имеют форму пластин, сужающихся к концу, под микроскопом такая структура выглядит как игольчатая. Образуясь мгновенно пластины растут либо до границы зерна аустенита, либо до дефекта. Следующие пластины расположены к первым под углами 60 o или 120 o, их размеры ограничены участками между первыми пластинами (рис. 13.2).
Рис. 13.2. Ориентированность кристаллов мартенсита
Ориентированный (когерентный) рост кристаллов мартенсита обеспечивает минимальную поверхностную энергию. При когерентном росте, из-за различия объемов аустенита и мартенсита, возникают большие напряжения. При достижении определенной величины кристаллов мартенсита, эти напряжения становятся равными пределу текучести аустенита. В результате этого нарушается когерентность и происходит отрыв решетки мартенсита от решетки аустенита. Рост кристаллов прекращается.
3. Очень высокая скорость роста кристалла, до 1000 м/с.
4. Мартенситное превращение происходит только при непрерывном охлаждении. Для каждой стали начинается и заканчивается при определенной температуре, независимо от скорости охлаждения. Температуру начала мартенситного превращения называют мартенситной точкой МН, а температуру окончания превращения – МК. Температуры МН и МК зависят от содержания углерода и не зависят от скорости охлаждения Для сталей с содержанием углерода выше 0,6 % МК уходит в область отрицательных температур (рис.13.3)
Рис. 13.3. Зависимость температур начала (МН) и конца (МК)мартенситного превращения от содержания углерода в стали
Мартенситное превращение чувствительно к напряжениям, и деформация аустенита может вызвать превращение даже при температурах выше МН.
В сталях с МК ниже 20oС присутствует аустенит остаточный, его количество тем больше, чем ниже МН и МК.(при содержании углерода 0,6…1,0 % количество аустенита остаточного – 10 %, при содержании углерода 1,5 % - до 50 %). В микроструктуре наблюдается в виде светлых полей между иглами мартенсита.
5. Превращение необратимое. Получить аустенит из мартенсита невозможно.
Свойства мартенсита обусловлены особенностями его образования. Он характеризуется высокой твердостью и низкой пластичностью, что обуславливает хрупкость.
Твердость составляет до 65 HRC. Высокая твердость вызвана влиянием внедренных атомов углерода в решетку -фазы, что вызывает ее искажение и возникновение напряжений. С повышением содержания углерода в стали возрастает склонность к хрупкому разрушению.
4. Превращение мартенсита в перлит.
Имеет место при нагреве закаленных сталей. Превращение связано с диффузией углерода.
Мартенсит закалки неравновесная структура, сохраняющаяся при низких температурах. Для получения равновесной структуры изделия подвергают отпуску.
При нагреве закаленной стали происходят следующие процессы.
При нагреве до 200oС происходит перераспределение углерода в мартенсите. Образуются пластинки – карбидов толщиной несколько атомных диаметров. На образование карбидов углерод расходуется только из участков мартенсита, окружающих кристаллы выделившихся карбидов. Концентрация углерода на этих участках резко падает, тогда как удаленные участки сохраняют концентрацию углерода. В стали присутсвуют карбиды и два
-твердых раствора мартенсита (с высокой и низкой концентрацией углерода. Такой тип распада мартенсита называется прерывистым. Скорость диффузии мала, карбиды не увеличиваются, распад мартенсита сопровождается зарождением новых карбидных частиц. Таким образом имеем структуру с неравномерным распределением углерода – это мартенсит отпуска. При этом несколько снижается тетрагональность решетки.
При нагреве до 300oС идет рост образовавшихся карбидов. Карбиды выделяются из мартенсита и он обедняется углеродом. Диффузия углерода увеличивается и карбиды растут в результате притока углерода из областей твердого раствора с высокой его концентрацией. Кристаллическая решетка карбидов когерентно связана с решеткой мартенсита.
В высокоуглеродистых сталях аустенит остаточный превращается в мартенсит отпуска. Наблюдается снижение тетрагональности решетки и внутренних напряжений. Структура – мартенсит отпуска:
При нагреве до 400oС весь избыточный углерод выделяется из . Карбидные частицы полностью обособляются, приобретают строение цементита, и начинают расти. Форма карбидных частиц приближается к сферической.
Высокодисперсная смесь феррита и цементита называется троостит отпуска;
При нагреве выше 400oС изменение фазового состава не происходит, изменяется только микроструктура. Имеет место рост и сфероидизация цементита. Наблюдается растворение мелких и рост крупных карбидных частиц.
При температуре 550…600oС имеем сорбит отпуска. Карбиды имеют зернистое строение. Улучшаются свойства стали.
При температуре 650…700oС получают более грубую ферритно- цементитную смесь – перлит отпуска (зернистый перлит).
Технологические возможности и особенности отжига, нормализации, закалки и отпуска
При разработке технологии необходимо установить:
· режим нагрева деталей (температуру и время нагрева);
· характер среды, где осуществляется нагрев и ее влияние на материал стали;
· условия охлаждения.
Режимы термической обработки назначают в соответствии с диаграммами состояния и диаграммой изотермического распада аустенита.
Нагрев может осуществляться в нагревательных печах, топливных или электрических, в соляных ваннах или в ваннах с расплавленным металлом, пропусканием через изделие электрического тока или в результате индукционного нагрева.
С точки зрения производительности, нагрев с максимальной скоростью уменьшает окалинообразование, обезуглероживание и рост аустенитного зерна. Однако необходимо учитывать перепад температур по сечению, что ведет к возникновению термических напряжений. Если растягивающие напряжения превысят предел прочности или предел текучести, то возможно коробление или образование трещин.
Рис. 13. 4. Левый угол диаграммы состояния железо – цементит и температурные области нагрева при термической обработке сталей
Скорость нагрева тем выше,чем менее легирована сталь, однороднее ее структура, проще конфигурация.
Скорость нагрева принимается 0,8…1 мин на 1 мм сечения. Время выдержки принимается около 20 % от времени нагрева.
Среда нагрева при нагреве в печи с газовой средой.
Составляющие могут оказывать на сталь различное действие:
· окисляющее (О2, СО2, Н2О);
· восстанавливающее (СО, СН4);
· обезуглероживающее (О2, Н2);
· науглероживающее (СО, СН4);
· нейтральное (N2, инертные газы).
Окисление с образованием окалины , препятствует получению высокой и равномерной твердости при закалке, приводит к изменению размеров, требует увеличения припусков на механическую обработку.
Обезуглероживание (выгорание углерода в поверхностном слое металла) способствует появлению мягких пятен при закалке и возникновению растягивающих напряжений в поверхностном слое, снижающих усталостную прочность.
На рис. 13.4 показаны температурные области нагрева при термической обработке сталей.
Отжиг и нормализация. Назначение и режимы
Отжиг, снижая твердость и повышая пластичность и вязкость за счет получения равновесной мелкозернистой структуры, позволяет:
· улучшить обрабатываемость заготовок давлением и резанием;
· исправить структуру сварных швов, перегретой при обработке давлением и литье стали;
· подготовить структуру к последующей термической обработке.
Характерно медленное охлаждение со скоростью 30…100oС/ч.
Отжиг первого рода.
1. Диффузионный (гомогенизирующий) отжиг. Применяется для устранения ликвации, выравнивания химического состава сплава.
В его основе – диффузия. В результате нагрева выравнивается состав, растворяются избыточные карбиды. Применяется, в основном, для легированных сталей.
Температура нагрева зависит от температуры плавления, ТН = 0,8 Тпл.
Продолжительность выдержки: часов.
2. Рекристаллизационный отжиг проводится для снятия напряжений после холодной пластической деформации.
Температура нагрева связана с температурой плавления: ТН = 0,4 Тпл.
Продолжительность зависит от габаритов изделия.
3. Отжиг для снятия напряжений после горячей обработки (литья, сварки, обработки резанием, когда требуется высокая точность размеров).
Температура нагрева выбирается в зависимости от назначения, находится в широком диапазоне: ТН = 160……700oС.
Продолжительность зависит от габаритов изделия.
Детали прецизионных станков (ходовые винты, высоконагруженные зубчатые колеса, червяки) отжигают после основной механической обработки при температуре 570…600oС в течение 2…3 часов, а после окончательной механической обработки, для снятия шлифовочных напряжений – при температуре 160…180oС в течение 2…2,5 часов.
Отжиг второго рода предназначен для изменения фазового состава.
Температура нагрева и время выдержки обеспечивают нужные структурные превращения. Скорость охлаждения должна быть такой, чтобы успели произойти обратные диффузионные фазовые превращения.
Является подготовительной операцией, которой подвергают отливки, поковки, прокат. Отжиг снижает твердость и прочность, улучшает обрабатываемость резанием средне- и высокоуглеродистых сталей. Измельчая зерно, снижая внутренние напряженияи уменьшая структурную неоднородность способствует повышению пластичности и вязкости.
В зависимости от температуры нагрева различают отжиг:
1. полный, с температурой нагрева на 30…50 oС выше критической температуры А3
Проводится для доэвтектоидных сталей для исправления структуры.
При такой температуре нагрева аустенит получается мелкозернистый, и после охлаждения сталь имеет также мелкозернистую структуру.
2. неполный, с температурой нагрева на 30…50oС выше критической температуры А1
Применяется для заэвтектоидных сталей. При таком нагреве в структуре сохраняется цементит вторичный, в результате отжига цементит приобретает сферическую форму (сфероидизация). Получению зернистого цементита способствует предшествующая отжигу горячая пластическая деформация, при которой дробится цементитная сетка.Структура с зернистым цементитом лучше обрабатываются и имеют лучшую структуру после закалки. Неполный отжиг является обязательным для инструментальных сталей.
Иногда неполный отжиг применяют для доэвтектоидных сталей, если не требуется исправление структуры (сталь мелкозернистая), а необходимо только понизить твердость для улучшения обрабатываемости резанием.
3. циклический или маятниковый отжиг применяют, если после проведения неполного отжига цементит остается пластинчатым. В этом случае после нагрева выше температуры А1 следует охлаждение до 680 oС, затем снова нагрев до температуры 750…760) oС и охлаждение. В результате получают зернистый цементит.
4. изотермический отжиг – после нагрева до требуемой температуры, изделие быстро охлаждают до температуры на 50…100oС ниже критической температуры А1 и выдерживают до полного превращения аустенита в перлит, затем охлаждают на спокойном воздухе (рис. 13.5). Температура изотермической выдержки близка к температуре минимальной устойчивости аустенита.
В результате получают более однородную структуру, так как превращение происходит при одинаковой степени переохлаждения. Значительно сокращается длительность процесса. Применяют для легированных сталей.
Рис. 13.5. Режимы изотермического отжига
5. Нормализация. – разновидность отжига.
Термическая обработка, при которой изделие нагревают до аустенитного состояния, на 30…50 oС выше А3 или Аст с последующим охлаждением на воздухе.
или
В результате нормализации получают более тонкое строение эвтектоида (тонкий перлит или сорбит), уменьшаются внутренние напряжения, устраняются пороки, полученные в процессе предшествующей обработки. Твердость и прочность несколько выше чем после отжига.
В заэвтектоидных сталях нормализация устраняет грубую сетку вторичного цементита.
Нормализацию чаще применяют как промежуточную операцию, улучшающую структуру. Иногда проводят как окончательную обработку, например, при изготовлении сортового проката.
Для низкоуглеродистых сталей нормализацию применяют вместо отжига.
Для среднеуглеродистых сталей нормализацию или нормализацию с высоким отпуском применяют вместо закалки с высоким отпуском. В этом случае механические свойства несколько ниже, но изделие подвергается меньшей деформации, исключаются трещины.
Лекция 14
Технологические особенности и возможности закалки и отпуска
1. Закалка
2. Способы закалки
3. Отпуск
4. Отпускная хрупкость
Закалка
Конструкционные стали подвергают закалке и отпуску для повышения прочности и твердости, получения высокой пластичности, вязкости и высокой износостойкости, а инструментальные – для повышения твердости и износостойкости.
Верхний предел температур нагрева для заэвтектоидных сталей ограничивается, так как приводит к росту зерна, что снижает прочность и сопротивление хрупкому разрушению.
Основными параметрами являются температура нагрева и скорость охлаждения. Продолжительность нагрева зависит от нагревательного устройства, по опытным данным на 1 мм сечения затрачивается: в электрической печи – 1,5…2 мин.; в пламенной печи – 1 мин.; в соляной ванне – 0,5 мин.; в свинцовой ванне – 0,1…0,15 мин.
По температуре нагрева различают виды закалки:
– полная, с температурой нагрева на 30…50oС выше критической температуры А3
.
Применяют ее для доэвтектоидных сталей. Изменения структуры стали при нагреве и охлаждении происходят по схеме:
.
Неполная закалка доэвтектоидных сталей недопустима, так как в структуре остается мягкий феррит. Изменения структуры стали при нагреве и охлаждении происходят по схеме:
– неполная с температурой нагрева на 30…50 oС выше критической температуры А1
Применяется для заэвтектоидных сталей. Изменения структуры стали при нагреве и охлаждении происходят по схеме:
.
После охлаждения в структуре остается вторичный цементит, который повышает твердость и износостойкость режущего инструмента.
После полной закалки заэвтектоидных сталей получают дефектную структуру грубоигольчатого мартенсита.
Заэвтектоидные стали перед закалкой обязательно подвергают отжигу – сфероидизации, чтобы цементит имел зернистую форму.
Охлаждение при закалке.
Для получения требуемой структуры изделия охлаждают с различной скоростью, которая в большой степени определяется охлаждающей средой, формой изделия и теплопроводностью стали.
Режим охлаждения должен исключить возникновение больших закалочных напряжений. При высоких скоростях охлаждения при закалке возникают внутренние напряжения, которые могут привести к короблению и растрескиванию.
Внутренние напряжения, уравновешиваемые в пределах макроскопических частей тела, называются напряжениями I рода. Они ответственны за искажение формы (коробление) и образование трещин при термообработке. Причинами возникновения напряжений являются:
· различие температуры по сечению изделия при охлаждении;
· разновременное протекание фазовых превращений в разных участках изделия.
Для предупреждения образования трещин необходимо избегать растягивающих напряжений в поверхностных слоях изделия. На характер распределения напряжений при закалке, помимо режима охлаждения, оказывает влияние и температура нагрева под закалку. Перегрев содействует образованию закалочных трещин, увеличивает деформации.
Режим охлаждения должен также обеспечить необходимую глубину закаленного слоя.
Оптимальный режим охлаждения: максимальная скорость охлаждения в интервале температур А1 – MН, для предотвращения распада переохлажденного аустенита в области перлитного превращения, и минимальная скорость охлаждения в интервале температур мартенситного превращения MН – MК, с целью снижения остаточных напряжений и возможности образования трещин. Очень медленное охлаждение может привести к частичному отпуску мартенсита и увеличению количества аустенита остаточного, а следовательно к снижению твердости.
В качестве охлаждающих сред при закалке используют воду при различных температурах, технические масла, растворы солей и щелочей, расплавленные металлы.
Вода имеет существенный недостаток: высокая скорость охлаждения в интервале мартенситного превращения приводит к образованию закалочных дефектов. С повышением температуры воды ухудшается ее закалочная способность.
Наиболее высокой и равномерной охлаждающей способностью отличаются холодные 8…12 %-ные водные растворы NaCl и NaOH. Они мгновенно разрушают паровую рубашку и охлаждение происходит более равномерно и на стадии пузырькового кипения.
Увеличения охлаждающей способности достигают при использовании струйного или душевого охлаждения, например, при поверхностной закалке.
Для легированных сталей с высокой устойчивостью аустенита используют минеральное масло (нефтяное). Обеспечивающее небольшую скорость охлаждения в интервале температур мартенситного превращения и постоянство закаливающей способности. Недостатками минеральных масел являются повышенная воспламеняемость, низкая охлаждающая способность в интервале температур перлитного превращения, высокая стоимость.
При выборе охлаждающей среды необходимо учитывать закаливаемость и прокаливаемость стали.
Закаливаемость – способность стали приобретать высокую твердость при закалке.
Закаливаемость определяется содержанием углерода. Стали с содержанием углерода менее 0,20 % не закаливаются.
Прокаливаемость – способность получать закаленный слой с мартенситной и троосто-мартенситной структурой, обладающей высокой твердостью, на определенную глубину.
За глубину закаленной зоны принимают расстояние от поверхности до середины слоя, где в структуре одинаковые объемы мартенсита и троостита.
Чем меньше критическая скорость закалки, тем выше прокаливаемость. Укрупнение зерен повышает прокаливаемость.
Если скорость охлаждения в сердцевине изделия превышает критическую то сталь имеет сквозную прокаливаемость.
Нерастворимые частицы и неоднородность аустенита уменьшают прокаливаемость.
Характеристикой прокаливаемости является критический диаметр.
Критический диаметр – максимальное сечение, прокаливающееся в данном охладителе на глубину, равную радиусу изделия.
С введением в сталь легирующих элементов закаливаемость и прокаливаемость увеличиваются (особенно молибден и бор, кобальт – наоборот).
Способы закалки
В зависимости от формы изделия, марки стали и нужного комплекса свойств применяют различные способы охлаждения (рис. 14.1)
Рис.14.1. Режимы закалки
1. Закалка в одном охладителе (V1).
Нагретую до нужной температуры деталь переносят в охладитель и полностью охлаждают. В качестве охлаждающей среды используют:
· воду – для крупных изделий из углеродистых сталей;
· масло – для небольших деталей простой формы из углеродистых сталей и изделий из легированных сталей.
Основной недостаток – значительные закалочные напряжения.
2. Закалка в двух сферах или прерывистая (V2).
Нагретое изделие предварительно охлаждают в более резком охладителе (вода) до температуры ~ 3000C и затем переносят в более мягкий охладитель (масло).
Прерывистая закалка обеспечивает максимальное приближение к оптимальному режиму охлаждения.
Применяется в основном для закалки инструментов.
Недостаток: сложность определения момента переноса изделия из одной среды в другую.
3. Ступенчатая закалка (V3).
Нагретое до требуемой температуры изделие помещают в охлаждающую среду, температура которой на 30 – 50oС выше точки МН и выдерживают в течении времени, необходимого для выравнивания температуры по всему сечению. Время изотермической выдержки не превышает периода устойчивости аустенита при заданной температуре.
В качестве охлаждающей среды используют расплавленные соли или металлы. После изотермической выдержки деталь охлаждают с невысокой скоростью.
Способ используется для мелких и средних изделий.
4. Изотермическая закалка (V4).
Отличается от ступенчатой закалки продолжительностью выдержки при температуре выше МН, в области промежуточного превращения. Изотермическая выдержка обеспечивает полное превращение переохлажденного аустенита в бейнит.При промежуточном превращении легированных сталей кроме бейнита в структуре сохраняется аустенит остаточный. Образовавшаяся структура характеризуется сочетанием высокой прочности, пластичности и вязкости. Вместе с этим снижается деформация из-за закалочных напряжений, уменьшаются и фазовые напряжения.
В качестве охлаждающей среды используют расплавленные соли и щелочи.
Применяются для легированных сталей.
5. Закалка с самоотпуском.
Нагретые изделия помещают в охлаждающую среду и выдерживают до неполного охлаждения. После извлечения изделия, его поверхностные слои повторно нагреваются за счет внутренней теплоты до требуемой температуры, то есть осуществляется самоотпуск. Применяется для изделий, которые должны сочетать высокую твердость на поверхности и высокую вязкость в сердцевине (инструменты ударного действия: мототки, зубила).
Отпуск
Отпуск является окончательной термической обработкой.
Целью отпуска является повышение вязкости и пластичности, снижение твердости и уменьшение внутренних напряжений закаленных сталей.
С повышением температуры нагрева прочность обычно снижается, а пластичность и вязкость растут. Температуру отпуска выбирают, исходя из требуемой прочности конкретной детали.
Различают три вида отпуска:
1. Низкий отпуск с температурой нагрева Тн = 150…300oС.
В результате его проведения частично снимаются закалочные напряжения. Получают структуру – мартенсит отпуска.
Проводят для инструментальных сталей; после закалки токами высокой частоты; после цементации.
2. Средний отпуск с температурой нагрева Тн = 300…450oС.
Получают структуру – троостит отпуска, сочетающую высокую твердость 40…45HRC c хорошей упругостью и вязкостью.
Используется для изделий типа пружин, рессор.
3. Высокий отпуск с температурой нагрева Тн = 450…650oС..
Получают структуру, сочетающую достаточно высокую твердость и повышенную ударную вязкость (оптимальное сочетание свойств) – сорбит отпуска.
Используется для деталей машин, испытывающих ударные нагрузки.
Комплекс термической обработки, включающий закалку и высокий отпуск, называется улучшением.
Отпускная хрупкость
Обычно с повышением температуры отпуска ударная вязкость увеличивается, а скорость охлаждения не влияет на свойства. Но для некоторых сталей наблюдается снижение ударной вязкости. Этот дефект называется отпускной хрупкостью (рис. 14.2).
Рис.14.2. Зависимость ударной вязкости от температуры отпуска
Отпускная хрупкость I рода наблюдается при отпуске в области температур около 300oС. Она не зависит от скорости охлаждения.
Это явление связано с неравномерностью превращения отпущенного мартенсита. Процесс протекает быстрее вблизи границ зерен по сравнению с объемами внутри зерна. У границ наблюдается концентрация напряжений, поэтому границы хрупкие.
Отпускная хрупкость I рода “необратима“, то есть при повторных нагревах тех же деталей не наблюдается.
Отпускная хрупкость II рода наблюдается у легированных сталей при медленном охлаждении после отпуска в области 450…650oС.
При высоком отпуске по границам зерен происходит образование и выделение дисперсных включений карбидов. Приграничная зона обедняется легирующими элементами. При последующем медленном охлаждении происходит диффузия фосфора к границам зерна. Приграничные зоны обогащаются фосфором, снижаются прочность и ударная вязкость. Этому дефекту способствуют хром, марганец и фосфор. Уменьшают склонность к отпускной хрупкости II рода молибден и вольфрам, а также быстрое охлаждение после отпуска.
Отпускная хрупкость II рода “обратима“, то есть при повторных нагревах и медленном охлаждении тех же сталей в опасном интервале температур дефект может повториться.
Стали, склонные к отпускной хрупкости II рода, нельзя использовать для работы с нагревом до 650oС без последующего быстрого охлаждения.
Лекция 17
Конструкционные материалы. Легированные стали.
1. Конструкционные стали.
2. Легированные стали
3. Влияние элементов на полиморфизм железа
4. Влияние легирующих элементов на превращения в стали
5. Влияние легирующих элементов на превращение перлита в аустенит.
6. Влияние легирующих элементов на превращение переохлажденного аустенита.
7. Влияние легирующих элементов на мартенситное превращение
8. Влияние легирующих элементов на преврашения при отпуске.
9. Классификация легированных сталей
Конструкционные стали.
К конструкционным сталям, применяемым для изготовления разнообразных деталей машин, предъявляют следующие требования:
· сочетание высокой прочности и достаточной вязкости
· хорошие технологические свойства
· экономичность
· недефицитность
Высокая конструкционная прочность стали, достигается путем рационального выбора химического состава, режимов термической обработки, методов поверхностного упрочнения, улучшением металлургического качества.
Решающая роль в составе конструкционных сталей отводится углероду. Он увеличивает прочность стали, но снижает пластичность и вязкость, повышает порог хладоломкости. Поэтому его содержание регламентировано и редко превышает 0,6 %.
Влияние на конструкционную прочность оказывают легирующие элементы. Повышение конструкционной прочности при легировании связано с обеспечением высокой прокаливаемости, уменьшением критической скорости закалки, измельчением зерна.
Применение упрочняющей термической обработки улучшает комплекс механических свойств.
Металлургическое качество влияет на конструкционную прочность. Чистая сталь при одних и тех же прочностных свойствах имеет повышенные характеристики надежности.
Легированные стали
Элементы, специально вводимые в сталь в определенных концентрациях с целью изменения ее строения и свойств, называются легирующими элементами, а стали – легированными.
Cодержание легируюшихх элементов может изменяться в очень широких пределах: хром или никель – 1% и более процентов; ванадий, молибден, титан, ниобий – 0,1… 0,5%; также кремний и марганец – более 1 %. При содержании легирующих элементов до 0,1 % – микролегирование.
В конструкционных сталях легирование осуществляется с целью улучшения механических свойств (прочности, пластичности). Кроме того меняются физические, химические, эксплуатационные свойства.
Легирующие элементы повышают стоимость стали, поэтому их использование должно быть строго обоснованно.
Достоинства легированных сталей:
· особенности обнаруживаются в термически обработанном состоянии, поэтому изготовляются детали, подвергаемые термической обработке;
· улучшенные легированные стали обнаруживают более высокие показатели сопротивления пластическим деформациям ( );
· легирующие элементы стабилизируют аустенит, поэтому прокаливаемость легированных сталей выше;
· возможно использование более «мягких» охладителей (снижается брак по закалочным трещинам и короблению), так как тормозится распад аустенита;
· повышаются запас вязкости и сопротивление хладоломкости, что приводит к повышению надежности деталей машин.
Недостатки:
· подвержены обратимой отпускной хрупкости II рода;
· в высоколегированных сталях после закалки остается аустенит остаточный, который снижает твердость и сопротивляемость усталости, поэтому требуется дополнительная обработка;
· склонны к дендритной ликвации, так как скорость диффузии легирующих элементов в железе мала. Дендриты обедняются, а границы – междендритный материал – обогащаются легирующим элементом. Образуется строчечная структура после ковки и прокатки, неоднородность свойств вдоль и поперек деформирования, поэтому необходим диффузионный отжиг.
· склонны к образованию флокенов.
Флокены – светлые пятна в изломе в поперечном сечении – мелкие трещины с различной ориентацией. Причина их появления – выделение водорода, растворенного в стали.
При быстром охлаждении от 200o водород остается в стали, выделяясь из твердого раствора, вызывает большое внутреннее давление, приводящее к образованию флокенов.
Меры борьбы: уменьшение содержания водорода при выплавке и снижение скорости охлаждения в интервале флокенообразования.
Влияние элементов на полиморфизм железа
Все элементы, которые растворяются в железе, влияют на температурный интервал существование его аллотропических модификаций (А = 911oС, А
=1392oС).
В зависимости от расположения элементов в периодической системе и строения кристаллической решетки легирующего элемента возможны варианты взаимодействия легирующего элемента с железом. Им соответствуют и типы диаграмм состояния сплавов системы железо – легирующий элемент (рис. 17.1)
Большинство элементов или повышают А и снижают А
, расширяя существовавшие
–модификации (рис.17.1.а), или снижают А4 и повышают А
, сужая область существования
– модификации (рис.17.1.б).
Рис. 17.1. Схематические диаграммы состояния Fe – легирующий элемент. а – для элементов, расширяющих область существования –модификации; б – для элементов, сужающих область существования
–модификации
Свыше определ¨нного содержания марганца, никеля и других элементов, имеющих гранецентрированную кубическую решетку, – состояние существует как стабильное от комнатной температуры до температуры плавления, такие сплавы на основе железа называются аустенитными.
При содержании ванадия, молибдена, кремния и других элементов, имеющих объемно-центрированную кубическую решетку. выше определ¨нного предела устойчивым при всех температурах является – состояние. Такие сплавы на основе железа называются ферритными.
Аустенитные и ферритные сплавы не имеют превращений при нагреве и охлаждении.
Влияние легирующих элементов на превращения в стали
Влияние легирующих элементов на превращение перлита в аустенит.
Легирующие элементы в большинстве случаев растворяются в аустените, образуя твердые растворы замещения. Легированные стали требуют более высоких температур нагрева и более длительной выдержки для получения однородного аустенита, в котором растворяются карбиды легирующих элементов.
Малая склонность к росту аустенитного зерна – технологическое преимущество большинства легированных сталей. Все легирующие элементы снижают склонность аустенитного зерна к росту, кроме марганца и бора. Элементы, не образующие карбидов (кремний, кобальт, медь, никель), слабо влияют на рост зерна. Карбидообразующие элементы (хром, молибден, вольфрам, ванадий, титан) сильно измельчают зерно.
Влияние легирующих элементов на превращение переохлажденного аустенита.
По влиянию на устойчивость аустенита и на форму С-образных кривых легирующие элементы разделяются на две группы.
Элементы, которые растворяются в феррите и цементите (кобальт, кремний, алюминий, медь, никель), оказывают только количественное влияние на процессы превращения. Замедляют превращение (большинство элементов), или ускоряют его (кобальт) (рис.17.2 а)
Рис 17.2. Влияние легирующих элементов на превращение переохлажденного аустенита: а – некарбидообразующие элементы; б — карбидообразующие элементы
Карбидообразующие элементы (хром, молибден, вольфрам, ванадий, титан) вносят и качественные изменения в кинетику изотермического превращения. При разных температурах они по разному влияют на скорость распада аустенита: при температуре 700…500oС — замедляют превращение в перлитной области, при температуре 500…400oС (образование троостита) – очень сильно замедляют превращение, при температуре 400…300oС (промежуточное превращение) – замедляет превращение аустенита в бейнит, но меньше, чем образование троостита. Это отражается на форме С-образных кривых: наблюдаются два максимума скорости изотермического распада, разделенных областью высокой устойчивости переохлажденного аустенита (рис. 17.2 б )
Температура максимальной устойчивости аустенита зависит от карбидообразующего элемента: хром – 400…500oС, вольфрам – 500…550oС, молибден – 550…575oС, ванадий – 575…600oС. Время максимальной устойчивости при заданной температуре возрастает с увеличением степени легированности (очень велико для высоколегированных сталей).
Важным является замедление скорости распада. Это способствует более глубокой прокаливаемости и переохлаждению аустенита до интервала мартенситного превращения при более медленном охлаждении (масло, воздух). Увеличивают прокаливаемость хром, никель, молибден, марганец, особенно при совместном легировании
Влияние легирующих элементов на мартенситное превращение
При нагреве большинство легирующих элементов растворяются в аустените. Карбиды титана и ниобия не растворяются. Эти карбиды тормозят рост аустенитного зерна при нагреве и обеспечивают получение мелкоигольчатого мартенсита при закалке. Остальные карбидообразующие элементы, а также некарбидообразующие, при нагреве растворяются в аустените и при закалке образуют легированный мартенсит.
Некоторые легирующие элементы (алюминий, кобальт) повышают мартенситную точку и уменьшают количество остаточного аустенита, другие не влияют на эту точку (кремний). Большинство элементов снижают мартенситную точку и увеличивают количество остаточного аустенита.
Влияние легирующих элементов на преврашения при отпуске.
Легирующие элементы замедляют процесс распада мартенсита: никель, марганец – незначительно; хром, молибден, кремний – заметно. Это связано с тем, что процессы при отпуске имеют диффузионный характер, а большинство элементов замедляют карбидное превращение. Легированные стали сохраняют структуру мартенсита отпуска до температуры 400…500oС. Так как в легированных сталях сохраняется значительное количество остаточного аустенита, то превращение его в мартенсит отпуска способствует сохранению твердости до высоких температур.
Таким образом, легированные стали при отпуске нагревают до более высоких температур или увеличивают выдержку.
Классификация легированных сталей
Стали классифицируются по нескольким признакам.
1. По структуре после охлаждения на воздухе выделяются три основных класса сталей:
· перлитный;
· мартенситный;
· аустенитный
Стали перлитного класса характеризуются малым содержанием легирующих элементов; мартенситного – более значительным содержанием; аустенитного – высоким содержанием легирующих элементов.
Классификация связана с кинетикой распада аустенита. Диаграммы изотермического распада аустенита для сталей различных классов представлены на рис. 17.3
Рис.17.3. Диаграммы изотермического распада аустенита для сталей перлитного (а), мартенситного (б) и аустенитного (в) классов
По мере увеличения содержания легирующих элементов устойчивость аустенита в перлитной области возрастает, а температупная область мартенситного превращения снижается.
Для сталей перлитного класса кривая скорости охлаждения на воздухе пересекает область перлитного распада (рис. 17.3.а), поэтому образуются структуры перлита, сорбита или троостита.
Для сталей мартенситного класса область перлитного распада сдвинута вправо (рис.17.3 б). Охлаждение на воздухе не приводит к превращению в перлитной области. Аустенит переохлаждается до температуры мартенситного превращения и происходит образование мартенсита.
Для сталей аустенитного класса увеличение содержания углерода и легирующих элементов сдвигает вправо область перлитного распада, а также снижает мартенситную точку, переводя ее в область отрицательных температур (рис. 17.3.в). Сталь охлаждается на воздухе до комнатной температуры, сохраняя аустенитное состояние.
2. По степени легирования (по содержанию легирующих элементов):
· низколегированные – 2,5…5 %;
· среднелегированные – до 10 %;
· высоколегированные – более 10%.
3. По числу легирующих элементов:
· трехкомпонентные (железо, углерод, легирующий элемент);
· четырехкомпонентные (железо, углерод, два легирующих элемента) и так далее.
4. По составу:
никелевые, хромистые, хромоникелевые, хромоникельмолибденовые и так далее (признак– наличие тех или иных легирующих элементов).
5. По назначению:
· конструкционные;
· инструментальные (режущие, мерительные, штамповые);
· стали и сплавы с особыми свойствами (резко выраженные свойства –нержавеющие, жаропрочные и термоустойчивые, износоустойчивые, с особыми магнитными и электрическими свойствами).
Лекция 18
Конструкционные стали. Классификация конструкционных сталей.
1. Классификация конструкционных сталей
2. Углеродистые стали.
3. Цементуемые и улучшаемые стали
4. Цементуемые стали.
5. Улучшаемые стали.
6. Высокопрочные, пружинные, шарикоподшипниковые, износостойкие и автоматные стали
7. Высокопрочные стали.
8. Пружинные стали.
9. Шарикоподшипниковые стали.
10. Стали для изделий, работающих при низких температурах
11. Износостойкие стали.
12. Автоматные стали.
Классификация конструкционных сталей
Машиностроительные стали предназначены для изготовления различных деталей машин и механизмов.
Они классифицируются:
· по химическому составу ( углеродистые и легированные);
· по обработке (цементуемые, улучшаемые);
· по назначению (пружинные, шарикоподшипниковые).
Углеродистые стали.
Низкоуглеродистые стали 05 кп, 08, 10, 10 пс обладают малой прочностью высокой пластичностью. Применяются без термической обработки для изготовления малонагруженных деталей – шайб, прокладок и т.п.
Среднеуглеродистые стали 35, 40, 45 применяются после нормализации, термического улучшения, поверхностной закалки.
В нормализованном состоянии по сравнению с низкоотпущенным обладают большей прочностью, но меньшей пластичностью. После термического улучшения наблюдается наилучшее сочетание механических свойств. После поверхностной закалки обладают высокой поверхностной твердостью и сопротивлением износу.
Высокоуглеродистые стали 60, 65, 70,75 используются как рессорно-пружинные после среднего отпуска. В нормализованном состоянии – для прокатных валков, шпинделей станков.
Достоинства углеродистых качественных сталей – дешевизна и технологичность. Но из-за малой прокаливаемости эти стали не обеспечивают требуемый комплекс механических свойств в деталях сечением более 20 мм.
Цементуемые и улучшаемые стали
Цементуемые стали.
Используются для изготовления деталей, работающих на износ и подвергающихся действию переменных и ударных нагрузок. Детали должны сочетать высокую поверхностную прочность и твердость и достаточную вязкость сердцевины.
Цементации подвергаются низкоуглеродистые стали с содержанием углерода до 0,25%, что позволяет получить вязкую сердцевину. Для деталей, работающих с большими нагрузками, применяются стали с повышенным содержанием углерода (до 0,35 %).
С повышением содержания углерода прочность сердцевины увеличивается, а вязкость снижается. Детали подвергаются цианированию и нитроцементации.
Цементуемые углеродистые стали 15,20,25 используются для изготовления деталей небольшого размера, работающих в условиях изнашивания при малых нагрузках (втулки, валики, оси, шпильки и др.). Твердость на поверхности составляет 60…64 HRC, сердцевина остается мягкой.
Цементуемые легированные стали применяют для более крупных и тяжелонагруженных деталей, в которых необходимо иметь, кроме высокой твердости поверхности, достаточно прочную сердцевину (кулачковые муфты, поршни, пальцы, втулки).
Хромистые стали 15Х, 20Х используются для изготовления небольших изделий простой формы, цементуемых на глубину h =1…1,5 мм. При закалке с охлаждением в масле, выполняемой после цементации, сердцевина имеет бейнитное строение. Вследствие этого хромистые стали обладают более высокими прочностными свойствами при несколько меньшей пластичности в сердцевине и большей прочностью в цементованном слое.
Дополнительное легирование хромистых сталей ванадием (сталь 15ХФ), способствует получению более мелкого зерна, что улучшает пластичность и вязкость.
Никель увеличивает глубину цементованного слоя, препятствует росту зерна и образованию грубой цементитной сетки, оказывает положительное влияние на свойства сердцевины. Хромоникелевые стали 20ХН, 12ХН3А применяют для изготовления деталей средних и больших размеров, работающих на износ при больших нагрузках (зубчатые колеса, шлицевые валы). Одновременное легирование хромом и никелем, который растворяется в феррите, увеличивает прочность, пластичность и вязкость сердцевины и цементованного слоя. Стали мало чувствительны к перегреву. Большая устойчивость переохлажденного аустенита в области перлитного и промежуточного превращений обеспечивает высокую прокаливаемость хромоникелевых сталей и позволяет проводить закалку крупных деталей с охлаждением в масле и на воздухе.
Стали, дополнительно легированные вольфрамом или молибденом (18Х2Н4ВА, 18Х2Н4МА), применяют для изготовления крупных тяжелонагруженных деталей. Эти стали являются лучшими конструкционными сталями, но дефицитность никеля ограничивает их применение.
Хромомарганцевые стали применяют вместо дорогих хромоникелевых, однако эти стали менее устойчивы к перегреву и имеют меньшую вязкость. Введение небольшого количества титана (0,06…0,12 %) уменьшает склонность стали к перегреву (стали 18ХГТ, 30ХГТ).
С целью повышения прочности применяют легирование бором (0,001…0,005 %) 20ХГР, но бор способствует росту зерна при нагреве.
Улучшаемые стали.
Стали, подвергаемые термическому улучшению, широко применяют для изготовления различных деталей, работающих в сложных напряженных условиях ( при действии разнообразных нагрузок, в том числе переменных и динамических). Стали приобретают структуру сорбита, хорошо воспринимающую ударные нагрузки. Важное значение имеет сопротивление хрупкому разрушению.
Улучшению подвергаются среднеуглеродистые стали с содержанием углерода 0,30…0,50 %.
Улучшаемые углеродистые стали 35, 40, 45 дешевы, из них изготавливают детали, испытывающие небольшие напряжения (сталь 35), и детали, требующие повышенной прочности (стали 40, 45). Но термическое улучшение этих сталей обеспечивает высокий комплекс механических свойств только в деталях небольшого сечения, так как стали обладают низкой прокаливаемостью. Стали этой группы можно использовать и в нормализованном состоянии.
Детали, требующие высокой поверхностной твердости при вязкой сердцевине (зубчатые колеса, валы, оси, втулки), подвергаются поверхностной закалке токами высокой частоты. Для снятия напряжений проводят низкий отпуск.
Улучшаемые легированные стали.
Улучшаемые легированные стали применяют для более крупных и более нагруженных ответственных деталей. Стали обладают лучшим комплексом механических свойств: выше прочность при сохранении достаточной вязкости и пластичности, ниже порог хладоломкости.
Хромистые стали 30Х, 40Х, 50Х используются для изготовления небольших средненагруженных деталей. Эти стали склонны к отпускной хрупкости, поэтому после высокого отпуска охлаждение должно быть быстрым.
Повышение прокаливаемости достигается микролегированием бором (35ХР). Введение в сталь ванадия значительно увеличивает вязкость (40ХФА).
Хромокремнистые (33ХС) и хромокремниймарганцевые (хромансил) (25ХГСА) стали обладают высокой прочностью и умеренной вязкостью. Стали хромансилы обладают высокой свариваемостью, из них изготавливают стыковочные сварные узлы, кронштейны, крепежные и другие детали. Широко применяются в автомобилестроении и авиации.
Хромоникелевые стали 45ХН, 30ХН3А отличаются хорошей прокаливаемостью, прочностью и вязкостью, но чувствительны к обратимой отпускной хрупкости. Для уменьшения чувствительности вводят молибден или вольфрам. Ванадий способствует измельчению зерна.
Стали 36Х2Н2МФА, 38ХН3ВА др. обладают лучшими свойствами, относятся к мартенситному классу, слабо разупрочняются при нагреве до 300…400 oС. из них изготавливаются валы и роторы турбин, тяжелонагруженные детали редукторов и компрессоров.
Высокопрочные, пружинные, шарикоподшипниковые, износостойкие и автоматные стали
Высокопрочные стали.
Высокопрочными называют стали, имеющие предел прочности более 1500 МПа, который достигается подбором химического состава и оптимальной термической обработки.
Такой уровень прочности можно получить в среднеуглеродистых легированных сталях, (30ХГСН2А,40ХН2МА), применяя закалку с низким отпуском (при температуре 200…250oС) или изотермическую закалку с получением структуры нижнего бейнита.
После изотермической закалки среднеуглеродистые легированные стали имеют несколько меньшую прочность, но большую пластичность и вязкость. Поэтому они более надежны в работе, чем закаленные и низкоотпущенные.
При высоком уровне прочности закаленные и низкоотпущенные среднеуглеродистые стали обладают повышенной чувствительностью к концентраторам напряжения, склонностью к хрупкому разрушению, поэтому их рекомендуется использовать для работы в условиях плавного нагружения.
Легирование вольфрамом, молибденом, ванадием затрудняет разупрочняющие процессы при температуре 200…300 oС, способствует получению мелкого зерна, понижает порог хладоломкости, повышает сопротивление хрупкому разрушению.
Высокая прочность может быть получена и за счет термомеханической обработки.
Стали 30ХГСА, 38ХН3МА после низкотемпературной термомеханической обработки имеют предел прочности 2800 МПа, относительное удлинение и ударная вязкость увеличиваются в два раза по сравнению с обычной термической обработкой. Это связано с тем, что частичное выделение углерода из аустенита при деформации облегчает подвижность дислокаций внутри кристаллов мартенсита, что способствует увеличению пластичности.
Мартенситно-стареющие стали (03Н18К9М5Т, 04Х11Н9М2Д2ТЮ) превосходят по конструкционной прочности и технологичности среднеуглеродистые легированные стали. Они обладают малой чувствительностью к надрезам, высоким сопротивлением хрупкому разрушению и низким порогом хладоломкости при прочности около 2000 МПа.
Мартенситно-стареющие стали представляют собой безуглеродистые сплавы железа с никелем (8..25 %), дополнительно легированные кобальтом, молибденом, титаном, алюминием, хромом и другими элементами. Благодаря высокому содержанию никеля, кобальта и малой концентрации углерода в результате закалки в воде или на воздухе фиксируется высокопластичный, но низкопрочный железоникелевый мартенсит, пересыщенный легирующими элементами. Основное упрочнение происходит в процессе старения при температуре 450…550 oС за счет выделения из мартенситной матрицы когерентно с ней связанных мелкодисперсных фаз. Мартенситно-стареющие стали обладают высокой конструкционной прочностью в интервале температур от криогенных до 500 oС и рекомендуются для изготовления корпусов ракетных двигателей, стволов артиллерийского и стрелкового оружия, корпусов подводных лодок, батискафов, высоконагруженных дисков турбомашин, зубчатых колес, шпинделей, червяков и т.д.
Пружинные стали.
Пружины, рессоры и другие упругие элементы являются важнейшими деталями различных машин и механизмов. В работе они испытывают многократные переменные нагрузки. Под действием нагрузки пружины и рессоры упруго деформируются, а после прекращения действия нагрузки восстанавливают свою первоначальную форму и размеры. Особенностью работы является то, что при значительных статических и ударных нагрузках они должны испытывать только упругую деформацию, остаточная деформация не допускается. Основные требования к пружинным сталям – обеспечение высоких значений пределов упругости, текучести, выносливости, а также необходимой пластичности и сопротивления хрупкому разрушению, стойкости к релаксации напряжений.
Пружины работают в области упругих деформаций, когда между действующим напряжением и деформацией наблюдается пропорциональность. При длительной работе пропорциональность нарушается из-за перехода части энергии упругой деформации в энергию пластической деформации. Напряжения при этом снижаются.
Самопроизвольное снижение напряжений при постоянной суммарной деформации называется релаксацией напряжений.
Релаксация приводит к снижению упругости и надежности работы пружин.
Пружины изготавливаются из углеродистых (65, 70) и легированных (60С2, 50ХГС, 60С2ХФА, 55ХГР) конструкционных сталей.
Для упрочнения пружинных углеродистых сталей применяют холодную пластическую деформацию посредством дробеструйной и гидроабразивной обработок, в процессе которых в поверхностном слое деталей наводятся остаточные напряжения сжатия.
Повышенные значения предела упругости получают после закалки со средним отпуском при температуре 400…480 oС.
Для сталей, используемых для пружин, необходимо обеспечить сквозную прокаливаемость, чтобы получить структуру троостита по всему сечению.
Упругие и прочностные свойства пружинных сталей достигаются при изотермической закалке.
Пружинные стали легируют элементами, которые повышают предел упругости – кремнием, марганцем, хромом, вольфрамом, ванадием, бором.
В целях повышения усталостной прочности не допускается обезуглероживание при нагреве под закалку и требуется высокое качество поверхности.
Пружины и другие элементы специального назначения изготавливают из высокохромистых мартенситных (30Х13), мартенситно-стареющих (03Х12Н10Д2Т), аустенитных нержавеющих (12Х18Н10Т), аустенито-мартенситных (09Х15Н8Ю), быстрорежущих (Р18) и других сталей и сплавов.
Шарикоподшипниковые стали.
Подвергаются воздействию высоких нагрузок переменного характера. Основными требованиями являются высокая прочность и износостойкость, высокий предел выносливости, отсутствие концентраторов напряжений, неметаллических включений, полостей, ликваций.
Шарикоподшипниковые стали характеризуются высоким содержанием углерода (около 1 %) и наличием хрома (ШХ9, ШХ15).
Высокое содержание углерода и хрома после закалки обеспечивает структуру мартенсит плюс карбиды, высокой твердости, износостойкости, необходимой прокаливаемости.
Дальнейшее увеличение прокаливаемости достигается дополнительным легированием марганцем, кремнием (ШХ15СГ).
Повышены требования в отношении чистоты и равномерности распределения карбидов, в противном случае может произойти выкрашивание. Стали подвергаются строгому металлургическому контролю на наличие пористости, неметаллических включений, карбидной сетки, карбидной ликвации.
Термическая обработка включает отжиг, закалку и отпуск. Отжиг проводят после ковки для снижения твердости и подготовки структуры к закалке. Температура закалки составляет 790…880 oС в зависимости от массивности деталей. Охлаждение – в масле (кольца, ролики), в водном растворе соды или соли (шарики). Отпуск стали проводят при температуре 150…170oС в течение 1…2 часов. Обеспечивается твердость 62…66 НRC.
Из стали ШХ9 изготавливают шарики и ролики небольших размеров, из стали ШХ15 – более крупные.
Детали подшипников качения, испытывающие большие динамические нагрузки (подшипники прокатных станов), изготавливают из сталей 20Х2Н4А и 18ХГТ с последующей глубокой цементацией на глубину 5…10 мм. Для деталей подшипников, работающих в азотной кислоте и других агрессивных средах, используется сталь 95Х18.
Стали для изделий, работающих при низких температурах
Для изделий, работающих при низких температурах, необходимо применять стали с пониженным порогом хладоломкости. Особенно сильно понижены температурные пороги хладоломкости в никельсодержащих сталях. Эффективными материалами являются низколегированные малоуглеродистые стали, которые обладают хорошей свариваемостью.
В строительных металлоконструкциях наибольший эффект достигается при использовании термомеханически упрочненного проката.
Для обеспечения высокого комплекса механических свойств деталей машин используются малоуглеродистые стали, легированные элементами способствующими дисперсионному упрочнению и образованию мелкозернистой структуры после термической обработки, 10ХСНД, 15Г2СФ, 12ГН2МФАЮ.
Для работы при сверх низких температурах применяют криогенные стали и сплавы для изготовления емкостей для хранения и перевозки сжиженных газов, имеющих очень низкую температуру кипения (кислород – –183 oС, водород – –253 oС). Основными материалами для работы в подобных условиях являются аустенитные стали с повышенным содержанием никеля 10Х14Г14Н4Т, 10Х18Н10Т,03Х20Н16АГ6.
Износостойкие стали.
Для работы в условиях изнашивания, сопровождаемого большими удельными нагрузками используется высокомарганцевая сталь 110Г13Л, имеющая в своем составе 1…1,4% углерода, 12…14 % марганца. Сталь имеет аустенитную структуру и относительно низкую твердость (200…250 НВ). В процессе работы, когда на деталь действуют высокие нагрузки, которые вызывают в материале напряжения, превосходящие предел текучести, происходит интенсивное наклепывание стали и рост ее твердости и износостойкости. При этом сталь сохраняет высокую вязкость. Благодаря этим свойствам сталь широко используется для изготовления корпусов шаровых мельниц, щек камнедробилок, крестовин рельсов, гусеничных траков, козырьков землечерпалок и т.д.
Склонность к интенсивному наклепу является характерной особенностью сталей аустенитного класса.
Автоматные стали.
Автоматными называют стали, обладающие повышенной обрабатываемостью резанием.
Эффективным металлургическим приемом повышения обрабатываемости резанием является введение в сталь серы, селена, теллура, кальция, которые изменяют состав неметаллических включений, а также свинца, который образует собственные включения.
Автоматные стали А12, А20 с повышенным содержанием серы и фосфора используются для изготовления малонагруженных деталей на станках автоматах (болты, винты, гайки, мелкие детали швейных, текстильных, счетных и других машин). Эти стали обладают улучшенной обрабатываемостью резанием, поверхность деталей получается чистой и ровной. Износостойкость может быть повышена цементацией и закалкой.
Стали А30 и А40Г предназначены для деталей, испытывающих более высокие нагрузки.
У автоматных сталей, содержащих свинец, (АС11, АС40), повышается стойкость инструмента в 1…3 раза и скорость резания на 25…50 %.
Легированные хромистые и хромоникелевые стали с присадкой свинца и кальция (АЦ45Г2, АСЦ30ХМ, АС20ХГНМ) используются для изготовления нагруженных деталей в автомобильной и тракторной промышленности.
Автоматные стали подвергают диффузионному отжигу при температуре 1100…1150oС, для устранения ликвации серы.
Дата добавления: 2018-06-01; просмотров: 242; Мы поможем в написании вашей работы! |
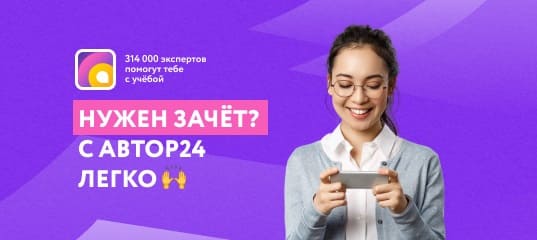
Мы поможем в написании ваших работ!