Дефектоскопы и намагничивающие устройства
МПС РФ
Уральский государственный университет путей сообщения
Челябинский институт путей сообщения
ЦДПО ИДПО
В.Г. Денисенко
МАГНИТОПОРОШКОВЫЙ МЕТОД НЕРАЗРУШАЮЩЕГО КОНТРОЛЯ ДЕТАЛЕЙ ПОДВИЖНОГО СОСТАВА ЖЕЛЕЗНЫХ ДОРОГ
Учебное пособие по обучению и повышению квалификации инженерно-технического персонала и дефектоскопистов
ремонтных предприятий МПС РФ
КОНСПЕКТ ЛЕКЦИЙ
Челябинск
2004г
СОДЕРЖАНИЕ
ВВЕДЕНИЕ 3
Основные положения 4
1.1 Основы и назначение магнитопорошкового метода 4
1.2 Чувствительность метода 4
1.3 Способы контроля 5
Средства контроля 6
2.1 Дефектоскопы и намагничивающие устройства 6
2.2 Вспомогательные средства 6
2.3 Дефектоскопические материалы 7
|
|
Технология контроля 9
3.1 Подготовка средств контроля 9
3.2 Подготовка детали к контролю 11
3.3 Намагничивание деталей 11
3.4 Проведение контроля 15
3.5 Нанесение дефектоскопического материала 19
3.6 Осмотр контролируемой поверхности 19
3.7 Распознавание дефектов 19
3.8 Размагничивание 21
Список использованных источников 22
Введение
Настоящий технический материал предназначен для инженерно-технического персонала и дефектоскопистов железнодорожных предприятий, выполняющих ремонт вагонов. Правила контроля установлены в руководящих документах РД32.174-2001 НЕРАЗРУШАЮЩИЙ КОНТРОЛЬ ДЕТАЛЕЙ ВАГОНОВ и РД32.159-2000 МАГНИТОПОРОШКОВЫЙ МЕТОД НЕРАЗРУШАЮЩЕГО КОНТРОЛЯ, от выполнения которых зависит безопасность и бесперебойность перевозок. Одним из средств обеспечения эксплуатационной надёжности вагонов является магнитопорошковый метод неразрушающего контроля их деталей. Настоящее учебное пособие предназначено для оказания методической помощи в освоении основ магнитопорошкового метода контроля деталей вагонов при обучении и повышении квалификации инженерно-технического персонала и дефектоскопистов ремонтных предприятий МПС России. Пособие рассчитано на лиц со средним и высшим техническим образованием, имеющих опыт работы по ремонту или контролю деталей вагонов.
|
|
Составитель: В.Г. Денисенко, преподаватель ЦДПО.
ОСНОВНЫЕ ПОЛОЖЕНИЯ
Основы и назначение магнитопорошкового метода
Магнитопорошковый метод неразрушающего контроля основан на явлении притяжения частиц магнитного порошка магнитными потоками рассеяния, возникающими над дефектами при намагничивании деталей.
|
|
Магнитопорошковый метод НК предназначен для выявления поверхностных дефектов типа усталостных, закалочных и шлифовочных трещин, волосовин, плен и расслоений в изделиях из ферромагнитных материалов. Метод позволяет контролировать всю поверхность детали или отдельные части ее.
Чувствительность метода
Чувствительность метода, определяемая минимальными размерами выявляемых дефектов (шириной раскрытия, длиной и глубиной), зависит от следующих факторов:
шероховатости контролируемой поверхности;
магнитных характеристик (остаточной индукции Вг и коэрцитивной силы Нс) материала, из которого сделана контролируемая деталь;
значения напряженности магнитного поля на контролируемой поверхности детали;
ориентации магнитного поля относительно направления выявляемых дефектов;
качества магнитного порошка или суспензии и т.д.
Для выбора режима намагничивания в зависимости от размеров выявляемых поверхностных дефектов и шероховатости контролируемой поверхности ГОСТ 21105 устанавливает условные уровни чувствительности, приведенные в таблице 3.1.
|
|
Необходимость магнитопорошкового контроля и требуемый условный уровень чувствительности контроля устанавливаются в конструкторско-технологической или ремонтной документации на конкретную деталь.
Таблица 3.1 Условные уровни чувствительности
Условный уровень чувствительности | Минимальная ширина раскрытия условного дефекта, мкм | Максимальная протяженность условного дефекта, мм | Шероховатость контролируемой поверхности, Ra, мкм не более |
А Б В | 2.0 10.0 25.0 | 0.5 0.5 0.5 | 2.5 10.0 10.0 |
Примечание: при выявлении подповерхностных дефектов, а также при шероховатости Ra > 10 мкм чувствительность метода не нормируется.
|
Способы контроля
Способ и средства контроля (аппаратура и дефектоскопические материалы) выбираются в зависимости от геометрических размеров, формы контролируемой детали, магнитных характеристик материала детали и требуемого условного уровня чувствительности.
Магнитопорошковый метод включает следующие основные технологические операции:
- подготовка деталей к контролю;
- намагничивание контролируемой детали;
-нанесение сухого магнитного порошка или суспензии на контролируемую поверхность;
- осмотр контролируемой поверхности и расшифровку результатов контроля;
- размагничивание (при необходимости).
В зависимости от последовательности проведения технологических операций различают способ приложенного поля (СПП) и способ остаточной намагниченности (СОН).
При контроле СПП операции намагничивания и нанесения магнитного порошка (или суспензии) на контролируемую поверхность выполняют одновременно. Намагничивающий ток выключают после окончания отекания суспензии и осмотра контролируемой поверхности.
При контроле СОН контролируемую деталь предварительно намагничивают, а затем, после снятия намагничивающего поля, на его поверхность наносят магнитный порошок (или суспензию), но не позднее, чем через 1 час после намагничивания. Осмотр проводят после стекания основной массы суспензии.
В технологических картах для каждой детали указаны рекомендуемые способ контроля, условный уровень чувствительности и значение продольной составляющей напряженности магнитного поля, при котором обеспечивается выявление трещин соответствующих этому уровню чувствительности.
Для деталей, не вошедших в перечень, способ контроля СПП или СОН выбираются в зависимости от магнитных характеристик материала в соответствии с требованиями ГОСТ 21105-87.
Так как при контроле СОН детали должны быть намагничены в полях более сильных, чем при СПП (до состояния близкого к насыщению), что не всегда может быть обеспечено имеющимися на предприятии дефектоскопом, то детали из магнитотвердых материалов в таких случаях рекомендуется контролировать СПП.
Подлежащие неразрушающему контролю детали, которые необходимо ремонтировать или восстанавливать сваркой, наплавкой или другими технологическими процессами должны до проведения данных работ пройти дефектоскопирование. Если после ремонта или восстановления деталь испытывают на растяжение, то контроль необходимо производить как перед ремонтом (наплавкой), так и после испытания детали на растяжение.
СРЕДСТВА КОНТРОЛЯ
Дефектоскопы и намагничивающие устройства
При магнитопорошковом контроле применяются:
- дефектоскопы и намагничивающие устройства (стационарные, передвижные, переносные);
- дефектоскопические материалы
- вспомогательные средства.
Магнитопорошковые дефектоскопы включают в свой состав блок питания (или блок управления), предназначенный для формирования намагничивающего тока, а также различные намагничивающие устройства, например, соленоиды, электромагниты, электроконтакты для пропускания электрического тока по контролируемой детали, гибкие силовые кабели и т.д.
К основным техническим характеристикам дефектоскопов и намагничивающих устройств относятся значение напряженности магнитного поля в заданной точке и\или значение намагничивающего тока, пропускаемого по проводникам соответствующего намагничивающего устройства или приспособления (соленоида, кабеля и т.д.), или по специально изготовленному образцу с заданными геометрическими размерами, изготовленному из известного материала.
Основные типы рекомендуемых к применению в отрасли магнитопорошковых дефектоскопов и намагничивающих устройств, в том числе разрабатываемых и серийно выпускаемых, их основные технические характеристики и назначение приведены в приложении 1.
Допускается для контроля вагонных деталей применение других магнитопорошковых дефектоскопов и установок, прошедших Государственные и/или ведомственные испытания и согласованные МПС к применению.
Вспомогательные средства.
К вспомогательным средствам контроля относятся:
- устройства для нанесения порошка или суспензии на контролируемую поверхность;
- устройства для осмотра контролируемой поверхности;
- приборы и устройства для проверки дефектоскопов, намагничивающих устройств и режимов намагничивания контролируемых деталей;
- приборы и устройства и для проверки качества магнитных порошков и суспензий;
- стандартные и контрольные образцы.
Перечень вспомогательных приборов, устройств и средств для магнитопорошкового контроля приведены в приложении 2.
Устройства для нанесения сухого магнитного порошка должны обеспечивать равномерное распределение его ферромагнитных частиц на контролируемой поверхности. Для нанесения сухого порошка следует использовать специальный распылитель, представляющий собой цилиндрическую коробку диаметром (40 - 50) мм с дном, выполненным из проволочного сита немагнитного материала с размером ячейки 0.1 мм.
К устройствам для нанесения магнитной суспензии относятся сосуды для ручного нанесения суспензии и гидросистемы, обеспечивающие циркуляцию суспензии: перемешивание, подачу ее к объекту контроля, сбор и т.д.
Для ручного нанесения суспензии можно использовать кружки, фляжки, лейки, опрыскиватели и т.п. При этом размешивать суспензию перед нанесением на контролируемую поверхность необходимо деревянной или пластмассовой лопаточкой. Все устройства для нанесения суспензии должны быть изготовлены из немагнитного материала (алюминий, медь, латунь, пластмасса и т.п.).
К устройствам для осмотра контролируемой поверхности относятся осветители ручного или настольного типа, используемые при применении черного или цветного магнитных порошков, или ультрафиолетовые облучатели (УФ-облучатели), используемые при применении люминесцентных магнитных порошков, а также различные оптические устройства (лупы). Технические характеристики УФ-облучателей должны соответствовать требованиям ГОСТ 28369-89.
Для измерения напряженности магнитного поля (или магнитной индукции) при проверке дефектоскопов или намагничивающих устройств, а также при определении и проверке режимов намагничивания контролируемых деталей применяются магнитометры или тесламетры (миллитесламетры) с преобразователями Холла, проверенные в установленном порядке.
Для проверки качества сухих магнитных порошков или суспензий применяются приборы МФ-10СП, МОН 721 и/или стандартные образцы (далее СО)
СО с искусственными или естественными трещинами, размеры которых соответствуют принятому уровню чувствительности, специально изготавливаются или отбираются из числа забракованных деталей по методике, изложенной в приложении 3.
СО должны быть аттестованы метрологической службой предприятия, отрасли или государственными центрами аттестации и метрологии. В зависимости от уровня аттестации различают:
СОП - стандартные образцы предприятий;
ОСО - отраслевые стандартные образцы;
ГСО - государственные стандартные образцы.
Для проверки работоспособности всей магнитопорошковой системы, включающей средства и технологию контроля применительно к конкретной детали, а также квалификацию оператора применяются контрольные образцы (далее КО). Контрольные образцы необходимы для ежедневной проверки качества магнитных порошков и суспензий на участке контроля.
В качестве КО могут быть использованы контролируемые детали или части деталей с дефектами, отобранные из группы забракованных деталей (приложение 3) и аттестованные метрологической службой предприятия.
Каждому СО (СОП, ОСО или ГСО) и КО присваивается номер и составляется паспорт в соответствии с Приложением 3. К паспорту должна быть приложена дефектограмма (фотография или отпечаток индикаторного рисунка на клейкой ленте).
Дефектоскопические материалы
При проведении контроля в качестве индикатора магнитного поля рассеяния дефекта применяют сухие магнитные порошки или магнитные суспензии, взвесь магнитного порошка в дисперсионной среде, содержащей, при необходимости, смачивающие, антикоррозионные, антикоагулирующие, антивспенивающие и другие добавки.
В качестве дисперсионной среды при приготовлении суспензий могут быть использованы: технические масла, масляно-керосиновые смеси, вода.
Дисперсионная среда суспензий в соответствии с ГОСТ 21105-87 должна иметь вязкость не более 36 сСт при температуре контроля. При вязкости более 10 сСт время отекания суспензии должно быть не менее 30 с. При использовании порошка ПЖВ5-71 (ГОСТ 9849-86) вязкость дисперсионной среды должна быть в пределах (5 - 36) сСт. Для остальных порошков нижний предел вязкости не нормируется.
Вязкость дисперсионной среды измеряется по ГОСТ 33-82 вискозиметром марки ВПЖ-2 (ГОСТ 10028-81) или его заменяющим.
Применение керосина должно быть согласовано с органами Государственной пожарной инспекции.
Магнитные порошки выпускаются и поставляются потребителям либо в сухом виде, либо в виде концентратов и паст, содержащих все необходимые добавки (см. таблицу 1 приложения 4).
Рекомендуемые составы и способы приготовления магнитных суспензий для контроля деталей вагонов приведены в таблице 2 приложения 5.
В зависимости от состояния контролируемой поверхности (ее цвета и шероховатости), требуемой чувствительности контроля и типа применяемого дефектоскопа выбирается тип порошка или концентрата (пасты), исходя из следующих рекомендаций.
Для контроля деталей с светлой поверхностью, имеющей шероховатость не более Rz 80, рекомендуются суспензии с черными или темно-серым порошками.
Для контроля темной и серой поверхности любой шероховатости рекомендуются суспензии красного цвета (Диагма-1200) или люминесцентные.
Для темной и светлой необработанной поверхности с шероховатостью более Rz 80 допускается применение сухого железного порошка ПЖВ5, имеющего класс крупности 160.
Не рекомендуется применение сухого железного порошка в следующих случаях:
-при намагничивании цилиндрических (например, средняя часть оси) деталей седлообразным намагничивающим устройством дефектоскопа МД-12ПС;
- при контроле мелких деталей ,например, стопорных планок);
- при невозможности обезжирить и просушить контролируемую поверхность.
При необходимости контролировать на одном участке детали, имеющие разные типы поверхностей, допускается применение одной суспензии из рекомендованных в приложении 5.
В случае использования черного порошка при контроле деталей с темной поверхностью на нее следует наносить покрытие толщиной не более 20 мкм, обеспечивающее необходимый контраст индикаторного рисунка.
Готовую суспензию перед нанесением ее на контролируемую поверхность необходимо тщательно размешать деревянной лопаточкой так, чтобы частицы магнитного порошка оказались во взвешенном состоянии и равномерно распределялись во всем объеме жидкости.
Водную магнитную суспензию при нанесении ее на поверхность контролируемой детали и хранении необходимо оберегать от органических загрязнений (масло, керосин и т.п.), которые вызывают коагуляцию (слипание частиц) порошка и соответственно снижение чувствительности суспензии.
Хранить сухой магнитный порошок необходимов герметическизакрытых сосудах, концентраты и пасты - в заводской упаковке и в условиях, соответствующих требованиям инструкции по эксплуатации.
Хранить готовую к применению магнитную суспензию следует в изготовленных из немагнитных материалов плотно закрытых емкостях и не более 10 дней после ее приготовления.
Качество сухих магнитных порошков, концентратов и паст, поступающих с завода - изготовителя и по окончании гарантийного срока, указанного в сертификате, необходимо проверять в составе суспензии с помощью прибора МФ-10СП, МОН-721 или СОП.
Результаты проверки должны быть оформлены актом о пригодности, порошка для дефектоскопии.
Качество используемой при проведении контроля магнитной суспензии необходимо проверять непосредственно после ее приготовления и регулярно по мере ее применения, но не реже одного раза в неделю.
Ежедневно перед началом работы необходимо проверять качество суспензии или сухого порошка путем выявления дефектов на КО (п.3.2.12) и сравнения полученного индикаторного рисунка с дефектограммой.
При необходимости состав суспензии корректируется добавлением магнитного порошка (концентрата) или готовится новая суспензия.
ТЕХНОЛОГИЯ КОНТРОЛЯ
Подготовка средств контроля
Ежедневно перед началом работы дефектоскопист должен выполнить следующие работы:
- провести внешний осмотр дефектоскопов, намагничивающих устройств и других вспомогательных приборов и устройств;
- подготовить дефектоскопы и намагничивающие устройства к работе;
- подготовить магнитную суспензию или сухой порошок;
- проверить работоспособность всей магнитопорошковой системы (аппаратуры, дефектоскопических материалов и технологии контроля) с помощью СО или КО;
- проверить на СО или КО качество размагничивания.
При проведении внешнего осмотра необходимо проверить целостность корпуса блока питания и всех остальных узлов (отсутствие вмятин, загрязнений и следов коррозии). Проверить надежность соединения шнура питания и соединительных кабелей, состояние переключателей и ручек управления на панели блока питания. Если имеются подвижные узлы (например, шарнирные или раздвижные полюсы электромагнитов, механизмы для зажима или поворота контролируемых деталей), то необходимо проверить их исправность.
Проверить надежность заземления (все дефектоскопы перед включением их в сеть должны быть дополнительно заземлены через трехконтактную вилку или путем подсоединения специальной клеммы на корпусе дефектоскопа к контуру заземления).
При подготовке к работе дефектоскопов необходимо выполнить следующие работы:
- подключить к блоку питания намагничивающее устройство (соленоид, электромагнит и т.п.);
- подключить блок питания к электрической сети и включить дефектоскоп;
- по показаниям амперметра на лицевой панели блока питания проверить соответствие намагничивающего тока данным, указанным в эксплуатационной документации.
При проверке намагничивающего тока все металлические предметы, в том числе и контролируемые детали, должны быть удалены от намагничивающего устройства на расстояние не менее 100 мм, так как при помещении металлического предмета в отверстие соленоида или рядом с ним происходит уменьшение тока, зависящее от формы, размеров, материала детали и расстояния до соленоида.
Проверку работоспособности магнитопорошковой системы, включающей дефектоскоп, магнитную суспензию или сухой порошок и технологию контроля, необходимо проводить с помощью КО или СО, если он изготовлен из контролируемой на данном участке детали.
Для этого необходимо предварительно размагниченный КО или СО проконтролировать по технологии, указанной в его паспорте или рекомендованной для контроля таких же деталей, и сравнить полученный индикаторный рисунок с дефектограммой,
Если на КО или СО выявились не все трещины или не вся длина трещины, то необходимо проверить напряженность поля на поверхности КО или СО в положении контроля с помощью измерительного прибора по методике, изложенной в приложении 6. Если значение напряженности поля не менее указанного в паспорте на КО (СО), то необходимо сменить суспензию. Если менее, то необходимо проверить на соответствие паспортным данным напряженность поля в намагничивающем устройстве по методике, изложенной в приложении Л.
При отсутствии измерителя напряженности магнитного поля допускается провести повторный контроль КО или СО свежеприготовленной суспензией и в случае повторного невыявления трещин необходимо проверить дефектоскоп.
Для проверки качества размагничивания необходимо СО или КО размагнитить по методике, рекомендуемой для данного дефектоскопа, очистить от остатков магнитного порошка и нанести суспензию или сухой порошок вторично, при этом на трещине не должно быть никакого отложения порошка.
Проверку качества размагничивания можно также проводить измерением остаточной намагниченности в заданных для данного СО (КО) точках по методике, приведенной в приложении 6 и сравнением допустимых и измеренных значений.
После выполнения указанных работ можно приступать к проведению контроля деталей.
Дата добавления: 2018-06-01; просмотров: 1964; Мы поможем в написании вашей работы! |
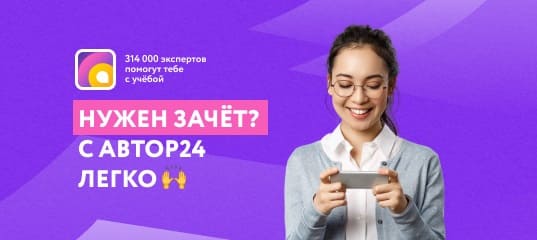
Мы поможем в написании ваших работ!