Конвертирование медно-никелевых штейнов.
Лекция №8. Получение никеля из сульфидных медно-никелевых руд.
Плавка медно-никелевого сырья на штейн
Исходным сырьем при плавке на штейн при переработке сульфидного медно-никелевого сырья могут служить богатые руды, никелевые или медно-никелевые концентраты. Плавку такого сырья можно вести в шахтных печах по методу полупиритной плавки, в отражательных или электрических печах и любым автогенным процессом.
Шахтная плавка сохранилась до настоящего времени на заводе «Конистон» (Канада). Отражательную плавку никелевых концентратов с содержанием 5-8 % Ni, 1-2 % Cu и 5-10 % MgO используют на канадском заводе «Коппер-Клифф». Перед плавкой концентраты обжигают в печах КС. Плавку ведут на штейны, содержащие около 16 % Ni+Cu. Основным способом плавки, сульфидных медно-никелевых руд и концентратов в России является плавка в руднотермических печах. Плавку в электрических печах применяют также на двух заводах в Канаде. На Норильском ГМК была освоена плавка никелевых концентратов во взвешенном состоянии на подогретом, обогащенном кислородом дутье.
Плавка в электрических печах требует тщательной подготовки шихты, заключающейся в первую очередь в ее усреднении и сушке. Плавка влажной шихты в электропечах недопустима, так как при контакте влаги с расплавленными сульфидами происходит разложение воды со взрывом. Технология подготовки шихты к электроплавке определяется видом исходного сырья. Сульфидные медно-никелевые руды с содержанием никеля более 1,5 % обычно плавят без обогащения. Их подготовка к плавке сводится к дроблению, сушке и шихтовке. Флотационные концентраты перед электроплавкой укрупняют методами агломерирующего обжига или окатывания с последующим окислительным обжигом. Предварительную сушку рудных материалов проводят перед плавкой руды или для подсушки концентратов перед окатыванием в трубчатых сушильных печах.
|
|
Агломерирующий обжиг как метод окускования мелкой шихты применяют на Норильском ГМК. Шихта агломерации состоит из концентратов, оборотного агломерата и каменноугольной мелочи. Цель агломерации - окускование шихты за счет ее спекания и удаление части серы. Для обжига со спеканием применяют ленточные агломерационные машины с площадью всасывания 50 и 75 м2. Основными элементарными стадиями агломерирующего обжига являются: сушка шихты; термическое разложение высших сульфидов (пирротина, халькопирита и пентландита); окисление части сульфидов железа; расплавление легкоплавких компонентов шихты за счет тепла от окисления сульфидов и углеродистых материалов; спекание шихты при охлаждении расплавленной фазы. Агломерат является хорошо термически подготовленным для электроплавки материалом.
|
|
Более прогрессивным способом укрупнения медно-никелевых концентратов является их окатывание в гранулы диаметром 8-15 мм на чашевых грануляторах с последующим термическим упрочнением на ленточной конвейерной машине. Перед окатыванием концентрат подсушивают и в случае необходимости шихтуют с оборотными и другими материалами. Сырые окатыши имеют недостаточную механическую прочность и легко разрушаются при транспортировке и перегрузках.
Термическую обработку окатышей для их упрочнения производят на ленточных конвейерных машинах, отличающихся от агломерационных машин только системой газового тракта. Рабочая площадь используемых машин равна 18, 21 и 72 м2. Термическая обработка включает три последовательных стадии: сушку, окислительный обжиг и охлаждение гранул, для чего по длине ленты конвейерной машины создаются три соответствующие зоны. Максимальные температуры (1050°С) достигаются в зоне окислительного обжига. Работа конвейерных машин организована с рециркуляцией части газов, что повышает степень использования тепла отходящих газов. При таком методе подготовки шихты степень десульфуризации можно регулировать в, пределах от 30 до 50-55% путем изменения температуры в зоне обжига и скорости движения ленты.
|
|
По химизму электроплавка сульфидного сырья является аналогом отражательной плавки. Однако механизм плавления шихты этих двух видов плавки различен.
Рис.8.1 Цех для плавки никелевого сырья в электропечах (поперечный разрез):
1-руднотермическая электропечь; 2- конвертер; 3-мостовой кран; 4-сборный газоход. [1, стр.40]
Рис.8.2 Цех для плавки никелевого сырья в электропечах (продольный разрез):
1-распределитель пульпы концентрата; 2- сгуститель; 3-чансгущенной пульпы; 4-барабанный фильтр;
5-транспортер; 6-вращающийся бункер; 7-обжиговая печь КС; 8- воздухопровод; 9-котел-утилизатор;
10-циклон; 11-скребковый транспортер; 12-газоход обжиговых печей; 13- электропечь; 14-желоб для грануляции шлака; 15-шины; 16-вентиляция; 17-электроды; 18-сборный газоход; 19-мостовой кран; 20-желоб для штейна; 21-желоб для конвертерного шлака; 22-ковш; 23-конвертер; 24-газоход конвертера;
25-пневматический насос для подачи пыли; 26-воздухопровод; 27-электрофильтр; 28-труба. [1, стр.41]
Ванна расплавов руднотермической печи состоит из двух слоев. Высота верхнего шлакового слоя составляет 1700-1900 мм, а нижнего штейнового 600-800 мм. Исходная твердая шихта погружена в шлаковый слой ванны в виде конических куч - откосов; часть шихты «растекается» по поверхности шлака. Плавление шихты осуществляется за счет тепла, выделяемого в шлаковом расплаве при пропускании через него электрического тока. Ток в рабочее пространство печи подводится с помощью трех или шести угольных электродов, концы которых погружены на 300-500 мм в слой шлакового расплава.
|
|
В шлаковой ванне электрическая энергия преобразуется в тепловую двумя путями. Значительная часть тепла (40-80 %) выделяется в переходном контакте электрод-шлак, где вследствие образования тонкого газового слоя возникают мелкие точечные микродуги, а остальная часть в шлаковом расплаве, являющемся проводником тока с высоким электрическим сопротивлением. В результате тепловыделений шлаковый расплав разогревается. Максимальный перегрев шлака происходит вблизи электродов. Здесь же шлак наиболее насыщен газовыми пузырьками. Вследствие этого возникает разность в плотностях слоев шлака, прилегающих к электродам и отдаленных от них.
Более легкие массы перегретого шлака непрерывно поднимаются вверх и растекаются по зеркалу ванны во все стороны от электродов. Встречая на своем пути плавающую шихту, потоки шлака отдают ей избыток своего тепла и подплавляют шихтовую кучу с поверхности, погруженной в шлак. Массы частично охлажденного шлака основной ванны и образовавшегося при плавлении шихты расплава опускаются вниз и замыкают циркуляцию шлакового расплава. В подэлектродном слое шлака, где конвекция почти отсутствует, завершается разделение штейна и шлака. Таким образом, циркуляционное движение шлака - важнейший рабочий процесс в руднотермических печах - обеспечивает достаточно хороший массо- и теплообмен в ванне. Это позволяет разогревать шлак до 1450°С и выше, что дает возможность перерабатывать в электропечах тугоплавкие шихты, а плавку вести на шлаки с повышенным содержанием оксида магния (до 24 %).
Рис.8.3 Общий вид руднотермической печи для плавки медно-никелевого сульфидного сырья:
1-каркас печи; 2- футеровка; 3-свод; 4-электродное уплотнение; 5-контактные щеки; 6-пакет шин;
7-гидроподъемник электрода; 8- 9-верхнее и нижнее кольцо пружинно-гидравлического устройства перепуска электродов; 10-11-верхний и нижний концевые ограничители; 12-реверсивный транспортер; 13- бункер; 14-загрузочный рукав; 15-телескопическая труба; 16-электрод; 17-печной трансформатор. [3, стр.193]
Жидкими продуктами электроплавки являются медно-никелевый штейн и шлак. Штейны плавки сульфидных руд и концентратов обычно содержат, %: 7-16 Ni; 7-12 Cu; 0,3-0,5 Со; 47-55 Fe; 23-27 S. Штейны из печи выпускают при 1100-1150 °С.
Шлаки руднотермических печей представляют собой сплавы оксидов кремния (SiO2), железа (FeO), магния (MgO) и алюминия (А12О3). Высокие температуры процесса электроправки, циркуляция шлакового расплава и присутствие в печах восстановителя обеспечивают получение шлаков, которые по содержанию извлекаемых металлов беднее шлаков других традиционных методов плавки на штейн. Шлаки содержат, %: 0,07-0,11 Ni; 0,06-0,10 Cu; 0,03-0,04 Со; 41-45 SiO2; 24-30 FeO; 10-22 MgO; 5-12 А12О3; 3-5 CaO.
Кроме штейна и шлака, при плавке образуются газы. Они состоят из азота, кислорода, диоксидов серы и углерода (SO2 и СО2) и паров воды. Объем отходящих газов электроплавки по сравнению с отражательной плавкой, где их основу составляют топочные газы, во много раз меньше. Они образуются в основном в результате термической диссоциации высших сульфидов и карбонатов и горения углеродистых материалов шихты и электродов. Взаимодействие между высшими оксидами железа и сульфидами при электроплавке носит подчиненный характер, так как Fe3O4 быстро восстанавливается добавляемым в шихту углеродистым восстановителем- коксовой или угольной мелочью. По этой причине десульфуризация при электроплавке руд и окатышей составляет всего 15-20%, а агломерата 2-5% и газы бедны по содержанию SO2.
Теоретическое количество технологических газов электроплавки составляет не более 120 м3 на 1 т рудной шихты. На практике за счет подсосов воздуха через неплотности в своде печи объем газов увеличивается до 1100-1200 м3/т шихты. Однако объем их и в этом случае примерно в 10 раз меньше, чем при плавке в отражательных печах.
Технологические газы, образующиеся преимущественно в шлаковом расплаве, выделяясь из него, отдают часть своего тепла плавающей на поверхности шихте и разбавляются подсасываемым холодным воздухом. В результате этого температура отходящих газов не превышает 500-600 °С.
Относительно небольшой объем отходящих газов, низкая их температура и более рациональный метод нагрева шихты и расплавов обусловливают высокий коэффициент использования тепла в руднотермических печах (до 85%). Малый объем отходящих газов и небольшое количество мелочи в шихте определяют сравнительно небольшой пылевынос при электроплавке - всего 0,4-0,5% от массы твердой шихты.
Для плавки сульфидных медно-никелевых руд и концентратов применяют прямоугольные руднотермические печи с тремя или преимущественно шестью электродами. Трехэлектродные печи работают только на комбинате «Североникель». Они имеют площадь пода 58 м3 (11,2х5,2 м), удельную мощность около 520 кВА/м2. Площадь пода шестиэлектродных печей при длине 20,5- 27,5 м и ширине 5,5-6,7 м составляет 113-184 м2. Удельная мощность таких печей колеблется от 98 до 324 кВА/м2.
Современные мощные печи оборудованы самообжигающимися электродами, представляющими собой железный кожух диаметром 1200 мм, заполненный электродной (углеродистой) брикетированной массой. По мере сгорания и опускания электрода кожух наращивают, а электродная масса, нагреваясь, спекается и превращается в монолит.
Шихту в печь загружают через боковые и центральные загрузочные отверстия в своде, чаще всего «на электроды», где температура выше, а циркуляция шлака более интенсивна. Штейн выпускают через шпуровые отверстия, расположенные на одной из торцовых стен печи. В связи с отсутствием в руднотермических печах отстойной зоны и наличием на поверхности шлаковой ванны плавающей шихты выпуск шлака также осуществляют через шпуры, расположенные на противоположной стороне печи на расстоянии 1350-1750 мм от подины (550-900 мм от зеркала расплавленной ванны).
Работа руднотермических печей при плавке медно-никелевого сырья характеризуется следующими технико-экономическими показателями:
Таблица 8.1 Показатели электроплавки медно-никелевого сырья
1 | Суточная производительность печи по шихте, т | 600-900 |
2 | Проплав иа 1000 кВА установочной мощности, т/сут | 25-30 |
3 | Удельный проплав, т/(м2-сут) | 8-10 |
4 | Расход электроэнергии на 1 т шихты, кВт-ч | 570-820 |
5 | Извлечение в штейн, %: | |
никеля | 94-97 | |
меди | 94-96 | |
кобальта | 75-80 |
Конвертирование медно-никелевых штейнов.
Для конвертирования медно-никелевых штейнов используют горизонтальные конвертеры емкостью 75-100 т. В связи с тем, что никель, получаемый из сульфидных руд, обязательно подвергается электролитическому рафинированию, при котором можно наиболее рационально извлечь кобальт, при конвертировании медно-никелевых штейнов стремятся кобальт полнее оставить в файнштейне.
Присутствующие в медно-никелевых штейнах основные металлы по убыли сродства к кислороду располагаются в ряд Fe-Co-Ni-Cu. Для того чтобы кобальт сохранить в файнштейне, процесс конвертирования нужно вести с неполным окислением железа. В противном случае кобальт преимущественно будет переходить в конвертерный шлак.
Медно-никелевые штейны в отличие от никелевых штейнов содержат Cu2S и металлическую медь. Содержание магнетита Fe3O4 в штейне зависит от способа плавки и состава печной атмосферы.
При автогенных способах плавки с высоким окислительным потенциалом печной атмосферы содержание магнетита в штейнах возрастает, а при нейтральной или слабо восстановительной атмосфере содержание магнетита в штейне снижается. В штейнах электроплавки при наличии углерода в шихте его мало и штейны могут содержать до 10-20% металлической фазы. При конвертировании металлизированных штейнов в первую очередь будут взаимодествовать с кислородом дутья металлы по схеме:
2 Me + O2 = 2 MeO
Последовательно может окисляться Fe до FeO и Fe3O4 , далее может окисляться кобальт, а затем никель. При определенных условиях могут протекать обменные реакции:
(CoO) + [Fe] = (FeO) + [Co]
(NiO) + [Fe] = (FeO) + [Ni]
Оксиды никеля и кобальта из шлака и шихты могут реагировать с FeS штейна:
3 (NiO) + 3 [FeS] + O2 = [Ni3S2] + 3 (FeO) + SO2
(CoO) + [FeS] = [CoS] + (FeO)
Пока в штейне присутствует металлическое железо и сульфид железа, степень окисления никеля, кобальта и меди будет невелика. По мере окисления металлического железа и его ошлакования за счет кремнезема флюсов выравниваются значения химических потенциалов или величин изменения энергии Гиббса, реакций окисления металлического железа и сульфида. Начинается совместное протекание реакций:
2 Fe + O2 + SiO2 = Fe2SiO4
FeS + 1,5 O2 + SiO2 = Fe2SiO4 +SO2
Продувку медно-никелевых штейнов в конвертерах заканчивают получением файнштейна, содержащего, %: 35-42 Ni; 25-30 Cu; 0,7-1,3 Со; 3-4 Fe; 23-24 S. При этом получают конвертерные шлаки с 2-2,5 % суммы никеля, меди и кобальта. С целью обеднения конвертерные шлаки подвергают дополнительной переработке в электрических печах в присутствии восстановителя и бедной извлекающей фазы (рудного штейна). Продуктами плавки являются штейн, направляемый на конвертирование, и отвальный шлак.
Разделение меди и никеля
Медно-никелевый файнштейн представляет собой в основном сплав сульфидов Ni3S2 и Cu2S, содержащий кобальт, платиноиды и небольшое количество железа. Если такой файнштейн по аналогии с никелевым файнштейном сразу подвергнуть окислительному обжигу с последующей восстановительной плавкой огарка на металл, то это приведет к получению сложного по составу металлического сплава, разделение которого на металлы технически невозможно. Поэтому медно-никелевые файнштейны вначале направляют на разделение меди и никеля. Разделение меди и никеля можно осуществить несколькими методами. Наибольшее распространение получил флотационный метод, при котором никель концентрируют в богатом никелевом концентрате, а медь в медном.
Перед флотационным разделением файнштейн необходимо медленно охладить в течение 40-80 ч с тем, чтобы обеспечить хорошее механическое вскрытие кристаллических фаз при последующем его дроблении и измельчении. Медленно охлажденный файнштейн состоит из обособленных кристаллов трех видов: сульфидов меди и никеля и металлического сплава. Последний представляет собой твердый раствор никеля и меди переменного состава. В нём концентрируется до 80 % платиновых металлов, содержащихся в файнштейне. Металлический сплав можно перед флотацией выделить магнитной сепарацией и направить на самостоятельную переработку. В России магнитную фракцию не выделяют, и она полностью переходит в никелевый концентрат. Флотацию ведут в сильнощелочной среде. Пенный продукт- богатый медный концентрат- после перечисток направляют в медное производство, где его расплавляют в отражательных или электрических печах, а расплав конвертируют до получения черновой меди.
В медном концентрате содержится 68-73 % Cu и до 5 % Ni. Вторым продуктом флотационного разделения является богатый никелевый концентрат («хвосты» флотации), содержащий, %: 68-72Ni; 3-4 Cu; до 1 Со; 2-3Fe; 22-23,5 S, а также большую часть платиновых металлов.
Другим применяемым в современной практике способом разделения меди и никеля является карбонильный процесс. Его используют для переработки медно-никелевых файнштейнов, восстановленной закиси никеля и рафинирования чернового никеля. Карбонильное разделение меди и никеля основано на способности никеля образовывать при взаимодействии с СО карбонил - соединение металла с СО. Вместе с никелем образуют карбонилы железо и кобальт; медь карбонилов не образует.
Карбонил никеля Ni(CO)4 плавится при температуре 25 °С и кипит при 43°С. Температура кипения карбонила железа 105°С. Карбонил кобальта плавится при 51 °С с разложением. При нагревании до температуры выше 180°С пары карбонила никеля разлагаются. Cущность карбонильного процесса можно описать уравнением:
Ni + 4 CO = Ni(CO)4 180-200°С
При атмосферном давлении образование карбонилов идет очень медленно. Равновесие этой реакции можно сдвинуть вправо, т.е. ускорить процесс, проводя его под давлением 17-23 МПа и при температуре 190-220 °С.
Известно, что образование карбонилов металлов происходит из металлической фазы сплавов. Окись углерода хотя и взаимодействует с сульфидами, но очень медленно. В 1960-70 гг. установлено взаимное влияние компонентов сплава на их карбонилирование при высоком давлении. Оно выражается, в частности, в отсутствии избирательного извлечения металлов из железо-никелевого твердого раствора. Так, контроль состава смеси карбонилов никеля и железа, образующейся при взаимодействии окиси углерода с сульфидированными (5,06 -6,45% S) сплавами ферроникеля, показал, что соотношение этих карбонилов в смеси остается практически постоянным вплоть до извлечения 98% Ni и 91% Fe.
Процесс образования карбонила никеля протекает на границе раздела твердой и газообразной фаз и для случая взаимодействия СО с чистым металлом может представлять собой несколько последовательно протекающих стадий:
· адсорбцию окиси углерода на поверхности твердого металла с образованием вначале промежуточных комплексов, а затем молекул карбонила:
· образования молекулярного слоя карбонила, который удерживается на поверхности кусочков сырья силами сцепления:
· перехода молекул карбонила из адсорбционного слоя в газовую фазу под действием сил кинетического движения молекул.
Карбонильный процесс при атмосферном давлении был впервые применен в Клайдахе (Англия) и отличался громоздкостью аппаратуры и большой продолжительностью. В последнее время технология карбонильного процесса при атмосферном давлении и его аппаратурное оформление на заводе в Клайдахе подверглись коренному усовершенствованию. Аппараты для восстановления закиси никеля, сульфидизации восстановленного продукта, а также испарители заменены противоточными вращающимися печами непрерывного действия. Исходным материалом для карбонильного процесса является гранулированная закись никеля завода «Коппер-Клифф», имеющая следующий состав: 74,5% Ni; 2,5% Си; 0,3% Fe; 0,7% Со; 0,2% S. Закись никеля восстанавливают в трубчатой печи водородом при 425* С, затем подвергают сульфидной активации смесью Н2 + S02. При этом вводят серу в количестве примерно 1-1,5% (по массе).
В реакторе-испарителе (рис.8.4) длиной около 40 м и диаметром 5 м одновременно находится около 200 т материала. Аппарат разделен на два отсека: один (главный) предназначен для извлечения основной массы никеля, другой - для доработки материала. В главном отсеке установлены гребки, перемешивающие материал, что улучшает его контакт с газом.
Рис 8.4 Реактор-испаритель для синтеза карбонила никеля при атмосферном давлении (з-д Клайдах):
1-устройство загрузки; 2-неподвижная часть аппарата; 3-главный (загрузочный) отсек реактора; 4-шнек возврата вынесенной мелочи; 5-вращающаяся часть аппарата; 6-вспомогательный (разгрузочный) отсек; 7-неподвижная часть аппарата. [1, стр.100]
Во вспомогательной части аппарата гребки отсутствуют, и бедный по содержанию никеля материал медленно перемещается к разгрузочному концу. В эту часть аппарата по центральной трубе со шнеком возвращают уловленную пыль, которую газовый поток выносит из реактора. Главный отсек снабжен змеевиками с водяным охлаждением для регулирования температуры. С этой же целью осуществлен рассредоточенный по длине реактора ввод окиси углерода. Существующую производительность завода (36 000 т никеля в год) обеспечивают два реактора новой конструкции. Никелевые гранулы, получаемые в аппаратах разложения карбонила никеля, имеют следующий состав: 99,95% Ni; 0,0005% Со; 0,001% Сu; 0,01% Fe; 0,001% S; 0,0001% As; 0,0001% Pb и 0,01% С.
Применение высокого давления позволило осуществлять карбонилирование медно-никелевых сплавов типа передутых файнштейнов с различным содержанием серы.
Результаты исследований показали, что сера вызывает изменение структуры сплавов и катализирует процесс. Установлено, в частности, что максимальная реакционная способность железоникелевых сплавов наблюдается при содержании серы, равном 6-8%. Положительное влияние серы на скорость процесса связывают с разрыхлением структуры сплава вследствие разделения металлических зерен сеткой сульфидов. В результате этого реакционная поверхность резко увеличивается. Для интенсификации процесса малосернистый материал, например восстановленную закись никеля, подвергают сульфидированию с целью активирования металлического никеля.
Повышение устойчивости карбонилов металлов под давлением позволяет увеличить температуру реакции, а следовательно, ускорить процесс. Это особенно важно для процессов, связанных с твердофазными превращениями, скорость которых резко увеличивается с ростом температуры. Поэтому применение высокого давления позволило осуществлять карбонилирование медно-никелевых сплавов типа передутых файнштейнов с различным содержанием серы.
Карбонил процесс среднего давления. На заводе в Клайдахе еще во время Второй мировой войны было организовано производство порошков никеля и железа карбонильным способом при повышенном давлении. В настоящее время исходным сырьем для получения никелевого порошка, как и при производстве гранулированного карбонильного никеля, является закись никеля, которую восстанавливают водородом.
Восстановленный продукт охлаждают в атмосфере инертного газа и направляют в испарители, которые представляют собой водоохлаждаемые вертикальные автоклавы, работающие при температуре 120°С и давлении 2 МН/м2. Обогащенный карбонилами никеля и железа газ передают из испарителя в конденсатор, охлаждаемый водой. Выделяющийся в конденсаторе жидкий карбонил перекачивают в запасные баки, а окись углерода возвращают в цикл.
Перед получением порошка никеля карбонил направляют на очистку в ректификационную колонну. Температуру жидкости в кубе-испарителе, расположенном в нижней части колонны, поддерживают между точкой кипения карбонила никеля (43 и точкой кипения карбонила железа (104 °С). Верхний продукт колонны - чистый карбонил никеля — направляют на разложение. Кубовый остаток содержит некоторое количество карбонпла никеля и его подвергают повторной очистке.
Рис 8.5 Схема получения никелевого порошка в карбонил-процессе среднего давления (з-д Клайдах):
1-реактор восстановления закиси никеля (600 оС); 2-переток с затвором для перевода восстановленного никеля в реактор карбонилирования; 3-реактор карбонилирования (120 оС, 2 Мн/м2); 4-холодильник-конденсатор; 5-отделитель жидкого карбонила; 6-ректификационная колонна; 7-разложитель. [1, стр.101]
Карбонил никеля, загрязненный карбонилом железа, возгоняется, а вся медь, платиноиды и кобальт остаются в остатке. Технический карбонил никеля для очистки от железа подвергают фракционной перегонке (ректификации). Очищенный карбонил направляют в башню разложения, обогреваемую до 200-220°С.
Рис 8.6 Схема башни разложения карбонила никеля (з-д Клайдах):
1-ковшовый элеватор; 2-камера подогревания; 3-реакционная камера. [3, стр.196]
Разложение чистого газообразного карбонила никеля осуществляют в стальном цилиндрическом аппарате, температуру стенок которого поддерживают около 315 °С. Образующийся тонкий порошок металла с размерами частиц менее 10 мкм выпадает на дно аппарата. Его просеивают, уплотняют в шаровой мельнице и отправляют потребителям. Физические свойства порошка регулируют в зависимости от требования потребителей, для чего изменяют режим осаждения и обработки. Получение порошка полностью автоматизировано. Продуктом разложения могут быть карбонильный порошок или дробь диаметром до 10-15 мм. Карбонильный никель содержит не более 0,001 % Cu; 0,005 % Fe; 0,002 % S и до 0,03 % С.
В начале 40-х годов фирмой «И. Г. Фарбениндустрп» (ФРГ) -был разработан и освоен на заводе в Оппау карбонильный процесс под высоким давлением (до 20-25 МН/м2). Этот процесс применяли для переработки медно-никелевых файнштейнов, никелевого лома и отходов.
Карбонильный процесс при высоком давлении состоит из основных операций: 1) обработки сырья после соответствующей его подготовки окисью ут рода под высоким давлением; 2) ректификации загрязненного карбонила никеля и 3) термического разложения чистого карбонила с получением порошка никеля и оборотной окиси углерода.
Исходным сырьем для карбонильного процесса могут служить медно-никелевый файнштейн, анодный скрап, гранулированные сплавы (обогащенный ферроникель, черновой никель или сплав, полученные в вертикальном кислородном конвертере), металлическая фракция, выделяемая при разделительной флотации файнштейна, и другие материалы, содержащие никель, медь и железо. Физический характер сырья и форма металлов, входящих в его состав, имеют существенное значение для достижения необходимых результатов. При крупности материала больше 30 мм снижается эффективность работы установки из-за трудности диффузии окиси углерода внутрь отдельных кусков. Применение материала мельче 1-5 мм затрудняет просасывание реакционного газа через слои (в случае использования реактора типа полого автоклава) и приводит к высокому пылевыносу. Оптимальная крупность материала 10-25 мм. Содержание серы в сырье определяется его составом. Так, на заводе в Оппау в передутом файнштейне оставляли количество серы, необходимое для образования сульфида меди Cu2S.
Подготовленный материал обрабатывают окисью углерода в реакционной колонне периодического действия, представляющей собой цельнокованый цилиндр из малоуглеродистой низколегированной стали, футерованный изнутри нержавеющей сталью. Снаружи корпус колонны имеет тепловую изоляцию. Перед работой колонну продувают азотом для вытеснения воздуха, затем проверяют аппаратуру на герметичность и тщательно промывают реакционным газом. После промывки давление газа постепенно увеличивают до 21-25 МН/м2. Температура процесса составляет 200-220 °С. Следует отметить, что в присутствии металлического никеля при температуре выше 250 °С энергично протекает реакция диспропорционирования СО с выделением сажистого углерода, поэтому на практике температуру в колонне не поднимают выше 220 °С.
Среднее содержание карбонила никеля в циркулирующем газе на выходе его из колонны составляет 18 г/л. Газ проходит пылевые сетчатые фильтры и поступает в трубчатый теплообменник (трубы медные), где отдает свое тепло холодному циркулирующему газу, движущемуся по межтрубному пространству. Охлажденный до 150° С газ далее поступает в холодильник-конденсатор, где его температура снижается до 10—15° С. При этом карбонил никеля конденсируется и собирается в сборниках-осадителях высокого давления. Окись углерода возвращают в реакционную колонну.
Общая продолжительность обработки материалов окисью углерода составляет примерно 3-4 сут. При этом в карбонил извлекают 96-98% Ni. Образование карбонилов железа и кобальта, как отмечалось, зависит от фазового состава материалов. При переработке передутого файнштейна значительная часть железа и кобальта, вся медь и благородные металлы оставались в твердом остатке.
Жидкий карбонил никеля, находящийся под давлением до 25 МН/м2, из сборников-отделителей выпускают в отстойник, где давление снижают до 8 МН/м2. После отстаивания для конденсации оставшегося карбонила его перепускают в следующий отстойник. Здесь давление снижают до 2-2,5 МН/м2. Далее карбонил направляют в колонну для ректификации. Постепенное снижение давления карбонила обусловливается большим количеством поглощенного газа, который при резком снижении давления бурно выделяется из жидкого карбонила, увеличивая вынос последнего в виде тумана с газами. Следует отметить, что оптимальный интервал давлений для конденсации карбонилов никеля и железа составляет 2-7 МН/м2. В связи с этим в последние годы в карбонильной технологии отдают предпочтение области средних давлений.
После окончания операции реакционную колонну охлаждают, газ из нее выпускают в газгольдер, твердый остаток выгружают и направляют на извлечение меди, кобальта и благородных металлов. Для ректификации карбонила никеля применяют ректификационные колонны непрерывного действия с насадкой из фарфоровых или медных колец. Для сокращения потерь никеля вследствие частичного термического разложения карбонила процесс ведут в два приема. При первой ректификации, которая идет при 55 – 60 °С, получают чистый карбонил никеля - дистиллят и кубовый остаток, содержащий 50% карбонила никеля и 50% карбонила железа. Кубовый остаток подвергают повторной ректификации в отдельной колонне при температуре 65 – 70 °С. Второй дистиллят, имеющий повышенное содержание железа, направляют на первую ректификацию.
Вверху колонны дистиллят конденсируется в холодильнике обратного тока и стекает в дефлегматор. Из дефлегматора часть дистиллята возвращают в колонну в качестве флегмы, остальной дистиллят охлаждают и он поступает в сборник чистого карбонила. Кубовый остаток второй ректификации состоит из смеси карбонилов кобальта и железа, воды, масла и небольшого количества карбонила никеля. Его направляют в печь для сжигания, где карбонилы разлагаются, а металлы окисляются. Окислы металлов идут на извлечение кобальта. Ректификационную колонну и аппаратуру на линии чистого карбонила изготовляют из меди, чтобы избежать загрязнения карбонила никеля примесями.
Рис 8.7 Технологическая схема карбонил-процесса (з-д Копер-Клифф, Канада):
1-кислородный конвертер; 2-реактор карбонилирования; 3-ректификационная колонна; 4-разложитель для получения никелевых гранул; 5- разложитель для получения никелевого порошка; 6- разложитель для получения железо-никелевого порошка; 7-автоклавное выщелачивание; 8-очистка растворов; 9-удаление серы из остатков; 10-выщелачивание; 11-электроосаждение меди; 12-плавка. [1, стр.106]
Чистый карбонил никеля после предварительного испарения при температуре 55-60° С подвергают термическому разложению. Пары карбонила поступают на разложение в верхнюю часть аппарата, который представляет собой цилиндр окруженный рубашкой для обогрева горячим газом. Для направления потока газа между стенками цилиндра и рубашки служит направляющая спираль. Снаружи аппарат имеет тепловую изоляцию. Получающийся при разложении никелевый порошок накапливается в нижней конической части аппарата, а окись углерода после очистки от частиц никеля направляют в газгольдер. Никелевый порошок получается крупностью 2 - 4 мкм. В нем содержится до 0,5% С, до 0,01% Fe, до 0,005% S и до 0,01% 02; другие примеси отсутствуют.
Рис 8.8 Реактор для синтеза карбонила под давлением (з-д Копер-Клифф, Канада):
1-неподвижный корпус высокого давления; 2-вращающийся сосуд с газопроницаемыми стенками; 3-газовый клапан; 4-внутренний фильтр. [1, стр.106]
На новом рафинировочном заводе «Коппер-Клифф» исходное сырье состоит из смеси металлизированной фракции, получаемой при разделительной флотации медно-никелевого файнштейна; электролитного шлама, содержащего благородные металлы; медно-никелевого сплава; остатков сульфидных анодов и файнштейна. Из этих материалов составляют шихту, содержащую 62% Ni, 14% Cu, 1% Со, 2% Fe и 20% S. Проектная производительность завода 45,3 тыс. т в год гранулированного никеля и 11,3 тыс. т в год никелевого и железо-никелевого порошков.
В настоящее время наметилась тенденция к сокращению схемы подготовки материалов к карбонил-процессу. Проведены исследования по переработке обожженных и восстановленных флотационных концентратов, рудных штейнов, обогащенного ферроникеля, различных отходов и даже окисленной никелевой руды.
Дата добавления: 2018-06-01; просмотров: 1501; Мы поможем в написании вашей работы! |
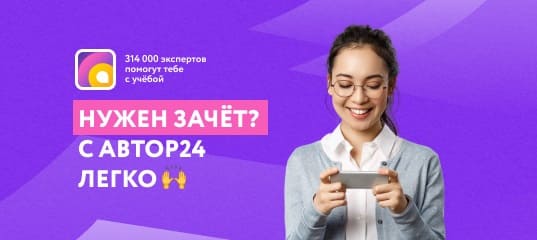
Мы поможем в написании ваших работ!