Восстановительная плавка закиси никеля на металл.
Лекция №7. Обжиг файнштейна, плавка закиси никеля на металл.
Технология получения огневого никеля из файнштейна включает стадии окислительного обжига с промежуточным обезмеживанием огарка и восстановительную плавку закиси никеля на металл.
Окислительный обжиг файнштейна.
Цель окислительного обжига файнштейна - удаление из него серы до содержания не выше 0,02 % и перевод никеля в NiO.
Глубокое удаление серы требует высоких температур, а сульфид никеля Ni3S2 легкоплавок (t = 788°С). Это вынуждает проводить окисление файнштейна в две стадии. Вначале обжиг проводят в печах КС с целью удаления серы до 1-1,5 %. Для повышения тугоплавкости шихты измельченный файнштейн смешивают с оборотной нылью. Это вместе с разобщенностью частиц, витающих в кипящем слое, позволяет вести первую стадию при 950-1000°С. Окисление файнштейна протекает по реакции
2 Ni3S2 + 7 О2 = 6 NiO + 4 SO2
Печи КС с площадью пода 7-8 м2 для первой стадии обжига никелевого файнштейна имеют ряд конструктивных особенностей. Они, во-первых, имеют увеличенный диаметр вверху, что снижает скорость газов на выходе из печи и уменьшает пылевынос богатого никелем огарка. Кроме того, разгрузка огарка производится не через сливной порог, а с уровня пода и регулируется стопорным или дисковым затвором.
Рис.7.1 Печь КС для обжига никелевого файнштейна:
1-под; 2- загрузочная труба; 3-кожух печи; 4-огнеупорная футеровка;
|
|
5-сопло; 6- воздухораспределительная коробка [3, стр171]
К горячему огарку (700-800 0С) по выходе из печи подмешивают 10-15 % природного сильвинита (NaCl, КCl) и смесь подвергают сульфато-хлорирующему обжигу в трубчатом реакторе-холодильнике. Процесс идет за счет физического тепла огарка. При, обжиге хлористый натрий разлагается по реакции
2 NaCl + SO2 + О2 = Na2SO4 + Cl2
Продукты этой реакции способствуют переводу меди в форму водорастворимых хлоридов и сульфатов. Никель и кобальт при этом остаются в оксидном состоянии.
Рис.7.2 Трубчатый реактор для сульфатохлорирующего обжига никелевого огарка:
1-загрузочная труба; 2- кожух печи; 3-огнеупорная футеровка; 4-разгрузочное устройство [1, стр118]
Из реактора огарок направляют на обезмеживание, заключающееся в выщелачивании меди горячей подкисленной водой методом просачивания. После выщелачивания огарок с остаточным содержанием 0,3-0,4 % Cu направляют на окончательный обжиг в трубчатую вращающуюся печь. Печь отапливается природным газом или мазутом, которые с целью создания в печи окислительной атмосферы сжигают с большим избытком воздуха.
Рис.7.3 Обжиговая трубчатая печь для 2-стадии обжига никелевого огарка:
|
|
1-загрузочная часть; 2- рабочая часть; 3-разгрузочная часть; 4-разгрузочное устройство; 5-холодильник; 6-пылевая камера [1, стр119]
Огарок из бункера питателем подается в хвостовую часть печи с температурой около 800 oС. Далее он движется навстречу топочным газам, содержащим 8-10 % кислорода и нагретым до 1200-1300 °С. Высокая температура и присутствие в газах кислорода приводит к почти полному окислению серы (до 0,02 % и менее). Расход топлива на второй обжиг достигает 40 % от массы огарка. Полученная в трубчатых печах закись никеля в среднем содержит, % : 78 Ni; 0,4 Cu; 0,4-0,5 Со; 0,3-0,4 Fe.
Из обжиговой печи закись никеля с температурой 900-1000 °С по течке ссыпается в трубчатый реактор, куда вводят также 4-8 % нефтяного кокса. За счет физического тепла огарка в холодильнике по реакции NiO+C = Ni+CO закись никеля частично (до 40-50 %) восстанавливается и из реактора выходит металлизированный огарок с содержанием никеля 82-86%, что ускоряет и удешевляет его дальнейшую переработку в электропечах.
Восстановительная плавка закиси никеля на металл.
Процесс восстановительной электроплавки осуществляют в дуговых электрических печах за счет тепла, выделяющегося при горении дуги между угольными (графитовыми) электродами и металлом. Для получения никеля из окисленных руд применяют трехэлектродные круглые печи емкостью 4,5-10 т. Они работают с продолжительностью цикла от 6 до 8 ч.
|
|
Технологический процесс электроплавки закиси никеля состоит из ряда операций:
· шихтовки закиси никеля с восстановителем;
· загрузки шихты и ее расплавления;
· доводки металла;
· выпуска и грануляции никеля.
Во время приготовления шихты закись никеля смешивают в заданной пропорции с Твердым восстановителем, чаще всего нефтяным коксом, содержащим 0,2-0,5 % S.
При расплавлении шихты происходит восстановление закиси никеля до металла и одновременно его науглероживание за счет растворения углерода и образующегося карбида Ni3С. При содержании углерода около 2,2 % температура плавления металла снижается до 1315°С, это сокращает время расплавления шихты и расход электроэнергии. В конце плавки избыток углерода удаляют путем доводки металла забрасыванием в печь закиси никеля. При этом происходит взаимодействие карбида никеля с NiО по реакции:
Ni3C+2 NiO=5 Ni+CO2
При доводке с целью предотвращения вторичного окисления никеля кислородом печной атмосферы в печи наводят известковый шлак. Этот шлак позволяет также очистить металл от серы за счет взаимодействия по реакции
|
|
Ni3S2 + 2 CaO + 2 C= 3 Ni + 2 CaS + 2 CO.
Образующийся сульфид кальция не растворяется в никеле и переходит в шлак. После снятия шлака металл разливают, наклоняя печь в сторону разливочного желоба.
Готовый металл льют в грануляционные бассейны с проточной холодной водой, на дне которых установлена дырчатая металлическая корзина. Полученные гранулы никеля извлекают из бассейна, сушат, упаковывают в фанерные бочки и отправляют потребителю. Огневой никель по ГОСТ 849-70 должен содержать суммарно никеля и кобальта не менее 98,6 % (Н-3) и кобальта не более 0,7 %.
7.3. Производство ферроникеля из окисленных никелевых руд.
Устранение большинства недостатков традиционной технологии переработки окисленных никелевых руд достигается при их переработке на ферроникель - сплав железа с никелем, в который переходит и кобальт. Этот способ в последние годы получает все большее распространение и относится к восстановительным процессам. При плавке на ферроникель достигается значительное упрощение технологической схемы переработки окисленных никелевых руд, существенное повышение извлечения никеля и кобальта, улучшение использования вещественного состава руды, а также экономия топлива.
Плавку на ферроникель в основном ведут в рудно-термических печах. Главные преимущества электроплавки - возможность использования руд с тугоплавкой, магнезиально-силикатной пустой породой, получение достаточно высокого извлечения металлов, небольшой расход низкосортного восстановителя и высокая комплексность использования
Ферроникель можно применять непосредственно в черной металлургии при получении легированных сталей или перерабатывать на, марочные сорта никеля и кобальта. Применяется переработка окисленных никелевых руд на ферроникель электротермическим способом в промышленном масштабе в России, Новой Каледонии, США, Японии и Бразилии. В России по такой технологии работает Побужский никелевый завод. Технологическая схема получения ферроникеля включает агломерацию или сушку или прокаливание руды с частичным восстановлением оксидов железа и никеля до металла, электроплавку в руднотермической печи на ферроникель и шлак, рафинирование и обогащение ферроникеля в конвертерах.
При электроплавке оксиды никеля восстанавливаются углеродом по реакции
NiО + С = Ni + СО.
Одновременно с никелем восстанавливаются кобальт, железо, хром и кремний. В результате плавки получают ферроникель, загрязненный в основном кремнием, серой и углеродом.
Состав получаемого чернового ферроникеля определяется составом исходной руды и степенью восстановления железа. Так, в Новой Каледонии при электроплавке окисленных руд, содержащих около 3 % Ni, получают ферроникель с содержанием 23-24 % Ni+Co. При переработке бедной окисленной никелевой руды (0,8-0,9 % Ni), на Побужском заводе оказалось целесообразным получать сплав с 5-10 % Ni+Co. Получающиеся при этом шлаки содержат, % : 0,04-0,07 Ni; 0,004-0,02 Со; 48-52 SiO2; 12-14 FeO; 20-30 (CaO+MgO). Извлечение никеля при плавке составляет 95-97%, кобальта 85-90%.
При использовании в черной металлургии черновой сплав рафинируют в конвертере с получением ферроникеля с содержанием кремния, углерода, серы и фосфора не более 0,03 % каждого. Для селективного извлечения никеля и кобальта в самостоятельные продукты ферроникель обогащают. Для этого черновой сплав подвергают окислительной продувке в конвертерах с целью перевода части железа в шлак, который можно использовать в качестве сырья для доменного производства.
Обогащение ферроникеля за счет окисления железа на Побужском заводе ведут в вертикальных конвертерах путем продувки расплава технологическим кислородом (99,2-99,6 % О2) с помощью вертикальных фурм (сопел).
Товарный ферроникель с содержанием 19-25 % Ni и 1-1,2 % Со разливают в слитки массой по 45-50 кг. Извлечение никеля и кобальта при рафинировании составляет около 95-96 %. Одним из возможных способов извлечения никеля и кобальта из такого ферроникеля является его переработка в качестве холодных присадок при конвертировании штейнов на файнштейн. Файнштейн и кобальтсодержащие конвертерные шлаки перерабатывают по описанной выше технологии.
Дата добавления: 2018-06-01; просмотров: 1948; Мы поможем в написании вашей работы! |
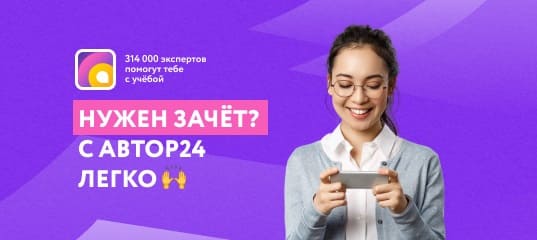
Мы поможем в написании ваших работ!