Технологическая схема переработки сульфидных никелевых руд.
Лекция №6. МЕТАЛЛУРГИЯ НИКЕЛЯ, Технологические схемы переработки окисленных и сульфидных руд.
Никелевая промышленность, возникшая в конце XIX столетия, является сейчас одной из крупнейших отраслей цветной металлургии. По производству и потреблению никель занимает пятое место среди цветных металлов. Для извлечения никеля из всех видов рудного сырья используют как пиро-, так и гидрометаллургические процессы. Применяемые в настоящее время при производстве никеля технологические схемы построены преимущественно на сочетании пирометаллургических и гидрометаллургических методов.
В металлургии никеля существует как бы два самостоятельных технологических направления, что связано с использованием двух видов руд - окисленных и сульфидных, которые различаются по химическому составу и физическим свойствам.
Технологическая схема переработки окисленных никелевых руд.
Из пирометаллургических методов переработки окисленного никелевого сырья применяется восстановительно-сульфидирующая шахтная плавка на никелевый штейн и плавка на ферроникель в электропечах. Переработка окисленных никелевых руд заканчивается получением, как правило, так называемого огневого никеля, отправляемого потребителю без дополнительного рафининирования. Никель очищается от небольшого числа примесей (Fe, Co, Cu, S) в течение всей многостадийной технологии. Этот никель по ГОСТ 849-70 отвечает маркам Н-3 и Н-4.
|
|
При переработке окисленных никелевых руд на ферроникель технология упрощается, сохраняя лишь операции подготовки шихты и плавки материалов в электропечах. Ферроникель после проведения рафинирования от вредных примесей в конвертерах с кислой и основной футеровкой является товарной продукцией и применяется в производстве сплавов. На заводах цветной металлургии применяются и другие технологии, имеющие особенности, обусловленные составом исходного сырья и другими причинами.
Технологическая схема восстановительно-сульфидирующей плавки окисленных никелевых руд приведена на рис.6.1.
1.Окисленная никелевая руда после сушки и подготовки по крупности смешивается с сульфидизатором и брикетируется на валковых прессах. Готовые брикеты совместно с коксом загружаются в шахтную плавильную печь для выплавки никелевого штейна.
2. В шахтную печь загружают порции никелевых брикетов или никелевый агломерат, а также кокс и оборотные материалы. Для сжигания кокса, являющегося топливом и восстановителем в печь, через фурмы подается воздушное дутье. В шахтной печи при достижении необходимых температур протекают реакции восстановления оксидов никеля и железа, образования сульфидов указанных металлов, плавление компонентов пустой породы с образованием шлака и сульфидов с образованием штейна. Продукты шахтной плавки- штейн и шлак выпускаются совместно в наружный горн, где разделяются по плотности, а технологические газы после очистки от пыли сбрасываются в атмосферу. Шлак, содержащий до 0,17% никеля, является отвальным.
|
|
3. Штейн выпускается из наружного горна в ковши и подается в расплавленном виде в конвертер. Конвертирование никелевого штейна проводится обычно в горизонтальных цилиндрических конвертерах при подаче воздушного дутья в расплав через фурмы и загрузке через горловину кварцевого флюса. При конвертировании окисляется металлическое и сульфидное железо штейна. Оксиды железа с кремнеземом кварца образуют силикаты и переходят в шлак. Процесс заканчивается получением никелевого файнштейна, состоящего в основном из сульфида никеля с небольшим количеством сульфида меди и других примесей. Файнштейн из конвертера отливают в чугунные изложницы, охлаждают, дробят, измельчают и обжигают.
4. Файнштейн перерабатывают по 2-3-х стадийной схеме обжига на закись никеля и восстановительной плавки закиси на металл. Если окисленная руда содержала примеси меди и других цветных металлов, то файнштейн медленно охлаждают, что способствует росту кристаллов составляющих сульфидов. После операций дробления и измельчения файнштейн направляется в процесс флотации с выделением медного и никелевого концентратов. Медный концентрат отправляется на медеплавильные заводы, а никелевый подвергается окислительному и хлорирующему обжигу. Первая стадия окислительного обжига проводится в печах кипящего слоя до остаточного содержания серы 1-3%. Полученный огарок поступает на хлорирующий обжиг в трубчатых реакторах с последующим водным выщелачиванием огарка. При хлорирующем обжиге и выщелачивании большая часть примеси меди выводится из огарка в виде хлорида меди (CuCl2). Остаток от выщелачивания подвергают второй стадии окислительного обжига в трубчатых печах с получением закиси никеля (NiO).
|
|
Рис.6.1 Технологическая схема восстановительно-сульфидирующей шахтной плавки окисленных никелевых руд.
5. Закись никеля подают на восстановительную электроплавку в дуговых печах. Плавку ведут с восстановителем (кокс) и известняковым флюсом. Огневой никель в зависимости от содержания примесей (кобальт, платиноиды, медь) разливают в изложницы в виде анодов, направляемых на электролиз, либо гранулируют водой.
|
|
6. При содержании ценных примесей никель направляется на электролитическое рафинирование в ваннах с разделением анодного и катодного пространства пористой перегородкой (диафрагмой). Никель, при электролизе растворяясь на анодах, осаждается на катодах в виде металла чистотой до 99,99%. Ценные сопутствующие компоненты (Co, Se, Te, Au, Ag, Pt-ды) концентрируются в шламе и извлекаются при его переработке.
В значительных масштабах никель получается при плавке окисленных никелевых руд на сплав железа и никеля (ферроникель) в электропечах. При переработке окисленных никелевых руд на ферроникель технология значительно упрощается, сохраняя лишь операции подготовки шихты и плавки материалов в электропечах. Ферроникель после проведения рафинирования от вредных примесей в конвертерах с кислой и основной футеровкой является товарной продукцией и применяется в производстве сплавов. Кроме приведенных принципиальных технологических схем, на заводах цветной металлургии применяются и другие технологии, имеющие особенности, обусловленные составом исходного сырья и другими причинами.
Технологическая схема переработки сульфидных никелевых руд.
Значительные запасы никеля сосредоточены в сульфидных медно-никелевых рудах, технологическая схема переработки которых дана на рис. 8.2. Головные операции обжига и плавки медно-никелевого сырья аналогичны операциям в металлургии меди и для их проведения используются в целом идентичные обжиговые и плавильные печи. Сырье содержит значительное количество тугоплавких компонентов (кремнезем, оксиды магния) и для плавки более приемлема рудно-термическая электропечь, в которой возможна концентрация выделяемого тепла и достижение высоких температур шлака.
В отличие от медного производства при конвертировании медно-никелевого штейна получают файнштейн, состоящий из сульфида никеля (Ni3S2), сульфида меди (Cu2S) и небольшого количества металлической фазы на основе железа и никеля (ферроникель), в которой растворены металлы платиновой группы. Файнштейн медленно охлаждают, дробят, измельчают и направляют в процесс флотации с выделением медного и никелевого концентратов. Медный концентрат отправляется на медеплавильные заводы, а никелевый подвергается окислительному и хлорирующему обжигу. Первая стадия окислительного обжига проводится в печах кипящего слоя до остаточного содержания серы 1-3%. Полученный огарок поступает на хлорирующий обжиг в трубчатых реакторах с последующим водным выщелачиванием огарка. При хлорирующем обжиге и выщелачивании большая часть примеси меди выводится из огарка в виде хлорида меди (CuCl2). Остаток от выщелачивания подвергают второй стадии окислительного обжига в трубчатых печах с получением закиси никеля (NiO), которую подают на восстановительную электроплавку в дуговых печах. Плавку ведут с восстановителем (кокс) и известняковым флюсом. Огневой никель в зависимости от содержания примесей (кобальт, платиноиды, медь) разливают в изложницы в виде анодов, направляемых на электролиз, либо гранулируют водой.
При содержании ценных примесей никель направляется на электролитическое рафинирование в ваннах с разделением анодного и катодного пространства пористой перегородкой (диафрагмой). Никель при электролизе растворяясь на анодах осаждается на катодах в виде металла чистотой до 99,99%. Сопутствующие компоненты (Co, Se, Te, Au, Ag, Pt-ды) концентрируются в шламе и извлекаются при его последующей переработке.
Технологическая схема переработки сульфидных медно-никелевых руд заканчивается обязательным рафинированием чернового (огневого) никеля. Это позволяет не только получать никель высших марок, вплоть до никеля особой чистоты (>99,99 % Ni), но и обеспечивает высокое извлечение еще 13 ценных компонентов, содержащихся в перерабатываемых рудах или концентратах. Технологическая схема переработки сульфидных никелевых руд складывается из следующих операций:
1.На никелевые заводы поступают сульфидные никелевые и медно-никелевые концентраты. Концентраты смешивают в шихтарниках с флюсами и оборотными материалами, усредняют до состава принятого технологической инструкцией.
2. Шихта направляется на агломерирующий обжиг на прямолинейных ленточных машинах с площадью спекания 50-75 м2. Так как никелевые концентраты содержат меньше серы сульфидов, при окислении которых выделяется необходимое тепло для спекания, в шихту никелевой агломерации добавляется коксик.
3. Никельсодержащая шихта либо агломерат проплавляется в печах с получением медно-никелевого штейна, отвального шлака и запыленных технологических газов. Головные операции обжига и плавки медно-никелевого сырья аналогичны операциям в металлургии меди и для их проведения используются в целом идентичные обжиговые и плавильные печи. Сырье обычно содержит значительное количество тугоплавких компонентов (кремнезем, оксиды магния) и для его плавки более приемлема рудно-термическая электропечь, в которой возможна концентрация выделяемого тепла в объеме шихты и достижение высоких температур шлака. Штейн никелевой плавки беднее по содержанию металла (Ni+Cu около 15-20%) нежели штейн медного производства (30-55% Cu). Штейновый расплав ковшами подается для конвертирования в горизонтальных конвертерах. Шлак после грануляции водой вывозится в отвал. Запыленные газы направляются для очистки в систему грубого и тонкого пылеулавливания.
4. Конвертирование штейна заключается в продувке расплава воздухом при подаче кварцевого флюса, с целью окисления и ошлакования железа присутствующего в штейне в виде сульфида (FeS), а также магнетита (Fe3O4) или металла (Fe-Ni). В отличие от медного производства при конвертировании медно-никелевого штейна получают медно-никелевый файнштейн, состоящий из сульфида никеля (Ni3S2), сульфида меди (Cu2S) и небольшого количества металлической фазы на основе железа и никеля (ферроникель), в которой растворены металлы платиновой группы. Медно-никелевый штейн охлаждают в чугунных изложницах и направляют на дробление, измельчение и разделение флотацией. Конвертерный шлак возвращается в плавильный агрегат, либо перерабатывается с целью извлечения кобальта.
5. Для разделения меди и никеля содержащихся в файнштейне применяют различные способы: ликвационное разделение в котлах на топ и ботом; электролиз файнштейна; карбонил процесс высокого давления; разделение сульфидов файнштейна флотацией. Способ разделения флотацией основан на медленном охлаждении расплава файнштейна в изложницах с целью увеличения размеров кристаллов сульфидов в области температур между линиями ликвидуса и солидуса, по диаграмме состояния Cu2S-NiS. При флотации измельченного файнштейна получают никелевый и медный сульфидные концентраты с высоким содержанием основного металла. Эти концентраты направляют на дальнейшую переработку по схемам никелевого и медного производств.
6. Никелевый концентрат содержит сульфид Ni3S2, а также примеси меди, железа, кобальта, платиновых и благородных металлов. Концентрат направляют в схему 3-х стадийного обжига с целью получения закиси никеля NiO. На первой стадии концентрат обжигают в печах кипящего слоя с получением огарка содержащего 1-3% серы. На второй стадии огарок подвергают сульфато-хлорирующему обжигу в трубчатых вращающихся печах с добавлением хлоридов. В конце печи имеется барабан для выщелачивания образовавшихся хлоридов и сульфатов меди из огарка водой. После выщелачивания огарок содержащий 0,1-0,3% S подается в трубчатые печи отапливаемые малосернистым топливом для окончательногшо удаления серы при температурах 1000-1100 оС. Дисперсная закись никеля NiO после обжига загружается в кюбели и направляется для восстановительной плавки в дуговых печах.
Рис.6.2 Технологическая схема электроплавки сульфидных медно-никелевых руд.
7. Восстановительная плавка закиси никеля проводится в трехэлектродных дуговых печах с получением расплава никеля. Для восстановления никеля в шихту плавки задается малосернистый нефтекокс. Для удаления примеси серы загружается известняк и добавляется свежая порция закиси никеля. Для окончательного удаления кислорода внесенного закисью никеля на этапе десульфуризации загружается металлический кремний. Полученный никель разливается на аноды в охлаждаемые изложницы. Аноды с целью получения никеля чистотой 99,99% и извлечения платиновых и благородных металлов, а также кобальта направляются в процесс электролиза.
8. Электролитическое рафинирование проводится в прямоугольных ваннах - электролизерах. Ванна изготавливается из железобетона футерованного изнутри полимерной коробкой, либо из полимербетона. Катоды из тонкого никеля помещают в диафрагмы - коробки обтянутые тканью устойчивой в электролите. Аноды из никеля с примесями подвешивают за ушки в пространстве между диафрагменными коробками. В катодное пространство диафрагм подают электролит очищенный от примесей меди, железа, кобальта, мышьяка, сурьмы и др. На анодах происходит электролитическое растворение никеля и примесей и образование шлама содержащего платиновые металлы, золото и серебро. Образовавшийся при растворении анодов загрязненный примесями электролит (анолит) выводится из ванны через сифоны, предотвращая вынос частиц шлама. Анолит направляется для очистки от примесей методам нейтрализации кислоты закисью никеля, осаждения гидратов трехвалентных металлов (железа, мышьяка, сурьмы), выделения солей примесей. Очищенный анолит после коррекции состава по серной кислоте и ионов хлора направляется в качестве католита в катодное пространство диафрагм электролизеров.
При рассмотрении технологических схем переработки окисленных никелевых и сульфидных медно-никелевых руд обращает на себя внимание следующее:
· подготовка окисленных и сульфидных рук к плавке на штейн различна;
· обязательными процессами для обеих технологических схем являются плавка на штейн, конвертирование штейнов, окислительный обжиг файнштейна или богатого никелевого концентрата, восстановительная плавка закиси никеля на металл;
· для образования штейна при плавке окисленных никелевых руд, в шихту вводится серусодержащий материал - сульфидизатор (гипс CaSO4.2H2O или пирит FeS2);
· при переработке сульфидных руд обязательно проводят операции разделения меди и никеля и электролитического рафинирования чернового никеля;
· никель, полученный из сульфидных руд, отличается более высокой чистотой по сравнению с огневым никелем;
· кобальт из технологической цепочки выводится в первом случае с конвертерными шлаками, а во втором - при электролитическом рафинировании.
Попутное получение кобальта при металлургической переработке никелевых руд является характерной особенностью никелевой промышленности. В России из окисленных никелевых и сульфидных медно-никелевых руд получают более 80 % кобальта от общего выпуска в стране. Так кобальт впервые в мире был получен в 1937 г. на Уфалейском никелевом заводе. Позднее производство кобальта было организовано также на всех никелевых заводах. В 1970 г. впервые выдал кобальтовую продукцию комбинат «Тувакобальт», работающий на базе кобальтово-никелево-медных мышьяковистых руд.
Технологическая схема получения никеля из окисленных руд сложна, приводит к высоким потерям никеля и кобальта, требует большого расхода дорогостоящего кокса. Упрощение технологии, повышение извлечения никеля и кобальта и сокращение электрических затрат достигаются при плавке окисленных никелевых руд на ферроникель.
На ряде заводов для переработки как окисленных (Куба), так и сульфидных руд (Россия и Канада) применяют гидрометаллургические схемы. Обладая рядом преимуществ при переработке бедных руд (выше извлечение), эти схемы сложны и применимы для ограниченного состава руд.
Дата добавления: 2018-06-01; просмотров: 2514; Мы поможем в написании вашей работы! |
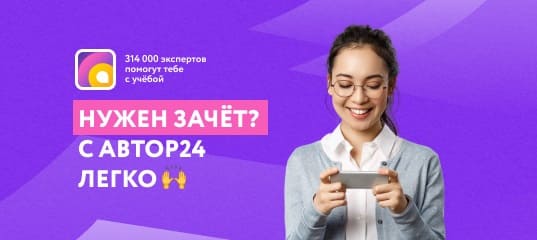
Мы поможем в написании ваших работ!