Обжиг сульфидных медных концентратов.
Лекция №2. МЕТАЛЛУРГИЯ МЕДИ
Тенденции в развитии производства меди
Крупнейшими производителями меди являются Чили, США, Китай и Россия. Ранее крупным производителем была Япония - импортировавшая почти все сырье из стран Азии, Океании и Австралии. В больших количествах производят медь в Замбии, Канаде и ФРГ. В Казахстане медь производят предприятия ТОО «Корпорация Казахмыс» (Балхашский и Джезказганский МЗ), в Узбекистане - Алмалыкский ГМК. В России на базе крупных месторождений работают Норильский ГМК, Красноуральский и Североуральский медеплавильные заводы, Пышминский МЭЗ. В Восточном Забайкалье, на базе Удоканского месторождения медных руд, в Сибири в ближайшее время возникнет новый мощный горно-обогатительный и металлургический комплекс.
На металлургических предприятиях внимание уделяется вопросам рационального использования энергетических ресурсов, включая вторичные. При этом основными направлениями развития с 70-х годов являлись: разработка и внедрение автогенных энергосберегающих технологий, внедрение экономичных схем энергоснабжения, повышение степени использования вторичных энергоресурсов до 80-85%.
Характерной чертой развития производства цветных металлов является увеличение доли развивающихся стран в общем объеме производства и потребления. В развивающихся странах создаются дочерние предприятия крупных фирм с полным производственным циклом от добычи руды до получения полуфабрикатов, металлов и изделий. В выпуске цветных металлов возрастает роль вторичного сырья, что обусловлено высоким экономическим эффектом за счет снижения затрат на проведение горных работ, энергию и охрану окружающей среды. В структуре сырья увеличивается доля автомобильного и электробытового лома, городских отходов, отработанных катализаторов, тары и т.п.
|
|
Расширяется применение гидрометаллургии схем при вскрытии руд и концентратов, рафинировании, разделении и выделении металлов, а также при переработке промпродуктов. Гидрометаллургия все шире применяется для переработки низкосортных и забалансовых руд. До 15% меди от общего выпуска получают способами отвального, кучного и подземного выщелачивания. В гидрометаллургии активно исследуются и внедряются автоклавные процессы, позволяющие решать проблемы комплексности использования сырья, экологии и достижения высокой производительности, сопоставимой с пирометаллургическими процессами.
Технология переработки сульфидных медных концентратов.
Основное количество меди из первичного сырья получают методами пирометаллургии, а гидрометаллургические схемы применяются в ограниченных масштабах для переработки забалансового сырья, отходов обогатительных фабрик и рудников. Пирометаллургическая схема (рис.2.1) переработки медного сырья может включать операции предварительного окислительного обжига на порошок или окускованный агломерат. Наличие в схеме обжига определяется последующей технологией плавки и содержанием серы в исходных концентратах. Целью окислительного обжига медных руд и концентратов в пирометаллургии является удаление избытка серы. Плавка обожженных материалов позволяет получать более богатые по меди штейны, сокращает топливные и энергетические затраты за счет использования тепла горячего огарка. Обжиг на порошок проводится в многоподовых печах или в печах кипящего слоя, а спекающий обжиг на ленточных агломерационных машинах. Агломерация шихты необходима перед шахтной плавкой.
|
|
Распространенная до настоящего времени технология предусматривает использование следующих металлургических процессов: плавку на штейн, конвертирование медного штейна, огневое и электролитическое рафинирование меди. В ряде случаев перед плавкой проводят окислительный обжиг сульфидного сырья.
|
|
1. Поступающие на медеплавильные заводы, сульфидные концентраты смешивают с необходимыми флюсами (кварцевая руда, окисленная железная руда, известняк, оборотные материалы). Полученная смесь материалов - шихта, при высоком содержании серы подвергается предварительно обжигу с частичным удалением серы в газы. При обжиге может преследоваться цель спекания мелкодисперсных материалов для получения кускового агломерата.
Рис.2.1 Технологическая схема переработки сульфидных медных концентратов.
2.Медный огарок, агломерат или необожжённая шихта подвергаются плавке на штейн (расплав Cu2S-FeS) в печах различного типа. Распространенным способом плавки остается отражательная плавка, расширяется применение процессов плавки в рудно-термических электропечах, а также различные варианты автогенных процессов. В процессе плавки медь на 96-98% переходит в штейн. В штейне также концентрируются благородные металлы, растворяются примеси свинца, теллура, селена и т.д. Основная часть железа, кремнезем и другие компоненты пустой породы переходят в шлак. Часть серы при плавке за счет диссоциации высших сульфидов и реакций взаимодействия оксидов с сульфидами при плавке удаляется с технологическими газами в виде сернистого ангидрида.
|
|
3.Штейн, состоящий из сульфидов меди и железа, направляется на конвертирование в горизонтальных конвертерах. В процессе конвертирования расплав штейна продувается воздухом для окисления и ошлакования железа в первом и получения меди во втором периоде процесса. Продуктами процесса конвертирования являются: черновая медь, направляемая на рафинирование; оборотный конвертерный шлак, содержащий до 3% меди и возвращаемый в печь для выплавки штейна; технологические газы, содержащие до 6-8% SO2.
4.Запыленные технологические газы очищаются в системе грубого пылеулавливания (пылевые камеры, котлы утилизаторы, циклоны). Грубая пыль содержащая механически увлеченные частицы шихты, возвращается в систему подготовки шихты. Технологические газы из системы грубой очистки направляются в систему тонкой очистки (рукавные фильтры, мокрые или сухие электрофильтры). Тонкие пыли обычно содержат легколетучие металлы (свинец, цинк) и редкие металлы. Тонкую пыль направляют либо в гидрометаллургические цеха для извлечения ценных компонентов.
5.Рафинирование черновой меди осуществляют последовательно в две стадии. На первой стадии огневого рафинирования, проводимой в анодных печах, примеси удаляют путем окисления воздухом и ошлакования. Окисленный металл восстанавливают мазутом или природным газом и разливают в виде анодов специальной формы. Аноды после охлаждения направляют на электролитическое рафинирование.
6.Электролиз анодной меди проводят в ваннах из железобетона, футерованных полимерами или в полимербетонных ваннах. В ванны подвешивают катоды из чистой тонкой меди и аноды. Электролиз проводится в водных растворах H2SO4-CuSO4-примеси-добавки ПАВ. При электролизе медь растворяется на анодах, переносится в виде ионов в растворе и осаждается на катодах. Примеси более электроположительных металлов по сравнению с медью (Ag, Au, Cu2Te, Cu2Se) переходят в осадок (шлам). Часть электролита, в котором накапливаются более электроотрицательные примеси (Fe, Ni, As, Sb), выводится на очистку в купоросное отделение. Часть электролита охлаждается и возвращается в ванны после коррекции состава.
7.Осаждение меди на катодах проводится 6-8 суток. Товарные катоды промывают горячей и холодной водой с добавкой моющих средств, сушат и укладывают в пакеты на специальной установке. Пакеты упаковывают в полиэтилен на вакуумной установке. Катодная медь чистотой 99,9-99,99% в необходимых случаях подвергается индукционной вакуумной переплавке с получением бескислородной вайербарсовой меди для проката.
8. Электролит содержит 50-60 г\л Cu, до 110-120 г\л H2SO4, а также примеси Fe, Ni, As, Sb и др. Содержание примесей в зависимости от режима электролиза составляет 2-20 г\л. Электролит направляют на нейтрализацию кислоты за счет растворения медного лома и отходов и окисление примесей Fe2+ до Fe3+, также мышьяка и сурьмы за счет аэрации раствора воздухом. При нейтрализации раствора повышается концентрация меди в виде CuSO4 и снижается кислотность до PH=3,5-4,5. При низкой кислотности протекают реакции гидролитического осаждения железа (Fe(OH)3) и частично мышьяка и сурьмы. Очищенный от примесей раствор сульфата меди направляется на упаривание и кристаллизацию медного купороса CuSO4.5H2O. Операции повторяют 2-3 раза с получением купороса 1,2 и 3 сорта.
Обжиг сульфидных медных концентратов.
Наиболее распространенными способами переработки сульфидного медного сырья до настоящего времени являются различные методы концентрационной плавки на штейн.
Перед плавкой в отражательных или электрических печах обжиг проводится без расплавления шихты. Плавка в шахтных печах требует окускования мелких руд или флотационных концентратов. В этих случаях обжиг сопровождается спеканием шихты с получением крупнокускового продукта - агломерата. Процесс проводится на прямолинейных агломерационных машинах с верхней или нижней подачей дутья. На заводах применяются агломашины с площадью спекания 50 - 75 м2.
В отражательных печах плавят мелкодисперсное сырье и в этом случае для окислительного обжига используют многоподовые или более современные и производительные печи кипящего слоя.
В металлургии меди применяют сульфатизирующий и окислительный виды обжига. Целью сульфатизирующего обжига применяемого в гидрометаллургии является перевод извлекаемых металлов в легко растворимые в воде сульфаты и растворимые в растворах кислот оксиды.
Целью окислительного обжига, в пирометаллургии меди является частичное удаление серы и перевод части сульфидов железа в оксиды легко шлакуемые при последующей плавке. Обжиг позволяет получить при плавке, богатые штейны с содержанием не менее 25-30% Cu, а также использовать богатые по содержанию SO2 газы для производства серной кислоты. Окислительный обжиг применяется при переработке высокосернистых, бедных по меди концентратов, а также при переработке медного сырья с повышенным содержанием цинка с целью окисления сульфида и перевода оксида цинка в шлак.
Окислительный обжиг проводят при 750-900 °С. Процесс обжига состоит из следующих основных элементарных стадий:
· нагрева и сушки шихты,
· термической диссоциации высших сульфидов,
· воспламенения и горения сульфидов.
Нагрев шихты сопровождается удалением влаги и происходит как за счет теплопередачи от горячих газов, так и за счет тепла реакций окисления. После нагрева шихты до 350-400°С начинаются процессы диссоциации сульфидных минералов и их воспламенение. Термическому разложению подвергаются только высшие сульфиды по реакциям:
FeS2 = FeS + 1/2 S2
2 CuFeS2 = Cu2S + 2 FeS + 1/2 S2
2 CuS = Cu2S + 1/2 S2
Выделяющиеся пары серы сгорают в окислительной атмосфере печи по реакции:
S + O2 = SO2
Все реакции термической диссоциации эндотермичны и требуют затрат тепла на их осуществление. В процессе обжига возможно частичное разложение карбонатов:
СаСО3 = СаО + СО2
Окисление сульфидов начинается с их воспламенения. Под температурой воспламенения подразумевают температуру, при которой количество выделяющегося тепла становится достаточным для начала интенсивного горения всей массы сульфидного материала. Температура воспламенения сульфидов зависит от их физико-химических свойств и тонины помола. Пирит, халькопирит и халькозин при крупности зерен около 0,1 мм начинают гореть при температурах соответственно 325, 360 и 430 °С.
При окислительном обжиге медных концентратов преимущественно окисляются сульфиды железа. Основные реакции окислительного обжига медных концентратов:
2 FeS + 3,5 О2 = Fe2O3 + 2 SO2 + 921000 кДж
2 FeS2 + 5,5 О2 = Fe2O3 + 4 SO2 + 1655000 кДж
2 CuFeS2 + 6 О2 = Fe2O3 + Cu2O + 4 SO2
При обжиге возможно также окисление сульфидов меди по реакции
Cu2S + 1,5 O2 = Cu2O + SO2 + 38435 кДж
Однако вследствие большого сродства меди к сере она вновь сульфидируется по обменной реакции и Cu2O фактически в огарке не будет.
Cu2O + FeS = Cu2S + FeO + 168060 кДж.
Все реакции окисления сульфидов и элементарной серы экзотермичны. Выделяющегося в условиях обжига медных концентратов тепла, достаточно для самопроизвольного протекания обжига, который является типичным автогенным процессом.
При взаимодействии кислорода с каким-либо сульфидом на поверхности его зерна образуется оксидная пленка. Скорость роста пленки оксидов будет зависеть от количества подводимого к реакционной поверхности кислорода и скорости его диффузионного проникновения внутрь частицы. Для ускорения процесса окисления нужен интенсивный массообмен в газовой фазе, обеспечивающий удаление от поверхности твердых частиц продукта реакции - сернистого ангидрида, а следовательно, облегченный подвод к частице окислителя. При недостаточной продолжительности обжига внутри частицы может сохраниться сульфидное ядро.
Продуктами обжига являются огарок, газы и пыль. Минералогический состав огарка будет резко отличаться от состава исходного концентрата. Получающийся огарок характеризуется наличием в нем наряду с сульфидами- оксидов и практически полным отсутствием высших сульфидов. При проведении обжига возможно образование небольших количеств сульфатов меди, железа и цинка. Окислительный обжиг сульфидных материалов перед плавкой на штейн сохраняет одну и ту же физико-химическую основу независимо от вариантов аппаратурного оформления.
Рис.2.2 Многоподовая печь с механическим перегребанием;
1-опорные колонны; 2- корпус печи; 3- дверца; 4- опорное кольцо; 5 – лапа рабочего пода;
6 – воздухоподводящая труба; 7 – лапа подсушивающего пода; 8 – опорная конструкция;
9 – соединительная муфта; 10 – опорные ролики; 11- рама; 12-питающее устройство; 13-рычаг;
14-тяга гребка, регулирующего подачу концентрата; 15-разгрузочное отверстие; 16-грохот;
17-воронка для огарка; 18-воронка для крупного материала; 19-подпятник; 20-коническая шестерня;
21- вал печи. [4, стр.515]
Режимные параметры и показатели обжига медных сульфидных концентратов. Обжиг в кипящем, слое является высокопроизводительным процессом. Это обусловлено развитой удельной поверхностью контакта твердой и газообразной фаз. Окисление сульфидов в этих условиях идет очень интенсивно, даже при небольшом избытке воздуха (10 - 20 % более от теоретически необходимого). При достаточной герметизации печей это позволяет получать газы, содержащие до 12 - 14 % SO2. Производительность печей КС по концентрату в 4-5 раз выше, чем при обжиге в механических многоподовых печах. Конструкция печей КС проста, а их работа легко поддается механизации и автоматизации.
Шихта поступающая на обжиг содержит, %: 9-14 Cu; 2-16 Zn; 22-29 Fe; 22-35 S; 2-3 CaO; 20-25 SiO2. Выход огарка при скорости псевдоожижжения 0,18-0,22 м/сек составляет 60-70% и выход пыли соответственно-30-40%. С увеличением скорости дутья в печи КС до 0,3-0,6 м/сек выход огарка выгружаемого через порог печи снижается до 15-20%, а выход пыли возрастает до 80-85%.
Обжиг в кипящем слое позволяет поддерживать температуру в достаточно узких пределах и создавать нужный состав газов в печи. Это дает возможность проводить в печах КС как окислительный , так и сульфатизирующий виды обжига.
Обжиг медных концентратов начиная с 1959 г. применялся на медеплавильном комбинате им.Г.Дамянова (Болгария), с 1964 г на Среднеуральском медеплавильном заводе (Россия), а также с 1980-х годов на заводах "Копперхилл" (США), "Наосима" (Япония), "Люаншиа" (Замбия) и др.
Рис.2.3 Печь кипящего слоя для обжига сульфидных концентратов:
а) печь СУМЗа; б) печь АМХК; 1-воздушная коробка; 2- уровень шихты; 3- окна для форсунок;
4- подина; 5 – форкамера. [Гудима-3,стр.108]
Таблица 2.1 Технико-экономические показатели обжига медных концентратов:
Показатели | Печи КС | Многоподовые печи |
Производительность по шихте, т/сут | 1000-1100 | 200-250 |
Десульфуризация, % | 55-60 | 58-60 |
Температура обжига, °С | 870-890 | 800 |
Вынос пыли, % | 83-84 | 10-15 |
Содержание SO2 в газах, % | 13-15 | 6-7 |
Дата добавления: 2018-06-01; просмотров: 2869; Мы поможем в написании вашей работы! |
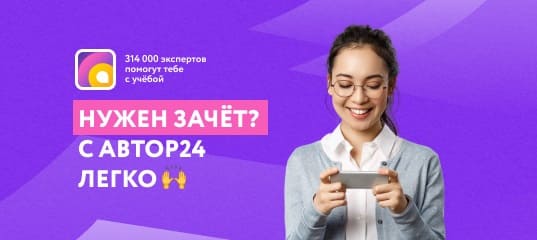
Мы поможем в написании ваших работ!