Подшипниковые щиты и подшипники
Глава З
КОНСТРУКЦИЯ ЭЛЕКТРИЧЕСКИХ МАШИН
Общие принципы конструирования
Конструирование начинается с разработки общих видов машины — продольного и поперечного. При конструировании учитываются требования к повышению надежности и экономичности в эксплуатации, к удобству в обслуживании, к снижению трудоемкости изготовления, к стоимости, к размерам и массе машин.
Трудоемкость изготовления машин определяется не только применяемым в производстве оборудованием, но и технологичностью конструкции. Для того чтобы конструкция деталей и узлов больше содействовала прогрессивным методам производства, конструкторы должны работать в непосредственном контакте с технологами. При наличии противоречивых требований к конструкции выносимое решение определяется с учетом технико-экономической эффективности вариантов конструкции.
Особенно важно соблюдение принципов технологичности конструкции для серийных машин, изготовляемых в массовых количествах. Серийное производство создает возможность как для широкой унификации деталей и узлов, так и для узкой специализации заводов по ограниченному количеству типоразмеров и изготовлений машин, что делает целесообразным и рентабельным использование автоматического оборудования, агрегатных станков, конвейеров и т. п. Трудоемкость и стоимость производства в этих случаях значительно снижаются.
|
|
Разработку конструкции ведут с учетом требований стандартов. ГОСТы регламентируют основные выходные параметры машин, ассортимент и качество материалов и полуфабрикатов. Однако ГОСТами предусмотрен довольно обширный ассортимент материалов и полуфабрикатов, рассчитанный на удовлетворение потребностей всего народного хозяйства. Для электромашиностроительных предприятий целесообразно применение только небольшой части этого ассортимента, что содействует упрощению материально-технического снабжения, планирования и учета работы предприятий. Поэтому в электропромышленности создаются отраслевые стандарты, а на заводах — стандарты предприятия, которые регламентируют для предприятий сокращенную номенклатуру материалов, полуфабрикатов и деталей, учитывающую условия работы на данном заводе; это относится в первую очередь к крепежным деталям, проводам и кабелям, электротехнической стали, а также к посадкам и квалитетам отдельных сборочных единиц и деталей.
Оболочка машин (станина и подшипниковые щиты) имеет механическое назначение (за исключением машин постоянного тока, выполняемых с монолитной стальной станиной, которая одновременно является и частью магнитопровода) оболочку машин выполняют главным образом из чугуна. В машинах меньшей мощности применяют также оболочку либо целиком из алюминиевых сплавов либо, для повышения механической прочности, — смешанную конструкцию: алюминиевую станину и чугунные подшипниковые щиты; в машинах большей мощности — стальную сварную конструкцию оболочки. Достоинства и недостатки каждого из этих исполнений рассмотрены в § 3-10 и 3-11.
|
|
При проектировании следует учитывать, что основными исполнениями по степени защиты являются у машин переменного тока IР23 и IР44, а у машин постоянного тока — IР22 и IР44. В меньших машинах, где разница в эффективности охлаждения закрытого и защищенного исполнений меньше, чем в больших, степень защиты IР44 постепенно вытесняет IР23 и IР22, как повышающая надежность машин в эксплуатации. В области асинхронных двигателей мощностью до 18,5 кВт включительно (при 2р = 4) в России вообще исключено исполнение IР2З и оставлено только исполнение IР44 со способом охлаждения IС0141. Аналогичная тенденция наблюдается и в других странах.
Разработку конструкции машин переменного тока (кроме асинхронных двигателей с фазным ротором) по данным электромагнитного расчета обычно начинают со статора. После определения вылета лобовых соединений обмотки статора вычерчивают продольный разрез машины. Длину станины выбирают с учетом выбранного способа закрепления сердечника статора в станине. Конструкция и длина подшипниковых щитов зависят от выбранной схемы вентиляции. Из построения продольного разреза определяются размеры вала, подлежащие проверке механическим расчетом.
|
|
Разработку конструкции машин постоянного тока целесообразно начинать с вращающейся части машины — якоря. После определения вылета лобовых частей и расположения коллектора в продольном разрезе устанавливают размеры вала, подлежащие проверке механическим расчетом. При аксиальной системе вентиляции должно быть дополнительно учтено размещение центробежного вентилятора. Затем разработке подвергают неподвижную часть машины — станину с полюсами и обмотками возбуждения.
Конструкцию асинхронных двигателей с фазным ротором разрабатывают, начиная с вращающейся части.
Вал
Вал электрической машины служит либо для передачи вращающего момента электродвигателя к приводимому механизму, либо для передачи вращающего момента генератору от соединенного с ним первичного двигателя. Вал несет на себе массу вращающейся части машины и нагружен моментом вращения и изгибающим моментом передачи. Кроме того, вал испытывает воздействие одностороннего магнитного притяжения, возникающего при неравномерном воздушном зазоре.
|
|
Основные требования, предъявляемые к валу: жесткость в средней части, несущей сердечник ротора или якоря, с тем чтобы при работе машины прогиб вала не достигал недопустимых значений; прочность во всех его поперечных сечениях, достаточная для того, чтобы выдерживать без остаточных деформаций все нагрузки, возникающие при эксплуатации машины; превышение первой критической частоты вращения над рабочей не менее чем на 30%.
Соответствие вала проектируемой машины указанным требованиям проверяется механическим расчетом после построения продольного разреза машины.
Размеры вала определяют при разработке конструкции машины, начиная с диаметра d1 и длины выступающего цилиндрического конца вала , которые принимают в зависимости от момента вращения при номинальном режиме работы машины согласно табл. 1-З (все размеры в мм). Номинальный момент вращения (Нм) двигателя
;(3-1 а)
генератора
.(3-1 б)
где Р2 — номинальная мощность, Вт; n — номинальная частота вращения, об/мин.
Для машин постоянного тока с h ≥ 355 мм, работающих главным образом в относительно тяжелых условиях с большими перегрузками, применяют валы с конусной формой выступающего конца вала и размерами в соответствии с ГОСТ 12081.
Диаметр вала под подшипник d2 и диаметр вала за подшипником d3 принимают в зависимости от выбранного наружного диаметра выступающего конца вала d1согласно данным табл. 3-1.
Таблица 3-1
d1 | d2 | d3 |
7 | 8 | 12 |
9 | 10 | 15 |
11 | 12 | 17 |
14 | 15 | 20 |
16 | 17 | 22 |
19 | 20 | 26 |
24 | 25 | 32 |
28 | 30 | 37 |
32 | 35 | 44 |
38 | 40 | 49 |
42 | 45 | 54 |
48 | 50 | 60 |
55 | 60 | 72 |
60 | 65 | 77 |
65 | 70 | 82 |
70 | 75 | 87 |
75 | 80 | 92 |
80 | 85 | 99 |
85 | 90 | 104 |
90 | 95 | 109 |
95 | 100 | 114 |
100 | 105 | 119 |
110 | 120 | 134 |
120 | 138 | 148 |
Валы диаметром в средней части до 100 мм изготовляют, преимущественно из прокатанных цилиндрических прутков стали 45, но могут использоваться и другие марки; такие валы проектируют с возможными минимальными переходами от одной ступени к другой, чтобы уменьшить трудоемкость механической обработки и количество отходов. Для изготовления валов с большим диаметром применяют заготовки также из стали 45, получаемых методомковки или прессовки.
На выступающем конце вала фрезеруют шпоночную канавку, ширину и глубину которой принимают по табл. 1-3. Шпоночные канавки фрезеруют также и на других участках вала — вместе расположения сердечника, вентилятора и коллектора (у машин постоянного тока). Для унификации на перечисленных участках вала целесообразно применять шпоночные канавки таких же размеров, как на выступающем конце вала, у асинхронных двигателей с короткозамкнутым ротором при h ≤ 250 мм сердечник ротора насаживают на вал с прессовой посадкой с нагревом без шпонки. У асинхронных двигателей с фазным ротором и у синхронныхмашин в валу просверливают центральное отверстие для размещения кабелей или шин, соединяющих обмотку с контактными кольцами.
§ 3-3. Механический расчет вала
Расчет вала на жесткость. Сила тяжести (Н) сердечника ротора с обмоткой и участком вала по длине сердечника асинхронного двигателя
;(3-2)
синхронной машины
. (3-3)У машин постоянного тока определяют силу тяжести сердечника якоря с обмоткой иучастком вала по длине сердечника с прибавлением силы тяжести коллектора, принимая ее приложенной к середине сердечника:
(3-4)
Здесь - длина сердечника ротора или якоря без радиальных вентиляционных каналов, мм;
и
— наружный диаметр и длина коллектора, мм.
Для расчета прогиба вала составляют эскиз вала размерами (рис. 3-1)
Рис. 3-1. Эскиз вала к механическому расчету.
Для этого должна быть разработана предварительно конструкция машины. Вал разбивают на три участка: а, b и с.
Под воздействием силы тяжести прогиб вала посередине сердечника (мм)
,(3-5)
где Па — модуль упругости стали; а, b и
— из рис. 3-1, мм.
Значения Sa и Sb определяют в соответствии с размерами d, x и у, указанными на рисунке и с расположением расчетных данных по форме, указанной в табл. 3-2.
Таблица 3-2
Участок b | |||||||||||||
![]() | ![]() |
|
мм³ |
мм3 | ![]() |
мм2 |
мм2 | ![]() | |||||
75 | 155·104 | 45 | 91· 10³ | 91· 10³ | 0,059 | 2,02·10³ | 2,02·10³ | 0,00130 | |||||
87 | 281·104 | 125 | 1953·103 | 1862·10³ | 0,663 | 15,62·10³ | 13,6·10³ | 0,00484 | |||||
95 | 397·104 | 165 | 4492·10³ | 2539·10³ | 0,639 | 27,22·10³ | 11,6·10³ | 0,00292 | |||||
90 | 322·104 | 330 | 35937·10³ | 31445·10³ | 9,766 | 108,9·10³ | 81,7·10³ | 0,02537 | |||||
S0 =11,128 | Sb=0,03443 | ||||||||||||
Участок а | |||||||||||||
|
|
|
|
|
| ||||||||
75 | 155·104 | 45 | 91·10³ | 91·10³ | 0,059 | ||||||||
87 | 281·104 | 125 | 1953·10³ | 1862·10³ | 0,663 | ||||||||
— | — | — | — | — | — | ||||||||
90 | 322·104 | 377 | 50653·10³ | 48700·10³ | 15,124 | ||||||||
Sа = 15,846
В этой таблице и
— диаметр и экваториальный момент инерции рассматриваемого участка вала,
и
— расстояния, соответствующие диаметру вала
.
Экваториальный момент инерции вала (мм4)
.(3-6)
При работе машины возникает поперечная сила, вызываемая передачей через упругую муфту или клиноременной передачей и приложенная к выступающему концу вала.
Эта сила от передачи (Н)
, (3-7)
где =0,3 — при передаче упругой муфтой (учитывая неоднородность плотности втулок) и
=1,8 - при передаче клиновыми ремнями (размеры упругих муфт принимают по приложению 37, а клиноременных шкивов — по приложению 38), r — радиус окружности расположения пальцев упругой муфты или окружности шкива, мм.
От поперечной силы передачи прогиб вала посередине сердечника (мм)
,(3-8)
где (рис. 3-1 и табл. 3-2).
Возникающий из-за неравномерности воздушного зазора, а также из-за прогиба вала под действием сил и Fn , - начальный расчетный эксцентриситет сердечника ротора или якоря (мм)
,(3-9)
где = 0,1 при
≥ 0,5 мм,
=0,15 при
<0,5 мм.
Эксцентриситет сердечника ротора или якоря вызывает неравенство магнитных потоков полюсов, а именно увеличение потоков в зоне меньших воздушных зазоров. При смещении сердечника на сила одностороннего магнитного притяжения (Н)
; (3-10)
при 2р=2 вместо 0,15 в (3-10) подставляют 0,1.
Дополнительный прогиб от силы Т0 (мм)
.(3-11)
Увеличение прогиба на вызовет усиление силы магнитного притяжения, а следовательно, и дальнейшее увеличение прогиба. Так будет продолжаться до тех пор, пока магнитное притяжение и жесткость вала не уравновесятся. Под действием сил магнитного притяжения установившийся прогиб вала (мм)
.(3-12)
Когда отдельные составляющие прогиба суммируются (в худшем случае), результирующий прогиб вала (мм)
. (3-13)
Величина должна составлять не более 10% от
у асинхронных двигателей и не более 12% у машин постоянного тока и синхронных машин; при превышении этого значения увеличивают диаметр вала в средней части с повторением расчета.
Определение критической частоты вращения. Первая критическая частота вращения машины может рассматриваться в качестве характеристики изгибной жесткости вала.
Прогиб (мм) от силы тяжести упругой полумуфты
, (3-14)
шкива
, (3-15)
где — сила тяжести соединительного устройства (упругой полумуфты или шкива); m — масса упругоймуфты или шкива (см. приложёния 37 и 38), кг.
С учетом влияния силы тяжести соединительного устройства первая критическая частота вращения (об/мин)
. (3-16)
Значения должно превышать максимальную рабочую частоту вращения не менее чем на 30%.
Расчет вала на прочность. Расчет ведется, исходя из теории максимальных касательных напряжений. Вал рассчитывают на участке с в наиболее нагруженном сечении 1—1 выступающего конца вала; в расчете прочности момент сопротивления определяют по диаметру выступающего конца вала, уменьшенному на высоту шпоночной канавки. На участке а напряжения будут ниже вследствие унификации диаметров вала под подшипниками. В рассматриваемом сечении вала на участие с изгибающий момент (Нм)
,(3-17)
где к = 2 — принимаемый коэффициент перегрузки.
При соединении машины упругой муфтой отрезки z1 и с отсчитывают от середины втулки муфты. В этом случае (см. приложение 37)
. (3-18)
Соответственно определяют и другие размеры на участке с. При соединении машины шкивом z1и с отсчитывают от середины длины выступающего конца вала.
Момент кручения (Н.м)
;(3-19)
момент сопротивления при изгибе (мм3)
.(3-20)
При совместном действии изгиба и кручения приведенное напряжение (Па)
=
.(3-21)
Значение
ни в одном сечении вала не должно превышать 0,7
, где
— предел текучести качественной стали на растяжение:
Марка стали | 30 | 35 | 40 | 45 | 50 |
![]() | 230·105 | 270·105 | 310·105 | 350·105 | 390·105 |
Пример расчета вала. Вал асинхронного двигателя (100 кВт, 1470 об/мин), соединенный с приводимым механизмом упругой муфтой: =288 мм;
= 330 мм;
=1 мм; муфта — тип МУВП 1—70 (см. приложение 37); m = 38,5 кг;
L= 288 мм; r = 95 мм. Размеры вала (см. рис. 3-1) мм: d1 =70; d2=75; d3=87; d4=95; d5 = 90; d6 = 87; d7 = 75; с = 120; =45;
= I25;
=165; b = 330; .a = 370;
=700; x1= 45; х2=125; t=7,5 (см. табл. 1-3); сталь 45.
Определение Sa , Sb и S0по табл. 3-2.
Параметр | Источник | Расчет |
![]() | (3-2) | 64·2882·330·10-6=1752 |
![]() | (3-5) | 1752(3702·11,128+3302·15,846)106/(3·2,06·1011·7002)=0,0188 |
![]() | (3-1) | 9,55·100·103/1470=650 |
![]() | (3-7) | (0,3·650/95)103=2053 |
![]() | (3-8) | 2053·120 ![]() |
![]() | (3-9) | 0,1·1+0,0188+0.0118=0.1306 |
![]() | (3-10) | 0,15·288·300·0,1306/1=1692 |
![]() | (3-11) | 0,0188·1692/1752=0,0182 |
![]() | (3-12) | 0,0182/(1-0,0182/0.1306)=0.0211 |
![]() | (3-13) | 0,0188+0,0118+0,0211=0.0517 (менее допустимого значения = 0.1·1=0,1 мм) |
![]() | (3-14) | 0.0118·9,81·38.5/(2·2053)=0,0011 |
![]() | (3-16) | 950 ![]() |
z1, мм | (3-18) | 288/2+58/2=173 |
![]() | (3-17) | 2(2053+9,81·38,5/2)173·10-3=776 |
![]() | (3-19) | 2·650=1300 |
![]() | (3-20) | 0,1(70-7,5)3=24414 |
![]() | (3-21) | ![]() ![]() |
§ 3-4. Сердечник и обмотка ротора
Штамповка листов ротора асинхронных двигателей производится из высечки листов статора. На листах ротора создают изолирующую оксидную пленку путем термической обработки от дельных штампованных листов у двигателей с h ≤ 250 мм или собранного сердечника у двигателей с h > 250мм.
Сердечник короткозамкнутого ротора двигателей с h ≥ 160 мм набирают из отштампованных листов на центрирующую оправку по специальному знаку, прессуют и без снятия давления закрепляют на оправке, после чего сердечник поступает на заливку алюминием. Сердечник ротора двигателей с h ≤ 132 мм сваривают на полуавтоматах внутренним швом, затем их заливают алюминием без применения специальной оправки. После заливки сердечники роторов двигателей с h ≤ 250 мм насаживают на вал без шпонки в нагретом состоянии (рис. 3-2), а у двигателей с h > 250мм — на вал со шпонкой при прессовой посадке (рис. 3-3).
Короткозамкнутые роторы асинхронных двигателей с h ≥ 400мм выполняют со сварной алюминиевой клеткой. С листов роторов снимают заусенцы, затем покрывают изолирующим лаком, после чего листы набирают непосредственно на вал. Собранный сердечник, размещенный между нажимными шайбами, прессуется и закрепляется с одной стороны упорным заплечиком вала, с другой — кольцевой шпонкой.
Сердечники фазных роторов выполняют таким же образом, как и у короткозамкнутых роторов, со сварной клеткой; при этом нажимные шайбы ротора имеют приливы, являющие обмоткодержателями, на которые опираются лобовые части обмотки (рис. 3-4).
Рис. 3-2. Общий вид асинхронного двигателя с высотой оси вращения h = 180 мм; степень защиты IP44; способ охлаждения IC0141; 22кВт, 220/380 В; 2р = 4; ротор короткозамкнутый:
1-вал; 2-крышка подшипниковая наружная; 3-крышка подшипниковая внутренняя; 4-Щит подшипниковый; 5-коробка выводов; 6-сердечник статора; 7-сердечник ротора; 8-обмотка статора; 9-обмотка ротора; 10- щит подшипниковый; 11-вентилятор; 12-кожух вентилятора; 13-болт заземления.
Рис. 3-3. Общий вид асинхронного двигателя с высотой оси вращения h=280 мм; степень защиты IР23; способ охлаждения IСОI; 110 кВт; 380/660 В; 2р = 4, ротор короткозамкнутый:
1 — вал; 2 — капсула подшипника; З — шайба, сбрасывающая отработанную смазку; 4 - крышка подшипниковая внутренняя; 5 — щит подшипниковый; 6 — обмотка статора; 7— сердечник статора; 8 — сердечник ротора; 9 — обмотка ротора;10 — кольцо бандажное;11 — щиток, направляющий воздух; 12 — щит подшипниковый; 13 —жалюзи; 14— крюк транспортный; 15 — кожух; 16 — коробка вывода; 17 —полустанина; 18 —болт заземления.
При наличии радиальных вентиляционных каналов в роторе их располагают против соответствующих каналов в сердёчнике статора. Крепят вентиляционные распорки ротора особо тщательно, чтобы исключить возможность их выпадения при вращении ротора. Изготовленный сёрдечник ротора с валом протачивают по наружному диаметру для обеспечения необходимой величины воздушного зазора между сердечниками статора и ротора.
У синхронных машин с h ≤ 315 мм сердечник ротора собирают на валу из штампованных листов, имеющих форму многополюсной звезды (см. рис. 3-8 и 11-6). Сердечник состоит из черёдующихся высоких и низких пакетов, создающих гребенчатую конструкцию, которая обеспечивает получение формы кривой поля, близкой к синусоидальной при равномерном зазоре под полюсами. При сборке ротора, после установки катушек, на низкие пакеты закрепляют роторные сегменты, имеющие форму полюсных наконечников. Сегменты скрепляют с сердечником ротора двумя продольными шпильками, продетыми через отверстия в сегментах и высоких пакетах. Сердечник ротора крепят на валу по всей длине шлицевым соединением, а с торцов — двумя кольцевыми шпонками.
У синхронных машин с h >315 мм, выполняемых с традиционной формой наконечников, при которой полюсные сердечники, склепанные из стальных листов толщиной 1—1,5 мм, крепят к многогранной или цилиндрической втулке, собранной также из отдельных стальных листов и расположенной на валу (см. рис. 3-9). Крепление осуществляется с помощью выступов Т-образной формы или в виде ласточкина хвоста. В наконечниках полюсных сердечников выштампованы круглые пазы для расположения в них стержней пусковой обмотки электродвигателя или успокоительной обмотки генератора.
Обмотка короткозамкнутого ротора асинхронного двигателя. Обмотка короткозамкнутого ротора асинхронных двигателей с h ≤ 355мм создается путем заливки пазов собранного сердечника алюминием А5. Для получения специальных характеристик, например у двигателей, с повышенным скольжением, пазы ротора могут заливаться алюминиевым сплавом АКМ12-4.
Рис.3-4. Общий вид асинхронного двигателя с высотой оси вращения h = 450 мм; степень защиты IP23; способ охлаждения IC0161; 630 кВт; 6000 В; 2р = 6; ротор фазный:
а - продольный разрез; б - поперечный разрез; 1 - вал; 2 - крышка подшипниковая наружная; 3 -крышка подшипниковая внутренняя; 4 - щит подшипниковый; 5 - обмотка статора; 6 - сердечник статора; 7-сердечник ротора; 8 - воздухоохладитель; 9 - обмотка ротора; 10 - щиток направляющий воздух; 11 - щит подшипниковый; 12 - узел контактных колец; 13 - вентилятор; 14 - ушко транспортное; 15 - коробка выводов.
При заливке пазов одновременно образуются короткозамыкающие кольца с вентиляционными лопатками и с расположенными между лопатками штырями, на которых крепят балансировочные грузы (см. рис. 3-3). Количество лопаток Nл принимают в следующих пределах:
h, мм | 50 - 100 | 112 - 250 | 280 - 355 |
Nл* | 6 -9 | 10 - 14 | 17 - 22 |
Толщина лопатки , длина
, высота
(все размеры в мм).
Роторы двигателей с h ≤ 250 мм обычно заливают в машинах для литья под давлением, а при h = 280 ÷ 355 мм — с помощью вибрационной установки. Сварную клетку короткозамкнутого ротора двигателей с h ≥ 400 мм изготовляют из алюминиевых шин.
* Меньшие значения Nл соответствуют меньшим значениям h.
Концы пазных стержней размещают в канавках, выфрезерованных в короткозамыкающих кольцах, а затем приваривают, причем стержни поочередно выступают с каждой стороны за короткозамыкающее кольцо, образуя вентиляционные лопатки. Стержни крепят в пазах чеканкой по всей длине сердечника через шлиц паза; при этом алюминий стержней затекает в предусмотренные для этого канавки.
Обмотка фазного ротора асинхронных двигателей. Фазный ротор двигателей с h ≤ 225мм выполняют с овальными полузакрытыми пазами и всыпной обмоткой из круглых проводов. Обмотка катушечная однослойная двухплоскостная; конструкция изоляции обмотки такая же, как у якорей машин постоянного тока (см. приложение 24).
Роторы двигателей с h > 225 мм (рис. 3-4) выполняют с прямоугольными полузакрытыми пазами и обмоткой из изолированных медных стержней прямоугольного поперечного сечения, которые вставляют в пазы с торца. Обмотка волновая двухслойная; для получения секции волновой обмотки одному концу стержня придают изгиб заранее по шаблону, а второй конец изгибают после вставки стержня в паз. Каждый стержень предварительно изолируют, после чего спрессовывают. Соединяют стержни в лобовых частях хомутами, в которые дополнительно впаивают вентиляционные лопатки. Конструкция изоляции стержневой обмотки приведена в приложении 22.
Марки пропиточных лаков и способы пропитки обмоток фазных роторов такие же, как для обмоток статоров (см. § 3-13). Лобовые части обмоток фазных роторов опираются на обмоткодержатели и крепятся бандажами из стеклянной нетканой ленты. Механический расчет бандажей выполняют по методике приведенной в § 3-7 для якорей машин постоянного тока.
Обмотка ротора синхронных машин. Обмотка ротора состоит из отдельных катушек, намотанных из прямоугольной меди — изолированной (в меньших машинах) или неизолированной, гнутой на ребро (в больших машинах); катушки соединены последовательно. Выводы обмотки ротора пропускают через полый конец вала и соединяют с контактными кольцами. Конструкция изоляции обмотки ротора приведена в приложении 23. Марки пропиточных лаков и способы пропитки обмоток роторов такие же, как для обмоток статоров (см. § 3-13).
Узел контактных колец
Контактные кольца применяют в асинхронных двигателях с фазным ротором и в синхронных машинах. Контактные кольца располагают на валу, обычно за подшипниковым щитом, и заключают их в коробку. При радиальной системе вентиляции такое расположение колец дает возможность унифицировать оба подшипниковых щита машины. Коробку контактных колец выполняют чугунной литой или стальной сварной, закрываемой съемным кожухом из листовой стали. В торцовой части кожухаимеются отверстия для входа вентилирующего воздуха (отверстия защищены жалюзи, выдавленными в кожухе), в нижней части кожуха — отверстия для выхода воздуха. В меньших асинхронных двигателях с фазным ротором (h = 200 ÷ 250 мм) коробку контактных колец выполняют из алюминиевого сплава (коробка имеет боковые жалюзи). Узел контактных колец охлаждается за счет вентилирующего эффекта колец.
Контактные кольца медные или латунные у машин мощностью до 100 кВт и стальные или чугунные в машинах большей мощности. Наружный диаметр контактных колец принимают меньше наружного диаметра подшипника качения для того, чтобы коробка контактных колец и подшипниковый щит машины могли быть при разборке сняты без предварительного съема контактных колец с вала.
Сердечник и обмотка якоря
С листов сердечника якоря после штамповки снимают заусенцы, затем покрывают изолирующим лаком. Листы набирают непосредственно на вал; при этом по торцам сердечника во избежание «распушения» располагают утолщенные листы, образуемые точечной сваркой несколько листов толщиной 0,5 мм. Собранный сердечник якоря размещают между стальными нажимными шайбами, прессуют и закрепляют с одной стороны заплечиком вала, с другой — упорным кольцом, насаженным на вал с прессовой посадкой с нагревом.
Нажимные шайбы могут выполняться в виде обмоткодержателей с дополнительной опорой для лобовых частей обмотки. Обмоткодержатели — литые чугунные, а в больших машинах — стальные сварные. В небольших машинах применяют также опоры для лобовых частей в виде пластмассовых втулок.
Мягкие катушки двухслойной всыпной обмотки якоря из круглых проводов изготовляют намоткой на специальных шаблонах и укладывают(«всыпают») через шлиц в полузакрытые пазы, выложенные корпусной изоляцией. Ширина шлица паза якоря должна обеспечивать достаточную технологичность укладки катушек. Для повышения механической прочности торцов корпусной изоляции ее края загибают на 180о.Между верхними и нижними сторонами катушек в пазах и в лобовых частях обмотки размещают изоляционные прокладки. Конструкция изоляции обмотки приведена в приложении 24.
Для закрепления всыпной обмотки от перемещения в радиальном направлении из-за действия центробежных сил применяют клинья из стеклотекстолита полукруглого поперечного сечения, а в лобовых частях — бандажи. Бандажи выполняют из нетканой стеклоленты, состоящей из параллельно уложенных стеклонитей, которые пропитаны полиэфирным связующим.
Катушки жесткой двухслойной обмотки якоря из прямоугольногопровода изготовляют на шаблонах, изолируют, опрессовывают и закладывают в открытые пазы, выложенные корпусной изоляцией. Между верхними и нижними катушками размещают в пазу изоляционные прокладки из стеклотекстолита, а в лобовых частях — полосы из лакостеклослюдопласта или гибкого миканита. Конструкция изоляции обмотки приведена в приложении 25.
Обмотку в пазах крепят бандажами из стеклоленты или стальной проволоки, располагаемых в кольцевых бандажных канавках сердечника якоря. Канавки образуются при сборке сердечника путем размещения на протяжении канавок листов якоря с уменьшенным диамётром. По длине якоря устраивают несколько канавок , с тем чтобы длина каждой канавки
не превышала 20 мм, а общая длина канавок
< 0,35
.На лобовые части обмотки также накладывают бандажи.
Для больших машин (h > 355 мм), работающих в тяжелых условиях, применяют обмотку якоря повышенной надежности с усилением витковой изоляции путем применения прямоугольных проводов со стеклопряжей марок ПСД или ПСДК и дополнительного изолирования промежуточных секций в катушках стеклянной лентой или полиимидной пленкой. Конструкция изоляции обмотки повышенной надежности при классах нагревостойкости F и Н приведена в приложении 26. Применение класса В для таких обмоток нецелесообразно. Крепятся обмотки в пазах клиньями из стеклотекстолита, у которых высота hk = 4 мм. На лобовые части обмотки якоря накладывают бандажи из стеклоленты.
Марки пропиточных лаков и способы пропитки якорей такие же, как для обмоток статоров (см. § 3-13).
Применяемая в специальных машинах (тяговых, крановых, металлургических и др.) изоляция, именуемая «Монолит», находит в настоящее время благодаря своим преимуществам все большее распространение в машинах общего назначения. Изоляции представляет собой сочетание стеклоткани и слюдинита с термореактивным компаундом. Компаунд вводится в обмотку и в изоляцию под вакуумом с последующим применением давления.
Машины с изоляцией «Монолит» обладают высокой теплопроводностью и усиленной надежностью в эксплуатации благодаря стойкости к тепловым ударам и температурным перегрузкам. Испытания машин со способом защиты IР22 и способом охлаждения IСО1, а также машин со степенями защиты IР22 или IР44 и способами охлаждения IС17 или IС37 показывают, что при применении изоляции «Монолит» превышение температуры обмотки якоря над температурой воздуха внутри машины значительно снижается (см. § 10-16). В машинах со степенью защиты IР44 и способами охлаждения IС0141 или IС0041 влияние изоляции «Монолит» на превышение температуры обмотки незначительно. Перевод обмоток на изоляцию «Монолит» требует замены материалов, в основе которых содержатся синтетические пленки, не стеклослюдинитовые и слюдопластовые материалы. При использовании изоляции «Монолит» сцепление катушек обмотки якоря стенками пазов настолько прочное, что якоря машин с h < 315 мм могут работать в бесклиновом исполнении.
§ 3-7. Расчет бандажей и пазных клиньев
Бандажи и пазные клинья должны быть подвергнуты механическому расчету.
Расчет стеклобандажей. Общее число витков бандажей
, (3-22),
где Gм2 = 9,81 mM2- сила тяжести обмотки якоря, Н; nР-разгонная частота вращения, равная 1,2 наибольшей частоты вращения машины; — допустимое напряжение растяжения, принимаемое для стеклоленты равным 150 ·106 Па при классе нагревостойкости изоляции В и 130 ·106 Па — при классах F и Н; Sл - площадь поперечного сечения ленты, мм2.
При вычислении для активной части якоря в (3-22) подставляют силу тяжести активной части обмотки якоря
=
, а для каждой из лобовых частей — силу тяжести одной из них —
=
.
Расчет бандажей из стальной немагнитной проволоки. Расчет проводится также по (3-22) с заменой Sл на площадь поперечно го сечения Sпробщего числа витков проволоки (мм2) и подстановкой допустимого напряжения растяжения = 450·106 Па (для стальной проволоки).
Расчет пазных клиньев.Напряжение изгиба в клине (Па)
.(3-23)
Значение σне должно превышать для стеклотекстолита 25 Х 106 Па. Напряжение на срез в клине (Па)
. (3-24)
Значение не должно превышать 15·106 Па.
Узел коллектора
Коллектор собирают из медных пластин трапецеидального поперечного сечения, между пластинами располагают изоляционные прокладки из миканита или слюдопласта.
У машин с h < 200 ÷ 250 мм обычно коллекторные пластины крепят пластмассой К6 или АГ-4с (рис. 3-5). При такой конструкции крепления коллекторные и изоляционные пластины штампуют по размеру, одновременно создавая в них ласточкины хвосты или кольцевые канавки для закрепления пластин в монолитный блок. Для повышения механической прочности коллектора в ласточкиных хвостах или кольцевых канавках располагают стальные армирующие кольца.
Рис. 3-5 Общий вид двигателя постоянного тока с высотой оси вращения h =160 мм; степень защиты IР44; способ охлаждения IС0141; 7,5 кВт; 220В; 1500 об/мин:
а – продольный разрез; б – поперечный разрез; 1 – вал; 2 – крышка подшипниковая наружная; 3 – кольцо для размещения балансировочных грузов; 4 – щит подшипниковый; 5 – коллектор; 6 – траверса; 7 – обмоткодержатель; 8 – обмотка якоря; 9 – сердечник якоря; 10 – обмотка добавочных полюсов; 11 – сердечник добавочного полюса; 12 – сердечник главного полюса; 13 – станина; 14 – параллельная обмотка главных полюсов; 15 – бандаж лобовой части обмотки якоря; 16 – вентилятор внутренний; 17 – крышка подшипниковая внутренняя; 18 – вентилятор наружный; 19 – кожух наружного вентилятора; 20 – щит подшипниковый; 21 – коробка выводов; 22- ушко транспортное
Рис 3-6. Общий вид двигателя постоянного тока с высотой оси вращения h = 280 мм; степень защиты IР22; способ охлаждения IС01; 132; 220 В, 1500 об/мин:
1 — вал; 2 — траверса; З — коллектор; 4 — щит подшипниковый; 5 — станина;6 —обмоткодержатель; 7 — обмотка добавочных полюсов; 8 — сердечник якоря; 9 —сердечник добавочного полюса;10 — канал аксиальный вентиляционный;11 -сердечник главного полюса; 12 — бандаж лобовой частиобмотки якоря; 13 — обмотка якоря; 14 — вентилятор; 15 — щит подшипниковый; 15 — крышка подшипниковая внутренняя; 17 — крышка подшипниковая наружная; 18 —жалюзи: 19 — ушко транспортное; 20 — коробка выводов.
Кроме того, для обеспечения прессовой посадки при повторном насаживании коллектора на вал предусматривают запрессовку в центральную часть пластмассового корпуса стальной втулки. В коллекторных пластинах фрезеруют канавки, которые лудят оловянным припоем. В этих канавках располагают луженые концы секций обмотки якоря из круглых проводов и соединяют эти концы с коллекторными пластинами пайкой. Пайка производится мягким (при классе нагревостойкости изоляции В) или твердым (при классах F и Н) припоем. Коллекторы с креплением пластин пластмассой имеют сниженную трудоемкость и стоимость, так как при их изготовлении исключается механическая обработка крепежных деталей. Недостатком таких коллекторов является то, что условия охлаждения пластмассового корпуса затруднены (низкая теплопроводность пластмассы, большая ее толщина, отсутствие аксиальных вентиляционных каналов).
У машин с h > 200 ÷ 280мм (рис. 3-6) коллекторные пластины крепят с помощью чугунной или стальной втулки, стальных нажимных конусных фланцев и кольцевой гайки, заменяемой в длинных коллекторах шпильками. В коллекторах с металлическим креплением дня улучшения охлаждения устраивают аксиальные вентиляционные каналы. Коллекторные пластины изолируют от корпуса втулкой и от нажимных фланцев конусными манжетами, изготовленными из миканита или слюдинита. В пластинах коллектора фрезеруют канавки, в которых размещают и припаивают медные петушки (флажки). Концы секций обмотки якоря соединяют с петушками также пайкой. Паяют мягким и твердым припоем, в зависимости от класса нагревостойкости изоляции, как указано выше для коллекторов с креплением пластин пластмассой. Конструкция переднего (со стороны, противоположной сердечнику якоря) нажимного фланца обычно предусматривает возможность размещения балансировочных грузов.
Предварительное значение высоты (мм) коллекторных пластин, с учетом 20% припуска на проточку коллекторов при эксплуатации
.(3-25)
Щеткодержатели прикрепляют к призматическим бракетам, расположенным на траверсе; у больших машин бракеты крепят неподвижно к подшипниковому щиту. Бракеты выполняют из стеклотекстолита или из полосовой стали, изолируемой в месте крепления к траверсе. Траверсы должны обеспечивать возможность поворота при регулировании машины на испытательной станции, а затем фиксирования ее стопорным винтом в положении, установленном при испытании. Щеткодержатели выполняют литыми латунными или штампованными из листовой латуни. Конструкция щеткодержателей должна обеспечивать постоянство нажатия пружины по мере износа щетки.
Вентилятор
Центробежный вентилятор, располагаемый при аксиальной системе вентиляции на валу внутри машины со степенью защиты IР22 или IР2З и способом охлаждения IС01, выполняют литым из алюминиевых сплавов у машин меньшей мощности и стальным сварным или клепаным — у машин большей мощности. Алюминиевый вентилятор обычно имеет залитую стальную втулку, дающую возможность сохранить необходимую посадку при повторной насадке на вал (рис. 3-6). У машин меньшей мощности в последнее время применяют вентиляторы из пластмассы.
Для машин со степенью защиты IР44 и способом охлаждения IC0141 для наружного обдува корпуса используют радиальный вентилятор (с прямыми лопатками), расположенный на конце валасо стороны, противоположной приводу. Вентиляторы также выполняютлитыми из алюминиевых сплавов у меньших машин, сварными или клепаными из листовой стали -у больших. Наружный диаметр вентилятора Dвен2 ≈ 0,85 Dкорп, ширина (длина) лопатки , число лопаток при n < 1500 об/мин
при n >1500 об/мин
.
У асинхронных двигателей и машин постоянного тока со степенью защиты IР44 и способом охлаждения IС0141 для улучшения теплообмена на валу внутри машины располагают дополнительно вентилятор-мешалку (см. рис. 3 - 5). Наружный диаметр мешалки обычно такой же, как у вентилятора для обдува, а .
Вентилятор закрывают штампованным или сварным кожухом, изготовленным из стали толщиной 1 — 2 мм. На торце кожуха выполняют отверстия любой формы для входа воздуха; при этом степень защиты кожуха должна удовлетворять ГОСТ 17494.
Станина
Машины переменного тока. Станины машин переменного тока в основном изготовляют чугунными литыми; при этом обеспечивается высокая надежность машин благодаря достаточной механической прочности и коррозионной стойкости чугуна, а также
стабильности размеров при сборочных операциях. В малых асинхронных двигателях с высотой оси вращения h < 71 мм наряду с чугунными применяют также станины из алюминиевых сплавов, образуемые обливкой сердечника статора в машинах для литья под давлением. Такая конструкция весьма технологична, сокращает трудоемкость изготовления статора, однако приh > 71 мм значительно сказываются деформация внутреннего отверстия сердечника статора при обливке его алюминиевыми сплавами и снижение механической прочности.
В машинах с h > 280мм кроме чугунных используют также сварные станины из стального проката. Один из видов таких станин — коробчатая станина асинхронных двигателей с h = 280 ÷ 355 мм — представляет собой сварную трубу со стойками, образующими опорные лапы и полукруговые ребра для посадки сердечника и подшипниковых щитов. В машинах с h <280 мм сварные станины применяют реже из-за многообразия отдельных элементов деталей, предназначенных для сварки (ребер, ушек, бобышек и др.), затрудняющего использование автоматизированных и механизированных производственных процессов на участке сварки.
Станины машин со степенью защиты IР23 (см. рис. 3-3) выполняются с внутренними продольными ребрами, обрабатываемыми под посадку сердечника статора. Станины при радиальной системе вентиляции имеют в боковых частях вентиляционные отверстия, предназначенные для выхода охлаждающего воздуха. Для обеспечения степени защиты IР23 отверстия закрывают жалюзи, которые могут изготовляться методом штамповки из листовой стали или литыми из алюминиевых сплавов. При аксиальной системе вентиляции отверстия в станине отсутствуют.
Станины машин со степенью защиты IР44 (см. рис. 3-2) обычно имеют продольные ребра на наружной поверхности. Высота ребра ,число ребер
. В машинах с h > 355 ммдля увеличения поверхности охлаждения в стальной станине применяют вваренные по всей окружности трубки распределенного воздухоохладителя.
Станины машины со способом монтажа IM1001 имеют опорные лапы, отливаемые заодно с чугунной станиной или приваренные в стальной станине. В станинах асинхронных двигателёй, образуемых из алюминиевых сплавов, лапы отливают отдельно, а затем крепят к статору.
Для размещения коробки выводов в станине предусматривают прилитые или приваренные фланцевые основания с окна для выводных проводов обмотки. Удобнымв эксплуатации является расположение коробки выводов сверху станины, так как при повороте коробки подводимый кабель может присоединяться с разных сторон машины.
Для обеспечения требований по технике безопасности на станине размещают наружные зажимы для заземления корпуса машины. Зажимы снабжают устройством от самоотвинчивания и крепят около опорных лап и в коробке выводов. При выполнении машин без лап один зажим располагают на фланцевом щите.
Для обеспечения посадки и центрирования подшипниковых щитов на торцах станины предусматривают кольцевые цилиндрические заточки (внутренние или наружные), а для крепления щитов — приливы или ушки с нарезанными отверстиями для болтов.
Станины протачивают по внутреннему диаметру под посадку отдельно изготовленных сердечников. Если сердечники набирают из отдельных листов прямо в станину, то при проточке в станине выбирают круговые канавки для крепления спрессованного сердечника кольцевыми или поперечными шпонками.
На станине в верхней части предусмотрены рым-болты (см. приложение 39) или транспортные ушки, предназначенные для подъема машины. Машины массой менее 30 кг не имеют специальных устройств для подъема. К станине на видном месте крепят табличку из некоррозийных материалов с техническими данными машины.
Машины постоянного тока. Исполняются с монолитной или шихтованной станиной. Монолитная станина имеет не только механическое назначение, но и одновременно является частью магнитопровода; поэтому ее изготовляют из стали с достаточно высокой магнитной проницаемостью. У машин меньшей мощности с h = 80 ÷ 200мм для изготовления монолитной станины обычно применяют отрезки стальных цельнотянутых труб, к которым приваривают опорные лапы. Такой способ изготовления станины снижает ее трудоемкость и стоимость. Для больших машин с h =225 ÷ 315мм цилиндрическую часть станины изготовляют из загнутого толстолистового проката, причем для обеспечения магнитной симметрии продольный сварной шов цилиндра располагают по оси главных полюсов. К цилиндрической части приваривают опорные лапы.
В станинах предусматривают кольцевые центрирующие заточки, рым-болты или транспортные ушки и наружные зажимы для заземления корпуса машины, крепление таблички с техническими данными машины (такое же, как в машинах переменного тока).
Коробку выводов у машин сh = 80 ÷ 200 мм располагают сверху станины, а у машин сh > 200 мм — обычно сбоку.
Для повышения жёсткости оболочки машин целесообразно укорачивать вылеты подшипниковых щитов за счет удлинения станины, стремясь к дисковой форме щитов. При таком удлинении части станин значительно выступающие за пределы длины сердечника якоря, могут выполняться с уменьшенной толщиной, особенно в тех местах, где должны располагаться люки для обслуживания коллектора и щеточного узла.
Шихтованные сердечники станин у машин с h < 315 мм выполняют набором круглых штампованных колец или сегментов из электротехнической стали. Сердечники скрепляют по наружной поверхности утопленными скобами, и размещают в станине (корпусе) в основном такой же конструкции, как и в машинах, переменного тока.Сердечники могут также изготовляться из отштампованных листов, образующих цельный блок станины с сердечникомглавных и добавочных полюсов; наконечники полюсов при этом изготовляют и скрепляют заклепками отдельно, а затем привинчивают к сердечникам. У машин с h > 355 мм шихтованные сердечники выполняются восьмигранной формы без обшивки; с приваренными к ним с двух сторон опорными частями из стального листового проката (рис. 3 - 7). При такой форме сердечников главные и добавочные полюсы размещаются более компактно, благодаря чему уменьшаются габариты и высота оси вращения машины. К станине приварены сегменты с нарезанными отверстиями для крепления подшипниковых щитов болтами. Для подъема и транспортировки машин в станине предусмотрены транспортные ушки.
Рис. 3-7. Общий вид двигателя постоянного тока с высотой оси вращения h = 450 мм; степень за щиты IР22; способ охлаждения IС01; 500 кВт; 440 В, 500 об/мин:
а — продольный разрез; б — поперечный разрез; 1 — крышка подшипниковая наружная; 2 — вал; 3 — крышка подшипниковая внутренняя; 4 - -щит подшипниковый; 5 – сердечникстанины; 6 — сердечник якоря; 7 — сердечник главного полюса;8 - обмотка возбуждения главных полюсов; 9 — обмотка якоря; 10 — уравнительные соединения; ‚11 — бракет щеткодержателей; 12 — люк коллекторный; 13 — обмотка добавочных полюсов; 14 – сердечникдобавочного полюса.
Подшипниковые щиты и подшипники
Подшипниковые щиты изготовляют либо чугунными литыми, либо сварными из стального проката. Для малых машин применяют щиты, изготовляет литьем под давлениём из алюминиевых сплавов. Для обеспечения минимальной деформации при закреплении щитов в приспособлениях металлообрабатывающих станков, а также уменьшения перекоса подшипников при сборке машин аксиальные размеры проектируемых щитов целесообразно сокращать, стремясь приблизить их форму к диску.
В защищенных машинах с исполнением по защите IР23 подшипниковые щиты при радиальной системе вентиляции одинаковые с обеих сторон машины; при аксиальной системе вентиляции щиты обычно не унифицируют из-за наличия с одной стороны машины внутреннего вентилятора (рис. 3-8). При радиальной вентиляции в торцовой части подшипниковых щитов располагают отверстия для входа охлаждающего воздуха; при аксиальной — отверстия для входа и выхода воздуха устраивают в нижней части щитов. Вентиляционные отверстия закрывают жалюзи.
При радиальной: вентиляции для повышения ее эффективности на внутренней части подшипниковых щитов крепят направляющие воздух щитки, выполняемые из листовой стали в виде воронок. Щитки располагают на расстоянии 5—7 мм от торцов лопаток ротора в аксиальном направлении.
Подшипниковые щиты закрытых машин с исполнением по защите IР44 и со способами охлаждения IС0141 и IС0041 — глухие. При выполнении таких щитов из алюминиевых сплавов у них предусматривают оребренные торцы, увеличивающие поверхность охлаждения машины. Щиты имеют цилиндрическую круговую заточку (замок) для посадки на заточку станины при сборке машины, для крепления к станине в щитах имеются ушки с отверстиями для болтов.
В центральной части щитов предусматривается втулка со сквозной проточкой для посадки подшипников качения, которые практически полностью вытеснили в машинах мощностью до 1000 кВт подшипники скольжения. Основными преимуществами подшипников качения являются упрощение обслуживания в эксплуатации, компактность и уменьшенные размеры подшипникового узла, малые потери на трение, незначительный износ, обеспечивающий постоянство воздушного зазора.
Рис. 3-8. Общий вид синхронного генератора с высотой оси вращения h =250 мм; степень защиты IР23; способ охлаждения IС01; 30 кВт; 230 В, 1500 об/мин:
а— продольный разрез; б — поперечный разрез; 1 — вал;2 — крышка подшипниковая наружная; 3— щит подшипниковый передний; 4 — вентилятор; 5 — корпус статора; 6— блок регулирования напряжения: 7 — сердечник статора; 8 — обмотка статора; 9 — щит подшипниковый задний; 10 — обмотка возбуждения полюсов; 11 — колпак 12— крышка подшипниковая внутренняя; 13— узел контактных колец; 14 — жалюзи; 15 — рым-болт
Рис. 3-9. Общий вид синхронного двигателя с высотой оси вращения h = 450мм; степень защиты IP23; способ охлаждения IС01; 250 кВт, 380 В, 500 об/мин:
1 – вал; 2 – крышка подшипниковая наружная; 3 – крышка подшипниковая внутренняя; 4 – щит подшипниковый4 5 – обмотка статора;6 – корпус статора; 7 – сердечник статора; 8 – сердечник полюса; 9 – втулка ротора; 10 –обмотка возбуждения полюсов; 11 – лопатка вентиляционная; 12 - узел контактных колец ротора; 13 – колпак; 14 – ушко транспортное; 15 – коробка выводов; 16 – пусковая обмотка.
Наружные кольца подшипников крепят по торцам подшипниковыми крышками, фиксирующими расположение подшипников в аксиальном направлении. Внутреннее кольцо подшипника насаживается на вал с плотной посадкой, а наружное входит во втулку подшипникового щита подвижно, так что при разборке машины подшипники остаются на валу. Этим самым облегчается как сборка, так и разборка машины.
В малых машинах с h <160 ÷ 200 мм оба подшипника шариковые радиальные однорядные по ГОСТ 8338; при этом с одной стороны машины между подшипниковой крышкой и подшипником оставляют зазор, который обеспечивает возможность аксиального перемещения вала, компенсирующего неточности осевых размеров при сборке машины. Для компенсации указанных отклонений могут также применяться с обеих сторон машины, пружинящие стальные гофрированные шайбы.
В больших машинах со стороны выступающего конца вала располагают роликовый подшипник радиальный с короткими цилиндрически роликами по ГОСТ 8328; при этом отпадает надобность в зазоре или в пружинящих шайбах, так как роликовый подшипник обеспечивает возможность аксиального перемещения вала (рис. 3-9).
Радиальные подшипники могут воспринимать как радиальную, также и осевую нагрузку, не превышающую 70% неиспользованной радиальной нагрузки. При соблюдении этого условия машины с шарикоподшипниками могут работать как с горизонтальным, так и вертикальным расположением вала.
В машинах, предназначенных для тяжелых режимов работы,например в используемых во вспомогательных устройствах металлургической промышленности двигателях постоянного тока с h > 355 мм, применяют сдвоенные радиально-упорные шариковыеподшипники по ГОСТ 832, которые воспринимают на себя нагрузку от силы тяжести якоря и осевую составляющую нагрузки от передачи момента.
Для подшипников качения используют консистентную мазеобразную смазку, которой заполняют около 2/3 смазочной камеры; заполнение смазкой всего объема камеры ведет к повышению нагрева подшипников. Для консистентной смазки достаточны несложные уплотнения в виде прямоугольных кольцевых канавок, протачиваемых в подшипниковых крышках; канавки при сборке машины также заполняют консистентной смазкой.
В подшипниковых щитах может быть предусмотрено устройство для пополнения и частичной замены консистентной смазки. При этом свежая смазка подается специальным приспособлением под давлением в пространство за внутренней подшипниковой крышкой, вытесняя отработанную смазку через наружную крышку подшипникового узла.
Смена и пополнение смазки не требуются, когда в машинах применяют шариковые радиальные однорядные подшипники закрытого типа с двусторонним уплотнением, не выходящим за габариты подшипников, и с заложенной на весь срок службы консистентной смазки по ГОСТ 8882. При установке таких подшипников отверстие под их посадку во втулке подшипникового щита делают не сквозным, а глухим, т. е. совмещают подшипниковую крышку со щитом.
У машин, крепление которых осуществляется фланцем (с лапами и без лап), подшипниковый щит отливается совместно с фланцем. Размеры фланцев должны соответствовать ГОСТ 18709 и 20839.
Расчет подшипников
Расчет подшипников качения. При расчете подшипников качения определяют их типоразмеры,которые обеспечивают необходимый срок службы при заданных нагрузке и частоте вращения. Условные обозначения и размеры подшипников, а также другие параметры их приведены в приложении 36.
Наибольшая радиальная нагрузка (Н) на подшипник А
(3-26)
на подшипник В
(3-27)
Динамическая приведенная нагрузка (Н) для шарикоподшипника однорядного радиального
при А/R < е;(3-28)
при А/R > е (3-29)
роликоподшипника радиального с короткими цилиндрическими роликами – по (3-28);
шарикоподшипника радиально-упорного сдвоенного
при А/R < 0,68 (3-30)
при А/R > 0,68(3-31)
Здесь — коэффициент, учитывающий характер нагрузки машины; при режиме работы с умеренными толчками и кратковременной перегрузкой до 150% от номинальной нагрузки —
=1,5; А — аксиальная нагрузка, Н; Y — коэффициент приведения аксиальной нагрузки к радиальной.
Значения е и Y однорядных радиальных подшипников в зависимости от А/Со (Со — статическая грузоподъемность (Н), предварительно принятого типа подшипника (из приложения 36)) определяют по следующим данным:
A/C | 0,014 | 0,028 | 0,056 | 0,084 | 0,11 | 0,17 | 0,28 | 0,42 | 0,56 |
e | 0,19 | 0,22 | 0,26 | 0,28 | 0,30 | 0,34 | 0,38 | 0,42 | 0,44 |
Y | 2,30 | 1,99 | 1,71 | 1,55 | 1,45 | 1,31 | 1,15 | 1,04 | 1,00 |
Для промежуточных значений А/С0 применяют линейную интерполяцию. При А/С0 < 0,19 приведенная нагрузка Q = R. При отсутствииаксиальной нагрузки и горизонтальном расположении вала осевое магнитное притяжение в расчете не учитывается, а при вертикальном расположении вала
(3-32)
Необходимаядинамическая грузоподъемность (Н) шарикоподшипника
(3-33)
роликоподшипника
(3-34)
где L — расчетный срок службы подшипника, ч (о6ычно принимают 12000 ч); n — наибольшая рабочая частота вращения машины, об/мин.
Из приложения 36 выбирают подшипник соответствующей серии, у которого внутренний диаметр равен диаметру шейки вала, а динамическая грузоподъемность — не менее значения, вычисленного по (3-33) или(3-34).
Пример расчета подшипников качения. Подшипники рассчитывают по данным, указанным в примере расчета вала (см.§ 3-З). При этом принимаем нагрузку с умеренными толчками ( =1,5);подшипник со стороны А — шариковый; со стороны В — роликовый; аксиальная нагрузка отсутствует; расчетный срок службы подшипников 12000 ч; наибольшая частота вращения 1500 об/мин
Параметр | Источник | Расчет параметров |
RA, Н | (3-26) | ![]() |
QA, Н | (3-28) | 1,5 · 1975 = 2962 |
С, Н | (3-33) | ![]() |
RВ, Н | (3-27) | ![]() |
QВ, Н | (3-28) | 1,5 · 4220 = 6330 |
C, Н | (3-34) | ![]() |
Из приложения 36 для стороны А выбираемшарикоподшипник № 215 легкой серии созначением С = 51000 (с запасом надежности), для стороны В — роликоподшипник №2215 легкой узкой серии со значением С = 76500 (с запасом надежности).
§ 3-13. Сердечник и обмотка статора
Сердечник статора. Сердечник статора машин с h < 250мм набирают на центрирующую оправку вне станины из отштампованных листов стали, спрессовывают, потом без снятия давления проверяют длины в канавках,расположенных на наружной поверхности сердечника. Для сердечника статора применяют крепление стальными скобами, расположенными в канавках по наружной поверхности сердечника. При таких способах сборки выдерживаются необходимые внутрённий диаметр и форма сердечника без растачивания, снижаются потери в стали, уменьшается трудоемкость укладывания обмотки, выполнения соединений и пропитки.
При коробчатой станине сердечники статоров двигателей также изготовляют вне станины с обмоткой и укладывают при сборке двигателей в соответствующие заточки на внутренних ребрах полустанины. К собранному сердечнику приваривают по бокам стальные пластины, которыми сердечник опирается на края станины и крепится к ней болтами.
У машин с h> 250ммсердечник собирают набором листов непосредственно в станину; после опрессовки сердечник закрепляют в станине кольцевыми или поперечными шпонками.При таком способе сборки сердечника возникает необходимость расточки его по внутреннему диаметру.
Сердечники статоров двигателейс h < 250мм протачивают по наружному диаметру для улучшения теплового контакта со станиной. Обмотанный и пропитанный сердечник впрессовывают в станину, если станина не образуется путем обливки сердечника алюминиевыми сплавами.
У сердечников длиной более 300—350 мм радиальные вентиляционные каналы образуют с помощью двутавровых распорок, расположенныхрадиально на каждом зубце, с обеспечением их надежного закрепления приваркой к листам статора.
Обмотка статора. Однослойная обмотка статора распространена только у асинхронных двигателей относительно небольшой мощности с h < 160 мм, двухслойная обмотка статора — в больших асинхронных двигателях, а также в синхронных машинах. Для низковольтных машин (U < 660 В) с h < 280мм обычно применяют трапецеидальные полузакрытые пазы со всыпной обмоткой,в низковольтных машинах с большими значениями h— прямоугольные полуоткрытые,в высоковольтных — прямоугольные открытые пазы с жесткими формованными катушками.
У асинхронных двигателей с h = 50 ÷ 160 мм,выпускаемых в больших количествах,для всыпной обмотки статора используют автоматические станки, работа которыхболее эффективна при заполнении двигателей с однослойной концентрической обмоткой. При этом катушечные группы наматывают обычно раздельно, а затем статорообмоточный станок выполняет операцию втягивания катушек в пазы статора, заклинивает обмотку в пазах и формует лобовые части обмотки. Концентрические катушки изготовляют из круглых проводов соответствующего класса нагревостойкости изоляции, причем ширина шлица полузакрытого паза должна обеспечивать достаточную технологичность укладки обмотки.
Пазовые коробочки, нарезанные из однослойного рулонного материала, также формуют и укладывают в пазы станками автоматами. Вылет коробочек с каждой стороны сердечника составляет 4—7 мм, причем для повышения механической прочности торцов пазовых коробочек их края загибают на 1800.
Клинья выполняют из листового изоляционного материала, придавая им изгиб по форме верхней части паза. Из этого же материала изготовляют прокладки, укладываемые в лобовые части обмотки между головками катушек. Пайки соединений катушечных групп, образующих фазы обмотки, заключают в изоляционные трубки. Лобовые части обмотки с обеих сторон двигателя бандажируют на специальных станках стеклошнуром. Обмотанные статоры пропитывают.
Двухслойную всыпную обмотку статора из круглых проводов у машин с h > 180 мм изготовляют вручную или с механизированной укладкой катушек. Принципиальная конструкция изоляции обмотки этих машин такая же, как у асинхронных двигателей с h = 50 ÷ 160 мм, за исключением того, что между верхними и нижними слоями обмотки размещают коробчатые изоляционные прокладки. Вылеты коробочек с каждой стороны сердечника составляют 7—10 мм. Конструкция изоляции одно- и двухслойной всыпной обмотки статора приведена в приложении 27.
Двухслойную обмотку статора машин с h > 250 ÷ 280ммизготовляют из формованных полукатушек, укладываемых в прямоугольные полуоткрытые пазы. Провод обмотки — прямоугольный. Предварительно намотанной на шаблоне заготовке – «лодочке», состоящей из двух полукатушек, скрепленной обволакивающим компаундом, придают необходимую форму на растягивающем устройстве; затем полукатушки опрессовывают в пазовых частях и дополнительно скрепляют лакированной фенилоновой бумагой. Лобовые части полукатушек скрепляют в двух - трех местах бандажами из стеклоленты, а у крайних полукатушек фаз обмотки лобовые части дополнительно изолируют стеклолентой. Полукатушки укладывают поочередно через шлиц в полуоткрытые пазы.
Для обеспечения механической прочности обмотки при воздействии на нее значительных усилий, возникающих при прямом включении двигателя в сеть, а у генераторов при к. з., лобовые части обмотки крепят стеклошнуром к бандажным кольцам.Между лобовыми частями катушек располагают распорки из стеклотекстолита с последующим перевязыванием стеклошнуром в шахматном порядке. Торцы пазовых коробочек выступают из сердечника статора на 15—20 мм. Конструкция изоляции машин с полуоткрытыми пазами статора приведена в приложении 28.
У тихоходных двигателей с h = 280и 315 мм при 2р = 10 и 12 обычно применяют для повышения энергетических показателей трапецеидальные полузакрытые пазы с двухслойной всыпной обмоткой, хотя при этом надежность обмотки несколько снижается в сравнении с обмоткой из жестких формованных катушек в полуоткрытых пазах. Конструкция изоляции обмотки статора таких двигателей приведена в приложении 29.
Для пропитки обмоток статора рекомендуются следующие лаки и способы пропитки:
Класс нагревостойкости изоляции | В | F, H |
Марка лака и способ пропитки | КП-34, КП-103, БСП (без растворителей, струйный метод) | КО-964Н (с растворителем, под вакуумом и давлением) |
При использовании этих пропиточных лаков отпадает необходимость в применении покровных эмалей на лобовых частях обмоток.
Обмотку статора двигателей с h > 400ммна напряжение 6000 В выполняют двухслойной из жестких формованных катушек. Провод обмотки прямоугольный; намотанные из этого провода «лодочки» растягивают и опрессовывают, затем катушки изолируют и укладывают в прямоугольные открытые пазы. Крепление лобовых частей такое же, как у низковольтных двигателей с жесткими катушками. Для повышения надежности и улучшения теплопроводности изоляции обмотки статора в высоковольтных машинах целесообразно применение изоляции «Монолит» (см.§ 3-6). Конструкция изоляции обмотки статора двигателей на напряжение 6000 В приведена в приложении 30.
Главные и добавочные полюса
Сердечники главных и добавочных полюсов собирают из неизолированных штампованных листов электротехнической стали толщиной 0,5 или 1,0 мм. Крайние листы полюсов выполняют утолщенными путем точечной сварки нескольких листов обычной толщины; это необходимо для уменьшения распушения полюсов. При штамповке в листах полюсов предусматривают отверстия для заклепок. Собранный из отдельных листов полюс прессуют и скрепляют стальными заклепками (не менее четырех). Общая площадь поперечного сечения заклепок составляет 2 — 3% площади листа полюса.
Полюса к монолитной станине крепят болтами, ввинчиваемыми в машинах с h < 315 ммв отверстия, нарезанные непосредственно в сердечниках полюсов, а при h > 315 мм — в стальных стержнях, вставляемых в выштампованные для них отверстия в полюсах. В машинах с компенсационной обмоткой в наконечниках главных полюсов предусматривают пазы для ее размещения.
Наконечники добавочных полюсов машин с h < 315 мм шире сердечников; образуемые при этом боковые выступы служат в качестве опоры для катушек полюсов. В машинах с h > 315 мм необходимость в таких выступах отпадает, так как катушки крепят к сердечникам полюсов хомутами; сердечники добавочных полюсов этих машин выполняют из листов Т-образной формы для уменьшения магнитной индукции в наиболее насыщенной части полюсов и для повышения механической прочности их крепления.
Между полюсами и станиной располагают прокладки из листовой стали, изменением количества которых регулируют величину воздушного зазора между якорем и полюсами. В добавочных полюсах машин с h > 315 мм регулирование может осуществляться также прокладками из немагнитных материалов. В машинах с h < 315 мм и шихтованной станиной полюсы могут входить в единый блок с сердечником станины, либо привинчиваться к сердечнику. Рассчитывают крепления главных и добавочных полюсов.
Дата добавления: 2018-06-01; просмотров: 1786; Мы поможем в написании вашей работы! |
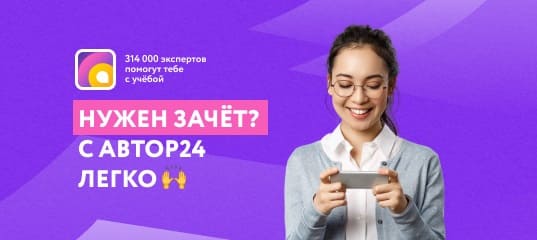
Мы поможем в написании ваших работ!