Шахтное выщелачивание без дробления руд.
ПОДЗЕМНОЕ ВЫЩЕЛАЧИВАНИЕ МЕТАЛЛОВ (ПВ)
Подземное выщелачивание (ПВ) для добычи цветных металлов известно с XVI в. B настоящее время оно широко применяется для извлечения металлов из полиэлементных руд, руд цветных металлов и золота.
С начала шестидесятых годов ХХ в. метод начал применяться для добычи урановых руд в СССР, а затем и золота. Познакомимся с основами подземного выщелачивания.
Основные сведения о ПВ
Подземным выщелачиванием называют метод добычи полезного ископаемого избирательным химическим растворением его на месте залегания и последующего извлечения образованных в зоне реакции химических соединении на поверхность.
В зависимости от геотехнологических свойств и горно-геологических условий отрабатываемых месторождений ПВ осуществляется через скважины, пробуренные с поверхности к рудам, обладающим естественной проницаемостью (рис. 14.1), или из выработок, созданных путем обычной шахтной подготовки месторождения с отработкой отдельных блоков руды системами с выщелачиванием (рис. 14.2). Возможны также их различные сочетания, т.е. шахтная подготовка месторождения и скважинное выщелачивание.
Эффективность использования ПВ приходится определять для каждого конкретного месторождения или даже его участка. В табл. 14.1 представлен пооперационный анализ технологии ПВ с определением основных задач каждой операции.
В табл. 14.2 представлены факторы, влияющие на экономику.
|
|
В качестве показателя, характеризующего эффективность отработки месторождения методом ПВ, можно использовать отношение Ж/Т - массу рабочего раствора, приходящуюся на единицу массы отрабатываемого полезного ископаемого (при заданном коэффициенте извлечения). На основании величины отношения Ж/Т определяется удельный расход реагента (м3/т).
Минеральная база ПВ
Особенности месторождений, пригодных для ПВ, связаны с наличием минералов, содержащих металл и способных легко разрушаться рабочим раствором. Вмещающие породы должны быть инертны к рабочим растворам, а руды обладать естественной или искусственной проницаемостью.
Для ПВ перспективны:
1) месторождения в сильно обводненных и неустойчивых осадочных породах; сюда следует отнести большое число эпигенетических месторождений урана, сформировавшихся в зоне перехода от окислительной к восстановительной среде;
2) руды зоны окисления сульфидных месторождений, где уран и медь находятся в форме легкорастворимых минералов;
3) забалансовые участки месторождений, отработанных обычными методами;
4) крупные и глубокозалегающие месторождения с бедными рудами;
5) отвалы действующих и отработанных месторождений.
|
|
Для столь разнообразных объектов трудно создать универсальную методику оценки применимости технологии ПВ. Поэтому такая оценка проводится в каждом конкретном случае. Так, во многих работах (М.И. Фазлуллина, Б.Д. Халезова, В.Н. Келина, Н.Б. Коростышевского и др.) оцениваются запасы различных рудных месторождений, пригодных для подземного выщелачивания. ВНИПИГОРЦВЕТМЕТом подготовлена методическая работа по оценке и классификации месторождений меди для ПВ,которую можно использовать при рассмотрении сырьевых баз различныхместорождений.
Выполненный Унипромедью анализ сырьевой базы для подземноговыщелачивания медных руд выявил перспективность ПВ более чем для 30месторождений.
Для подземного выщелачивания свинца и цинка могут быть использованы месторождения, а также сульфидные руды в отработанных пространствах и оруденелых боковых породах рудников Садонского свинцово-цинкового комбината.
Может быть перспективно применение ПВ в железорудной промышленности, например для разработки месторождения бурых железняков вСеверном Казахстане.
Широкое применение ПВ должно найти в золотодобывающей промышленности, на месторождениях со сложным, как правило, строением,низким содержанием золота и расположенных вдали от освоенных промышленных районов и в неблагоприятных климатических условиях и поэтому большей частью отнесенных к забалансовым.
|
|
ПВ может быть перспективно и при разработке месторождений фосфатных руд, так как многие фосфатные месторождения нашей страны из-за сложности залегания и трудной обогатимости руд в ближайшей перспективе не могут быть разработаны традиционными методами.
Технология ПВ
В практике подземного выщелачивания в зависимости от вещественного состава руд используются водные растворы минеральных кислот или солей карбонатов щелочных металлов. В России используют растворы серной кислоты (5-50 г/л, рН = О,8-1‚2).
Основной недостаток подземного выщелачивания - неэкономичность использования растворителя при повышенной (более 2-3 %) карбонатности руд и снижение проницаемости продуктивного пласта, которое может быть связано с временной кольматацией (выпадением из растворов соединений железа и алюминия). Например, при рН, равном 1,5-4,1 и 3,3-5‚2 соответственно гидрооксиды железа и алюминия выпадают в осадок.
При значении рН<2 гидроокислы растворяются и проницаемость восстанавливается. Кроме того, к недостаткам способа можно отнести следующие явления кольматации: постоянную, вызванную выпадением гипса в поровом пространстве, газовую, которая идет из-за выделения углекислоты, и механическую, связанную с зашламованиемпризабойной зоны.
|
|
В США при ПВ урана в основном применяют карбонатное выщелачивание, когда используется карбонат и бикарбонат натрия или аммония (концентрация рабочих растворов: 0,5-10 г/л солей металлов, 0,1-0,3 перекиси водорода, 100-300 мл/л кислорода, рН 8-11). Преимущество этого способа: высокая селективность, меньшая зависимость от карбонатности, отсутствие переотложения урана в твердой фазе, более простая схема переработки продуктивных растворов. К недостаткам следует отнести необходимость использования окислителей (перекиси водорода с ингибиторами, кислорода воздуха в присутствии катализаторов-ионов меди). Кроме того, карбонатному выщелачиванию мешают сульфиды, и вообще процесс идет замедленно и хуже вскрывает минералы руд.
Обычно технологический процесс ПВ ведется в несколько стадий:
1 закисление (ведется более слабыми растворами до появления промышленной концентрации металла);
2 - отработка руд рабочими растворами;
3 - вытеснение из пласта продуктивных растворов водой.
При ПВ применяют в большинстве случаев две схемы подачи растворителя в залежь - орошение разрыхленных скальных руд и замена пластовых вод растворителем.
При первой схеме рабочие растворы стекают по кускам руды под действием силы тяжести в виде тонких пленок, а расход раствора не лимитируется проницаемостью залежи и подбирается таким образом, чтобы добиться наибольшей производительности процесса.
При второй схеме движение растворов представляет собой напорную фильтрацию между взаимодействующими выработками. Гидродинамическое поле в этом случае определяется расположением скважин и фильтрационными свойствами рудовмещающего водоносного горизонта, а также темиизменениями, которые происходят при взаимодействии руды с рабочимраствором.
Успешное применение выщелачивания для разработки месторождениязависит от правильного учета гидрогеологических факторов, влияющихна ход отработки. Кроме того, важную роль играют и такие факторы, как состав руд и вмещающих пород, размеры и форма залежей, глубина их залегания, текстура и структура руд, гидродинамические параметры рудовмещающего водоносного горизонта, степень и характер неоднородности в плане и разрезе.
При современном развитии техники не всякое месторождение можно отрабатывать методом ПВ. Для этого оно должно удовлетворять определенным требованиям. Так, минералогический состав залежи и вмещающих пород должен обеспечивать избирательное извлечение полезного ископаемого при экономически допустимом расходе рабочих агентов.
Проницаемость залежи должна превышать проницаемость вмещающих пород. Взаимодействие рабочего раствора с породами не должно приводить к прекращению фильтрации и др.
Возможны различные технологические схемы ПВ, из которых наиболее широко применяются схемы выщелачивания из проницаемых руд в естественном залегании через скважины и с предварительным дроблением скальных руд взрывами с использованием горных выработок для подачи и отвода растворов.
По первой схеме (см. рис. 14.1) месторождение вскрывается системой скважин, располагаемых рядами, многоугольниками, кольцами. В скважины подают растворитель, который, фильтруясь по залежи, выщелачивает полезные компоненты и затем откачивается через другие скважины. Конструкция скважин для ПВ проста (рис. 14.3, 14.4). Особенностью скважин является применение труб из полиэтилена.
По второй схеме (см. рис. 14.2) залежь вскрывают подземными горными выработками. Отдельные блоки разбуривают скважинами и производят взрыв. Затем с верхнего горизонта ведут орошение массива рабочим агентом, который стекает вниз под действием силы тяжести, омывает куски руды и растворяет минералы полезного ископаемого. На нижнем горизонте растворы собирают и перекачивают на поверхность для переработки. Орошение ведется периодически. При снижении концентрации продуктивного раствора орошение прекращают и дают массиву выстояться. Режим чередования этих операций определяется опытным путем. Эта схема применяется главным образом на месторождениях, отрабатываемых подземным способом.
Для ориентировочного расчета параметров процесса ПВ необходимо:
1. Получить исходные данные, содержащие характеристику физико-геологических условий месторождения (глубина залегания, мощность и площадь месторождения, содержание полезного компонента и вредных примесей, вещественный состав, коэффициент фильтрации, эффективная пористость, уровень вольт над кровлей продуктивной залежи и т. д.).
2. Подобрать растворитель, а в лабораторных опытах с реальной рудной массой установить его селективность, газовую составляющую и рассчитать необходимый удельный объем раствора на обработку 1 т руды Ж/Т.
3. Зная Ж/Т, рассчитывают необходимое количество раствора для отработки месторождения как произведение объема руды на удельный расход реагента на выщелачивание 1 т руды, а также задавшись производительностью по объему продуктивных растворов, определить срок отработки месторождения по принятому годовому числу часов работы предприятия и часовую производительность узла приготовления рабочих растворов.
Из гидрогеологических исследований и опытных работ определяется средняя приемистость добычных скважин. Зная приемистость добычных скважин и часовую производительность узла приготовления рабочих растворов, можно определить число закачных скважин, а в зависимости отпринятой системы разработки и число откачных скважин.
Продолжительность работы добычной скважины определяется ее дебитом, запасами полезного ископаемого в зоне действия скважины и коэффициентом извлечения, который устанавливают по лабораторным опытам (технологический коэффициент извлечения), а также коэффициентомохвата. Получив все технологические параметры,можно установить основные экономические показатели метода.
Шахтное выщелачивание без дробления руд.
Имеется удовлетворительный опыт выщелачивания забалансовых урановых руд подачей растворов самотеком из верхних горизонтов рудника (рис. 14.1) или из вееров нагнетательных скважин, в сочетании с веерами дренажных скважин (рис. 14.2) и др.
Первый вариант представлен месторождением Киик-Тал, в предгорьях хребта Моголтау (Таджикистан), приуроченного к пологозалегающему интрузиву мелкозернистых лейкократовых (Лейкократовые горные породы(от греч. leukos - белый, светлый и krateo - господствую * a. leucocraticrocks; н. leukokrateGesteine; ф. rochesleucocrates, leucocrates; и. rocasleucocratas) - магматич. горн. породы, состоящие в осн. из светлоокрашенных или бесцветных минералов (полевые шпаты, кварц и т.п.)) гранитов пермского возраста.
Структура месторождения определяется двумя субширотными разломами, падающими навстречу друг другу под углом 60-80°. Между разломами развиты многочисленные крутопадающие зоны интенсивной трещиноватости с некоторым преобразованием вмещающих пород (грейзенизация, хлоритизация, пиритизация).
Содержание урана в рудах 0,015-0‚020 %. Размеры рудоносной зоны по простиранию 700 м, по падению 250 м и мощностью 200 м. Было задействована опытная установка, результаты её работы B 1973-1977 гг. приведены в табл. 14.3.
Были выявлены благоприятные факторы:
· приуроченность урановой минерализации к зонам повышенной трещиноватости;
· благоприятные формы урановой минерализации (корочки, сажистые налёты по плоскостям приоткрытых трещин);
· простые гидрогеологические условия с циркуляцией подземных вод по трещинам в интрузивных породах;
· вскрытие месторождения дешевым штольневым способом.
Было подготовлено 1500 тыс. т забалансовой руды со средним содержанием урана 0,014-0‚022%. Среднее содержание урана в продуктивных растворах изменялось в пределах от 400 до 40 мг/л, иногда достигая 1 г/л. Активное выщелачивание с такими содержаниями урана продолжалось 1,5-2 года. Затем оно постепенно снижалось до непромышленных концентраций (менее 10 мг/л).
Забалансовые руды на месторождении Кёнигштайн (ГДР) в 1977-78 гг. отрабатывали из 19 блоков выщелачиванием в естественном залегании (без магазинирования) гидродинамическим потоком реагента с подачей растворов под давлением в нагнетательные скважины (горизонтальные, вертикальные, веерные). Активные запасы руды составили около 1,2 млн. т при среднем содержании урана 0,039%‚ а извлечение находилось в пределах 57-66 %. Лучшие показатели характерны для первого периода выщелачивания в 1971-1975 гг., когда основные запасы урана были сосредоточены в хорошо проницаемых кварцевых песчаники, а преимущественная трещиноватость пород ориентировалась в направлении потоков выщелачивания.
Предложен ряд схем интенсификации процессов выщелачивания:
· реверсирование потоков подачи растворов в скважины;
· пульсационное нагнетания растворов;
· с помощью взрывания камуфлетных (подземный взрыв заряда взрывчатых веществ без разрушения грунта на поверхности) зарядов;
· электрообработкой массива;
· улучшения проработки рудного массива по схемам, представленным на рис. 14.5.
Дата добавления: 2018-06-01; просмотров: 855; Мы поможем в написании вашей работы! |
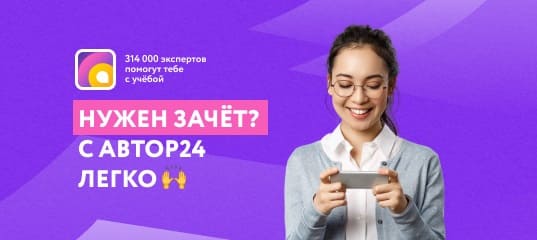
Мы поможем в написании ваших работ!