Вопрос. Ударно-волновой синтез
Действие ударной волны создает условия для синтеза продуктов и для их диспергирования. Однако в отличие от медленного механохимического синтеза происходящие процессы очень быстры и могут рассматриваться в адиабатическом режиме, что приводит к эффективному использованию энергии. С помощью ударно-волновой обработки смесей графита с металлами при давлении во взрыве до нескольких десятков ГПа получаются нанокластеры алмаза со средним размером 4 нм. Размер нанокристаллического алмаза зависит не только от давления, развиваемого в ударной волне, но и от времени прохождения ударной волны. Получаемые с помощью фафито-металлической смеси наноалмазы могут образовывать микронные кристаллиты, содержащие более мелкие нанокластеры алмаза. Так, при длительности ударной волны 10 -г 20 мкс и давлении 20-г 40 ГПа получались как одиночные алмазные нанокластеры 50 нм, так и агломераты размером 5 мкм и более, состоящие из алмазных кластеров 1-г 4 нм и 10-г 60 нм.
Другой метод получения наноалмазов с помощью взрыва состоит в применении детонации взрывчатых веществ с недостатком кислорода, который приводит к выделению свободного углерода, из которого образуется алмазная нанофаза.
Такой процесс реализуется с последующим расширением и охлаждением продукта в газовой фазе инертной атмосферы.
Для получения наноалмазов используются и более мощные взрывчатывешества, например, смесь тринитротолуола и гексогена. Для этих смесей давление и температура в детонационной волне составляют 15 ГПа и Т 3000 К. Выход алмазов составляет 8 9 % от исходной массы.
|
|
Характерной особенностью алмазных нанокластеров, получаемых с помощью детонационного синтеза, является их высокая монодисперсность размера вблизи 4-г 5 нм. Это связано с большей термодинамической стабильностью наноалмаза, по сравнению с фафитом.
Еще один детонационный способ синтеза связан с образованием нанокластеров металлов, оксидов металла с помощью воздействия контактного заряда взрывчатого вещества.
При использовании солей или комплексов металлов для получения нанокластеров и нейтральной среды благодаря их быстрому охлаждению стабилизируются высокотемпературные и метастабильные кристаллические модификации, например кубическая модификация ZTO2.
Воздействие взрыва и ударной волны с целью получения нанокластеров инициируется также с помощью электрического взрыва проводника при прохождении по нему мощного импульса тока длительностью 10 -7-10 с и плотностью 10 -f 10 А/мм.
Самораспространяющийся высокотемпературный синтез.
Самораспространяющийся высокотемпературный синтез (СВС) твердых химических соединений – новый технологический процесс получения материалов, основанный на проведении экзотермической химической реакции взаимодействия исходных реагентов в форме горения. Проще говоря, СВС – синтез материалов горением. Для организации такого процесса горения твердые реагенты практически всегда приходится использовать в виде порошков. Однако здесь горение является не обычной реакцией окисления порошкообразных веществ кислородом с образованием соответствующих газообразных оксидов, а сильноэкзотермической реакцией взаимодействия порошкообразных реагентов между собой или порошкообразных реагентов с жидкими или газообразными реагентами, например, сжиженным или газообразным азотом, с образованием твердых химических соединений. Чаще всего это тугоплавкие неорганические соединения (карбиды, нитриды, бориды и т.п.), которые не разлагаются при горении, и материалы на их основе.
|
|
Типичной реакцией СВС является реакция синтеза карбида титана:
Ti + C®TiС + Q, Q = 3480 кДж/кг,
Tад = 3290К, при Т0 = 300К, (Тad = T0+Q/c),
где Q – тепловой эффект реакции, Tад – температура продукта реакции в адиабатических условиях, Т0– начальная температура реагентов, с – теплоемкость продукта.
|
|
Для осуществления этой реакции готовят смесь порошков титана и углерода (сажи), которую зажигают (инициируют) раскаленной вольфрамовой спиралью. В месте зажигания под действием высокой температуры спирали начинается (инициируется) реакция взаимодействия между порошком титана и сажей с образованием карбида титана. При этом выделяется большое количество тепла (3480 кДж/кг), которое дает высокую температуру продукта (3290К). Раскаленный продукт прогревает и зажигает соседний слой смеси порошка, в котором в свою очередь проходит реакция синтеза карбида титана с выделением большого количества тепла. Этот разогретый слой зажигает следующий слой и т.д. Теперь уже раскаленная спираль не нужна. По исходной смеси порошков начинает самораспространяться реакция синтеза карбида титана в виде ярко светящейся волны горения. За волной (фронтом) горения остается раскаленный продукт TiC, который постепенно остывает. После остывания мы получаем спеченную массу карбида титана. Схема процесса представлена на рис. 0.1.
![]() |
Рис. 0.1. Схема процесса СВС карбида титана |
Другой типичной реакцией СВС, но уже с участием газообразного реагента, является реакция синтеза нитрида титана при сжигании порошка титана в атмосфере газообразного азота:
|
|
Ti+ N2®TiN + Q, Q = 5218 кДж/кг, Tад = 4897К.
Здесь порошок титана засыпают в реактор СВС, представляющий собой цилиндрический толстостенный сосуд (рис. 0.2.). Этот сосуд закрывают герметично крышкой, вакуумируют и заполняют газообразным азотом под повышенным давлением. Затем раскаленной спиралью нагревают локальный участок порошка титана и инициируют реакцию синтеза нитрида титана, при которой газообразный азот поглощается порошком. Эта реакция является также сильно экзотермической и в форме волны горения начинает самораспространяться по всей массе порошка титана. После прохождения волны синтеза и остывания продукта, мы открываем крышку реактора и достаем из него спеченную массу продукта – нитрида титана.
Отметим, что синтез карбида титана, представленный схематически на
рис. 0.1, также ведут в реакторе СВС подобно синтезу нитрида титана, представленному на рис. 0.2.
Из курса процессов порошковой металлургии известно, что неорганические тугоплавкие соединения TiC иTiN можно получать по технологии порошковой металлургии. По этой технологии исходные порошки не сжигают, а нагревают до высоких температур и выдерживают длительное время при таких температурах. Например, при синтезе карбида титана порошки нагревают до 1370 – 1450К и выдерживают 2,5 часа. При синтезе нитрида титана параметры процесса составляют 1370 – 1470К и 1 – 2 часа. Синтез ведут в сложных и громоздких нагревательных устройствах: печах и реакторах. На длительный высокотемпературный нагрев реакционной массы потребляется много энергии от внешних источников.
![]() |
Рис. 1. Схема организации процесса СВС нитрида титана в реакторе |
Из сопоставления процессов получения тугоплавких соединений TiC и TiN методом СВС и методом порошковой металлургии очевидны преимущества метода СВС.
Во–первых, это низкое энергопотребление. Немного энергии нужно в методе СВС для нагрева воспламенительной спирали и зажигания исходного порошка. Далее процесс синтеза идет за счет собственного внутреннего тепловыделения в результате сильноэкзотермической реакции синтеза, т.е. за счет саморазогрева. Энергия здесь не потребляется извне, а наоборот выделяется внутри. Так что потом, после синтеза, ее приходится отводить вовне, охлаждая раскаленные продукты синтеза.
Во–вторых, для метода СВС характерно простое и малогабаритное оборудование. Для реализации процесса СВС нет необходимости в длительном высокотемпературном внешнем нагреве, в громоздких печах с системами нагрева, теплозащиты и терморегуляции. Саморазогрев порошка при СВС позволяет проводить процесс в простых малогабаритных реакторах, а не в печах.
В–третьих, методу СВС присуща высокая производительность. В результате саморазогрева при горении достигаются очень высокие температуры, значительно превышающие температуры нагрева в процессах порошковой металлургии, поэтому скорость реакции синтеза значительно выше. По исходной массе порошка бежит волна синтеза в виде волны горения со скоростью от нескольких мм/с до десятка см/с. Длительность синтеза занимает в реакторе СВС времена от нескольких секунд до нескольких минут, в то время как при печном синтезе эти времена составляют от нескольких десятков минут до нескольких часов.
В–четвертых, метод СВС отличается высокой чистотой продуктов и экологической безопасностью. Это также связано с очень высокими температурами синтеза по сравнению с печным синтезом. При таких высоких температурах вредные примеси разлагаются и испаряются из продукта, обеспечивая его повышенную чистоту и экологическую безопасность процесса СВС.
В–пятых, метод СВС дает широкую гамму материалов: порошки, пористые материалы, беспористые компактные, литые, композиционные, наплавки и покрытия.
Это достигается изменением состава исходных порошков и условий их сжигания. Изменяя их, в первую очередь, температуру горения и давление, мы можем получить самые разные продукты синтеза в самом разном виде. В результате метод СВС обладает большой гибкостью, позволяя получать практически на одном и том же оборудовании самую разнообразную продукцию.
В–шестых, продукты СВС находят практическое применение во многих отраслях промышленности:
- машиностроение: абразивы, твердые сплавы, инструментальные материалы;
- металлургия: огнеупоры, ферросплавы;
- электротехника и электроника: нагревательные элементы, ферриты, сверхпроводники, высокотеплопроводные керамики и клеи – герметики, электропроводные твердые смазки;
- химическая промышленность: катализаторы;
- медицина: материалы с памятью формы и т.д.
Главный недостаток СВС – требование высокой экзотермичности реакции взаимодействия исходных порошковых реагентов, чтобы реакция синтеза продуктов прошла в виде явления горения, чтобы исходный порошок можно было поджечь.
Однако достоинства процесса СВС значительно перевешивают его недостатки, и этот новый перспективный процесс привлекает большое внимание как ученых, так и производственников.
Необычные условия СВС, характеризующиеся высокими температурами в конденсированной фазе (до 5000К), кратковременностью (1секунда и менее), высокой скоростью внутреннего саморазогрева (до 1 млн К/с), резкими градиентами температур и др., обеспечивают получение новых материалов, часто с новыми свойствами, отличающихся от аналогичных материалов, полученных другими способами. К настоящему времени методом СВС синтезировано более тысячи веществ и материалов, создан ряд производств на его основе.
СВС как новый способ синтеза тугоплавких соединений [1] был изобретен, когда для моделирования безгазового горения, при котором исходные твердые реагенты полностью превращаются в твердые продукты, была выбрана смесь порошков титана и бора. При поджигании этой смеси была реализована в форме горения высокоэкзотермическая реакция:
Ti+ 2B®TiB2 + Q,Q = 4250 Дж/кг, Tад = 3193К.
В первых же экспериментах исследователи обратили внимание на продукт горения TiB2 – он сохранял первоначальную форму образца исходной смеси, был подплавленным и очень твердым, резал стекло. Исследователи поняли, что имеют дело с синтезом в волне горения ценного тугоплавкого продукта и назвали процесс "Самораспространяющийся высокотемпературный синтез" или сокращенно, СВС.
В дальнейшем методом СВС стали получать не только тугоплавкие неорганические соединения (карбиды, бориды, интерметаллиды, нитриды и т.п.), но и неорганические соединения с более низкой термической стабильностью (халькогениды, гидриды, фосфиды и т.п.), и даже органические соединения. В качестве исходных реагентов стали использовать не только порошки элементов (Ti, C, B и т.п.), но и некоторых соединений (оксидов, гидридов, углеводородов и т.п.). В результате понятие СВС расширилось и под ним стал пониматься самоподдерживающийся процесс типа горения, приводящий к образованию ценных в практическом отношении твердых продуктов (материалов). Можно сказать, что СВС – это пограничная область между теорией горения и материаловедением.
Поскольку порошки металлов и неметаллов являются основными реагентами практически во всех процессах СВС, а конечным продуктом в подавляющем большинстве случаев является порошковый материал, т.е. или собственно порошок, или спеченный из порошка материал, то технологии на основе процесса СВС можно называть порошковыми технологиями СВС, а получаемые материалы – порошковыми материалами СВС.
При первоначальном знакомстве с СВС часто возникает ошибочное представление, что с помощью СВС легко получить желаемый результат, например, материал – достаточно сделать смесь необходимых реагентов и поджечь. Но при таком подходе трудно надеяться на получение желаемого продукта, причем высокого качества, так как процесс СВС является очень сложным физико–химическим процессом и его протекание зависит от многих факторов: теплового эффекта реакции, состава и структуры исходной смеси порошков, размера их частиц, плотности, размера и температуры образцов, состава и давления окружающего газа и др. Чтобы получить желаемый продукт высокого качества, необходимо глубоко знать процесс СВС и уметь управлять им. Для этого необходимо знать теорию процессов СВС, понимать механизм их протекания, влияние различных параметров. Необходимо уметь подбирать оптимальные технологические режимы, использовать приемы регулирования скорости, температуры и полноты горения, а также состава и структуры продуктов горения. Необходимо знать и правильно выбирать оборудование для реализации процесса СВС. Мы должны знать виды и особенности материалов, получаемых методом СВС, уметь правильно определять их свойства, аттестовывать конечные СВС – продукты. Наконец, мы должны правильно оценить техническую и экономическую эффективность конкретной технологии СВС, чтобы принять правильное решение о создании производства на основе этой технологии СВС, которое было бы рентабельным в условиях рыночной экономики.
Дата добавления: 2018-06-27; просмотров: 639; Мы поможем в написании вашей работы! |
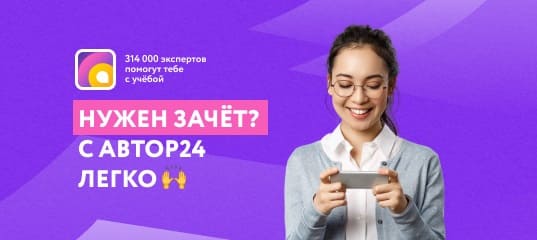
Мы поможем в написании ваших работ!