Прочностные расчеты механических систем
МИНИСТЕРСТВО ОБРАЗОВАНИЯ И НАУКИ РОССИЙСКОЙ ФЕДЕРАЦИИ
федеральное бюджетное государственное образовательное учреждение
высшего профессионального образования
«Курганский государственный университет»
Кафедра «Гусеничные машины и прикладная механика»
Секция «Детали машин и прикладная механика»
ПРИКЛАДНАЯ МЕХАНИКА
Задачи и методические указания
к выполнению контрольных работ
для студентов направлений:
140400.62, 220400.62, 220700.62,
221700.62, 222000.62
Курган 2015
Кафедра: «Гусеничные машины и прикладная механика»
Дисциплина: «Прикладная механика» (направления 140400.62, 220400.62, 220700.62, 221700.62, 222000.62).
140400.62 - Энергетика и электротехника (Электроснабжение);
220400.62 - Управление в технических системах (Системы и технические
средства автоматизации и управления);
220700.62 - Автоматизация технологических процессов и производств
(Автоматизация технологических процессов и производств. Машиностроение);
221700.62 - Стандартизация и метрология (Стандартизация и сертификация); 050100.62 - Педагогическое образование (Технология).
Составили: д-р. техн. наук, проф. Г.Ю. Волков, канд. техн. наук, доц. Л.Н. Тютрина, канд. техн. наук, доц. Д.А. Курасов
Утверждены на заседании кафедры «23» октября 2014 г.
Рекомендованы методическим советом университета «_20_» декабря_ 2013 г.
|
|
ВВЕДЕНИЕ
Предлагаемые методические указания предназначены для студентов немеханических специальностей, изучающих прикладную механику, не проходя или до прохождения в стенах вуза теоретической механики, сопротивления материалов, а иногда даже физики. Цель составителей заключалась в том, чтобы обучающиеся получили тем не менее целостное представление об объектах, характерных задачах и методах прикладной механики. Студентам предлагается решить 6 задач, относящихся к структуре механических систем, кинематике механизмов и прочностным расчетам конструкций. Варианты задач следует выбрать по двум последним цифрам шифра зачетной книжки. Оформлять работу нужно на листах формата А4 или в школьных тетрадях, применяя при необходимости вставки большего формата.
Структура механических систем
Базисными элементами механических систем являются детали. Деталь – это часть изделия, не содержащая соединений. Между собой детали могут быть соединены подвижно или неподвижно(таблица 1).
Таблица 1 – Подвижные и неподвижные соединения
Неподвижные соединения | Подвижные (кинематические) соединения
| |||||
W=0 | Одноподвижные (W=1) | Двухподвижные (W=2) | ||||
| ![]() ![]() ![]() | ![]() | ![]() | ![]() | ||
вращательная пара (шарнир) | поступательная пара | двух- точечная (центроид-ная пара) | высшая пара |
Неподвижные соединения (или просто соединения) деталей делятся на неразъемные (сварное, заклепочное, паянное, клеевое) и разъемные (обычно резьбовые). В расчетных схемах конструкций неподвижное соединение детали со стойкой называют заделкой. В теории механизмов и машин (ТММ) деталь или совокупность деталей, жестко связанных между собой и совершающих общее движение, называют звеном.
Подвижные соединения звеньев в ТММ называютсякинематическими соединениями.Понятие «кинематическое соединение» применимо и по отношению к деталям. Кинематическое соединение между двумя звеньями (или двумя деталями), не содержащее промежуточных элементов, называется кинематической парой.
Кинематические соединения (в том числе кинематические пары) различаются по числу S связей, накладываемых данным соединением, или числу W (W = 6 – S), оставшихся степеней свободы относительного движения двух соответствующих звеньев (деталей). В плоских механических системах встречаются только одноподвижные (W = 1, S = 5) кинематические пары, их называют также парами 5-го класса, и двухподвижные(W = 2, S = 4) кинематические пары, их называют парами 4-го класса. Одноподвижные пары (соединения) плоских систем обычно бывают двух видов – вращательные и поступательные (таблица 1). Вращательная и поступательная пары характеризуются контактом тел по поверхности и называются низшими. Двухподвижные пары плоских систем являются высшими, так как в них контакт тел локализован (происходит по линии).
|
|
Число степеней свободы W в относительном движении звеньев всей плоской механической системы определяется по формуле Чебышева:
W = 3·n – 2Р5 – Р4,
где n – число подвижных звеньев (или деталей, которые на данном этапе структурного анализа рассматриваются как отдельные звенья);
Р5 – число кинематических соединений (пар) 5-го класса;
Р4 – число кинематических соединений (пар) 4-го класса.
Механические системы, характеризующиеся общей величиной W 0, называются фермами, асистемы, для которых общая величина W > 0 – это различные механизмы.
Схематические изображения некоторых механических систем показаны на рисунке 1. Проанализируем их структуру. Для этого вначале найдем и обозначим латинскими буквами соединения деталей, допускающие их относительную подвижность. Сами детали (звенья), образующие между собой подвижные соединения, обозначим цифрами. Заведомо неподвижная деталь (звено), называемая стойкой, считается нулевым элементом системы. На схемах стойка обычно отмечается подштриховкой.
|
|
Рассмотрим механическую систему (рисунок 1 а). Она содержит две детали (помимо стойки), образующих между собой и со стойкой три подвижные (кинематические) соединения: А (0-1) вращательная 5 кл.; В (2-1) вращательная 5 кл.; С (0-2) вращательная 5 кл.; W = 3n – 2Р5 – Р4 = 3∙2 – 2∙3 – 0 = 0. Это, так называемая, статически определимая ферма.
Механическая система, показанная на рисунке 1 в, также является неподвижной и статически определимой: А (0-1) вращательная 5 кл.; В (0-1) 4 кл.; W = 3∙1–2∙1–1∙1=0.
Система (рисунок 1 б) содержит пять кинематических соединений 5-го класса: А (0-1); В (0-2); С (0-3); D (1-2); D1(3-2) и три детали (кроме стойки), входящие в эти соединения. Для нее W = 3∙3 – 2∙5 – 0 = – 1. Системы с числом W < 0 называют статически неопределимыми фермами.
На рисунке 1 г показана система, которая является механизмом. Она содержит три подвижных звена и четыре кинематических пары 5 кл.: А (0-1, вращательная); В (1-2, вращательная); С (2-3, вращательная); D (3-0, поступательная). По формуле Чебышева получаем: W = 3∙3 – 2∙4 – 0 = 1. Таким образом, система является механизмом с одной степенью свободы. Стрелкой показано направление движения ведущего звена 1.
Система (рисунок 1 д) содержит два подвижных звена, две кинематические пары 5-го класса: А (0-1, вращательная), В (0-2, поступательная) и одну пару 4-го класса – С (0-3, высшая). W = 3∙2 – 2∙2 – 1 = 1, следовательно это тоже механизм с одной степенью свободы.
Система (рисунок 1 е) включает три подвижных звена, три вращательные кинематические пары 5-го класса: А (0-1), В (0-2), С (2-3) и одну высшую пару 4-го класса D (0-3). W = 3∙3 – 2∙3 – 1 = 2. Формально, данный механизм имеет две степени свободы, однако, одна их них является «лишней», так как вращение ролика 3 вокруг своей оси не влияет на положение и движение других звеньев. Можно перейти к эквивалентной схеме (рисунок 1 ж): W = 3∙2 – 2∙2 – 1 = 1.
Механическая система, показанная на рисунке 1 з, содержит семь подвижных деталей, обозначенных цифрами, и десять вращательных кинематических пар 5-го класса. В точках С, D, Е присутствуют по две пары (С 2-5; С1 6-5; D 4-5; D1 7-5; Е 3-6; Е1 7-6) W = 3∙7 – 2∙10 – 0 = 1, таким образом – это механизм. Замечаем, что детали 5, 6, 7 неподвижны друг относительно друга и образуют единое звено. С точки зрения теории механизмов более корректно перейти к эквивалентной схеме (рисунок 1 и), содержащей пять звеньев и семь пар 5-го класса: W = 3∙5 – 2∙7 – 0 = 1.
На рисунке 1 к изображен простейший зубчатый механизм. Он включает два подвижных звена (зубчатых колеса) и стойку. Кинематические пары А (0-1) и В (0-2) вращательные 5 кл., а пара С (2-1) высшая 4 кл.: W = 3∙2 – 2∙2 – 1 = 1.
а, в – статически определимые фермы; б – статически неопределимая ферма; г – рычажный (кривошипно-ползунный) механизм; д – кулачковый механизм с плоским толкателем; е – кулачковый механизм с роликовым толкателем; ж – эквивалентный ему кулачковый механизм без ролика; з, и – рычажный механизм; к – зубчатый механизм (зубчатая передача)
Рисунок 1 – Примеры структурных схем механических систем
Задание 1
Выполнить структурный анализ двух механических систем, показанных на рисунке 2 под номерами, соответствующими последней и предпоследней цифрам шифра по зачетной книжке. Для этого:
1) обозначить цифрами детали (звенья) подвижно соединенные между собой;
2) обозначить латинскими буквами кинематические соединения (кинематические пары), образуемые этими деталями (звеньями);
3) определить по формуле Чебышева число W рассматриваемой системы;
4) ответить на вопрос: «Является ли данная система механизмом, статически определимой фермой или статически неопределимой фермой?»
Рисунок 2 – Схемы механических систем к заданию 1
Кинематика механизмов
Основная функция любого механизма заключается в преобразовании движения ведущего звена (звеньев) в определенное движение ведомого вена (звеньев). Процедура определения параметров этих движений называется кинематическим анализом механизма.
Задание 2
Выполнить кинематический анализ рычажного механизма, показанного на рисунке 3, графическим методом. Параметры механизма выбрать по таблице 2.
Рисунок 3 – Схема механизма и графические построения к заданию 2
Таблица 2 – Варианты параметров механизма к заданию 2
Переменные параметры | ||||||||||
| Последняя цифра шифра | |||||||||
1 | 2 | 3 | 4 | 5 | 6 | 7 | 8 | 9 | 0 | |
1,5 | 1,7 | 2.0 | 2,2 | 2,5 | 3,0 | 3,5 | 4,0 | 4,5 | 5,0 | |
| Предпоследняя цифра шифра | |||||||||
1 | 2 | 3 | 4 | 5 | 6 | 7 | 8 | 9 | 0 | |
0 | 0,1 | 0,2 | 0,3 | 0,4 | 0,5 | 0,6 | 0,7 | 0.8 | 0,9 | |
Постоянные параметры | ||||||||||
ω=1 мc–1 ; LOA=0,025 м; LAS=0,5 LAB |
Порядок работы:
1) вычертить кинематическую схему механизма в 8 совмещенных положениях, как показано на рисунке 3. Масштаб построения определить по формуле:
µl = LOA / [OA], м/мм,
где lOA – длина звена ОА, м;
[ОА], мм – отрезок, изображающий это звено на схеме.
2) вычертить шатунную кривую – траекторию точки S, принадлежащей звену 2;
3) построить диаграмму перемещений точки В, отложив по оси ординат линейное перемещение этой точки, а по оси абсцисс – время одного оборота кривошипа (звена 1). Масштаб по оси ординат µS принять равным µl. Масштаб по оси абсцисс:
µt = 2π/ωL, c–1/ мм,
где L – выбирается произвольно (например, 120 мм);
ω – угловая скорость кривошипа, c–1.
4) построить диаграмму скоростей точки В способом графического дифференцирования. Для этого на продолжении оси абсцисс диаграммы скоростей на расстоянии Hv (например, 20 мм) от ее начала выбрать точку Рv. Через эту точку провести прямую, параллельную хорде 1-21 (диаграммы перемещений). Пересечение проведенной прямой с осью ординат соответствует значению скорости точки В на середине отрезка 1-2 оси абсцисс диаграммы скоростей. Далее алогичным образом сносят хорды 21-31, 31-41, 41-51…
Масштаб скорости определить по формуле:
µv = µS/ Hv µt , м c–1 /мм.
5) аналогичным образом построить диаграмму ускорения точки В, дифференцируя по времени диаграмму скоростей. Масштаб ускорения:
µа = µS/ Hv µt , м c–1 /мм.
6) определить численные значения скорости и ускорения точки В для восьми положений механизма, умножив ординаты точек на диаграммах (в мм) на соответствующий масштаб (µv или µа). Так например скорость точки В в положении 2: vВ = 2–21∙µv, а ускорение аВ = 2–22∙ µа. Результаты занести в таблицу.
Задание 3
Обеспечить заданное (таблица 3) передаточное число редуктора, схема которого показана на рисунке 4.
а – коническо-цилиндрический (imax = 25); б – двухступенчатый цилиндрический (imax = 40); в – цилиндро-червячный ((imax = 150); г – двухступенчатый червячный ((imax = 2000); д – трёхступенчатый цилиндрический (imax = 125)
Рисунок 4 – Типы редукторов
Таблица 3 – Варианты задания 3 (две последние цифры шифра)
Передаточное число | Схема редуктора | ||||
а | б | в | г | д | |
8 | 01; 02 | 17; 18 | |||
10 | 03; 04 | 19; 20 | |||
12,5 | 05; 06 | 21; 22 | |||
16 | 07; 08 | 23; 24 | 38; 39; 40 | ||
20 | 09; 10 | 25; 26 | 41; 42; 43 | ||
25 | 11; 12 | 27; 28 | 44; 45; 46 | ||
31,5 | 13; 14 | 29; 30; 31 | 47; 48; 49 | ||
40 | 15; 16 | 32; 33; 34 | 50; 51; 52 | ||
50 | 35; 36; 37 | 53; 54; 55 | 68; 69; 70 | ||
63 | 56; 57; 58 | 71; 72; 73 | |||
80 | 59; 60; 61 | 74; 75; 76 | |||
100 | 62; 63; 64 | 77; 78; 79 | 89; 90; 91 | ||
125 | 65; 66; 67 | 80; 81; 82 | 92; 93; 94 | ||
160 | 83; 84; 85 | 95; 96; 97 | |||
200 | 86; 87; 88 | 98; 99; 100 |
Все представленные механизмы (редукторы) состоят из простейших зубчатых передач (ступеней), последовательно соединенных в кинематическую цепь. Передаточное отношение I12 простейшего зубчатого механизма (отдельной ступени) равно отношению числа зубьев Z2 ведомого колеса к числу зубьев Z1 ведущего колеса этой ступени. Общее передаточное число ступенчатого зубчатого механизма I1П, т.е. отношение угловой скорости ω1 ведущего звена к угловой скорости ωП ведомого звена, равно произведению передаточных отношений отдельных ступеней. Так например, общее передаточное число механизма, показанного на рисунке 4 а, определится по формуле:
I1П = I12 ∙ I34 = (Z2/Z1) ∙(Z4/Z3).
Рациональные диапазоны значений передаточных отношений:
цилиндрической ступени 2 – 8;
конической ступени 1 – 6;
червячной ступени 8 – 80.
Для выполнения задания необходимо:
1) подобрать передаточные отношения ступеней так, чтобы их значения находились в рациональном диапазоне, а произведение соответствовало заданному передаточному числу редуктора;
2) выбрать числа зубьев зубчатых колес так, чтобы сумма чисел зубьев двух колес цилиндрической ступени находилась в диапазоне 100 – 200; конической – 50 – 150, а число зубьев (заходов червяка) было от 1 до 4.
Допускается отклонение полученного общего передаточного числа I1П редуктора от заданного до 5 процентов.
Прочностные расчеты механических систем
Прочность – это способность конструкции сопротивляться силовому воздействию без разрушения. Расчетным, количественным критерием прочности является механическое напряжение, возникающее в наиболее нагруженных точках системы. Напряжение – это сила, действующая на элементарной площадке, отнесенная к площади этой площадки. Единицы измерения напряжения – Паскаль (Па), т.е Н/м2 и Мега-Паскаль (МПа), т.е. Н/мм2.
Различают нормальное σ и касательное τ напряжения. Действующее напряжение должно быть меньше предельно допускаемого напряжения ( [σ] или [τ]) для данного материала в данных условиях нагружения.
Для решения задачи о прочности конструкции нужно знать приложенные к ней силы и размеры соответствующих деталей. Наиболее просто найти силы, действующие на элементы статически определимой фермы.
Задание 4
Рассчитать на прочность ферму, показанную на рисунке 5, характеризующуюся параметрами, приведенными в таблице 4.
Рисунок 5 - Ферма
Таблица 4 - Варианты к заданию 4
Переменные параметры | ||||||||||
β, град. | Последняя цифра шифра | |||||||||
1 | 2 | 3 | 4 | 5 | 6 | 7 | 8 | 9 | 0 | |
10 | 15 | 20 | 25 | 30 | 35 | 40 | 45 | 50 | 60 | |
F, Н | Предпоследняя цифра шифра | |||||||||
1 | 2 | 3 | 4 | 5 | 6 | 7 | 8 | 9 | 0 | |
10 | 20 | 50 | 100 | 200 | 500 | 1000 | 2000 | 5000 | 1000 | |
Постоянные параметры | ||||||||||
α =90о; L=1м; d2=30мм; [σ] = 200 МПа (сталь) |
Для выполнения задания необходимо:
1) рассчитать силы, действующие на стержни 1 и 2. Для этого нужно рассмотреть равновесие сил (рисунок 6 а), действующих в узле (шарнире) В. В векторной форме это уравнение выглядит так: F + R1 + R2 =0,( рисунок 6 б)
в проекциях на оси X и Y:
- R1 +R2 sin (β)=0,
R2 cos (β) -F=0.
Откуда находим:
R2= F / cos (β),
R1= R2sin (β).
а б
Рисунок 6 – Силы, действующие в узле В фермы
2) проверить выполнение условия прочности стержня 2, испытывающего сжатие (проверочный расчет) для этого:
- найти действующее напряжение по формуле:
.
- сравнить его с допускаемым напряжением [σ];
- сделать вывод о выполнении условия прочности;
3) определить параметры сечения стержня 1, испытывающего растяжение (проектный расчет):
площадь сечения
S1 = πd12/4 = R1 / [σ];
откуда .
Ответ привести в мм.
Задание 5
Выполнить проектный прочностной расчет консольной балки, показанной на рисунке 7, и характеризующуюся параметрами, приведенными в таблице 5, для случаев ее изготовления из (рисунок 8): а) квадратного прутка (b=h), б) прямоугольного прутка (b=2·h), в) двутавра (№), г) круглого прутка (d), д) трубы (dо= 0,8d). Сравнить массы полученных конструкций.
Рисунок 7 – Консольная балка
а) б) в) г) д) е)
Рисунок 8 – Возможные сечения консольной балки
Таблица 5 – Варианты к заданию 5
Переменные параметры | ||||||||||
Сравнить варианты | Последняя цифра шифра | |||||||||
1 | 2 | 3 | 4 | 5 | 6 | 7 | 8 | 9 | 0 | |
а-б | а-в | а-г | а-д | б-в | б-г | б-д | в-г | в-д | г-д | |
F, Н | Предпоследняя цифра шифра | |||||||||
1 | 2 | 3 | 4 | 5 | 6 | 7 | 8 | 9 | 0 | |
10 | 20 | 50 | 100 | 200 | 500 | 1000 | 2000 | 5000 | 1000 | |
Постоянные параметры | ||||||||||
L=1м; [σ] = 200 МПа (сталь); плотность стали ρ =7,8 г/мм3 |
На балку действуют внешний силовой фактор – сосредоточенная сила F (таблица 5). Наиболее «опасный» внутренний силовой фактор, возникающий в теле балки, – изгибающий моментMu. График (эпюра) изменения Muвдоль оси балки показан на рисунке 6. Величины моментов Mu, действующих в сечениях консольной балки, нагруженной сосредоточенной силойF, пропорциональны этой силе и расстоянию Z от точки приложения силы до соответствующего сечения(Mu= FZ). То сечение рассматриваемой балки, в которомMu приобретает наибольшие по абсолютной величине значение («опасное» сечение) непосредственно примыкает к заделке. В нем действует изгибающий момент:
Mu мах= FL.
Изгиб вызывает искривление балки. В результате, ее слой, примыкающий к верхней поверхности, растягивается, слой у нижней поверхности сжимается, а слой, расположенный в центре («нейтральный» слой), не изменяет своей длины. Напряжения [σ], распределяются по сечению балки, пропорционально деформации соответствующих слоев (рисунок 8 е). Максимальная величина напряжений при изгибе может быть рассчитана по формуле:
,
где Wx – осевой момент сопротивления сечения.
Осевые моменты сопротивления Wx и площади сечений, показанных на рисунке 8, определяют по формулам:
прямоугольник: ; S = b·h;
квадрат ; S =h2;
круг: ; S = πd 2/4;
кольцо: ; S = π ( d 2–d0) /4;
двутавр – смотри рисунок 9 и таблицу 6. Заметим, что именно двутавр обеспечивает наилучшее сопротивление изгибу.
Рисунок 9 – Параметры сечения двутавра
Таблица 5 – Характеристики двутавров
Номер балки | Масса G 1метр кг | h, мм | b, мм | s, мм | t, мм | R, мм | r, мм | Площадь сечения S, мм2 | Момент сопротив ления Wх, мм3 | |
10 | 9,46 | 100 | 55 | 4,5 | 7,2 | 7,0 | 2,5 | 12,0·102 | 39,7·103 | |
12 | 11,5 | 120 | 64 | 4,8 | 7,3 | 7,5 | 3,0 | 14,7·102 | 58,4·103 | |
14 | 13,7 | 140 | 73 | 4,9 | 7,5 | 8,0 | 3,0 | 17,4·102 | 81,7·103 | |
16 | 15,9 | 160 | 81 | 5,0 | 7,8 | 8,5 | 3,5 | 20,2·102 | 109·103 | |
18 | 18,4 | 180 | 90 | 5,1 | 8,1 | 9,0 | 3,5 | 23,4·102 | 143·103 | |
18а | 19,9 | 180 | 100 | 5,1 | 8,3 | 9,0 | 3,5 | 25,4·102 | 159·103 | |
20 | 21,0 | 200 | 100 | 5,2 | 8,4 | 9,5 | 4,0 | 26,8·102 | 184·103 | |
20а | 22,7 | 200 | 110 | 5,2 | 8,6 | 9,5 | 4,0 | 28,9·102 | 203·103 | |
22 | 24,0 | 220 | 120 | 5,4 | 8,7 | 10,0 | 4,0 | 30,6·102 | 232·103 | |
22а | 25,8 | 220 | 115 | 5,4 | 8,9 | 10,0 | 4,0 | 32,8·102 | 254·103 | |
24 | 27,3 | 240 | 115 | 5,6 | 9,5 | 10,5 | 4,0 | 34,8·102 | 289·103 | |
24а | 29,4 | 240 | 125 | 5,6 | 9,8 | 10,5 | 4,0 | 37,5·102 | 317·103 | |
27 | 31,5 | 270 | 125 | 6,0 | 9,8 | 11,0 | 4,5 | 40,2·102 | 371·103 | |
27а | 33,9 | 270 | 135 | 6,0 | 10,2 | 11,0 | 4,5 | 43,2·102 | 407·103 | |
30 | 36,5 | 300 | 135 | 6,5 | 10,2 | 12,0 | 5,0 | 46,5·102 | 472·103 | |
30а | 39,2 | 300 | 145 | 6,5 | 10,7 | 12,0 | 5,0 | 49,9·102 | 518·103 | |
33 | 42,2 | 330 | 140 | 7,0 | 11,2 | 13,0 | 5,0 | 53,8·102 | 597·103 | |
36 | 48,6 | 360 | 145 | 7,5 | 12,3 | 14,0 | 6,0 | 61,9·102 | 743·103 | |
40 | 57,0 | 400 | 155 | 8,3 | 13,0 | 15,0 | 6,0 | 72,6·102 | 953·103 | |
Для выполнения задания необходимо:
1) рассчитать максимальный изгибающий момент, (Н мм):
Mu мах= FL;
2) рассчитать осевой момент сопротивления в опасном сечении, (мм3):
;
3) рассчитать характерный размер сечения балки для выбранных вариантов формы сечения, используя формулы, связывающие этот размер с Wx, или определить № двутавра по таблице 5.
Изобразить сечения в масштабе;
4) рассчитать площадь сечения S и массу G (G = S·L·ρ, кг) балки для выбранных вариантов формы ее сечения.
Задание 6
Выполнить ориентировочный проектный расчет вала (рисунок 10) на прочность и рассчитать шпонку. Значения параметров приведены в таблице 7.
1 – вал; 2 – втулка; 3 – шпонка.
Рисунок 10 – Соединение вала с полумуфтой призматической шпонкой
Таблица 7 – Варианты задания 6
Переменные параметры | ||||||||||
Крутящий момент Т, Нм | Последняя цифра шифра | |||||||||
1 | 2 | 3 | 4 | 5 | 6 | 7 | 8 | 9 | 0 | |
10 | 20 | 50 | 100 | 200 | 400 | 800 | 1000 | 1500 | 2000 | |
Предпоследняя цифра шифра | ||||||||||
1 | 2 | 3 | 4 | 5 | 6 | 7 | 8 | 9 | 0 | |
Количество шпонок | 1 | 2 | ||||||||
Материал колеса | сталь | чугун | сталь | чугун | сталь |
1 Расчет вала. На первом этапе проектирования диаметр d (мм) консольного участка вала редуктора определяем расчетом на чистое кручение по пониженным допускаемым напряжениям [τ]:
,
где Т · 103 – вращающий момент, передаваемый валом, Н·мм;
[τ]= 15…30 МПа, допускаемые касательные напряжения. Меньшие значения относятся к входным валам, большие к выходным.
Например, для Т = 500 Н·м (Т = 500 Нмм) и [τ]= 20 МПа диаметр вала:
(округляем до целого).
Длину конца вала ориентировочно принимаем L = 1,5d = 75 мм .
2 Выбор шпонки. Для обеспечения соединения полумуфты с валом (рисунок 10) нужно выбрать призматическую шпонку по диаметру d вала и определить ее длину l, исходя из данных, приведенных в таблице 8.
Таблица 8 - Размеры шпонок и пазов по (ГОСТ 23360-84)
Диаметр вала d, мм | Размеры сечения шпонок | Глубина паза | ||
Ширина b, мм | Высота h ,мм | Вал t1, мм | Втулка t2, мм | |
от 6 до 8 | 2 | 2 | 1,2 | 1,0 |
св. 8-10 | 3 | 3 | 1,8 | 1,4 |
св. 10-12 | 4 | 4 | 2,5 | 1,8 |
св. 12-17 | 5 | 5 | 3 | 2,3 |
св. 17-22 | 6 | 6 | 3,5 | 2,8 |
св. 22-30 | 8 | 7 | 4 | 3,3 |
св. 30-38 | 10 | 8 | 5 | 3,3 |
св. 38-44 | 12 | 8 | 5 | 3,3 |
св. 44-50 | 14 | 9 | 5,5 | 3,8 |
св. 50-58 | 16 | 10 | 6 | 4,3 |
св. 58-65 | 18 | 11 | 7 | 4,4 |
св. 65-75 | 20 | 12 | 7,5 | 4,9 |
св. 75-85 | 22 | 14 | 9 | 5,4 |
св. 85-95 | 25 | 14 | 9 | 5,4 |
св. 95-110 | 28 | 16 | 10 | 6,4 |
Примечание: Длины призматических шпонок (мм) выбирают из ряда (по ГОСТ 23360-84): 6; 8; 10; 12; 14; 16; 18; 20; 22; 25; 28; 32; 36; 40; 45; 50; 56; 63; 70; 80; 90; 100; 110; 125; 140; 160; 180; 200; 220; 250; 280; 320.
В рассматриваемом примере диаметр вала d=50 мм, L= 75 мм. По таблице 8 определяем размеры шпонки и шпоночных пазов вала и полумуфты.
Сечение шпонки: b=14 мм, h= 9 мм.
Глубина паза вала: t1= 5,5 мм.
Глубина паза ступицы: t2= 3,8 мм.
Длина l = 70 мм (l < L, концы шпоночного паза не должны подходить к краям посадочного участка вала ближе 2 – 5мм).
3 Проверочный расчет шпонки
Крутящий момент передается боковыми гранями шпонки. При этом на них возникают напряжения смятия σсм, а в продольном сечении шпонки – напряжения среза τср.
Условие прочности шпоночного соединения на смятие: .
Допускаемое напряжение смятия [σ]см при ориентировочных расчетах для стальной ступицы (втулки) принимают [σ]см=150-200 МПа, для чугунной – [σ]см= 70-100 МПа.
Действующее напряжение смятия определяется по формуле:
σсм= F1/ Sсм ,
где F1 – окружная сила на поверхности вала, (H), приложенная к одной
шпонке. F1= Т/( d/2) · z;
z – количество шпонок;
Sсм– площадь смятия, мм2. Sсм=(0,94h – t1) lp;
lp= l-b – рабочая длина шпонки со скругленными торцами, мм.
В рассматриваемом примере при z=1:
F1= 500·103/ 25 = 20000 Н;
lp = 70 -14= 56 мм;
Sсм=(0,94·9 – 5,5)·56=170 мм2;
σсм= 20000/170= 112 H/мм2.
112 <150 H/мм2. Условие прочности шпонки на смятие выполнено.
Условие прочности шпонки на срез: τср [τ]ср ,
где [τ]ср – допускаемое напряжение среза. При ориентировочных расчетах для стальной шпонки можно принять [τ]ср= 90МПа.
Действующее напряжение среза τср определяется по формуле:
τср = F1/ Sср ,
где Sср – площадь среза (Sср= b·lp).
В рассматриваемом примере получаем:
Sср= 14·56 = 785 мм2;
τср =20000/785=25,5 Н/мм2.
25,5 < 90 H/мм2, следовательно условие прочности шпонки на срез выполнено.
По результатам расчета изобразить в масштабе поперечное сечение вала со шпонкой (подобно сечению А-А на рисунке 10).
СПИСОК ЛИТЕРАТУРЫ
1 Теория механизмов и машин / К. В. Фролов, С. А. Попов, А. К. Мусатов [и др.] ; под ред. К. В. Фролова. – М. : Высш. шк., 2001. – 496 с.
2 Прикладная механика : учебник для вузов / В. В. Джамай, Ю. Н. Дроздов, Е. А. Самойлов [и др.] ; под ред. В. В. Джамая. – М. : Дрофа, 2004. – 414 с.
3 Артоболевский, И.И. Теория механизмов и машин [Текст] /И.И. Артоболевский.: – М. : Наука, 1990. – 638 с.
Глеб Юрьевич Волков
Лариса Николаевна Тютрина
Дмитрий Алексеевич Курасов
ПРИКЛАДНАЯ МЕХАНИКА
Задачи и методические указания
к выполнению контрольных работ
для студентов направлений:
140400.62, 220400.62, 220700.62,
221700.62, 222000.62
Редактор Е.А. Могутова
Подписано впечать Формат 60 х 84 1/16 Бумага 65 г/м2
Печать цифровая Усл.печ.л. 1,5 Уч-изд.л 1,5
Заказ Тираж 25
РИЦ Курганского государственного университета
640000, г. Курган, ул. Советская, 63/4
Курганский государственный университет.
Дата добавления: 2018-06-27; просмотров: 523; Мы поможем в написании вашей работы! |
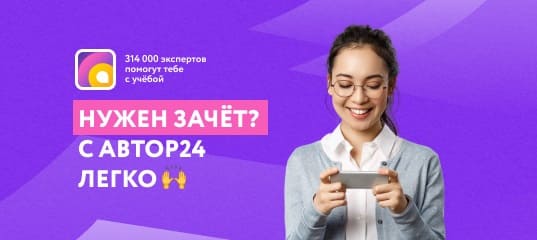
Мы поможем в написании ваших работ!