Химико- термическая обработка металлов: цементация и азотирование.
Nbsp; Кировское областное государственное образовательное бюджетное учреждение среднего профессионального образования «Кировский авиационный техникум»
Контрольная работа
По дисциплине « МАТЕРИАЛОВЕДЕНИЕ»
Специальность 15.02.08 Технология машиностроения
Группа ЗТ – 3Б
вариант № 2
Студент ________________ Галкина Елена Анатольевна
|
Преподаватель ______________ Пирогов А.А.
Оценка за контрольную работу ________________________________________
2018
СОДЕРЖАНИЕ
1. Механические технологические свойства металлов 2. Химико-термическая обработка металлов: цементация и азотирование. 3. Записать марку: а) бронзы, содержащей 6% олова, 6% цинка, 3% свинца б) качественной стали, содержащей углерода 0,45% в) легированной стали, содержащей 0,30% углерода, 1% хрома, 1% никеля, 1% молибдена г) быстрорежущей стали, содержащей 18% вольфрама д) высокопрочного чугуна с пределом прочности на растяжение 30Мпа и относительным удлинением 6% 4. Выбрать и расшифровать: а) качественную сталь с повышенным содержанием марганца б) высоколегированную высококачественную сталь в) чугуны г) сплавы алюминия д) углеродистую сталь обыкновенного качества из предложенных ниже: сталь 32Х4Г2ВС2Т2А ; У8Г ; сталь 65Г; ВК8 ; ВЧ 20-3 ; Ст3пс ; КЧ 25-4 ; ЛАЖМц 66-3-2 ; АЛ4 ; сталь 12Х2Н4Ф3ТС ; сталь 50Г ; сталь 10ХВГ ; Т10К8 ; ВСт3кп ; СЧ 15; Р18 ; сталь 40; БрАЖМц 10-3-1,5 ; Д16 ; У7А. | ||
|
|
Механические и технологические свойства металлов.
К основными механическим свойствам металлов относятся:
¦ твёрдость,
¦ прочность,
¦ пластичность,
¦ вязкость.
Твердость является одной из важнейших характеристик. Твёрдость - это свойство металла оказывать сопротивление пластической деформации при проникновении в него другого более твердого тела на поверхностные слои материала. Измерение твёрдости имеет широкое применение для контроля качества изделий.
В зависимости от методов испытания различают значение твердости по Бринеллю, Виккерсу, Роквеллу. Твердость по Бринеллю обозначают символом HB (твердостью менее 450 единиц) и HBW (твердостью более 450 единиц). Твердость по Виккерсу обозначают буквами HV. Твердость по Роквеллу обозначают символом HR с указанием шкалы твердости A, B или C.
Под деформацией металла понимают изменение формы и размеров тела под действием внешних воздействий или внутренних сил. Деформация в твердых телах может быть упругой и пластической. Упругой называется деформация, полностью исчезающая после прекращения действующих на неё нагрузок, и пластической если она после снятия нагрузок не исчезает.
|
|
Прочность - способность металла сопротивляться деформациям и разрушению. Под разрушением понимают процесс развития в металле трещин, приводящий к разделению его на части. Прочность определяют в результате статического испытания на растяжение.
Пластичность - способность металла к пластической деформации (т.е. получению остаточных изменений формы и размеров без нарушения сплошности). Пластичность используют при обработке металлов давлением.
Вязкость - это способность металла поглощать механическую энергию внешних сил за счёт пластической деформации.
Под технологическими свойствами понимают способность подвергаться различным видам обработки.
Технологические свойства определяют при технологических пробах, которые дают качественную оценку пригодности металлов к тем или иным способам обработки. Образец, подвергнутый технологической пробе (рис.2, приложение Б), осматривают. Признаком того, что образец выдержал испытание, является отсутствие трещин, надрывов, расслоения или излома.
Из технологических свойств наибольшее значение имеют:
¦ обрабатываемость резанием,
|
|
¦ свариваемость,
¦ ковкость,
¦ прокаливаемость
¦ литейные свойства.
Обрабатываемость резанием - комплексное свойство металла, характеризующее способность его подвергаться обработке резанием и определяется по скорости, усилию резания и по чистоте обработки. Испытания по скорости и усилию резания производятся путем сравнения показателей, полученных при обработке данного металла, с показателями обрабатываемости эталонной марки стали (автоматная сталь марки А12). Показатель чистоты обработанной поверхности определяется измерением высоты неровностей, образующихся на поверхности металла после снятия стружки режущим инструментом.
Свариваемость - способность металла давать доброкачественное соединение при сварке, характеризуется отсутствием трещин и других пороков в швах и прилегающих к шву зонах основного металла. Хорошей свариваемостью обладают конструкционные стали; значительно худшую свариваемость имеют чугуны, медные и алюминиевые сплавы, которые требуют специальных технологических условий при сварке.
Ковкость - способность металлов и сплавов без разрушения изменять свою форму при обработке давлением. Многие металлы и сплавы обладают достаточно хорошей ковкостью в нагретом состоянии, а в холодном состоянии - латунь и алюминиевые сплавы; пониженной ковкостью характеризуется бронза.
|
|
Прокаливаемость - способность стали воспринимать закалку на определенную глубину от поверхности. Она зависит от присутствия легирующих элементов в составе и размеров зерен структуры.
Литейные свойства металлов и сплавов характеризуются жидкотекучестъю и усадкой.
Жидкотекучесть - способность металла или сплава в расплавленном состоянии заполнять литейную форму. Для повышения жидкотекучести к ним добавляют легирующие компоненты, например, фосфор - в медные сплавы и чугун, кремний - в алюминиевые сплавы.
Усадкой называется уменьшение объема расплавленного металла или сплава при его затвердевании. На степень усадки влияют многие факторы: химический состав расплава, скорость охлаждения и др.
Химико- термическая обработка металлов: цементация и азотирование.
Химико-термическая обработка металлов - нагрев и выдержка металлических (а в ряде случаев и неметаллических) материалов при высоких температурах в химически активных средах (твёрдых, жидких, газообразных).
В подавляющем большинстве случаев химико-термическую обработку проводят с целью обогащения поверхностных слоев изделий определёнными элементами. Их называют насыщающими элементами или компонентами насыщения.
В зависимости от насыщающего элемента различают следующие процессы химико-термической обработки:
· однокомпонентные: цементация - насыщение углеродом; азотирование - насыщение азотом; алитирование - насыщение алюминием; хромирование - насыщение хромом; борирование - насыщение бором; силицирование - насыщение кремнием;
· многокомпонентные: нитроцементация (цианирование, карбонитрация) - насыщение азотом и углеродом; боро- и хромоалитирование - насыщение, бором или хромом и алюминием, соответственно; хромосилицирование – насыщение хромом и кремнием и т.д.
Широкое промышленное применение получили только традиционные процессы насыщения: азотирование, цементация, нитроцементация, цианирование. Цинкование, алитирование, борирование, хромирование, силицирование применяют значительно в меньшей мере.
Цементация
Это процедура, при которой на изделия воздействуют высокой температурой при помещении их в жидкую, газовую или твёрдую среду, что делается для придания им измененного химического состава. Причем этот эффект обеспечивает насыщение углеродом поверхностного слоя обрабатываемых объектов. Благодаря такой обработке можно обеспечить изделиям высокие характеристики устойчивости к износу и повышенную твердость. Примечательно то, что сердцевина этих деталей сохраняет свою начальную вязкость. Эффективность метода цементации наблюдается при условии, что работа проводится с низкоуглеродистыми сталями, в составе которых доля углерода не превышает значения 0,2%. Термическая обработка обеспечивает насыщение поверхностного слоя деталей, причем для этого их помещают в специально подобранную среду, которая может легко выделить активный углерод, где поддерживается температура в диапазоне от 850 до 950 градусов Цельсия. Создание подобных условий обработки позволяет изменять помимо химического состава обрабатываемых элемента и микроструктуру вместе с фазовым составом. Положительный эффект от такой обработки заключается в повышении прочности, в результате по характеристикам такая деталь не отличается от изделий, прошедших операцию закалки. Для достижения наилучших результатов особое внимание следует уделить грамотному расчету времени, в течение которого деталь должна выдерживаться в создаваемой среде, а также подбору температуры цементации. Особенностью цементации стали является то, что на эту процедуру уходит достаточно много времени. Чаще всего процесс насыщения поверхности и придания ей специальных свойств проходит со скоростью около 0,1 мм за один полный час выдержки. Многие элементы нуждаются в создании упрочненного слоя толщиной более 0,8 мм, что позволяет говорить о том, что на эту обработку придется потратить как минимум 8 часов. На текущий момент технология цементации металла предусматривает использование нескольких сред: газовые; пастообразные; твердые; растворы электролитов; кипящий слой. Обычно при выборе среды для обработки металла используют газовые и твёрдые карбюризаторы
Азотирование
Это технологический процесс химико-термической обработки, при которой поверхность различных металлов или сплавов насыщают азотом в специальной азотирующей среде. Поверхностный слой изделия, насыщенный азотом, имеет в своём составе растворённые нитриды и приобретает повышенную коррозионную стойкость и высочайшую микротвёрдость и производится в несколько стадий:
1. Выполняется термическая предварительная обработка металла, включающая в себя две операции – его закалку и отпуск (высокий). Такая обработка обеспечивает высокую вязкость и прочность сердцевины детали. Закалка стали осуществляется при высоких температурах (в районе 940 ˚С) с последующим охлаждением в масле либо обычной воде. Температура отпуска – от 600 до 670 ˚С. Столь высокая ее величина обусловлена необходимостью придания изделию твердости, необходимой для выполнения эффективной его резки.
2. Производится механическая обработка заготовки, а затем и шлифование металла. Эти операции требуются для того, чтобы деталь имела требуемые (финальные) геометрические параметры.
3. Защита частей металлической поверхности, которые не планируется насыщать азотом. Сделать это несложно путем применения жидкого стекла либо олова, которое наносится толщиной не более 0,015 миллиметра на заготовку по электролитической технологии. Олово формирует непроницаемую тонкую пленку, которую азот преодолеть не может.
4. Непосредственно насыщение стали азотом.
После проведения всех этих процедур выполняется доводка либо шлифовка деталей.
3. Записать марку материала :
а) бронзы, содержащей 6% олова, 6% цинка, 3% свинца
Бр О6Ц6С3
б) качественной стали, содержащей 0,45% углерода
Сталь 45
в) легированной стали, содержащей углерода 0,30%; 1% хрома; 1% никеля; 1% молибдена
ХНМ
г) быстрорежущей стали, содержащей 18% вольфрама
Р18
д) высокопрочного чугуна с пределом прочности на растяжение 30Мпа и относительным удлинением 6%
ВЧ 30-6
4. Выбрать и расшифровать :
а) качественную сталь с повышенным содержанием марганца:
У8Г- сталь углеродистая, качественная, содержит 0,8% углерода и 1% марганца
Сталь 65Г – сталь обыкновенного качества, углеродистая, содержит 0,65% углерода, 1% марганца
Сталь 50Г – сталь углеродистая, обыкновенного качества, содержит 0,50% углерода, 1% марганца
Сталь 10ХВГ – сталь качественная, легированная, содержит углерода 0,10%, хрома, вольфрама и марганца по 1%
б) высоколегированную , высококачественную сталь
Сталь 32Х4Г2ВС2Т2А – сталь высококачественная, высоколегированная, содержит углерода 0,32%, хрома 4%, марганца 2%, вольфрама1%, кремния 2%, титана 2%.
в) чугуны
ВЧ 20-3 - высокопрочный чугун с пределом прочности на растяжение 20Мпа и относительным удлинением 3%
КЧ 25-4 - ковкий чугун с пределом прочности на растяжение 25Мпа и относительным удлинением 4%
Дата добавления: 2018-06-27; просмотров: 233; Мы поможем в написании вашей работы! |
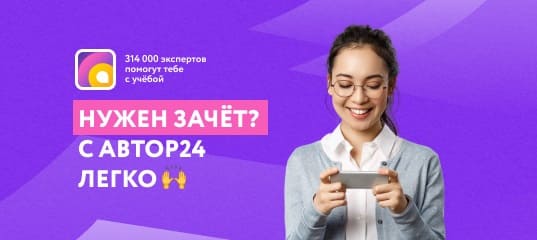
Мы поможем в написании ваших работ!