Огневое обезвреживание шламов металлургических производств
Оглавление
ВВЕДЕНИЕ. 4
Глава 1. Вторичные энергоресурсы.. 15
1.1. Газообразные горючие ВЭР. 15
1.2. Огневое обезвреживание шламов металлургических производств. 19
Глава 2. Утилизация высокотемпературных тепловых отходов. 23
2.1. Газотрубные котлы-утилизаторы.. 23
2.2. Водотрубные котлы-утилизаторы.. 28
2.3. Котлы-утилизаторы за обжиговыми печами серного колчедана. 31
2.4. Установки сухого тушения кокса (УСТК) 38
2.5. Котлы-утилизаторы сталеплавильных конвертеров. 46
Глава 3. Энерготехнологические установки. 51
3.1. Энерготехнологическое комбинирование в прокатном производстве. 51
3.2. Энерготехнологическое комбинирование в целлюлозно-бумажной промышленности. 52
3.3. Энерготехнологическое комбинирование в доменном производстве. 55
3.4. Энерготехнологическое комбинирование при получении водорода. 59
3.5. Охлаждение конструктивных элементов высокотемпературных установок. 61
Глава 4. Использование отработавшего пара. 64
Глава 5. Утилизация низкопотенциальных тепловых отходов. 70
5.1. Утилизация теплоты загрязненных стоков. 70
5.2. Утилизация теплоты агрессивных жидкостей. 72
5.3. Утилизация теплоты вентиляционных выбросов. 74
Глава 6. Глубокое охлаждение продуктов сгорания. 78
6.1. Влажный воздух, влажные продукты сгорания. 78
6.2. Утилизация теплоты низкотемпературных дымовых газов. 80
6.3. Расчет контактного экономайзера. 83
Глава 7. Парогазовые установки. 86
7.1. Основные типы парогазовых установок. 86
|
|
7.2. Количественные показатели термодинамических циклов ПГУ.. 92
7.3. Термическая эффективность парогазовых установок. 96
7.4. Соотношения между параметрами газового и парового циклов. 98
7.5. Парогазовые установки с впрыском пара. 100
7.6. Модернизация котельных в ТЭЦ.. 104
Глава 8. Энергосбережение в газовой промышленности. 106
8.1. Опытно-промышленная газотурбинная расширительная станция (ГТРС) на Среднеуральской ГРЭС 106
8.2. Оптимальное использование теплоты уходящих газов газовых турбин. 109
8.3. Теплоснабжение от утилизационных установок компрессорных станций. 112
Глава 9. Энергосбережение промышленности. 115
9.1. Энергосбережение в котельных и тепловых сетях. 115
9.2. Тепловые потери трубопроводов. 123
9.3. Энергосбережение в компрессорном хозяйстве. 124
9.4. Снижение теплопотерь за счет использования двухкамерного остекления. 128
9.5. Система инфракрасного обогрева производственных помещений. 130
Библиографический список. 134
ВВЕДЕНИЕ
Развитие человеческого общества всегда было связано с расширением использования энергетических ресурсов. За предыдущее столетие мировое энергопотребление увеличилось более чем в 5 раз и достигло 12 млрд. тонн условного топлива в год. Прирост мирового энергопотребления за десятилетний период с 1963 по 1972 гг. составил 2,6 млрд. т у. т., а за последующий десятилетний период – всего 1,7 млрд. т у. т., или в полтора раза меньше. Особенно резко снизились темпы прироста энергопотребления в промышленно развитых странах. Средний ежегодный прирост потребления в мире составил 1,7 % в год, а в США – 0,4 %, в странах Западной Европы – 0,25 %.
|
|
Многие страны уже миновали период расточительного использования энергетических ресурсов и встали на путь энергосбережения и одновременно с этим повышения качества использования энергии (табл. 1).
Рис. 1. Добыча энергоресурсов в мире
Таблица 1
Мировое потребление энергетических ресурсов1950-2020 г. [1]
Показатель | 1950 | 1960 | 1970 | 1980 | 1985 | 1990 | 2000 | 2010 | 2020 |
Потребление энергоресурсов, млрд. ту.т. | 2,85 | 4,35 | 6,44 | 10,10 | 10,90 | 12,20 | 13,00 | 15,50 | 19,00 |
Процент прироста потребления, % | - | 5,30 | 4,80 | 5,70 | 1,58 | 2,30 | - | Прог-ноз | Прог-ноз |
Переломным в изменении темпов прироста потребления стал 1970 г., когда произошло резкое изменение мировых цен на нефть, и промышленно развитые страны приступили к реализации энергосберегающих программ.
Экспертная оценка мирового потребления коммерческих энергоресурсов за период 1860-1990 гг. представлена в табл. 2. Электроэнергия как первичный энергоресурс (табл. 2) произведена на гидравлических, атомных и геотермальных электростанциях. Структуру мирового баланса энергоресурсов наглядно можно представить, если годовое потребление выразить в процентах от суммарного потребления топлива. Тогда становятся заметны долгосрочные тенденции (рис. 2).
|
|
Рис. 2. Мировой баланс энергоресурсов
Баланс показывает коренные, глубокие сдвиги, происходящие в энергетике ХХ века. В течение длительного времени нарастание использования нефтепродуктов, вызванное интенсивной «моторизацией» человеческого общества в автомобильном, морском, воздушном транспорте и других видах нестационарной энергетики, казалось неудержимым, однако тенденция последнего десятилетия свидетельствует об интенсивном использовании газа и угля за счет доли нефти.
Таблица 2
Мировое потребление энергоресурсов
Годы | Уголь, млн. т | Нефть, млн. т | Газ, млн. м3 | Электро-энергия, млн. кВт×ч | Прочие, млн. т |
1860 1900 1920 1940 1960 1970 1980 1985 1990 | 246 1350 2350 3300 3810 3930 5090 5590 6280 | - 26 123 494 1160 2590 4110 4170 4220 | - 7,3 22 88 423 1058 1423 1530 1920 | - 28 86 200 860 1390 1660 2590 3300 | 440 560 670 780 780 720 670 590 560 |
|
|
Вместе с изменениями структуры энергетического баланса в мире наблюдается увеличение неравномерности производства и потребления энергоресурсов различными регионами. Такие страны, как США, Япония, страны Западной Европы, занимая менее 10 % территории, при населении менее 20 % производят более 50 % мирового промышленного продукта, почти 65 % электроэнергии и потребляют более 55 % природных энергетических ресурсов.
Основным источником энергии для человечества является органическое топливо, и в ближайшем будущем эта ситуация вряд ли изменится. Достигнутое значение потребления топлива в 14-15 млрд. т у.т. не может быть обеспечено за счет других нетрадиционных источников энергии. Так запас всех гидроресурсов мира составляет 7,2 млрд. т у.т., а его использование связано с огромными капитальными затратами на сооружение ГЭС. Использование солнечной энергии ограничивается низким КПД преобразования, высокой стоимостью преобразователей и резкой суточной неравномерностью солнечного излучения, требующей создания мощных накопителей электроэнергии. Созданная в Крыму гелиоэлектростанция занимает площадь 40 га и имеет электрическую мощность всего 5 МВт. Использование всей энергии ветра на планете эквивалентно всего лишь 2,8 млрд. т у.т., а использование геотермальной энергии - 1 млрд. т у. т.
Энергетический потенциал СССР во многом складывался благодаря неисчерпаемым ресурсам Российской Федерации, которая занимала ¾ всей территории бывшего Советского Союза, на которой в 1990 г. проживало около 53 % населения страны.
В настоящее время и на долгие годы Россия обеспечена собственными энергетическими ресурсами:
- 37 % разведанных мировых запасов природного газа, 13 % нефти, 19 % угля, 14 % урана сосредоточено на ее территории;
- по технически реализуемому потенциалу гидроэнергетических ресурсов (около 1700 млрд. кВт×ч) уступает только Китаю;
- мощные трубопроводные системы – единая газоснабжающая и единая нефтеснабжающая системы в основной своей части охватывают территорию России;
- значительная часть российского потенциала природных энергетических запасов находится в Сибири: более 80 % природного газа и около 75 % нефти [1] (табл. 3).
В мировом производстве топливно-энергетических ресурсов Российская Федерация в 1990 г. занимала первое место в мире по добыче природного газа (30 % мировой добычи) и нефти – 17 %, второе место по выработке электроэнергии – 9 % и четвертое по добыче угля – 8 % [1].
Реальная обеспеченность Российской Федерации энергоресурсами составляет: по нефти – 15-20 лет, по газу – 55-60 лет, по углю – 300-500 лет.
Основным производителем электроэнергии в России является РАО «ЕЭС России», которое в прошедшее десятилетие формировало свою топливную политику, предусматривая повышение доли использования природного газа во внутреннем потреблении.
Таблица 3
Производство энергоресурсов в Российской Федерации
Энергоресурсы | 1940 | 1960 | 1970 | 1980 | 1990 | 1995 | 2000 | 2004 |
Всего, млн. т у.т в том числе: Природный газ, млн. т у.т Нефть и нефтепродукты, млн. т у.т Уголь, млн. т у.т Прочие виды топлива, млн. т у.т Электроэнергия, млрд. кВт×ч в том числе: Гидроэнергия Атомная энергия | 150 0,2 9,2 134 19 31,6 2,5 - | 368 27 101 436 31 197 24,7 - | 858 119 240 391 28 470 65,9 1,6 | 1465 301 782 261 26 805 107 64,3 | 1875 737 738 273 19,2 1082 170 102 | 1406 685 439 181 20 862 103 172 | 1267 584 324 258 101 846 - - | 1486 632 458 280 116 931 - - |
Однако в последние годы ситуация резко изменилась и прежде всего в газовой промышленности. В ней проявились негативные тенденции, связанные с падением добычи газа на действующих месторождениях Западной Сибири, отставанием освоения новых газовых площадей на Ямале, в Тюменской области и на шельфе Баренцева моря.
В этих условиях ОАО «Газпром» предлагает снизить поставку природного газа для электроэнергетики России, что означает кардинальную перестройку топливного баланса отрасли и возврат к топливной политике послевоенных лет.
В 1999 г. ОАО «Газпром» добыло 545,6 млрд. м3 природного газа, что на 7,4 % ниже уровня 1990 г. Падение спроса на газ российских потребителей за этот период составило 16,3 %, или 66 млрд. м3. Предприятиям электроэнергетики в прошлом году поставлено 134,9 млрд. м3, коммунально-бытовому сектору - 75 млрд. м3, в том числе населению - 38 млрд. м3, на экспорт в дальнее зарубежье - 126,8 млрд. м3, государствам СНГ и Балтии - 77,7 млрд. м3.
В настоящее время Газпром четко и однозначно дает понять, что в среднесрочной и долгосрочной перспективе не сможет обеспечить поставки газа электростанциям даже на современном уровне. Это связано с выработанностью трех уникальных действующих месторождений - Медвежье, Уренгойское и Ямбургское, которые совсем недавно обеспечивали максимальную суммарную добычу газа в объеме 535 млрд. м3 в год. В настоящее время эти месторождения вырабатываются и вступили в период падающей добычи. В 1999 г. из них добыто 419,3 млрд. м3, в 2005 г. добыча газа на них снизится до 273 млрд. м3, а к 2020 г. - до 83 млрд. м3. С аналогичными геологопромысловыми характеристиками осталось только одно месторождение - Заполярное, но годовая добыча из этого месторождения не превысит 100 млрд. м3 и срок поддержания такого уровня добычи не превысит 8-10 лет.
В рассматриваемой перспективе реальные источники нефти и газа перемещаются в труднодоступные районы, в зоны северных морей. Это вызывает многократный рост затрат, необходимость применения новых дорогостоящих технологий. Возрастающие удельные затраты на добычу и транспортировку газа из новых месторождений, в том числе месторождений газа полуострова Ямал, становятся сопоставимыми с затратами на развитие угледобычи, а в ряде случаев превышают их. Нет отечественного опыта проектирования, строительства и эксплуатации месторождений в условиях морского шельфа Баренцева моря и полуострова Ямал на больших глубинах, в ледовых условиях. Отсутствует необходимое оборудование и плавучие средства для освоения таких месторождений.
На поддержание достигнутого уровня добычи и транспорта газа постоянно требуются огромные капитальные вложения.
В связи с возможным сокращением ресурсов природного газа для электростанций рассматриваются следующие направления перестройки топливного баланса электроэнергетики:
· дополнительная загрузка тепловых электростанций, работающих на угле;
· модернизация электростанций, изначально запроектированных на угле (и ранее сжигавших это топливо, а в настоящее время использующих в основном газ), в целях возврата этих электростанций в проектный топливный режим;
· использование новых энергоэффективных технологий сжигания газа (ГТУ и ПГУ);
· использование новых энергоэффективных технологий сжигания твердого топлива (ПГУ с газификацией угля и ЦКС);
· дополнительное развитие ТЭС на угле;
· возможности использования попутного газа;
· возможности дополнительного использования ГЭС;
· возможности дополнительного использования АЭС;
· возможности использования нетрадиционных источников энергии.
Уголь остается основным видом топлива не только для регионов традиционного использования – Сибири, Урала и Дальнего Востока. Зона его значительного потребления на ТЭС распространяется и на европейскую часть страны.
Ожидается, что основная часть вновь вводимых мощностей на пылеугольных ТЭС будет работать на кузнецком и канско-ачинском углях. Использование других видов твердого топлива будет носить местный характер.
Замещение природного газа на электростанциях твердым топливом может быть экономически оправдано при правильном соотношении их цен. Мировые цены на энергоносители на конец 1999 г. составляли: газ - 80-120 $/м3, мазут –110 $/т, уголь – 25-35 $/т (при Q =6000-7000 ккал/кг) без транспортных издержек. Мировая практика показывает, что выработка электроэнергии на угле может быть вполне конкурентоспособной с электроэнергией, выработанной на газовом оборудовании. Однако это потребует осуществления технического переоснащения и реконструкции угольной промышленности в целях не только увеличения объема добычи углей, но и их переработки, обогащения в целях снижения издержек производства энергии, в том числе и расходов по доставке твердого топлива.
В Свердловской области (табл. 4) отсутствуют запасы газа и нефти. ОАО «Вахрушевуголь» добывает открытым способом богословский бурый уголь (г. Карпинск) и шахтным способом каменный газовый уголь (п. Буланаш). Добыча буланашского угля шахтным способом очень дорога, и его стоимость существенно выше, чем у привозных углей. Месторождение угля в районе г. Карпинска практически выработано, и в ближайшие 10 лет планируется закрытие разрезов. В области существуют запасы тощих углей и антрацитов Еловско - Трошковского месторождения, в ближайшем будущем планируется их разработка. Основным производителем тепловой и электрической энергии в Свердловской области является ОАО «Свердловэнерго» (рис. 3).
Таблица 4
Топливный баланс Свердловской области
Топливо | Пром. предприятия и ЖКХ | Свердловэнерго | % |
Газ | 10 млрд. м3 | 5,4 млрд. м3 | 42 |
Уголь | 1 млн. т 0,2 млн. т – местный 0,8 млн. т - привозной | 13 млн. т - экибастузский; 2 млн. т - кузнецкий; 2 млн. т – местный | 57 |
Мазут | 0,4 млн. т | 0,1 млн. т | 1 |
Торф | 0,135 млн. т | - | 0,1 |
Основной проблемой топливоснабжения ОАО «Свердловэнерго» является исторически сложившаяся ориентация на Казахские угли, которые значительно дороже кузнецкого и бородинского углей. В настоящее время рассматриваются вопросы технической возможности перевода станций системы ОАО «Свердловэнерго» на Российские угли.
Рис. 3. Структура топливного баланса АО «Свердловэнерго»
Энергоаудит
Энергетический аудит - это техническо-экономическое инспектирование систем энергогенерирования и энергопотребления предприятия с целью определить возможности экономии затрат на потребляемые топливно-энергетические ресурсы (ТЭР), разработки мероприятий, помогающих предприятию достичь реальной экономии денежных средств и энергоресурсов [2]. Экономия достигается путем выявления и устранения недопустимых потерь энергии, внедрения более экономичных схем и процессов, адаптирующихся к меняющимся условиям работы, использования постоянно действующей системы учета расхода и анализа энергопотребления.
Задача энергоаудита:
· выявить источники нерациональных затрат энергии и неоправданных потерь энергии;
· разработать на основе технико-экономического анализа рекомендации по их ликвидации, предложить программу по экономии энергоресурсов и рациональному энергопользованию.
Обязательному обследованию один раз в пять лет подлежат предприятия с суммарным энергопотреблением более 6000 т у.т. и финансируемые или имеющие дотации на энергоресурсы из Госбюджета. По данным МЭИ и ВТИ на выработку одного кВт×ч электрической энергии в среднем по РФ затрачивается 351 т у.т.
Право на проведение энергетических обследований потребителей ТЭР предоставляется:
· региональным (территориальным) органам Главгосэнергонадзора России.
· организациям, имеющим лицензию на проведение энергетических обследований предприятий.
Энергоаудитор в своих действиях должен руководствоваться Законами Российской Федерации, актами органов государственной власти субъектов РФ, правилами пользования тепловой электрической, тепловой энергии, газа, правилами учета электрической, тепловой энергии, газа, временными руководящими указаниями по организации работ в сфере энергосбережения в управлениях государственного энергетического надзора в субъектах Российской Федерации, ПТЭ и ПТБ в электроустановках.
Энергоаудитор должен отвечать следующим требованиям:
· обладать правами юридического лица;
· иметь необходимое инструментальное, приборное и методологическое оснащение;
· располагать квалифицированным и аттестованным персоналом;
· иметь опыт работы в соответствующей области деятельности;
· иметь аккредитацию в региональном органе Главгосэнергонадзора России.
Согласно правилам различается пять видов проведения энергетических обследований (энергоаудитов):
· предпусковой и предэксплуатационный (проводится энергоаудит заложенных в проект энергосберегающих технических решений, соответствие их современным требованиям ГОСТов и СНиПов);
· первичный(проводится экспресс-анализ резервов энергосбережения с целью оценить необходимость проведения глубокого энергетического обследования, определения планируемого объема затрат и стоимости энергоаудита, подготовки договора на проведение энергетического обследования);
· полный(повторный) энергоаудит (проведение глубокого энергетического обследования предприятия с целью определить эффективность использования потребляемых энергоресурсов - электроэнергии, теплоты, газа, воды;
· внеочередной энергоаудит (в случае, когда по ряду косвенных признаков возникли предположения о резком снижении эффективности использования ТЭР);
· локальные (проводится обследование эффективности использования отдельных видов ТЭР либо режимов наиболее энергопотребляющих установок, агрегатов).
Организация и проведение работ по энергоаудиту обследуемой организации обычно проводится в четыре этапа.
Этап 1
Предварительный контакт с руководителем.
Ознакомление с основными потребителями, производственными процессами и линиями, общим построением системы энергоснабжения. Проводится начальное ознакомление с системой генерирования, распределения и энергопотребления на предприятии, выявляются места нерационального энергопотребления, оценивается потенциал энергосбережения, намечается состав бригады энергоаудита и оценивается объем предполагаемой работы.
По отработанному перечню вопросов собирается информация по энергопотреблению за прошедшие периоды времени. По материалам первичного энергоаудита возможна корректировка планируемых объемов работ и заключаемого договора на проведение работ.
Этап 2 (первичный, экспресс - энергоаудит)
Общее энергопотребление организацией различных энергоносителей (как правило, отражаемое в финансовой отчетности предприятия, в разделе оплаты за энергоносители) разбивается по отдельным зданиям, группам технологических процессов, отдельным основным процессам и установкам, видам продукции (как составляющие в себестоимости). Этот этап работы называется созданием карты энергопотребления. При этом используются стационарные средства учета предприятия, проводятся дополнительные измерения в узловых точках предприятия с помощью переносных приборов, используются расчетные методы.
Опытный энергоаудитор, которым, как правило, является специалист - энергоснабженец, может быстро выявить места возможной экономии энергии:
· по завышенным температурам уходящих газов и разогретых поверхностей, свидетельствующих о наличии плохой теплоизоляции;
· низкому значению cos j асинхронного электропривода, свидетельствующему о его недогрузке и неэкономичном режиме работы системы;
· эффективности работы схемы химводоподготовки питательной воды, ее дегазации;
· невозврату конденсата и отсутствию конденсатоотводчиков;
· нереализованной возможной рекуперации энергии;
· соответствию реальных режимов эксплуатации насосного, компрессорного, вентиляционного оборудования и другого оборудования оптимальным режимам их эксплуатации и т.п.
Все выявленные возможности экономии энергии должны быть внесены в перечень рекомендаций с указанием приоритета на реализацию, определяемый технико-экономическим расчетом.
В объем работ полного энергоаудита входит также оценка удельных энергозатрат на единицу выпускаемой продукции, используемая при сравнении с показателями аналогичных передовых предприятий, и составление топливно-энергетического баланса.
Для организаций с суммарным энергопотреблением более 6 тыс. т у. т. в год составляется энергетический паспорт (согласно Положению Минтопэнерго от 1998 г. о проведении энергетических обследовании организаций ). Отчет по энергоаудиту содержит балансы для потребляемых ТЭР и предложения по энергосбережению.
Составление энергетического паспорта практически не дает новой информации, но на его составление расходуется около 35 % трудозатрат на выполнение энергоаудита. Энергетический паспорт целесообразно оформлять для предприятий, дотируемых из госбюджета.
Результаты энергоаудита согласовываются с органами энергонадзора в тех случаях, когда этого требует законодательство. Введение стимулирующих налоговых и других льгот для предприятий, занимающихся энергосбережением, позволит заинтересовать их в проведении энергоаудитов, при этом вопросы будут решаться в других условиях.
Для государственных и коммунальных организаций, энергоснабжение которых финансируется из госдотаций, задача составления энергетического паспорта связана с выявлением резервов для экономии общественных средств и лимитирования энергопотребления и выделяемых финансовых средств. Для этих случаев составление энергетического паспорта оправдано и целесообразно.
Этап 3 (полный энергоаудит)
Оценка экономии энергии и экономических преимуществ от внедрения различных предлагаемых мероприятий.
Выбор конкретной программы по энергосбережению с выделением первоочередных, наиболее эффективных и быстроокупаемых мероприятий.
Составление энергетического паспорта (обязательно для организаций, финансируемых из госбюджета).
Составление и представление руководству предприятия отчета (и энергетического паспорта) по результатам проведения энергетического аудита. Согласование их с органами Госэнергонадзора, если в этом есть необходимость.
Принятие руководством организации решения о реализации программы энергосбережения, составленной по результатам полного энергоаудита.
Этап 4(Мониторинг)
Организация на предприятии системы энергетического менеджмента, системы постоянно действующего учета и анализа эффективности расхода энергоресурсов.
Продолжение деятельности, дополнительное обследование, дополнение программы реализации мер по энергосбережению, изучение достигнутых результатов.
Энергетический аудитордолжен отвечать следующим требованиям:
· Обязательно иметь лицензию и аккредитацию в органах Госэнергонадзора, что подтвеждает квалификационное соответствие на проведение такого характера работ.
· Иметь хорошую теоретическую подготовку по электро- и теплоснабжению (на уровне инженера), практический опыт работы в области энергоснабжения и энергосбережения.
· Необходимо отметить, что теплотехнические задачи в общем объеме работ составляют 75 %, электротехнические – 25 %. Очень часто возможность экономии электрической энергии выявляется при анализе условий эксплуатации теплотехнического (насосы, компрессоры, вентиляторы и др.) оборудования. Это отражается при комплектации команды энергоаудиторов.
· Энергетический аудитор должен быть специалистом широкого профиля, в том числе иметь навыки финансового аудита в части, касающейся топливно-энергетических ресурсов (или иметь в своей бригаде такого специалиста).
· Энергоаудитор должен обладать способностью работать в качестве руководителя проекта.
Глава 1. Вторичные энергоресурсы
Вторичные энергоресурсы (ВЭР) подразделяются на следующие группы.
1. Горючие ВЭР, получаемые в результате технологических процессов с участием тепловых и сырьевых (горючих) ресурсов:
· коксовый и доменный газы в черной металлургии;
· водород – в производстве каустической соды;
· фракции СО – в производстве Са;
· танковые и продувочные газы – в производствах NH3 и метанола;
· печной газ – в производстве желтого фосфора;
· загрязненное дизельное топливо и др.
2. Тепловые ВЭР.
Тепло отходящих газов технологических агрегатов, тепло основной, побочной и промежуточной продукции, тепло рабочих тел, систем принудительного охлаждения агрегатов, тепло горячей воды и пара, отработанных в технологических и силовых установок.
3. ВЭР избыточного давления.
К ним относятся обладающие потенциальной энергией газы и жидкости, покидающие технологические агрегаты под избыточным давлением, достаточным для их дальнейшего использования.
Соответственно различают следующие основные направления использования ВЭР различных видов: топливное, тепловое, силовое и комбинированное.
ЦСУ при Совмине СССР утвердило в 1974 г. «Отчет об образовании и использовании вторичных горючих и тепловых энергетических ресурсов». Эти отчеты должны были ежегодно составлять и представлять все промышленные предприятия.
При этом подлежат учету тепловые ВЭР следующих параметров: уходящие газы при температуре более 300 °С, при расходе топлива на агрегат более 0,5 т/ч; горячая охлаждающая вода и загрязненный конденсат при температуре более 70 °С и непрерывном расходе более 1 м3/ч; другие тепловые ВЭР следует учитывать при выходе из агрегата более 232 кВт.
Газообразные горючие ВЭР
Рассмотрим основные принципы использования газообразных горючих отбросных газов на примере сажевого производства. Технологическая схема получения сажи, необходимой для производства резины, представлена на рис. 4 [3].
Сырье – масло специальных сортов подогревается в подогревателе и поступает в реактор с температурой ~300 °С. Подогрев осуществляется за счет теплоты уходящих из реактора газов. В реакторе при температуре 1400 °С происходит разложение сырья. Температура поддерживается за счет сжигания в камере сгорания природного газа либо дизельного топлива. В реакторе сжигание осуществляют при коэффициенте подачи топлива a<0,25, т.е. ниже границы сажевыделения. Чтобы не происходило реагирование сажи с СО2 и Н2О при медленном охлаждении продуктов – осуществляют закалку продуктов реакции, впрыскивая воду и охлаждая газы до 700°С. Воздух высокого давления, подаваемый на распыливание продукта, греют до 450 °С, воздух низкого давления, подаваемый на сжигание газа, подогревают до 350 °С. Температура газовзвеси после подогревателя сырья составляет 450 °С. Перед рукавными фильтрами ее охлаждают до 250 ° за счет впрыска воды. На 1 кг углерода образуется от 40 до 60 м3 сажевых газов следующего состава: Н2 = 7-8 %; СО = 6-7 %; СН4 = 0,5-0,7 %; О2 = 2-3 %; СО2 = 2 %; N2 = 40 %; Н2О = 40 %. Теплота сгорания газов данного состава составляет 1,5-2,1 МДж/м3, т.е. находится на пределе устойчивости горения. Если сконденсировать влагу, т.е. охладить газовзвесь после рукавных фильтров до 50-60 °С, то теплота сгорания газов повысится ~ в 1,54-2 раза, но при этом мелкодисперсная сажа попадет в сточные воды. Из каждого килограмма сырья (в том числе технологического топлива) в реакторе образуется 6,5-8,2 м3 сажегазовой смеси.
Рис. 4. Технологическая схема производства активных сортов углерода:
1 – теплообменник; 2 - сырьевой насос; 3 – печь для подогрева сырья; 4 - фильтр;
5 – реактор; 6 – подогреватель воздуха высокого давления; 7 - подогреватель воздуха низкого давления; 8 – подогреватель сырья; 9 – холодильник-ороситель; 10 - циклон;
11 – рукавные фильтры; 12 – котел-утилизатор; 13 – форсунка для подачи воды
Низкокалорийные газы сажевых производств сжигают в пакетно-конвективных котлах (ПКК), выпускаемых Белгородским заводом энергетического машиностроения (Б3ЭМ). Котлы имеют предтопок, в котором сажевый газ сжигается совместно с природным газом (либо мазутом). Воздух, поступающий на горелки, подогревают до 350 °С. Для сжигания отбросных газов используют специальные горелки, обеспечивающие совместное сжигание отбросного и природного газов. Единичная мощность горелок по сажевому газу доведена до 7,5-9,3 МВт. Наибольшая мощность горелки с учетом сжигания резервного топлива составляет 17,3 МВт. Выгорание сажи составляет 99 % в пределах предтопка даже при содержании сажи до 3 г/м3. При снижении нагрузки температура в предтопке падает до 1000-1050 °С и не обеспечивается выгорание сажи. Для полного выгорания сажи требуется обеспечить время пребывания частиц сажи в течение 1,5 с при температуре 1150-1200 °С.
Теплота сгорания сажевого газа при известном его составе рассчитывается по выражению:
,МДж/м3.(1)
Количество природного газа, подаваемого в предтопок для обеспечения устойчивого горения, может быть рассчитано либо по заданной теплоте сгорания смеси сажевого и природного газа, либо по заданной температуре газов в предтопке.
Расчет по заданной теплоте сгорания смеси.
Заданными являются теплота сгорания сажевого газа , теплота сгорания природного газа Qпр и теплота сгорания их смеси Qсм. Доля природного газа х, подаваемого на 1 м3 сажевого газа, рассчитывается из уравнения теплового баланса
. (2)
Расчет по заданной температуре устойчивого горения.
Заданными являются состав и теплота сгорания сажевого и природного газа, а также минимальная температура устойчивого горения tг в факеле, которую принимают обычно примерно равной 1150-1300 °С. По известному составу рассчитывают энтальпии сажевого Iг и природного Iпр газов при температуре tг. Считая, что вся теплота, вводимая в теплоизолированный предтопок, переходит в энтальпию продуктов сгорания, можно записать тепловой баланс в следующем виде:
. (3)
Расчет энтальпий продуктов сгорания при известных объемах продуктов сгорания проводят по следующим выражениям:
, (4)
где энтальпия теоретического количества продуктов сгорания, кДж/ м3:
, (5)
а энтальпия теоретически необходимого количества воздуха, кДж/ м3:
. (6)
Область применения котлов ПКК расширяется, их используют в нефтехимической промышленности за печами выжига катализатора, в сланцеперерабатывающей промышленности для сжигания забалластированных газов [2]. В сланцеперерабатывающей промышленности состав газов меняется во времени и составляет: Н2 = 6,2-10 %; СО = 3,1-4 %; СН4 = 1,25-3,6 %; СmHn = 0,77-1,1 %; О2 = 0,38-2 %; СО2 = 16,2-17,7 %; N2 = 22,1-31,6 %; Н2О » 30 %. Теплота сгорания газов может снижаться до 1,9 МДж/м3 за счет присутствия воды в капельно-жидких компонентах. Трудность сжигания этих газов обусловлена нестабильностью состава. Для сжигания газов, содержащих капельно-жидкую фракцию, предложена специальная горелка (рис. 5).
Рис. 5. Горелка для сжигания газов, содержащих жидкие фракции [3]:
1 – улиткообразный корпус; 2 – тангенциальный патрубок; 3 – цилиндрическая труба;
4 – внутренняя поверхность; 5 – перфорированная обечайка; 6 – желоб; 7 – форсунка;
8 – радиальная труба; 9 - сопло
Горелочное устройство работает следующим образом. Газы, содержащие вязкие капельно-жидкие компоненты во взвешенном состоянии, подаются в улиткообразный корпус 1 тангенциальным патрубком 2 и цилиндрической трубой 3, где в результате закручивания потока крупные капли жидкости тормозятся и оседают на внутренней поверхности 4 перфорированной обечайки 5 с выпускными отверстиями. Под действием силы тяжести они стекают в желоб 6, откуда подаются в форсунку 7, подключенную к радиальной трубе 8. На выходе из форсуночного сопла 9 жидкие компоненты распыливаются, испаряются и сгорают в потоке газовоздушной смеси. Сепарация жидкой фазы и ее дожигание вместе с газами позволяет стабилизировать работу горелки, поскольку сепарация, сбор и подача жидкой фазы с постоянным расходом обеспечивает более равномерную подачу топлива.
Большинство топок для сжигания низкокалорийных газов представляют собой адиабатно изолированные камеры [3]. Установка для сжигания сильно забалластированных газов для выжигания сажи на катализаторах (Alcorn bustion) представлена на рис. 6. Для выжигания используют циклонный предтопок, перед которым предварительно смешивают воздух и отбросные газы.
Отбросные газы поступают в камеру сгорания 1 по трубе 2 и каналу 3. Воздух нагнетается в эту камеру вентилятором. Из кольцевого коллектора 4 воздух поступает в смеситель 5 через отверстия 6 и непосредственно в камеру 1 через отверстия 7. Процесс горения локализуется в камере 1 и в камере догорания 8. Физическое тепло отбирается от продуктов сгорания в трубчатом теплообменнике 9, в котором можно осуществлять подогрев воды или других теплоносителей, например нефтепродуктов, поступающих в реактор для каталитического крекинга. Предварительный разогрев камеры сгорания до температуры выше 940 °С и осуществляется путем сжигания вспомогательного топлива (высококалорийного газа или мазута) в горелках 10.
Рис. 6. Установка для сжигания сильно забалластированных газов, образующихся при выжигании сажи на катализаторах: 1 – камера сгорания; 2 – труба, 3 – канал; 4 - кольцевой коллектор; 5 – смеситель; 6, 7 – отверстия для выхода воздуха; 8 - камера догорания; 9 - трубчатый теплообменник; 10 - горелка |
Огневое обезвреживание шламов металлургических производств
С середины 70-х годов прошлого века в черной металлургии активно начали использоваться схемы оборотного водоснабжения. Техническая вода отстаивается в баках отстойника от масел и окалины и направляется вновь в систему технического водоснабжения. Отделенные в баках шламы имеют в различных отраслях промышленности самый разнообразный состав. На Верх-Исетском заводе состав шламов следующий: Wр= 80-85 %; Ар = 5-10 %; содержание горючих веществ Гр = 10-15 %. Горючие - это масла состав которых в горючем состоянии можно принять приближенно равным Нг = 10 %; Сг = 90 %. Теплота сгорания шламов такого состава крайне низка и не может обеспечить устойчивого горения. Шламы на Верх-Исетском заводе подвергают огневому обезвреживанию в циклонных топках (рис.7), сжигая в них дополнительно природный газ. Температура в циклонной топке поддерживается на уровне 1100-1300 ºС за счет сжигания в тангенциально расположенных горелках природного газа с расходом 400 м3/ч. Шлам с расходом 20 т/сут распыливается радиально расположенными механическими форсунками в циклонную топку. Продукты сгорания охлаждаются на выходе из топки до температуры 400 ºС за счет впрыска воды через форсунки. Продукты сгорания очищаются от мелкодисперсной окалины в пенном газопромывателе и покидают его при температуре 70 ºС. Для повышения температуры газов перед дымососом до 120 ºС к ним подмешивается раскаленные продукты сгорания, отобранные из топки.
Целью расчета является определение необходимого расхода природного газа для обеспечения требуемой температуры в топке и объема циклонной топки. Теплоту сгорания шлама Qш и энтальпию продуктов сгорания шлама Iш при требуемой температуре в топке и сжигании с коэффициентом избытка воздуха ά = 1,3-1,5 рассчитывают по составу шлама, приведенному к рабочему состоянию. При известных значениях теплоты сгорания природного Qг газа и энтальпии продуктов сгорания природного газа Iг ( при тех же t и ά ) долю природного газа на единицу расхода шлама x =Bг/Bш рассчитывают по выражению
. (7)
Тепловая мощность топки при известном расходе шлама Bш определится как
. (8)
Тепловые напряжения зеркала горения принимаются при огневом обезвреживании шламов в диапазоне qv = 0,5-0,7 МВт/м3, тогда объем топки определяется как V = N/qv.
На Синарском трубном заводе (г. Каменск-Уральский) была внедрена более прогрессивная схема утилизации шламов (рис. 8). Шламы с фильтр-пресса подаются во вращающуюся барабанную печь, высокая температура в которой поддерживается за счет сжигания природного газа в горелке, установленной на фронте печи. В печи выгорает масло и испаряется влага, окалина улавливается в инерционном пылеосадителе и направляется на грануляцию в тарельчатом грануляторе. Продукты сгорания охлаждают в котле–утилизаторе и направляют для очистки от мелкодисперсных примесей в скруббера Вентури. В данной схеме утилизации шламов кроме огневого обезвреживания дополнительно вырабатывается (в котле-утилизаторе) теплота и получают гранулы окалины, которые в дальнейшем отправляются на металлургические заводы.
На Ревдинском заводе обработки цветных металлов огневому обезвреживанию подвергаются шламы (рис. 9) с содержанием влаги Wр ~ 50 %. В циклонной топке 1 при температуре 1100-1200 ºС сжигают поверхностное масло (масло, собранное с поверхности баков отстойников). Часть продуктов сгорания направляется во вращающуюся барабанную печь 2, в которую противотоком к продуктам сгорания подаются шламы. За счет контакта с раскаленными продуктами происходит испарение влаги и масла. Пары масла, влаги и рециркулирующие продукты сгорания отсасываются воздушным эжектором 4 из барабанной печи и подаются вместе с подогретым воздухом через горелку в циклонную топку. Другая часть продуктов сгорания последовательно поступает в радиационный 5, а затем в рекуперативный 6 воздухоподогреватели (ВЗП). В радиационном ВЗП подогревают воздух, поступающий в горелки, в рекуперативном ВЗП подогревают воздух для системы воздушного отопления цеха. Требуемые температуры перед радиационным (700 ºС) и рекуперативным ВЗП (400 ºС) обеспечиваются за счет подмеса к продуктам сгорания холодного воздуха.
Рис. 7. Схема огневого обезвреживания шламов на Верх-Исетском заводе:
1 – циклонная топка; 2 – газовые горелки; 3 – форсунки для распыливания шламов;
4 – пережим; 5 – форсунки для распыливания воды; 6 – бункер для сбора шлака; 7 – газоход; 8 – пенный газопромыватель; 9 – регулирующий шибер; 10 – каплеуловитель; 11 – дымосос; 12 – линия подмеса раскаленных продуктов сгорания
Рис. 8. Схема огневого обезвреживания шламов на Синарском трубном заводе:
1 – фильтр-пресс; 2 – барабанная печь; 3 – горелка; 4 – инерционный пылеуловитель;
5 – тарельчатый гранулятор; 6 – котел-утилизатор; 7 – скруббер; 8 – дымосос
Рис. 9. Схема огневого обезвреживания шламов на Ревдинском заводе ОЦМ:
1 - топка; 2 – барабанная печь; 3 – горелки для сжигания поверхностного масла;
4 – эжектор; 5 – радиационный воздухоподогреватель; 6 – рекуперативный воздухоподогреватель; 7 – вентилятор; 8 – дымосос
Глава 2. Утилизация высокотемпературных тепловых отходов
Дата добавления: 2018-06-27; просмотров: 406; Мы поможем в написании вашей работы! |
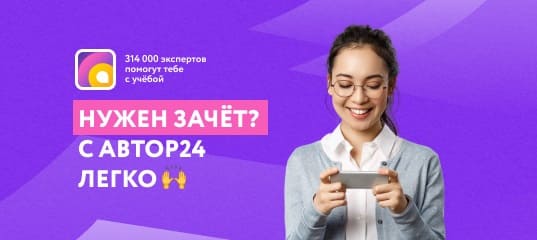
Мы поможем в написании ваших работ!