Дуговая наплавка в защитном газе плавящимся электродом
С целью увеличения производительности при наплавке больших поверхностей применяется ленточная порошковая проволока (рис. 37).
Для заполнения проволоки круглого и плоского сечения применяется порошкообразная смесь из железного порошка и ферросплавов: ферромарганца, феррохрома, феррованадия, ферровольфрама с небольшой добавкой графита.
Порошковые проволоки выпускаются различных марок, а именно: для сварки низкоуглеродистой стали— ПП-АН1; для сварки углеродистых и легированных конструкционных сталей — ПП-АН2 и ПП-АНЗ; для сварки и заварки дефектов чугуна — ПП-Ч1; ПП-Ч2 и ПП-ЧЗ.
В проволоке для сварки низкоуглеродистой стали порошок имеет состав: 0,18—0,2% углерода, 1,9—2,5% марганца, 0,9—1,0% кремния, остальное железо; для сварки теплоустойчивой стали 15ХМ применяется порошок, содержащий 0,12—0,14% углерода, 2—2,2% марганца, 0,9—1,1% кремния, 0,8—1% хрома, 0,45—0,5% молибдена, серы и фосфора не более 0,03% каждого, остальное железо.
Для наплавки под флюсом используются проволоки марок: ПП-ЗХ2В8; ПП-Х10В14; ПП2Г13А и др.; цифры обозначают состав наплавленного металла.
Для наплавки в углекислом газе — проволоки ПП-2ХЗВ10ГТ; ПП-Х12ВФТ; ПП-30Х10Г10Т; ПП-У50Х23Г6Т и др.; буква У и цифра после нее обозначают содержание углерода в десятых долях процента в наплавленном металле.
Для наплавки открытой дугой (с внутренней защитой) применяют проволоки ПП-ЗХ4ВЗФ-0; ПП-У15Х12М-0; ПП-У25Х17Т-0 и др.; буква О обозначает, что проволока предназначена для наплавки открытой дугой.
|
|
Основные способы дуговой наплавки цветных металлов и сплавов для получения биметаллических изделий
учная дуговая сваркавыполняется плавящимся или неплавящимся (угольным, графитовым, вольфрамовым, гафниевым) электродом. При сварке плавящимся электродом (рис. 5.1) дуга горит между ним и изделием. Формирование металла шва осуществляется за счет материала электрода и расплавления основного металла в зоне действия дуги. При сварке неплавящимся электродом для формирования металла шва в зону дуги извне подается присадочный материал.
![]() |
Рис. 5.1. Схема ручной дуговой сварки (наплавки) штучным электродом: 1– основной металл; 2 – сварочная ванна; 3 – электрическая дуга; 4 – проплавленный металл; 5 – наплавленный металл; 6 – шлаковая корка; 7 – жидкий шлак; 8 – электродное покрытие; 9 – металлический стержень электрода; 10 – электрододержатель
Наибольшее применение нашла сварка плавящимся электродом, так как ее можно применять во всех пространственных положениях, сваривая черные, цветные металлы и различные сплавы. При этом используются электроды диаметром 1÷ 12 мм. Однако основной объем работ выполняется электродами диаметром 3÷ 6 мм.
|
|
Электроды классифицируются по материалу, из которого они изготовлены, по назначению, по виду покрытия, по свойствам металла шва, по допустимым пространственным положениям сварки или наплавки, по роду и полярности тока.
По назначениюэлектроды подразделяются на следующие группы:
·для сварки углеродистых и низколегированных конструкционных сталей – У;
·для сварки теплоустойчивых легированных сталей – Т;
·для сварки высоколегированных сталей с особыми свойствами – В;
·для наплавки слоев с особыми свойствами – Н.
По толщине покрытия существуют следующие группы электродов:
·с тонким покрытием – М;-
·со средним покрытием – С;
·с толстым покрытием – Д;
·с особо толстым покрытием – Г.
Покрытия могут быть кислые – А, основные – В, целлюлозные – Ц, рутиловые – Р и прочие – П.
В настоящее время при ремонте техники на железнодорожном транспорте находят наибольшее применение кислые, основные и рутиловые покрытия.
Наплавку металлапри помощи дуговой сваркиприменяют для восстановления изношенных деталей. Для этого на поверхность изделия наносят металл, накладывая его слоями, обладающими необходимыми физико-механическими свойствами. Для этого применяют различные виды сварки (рис.27), в том числе и ручную дуговую с плавящимся или неплавящимся электродом.
|
|
Рис. 27 Основные способы наплавки плавлением:
А-угольным электродом (1), расплавлением сыпучего наплавочного сплава (2);
Б-покрытым электродом (1) или легирующим покрытием (2);
В-неплавящимся вольфрамовым электродом (1) в инертных газах с задействованием присадочного прутка (2);
Г-плавящимся электродом (1) в защитном газе;
Д-сварка плавящейся проволокой (1) под флюсом (2);
Е-лентой плавящейся (1) в защитном газе (под флюсом);
Ж-струей плазмотрона (1) с наложенным или спеченным из порошков наплавочного материала (2);
3-плавящимся электродом (1) с перемещаемым медным ползуном (2), 3-наплавляемая деталь; 4-наплавленный слой
Основным достоинством ручной дуговой наплавки является простота и универсальность метода, возможность выполнения сложных наплавочных работ в труднодоступных местах. К недостаткам относят низкую производительность, загазованность в месте производства работ, сложность получения необходимого качества наплавленной поверхности.
Наплавку плавящимся электродом ведут по той же технологии, что и обычную сварку. Перед наплавкой поверхность тщательно зачищают, следя особенно за тем, чтобы не осталось жировых пятен и коррозии. Электроды подбирают, исходя из условий эксплуатации наплавляемой поверхности. Для этого применяют как обычные сварочные электроды, предназначенные для сварки легированных сталей, так и специальные наплавочные электроды, обладающие заданными свойствами. Для наплавки износостойких поверхностей применяют порошковые проволоки с заданным химическим составом.
|
|
В качестве источников питания для сварочной дуги используют серийные выпрямители и сварочные трансформаторы.
Ручная дуговая наплавка
Ручную дуговую наплавку экономично применять при незначительном объеме наплавочных работ, а также при выполнении наплавки в различных пространственных положениях. Основное внимание при ручной дуговой наплавке стальными электродами (Рисунок 1) уделяется подготовке деталей к наплавке. Качество наплавочных работ в значительной степени зависит от состояния наплавляемой поверхности, поэтому все детали должны быть предварительно очищены. После очистки поверхности детали определяют величину и характер износа, наличие трещин, вмятин и т. п.
При выполнении любых наплавочных работ твердость и износостойкость наплавленного металла зависят от марки наплавочных электродов, химического состава основного металла, режима наплавки и количества наплавляемых слоев.
Недостатками ручной дуговой наплавки является ее относительно малая производительность, тяжелые условия труда, непостоянное качество наплавленного слоя. Повышения производительности при ручной дуговой наплавке можно добиться применением электродов больших диаметров, присадочного прутка, пучка электродов.
Рисунок 1. Схема ручной дуговой наплавки голым электродом (медь и ее сплавы)
Рисунок 2. Схема ручной дуговой наплавки покрытым электродом
Дуговая наплавка в защитном газе плавящимся электродом
Наплавка в защитных газах характеризуется универсальностью процесса: возможность наплавки во всех пространственных положениях, на объекты сложной геометрической формы без применения каких либо специальных приспособлений в зависимости от условий наплавки.
Наплавка в защитных газах целесообразна в тех случаях, когда невозможна или затруднена наплавка под флюсом.
При наплавке плавящимся электродом в защитных газах (Рисунок 3) сварочная ванна защищена от воздуха. Количество газа, которое необходимо подавать для оттеснения воздуха от сварочной ванны, зависит от ряда факторов: теплофизических свойств защитного газа, параметров наплавки (силы сварочного тока, напряжения на дуге, вылета электрода, скорости наплавки и т. д.) и конструкции газоэлектрической горелки.
Рисунок 3. Схема наплавки в защитном газе плавящимся электродом
В качестве защитных газов при наплавке (сварке) цветных металлов и сплавов применяют аргон, гелий или смесь инертных газов. При наплавке меди и ее сплавов можно применить азот. Для повышения стабильности горения дуги и отвода кислорода в защитный газ добавляют водород в количестве от 2 до 5 %.
Наплавку в защитных газах проводят обычно на постоянном токе обратной полярности. Это обеспечивает лучшую устойчивость горения дуги, мелкокапельный перенос металла, меньшее разбрызгивание.
При наплавке в защитных газах необходим мелкокапельный перенос электродного материала, при котором повышается стабильность горения дуги, уменьшается разбрызгивание, улучшается формирование шва. На характер электродного материала оказывает влияние совокупность следующих факторов: воздействие на металл электрических и магнитных сил, сил тяжести, поверхностного натяжения металла, давления выделяющихся из металла паров и газов. Степень влияния каждого из перечисленных факторов зависит от рода и полярности тока, режимов наплавки, материала электрода, состава дуговой атмосферы и т. д.
Увеличение производительности наплавки ограничивается диапазоном сварочного тока; увеличение тока приводит к повышению разбрызгивания наплавляемого металла, ухудшается формирование наплавляемого валика, в целом процесс наплавки начинает проистекать нестабильно.
Данная методика оптимальна для восстановления и придания особых свойств поверхностям деталей сложных конфигураций, отверстиям с большой глубиной. Она выполняется в разных положениях (пространственных) обрабатываемых изделий, позволяет автоматизировать и механизировать наплавку, используя серийные аппараты для сварки, а главное состоит в том, что специалист четко видит весь процесс и может внести в него необходимые корректировки.
Технология наплавки с применением флюсов и с использованием защитных газов по своей сути одна и та же. Но вторую методику разумнее реализовывать в тех случаях, когда по условиям выполнения операции сложно удалять корку шлака либо подавать в зону наплавки флюс. Осуществляется она в атмосфере одного из четырех газов (гелий, углекислый, азот, аргон).
Легированные и углеродистые металлы наплавляют в углекислом газе, который имеет малую стоимость, медные сплавы – в нейтральном по отношению к меди азоте, магниевых и алюминиевых сплавов, а также высоколегированных сталей – в гелии и аргоне. Причем в последнем случае чаще всего используются вольфрамовые неплавящиеся сварочные стержни, а в остальных – плавящиеся (процесс ведется на обратной полярности постоянного тока).
Недостатком описываемого вида наплавки признается то, что на открытом воздухе выполнять наплавочные мероприятия не рекомендуется, так как есть реальная опасность задувания ветром струи газа. Кроме того, жидкий металл при обработке металлов весьма активно разбрызгивается, засоряя тем самым горелку (ее сопло) и мундштук.
Некоторые особенности наплавки в защитных газах:
- для обработки внутренних поверхностей конической и цилиндрической формы рекомендуется использовать специальные мундштуки большой длины;
- операция выполняется на максимально возможной короткой электродуге, что обеспечивает минимальное разбрызгивание материала;
- изделия цилиндрической формы допускается восстанавливать по винтовой линии, применяя способ поперечного передвижения сварочного стержня либо методику непрерывного валика;
- плоские поверхности желательно наплавлять небольшими "разбросанными" участками, чтобы изделие не коробилось;
- когда используется углекислый газ, в проволоке для наплавки должен присутствовать кремний, марганец или иной раскисляющий компонент;
- допускается вести процесс порошковыми проволоками в тех ситуациях, когда наплавленная поверхность должна иметь после операции какие-либо специальные характеристики.
.
Дуговая наплавка под флюсом
По-сравнению с наплавкой в защитных газах, наплавка под флюсом характеризуется высокой производительностью, минимальным (0,5-3%) коэффициентом потерь электродного металла. Кроме того, закрытая дуга позволяет избежать применения каких-либо дополнительных средств защиты от ее теплового и светового излучения, брызг и возможных выплесков металла из сварочной ванны.
В общем случае при наплавке под флюсом (Рисунок 4) дуга горит между электродом и изделием, к которому подведен ток, и образует на поверхности изделия ванночку расплавленного металла. Наплавляемый участок покрывает толстый слой сыпучего флюса. Дуга частично расплавляет флюс и горит внутри полости с эластичной оболочкой из расплавленного флюса – шлака. Расплавленный шлак надежно изолирует жидкий и перегретый металл от газов воздуха, предупреждает разбрызгивание и способствует сохранению тепла дуги. После затвердевания металла образуется наплавленный валик, покрытый шлаковой коркой и нерасплавившимся флюсом.
Для электродуговой наплавки (сварки) алюминия и его сплавов плавящимся электродом по слою флюса (полуоткрытой дугой) применяют плавленые флюсы АН-А1, 48-АФ-1, МАТИ-1а и под слоем флюса - керамические флюсы ЖА-64 и ЖА-64А.
Рисунок 4. Схема наплавки под флюсом
Для наплавки (сварки) меди применяют плавленые флюсы марок АН-348А, ОСЦ-20С, АН-26С и бескислородные фторидные флюсы, например, марки АН-М1.
Для наплавки (сварки) титана и титановых сплавов применяют бескислородные флюсы АНТ-1, АНТ-3, АНТ-7 системы СаF2 – BCl2 – NaF.
Наплавка (сварка) никеля может осуществляться под флюсами двух типов: керамическим (марки ЖН-1) и плавлеными фторидными бескислородными и высокоосновными (марки АН-Ф5, АН-8, 48-ОФ-6, АН-29 и др.).
Дата добавления: 2018-06-27; просмотров: 1252; Мы поможем в написании вашей работы! |
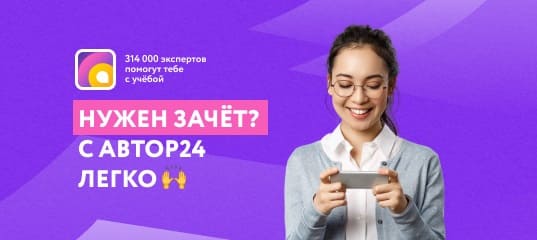
Мы поможем в написании ваших работ!