Второй этап коспоновки редуктора
В развитие первой компоновки здесь вычерчивают валы с насаженными на них деталями.
Диаметры участков валов под зубчатые колеса, подшипники и пр. назначают в соответствии с результатами предварительного расчета и с учетом технологических требований на обработку и сборку.
Взаимное расположение подшипников фиксируем распорной втулкой и установочной гайкой М39 х 1,5 с предохранительной шайбой. Толщину стенки втулки назначают (0,1¸0,15) dп; принимаем ее равной 0,15×40 = 6 мм.
Мазеудерживаюшие кольца устанавливают так, чтобы они выходили за торец стакана или стенки внутрь корпуса на 1—2 мм.
Подшипники размешаем в стакане, толщина стенки которого dст = (0,08¸0,12) D, где D — наружный диаметр подшипника: примем dст = 0,12×80 » 10 мм.
Для фиксации наружных колец подшипников от осевых перемещений у стакана сделан упор величиной К = 6 мм
У второго подшипника наружное кольцо фиксируем торцовым выступом крышки подшипника через распорное кольцо.
Для облегчения посадки на вал подшипника, прилегающего к шестерне, диаметр вала уменьшаем на 0,5 — 1 мм на длине, несколько меньшей длины распорной втулки.
Очерчиваем всю внутреннюю стенку корпуса, сохраняя величины зазоров, принятых в первом этапе компоновки: х = 10 мм, у2 = 20 мм и др.
Используя расстояния f2 и с2, вычерчиваем подшипники
Для фиксации зубчатое колесо упирается с одной стороны в утолщение вала Æ68 мма с другой — в мазеудерживающее кольцо; участок вала Æ60 мм делаем короче ступицы колеса, чтобы мазеудерживающее кольцо Æ55 мм упиралось в торец колеса, а не в буртик вала; переход вала от Æ60 мм к Æ55 мм смещен на 2 — 3 мм внутрь зубчатого колеса.
Наносим толщину стенки корпуса dк = 10 мм и определяем размеры основных элементов корпуса
Определяем глубину гнезда под подшипник lг » 1,5Т2 = 1,5 × 23 = 35 мм (Т2 = 23 мм — ширина подшипника 7211).
|
|
9. Проверка прочности шпоночных соединений
Здесь ограничимся проверкой прочности лишь одного соединения, передающего вращающий момент от ведомого вала к звездочке.
Диаметр вала в этом месте de2 = 48 мм. Сечение и длина шпонки
b∙h∙l = 14 ∙9 ∙63, глубина паза t1 = 5,5 мм по ГОСТ 23360-78.
Момент на звездочке Т3 = 400 × 103 Н×мм.
Напряжение смятия
σсм=2T3/dB2(h-t1)(I-b)= =97.2 МПа
10.Уточненный расчет валов
Материал валов — сталь 45 нормализованная; sв = 570 МПа
Пределы выносливости s-1=0,43 ∙570 = 245.1 МПа и t-1=0,58 ×245.1= 142.2МПа.
У ведущего вала определять коэффициент запаса прочности в нескольких сечениях нецелесообразно; достаточно выбрать одно сечение с наименьшим коэффициентом запаса, а именно сечение в месте посадки подшипника, ближайшего к шестерне В этом опасном сечении действуют максимальные изгибающие моменты Му и Мх и крутящий момент Тz = Т1.
Концентрация напряжений вызвана напрессовкой внутреннего кольца подшипника на вал.
|
|
Изгибающие моменты в двух взаимно перпендикулярных плоскостях
My=Rx2C1=1790∙120=214.8∙103Н∙мм
Mx=Ry2C1=505∙120=60.6∙103Н∙мм
Суммарный изгибающий момент
M= =222∙103Н∙мм
Момент сопротивления сечения
W=πdn13/32= =6.28∙103мм3
Амплитуда нормальных напряжений
σ𝛖=σmax= =36 МПа
Коэффициент запаса прочности по нормальным напряжениям
Sσ= =
≈2.62
Где ≈2.6
Полярный момент сопротивления
WP=πdn13/16=2W=2∙6.28∙103=12.56∙103 мм3
Амплитуда и среднее напряжение цикла касательных напряжений
τP=τm=τmax/2= ∙T1/Wp=
≈5 МПа
Коэффициент запаса прочности по касательным напряжениям
Sτ= =
13.79
Где =0.6
+0.4=1.96; коэффициент yt = 0,1;
Коэффициент запаса прочности
S=SσSτ/ Sσ2+Sτ2=
=2.57
Для обеспечения прочности коэффициент запаса должен быть не меньше [s] = 1,5¸1,7. Учитывая требования жесткости, рекомендуют [s] = 2,5¸3,0. Полученное значение s = 2,57 достаточно.
У ведомого вала следовало бы проверить прочность в сечении под колесом dк2 = 60 мм и под подшипником dп2 = 55 ммсо стороны звездочки. Через оба эти сечения передается вращающий момент Т2 = 400×103 Н×мм, но в сечении под колесом действует изгибающий момент
|
|
Mи2= (Rx3C2)2+(Ry3C2)2=
≈430∙103Н∙мм
а под подшипником Ми3 = Fвl3 = 3978 × 100 = 397,8 × 103 Н×мм. Ми2 больше Ми3
всего на 7%, а момент сопротивления W2 больше W3пропорционально =
= (60/55)3 = 1,30, т. е. на 30%. Поэтому заключаем, что из этих двух сечений более опасно сечение под подшипником. Для него и проведем расчет.
Изгибающий момент Ми3 = 397,8 × 103 Н×мм.
Момент сопротивления сечения
W=πdn23/32= =16.3∙103 мм3
Амплитуда нормальных напряжений
σ𝛖=σmax=Mиз/W= =24.4 МПа
Коэффициент запаса прочности по нормальным напряжениям
Sσ= =
=2.97
Где =3.4;
Полярный момент сопротивления
WP=πdn23/16=2W=2∙16.3∙103=32.6 мм3
Амплитуда и среднее напряжение цикла касательных напряжений
τ𝛖=τm=τmax/2= ∙T2/WP=
=6.1 МПа
Коэффициент запаса прочности по касательным напряжениям
Sτ= =
=9.13
Где =0.6+3.4=2.44; yt = 0,1:
Коэффициент запаса прочности
S=SσSτ/ Sσ2+Sτ2=
=2.82>[S]
11.Вычерчивание редуктора
Укажем некоторые конструктивные особенности проектируемого редуктора.
Подшипники ведущего вала смонтированы в общем стакане.
Рассмотрим, как передается осевая сила. От шестерни осевая сила передается через заплечик вала, мазеудерживающее кольцо, внутреннее кольцо правого подшипника, распорную втулку, левый подшипник, промежуточное кольцо, крышку подшипника и болты. С болтов осевая сила передается на корпус редуктора.
Подшипниковый узел ведущего вала уплотнен с одной стороны
|
|
мазеудерживающим кольцом, а с другой — манжетным уплотнением.
Подшипники ведомого вала уплотнены так же, как подшипники ведущего вала. Осевая сила от зубчатого колеса передается через мазеудерживающее кольцо на внутреннее кольцо подшипника, через ролики на наружное кольцо, далее через промежуточную втулку, крышку подшипника и болты на корпус редуктора..
Зубчатое зацепление регулируют набором металлических прокладок, устанавливаемых между фланцем стакана ведущего вала и бобышкой корпуса редуктора, а также прокладками на ведомом валу, которые могут изменять расположение зубчатого колеса.
Для осмотра зацепления и заливки масла служит окно в верхней части корпуса редуктора. Окно закрыто крышкой; для уплотнения под крышку окна помещают прокладку из технического картона.
Маслоспускное отверстие закрывают пробкой и уплотняют прокладкой из маслостойкой резины.
Уровень масла проверяется жезловыммаслоуказателем.
Относительное расположение корпуса и крышки редуктора фиксируется двумя коническими штифтами.
Редуктор крепят к фундаменту четырьмя болтами с резьбой М20
Выбор сорта масла
Смазывание зубчатого зацепления производится окунанием зубчатого колеса в масло, заливаемое внутрь корпуса до погружения колеса на всю длину зуба.
При контактных напряжениях sН = 470 МПа и средней скорости v = 4,35 м/с вязкость масла должна быть приблизительно равна 28×10-6 м2/с. принимаем масло индустриальное И-30А (по ГОСТ 20799-75*).
Подшипники смазываем пластичным смазочным материалом,
закладываемым в подшипниковые камеры при монтаже.
13. Сборка редуктора
Отличие состоит в необходимости регулировки роликовых конических подшипников и конического зубчатого зацепления.
Для нормальной работы подшипников следует следить за тем, чтобы, с одной стороны, вращение подвижных элементов подшипников проходило легко и свободно и, с другой стороны, чтобы в подшипниках не было излишне больших зазоров. Соблюдение этих требований, т. е. создание в подшипниках зазоров оптимальной величины, производится с помощью регулировки подшипников, для чего применяют наборы тонких металлических прокладок устанавливаемых под фланцы крышек подшипников. Необходимая толщина набора прокладок может быть составлена из тонких металлических колец толщиной 0,1; 0,2; 0,4; 0,8 мм.
Для регулирования осевого положения конической шестерни обеспечивают возможность перемещения при сборке стакана, в котором обычно монтируют узел ведущего вала редуктора.
В рассматриваемом редукторе подшипники ведущего вала установлены широкими торцами наружных колец наружу (см. рис. 12.19). Схему такой установки называют установкой «враспор»; она изображена на рис. 12.20,а. На этом рисунке показаны заштрихованными те детали, которые участвуют в передаче внешней осевой силы Fa. В радиально упорных подшипниках возникают радиальные реакции, которые считаются приложенными к валу в точках пересечения оси вала с нормалями к контактным поверхностям подшипников.
Рациональна конструкция, в которой подшипники установлены широкими торцами наружных колец внутрь. Схема такой установки «врастяжку» изображена на рис. 12.20,б. При консольном расположении шестерни повышается неравномерность распределения нагрузки по длине зуба шестерни. Это можно уменьшить за счет повышения жесткости узла. Конструкция по схеме б является более жесткой, чем конструкция по схеме а, за счет того, что при одном и том же расстоянии L между подшипниками расстояние с¢1> с1. К недостаткам второй схемы (см. рис. 12.20,б) относится то, что внешняя осевая сила Fa нагружает правый подшипник, на который действует большая радиальная сила Р¢пр>Р'л. В первой схеме (см. рис. 12.20, а) внешняя осевая сила Fa нагружает левый подшипник, на который действует меньшая радиальная сила Рл<Рпр. Поэтому неоднородность нагрузки подшипников при установке по второй схеме возрастает.
Список использованной литературы
1.Иванов М.Н., Финогенов В.А. Детали машин: Высшая школа, 2007-499с.
2.Леликов О.П. Основы расчета и проектирование деталей и узлов машин. Конспект лекций по курсу «Детали машин» .–Машиностроение, 2002-439с
3.Механика. Детали машин: учеб.пособие / Н.А. Дроздова, С.Ч. Туман, О.Н. Рябов.-Красноярск: СФУ; ИЦМиЗ, 2007-128с
4.Проектироване механических передач, : Учеб.пособие /Н.А. Дроздова, С.А. Косолапова, : ГАЦМиЗ –Красноярск, 2000-100с.
5.Чернавский С.А. Курсовое проектирование деталей машин: Машиностроение, 1987-414с.
Дата добавления: 2018-06-27; просмотров: 288; Мы поможем в написании вашей работы! |
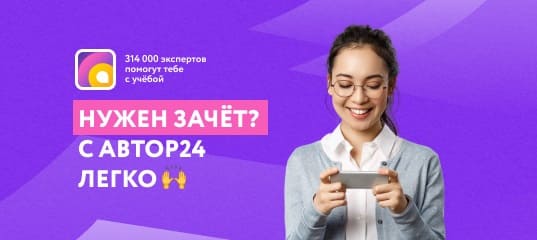
Мы поможем в написании ваших работ!