Монтаж компрессора и электродвигателя
Компрессор. После застывания бетона фундамента под компрессор дальнейшая последовательность работ должна быть следующей: удаляют шаблон; очищают поверхность фундамента от загрязнений; на поверхности фундамента делают насечку для разрушения цементной пленки, что обеспечивает хорошее схватывание с дальнейшей бетонной подливкой; в непосредственной близости от фундаментных болтов укладывают пакеты подкладок и клиньев, имеющих уклон 1:10 или 1:20 (рис. 4); резьбу фундаментных болтов очищают и смазывают; нижнюю часть компрессора промывают и очищают от грязи; устанавливают компрессор на пакеты подкладок и клиньев; подбивкой клиньев выставляют компрессор в двух взаимно перпендикулярных плоскостях по уровню, который размещают у вертикальных компрессоров на верхней плоскости блока цилиндров, у угловых — на фрезерованной площадке между цилиндрами.
Допустимая негоризонтальность компрессора вдоль оси коленчатого вала 0,1—0,2 мм, поперек — 0,2—0,3 мм на 1 м погонной длины.
Компрессор должен опираться на все пакеты равномерно. При отпущенных фундаментных болтах проверяют
зазор между пакетами и лапами компрессора: щуп 0,05 мм не должен проходить в этот зазор. При затянутых фундаментных болтах обстукивают пакеты молотком, дребезжащий звук свидетельствует о наличии зазора.
При затянутых, отпущенных и вновь затянутых болтах компрессор не должен менять своего положения более чем наполовину деления монтажного уровня. Далее подкладки и клинья сваривают в пакеты электросваркой.
Бетонная подливка делается для монолитного соединения компрессора с фундаментом с целью равномерной передачи фундаменту динамических нагрузок.
|
|
Бетонную массу полужидкой консистенции подливают под картер компрессора, установив вокруг фундамента опалубку, а сам фундамент покрывают метлахской плиткой.
Электродвигатель. Как правило, он устанавливается на одном фундаменте с компрессором, причем фундаментные болты должны быть заранее подготовлены.
При ременной передаче электродвигатель на фундаменте размещается на салазках, установка которых обеспечивает натяжение ремней и их замену; параллельность валов электродвигателя и компрессора; нахождение канавок обеих шкивов в одной плоскости.
Установку салазок производят совместно с закрепленным электродвигателем по струне, натянутой вдоль торцов, и уровню, установленному на шкиве электродвигателя (рис. 5). Торцовые поверхности шкивов компрессора и электродвигателя должны лежать в одной плоскости, поэтому расстояния от струны до крайних точек их торцов должны быть равны (a1=a2 = a3 = a4). Горизонтальность вала электродвигателей проверяется по уровню.
|
|
При муфтовом сцеплении добиваются соосности валов компрессора и электродвигателя.
Перед центровкой валы компрессора, электродвигателя и полумуфты должны быть проверены на биение индикатором (рис. 6): радиальное биение валов допускается не более 0,01—0,02 мм; радиальное и осевое биение полумуфт не должно превышать 0,03—0,04 мм на 100 мм радиуса полумуфты.
Центровку валов производят с помощью приспособления, показанного на рис. 7, а, б.
Радиальный зазор s и осевой зазор а устанавливают произвольно, замеряют щупом и замеры записывают в круговую диаграмму (s1 и а1 на рис. 7, в). После этого проворачивают валы совместно с приспособлением на 90 °, замеряют и записывают замеры s2 и а2, затем на 180 ° — s3 и а3 и на 270° — s4 и а4.
При соосности валов должно быть следующее равенство: s1=s2=s3=s4 и а1=а2=аз=а4.
Неравенство радиальных зазоров свидетельствует о параллельном смещении валов, неравенство осевых зазоров — о перекосе валов.
Разность радиальных зазоров s1 и s3 характеризует параллельное смещение валов в вертикальной плоскости.
Для его устранения изменяют толщину прокладок под всеми лапами электродвигателя на величину |s1 — s3|/2.
|
|
Разность радиальных зазоров s2 и s4 свидетельствует о параллельном смещении валов в горизонтальной плоскости. Для его устранения перемещают электродвигатель в горизонтальной плоскости на величину |s2 — s4|/2 в соответствующую сторону.
Разность осевых зазоров а1 и а2 свидетельствует о перекосе валов в вертикальной плоскости. Его устраня.ют изменением толщины прокладок под передними или задними лапами электродвигателя.
Разность осевых зазоров а2 и а4 характеризует перекос валов в горизонтальной плоскости. Его устраняют поворотом электродвигателя на определенный угол.
Общее правило:
вначале устраняют наибольшее отклонение от соосности;
все замеры зазоров в приспособлении производят только при полностью затянутых фундаментных болтах.
При установке электродвигателей с пальцевыми полумуфтами допускается следующая несоосность валов, мм: перекос на 1 м погонной длины — 0,2; параллельное смещение при диаметре муфт до 300 мм — 0,05, свыше 300 мм — 0,1.
В муфтах с резиновым эластичным элементом допуски на перекос и параллельное смещение валов составляют 0,3 мм.
Полумуфты соединяются для работы только в том положении, в котором производилась центровка.
Ревизия компрессора. Различают полную и неполную ревизию компрессора.
|
|
Неполная ревизия производится при соблюдении правил транспортировки и хранения оборудования не более 6 мес.
Она включает проверку качества сборки; состояния и чистоты шатунно-поршневой группы, системы смазки, КИП и автоматики; величины мертвого пространства и высоты подъема пластин всасывающих клапанов; легкости вращения коленчатого вала.
Полная ревизия производится при хранении компрессора более 6 мес или наличии у него повреждений. В этом случае компрессор разбирают на узлы и детали для проверки их исправности, чистоты поверхности и отсутствия коррозии.
Обкатка компрессора. Перед обкаткой должны быть полностью закончены все монтажные работы и произведена вентиляция компрессорного цеха.
Сначала кратковременным пуском проверяют направление вращения вала компрессора, которое должно соответствовать стрелке на передней крышке. При неправильном вращении на электродвигателе меняют местами два провода из трех.
Обкатка без клапанов и крышек цилиндров производится в три этапа, отличающихся между собой только длительностью: 5 мин, 30 мин и 2 ч. После второго и третьего этапов в картере компрессора заменяется масло. В процессе обкатки проверяют разность давлений масла в сальнике и картере, которая должна быть для низкооборотных компрессоров 0,05—0,15 МПа, для высокооборотных 0,2—0,3 МПа; нагрев отдельных частей компрессора; звук работы компрессора, который должен быть ровным, глухим, без стуков.
При отсутствии неполадок компрессор запускают в работу с установленными на место клапанами и крышками на 5 ч. При этом воздух засасывается из помещения цеха через марлевый фильтр, смоченный маслом.
Обкатка компрессоров серии П производится с закрепленными розетками всасывающих клапанов, удерживающими на месте гильзы цилиндров.
Монтаж агрегатов. В настоящее время большая часть холодильного оборудования выпускается в виде агрегатов с установленными по месту приборами автоматики и контроля.
Агрегаты поставляются в сборе и устанавливаются на заранее подготовленные фундаменты.
Требования к монтажу хладоновых агрегатов, устанавливаемых на животноводческих комплексах, предусматривают размещение агрегатов в сухих и чистых помещениях, объем которых должен быть не менее 1 м3 на 0,5 кг хладона-12, содержащегося в установке; кратность вентиляции помещения не менее 3; устройство специальных окон отвода теплоты конденсации при воздушном охлаждении конденсатора; возможность регулирования потока холодного воздуха и герметизации окон в зимнее время; ширину рабочего места у агрегата и щита управления не менее 1,2 м, ширину прохода 1,0 м; отсутствие нагревательных приборов в радиусе 1,5 м; установку ограждений у агрегатов в подсобных помещениях.
Агрегаты устанавливают на фундаментных плитах на настиле пола. Для уменьшения вибрации используются виброизоляторы (рис. 8).
Всасывающий и нагнетательный трубопроводы снабжают (в горизонтальной плоскости) компенсаторами (рис. 9).
Монтаж аппаратов
В целях повышения безопасности эксплуатации холодильной установки рекомендуется конденсаторы, линейные ресиверы и маслоотделители (аппараты высокого давления) с большим количеством хладагента размещать снаружи машинного отделения.
Это оборудование, как и ресиверы для хранения запаса хладагента, должны быть ограждены металлическим барьером с запирающимся входом. Ресиверы должны быть защищены навесом от солнечных лучей и осадков. Аппараты и сосуды, устанавливаемые в помещении, могут размещаться в компрессорном цехе или специальном помещении аппаратной, если оно имеет отдельный выход наружу. Проход между гладкой стеной и аппаратом должен быть не менее 0,8 м, но допускается установка аппаратов у стен без проходов. Расстояние между выступающими частями аппаратов должно быть не менее 1,0 м, а если этот проход является основным — 1,5 м.
При монтаже сосудов и аппаратов на кронштейнах или консольных балках последние должны быть заделаны в капитальную стену на глубину не менее 250 мм.
Допускается установка аппаратов на колоннах с помощью хомутов. Запрещается пробивать отверстия в колоннах для крепления оборудования.
Для монтажа аппаратов и дальнейшего обслуживания конденсаторов и циркуляционных ресиверов устраиваются металлические площадки с ограждением и лестницей. При длине площадки более 6 м лестниц должно быть две.
Площадки и лестницы должны иметь поручни и закраины. Высота поручней 1 м, закраин — не менее 0,15 м. Расстояние между стойками поручней не более 2 м.
Испытания аппаратов, сосудов и систем трубопроводов на прочность и плотность производятся по окончании монтажных работ и в сроки, предусмотренные «Правилами устройства и безопасной эксплуатации аммиачных холодильных установок».
Горизонтальные цилиндрические аппараты. Кожухотрубные испарители, горизонтальные кожухотрубные конденсаторы и горизонтальные ресиверы устанавливают на бетонных фундаментах в виде отдельных тумб строго горизонтально с допустимым уклоном 0,5 мм на 1 м погонной длины в сторону маслоотстойника.
Аппараты опираются на деревянные антисептированные брусья шириной не менее 200 мм с углублением по форме корпуса (рис. 10 и 11) и прикрепляются к фундаменту стальными поясами с резиновыми прокладками.
Низкотемпературные аппараты устанавливают на брусья толщиной не менее толщины теплоизоляции, а под
поясами размещают деревянные бруски длиной 50—100 мм и высотой, равной толщине изоляции, на расстоянии 250— 300 мм друг от друга по окружности (рис. 11).
Для очистки труб конденсаторов и испарителей от загрязнений расстояние между их торцовыми крышками и стенами должно составлять 0,8 м с одной стороны и 1,5—2,0 м с другой. При установке аппаратов в помещении для замены труб конденсаторов и испарителей устраивается «ложное окно» (в стене напротив крышки аппарата). Для этого в кладке здания оставляют проем, который заполняют теплоизоляционным материалом, зашивают досками и штукатурят. При ремонте аппаратов «ложное окно» вскрывают, а по окончании ремонта восстанавливают. По окончании работ по размещению аппаратов на них монтируют приборы автоматики и контроля, запорную арматуру, предохранительные клапаны.
Полость аппарата для хладагента продувают сжатым воздухом, испытание на прочность и плотность производят со снятыми крышками. При монтаже конденсаторно-ресиверного узла горизонтальный кожухотрубный конденсатор устанавливают на площадке над линейным ресивером. Размер площадки должен обеспечивать круговое обслуживание аппарата.
Вертикальные кожухотрубные конденсаторы. Аппараты устанавливают вне помещения на массивном фундаменте с приямком для слива воды. При изготовлении фундамента в бетон закладывают болты крепления нижнего фланца аппарата. Конденсатор устанавливают подъемным краном на пакеты подкладок и клиньев. Подбивкой клиньев аппарат выставляют строго вертикально с помощью отвесов, расположенных в двух взаимно перпендикулярных плоскостях. Для того чтобы исключить раскачивание отвесов ветром, их грузы опускают в емкость с водой или маслом. Вертикальное расположение аппарата вызвано винтообразным стеканием воды по его трубкам. Даже при незначительном наклоне аппарата вода не будет нормально омывать поверхность труб. По окончании выверки аппарата подкладки и клинья сваривают в пакеты и делают подливку фундамента.
Испарительные конденсаторы. Поставляются на монтаж в сборе и устанавливаются на площадке, размеры которой позволяют проводить круговое обслуживание этих аппаратов. ‘Высота площадки принимается с учетом размещения под ней линейных ресиверов. Для удобства обслуживания площадку оборудуют лестницей, а при верхнем расположении вентиляторов она устанавливается дополнительно между площадкой и верхней плоскостью аппарата.
После установки испарительного конденсатора к нему подключают циркуляционный насос и трубопроводы.
Наибольшее распространение находят испарительные конденсаторы типа TVKA и «Эвако» производства ВНР. Капле-отбойный слой этих аппаратов изготовлен из пластмассы, поэтому в районе установки аппаратов должны быть запрещены сварочные и другие работы с открытым пламенем. Электродвигатели вентиляторов заземляют. При установке аппарата на возвышении (например, на крыше здания) необходимо применение молниезащиты.
Панельные испарители. Поставляются в виде отдельных узлов, и их сборка производится в ходе монтажных работ.
Бак испарителя испытывается на герметичность наливом воды и устанавливается на бетонную плиту толщиной 300—400 мм (рис. 12), высота подземной части которой составляет 100—150 мм. Между фундаментом и баком укладывают деревянные антисептированные брусья либо железнодорожные шпалы и теплоизоляцию. Панельные секции устанавливают в баке строго горизонтально, по уровню. Боковые поверхности бака изолируют и штукатурят, налаживают работу мешалки.
Камерные приборы. Пристенные и потолочные батареи собирают из унифицированных секций (рис. 13) на месте монтажа.
Для аммиачных батарей используют секции из труб диаметром 38X2,5 мм, для хладоносителя — диаметром 38X3 мм. Трубы оребрены спирально навитыми ребрами из стальной ленты 1X45 мм с шагом ребер 20 и 30 мм. Характеристики секций представлены в табл. 6.
Суммарная длина шлангов батарей в насосных схемах не должна превышать 100—200 м. Установка батареи в камере производится с помощью закладных деталей, закрепленных в перекрытии при сооружении здания (рис. 14).
Шланги батарей размещают строго горизонтально по уровню.
Потолочные воздухоохладители поставляются для монтажа в сборе.Несущие конструкции аппаратов (швеллеры) соединяются со швеллерами закладных деталей. Горизонтальность установки аппаратов проверяют по гидростатическому уровню.
К месту монтажа аппаратов батареи и воздухоохладители поднимаются погрузчиками или другими грузоподъемными устройствами. Допустимый уклон шлангов не должен превышать 0,5 мм на 1 м погонной длины.
Для удаления талой воды во время оттаивания устанавливаются сливные трубы, на которых закрепляют нагревательные элементы типа ЭНГЛ-180. Нагревательный элемент представляет собой ленту из стеклонити, в основе которой находятся металлические нагревательные жилы из сплава с высоким удельным сопротивлением. Нагревательные элементы навивают на трубопровод спирально или прокладывают линейно, закрепляя на трубопроводе стеклолентой (например, лента ЛЭС-0,2Х20). На вертикальном участке сливного трубопровода нагреватели устанавливаются только спирально. При линейной прокладке нагреватели закрепляют на трубопроводе стеклолентой с шагом не более 0,5 м. После закрепления нагревателей трубопровод изолируют негорючей изоляцией и обшивают защитной металлической оболочкой. В местах значительных изгибов нагревателя (например, на фланцах) под него нужно подложить алюминиевую ленту толщиной 0,2—1,0 мм и шириной 40—80 мм во избежание местных перегревов.
По окончании установки все аппараты испытывают на прочность и плотность.
Монтаж насосов
Насосы для воды и хладоносителя. В системе охлаждения холодильной установки и в системе циркуляции хладоносителя применяются насосы типа «К» (рис. 15). Они поставляются в сборе с электродвигателями, установленными на чугунной плите или стальной раме. Монтируются они на бетонном фундаменте, масса которого должна быть больше массы насоса с электродвигателем в 5—6 раз. Несоосность их валов не должна превышать 0,3 мм.
Трубопроводы должны иметь собственные опоры (подвески кронштейны и т. д.) и не передавать усилии на насос. Обязательна установка задвижки и обратного клапана на напорном трубопроводе.
Для перекачивания хладоносителя устанавливаются насосы судового исполнения. Необходимо предусмотреть сбор хладоносителя в случае протекания его через сальник.
Насосы для хладагентов. Герметичные насосы для хладагента типа ЦГ для хладагентов входят в состав насосно-циркуляционных схем.
Схема монтажа насоса предусматривает, что эти насосы устанавливают в непосредственной близости от циркуляционного ресивера. Трубопровод между стояком ресивера и насосом не должен иметь поворотов, диаметр трубопровода должен соответствовать размеру всасывающего патрубка. На всасывающей линии насоса должны быть установлены задвижка (или вентиль) и фильтр, сетку которого после очистки аммиака от загрязнений удаляют. Корпус фильтра используют для сбора масла.
Расстояние от минимального рабочего уровня жидкости в циркуляционном ресивере до оси насоса должно быть не менее его допустимого кавитационного запаса, указанного в технической характеристике. Ориентировочно это расстояние Н должно быть не менее 1,8 м. Схема включения насоса изображена на рис. 16.
При недостаточной высоте помещения компрессорного цеха насосы могут быть установлены в открытом приямке, имеющем ограждение высотой не менее 1,1 м и две лестницы, а при глубине приямка более 2 м вместо одной из лестниц должен быть выход непосредственно наружу на уровне прилегающей территории.
Стояк циркуляционного ресивера диаметром 250—300 мм опускают в приямок. Насос подключают к стояку выше штуцера для выпуска масла на 300—400 мм.
Трубопровод отвода жидкости от задней крышки насоса подсоединяется ко всасывающей линии на расстоянии 400—500 мм от всасывающего патрубка насоса. Длина этого трубопровода не должна превышать 2,0—2,5 м при диаметре труб 38X2,5 мм. Запорная арматура на нем не устанавливается, а в случае установки — пломбируется в открытом положении. Для удаления пара из всасывающего трубопровода и задней крышки устраиваются линии, соединяющиеся с паровой частью циркуляционного ресивера.
Схема монтажа насоса, описанная выше, описывает установку. Насос комплектуется приборами автоматики. Поплавковое реле уровня (ПРУ-5), предназначенное для контроля наличия жидкости в полости охлаждения электродвигателя, устанавливается выше оси насоса ЦГ на 200 мм.
По окончании испытаний все трубопроводы изолируют.
Заполнение системы.
Хладоноситель готовят в специальном стальном, прямоугольной формы, открытом сверху баке-концентраторе, который обычно располагают в непосредственной близости от компрессорного цеха. В нижней части бака устанавливается стальная сетка на расстоянии 100—150 мм от дна. Сетка должна быть легкосъемной для периодического удаления со дна загрязнений. Патрубок забора хладоносителя должен располагаться выше сетки. В нижней точке бака устанавливают запорный вентиль или задвижку для слива загрязненного хладоносителя.
Для удобства выполнения работ по приготовлению хладоносителя расчетной концентрации следует иметь весы для взвешивания соли и мерную линейку или смотровое стекло для контроля заполнения бака водой.
С целью ускорения растворения соли к нижней части бака подсоединяют трубопроводы сжатого воздуха или котельного пара. Барботаж воздуха или пара обеспечивает активное перемешивание и растворение соли.
Для уменьшения коррозийной активности хладоносителя предпочтение отдается закрытым системам, которые оборудуются кожухотрубными испарителями. Кроме того, к приготовляемому хладоносителю добавляют в качестве пассиваторов хромат натрия Na2CrО4 и едкий натр NaOH для создания слабощелочной реакции (рН 7,5—8,5).
На 1 м³ хладоносителя добавляют Na2CrО4 в следующем количестве: NaCl — 3,2 кг; СаСl2 — 1,6 кг.
К каждым 10 кг хромата натрия надо добавить еще 2,7 кг едкого натра. Щелочность раствора определяют по изменению цвета бумажек индикатора рН. При добавлении хромата натрия следует соблюдать осторожность, поскольку он разрушающе действует на кожу.
Для повышения щелочности раствора хлористого кальция можно добавить 1,6 кг свежегашеной извести на 1 м³ хладоносителя.
Для понижения щелочности через хладоноситель пропускают углекислый газ из баллона.
В баке-концентраторе соль должна раствориться полностью.
Готовый хладоноситель проверяют на соответствие концентрации расчету и числу рН, а затем отстаивают для оседания загрязнений и с помощью насоса закачивают в систему.
По окончании заполнения системы, когда уровень в расширительном баке составит не менее 50—80 %, через специальные краны и пробки на испарителе, рассольных батареях и коллекторах распределения хладоносителя выпускают воздух. В открытых системах об окончании заполнения судят по уровню хладоносителя в испарителе.
Не допускается составление хладоносителя из смеси различных солей или добавление в систему раствора другой соли во избежание выпадения в осадок «двойной соли».
В настоящее время разработан ингибированный хладоносителькальтозин на основе водного раствора хлористого кальция. По теплофизическим свойствам он близок к водному раствору хлористого кальция, а по защитным превосходит известные хладоносители с ингибиторами.
3.Аэродинамический расчет системы воздуховодов.
Виды воздуховодов
В системах вентиляции применяются воздуховоды: металлические, металлопластиковые, неметаллические.
Воздуховоды могут быть гибкими, полугибкими, теплоизолированными, звукопоглощающими.
По форме воздуховоды бывают круглого и прямоугольного сечения.
Металлические воздуховоды изготавливаются из листовой кровельной, оцинкованной или нержавеющей стали на заводах или заготовительных мастерских Предпочтение следует отдавать круглым воздуховодам из за меньшего аэродинамического сопротивления, расхода металла и трудоемкости при изготовлении Преимущество прямоугольных воздуховодов, в том, что при открытых прокладках они лучше вписываются в интерьер общественных зданий, проще размещаются в пространстве с ограниченной высотой (например, за подшивным потолком)
Металлопластиковые воздуховоды изготавливаются из листовых панелей, которые представляют собой слой вспененного пластика толщиной 20 мм, проложенный между двумя слоями термообработанного гофрированного алюминия Эти воздуховоды легки, обладают высокой прочностью и теплоизоляционной способностью (коэффициент теплопроводности 1=0,019 Вт/(м °С)), имеют хороший внешний вид, могут изготавливаться непосредственно на объекте
Гибкие воздуховоды изготавливаются из многослойной ламинированной алюминиевой фольги и пленки из полиэфира Форму воздуховодам придает специальный стальной проволочный каркас Воздуховоды легки, термостойки, упрощают монтаж Однако создают большое аэродинамическое сопротивление Применяются в качестве присоединительных воздуховодов небольшой длины
Дата добавления: 2018-06-27; просмотров: 3437; Мы поможем в написании вашей работы! |
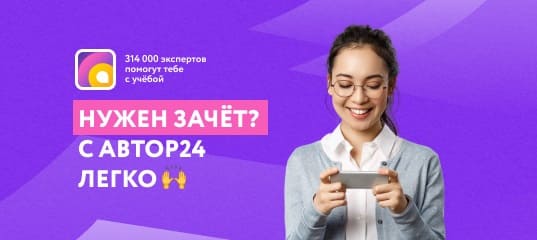
Мы поможем в написании ваших работ!