Узел испарительной системы непосредственного охлаждения
Билет №16
1.Для того чтобы оценить потери, вносимые регулирующим вентилем, рассмотрим цикл идеальной паровой холодильной компрессионной машины с расширителем и сравним его с циклом машины, которая имеет регулирующий вентиль. Условимся, что все другие потери отсутствуют, т. е. все остальные процессы, кроме дросселирования, обратимы.
На (рис. 1, а) показана принципиальная схема идеальной холодильной машины, состоящей из конденсатора, компрессора, расширительного цилиндра (детандера) и испарителя. Цикл такой машины происходит в области влажного пара между пограничными кривыми х = 0 и х = 1 (рис. 1, б).
В идеальной холодильной машине детандер предназначен для того, чтобы подготовить хладагент к восприятию тепла при низкой температуре, т. е. охладить его. Это достигается понижением энергии хладагента за счет дополнительной работы lp. После совершения такой работы в детандере жидкий хладагент поступает в испаритель, где кипит при постоянной температуре и постоянном давлении р0 (линия 4–1). Во время кипения хладагент отнимает тепло q0 от охлаждаемой среды. Из испарителя компрессор засасывает влажный пар хладагента и сжимает его адабатически (линия 1–2) до давления рк, на что затрачивается работа l. Температура пара при этом повышается до Тк.
Холодопроизводительность машины определяется площадью α – 1 – 4 – β.
Рис. 1 – Схема идеальной холодильной машины и ее цикл в координатах Т – s
|
|
Сухой насыщенный пар нагнетается компрессором в конденсатор, где конденсируется при постоянном давлении рк и температуре Тк (линия 2–3), отдавая охлаждающей среде (воде или воздуху) тепло q0 полученное в испарителе, и тепло, эквивалентное работе компрессора l.
Из конденсатора жидкий хладагент поступает в детандер. Здесь происходит его расширение при постоянной энтропии (линия 3–4), и работа l р, полученная за счет внутренней энергии, используется как вспомогательная для привода компрессора. В результате расширения температура хладагента понижается до T0 а давление – до р0. С этими параметрами он снова поступает в испаритель.
Таким образом, цикл, осуществляемый идеальной холодильной машиной в области влажного пара, совпадает с обратным циклом Карно. Но современные машины работают с отклонением от него, так как детандер заменен в них регулирующим вентилем РВ (рис. 2, а).
В компрессионных холодильных машинах детандер (расширительный цилиндр) не ставят из-за трудности изготовления цилиндра малых размеров с весьма ранней отсечкой. Отсечка определяется объемом жидкого хладагента, поступающего из конденсатора или переохладителя в цилиндр.
|
|
С заменой детандера регулирующим вентилем адиабатическое расширение заменяется дросселированием. При этом энтальпия в точках 3 и 4 одинаковая. Под процессом дросселирования понимают снижение давления жидкости или пара (газа) во время прохождения через суженное сечение регулирующего вентиля при отсутствии теплообмена с окружающей средой и без осуществления внешней работы. Дросселирование является необратимым процессом, так как тепло, развитое трением и завихрением в потоке, не может быть полностью превращено обратно в другой вид энергии. Это тепло подводится к хладагенту и вызывает бесполезное парообразование. При этом полезная холодопроизводительность каждого килограмма жидкого хладагента снижается.
Процесс в регулирующем вентиле идет не по адиабате 3–4, (рис. 2, б), а по изоэнтальпии 3–4ʹ. Как видно из диаграммы, при регулирующем вентиле не только теряется работа lp, полученная в детандере и изображенная площадью 5–3–4, но и уменьшается холодопроизводительность на величину, равную площади β – 4 – 4ʹ – γ.
Рис. 2 – Схема и циклы холодильной машины с регулирующим вентилем
Дросселирование сопровождается понижением температуры хладагента. На диаграмме lg р – i (рис. 2, в) этот процесс показан вертикальной прямой, т. е. линией 3–4ʹ постоянного теплосодержания. Конец дросселирования определяется точкой 4ʹ. Отрезок 3–4 представляет собой перепад давлений рк – р0 в регулирующем вентиле.
|
|
Работа, которую мог бы произвести хладагент в детандере, является потерянной, и количество затрачиваемой внешней энергии определяется полной работой компрессора, то есть без вычета из нее работы детандера. Тепловая энергия хладагента, которая могла быть использована в детандере, переносится за регулирующий вентиль и расходуется на кипение, в результате чего снижается холодопроизводительность.
Величина потерь холодопроизводительности зависит от рода и физических свойств хладагента, теплоемкости жидкости, теплоты парообразования и критических параметров. Для аммиака потери от дросселирования несколько меньше, чем для хладона-12. Кроме того, потери при дросселировании зависят от режима работы холодильной машины; они тем больше, чем больше разность между температурами конденсации и кипения.
Потери от дросселирования можно сократить, понизив температуру жидкого хладагента перед регулирующим вентилем ниже температуры конденсации, что является вторым отклонением от обратного цикла Карно. Этот процесс условно называется переохлаждением жидкости и достигается применением более холодной воды в специальных аппаратах – переохладителях. Значительное переохлаждение почти до температуры выходящей охлаждающей воды с отводом тепла qп возможно в противоточном переохладителе, устанавливаемом после конденсатора (рис. 3, а). Обозначения параметров на (рис. 3) такие же, как на (рис. 1).
|
|
Рис. 3 – Схема и циклы холодильной машины с переохлаждением
НЕПОНЯТНЫЙ ВОПРОС!!!!!!
Работа холодильной машины при низких температурах окружающего воздуха связана с рядом проблем, среди которых выделим пять основных:
1. Уменьшение холодо производительности в режиме «охлаждение».
Из-за снижения температуры воздуха, обдувающего конденсатор наружного блока, уменьшается температура и давление конденсации. Как следствие, уменьшается расход жидкого хладагента, поступающего в испаритель через регулятор расхода.
В результате уменьшения расхода хладагента падает давление испарения и возможно отключение холодильной машины при срабатывании устройств защиты по низкому давлению.
Особенно заметно снижение расхода хладагента и уменьшение холодо производительности в кондиционерах с капиллярной трубкой, которой оснащаются практически все бытовые кондиционеры.
В кондиционерах, оборудованных терморегулирующим вентилем, открытие ТРВ до какого-то момента компенсирует падение давления конденсации, но после того, как ТРВ откроется полностью, эффект будет таким же, как и в случае с капиллярной трубкой.
Для увеличения давления конденсации при низкой температуре окружающего воздуха принимаются следующие технические меры:
- уменьшается скорость вращения вентилятора (плавно или ступенчато) обдува конденсатора вплоть до полной его остановки;
- охлаждающий воздух перепускается мимо конденсатора или полностью перекрывается;
- перед конденсатором устанавливается специальный клапан регулирования давления конденсации, который обводит большую часть хладагента мимо конденсатора.
Такое техническое решение позволило, например, в прецизионных кондиционерах марки UNIFLAIR сохранить холодо производительность до температуры наружного воздуха минус 35ºС.
Эффективной мерой сохранения холодо производительности блоков с центробежными вентиляторами, установленных в помещении (подвале, на чердаке и т.д.), является выброс выходящего из конденсатора воздуха не на улицу, а в это же помещение. Для этого в воздуховоде отвода воздуха от конденсатора устанавливаются дополнительные воздушные заслонки с электроприводами пропорционального регулирования, которые перепускают часть или полный расход тёплого воздуха, идущего на охлаждение конденсатора.
2. Уменьшение тепло производительности в режиме «обогрева».
В режиме «обогрева» происходит реверсирование цикла и теплообменник наружного блока выполняет роль испарителя.
При низкой температуре наружного воздуха уменьшается перепад между температурой кипящего хладагента и температурой окружающего воздуха. Количество передаваемого тепла, необходимого для кипения хладагента — снижается и соответственно ухудшаются условия кипения хладагента.
Как следствие, снижается давление всасывания, падает производительность компрессора. Одновременно снижается давление и температура конденсации, что приводит к уменьшению тепло производительности кондиционера.
В этих условиях необходимо максимально увеличить обдув испарителя.
Обычно это достигается увеличением скорости вращения вентилятора наружного блока.
По мере приближения температуры наружного воздуха к температуре кипения хладагента тепло производительность кондиционера снижается. При достижении температуры наружного воздуха минус 20 — 22 ºС тепло производительность снизится на 20 — 25%.
3. Обмерзание теплообменника наружного блока при длительной работе в режиме «обогрева».
При работе кондиционера в режиме «обогрева» происходит охлаждение наружного воздуха, обдувающего кондиционер.
При определённом соотношении температурных и влажностных параметров атмосферного воздуха возможно появление конденсата на пластинах теплообменника наружного блока, образование льда и обмерзание теплообменника.
Образовавшийся лёд не только ухудшает характеристики кондиционера, уменьшая теплопередачу, но и может физически повредить наружный блок, что может привести к довольно дорогостоящему ремонту.
Поэтому предотвращение обмерзания и своевременному оттаиванию теплообменника наружного блока уделяется самое большое внимание.
Для удаления льда и снеговой шубы с теплообменника наружного блока кондиционер кратковременно переводят в режим «охлаждение». Теплообменник прогревается горячим конденсирующимся хладагентом, накопившийся лёд растапливается, и наружный блок вновь готов к эксплуатации. На время оттаивания теплообменника вентиляторы наружного и внутреннего блока останавливаются.
Алгоритм системы оттаивания должен быть построен таким образом, чтобы, с одной стороны, — режим оттаивания включался как можно реже и на минимальное время, с другой стороны, чтобы не возникало накопление льда на теплообменнике.
4. Возможность повреждения компрессора при запуске.
При низких температурах наружного воздуха жидкий хладагент может растворяться в масле компрессора. Поэтому во время остановки компрессора возможно попадание хладагента в масло, находящееся в картере компрессора.
Во время пуска поршневого компрессора при движении поршня вверх в картере возникает разряжение и может происходить вскипание хладагента. Одновременно вспенивается масло и происходит его выброс в выходной трубопровод.
Для исключения этого на компрессорах средней и большой мощности обязательно устанавливаются обогреватели картера, предотвращающие накопление жидкого хладагента в масле при выключенном компрессоре.
В компрессорах роторного типа, не имеющих масляного картера, эта проблема менее остра, чем в поршневых компрессорах. Поэтому на компрессорах SCROLL малой мощности (примерно до 8 — 10 кВт) отсутствие обогревателя картера практически не влияет на работоспособность компрессора.
5. Опасность попадания жидкого хладагента в компрессор при работе в режиме «обогрева».
Ухудшение условий кипения хладагента в теплообменнике наружного блока при работе кондиционера в режиме«охлаждение» может привести к «проскоку» жидкого хладагента и попаданию его в компрессор.
Возникающий при этом гидравлический удар может повредить компрессор.
В связи с этим приходится устанавливать дополнительный ресивер (отделитель жидкости) перед компрессором на линии всасывания.
Узел испарительной системы непосредственного охлаждения
В отличие от компрессорного и конденсаторного узлов узел испарительной системы имеет несколько принципиально разных решений. В основу каждого из вариантов положен способ подачи хладагента в испарительную систему, а именно: подача хладагента под действием разности давлений конденсации и кипения; подача под напором столба жидкости; подача под напором, создаваемым насосом. Таким образом, способ подачи определяет и название схемы холодильной установки непосредственного охлаждения. Первых Два способа подачи образуют группу безнасосных схем, при последнем способе подачи схемы называются насосными. Классификация схем холодильных установок с непосредственным и рассольным охлаждением представлена на рис. 67.
Безнасосные схемы разделяются на:
а — прямоточные без отделителя жидкости;
б — с нижним расположением отделителя жидкости;
в — с верхним расположением отделителя жидкости.
Схемы а и б работают под действием перепада давлений кипения и конденсации, а схема в — под напором столба жидкого хладагента.
В насосно-циркуляционных схемах различают варианты нижней или верхней подачи хладагента в охлаждающие приборы.
Современные компаундные схемы являются также разновидностью насосных схем.
Схемы рассольного охлаждения различают по типу используемых испарителей: открытых (типа панельных, оросительных) или закрытых (типа кожухотрубных).
Схема действующей холодильной установки может быть выполнена по одному из приведенных в классификации вариантов или представлять собой сочетание в одной схеме сразу нескольких вариантов. Например, одна и та же схема может иметь варианты безнасосной и насосной подачи хладагента в охлаждающие приборы или иметь параллельно работающие объекты с непосредственным и рассольным охлаждением. Каждому из предложенных вариантов решения испарительного узла присущи свои особенности эксплуатации, достоинства и недостатки, которые будут рассмотрены ниже.
Сложность создания оптимального решения испарительного узла заключается в том, что он должен удовлетворять двум трудно совместимым требованиям: с одной стороны, обеспечивать работу компрессора «сухим ходом», а с другой — обеспечивать хорошую заполняемость испарителя жидким хладагентом. Первое требование необходимо для безопасной работы компрессора, второе — для интенсивности теплообмена. Решение этой задачи усложняется еще и тем, что испарители работают в условиях переменных тепловых нагрузок, связанных с охлаждением продукта, загрузкой камер теплым продуктом, включением отепленного охлаждаемого объекта и т. п., что вызывает изменение интенсивности и характера процесса кипения хладагента и требует соответственно изменять количество жидкости, подаваемой в испарители. При большом количестве объектов охлаждения это довольно сложная задача, так как во всасывающей магистрали, идущей к компрессору, смешивается пар хладагента, поступающий из разных камер. Обслуживающий персонал контролирует состояние пара перед компрессором и при поступлении в компрессор влажного или сильно перегретого пара, но практически очень трудно определить, на какой конкретно из объектов охлаждения надо воздействовать, чтобы обеспечить и оптимальное заполнение испарителя и нормальный перегрев пара на всасывании.
Постоянный перегрев пара на выходе из испарителя, находящийся в оптимальных пределах независимо от теп-лопритоков, является признаком правильной подачи хладагента.
Другой важной характеристикой систем непосредственного охлаждения является кратность циркуляции хладагента в испарительной системе: n = Ga′ / Ga , где Ga′ — количество холодильного агента, подаваемого в охлаждающие приборы, кг/с; Ga — количество холодильного агента, испаряющегося в них, кг/с.
Масса Ga′ зависит от пропускной способности устройств регулирования подачи хладагента, а масса Ga эквивалентна тепловой нагрузке на испаритель в данный момент времени. Для обеспечения «сухого хода» компрессора желательно, чтобы весь холодильный агент, подаваемый в испаритель, превращался в сухой пар, т. е. Ga′ = Ga , а n = 1. Практически трудно обеспечить точное регулирование подачи его в испаритель в соответствии с постоянно изменяющейся тепловой нагрузкой, особенно при работе на несколько охлаждаемых объектов. Поэтому в действительности в камерных приборах имеет место либо избыток хладагента, т. е. n > 1, что вызывает угрозу работы компрессора «влажным ходом», либо недостаток хладагента, т. е. n < 1. И то и другое является отрицательными факторами, но даже при идеально отрегулированной подаче, когда n = 1 , хорошо выполняется только требование безопасной работы компрессора, а заполнение испарителя жидким хладагентом остается недостаточным, а это значит, что не вся поверхность охлаждающих приборов участвует в интенсивном теплообмене. Поэтому идеальным можно считать такой вариант работы испарительного узла, когда в камерных приборах поддерживается высокая кратность циркуляции хладагента n = 5 — 10 , но при этом обеспечивается «сухой ход» компрессора. При высоких значениях кратности циркуляции увеличивается эффект саморегулирования подачи, что освобождает от необходимости вмешиваться в раздачу жидкости по объектам охлаждения, улучшается и теплопередача в охлаждающих приборах. Резкое изменение тепловой нагрузки при такой цикруляции значительно меньше сказывается на заполнении приборов, что создает более безопасные условия работы системы.
Системам непосредственного охлаждения при некоторых схемных решениях свойственно явление отрицательного влияния гидростатического столба жидкого хладагента на температуру кипения. Давление, соответствующее кипению хладагента на некоторой глубине от его поверхности, составляет P0′ = P0 + h ρag , где P0 — давление кипения на поверхности, МПа; h — глубина от поверхности, м; ρa — плотность жидкого холодильного агента, кг/м3; g — ускорение свободного падения, Н/кг. Давление столба жидкости увеличивает P0 и соответственно t0 , что приводит к повышению температуры охлаждаемого объекта. Для поддержания нормального режима в объекте охлаждения приходится работать при более низких параметрах кипения, что вызывает дополнительный расход электроэнергии и снижение холодопроиз-водительности компрессоров. Следовательно, в схемных решениях нужно избегать образования гидростатических столбов жидкости.
Безнасосная прямоточная схема без отделителя жидкости. Применяется лишь на малых холодильных установках, преимущественно хладоновых. Применение хладона в качестве хладагента предъявляет определенные требования как к схеме испарительного узла, так и ко всей установке в целом, а именно:
регулирование подачи хладагента в приборы охлаждения в соответствии с тепловой нагрузкой;
защиту дроссельных устройств от замерзания в них влаги;
защиту компрессоров от попадания в них жидкого хладагента;
обеспечение возврата масла из испарителя в компрессор.
На рис. 68-а представлена схема хладоновой установки. Подача хладона в испарительную систему осуществляется под действием перепада давлений конденсации и кипения. Точное дозирование подачи жидкости в каждый прибор охлаждения (или группу параллельно включенных приборов) осуществляется с помощью терморегулирующего вентиля (ТРВ), который автоматически регулирует подачу хладагента в испаритель в зависимости от степени перегрева пара на всасывающей стороне, а это в свою очередь зависит от величины тепловой нагрузки. Термочувствительный патрон ТРВ укрепляют на выходе пара из прибора охлаждения.
Так как хладоны не растворимы в воде, то для защиты дроссельных устройств от образования в них ледяных пробок перед ними устанавливают фильтры-осушители, которые поглощают влагу.
Чтобы исключить возможность попадания жидкого хладона (или большого количества масла) в компрессор, целесообразно установить регенеративный теплообменник, особенно при использовании испарителей непосредственного охлаждения с подачей хладона через ТРВ. Во время простоя установки ТРВ часто не закрываются достаточно плотно, в результате чего жидкий хладагент попадает в испаритель. Если нет регенеративного теплообменника, то при пуске компрессора избыточное количество жидкости выбрасывается во всасывающий трубопровод и может попасть в компрессор. Теплообменник предназначен также для сбора и испарения жидкости, попадающей во всасывающий трубопровод из-за избыточной подачи хладагента РВ при пуске или внезапном изменении нагрузки на испаритель.
Для предотвращения перетекания жидкого хладагента через ТРВ при остановке на жидкостной линии перед ТРВ устанавливается соленоидный вентиль, сблокированный с магнитным пускателем компрессора. При пуске компрессора соленоидный вентиль открывается, а при остановке — закрывается.
На хладоновых установках непосредственного охлаждения используют верхнюю, нижнюю или комбинированную подачи жидкости в охлаждающие приборы. На рис. 68-а показан вариант верхней подачи в две последовательно соединенные испарительные батареи, что облегчает возврат масла из испарителей. При этом всасывающий трубопровод монтируют с уклоном его горизонтальных участков на 1—2 % в сторону компрессора, который устанавливают ниже уровня расположения приборов охлаждения. Недостатком такой схемы является стекание жидкого хладагента из батарей во всасывающий трубопровод при остановке компрессора. Для устранения этого недостатка на выходе из батарей предусматривают вертикальный стояк с маслоподъемной петлей (пунктирная линия на рис. 68, а), после которого трубопровод монтируют с уклоном к компрессору. При нижней подаче жидкости батареи лучше заполняются хладагентом и работают более эффективно, однако возврат масла в этом случае бывает затруднен.
При последовательном соединении более двух батарей можно применить комбинированный способ питания (рис. 68, б), когда в первую по ходу батарею хладагент подается снизу, а в следующие батареи — сверху.
В некоторых схемах компрессор может оказаться расположенным выше охлаждающего прибора (рис. 68, в), тогда для обеспечения возврата масла необходимо на всасывающем трубопроводе выполнить маслоподъемную петлю. Для присоединения вертикальной трубы к верхнему горизонтальному участку линии применяют перевернутую петлю, чтобы масло не стекало обратно. Если монтировать масло-подъемную петлю нецелесообразно, то чувствительный баллон ТРВ крепят к вертикальной трубе примерно на 0,3 — 0,5 м выше горизонтального участка (пунктирная линия на рисунке 68, в), так как скопление жидкости перед вертикальным участком может искажать действительное состояние пара на выходе из испарителя, а следовательно, и работу ТРВ. Все горизонтальные участки всасывающего трубопровода также монтируют с уклоном к компрессору. Всасывающий трубопровод подводят к компрессору сверху.
Безнасосная схема с нижним расположением отделителя жидкости.Подача жидкого хладагента в охлаждающие устройства осуществляется под действием разницы давлений конденсации и кипения непосредственно от регулирующей станции. Эта схема характерна для разветвленных аммиачных систем с несколькими объектами охлаждения. Поэтому согласно требованиям правил безопасной эксплуатации аммиачных установок на всасывающей стороне компрессора должен быть предусмотрен защитный комплекс с отделителем жидкости.
В качестве защитного комплекса используются следующие основные варианты:
отделитель жидкости со сливом жидкого хладагента в один из двух попеременно подключаемых горизонтальных защитных ресиверов типа РД;
два попеременно подключаемых вертикальных защитных ресивера типа РДВА, совмещающих функции отделителя жидкости;
два попеременно работающих горизонтальных защитных ресивера типа РЦЗ, совмещающих функции отделителя жидкости.
Во всех этих вариантах недопустимо использование защитных ресиверов одновременно как дренажных. Для оттаивания охлаждающих приборов следует предусматривать отдельный дренажный ресивер. Однако для небольших установок, если вместимость расчетной защитной емкости не превышает 1,5 м3 , допускается установка одного защитного ресивера при обеспечении самостоятельного слива из него жидкости в ниже расположенный дренажный ресивер.
На рис. 69 представлен испарительный узел безнасосной аммиачной схемы с нижним расположением отделителя жидкости и защитным комплексом по первому варианту. Отделитель жидкости (или сосуд, совмещающий его функции) располагается на любом уровне относительно охлаждающих приборов, но обязательно выше защитных ресиверов. Подача жидкости в охлаждающие приборы осуществляется от распределительной станции, причем регулирующие вентили располагаются непосредственно перед приборами. Для регулирования заполнения приборов могут быть применены ТРВ, которые контролируют перегрев пара на выходе из батарей. Соленоидные вентили, установленные перед ТРВ, управляются от реле температуры, установленных в камерах, и при достижении требуемой температуры в камере закрываются, прекращая подачу жидкого хладагента в охлаждающие приборы. Пар хладагента выходит из охлаждающих приборов и поступает в отделитель жидкости, предназначенный для отделения от всасываемого пара той жидкости, которая может быть выброшена из охлаждающих приборов при колебаниях тепловой нагрузки. Из отделителя жидкости сухой пар отсасывается компрессором, а отделенная жидкость сливается в один из защитных ресиверов. Для обеспечения бесперебойности и безопасности работы установки на каждую температуру кипения аммиака устанавливают по две защитные емкости, работающие попеременно. Пока один из защитных ресиверов, например № 1, заполняется жидкостью через ОЖ (вентили 1′ , 2′ закрыты; вентили 3′ , 4′ открыты), другой ресивер (№ 2) опорожняется за счет выдавливания из него жидкости на распределительную станцию парами высокого давления (вентили 5′ , 6′ , 9′закрыты; вентили 7′ , 8′ открыты). После заполнения рабочего ресивера № 1 до предельно допустимого уровня (80%) происходит переключение ресиверов. Дренажный ресивер после оттаивания камерных приборов опорожняется так же, как и защитные.
Требования и рекомендации для эффективной и безопасной эксплуатации безнасосных аммиачных схем с нижним расположением отделителя жидкости следующие:
подача в охлаждающие приборы должна быть отрегулирована таким образом, чтобы при нормальной тепловой нагрузке из батарей выходил сухой пар, т. е. вся жидкость испарялась бы в батареях, кратность циркуляции n = 1 ;
в качестве охлаждающих батарей требуется применять батареи коллекторного типа, так как из них меньше вероятность выброса жидкости;
применять только нижнюю подачу в охлаждающие приборы, так как в противном случае жидкость будет быстро сливаться из батарей и они могут оказаться пустыми;
наличие жидкого хладагента в отделителе жидкости недопустимо, при ее появлении компрессоры должны быть остановлены по сигналу от аварийных датчиков уровня.
Рассмотренной безнасосной схеме присущи недостатки, устранить которые либо трудно, либо практически невозможно, а именно:
большое количество ручных регулирующих и запорных устройств и вследствие этого трудность регулирования подачи в охладающие приборы;
использование аммиачных терморегулирующих вентилей для этой цели не дает хороших результатов из-за их низкой надежности в работе;
небольшая кратность циркуляции холодильного агента и невозможность ее увеличения из-за опасности залить компрессор;
большое количество различных переключений на защитных емкостях, что может вызвать ошибочные действия обслуживающего персонала и аварийные ситуации;
значительное замасливание охлаждающих приборов вследствие нижней подачи и низкой скорости движения хладагента, которое снижает коэффициент теплопередачи.
Безнасосная схема с верхним расположением отделителя жидкости.Испарительная система питается под действием столба жидкости, например Н1(рис. 70). Отделитель жидкости (ОЖ) располагается на 3 — 5 м выше всех верхних охлаждающих приборов. Холодильный агент после регулирующего вентиля направляется в отделитель жидкости, где происходит разделение парожидкостной смеси. Сухой насыщенный пар отсасывается компрессором, а жидкость, называемая первичной, через коллектор поступает в приборы охлаждения. Правильное распределение жидкости по объектам осуществляется регулированием степени открытия вентилей на коллекторе и на жидкостных этажных коллекторах ЖК , которое проводится при первоначальной настройке системы. Благодаря тому, что отделитель жидкости находится выше охлаждающих приборов, есть возможность рециркуляции жидкости, увлеченной паром из испарительной системы при колебаниях тепловой нагрузки и отделенной от пара в ОЖ. Эту жидкость называют вторичной, и ее наличие позволяет повысить кратность циркуляции n > 1 , а значит, улучшить саморегулирование системы и повысить внутренний теплообмен в приборах охлаждения. Несмотря на улучшение циркуляции и распределения холодильного агента данная схема обладает рядом серьезных недостатков:
остается большая опасность возникновения «влажного хода» и гидравлического удара из-за переполнения ОЖ вторичной жидкостью, поступающей из испарительной системы, так как регулирующим вентилем можно воздействовать только на подачу первичной жидкости из линейного ресивера, а вторичная жидкость оказывается неуправляемой;
совмещение отделителем жидкости функций питающего и защитного сосудов, первое требует поддержание в нем уровня жидкости, а второе — категорическое ее отсутствие;
вредное влияние гидростатического столба жидкости на повышение температуры кипения, что приводит к необходимости снижать рабочие параметры кипения, а иногда и к невозможности выйти на заданный температурный режим;
большая вместимость системы по хладагенту и трудность его распределения по объектам охлаждения.
Ниже приведены требования и рекомендации для эффективной и безопасной эксплуатации данной схемы:
для повышения безопасности работы компрессоров необходимо предусмотреть в машинном отделении на линии всасывания компрессоров дополнительный защитный комплекс, состоящий из двух или более защитных ресиверов типа РДВ или РЦЗ, либо ОЖ со сливом в защитные ресиверы типа РД (по аналогии с защитным комплексом схемы с нижним расположением ОЖ);
при эксплуатации существующих схем с верхним ОЖ и отсутствии защитного комплекса на всасывании компрессоров запрещается поддержание уровня жидкости в питающем ОЖ;
при появлении жидкости в ОЖ компрессор должен быть остановлен;
для снижения вредного влияния гидростатического столба жидкости рекомендуется применять данную схему для небольшого числа объектов охлаждения, находящихся на уровне одного этажа.
Анализ всех рассмотренных безнасосных схем показывает значительное число присущих им недостатков и ограниченные возможности их совершенствования.
Насосно-циркуляционная схема подачи хладагента. В насосно-циркуляционных схемах жидкий холодильный агент подается в приборы охлаждения насосом, подача которого выбирается такой, чтобы кратность циркуляции хладагента была не менее 4—5 в период расчетной нагрузки. Это увеличивает эффект саморегулирования раздачи жидкости по объектам охлаждения, значительно уменьшает влияние переменного заполнения охлаждающих приборов при изменении тепловой нагрузки, создает более безопасные условия работы установки. Все это позволяет решить главную задачу: обеспечение работы испарителя во влажном режиме и при этом гарантировать «сухой ход» компрессора. Достигается это благодаря наличию в схеме двух циркуляционных контуров хладагента, имеющих разную кратность циркуляции (рис. 71): по контуру циркуляционный ресивер — компрессор — конденсатор — регулирующий вентиль — циркуляционный ресивер циркулирует количество хладагента, эквивалентное тепловой нагрузке на испаритель с кратностью циркуляции n = 1; по контуру циркуляционный ресивер — насос — прибор охлаждения — циркуляционный ресивер циркулирует избыточное количество жидкости с кратностью циркуляции n = 5 — 10. Гарантией «сухого хода» компрессора является отсутствие возможности переполнения циркуляционного ресивера при любых режимах работы установки и выполнение им функций отделителя жидкости при совмещенном варианте исполнения. Первое обеспечивается правильным расчетом вместимости сосуда; второе — правильным расчетом скорости пара в паровой зоне сосуда, которая не должна превышать скорость витания капель жидкости. Расчетная скорость пара аммиака в отделителе жидкости не должна превышать 0,5 м/с.
Узел циркуляционного ресивера может иметь следующие конструктивные варианты:
горизонтальный циркуляционный ресивер типа РД, не совмещающий функции отделителя жидкости, с расположенным над ним ОЖ;
вертикальный циркуляционный ресивер типа РДВ, совмещающий функции ОЖ;
горизонтальный циркуляционный ресивер типа РЦЗ или РВЦЗ, совмещающий функции ОЖ.
В схеме с горизонтальным циркуляционным ресивером и отделителем жидкости подача жидкости через РВ производится в отделитель жидкости, а не в ресивер, для того чтобы облегчить отсос пара, образующегося при дросселировании, так как в ресивере пар может создать подпор, препятствующий свободному сливу из отделителя жидкости в ресивер. Рабочий уровень хладагента поддерживается и регулируется в циркуляционном ресивере на отметке 20 % емкости при отсутствии стояка и 10 % — при его наличии. Предельное заполнение ресивера 80 %. Парожидкостная смесь из камер возвращается в отделитель жидкости, откуда отделенная жидкость стекает в ресивер, а сухой пар отсасывается компрессором. Сливной трубопровод между отделителем и ресивером должен быть, по возможности, вертикальным или иметь постоянный уклон в сторону ресивера, чтобы не создавать препятствий для движения жидкости и не вызывать переполнения отделителя жидкости.
В последнее время преимущественное распространение в насосных схемах получили циркуляционные ресиверы, совмещающие функции ресивера и отделителя жидкости в одном сосуде. На рис. 72 изображена схема с вертикальным циркуляционным ресивером типа РДВ. Жидкий хладагент от линейного ресивера через РВ поступает в ресивер, где происходит разделение парожидкостной смеси. Сухой пар отсасывается из верхней зоны в компрессор, а жидкость собирается в нижней зоне сосуда, откуда через стояк забирается насосом и подается через жидкостные этажные коллекторы ЖК в камерные приборы охлаждения. После кипения в приборах охлаждения парожидкостная смесь через паровые этажные коллекторы ПК и сливные трубопроводы возвращается в верхнюю зону циркуляционного ресивера, работающую как отделитель жидкости. Пар отсасывается компрессором, а жидкость стекает в нижнюю зону ресивера, откуда вновь забирается насосом. Для проведения оттаивания камерных приборов на этажах предусмотрены дренажные ДК и оттаивательные ОК. коллекторы, а в машинном отделении установлен дренажный ресивер. Опорожнение дренажного ресивера после оттаивания в насосных схемах целесообразно осуществлять с помощью центробежных насосов прямо в испарительную систему. Такое опорожнение длится несколько минут в отличие от выдавливания горячим паром, которое может длиться несколько часов. Линия пара высокого давления, подходящая к дренажному ресиверу, предназначена в этом случае для подогревания аммиачно-масляной смеси при выпуске масла.
Для предотвращения явления кавитации в насосах предусматривается их заглубление относительно рабочего уровня в циркуляционном ресивере на величину не менее кавитаци-онного запаса, указанного в паспорте насоса. На линии нагнетания насоса устанавливается обратный клапан, препятствующий возврату жидкости в ресивер при остановке насоса. Учитывая возможность неисправности аммиачного насоса, в схеме должен быть предусмотрен резервный аммиачный насос с параллельным подключением.
В безнасосных схемах регулирование подачи хладагента в испарительную систему необходимо осуществлять индивидуально на каждый камерный прибор. В насосных схемах благодаря повышенной кратности циркуляции такой необходимости нет и регулирование подачи осуществляется путем поддержания рабочего уровня хладагента в циркуляционном ресивере. При автоматизации этого процесса датчик уровня ДУ, установленный на рабочем уровне ресивера, дает сигнал на открытие или закрытие соленоидного вентиля СВ, пропускающего жидкость через регулирующий вентиль в ресивер. Рабочий уровень для ресиверов типа РДВ составляет 25 % заполнения сосуда при отсутствии стояка и 10 % — при монтаже стояка. Предельное заполнение ресивера 70 %.
При подаче жидкости насосами применяют параллельное распределение хладагента по камерным приборам. При этом, учитывая разную удаленность камерных приборов от насоса, необходимо отрегулировать равномерную раздачу жидкости по объектам с одинаковой кратностью циркуля-
ции. Для этой цели на жидкостных этажных коллекторах устанавливаются дополнительные регулирующие вентили, диафрагмы или тонкие трубки, проходное сечение которых отрегулировано на создание определенного сопротивления потоку жидкости. Настройка этажных регулирующих вентилей осуществляется в момент первоначального запуска системы в эксплуатацию.
При эксплуатации насосных схем иногда возникают ситуации неравномерности раздачи хладагента или недостаточности напора насоса для подачи в наиболее удаленные приборы охлаждения. В этих случаях иногда подключают резервные аммиачные насосы параллельно с рабочими. При такой работе насосов увеличивается только подача хладагента, а напор остается практически прежним. Поэтому вместо суммирования подачи всех насосов целесообразнее разделить работу насосов на отдельные потребители. Можно рекомендовать разделение потребителей холода на отдельные группы со сходными тепловыми и гидравлическими характеристиками (например, группа камер интенсивного охлаждения с воздухоохладителями и группа камер хранения с батареями), и для каждой группы установить отдельные насосы для подачи жидкости из общего циркуляционного ресивера. Рекомендуемые значения кратности циркуляции для различного охлаждающего оборудования:
Для насосных схем рекомендуется змеевиковый тип батарей.
На рис. 73 представлена схема подключения горизонтального циркуляционного ресивера типа РЦЗ, совмещающего функции отделителя жидкости. Рабочее заполнение ресивера со стояком 10 %, предельное заполнение 70 %.
В насосных схемах имеют место два вида подачи в охлаждающие приборы: верхняя и нижняя. Применение того или иного вида подачи имеет свои специфические особенности, которые нужно учитывать при подборе оборудования, монтаже и эксплуатации схемы.
Преимущественное распространение имеет вариант верхней подачи, которому свойственны следующие особенности:
поперечное сечение трубы охлаждающего прибора заполнено жидкостью на 30 % для батарей и на 50 % для воздухоохладителей, что несколько снижает эффективность теплообмена;
рекомендуемые значения кратности циркуляции в схемах с верхней подачей должны быть больше, чем с нижней;
лучше удаляются масло и загрязнения из охлаждающих приборов, поэтому необходимо монтировать батареи с небольшим уклоном в сторону слива (1,0—1,5 %) и соблюдать постоянный уклон сливной линии от охлаждающих приборов к циркуляционному ресиверу, поскольку эта линия самотечна;
малая тепловая инерционность при регулировании температуры камеры, так как при сигнале от датчика температуры ДТ на закрытие подачи соленоидным вентилем СВ жидкий хладагент сливается из батарей в циркуляционный ресивер и охлаждение камеры прекращается;
объем циркуляционного ресивера должен быть рассчитан на прием жидкости из всей испарительной системы и сливных трубопроводов.
Верхнюю подачу хладагента иногда трудно применить для одноэтажных холодильников из-за недостаточной высоты помещений для проложения самотечного сливного трубопровода. В этих и некоторых других случаях применяют вариант нижней подачи, который имеет следующие особенности:
поперечное сечение трубы охлаждающих приборов (батарей и воздухоохладителей) заполняется жидкостью на 70%;
рекомендуемые значения кратности циркуляции меньше, чем для схем с верхней подачей;
при прекращении подачи холодильный агент остается в охлаждающих приборах, поэтому для выключения прибора из работы по сигналу от датчика температуры ДТ необходимо закрыть соленоидные вентили СВ на входе и выходе из охлаждающего прибора;
при остановке аммиачного насоса хладагент остается в камерных приборах, поэтому объем циркуляционного ресивера не рассчитан на прием жидкости из всей испарительной системы;
предъявляются особые требования к исправности обратного клапана насоса, так как его негерметичность может привести к переполнению ресивера;
жидкостные трубопроводы рекомендуется подводить к батареям и воздухоохладителям с устройством петли, чтобы не допустить слива из них аммиака при остановке насоса и неисправности обратного клапана.
Требования безопасной эксплуатации насосных схем связаны прежде всего с правильным выбором емкости циркуляционных ресиверов. В табл. 50 приведены формулы расчета для проверки достаточности вместимости циркуляционных ресиверов различных типов.
При недостаточной вместимости существующих циркуляционных ресиверов необходимо установить дополнительные ресиверы так, чтобы общая вместимость ресиверов была не менее полученной по расчету, или заменить на ресиверы большей вместимости. Даже при достаточной вместимости циркуляционных ресиверов недопустимо превышать уровень в сосуде выше предельно допустимого. Запрещается также работа компрессоров при остановленных аммиачных насосах, последние должны пускаться в работу раньше.
Кратность циркуляции зависит от выбранного способа раздачи хладагента по батареям. Для схем с верхней подачей хладагента она в 1,5—2 раза больше, чем с нижней.
3.
Дата добавления: 2018-06-27; просмотров: 890; Мы поможем в написании вашей работы! |
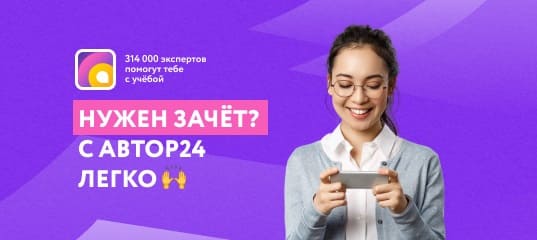
Мы поможем в написании ваших работ!