Обоснование контура регулирования, подлежащего расчету
Министерство образования и науки Российской федерации
Федеральное государственное бюджетное образовательное учреждение высшего образования
«Пермский национальный исследовательский политехнический университет»
Березниковский филиал
ОТЧЕТ ПО ПРАКТИКЕ
«Автоматизация процесса хлорирования титаносодержащей шихты
В цехе № 32 ПАО «АВИСМА
Филиал корпорации ВСМПО-АВИСМА »
Выполнил: студент группы АТП-12в ______________ Шерстобитов С.А.
Дата сдачи «____» _________ 2017 г.
Проверил: канд. техн. наук, профессор _____________ Беккер В.Ф.
Оценка «___________________»
Дата проверки «____» _________ 2017г.
Березники, 2017
СОДЕРЖАНИЕ
1. ОПИСАНИЕ ТЕХНОЛОГИЧЕСКОГО ПРОЦЕССА.. 3
1.1 Назначение процесса. 3
1.2 Структура производства. 4
1.3 Характеристика сырья и продуктов (полупродуктов) 6
1.4 Критерии качества управления производством.. 7
1.5 Описание основных аппаратов производства. 8
1.6 Описание технологической схемы.. 10
2. АНАЛИЗ ОБЪЕКТА УПРАВЛЕНИЯ.. 12
2.1. Обоснование выбора точек контроля, регистрации, регулирования и сигнализации. 12
2.2. Обоснование выбранной системы средств автоматизации. 14
2.3. Обоснование контура регулирования, подлежащего расчету. 14
3. ПРОВЕДЕНИЕ ЭКСПЕРИМЕНТА.. 16
Рис. 3.12. Кривая разгона по каналу возмущения W3(S)4. ОБРАБОТКА ЭКСПЕРИМЕНТАЛЬНЫХ ДАННЫХ.. 27
4. ОБРАБОТКА ЭКСПЕРИМЕНТАЛЬНЫХ ДАННЫХ.. 28
|
|
5. РАСЧЕТ СИСТЕМЫ РЕГУЛИРОВАНИЯ.. 29
5.1. Расчет оптимальных настроечных параметров регулятора в одноконтурной системе. 29
5.2. Расчет оптимальных настроечных параметров стабилизирующего и корректирующего регуляторов в каскадной системе регулирования. 30
5.3. Расчет комбинированной системы регулирования. 34
6. МОДЕЛИРОВАНИЕ РАССЧИТАННОЙ СИСТЕМЫ РЕГУЛИРОВАНИЯ.. 41
6.1. Переходные процессы в одноконтурной системе регулирования. 41
6.2. Переходные процессы во внутреннем контуре. 44
6.3. Переходные процессы в каскадной системе регулирования. 46
6.4. Переходные процессы по возмущению в каскадно-комбинированной системе регулирования без компенсирующего устройства и с компенсирующим устройством. 50
7. АНАЛИЗ КАЧЕСТВА ПЕРЕХОДНЫХ ПРОЦЕССОВ И ВЫБОР СИСТЕМЫ РЕГУЛИРОВАНИЯ 56
7.1 Анализ качества переходных процессов одноконтурной системы.. 56
7.2 Анализ качества переходных процессов каскадной системы.. 59
7.3. Сравнение качества переходных процессов одноконтурной и каскадной систем регулирования 63
8. РЕАЛИЗАЦИЯ РАСЧИТАНОЙ СИСТЕМЫ РЕГУЛИРОВАНИЯ.. 67
8.1. Обоснование выбранных программных и технических средств. 67
9. РАСЧЕТ РЕГУЛИРУЮЩЕГО ОРГАНА.. 81
10. СПЕЦИФИКАЦИЯ ИСПОЛЬЗУЕМЫХ ТЕХНИЧЕСКИХ СРЕДСТВ.. 85
|
|
1. ОПИСАНИЕ ТЕХНОЛОГИЧЕСКОГО ПРОЦЕССА
1.1 Назначение процесса
В дипломном проекте рассматривается автоматизация процесса хлорирования титаносодержащей шихты в цехе 32 ПАО «АВИСМА филиал корпорации «ВСМПО-АВИСМА». Хлорирование титаносодержащей шихты является одной из стадий получения губчатого титана. На этой стадии производства образуется технический тетрахлорид титана.
Возросшие требования к качеству металла и защите окружающей среды, сложность и интенсивность процесса хлорирования в металлургии повысили ответственность за управлением этим и другими процессами. Даже небольшие ошибки в управлении могут привести к большим потерям металла, электроэнергии, топлива, снизить производительность и ухудшить качество выпускаемого технического тетрахлорида титана. Роль автоматизации в производстве этого продукта очень велика. С внедрением автоматизации в процесс хлорирования титанового сырья (шлаков) повышается производительность хлораторов, снижаются расходы на сырье, улучшается качество технического тетрахлорида титана, так как нормы технологического режима выдерживаются без нарушений.
|
|
Отделение хлорирования входит в состав химико-металлургического цеха № 32, расположенного на площадке ПАО «АВИСМА». Цех хлорирования – это промежуточный этап производства титана и магния.
Основная задача работы цеха – получение очищенного тетрахлорида титана из титаносодержащей шихты. Отделение хлорирования играет большую роль при производстве титановой губки, пигментной двуокиси титана как катализатора в химической промышленности. Производство титановой губки является одним из самых значимых на предприятиях титано-магниевого производства. Она обладает уникальными химическими свойствами, важными для металлургии, является легирующим, рафинирующим и модифицирующим компонентом при производстве металлов и сплавов в цветной и чёрной металлургии. Титановая губка обладает высокой химической стойкостью к многим агрессивным средам неорганического и органического происхождения при нормальных и повышенных температурах.
1.2 Структура производства
Процесс хлорирования титаносодержащей шихты состоит из следующих этапов:
1. Взаимодействие хлора с расплавом и титановым шлаком. Для обеспечения условий теплопередачи, процесс хлорирования протекает при температуре расплава от 700 до 800 оС, при этом хлор взаимодействует с диоксидом титана по реакциям:
|
|
TiO2 + 2Cl2 + C = TiCl4 + CO2 + Q ккал
TiO2 +2Cl2 +2C = TiCl4 + 2CO + Q ккал
Кислород оксидов титаносодержащей шихты и кислород анодного хлоргаза при взаимодействии с углеродом образует окись углерода по реакции:
C + O2 = CO2 + Q ккал
Причиной образования хлора в отходящих газах могут являться вторичные реакции при взаимодействии кислорода анодного хлор газа с тетрахлоридом титана или кремния, окисляя при этом их в диоксид титана или кремния, что приводит к увеличению их содержания в «возгонах» и снижению извлечения титана на узле хлорирования:
TiCl4(газ) + O2(газ) = TiO2(тв.) + 2Cl2(газ)
SiCl4(газ) + O2(газ) = SiO2(тв.) + 2Cl2(газ)
В процессе хлорирования титаносодержащий шлак и восстановитель находятся в расплаве во взвешенном состоянии, причем наиболее легкий углеродистый восстановитель концентрируется преимущественно в верхних слоях хлоратора, а шлак распределяется равномерно по всему объему расплава. В зоне подачи хлора происходит интенсивное перемешивание расплава и газообразного хлора, преобразование газового потока в мелкие пузырьки, насыщение расплава анодным хлоргазом, процесс нагрева хлоргаза. Продолжительность процесса взаимодействия хлора с расплавом и шлаком определяется временем подъема пузырька от самого низа к поверхности расплава. Если возникает ситуация, что хлор во время подъема не вступил в реакцию, то он попадает в отходящие газы. Избыток тепла, образующегося в процессе хлорирования, отводится через водоохлаждаемые штанги, находящиеся внутри графитовых электродов, которые находятся в футеровке хлоратора, а также за счёт испарения пульпы, закачиваемой в хлоратор.
2. Охлаждение и частичная очистка ПГС в пылеосадительных камерах с плавильником возгонов, в которых происходит дохлорирование компонентов шихты, и без плавильника возгонов, где проводится более тонкая очистка от твердых хлоридов и продуктов пылеуноса.
3. Охлаждение ПГС в оросительном скруббере для частичной конденсации тетрахлорида титана в таком количестве, каком необходимо для получения транспортабельной пульпы.
4. Конденсация тетрахлорида титана в оросительном конденсаторе за счет дальнейшего охлаждения ПГС охлажденным тетрахлоридом титана.
5. Очистка отходящих газов (CO2, CO, SO2, N2, Cl2, пары TiCl4, SiCl4, HCl, COCl2,) в санитарном скруббере.
6. Охлаждение TiCl4 в теплообменниках типа «труба в трубе».
Рис. 1.1. Схема получения технического TiCl4
1.3 Характеристика сырья и продуктов (полупродуктов)
Хлорирование – процесс взаимодействия хлора с окислами элементов или их соединениями для получения хлоридов или оксихлоридов.
Производимой продукцией является технический тетрахлорид титана в процессе хлорирования титаносодержащей шихты.
Титаносодержащая шихта, поступающая на хлорирование, состоит из смеси измельченного титаносодержащего шлака, пекового кокса или угля и технического хлористого натрия или хлористого калия электролитного. Титаносодержащая шихта - однородная сыпучая масса темно-серого или чёрного цвета; насыпная плотность 1500-2500 кг/м3; массовая доля влаги 0,4-0,6 %; не токсична, не взрывоопасна, не пожароопасная. Техническая соль NaCl или отработанный электролит, входящие в состав титаносодержащей шихты, поддерживают постоянство состава расплава.
Анодный хлоргаз - смесь хлора и воздуха - токсичен, не взрывоопасен, не пожароопасен.
Образующиеся в процессе хлорирования продукты представляют собой сложную систему, которая состоит из хлоридов и газов. Продукты хлорирования можно условно разделить на четыре группы, которые сильно отличаются по своим физико-химическим свойствам:
1. газы – CO2, HCl, CO, COCl2, SO2, N2, Cl2 и др.;
2. низкокипящие жидкие хлориды - TiCl4, SiCl4, VOCl3, СCl4, и др.;
3. низкокипящие твердые хлориды - AlCl4, FeCl3, и др.;
4. высококипящие твердые хлориды – MgCl2, MnCl2, FeCl2,CrCl3,CaCl2 и др.
Основным продуктом является технический тетрахлорид титана, который представляет собой бесцветную сильно гидролизующуюся на воздухе жидкость, не взрывоопасен, не горюч. Химическая формула – TiCl4; молярная масса – 189,71 г/моль; температура кипения – 136,2 0С; температура кристаллизации – минус 23 0С; степень электролитической диссоциации – 279 при 20 0С; плотность при 20 0С – 1730 кг/м3 (1,73 г/см3). Предельно допустимая концентрация тетрахлорида титана в воздухе рабочей зоны (по хлористому водороду) – 5 мг/м3.
1.4 Критерии качества управления производством
Для управления технологическим процессом необходимо внедрять автоматизацию производства, так как человек медленно реагирует на изменение параметров технологического режима. С внедрением автоматизации в процесс хлорирования повышается производительность хлорирующих установок, снижаются расходные нормы на сырье, улучшается качество технического тетрахлорида титана, так как точно выдерживаются нормы технологического режима.
Основной продукт производства - технический тетрахлорид титана, получаемый в процессе хлорирования титаносодержащей шихты. Необходимо вести контроль параметров технологического процесса с целью получения качественного тетрахлорида титана.
Основной задачей оптимального управления является поиск параметров технологического процесса, при которых будет обеспечена высокая степень хлорирования титаносодержащей шихты, после чего снизится количество отходов и уменьшится расход самой шихты, что приведет к снижению себестоимости продукта. Для этого необходимо:
- обеспечить наиболее эффективное использование анодного хлоргаза, поступающего из отделения электролизного цеха;
- получить максимальное извлечение титана из титаносодержащей шихты при минимальном содержании примесей в тетрахлориде титана, и обеспечить максимальную производительность;
- обеспечить протекание процесса для поддержания оптимальной температуры расплава в хлораторе (при температуре расплава ниже 700°С может произойти вспенивание расплава, а если температура расплава будет выше 800°С, то это приведет к снижению качества получаемого тетрахлорида титана вследствие снижения степени хлорирования шихты. Вследствие этого реакция будет протекать в ненормальных условиях, и это приведет к снижению скорости реакции и к увеличению времени протекания процесса.
Полученный в результате хлорирования титаносодержащих материалов жидкий тетрахлорид титана содержит примеси. Концентрация примесей в тетрахлориде титана, получаемом в результате хлорирования, следующая: %: V 0,1 – 0,15; Si – 0,001-0,02; Cl (газообразного) 0,07-0,15; фосгена и хлорацетилхлоридов (в сумме) 0,003-0,25; твердого остатка 2-4 г/см3. Эти примеси берут под контроль, их уровень обозначают в регламенте и эти данные используют для выбора технологических режимов. Технический тетрахлорид титана должен соответствовать ТУ 1715-455-05785388-99.
1.5 Описание основных аппаратов производства
Хлоратор (XT) является основным технологическим аппаратом и предназначен для получения тетрахлорида титана хлорированием титаносодержащей шихты в расплаве хлористых солей.
XT представляет собой шахту переменного сечения с переходом от рабочей зоны к зоне газового пространства, выполненного из шамотного кирпича. Кожух хлоратора обклеен диабазовой плиткой. За счет разности плотности расплава в хлорирующих зонах и циркуляционных зонах в хлораторе создается направленная циркуляция расплава через переточные каналы.
Для подачи анодного хлоргаза имеются четыре фурменных узла, состоящие из фурмы (сталь и чугун), находящейся в бетонном блоке, фурменного камня и фурменного стояка. Для загрузки шихты в верхней части хлоратора установлены два канала для установки шнековых питателей с регулирующими приводами. При сливе расплава из хлоратора предусмотрены узлы верхнего и нижнего слива.
Для поддержания заданной температуры расплава в хлоратор вмонтированы три водоохлаждаемых графитовых электрода, расположенных под углом 120° относительно друг друга. Параметры температуры расплава хлоратора контролируются термопарой, установленной в графитовом блоке у кармана верхнего слива. Для поддержания необходимой концентрации расплава в хлораторе отработанный расплав периодически выводится из хлоратора в ванну гидроудаления и далее сливается в кислотную канализацию. Нерастворимый осадок из отстойника шнеком выгружается в короб и вывозится в отвал.
Газы и низкокипящие жидкие и твердые хлориды выводятся из хлоратора в виде парогазовой смеси (ПГС) через два газохода в систему конденсации, которая представляет собой серию теплообменных и пылеулавливающих аппаратов, предназначенных для охлаждения, конденсации и разделения сконденсированных продуктов хлорирования. Парогазовая смесь, выходящая из хлоратора, подвергается предварительному охлаждению и частичной очистке в пылеосадительных камерах с плавильником возгонов и без плавильника.
На своде хлоратора имеются отверстия, для установки двух мембран взрывных клапанов, для установки форсунки на линии закачки пульпы в хлоратор и отверстие для установки термопары, для измерения температуры парогазовой смеси (ПГС) под сводом хлоратора и отбора давления ПГС под сводом хлоратора.
Отметим некоторые технические характеристики:
производительность приблизительно 120 т/сутки;
максимальный расход С1-газа - 2 000 м3/ч;
температура расплава - 700-750 °С;
номинальные размеры: высота 11,170 м, диаметр 4,975 м;
объем парогазовой смеси - 65 м3; Р
рабочий уровень расплава - 4 380 мм;
площадь зеркала расплава - 7,6 м2;
Рис. 1.2. Реактор для хлорирования титановых шлаков в расплаве солей
1.6 Описание технологической схемы
Для хлорирования титаносодержащей шихты используется хлоратор (1) с жидкой ванной из расплавленных хлоридов щелочных и щелочноземельных металлов. Шихта, которая загружается в хлоратор, состоит из смеси титансодержащего шлака, пекового кокса, технического хлористого натрия или хлористого калия электролитного. Шихта доставляется автошихтовозом (20) и выдувается в приемный бункер (18). Из приемного бункера (18) через расходный бункер (19) винтовым конвейером шихта подается в расплав хлоратора.
Анодный хлоргаз, под давлением 0,10 – 0,11 МПа, подается в расплав через четыре фурмы хлоратора снизу.
Образующиеся в процессе хлорирования высококипящие твердые хлориды (кальция, магния, марганца и др.) вместе с не прохлорировавшейся частью окислов шихты накапливаются в расплаве.
Для поддержания необходимой концентрации «твердых», отработанный расплав периодически выводится из хлоратора в ванну гидроудаления (12) и далее сливается в кислотную канализацию. Нерастворимый осадок из отстойника шнеком выгружается в короб и вывозится в отвал.
Образующиеся в процессе хлорирования титансодержащих материалов продукты хлорирования представляют собой сложную систему, которая состоит из хлоридов (в парообразном или конденсированном состоянии) и газов.
Продукты хлорирования можно условно разделить на четыре группы, отличающиеся по своим физико-химическим свойствам:
- газы – CO2, HCl, CO, COCl2, SO2, N2, Cl2 и др.;
- низкокипящие жидкие хлориды - TiCl4, SiCl4, VOCl3, СCl4, и др.;
- низкокипящие твердые хлориды - AlCl4, FeCl3, и др.;
- высококипящие твердые хлориды – MgCl2, MnCl2, FeCl2,CrCl3,CaCl2 и др.;
Газы и низкокипящие жидкие и твердые хлориды выводятся из хлоратора в виде парогазовой смеси (ПГС) в систему конденсации, которая представляет собой серию теплообменных и пылеулавливающих аппаратов, предназначенных для охлаждения, конденсации и разделения сконденсированных продуктов хлорирования.
Парогазовая смесь выводится через два газохода, находящихся в верхней части хлоратора (1) и поступает в пылеосадительную камеру с плавильником возгонов (2) и пылеосадительную камеру без плавильника возгонов (3). Уловленные в пылеосадительной камере (3) «возгоны» выгружаются в установленные под конусами камер кюбели (10) и вывозятся на размывку. В пылеосадительной камере с плавильником (2), «возгоны» улавливаются расплавом и накапливаются в нагреваемом до температуры от 200 до 400 оС плавильнике, куда через фурмы подается воздух и происходит дохлорирование компонентов шихты. В пылеосадительной камере с плавильником осуществляется дополнительная очистка от твердых хлоридов и продуктов пылеуноса вследствие взаимодействия твердых хлоридов ПГС с расплавом. При накоплении расплава в плавильнике его периодически или непрерывно сливают через верхнюю летку в ванну гидроудаления (12).
Охлажденная и частично очищенная ПГС из пылеосадительных камер поступает в оросительный скруббер (4, 5) для дальнейшего охлаждения ПГС, улавливания твердых частиц, а также частичной конденсации тетрахлорида титана в количестве, необходимом для получения транспортабельной пульпы с массовой концентрацией в ней твердых примесей не более 300 г/дм3.
Пульпа собирается в баке с мешалкой (8) и через орошаемые водой холодильники (7) погружным насосом подается на оросительный скруббер (4,5) для орошения. Избыток пульпы, образующейся в процессе конденсации, непрерывно через регулирующий клапан закачивается в хлоратор, при этом тетрахлорид титана испаряется, снижается температура выходящей из хлоратора ПГС, а твердые хлориды, C и TiO2 переходят в расплав и участвуют в основных реакциях хлорирования.
Охлажденная до точки росы тетрахлорида титана и отмытая от твердых хлоридов ПГС из оросительного скруббера(4,5) поступает в оросительный конденсатор (6), где происходит конденсация тетрахлорида титана за счет дальнейшего охлаждения ПГС охлажденным тетрахлоридом титана.
Сконденсировавшийся тетрахлорид титана стекает в бак для TiCl4 (9), из которого подается для охлаждения в теплообменники (7) типа «труба в трубе» (ТТ), холодильник охлаждается рассолом хлористого кальция. Накопившийся в технический тетрахлорид титана, через перелив в баке стекает в сборный бак технического продукта, откуда перекачивается в цистерну номинальной вместимостью 50 м3, из которой, по мере необходимости, подается на передел очистки от ванадия или в другую баковую аппаратуру.
Отходящие газы после оросительного конденсатора (CO2, CO, SO2, N2, Cl2, пары TiCl4, SiCl4, HCl, COCl2,) идут на очистку в санитарном скруббере и далее поступают на газоочистку № 2, сточные воды из санитарного скруббера поступают в кислотную канализацию.
2. АНАЛИЗ ОБЪЕКТА УПРАВЛЕНИЯ
2.1. Обоснование выбора точек контроля, регистрации, регулирования и сигнализации
Контроль технологических параметров процесса хлорирования осуществляется стандартными средствами измерения.
Параметры технологического процесса необходимо контролировать с целью получения качественного тетрахлорида титана, отслеживая параметры его получения (очищения) на каждой стадии (скорость реакций, поддержание температуры и давления, и т.д.), также контроль необходим для безопасности работы установок, используемых в производственном процессе.
Контроль и регулирование данных параметров необходим для безопасности работы хлорирующей установки, для ускорения проведения процесса, получения более качественного тетрахлорида титана, так как можно проследить все параметры протекания процесса (поддержание температуры, скорости реакции и др.).
Температура расплава в хлораторе контролируется с целью получения качественного тетрахлорида титана (итогового продукта процесса хлорирования). Так, если температура расплава будет ниже 700°С, – это может привести к вспениванию расплава, а если температура расплава будет выше 800°С, то это приведет к снижению качества получаемого тетрахлорида титана, вследствие снижения степени хлорирования шихты, следовательно, реакция будет протекать в условиях, отличных от нормальных. Уменьшение температуры приведет к снижению скорости реакции, значит к увеличению времени протекания процесса.
Температура парогазовой смеси (ПГС) в хлораторе контролируется для обеспечения нормальной работы установки, в частности самого хлоратора. При высокой температуре ПГС может произойти выход из строя газоходов, соединяющих хлоратор (ХТ) с пылеосадительными камерами.
Температура ПГС в пылеосадительной камере с плавильником возгонов (ПК № 1) и на выходе из нее контролируется с целью определения работоспособности установки, в частности самой камеры, т.к. при очень высокой температуре ПГС может вывести из строя так же газоходы, который соединяют пылеосадительную камеру с оросительным скруббером.
Температура расплава в пылеосадительных камерах и других аппаратах, а также на выходе из каждого аппарата контролируется для поддержания оптимальной производительности хлорирующей установки и получения качественного готового продукта.
Температура ПГС на выходе из оросительного скруббера контролируется с целью определения эффективности работы аппарата.
Температура в баке–мешалке контролируется с целью определения степени конденсации паров TiCl4 из парогазовой смеси.
Расход анодного хлор-газа контролируется для отслеживания нагрузки на фурмы, а так же для получения максимально качественного продукта, и чтоб было меньше отработанного неиспользуемого материала.
Расход осушенного воздуха, подаваемого в ПК №1, контролируется для обеспечения нормального дохлорирования компонентов расплава.
Давление в аппаратах или при выходе из аппарата контролируется для определения состояния аппаратов.
Уровень в баке мешалке №2 контролируется для предотвращения переполнения бака.
Стабилизация расхода воздуха на фурму 1 и 2 пылеосадительной камеры с плавильником возгонов (ПК-1) происходит для того, чтобы не было потерь тетрахлорида титана.
Число оборотов шнековых питателей контролируется с целью подачи нужного количества шихты в хлоратор для хлорирования.
Параметры подлежат сигнализации для того, чтобы сообщать обслуживающему персоналу о критических изменениях хода технологического процесса, об аварийном отключении оборудования, из-за которых может измениться качество получаемого продукта.
Температура расплава в хлораторе подлежит обязательной сигнализации, так как при её увеличении до 750°С и выше может привести к снижению качества получаемого TiCl4.
Температура расплава в пылеосадительных камерах сигнализируется для нормального протекания технологического процесса, т.к. в каждой пылеосадительной камере (ПК №1, ПК №2) происходит охлаждения ПГС до определенной температуры, чтобы перейти в следующую стадию.
Давление под сводом хлоратора. При повышении давления может произойти разрушение футеровки ХТ. По данному параметру судят о загрязнении системы конденсации.
Уровень пульпы в баках-мешалках. По данному параметру судят о степени загрязнения системы конденсации.
Расход анодного хлоргаза сигнализируется для нормального протекания технологического процесса, качественного хлорирования и меньшего образования отработанного вещества.
Расход пульпы в хлоратор сигнализируется с целью поддержания оптимальной температуры в хлораторе, а, следовательно, с целью получения качественного продукта.
2.2. Обоснование выбранной системы средств автоматизации
При ведении процесса хлорирования необходимо контролировать вышеперечисленные параметры, так как они оказывают влияние на количество и качество получаемого тетрахлорида титана и на температуру расплава, а так же поддерживают стабильное протекание процесса, обеспечивают оптимальные условия работы и нормальное функционирование объекта.
Для нашего производства важно, чтобы была высокая точность измерения, а сигнал передавался с меньшим запаздыванием и большим быстродействием. Так же нужно предусмотреть, что приборы будут работать с агрессивной средой.
Существует два вида систем автоматизации технологического процесса: электрическая и пневматическая ветви. Электрические ветви более точные, обладают высоким быстродействием и способны передавать сигнал на большие расстояния. Но недостатком таких систем является - неудобство работы во влажных, запыленных и взрывоопасных средах, поэтому там мы будем использовать приборы пневматической ветви. Таким образом, будем использовать приборы электропневматической ветви.
Обоснование контура регулирования, подлежащего расчету
Основным регулируемым параметром технологического процесса является температура расплава в хлораторе, она должна поддерживаться в пределах 700-750°С.
Так, если температура расплава будет ниже 700°С, - это может привести к вспениванию расплава, а если температура будет выше 750°С, то это приведет к снижению качества получаемого тетрахлорида титана, вследствие снижения степени хлорирования шихты, следовательно, реакция будет протекать в условиях, отличных от нормальных. Уменьшение температуры приведет к увеличению времени протекания процесса.
Температура расплава зависит от множества параметров, основным из которых является расход пульпы в хлоратор. Пульпа подается в хлоратор непрерывно, и её расход варьируется в пределах 50-60 м3/ч. Если температура расплава высокая, то её можно изменить увеличением расхода пульпы (открыть клапан подачи пульпы в хлоратор), если наоборот – температура расплава низкая, то её можно повысить, закрыв клапан подачи пульпы, вследствие чего, расход уменьшится.
Так же на температуру расплава влияет расход анодного хлоргаза. В момент подачи хлоргаза в хлоратор температура расплава снижается, т.к. его температура низкая относительно температуры расплава в хлораторе, далее температура расплава увеличивается, т.к. реакции идут с выделением большого количества тепла (экзотермические).
Хлор в виде анодного газа поступает по трубопроводу из цеха электролиза MgCl2. Наличие примесей кислот (соляная, серная) в хлоргазе приводит к забиванию фурм хлоратора. Для приведения фурм хлоратора в работоспособное состояние необходимо периодически производить чистку. При проведении этой процедуры полностью снимается расход хлора на фурму подлежащую очистке. В результате происходит изменение общего расхода хлоргаза подаваемого в хлоратор.
Расход хлоргаза также влияет на количество итогового продукта, если хлоргаза будет подаваться мало, то это приведет к получению меньшего количества и менее качественного тетрахлорида титана, то же самое произойдет, если сырье будет подаваться в избытке. Расход анодного хлор-газа на каждую из четырех фурм должен находиться в пределах 200-600 м3/ч.
Таким образом, получаем зависимости:
- изменение температуры расплава при изменении положения клапана регулирующего органа подачи пульпы;
- изменение расхода пульпы поступающей в хлоратор при изменении положения регулирующего органа подачи пульпы;
- изменение температуры расплава при изменении расхода анодного хлоргаза.
3. ПРОВЕДЕНИЕ ЭКСПЕРИМЕНТА
Для оптимального управления объектом необходимо получить динамические и статические характеристики.
Активный эксперимент – это организация воздействий на входе объекта управления с одновременной регистрацией изменений выходных координат. Достоинства этого метода состоят в следующем: резко снижается количество экспериментов, полученная модель имеет минимально возможную ошибку.
Для проведения активного эксперимента рассмотрим объект как «черный ящик», на вход будем подавать возмущающее воздействие, а на выходе снимать отклик на это возмущающее воздействие.
Планирование и подготовка эксперимента включает в себя следующие мероприятия:
1. Изучение априорной (известной) информации об объекте управления. В результате должна получиться структура модели эксперимента. Структура должна четко определить параметры, подлежащие возмущению, параметры, подлежащие контролю, и наличие внутренних связей между указанными параметрами.
2. Изучение статики объекта по определившимся в структуре каналам
3. Выбор аппаратуры для проведения эксперимента.
4. Определение времени проведения эксперимента и числа экспериментов.
Время проведения эксперимента выбирается в зависимости от состояния объекта (стабильные работы, работы на заданной мощности, отсутствие на объекте каких-либо пуско-наладочных работ, отсутствие пусковых или остановочных пределов).
В результате проведения эксперимента получаем динамическую характеристику объекта управления, которая в дальнейшем подвергается специальной обработке с целью получения математического описания объекта в виде передаточной функции или частотной характеристики.
Составим структурную схему объекта:
Рис. 3.1. Структурная схема объекта
Таким образом, нам необходимо получить три передаточные функции:
W1(s) - изменение температуры расплава при изменении положения клапана регулирующего органа подачи пульпы;
W2(s) - изменение расхода пульпы поступающей в хлоратор при изменении положения регулирующего органа подачи пульпы;
W3(s) - изменение температуры расплава при изменении расхода анодного хлоргаза.
Составим функциональную схему:
Рис. 3.2. Функциональная схема
1 – хлоратор титановый;
2 – трубопровод подачи хлора;
3 – трубопровод пульпы орошения;
4 –расходный бункер;
5 –винтовой конвейер;
1а – термоэлектрический преобразователь ТХА;
1г, 39г – преобразователь электропневматический ЭП-3211;
1д,39д – клапан регулирующий мембранный МИМ-250;
30а, 39а - диафрагма камерная ДКС
30б, 39б – датчик разности давлений Метран-150-CD с индикаторным устройством;
Эксперимент будем проводить по структурной и функциональной схемам. Для проведения эксперимента был выбран период стабильной работы хлоратора на средней нагрузке. Снятие кривых разгона подразумевает внесение в объект управления заранее определённых возмущающих воздействий. При проведении эксперимента фиксируется величина возмущающего воздействия, время и величина отклика объекта управления. Изменение выходной величины регистрируется до тех пор, пока она не примет установившееся значение. Эксперимент проводим на действующем оборудовании с использованием ПЭВМ и установленным на нем программным обеспечением RSView, с помощью контроллера Compact Logic(Allen Bradley) и существующих средств автоматизации.
Снимем 1-ю и 2-ю кривые разгона для вычисления передаточных функций W1(s) основного канала и W2(s) внутреннего канала. При проведении эксперимента необходимо учитывать, что уменьшение расхода пульпы приводит к повышению температуры расплава в хлораторе. Эксперимент будем проводить с контроллера Compact Logic через программное обеспечение RSView (Рис. 4.3.), уменьшая подачу пульпы на 10%, т.е. исполнительный механизм для подачи пульпы орошения закроется на 10%.
Рис. 3.3. Обзор технологических параметров АРМ ТО RS View 32
Осуществляем это таким образом: перейдем в окно обзора технологических параметров, перейдем к строке . Кликнем «левой кнопкой мышью» на кнопку «ХТ» и перед нами откроется обзор двух контуров регулирования температуры расплава в ХТ.
Рис. 3.4. Обзор контуров регулирования АРМ ТО RS View 32
Рис. 3.5. Контур регулирования температуры расплава в ХТ
клапаном подачи пульпы на расплав ХТ
В правом нижнем углу (Рис. 3.4) выберем контур «управление CV1 клапаном подачи пульпы на расплав ХТ». Перейдем на ручной режим управления – для этого кликнем «мышью» на кнопку «авто». После нажатия на кнопку «авто» контроллер перейдет на ручной режим управления и на кнопке появится надпись «ручной» (как на Рис. 3.5).
Уменьшим подачу пульпы на 10%, для этого кликнем «мышью» в поле «Задание» и изменим текущее значение открытия клапана со 100% до 90% с клавиатуры, т.е. закроем исполнительный механизм закачки пульпы в хлоратор на 10%. Подождем стабилизации температуры расплава.
После проведения эксперимента по снятию кривых разгона основного и внутреннего каналов посмотрим первый тренд. Для этого нажимаем левой кнопкой мыши на экране монитора АРМ ТО оператора на значение параметра «Температура расплава в ХТ» (Рис. 3.3, указатель «стрелка» красного цвета).
Рис. 3.6. Технологический тренд «Температура расплава в ХТ»
Чтобы посмотреть второй тренд, нажимаем левой кнопкой мыши на экране монитора АРМ оператора на значение параметра «Расход пульпы в ХТ» (Рис. 3.3, указатель «стрелка» голубого цвета).
Рис. 3.7. Технологический тренд «Расход пульпы в ХТ»
Снимем кривую разгона для вычисления передаточной функции W3(s) канала возмущающего воздействия.
Хлор поступает в хлоратор непрерывно в виде анодного газа через четыре фурменных узла c постоянным давлением. При проведении эксперимента необходимо учитывать, что увеличение расхода хлоргаза приводит к повышению температуры расплава в хлораторе из-за протекания экзотермической реакции. Эксперимент осуществляем следующим образом:перейдем в окно обзора технологических параметров, перейдем к строке . Кликнем левой кнопкой мыши на кнопку «ХТ» и перед нами откроется обзор двух контуров регулирования температуры расплава в ХТ.
В правом нижнем углу (Рис. 3.4) выберем контур «управление CV2 клапаном подачи хлора в ХТ». Перейдем на ручной режим управления – для этого кликнем мышью на кнопку «авто». После нажатия на кнопку «авто» контроллер перейдет на ручной режим управления и на кнопке появится надпись «ручной».
Рис. 3.8. Контур регулирования температуры расплава в ХТ клапаном подачи хлора в ХТ
Увеличим подачу хлора на 20%, для этого кликнем левой кнопкой мыши в поле «Задание» и изменим текущее значение открытия клапана со 80% до 100% с клавиатуры, т.е. откроем исполнительный механизм подачи хлора в хлоратор на 20%. Подождем стабилизации температуры расплава.
После проведения эксперимента по снятию кривой разгона канала по возмущению посмотрим тренд. Для этого нажимаем левой кнопкой мыши на экране монитора АРМ ТО оператора на значение параметра «Температура расплава в ХТ» (Рис. 3.3, указатель «стрелка» красного цвета).
Рис. 3.9. Технологический тренд «Температура расплава в ХТ»
В результате проведенного эксперимента мы получили:
1. Регулирование по основному каналу W1(S), где на вход объекта было оказано возмущающее воздействие, при котором в течение 780 с температура расплава увеличилась с 711°С до 748°С. Положение регулирующего органа изменили на 10% (исполнительный механизм подачи пульпы орошения в хлоратор (3)закрылся на 10%). Время регулирования – 780 с. Время запаздывания – 60 с.
Таблица 1. Координаты кривой разгона по основному каналу
№ точки | время, сек | температура расплава, С | № точки | время, мин | температура расплава, С | № точки | время, сек | температура расплава, С |
1 | 0 | 711.128 | 10 | 270 | 737.1 | 19 | 540 | 748.1 |
2 | 30 | 711.131 | 11 | 300 | 738.5 | 20 | 570 | 748.2 |
3 | 60 | 712.1 | 12 | 330 | 740.1 | 21 | 600 | 748.4 |
4 | 90 | 715.8 | 13 | 360 | 741.2 | 22 | 630 | 748.44 |
5 | 120 | 720.1 | 14 | 390 | 744.1 | 23 | 660 | 748.46 |
6 | 150 | 725.2 | 15 | 420 | 745 | 24 | 690 | 748.47 |
7 | 180 | 728.3 | 16 | 450 | 746.8 | 25 | 720 | 748.48 |
8 | 210 | 731.8 | 17 | 480 | 747.4 | 26 | 750 | 748.481 |
9 | 240 | 734.4 | 18 | 510 | 747.8 | 27 | 780 | 748.483 |
Рис.3.10. Кривая разгона по основному каналу W1(S)
2. Регулирование по внутреннему каналу W2(S),где исполнительный механизм подачи пульпы в хлоратор (3)закрыли на 10%. В результате расход пульпы орошения уменьшился с 60 до 51 м3/ч. Время регулирования – 250 сек. Время запаздывания – 30 сек.
Таблица 2. Координаты кривой разгона по внутреннему каналу
№ точки | время, сек | Расход пульпы, м3/ч | № точки | время, мин | Расход пульпы, м3/ч | № точки | время, сек | Расход пульпы, м3/ч |
1 | 0 | 60 | 10 | 90 | 58,51 | 19 | 180 | 54,97 |
2 | 10 | 59,97 | 11 | 100 | 58,23 | 20 | 190 | 54,48 |
3 | 20 | 59,91 | 12 | 110 | 57,68 | 21 | 200 | 53,71 |
4 | 30 | 59,78 | 13 | 120 | 57,41 | 22 | 210 | 52,11 |
5 | 40 | 59,64 | 14 | 130 | 57,22 | 23 | 220 | 51,56 |
6 | 50 | 59,44 | 15 | 140 | 56,9 | 24 | 230 | 51,005 |
7 | 60 | 59,32 | 16 | 150 | 56,44 | 25 | 240 | 51,002 |
8 | 70 | 59,27 | 17 | 160 | 55,96 | 26 | 250 | 51,001 |
9 | 80 | 58,89 | 18 | 170 | 55,42 |
|
|
|
Рис. 3.11. Кривая разгона по внутреннему каналу W2(S)
3. Регулирование по каналу W3(S), где открыли исполнительный механизм подачи хлоргаза на общей нитке хлоратора(3) на 20%, следовательно, общий расход хлора на хлоратор увеличился. В результате температура расплава выросла с 705°C до 745°С. Время регулирования – 750 сек. Время запаздывания – 55 сек.
Таблица 3. Координаты кривой разгона каналу возмущения
№ точки | время, с | температура расплава, С | № точки | время, с | температура расплава, С | № точки | время, с | температура расплава, С |
1 | 0 | 705.1 | 10 | 270 | 731.1 | 19 | 540 | 743.4 |
2 | 30 | 705.3 | 11 | 300 | 732.4 | 20 | 570 | 744.3 |
3 | 60 | 705.7 | 12 | 330 | 734.7 | 21 | 600 | 744.7 |
4 | 90 | 709.5 | 13 | 360 | 735.5 | 22 | 630 | 744.9 |
5 | 120 | 714.4 | 14 | 390 | 738.9 | 23 | 660 | 744.95 |
6 | 150 | 719.3 | 15 | 420 | 739.7 | 24 | 690 | 744.97 |
7 | 180 | 722.7 | 16 | 450 | 740.6 | 25 | 720 | 744.98 |
8 | 210 | 725.2 | 17 | 480 | 741.3 | 26 | 750 | 745 |
9 | 240 | 728.8 | 18 | 510 | 742.8 |
Рис. 3.12. Кривая разгона по каналу возмущения W3(S)
4. ОБРАБОТКА ЭКСПЕРИМЕНТАЛЬНЫХ ДАННЫХ
Обработку данных эксперимента будем проводить в программном пакете «Калькулятор передаточных функций».
С полученными данными проведем линеаризацию, с целью устранения повторяющихся точек. Далее проведем сглаживание. Затем проведем нормирование кривой разгона, то есть, приводим её к единичному виду. Далее сделаем аппроксимацию динамической характеристики по каждому каналу методом Симою. Определим передаточную функцию объекта.
После этого сделаем проверку аппроксимации в программном пакете «Калькулятор передаточных функций». Полученный переходный процесс сравним с кривой разгона, высчитаем приведенную погрешность.
Проверка аппроксимации динамической характеристики по каждому каналу методом Симою показала, что приведенная погрешность составила менее 5%, таким образом, полученная передаточная функция может использоваться для дальнейших расчетов.
После обработки экспериментальных данных были получены передаточные функции:
Таблица 4. Сводная таблица передаточных функций
![]() | По основному каналу W1(S) - изменение температуры расплава при изменении положения регулирующего органа подачи пульпы |
![]() | По внутреннему каналу W2(S) - изменение расхода пульпы при изменении положения регулирующего органа подачи пульпы |
![]() | По каналу возмущения W3(S) - изменение температуры расплава при увеличении расхода анодного хлоргаза |
5. РАСЧЕТ СИСТЕМЫ РЕГУЛИРОВАНИЯ
Оптимальный регулятор будем считать в приложении «Simulink» программы «MATLAB». Для этого построим модель исследуемой системы регулирования и внутри нее рассчитаем передаточную функцию регулятора с помощью блока «PID-TUNER». Повторим эти действия для расчета параметров регуляторов одноконтурной и каскадной систем регулирования.
5.1. Расчет оптимальных настроечных параметров регулятора в одноконтурной системе
Рис.5.1. Структурная схема одноконтурной системы регулирования
Где: Xвх – входное воздействие (заданная температура расплава в хлораторе);
Xвых – выходная величина (температура расплава в хлораторе);
Wр1(S) – передаточная функция регулятора;
W1(S) – передаточная функция объекта регулирования.
Передаточная функция по основному каналу W1(S) - изменение температуры расплава при изменении положения регулирующего органа подачи пульпы:
Время чистого запаздывания t = 60 сек
Коэффициент передачи объекта Кп.о = 0,4625. Передаточная функция ПИ – регулятора:
Результаты расчета оптимальных настроек регулятора по основному каналу занесем в таблицу 8.
Таблица 5. Оптимальные настройки регулятора по основному каналу W1(S).
Показатель | Обозначение | Величина |
Коэффициент пропорциональности | ![]() | 2,0829 |
Время интегрирования | ![]() | 105,8196 |
Вид передаточной функции ПИ - регулятора | |
5.2. Расчет оптимальных настроечных параметров стабилизирующего и корректирующего регуляторов в каскадной системе регулирования
Рис.5.2. Структурная схема каскадной системы регулирования
Где:
Xвх– входное воздействие (заданная температура расплава в хлораторе);
Xвых– выходная величина (температура расплава в хлораторе);
WР1(S) – передаточная функция ведущего регулятора;
WР2(S) – передаточная функция ведомого регулятора;
W1(S) – передаточная функция объекта регулирования по основному контуру;
W2(S) – передаточная функция объекта регулирования по внутреннему контуру.
Каскадная система автоматического регулирования представляет собой систему, состоящую из двух контуров регулирования: внешнего (корректирующего) и внутреннего (стабилизирующего).
Порядок расчета:
1. Рассчитаем настройки ведомого регулятора аналогично расчету настроек основного регулятора одноконтурной АСР.
Время чистого запаздывания t = 30 с
Коэффициент передачи объекта Кп.о = 1,5
Передаточная функция ПИ – регулятора имеет вид:
Таблица 6. Предварительные настройки регулятора по внутреннему каналу W2(S)
Показатель | Обозначение | Величина |
Коэффициент пропорциональности | ![]() | 0.251 |
Время интегрирования | ![]() | 205,156 |
Вид передаточной функции ПИ - регулятора | |
Определим передаточную функцию эквивалентного объекта.
Построим в приложении «Simulink» программы «MATLAB» в одной системе координат переходный процесс во внутреннем контуре по возмущению и сопоставим его с динамической характеристикой внешнего контура (Рис.43-44).
Рис.5.3. Моделирование: сравнение переходных процессов в контурах W1(S) и W2(S).
Рис.5.4.
1)График переходного процесса во внутреннем контуре W2(S) по возмущению;
2)нормированная динамическая характеристика внешнего контура W1(S).
По кривым переходных процессов (Рис.5.4) видно, что за время запаздывания основного контура W1(S), который показан сплошной линией, переходный процесс во внутреннем контуре W2(S) не успевает полностью установиться.
Так как время регулирования превышает время запаздывания, переходные процессы во внутреннем контуре не успевают практически полностью затухнуть до того, как они возникнут во внешнем контуре, следовательно, передаточная функция эквивалентного объекта для регулятора WР1 (S) имеет вид:
Где:
WЭКВ(S) – передаточная функция эквивалентного объекта;
W1(S) – передаточная функция объекта регулирования по основному контуру
;
W2(S) – передаточная функция объекта регулирования по внутреннему контуру
;
WР2(S) – передаточная функция ведомого регулятора внутреннего канала
С помощью программы “MATLAB” в командном окне рассчитаем передаточную функцию эквивалентного объекта. После преобразований функция принимает следующий вид:
3. По передаточной функции эквивалентного объекта определим настройки ведущего регулятора. Занесем результаты расчета оптимальных настроек регулятора Wрэкв(S) в таблицу 7. Передаточная функция ПИ – регулятора имеет вид:
Таблица 7. Оптимальные настройки стабилизирующего регулятора Wрэкв(S)
Показатель | Обозначение | Величина |
Коэффициент пропорциональности | ![]() | 3,2098 |
Время интегрирования | ![]() | 72,2046 |
Вид передаточной функции ПИ - регулятора | |
Для того чтобы корректирующий регулятор более качественно выполнял задачу по устранению возмущений, настроим его внутри каскадной схемы, не отключая при этом стабилизирующий регулятор. Для этого снова воспользуемся блоком «PID-TUNER», нажав на кнопку «TUNE».
Результаты расчета оптимальных настроек регулятора по внутреннему каналу занесем в таблицу 10.
Таблица 8. Оптимальные настройки регулятора по внутреннему каналу W2(S)
Показатель | Обозначение | Величина |
Коэффициент пропорциональности | ![]() | 0.522 |
Время интегрирования | ![]() | 433,655 |
Вид передаточной функции ПИ - регулятора | |
5.3. Расчет комбинированной системы регулирования
Рис.5.5. Структурная схема комбинированной системы регулирования
Где:
Xвх– входное воздействие (заданная температура расплава в хлораторе);
Xвых– выходная величина (температура расплава в хлораторе);
Xв– возмущающее воздействие (расход хлора);
WР1(S) – передаточная функция ведущего регулятора;
WР2(S) – передаточная функция ведомого регулятора;
W1(S) – передаточная функция объекта регулирования по основному контуру;
W2(S) – передаточная функция объекта регулирования по внутреннему контуру;
W3(S) – передаточная функция объекта по каналу возмущения;
WК(S) – передаточная функция устройства ввода возмущения.
На систему воздействует дополнительное возмущающее воздействие – расход хлора. Добавочное звено, которое появилось на этой схеме, является компенсатором возмущения, через который проходит возмущающее воздействие, прежде чем войти в систему в виде управляющего воздействия.
Одноконтурная и каскадная системы автоматического регулирования не являются универсальными, поскольку в реальных системах на объект действуют различные возмущающие воздействия, которые отклоняют значение измеряемой величины, а с помощью одноконтурной и каскадной систем невозможно достичь полной ликвидации отклонения регулируемой величины от заданного значения. Поэтому целесообразно использовать комбинированную систему, в которую вводится специальное устройство – компенсатор. Он способен устранить возмущающее воздействие, влияющее на отклонение регулируемой величины от заданного значения
Передаточная функция компенсатора:
Где:
WК(S) – передаточная функция устройства ввода возмущения;
W3(S) – передаточная функция объекта по каналу возмущения
;
WРэкв(S) – передаточная функция ведущего регулятора каскадной АСР
;
WЭКВ(S) – передаточная функция эквивалентного объекта каскадной АСР
С помощью программы “MATLAB” рассчитаем передаточную функцию идеального компенсатора:
После того, как получили передаточную функцию идеального компенсатора (фильтра), рассчитаем реальное дифференцирующее звено. Отбросим коэффициенты передаточной функции идеального компенсатора при старших степенях оператора Лапласа. Получим передаточную функцию компенсатора в виде реального дифференцирующего звена следующего вида:
Преобразуем функцию так, чтобы последнее слагаемое знаменателя равнялось единице. Для этого умножим числитель и знаменатель передаточной функции на 9,0497. В результате получим следующую передаточную функцию:
Произведем расчет настроечных параметров компенсирующего устройства вторым способом. Для этого воспользуемся программой “Калькулятор передаточных функций”. Зададим коэффициенты передаточной функции идеального компенсатора (Рис.7.9.), определим настройки. Результаты расчета занесем в таблицу 7.4.
Рис. 5.6. Расчет частотных характеристик компенсатора
Таблица 9. Значения АФХ передаточной функции компенсатора.
Частота | Вещественная составляющая U | Мнимая составляющая V |
![]() | 0,00000 | 0,00000 |
![]() | 0,02000 | 0,36932 |
Коэффициенты реального дифференцирующего звена рассчитаем графическим методом по Ротачу с помощью расширенной версии калькулятора передаточных функций. Запустим калькулятор. Откроем меню «Расчет компенсатора методом Ротача» (Рис.5.7.).
Рис. 5.7. Калькулятор передаточных функций. Расширенная версия. Панель выбора функций.
Введем в поле «исходные данные» значения резонансной частоты, а также полученной для нее действительной и мнимой части (Рис. 5.8).
Рис. 5.8. Калькулятор передаточных функций. Расчет компенсатора методом Ротача.
Нажмем на кнопку «вычислить» и калькулятор графически рассчитает параметры построения и вычислит значения формулы для реального дифференцирующего звена. Подставим полученные значения Кd и Тd в следующую формулу:
Получена передаточная функция реального дифференцирующего звена, рассчитанного методом Ротача.
Как видно из графиков, представленных на рисунке 5.9, регулятор с реальным дифференцирующим звеном, рассчитанным по Ротачу и методом отброса старших коэффициентов, недостаточно хорошо справляется с возмущением. Регулятор имеет большое время регулирования (600 сек.) и динамическую ошибку (27%). Подберем коэффициенты передаточной функции реального дифференцирующего звена вручную.
Передаточная функция компенсатора, подобранная вручную, будет иметь вид:
Введем полученную передаточную функцию в структурную схему, представленную на рисунке 5.10. Посмотрим, как справляются с устранением возмущающих воздействий все рассчитанные выше нами компенсаторы. Для этого смоделируем их работу в приложении «Simulink» программы «MATLAB». Сравним графики переходных процессов (Рис.5.11.).
Рис. 5.10. Структурная схема. Сравнение работы рассчитанных компенсирующих устройств
Рис.5.11 . Переходные процессы по возмущению в системах регулирования: 1) без компенсатора; 2) c компенсатором, рассчитанным по методу Ротача; 3) c компенсатором, рассчитанным методом отброса коэффициентов передаточной функции идеального компенсатора при старших степенях оператора Лапласа; 4) с идеальным компенсатором;
5) с компенсатором, коэффициенты которого подобраны вручную.
6. МОДЕЛИРОВАНИЕ РАССЧИТАННОЙ СИСТЕМЫ РЕГУЛИРОВАНИЯ
Моделирование проводится с помощью программы “MATLAB”. Данный программный продукт предназначен для моделирования автоматических систем регулирования.
6.1. Переходные процессы в одноконтурной системе регулирования
Для моделирования переходных процессов одноконтурной системы регулирования по управлению и по возмущению воспользуемся пакетом Simulink программы MATLAB.
Рис.6.1. Структурная схема одноконтурной системы регулирования
Step upravlenie – блок, моделирующий единичный ступенчатый сигнал по управлению;
Step vozmuzchenie – блок, моделирующий единичный ступенчатый сигнал по возмущению;
Input Perturbation - точка подачи возмущающих воздействий анализатора Linear Analysis;
Output Measurement - точка снятия возмущающих воздействий анализатора Linear Analysis;
Scope – блок, моделирующий графическое отображение сигналов во времени;
- блок реализации вычитания двух сигналов;
- блок реализации сложения двух сигналов;
W1(S) – передаточная функция объекта регулирования по основному контуру;
;
Wр1(S) – на Рис. название «PID stabilizator» - передаточная функция регулятора по основному контуру;
W1(S) delay - блок, моделирующий запаздывание объекта регулирования по каналу W1(S);
Построим график переходного процесса по управлению (внешнего контура W1(S)) одноконтурной системы регулирования при оптимальных настройках ПИ-регулятора (Рис.6.2).
Рис.6.2. График переходного процесса одноконтурной системы по управлению
(внешний контур)
Показатели качества регулирования:
Время регулирования:
Т= 926 с.
Перерегулирование:
Степень затухания:
Построим график переходного процесса (внешнего контура W1(S)) по возмущению одноконтурной системы регулирования при оптимальных настройках ПИ-регулятора (Рис.6.3).
Рис.6.3. График переходного процесса одноконтурной системы по возмущению
(внешний контур)
Показатели качества регулирования:
Время регулирования:
Т= 1250 с.
Динамическая ошибка регулирования:
Степень затухания:
6.2. Переходные процессы во внутреннем контуре
Для моделирования переходных процессов одноконтурной системы регулирования по управлению и по возмущению воспользуемся пакетом Simulink программы MATLAB.
Step upravlenie – блок, моделирующий единичный ступенчатый сигнал по управлению;
Step vozmuzchenie – блок, моделирующий единичный ступенчатый сигнал по возмущению;
Input Perturbation - точка подачи возмущающих воздействий анализатора Linear Analysis;
Output Measurement - точка снятия возмущающих воздействий анализатора Linear Analysis;
Scope – блок, моделирующий графическое отображение сигналов во времени;
- блок реализации вычитания двух сигналов;
- блок реализации сложения двух сигналов;
W2(S) delay - блок, моделирующий запаздывание объекта регулирования по каналу W2(S);
W2(S) – передаточная функция объекта регулирования внутреннего контура;
Wр2(S) - на Рис. название «PID correct» – передаточная функция регулятора внутреннего контура;
Рис.6.4. Структурная схема одноконтурной системы регулирования (внутренний контур)
Построим график переходного процесса по управлению внутреннего контура регулирования при оптимальных настройках ПИ-регулятора (Рис.6.5).
Рис.6.5. Переходный процесс по управлению во внутреннем контуре канала W2(s)
Показатели качества регулирования:
Время регулирования:
Т= 425 с.
Перерегулирование:
Степень затухания:
Построим график переходного процесса по возмущению одноконтурной системы регулирования канала W2(S) при оптимальных настройках ПИ-регулятора (Рис.6.6).
Рис.6.6. Переходный процесс по возмущению во внутреннем контуре канала W2(s)
Показатели качества регулирования:
Время регулирования:
Т= 577 с.
Динамическая ошибка регулирования:
Степень затухания:
6.3. Переходные процессы в каскадной системе регулирования
В приложении «Simulink» программы «MATLAB» построим схему каскадной модели регулирования (Рис.6.7).
Рис.6.7. Структурная схема каскадной системы регулирования
Step upravlenie – блок, моделирующий единичный ступенчатый сигнал по управлению;
Step vozmuzchenie – блок, моделирующий единичный ступенчатый сигнал по возмущению;
Input Perturbation - точка подачи возмущающих воздействий анализатора Linear Analysis;
Output Measurement - точка снятия возмущающих воздействий анализатора Linear Analysis;
Scope – блок, моделирующий графическое отображение сигналов во времени;
- блок реализации вычитания двух сигналов;
- блок реализации сложения двух сигналов;
W1(S) delay - блок, моделирующий запаздывание объекта регулирования по каналу W1(S);
W2(S) delay - блок, моделирующий запаздывание объекта регулирования по каналу W2(S);
W1(S) – передаточная функция объекта регулирования по основному контуру;
;
W2(S) – передаточная функция объекта регулирования внутреннего контура;
Wрэкв(S) – на Рис. название «PID ekv (stabil)» - передаточная функция регулятора по основному контуру, настройки которого адаптированы для каскадной системы регулирования;
Wр2(S) - на Рис. название «PID correct» – передаточная функция регулятора внутреннего контура после оптимизации внутри каскадной системы регулирования;
Построим переходные процессы по управлению (Рис.6.8) и возмущению (Рис.6.9) в каскадной системе регулирования.
Рис.6.8. Переходный процесс каскадной системы по управлению.
Показатели качества регулирования:
Время регулирования:
Т= 1480 с.
Перерегулирование:
Степень затухания:
Рис.6.9. Переходный процесс каскадной системы по возмущению.
Показатели качества регулирования:
Время регулирования:
Т= 1710 с.
Динамическая ошибка регулирования:
Степень затухания:
6.4. Переходные процессы по возмущению в каскадно-комбинированной системе регулирования без компенсирующего устройства и с компенсирующим устройством.
Построим модель комбинированной системы регулирования без компенсатора.
Рис. 6.10. Структурная схема каскадно-комбинированной АСР без компенсатора.
Step upravlenie – блок, моделирующий единичный ступенчатый сигнал по управлению;
Step vozmuzchenie – блок, моделирующий единичный ступенчатый сигнал по возмущению;
Input Perturbation - точка подачи возмущающих воздействий анализатора Linear Analysis;
Output Measurement - точка снятия возмущающих воздействий анализатора Linear Analysis;
Scope – блок, моделирующий графическое отображение сигналов во времени;
- блок реализации вычитания двух сигналов;
- блок реализации сложения двух сигналов;
W1(S) – передаточная функция объекта регулирования по основному контуру;
;
W2(S) – передаточная функция объекта регулирования внутреннего контура;
W3(S) – передаточная функция канала по возмущению;
Wрэкв(S) – на Рис. название «PID stabil» - передаточная функция регулятора по основному контуру, настройки которого адаптированы для каскадной системы регулирования;
Wр2(S) - на Рис. название «PID correct» – передаточная функция регулятора внутреннего контура после оптимизации внутри каскадной системы регулирования;
W1(S) delay - блок, моделирующий запаздывание объекта регулирования по каналу W1(S);
W2(S) delay - блок, моделирующий запаздывание объекта регулирования по каналу W2(S);
W3(S) delay - блок, моделирующий запаздывание объекта регулирования по каналу W3(S);
Получим график переходного процесса по возмущению в комбинированной системе регулирования без компенсирующего устройства (Рис. 8.11).
Рис. 6.11. График переходного процесса по возмущению в каскадно-комбинированной
системе без компенсатора
Показатели качества регулирования:
Время регулирования:
Т= 1620 с.
Динамическая ошибка регулирования:
Степень затухания:
Построим модель каскадно-комбинированной системы регулирования с компенсатором:
Рис. 6.12. Структурная схема каскадно-комбинированной АСР с компенсатором
Step upravlenie – блок, моделирующий единичный ступенчатый сигнал по управлению;
Step vozmuzchenie – блок, моделирующий единичный ступенчатый сигнал по возмущению;
Input Perturbation - точка подачи возмущающих воздействий анализатора Linear Analysis;
Output Measurement - точка снятия возмущающих воздействий анализатора Linear Analysis;
Scope – блок, моделирующий графическое отображение сигналов во времени;
- блок реализации вычитания двух сигналов;
- блок реализации сложения двух сигналов;
- блок реализации сложения нескольких сигналов;
W1(S) – передаточная функция объекта регулирования по основному контуру;
;
W2(S) – передаточная функция объекта регулирования внутреннего контура;
W3(S) – передаточная функция канала по возмущению;
Wк(S) podbor – передаточная функция компенсатора (реального дифференцирующего звена);
Wрэкв(S) – на Рис. название «PID stabil» - передаточная функция регулятора по основному контуру, настройки которого адаптированы для каскадной системы регулирования;
Wр2 opt(S) - на Рис. название «PID correct» – передаточная функция регулятора внутреннего контура после оптимизации внутри каскадной системы регулирования;
W1(S) delay - блок, моделирующий запаздывание объекта регулирования по каналу W1(S);
W2(S) delay - блок, моделирующий запаздывание объекта регулирования по каналу W2(S);
W3(S) delay - блок, моделирующий запаздывание объекта регулирования по каналу W3(S);
Получим график переходного процесса по возмущению в комбинированной системе регулирования с компенсирующим устройством (Рис.8.13).
Рис. 6.13. График переходного процесса по возмущению в каскадно-комбинированной АСР с компенсатором.
Показатели качества регулирования:
Время регулирования:
Т= 1700 с.
Динамическая ошибка регулирования:
Степень затухания:
7. АНАЛИЗ КАЧЕСТВА ПЕРЕХОДНЫХ ПРОЦЕССОВ И ВЫБОР СИСТЕМЫ РЕГУЛИРОВАНИЯ
Для выбора АСР проведем сравнительный анализ систем регулирования, расчет и моделирование которых производились в п.7 и п.8. Необходимо сравнить переходные процессы одноконтурной системы, каскадной, каскадной системы без компенсатора и с компенсатором.
7.1 Анализ качества переходных процессов одноконтурной системы
Для получения передаточной функции замкнутой одноконтурной системы по управлению воспользуемся формулой:
где:
– передаточная функция одноконтурной системы по управлению;
- передаточная функция объекта управления одноконтурной системы;
– передаточная функция регулятора.
Для получения передаточной функции замкнутой одноконтурной системы по возмущению воспользуемся формулой:
где:
– передаточная функция одноконтурной системы по управлению;
- передаточная функция объекта управления одноконтурной системы;
– передаточная функция регулятора.
Построение графиков осуществляется в программе Mathcad. Для определения резонансной частоты построим амплитудно-частотные характеристики системы по управлению и возмущению.
Рис. 7.1. АЧХ одноконтурной САР по управлению
По графику АЧХ (Рис.7.1.) получили: ωр = 0,007 с-1.
По графику переходного процесса (рисунок 6.2): Т = 926 с.
Произведем проверку переходного процесса по резонансной частоте:
где:
Т – период колебания переходного процесса;
ωр – резонансная частота замкнутой системы;
Периоды расчитанный и определенный по графику приблизительно равны, следовательно, график переходного процесса одноконтурной САР по управлению правильный.
Рис. 7.2. АЧХ одноконтурной САР по возмущению
По графику АЧХ (Рис. 7.2.) получили: ωр = 0,005 с-1.
По графику переходного процесса (рисунок 6.3): Т = 1250 с.
Произведем проверку переходного процесса по резонансной частоте:
где:
Т – период колебания переходного процесса;
ωр – резонансная частота замкнутой системы;
Периоды рассчитанный и определенный по графику равны, следовательно, график переходного процесса одноконтурной САР по управлению правильный.
7.2 Анализ качества переходных процессов каскадной системы
Для получения передаточной функции замкнутой одноконтурной системы по управлению воспользуемся формулой:
где:
– передаточная функция каскадной системы по управлению;
- передаточная функция эквивалентного объекта каскадной системы;
– передаточная функция регулятора.
Для получения передаточной функции замкнутой каскадной системы по возмущению воспользуемся формулой:
где:
– передаточная функция каскадной системы по управлению;
- передаточная функция эквивалентного объекта каскадной системы;
– передаточная функция регулятора.
Построение графиков осуществляется в программе MathCad. Для определения резонансной частоты построим амплитудно-частотные характеристики системы по управлению и возмущению.
Рис. 7.3. АЧХ каскадной САР по управлению
По графику АЧХ (Рис.7.3.) получили: ωр = 0,0055 с-1.
По графику переходного процесса (рисунок 6.8): Т = 1090 с.
Произведем проверку переходного процесса по резонансной частоте:
где:
Т – период колебания переходного процесса;
ωр – резонансная частота замкнутой системы;
Периоды рассчитанный и определенный по графику приблизительно равны, следовательно, график переходного процесса каскадной САР по управлению правильный.
Рис. 7.4. АЧХ каскадной САР по возмущению
По графику АЧХ (Рис. 7.4.) получили: ωр = 0,0035 с-1.
По графику переходного процесса (рисунок 6.9): Т = 1710 с.
Произведем проверку переходного процесса по резонансной частоте:
где:
Т – период колебания переходного процесса;
ωр – резонансная частота замкнутой системы;
Периоды рассчитанный и определенный по графику приблизительно равны, следовательно, график переходного процесса каскадной САР по возмущению правильный.
7.3. Сравнение качества переходных процессов одноконтурной и каскадной систем регулирования
Качество переходных процессов определяется следующими показателями:
1. Динамическая ошибка – это максимальное отклонение регулируемой величины от заданного значения -
2. Время регулирования – это время, в течение которого регулируемая величина достигнет нового установившегося значения с заданной точностью. Время регулирования равно 5% от установившегося значения.
3. Перерегулирование – это максимальное отклонение регулируемой величины от заданного значения, выраженное в процентах.
5. Степень затухания – это относительное уменьшение амплитуды колебания.
, где А1 и А3 – это соседние амплитуды колебаний, направленные в одну сторону.
Для сравнения сведем полученные показатели качества в таблицу:
Таблица 10.
Сравнение показателей рассчитанных систем автоматического регулирования
Показатели | Одноконтурная САР | Каскадная САР | Каскадная САР без компенсатора | Каскадная САР с компенсатором | ||
по возм. | по упр. | по возм. | по упр. | по возм. | по возм. | |
Динамическая ошибка,% | 26 | - | 16 | - | 14 | 1,39 |
Время регулирования, с | 1250 | 926 | 1710 | 1480 | 1620 | 1700 |
Перерегулиро- вание, % | - | 9 | - | 4 | - | - |
Степень затухания, % | 98 | 77 | 97 | 75 | 97 | 97 |
На Рис. 7.5 представлена совокупная модель, состоящая из двух одноконтурной АСР и каскадной АСР. На Рис. 7.7 показана модель комбинированных САР с компенсатором и без компенсатора. Для визуальной оценки переходных процессов различных систем управления представим их в одной системе координат.
Рис.51. Совокупная модель одноконтурной АСР (внешнего и внутреннего контура) и каскадной АСР
Рис. 7.4. Сравнение переходных процессов по управлению
1) в одноконтурной и 2) каскадной САР
Рис. 7.5. Сравнение переходных процессов по возмущению
1) в одноконтурной и 2) каскадной САР
Рис. 7.6. Сравнение переходных процессов по возмущению в
комбинированной САР с компенсатором и без компенсатора
Вывод:
Вывод: исходя из полученных данных (Рис.7.4,7.5) видно, что значение динамической ошибки регулирования в каскадной САР значительно меньше, чем в одноконтурной. Следовательно, применение каскадной САР предпочтительнее, чем использование одноконтурной САР. При наличии внешнего возмущения каскадно-комбинированная система регулирования с компенсатором справляется лучше, чем без компенсатора (Рис.7.6.) Убедившись в том, что введение дополнительного регулятора в каскадной системе даёт улучшение качества переходных процессов (в данном случае уменьшилось значение динамической ошибки регулирования), принимаем решение использовать каскадно-комбинированную систему регулирования с компенсатором.
8. РЕАЛИЗАЦИЯ РАСЧИТАНОЙ СИСТЕМЫ РЕГУЛИРОВАНИЯ
8.1. Обоснование выбранных программных и технических средств
В данном проекте рассчитаны системы автоматического регулирования: одноконтурная и каскадная. Которые состоят из каналов:
- внутреннего (зависимость расхода пульпы от положения регулирующего органа);
- основного (зависимость температуры расплава от положения регулирующего органа);
- канала по возмущению (зависимость температуры расплава от подачи шихты).
Проанализировав полученные характеристики и качество полученных переходных процессов, к реализации была принята каскадная система автоматического регулирования.
В процессе получения тетрахлорида титана при проектировании хлорирующей установки закладывается автоматический контроль и управление. Процесс получения продукта в хлораторах является непрерывным, что создает условие для его автоматизации. Все значения контролируемых величин обрабатываются в контроллере и выводятся с помощью кабеля по интерфейсу RS-232 на ПЭВМ. Составим структурную схему управления данным технологическим процессом.
Составим структурную схему управления данным технологическим процессом.
Рис. 8.1. Структурная схема АСУТП
На 1 уровне: располагаются датчики, исполнительные механизмы. На этом уровне собирается первичная информация о технологическом процессе. Они располагаются вблизи объекта управления.
На 2 уровне: находится промышленный микропроцессорный контроллер CompactLogix 1769-L31. На этом уровне полученные с датчиков сигналы обрабатываются в устройствах связи с объектом. Устройства связи с объектом представляют собой модули ввода (1769-IT6, 1769-IR6, 1769-IF4, 1769-OB32) и вывода (1769-OF2), они соединяются с контроллером по системной шине через разъемы находящиеся в корзине.
На 3 уровне: Установлено АРМ оператора-технолога, на котором установлено специальное программное обеспечение, с его помощью оператор или диспетчер получает информацию о ходе технологического процесса. На этом уровне осуществляется диспетчерское управление и сбор данных от контроллера, их обработка и отображение результатов на АРМ оператора. Производится накопление обработанных результатов.
Реализация выполнена на контроллере CompactLogix 1769-L31.
Контроллер CompactLogix отличается от контроллеров своего семейства Logix, тем что он малогабаритный, используется в небольших производствах и имеет цену на порядок ниже своих старших собратьев.
Система CompactLogix это:
Единая – допускает простую интеграцию с существующими системами на основе PLC. Пользователи могут посылать или передавать сообщения к программам контроллера или от них, используя прозрачность сетей.
Быстрая – платформа CompactLogix поддерживает быструю передачу данных по задней шине шасси, обеспечивая тем самым быстродействующее управления.
Масштабируемая – обеспечивает модульный подход к управлению. Установив столько контроллеров и коммуникационных модулей, сколько необходимо, можно построить мультипроцессорную систему в одном шасси. Можно выбрать объем памяти контроллера, который необходим для выполнения прикладной программы.
Промышленная - предложенная аппаратная платформа разработана так, чтобы противостоять вибрации, экстремальным температурам и электрическому шуму, связанному с тяжёлыми промышленными условиями.
Интегрированная - установленная платформа включает в себя разнообразные технологии управления – управление последовательными и непрерывными процессами,
управление приводами и движением.
Компактная - отвечает потребностям множества применений, где управление сильно распределено.
Архитектура системы CompactLogix
Обеспечивая управление последовательными и непрерывными процессами, управление движением в сочетании с коммуникациями и современным вводом-выводом, позволяет получить компактную, конкурентную по цене платформу. Система является модульной, так что можно эффективно её проектировать, монтировать и модифицировать - при значительной экономии средств на обучение и проектирование.
Система CompactLogix может быть чем угодно - начиная от простого шасси до широко развернутой системы, состоящей из множества шасси и сетей, работающих совместно.
Простая система CompactLogix состоит из одиночного контроллера и модулей ввода-вывода в одном шасси, эта система будет применена к данному курсовому проекту.
Целью реализации является выполнение следующих задач регулирования:
- коррекция задания внутреннего регулятора в зависимости от изменения температуры расплава;
- стабилизация расхода пульпы орошения, которая будет осуществляться во внутреннем контуре предлагаемой каскадной схемы регулирования;
- коррекция возмущающего воздействия, расход хлора, оказывающего возмущение на работу схемы регулирования.
Для контроллера CompactLogix 1769-L31, выбираются следующие блоки, расположенные все в одной корзине:
1. 1769-IF4 – модуль ввода аналоговый, 4 канала (расход хлора и пульпы в хлоратор).
2. 1769-IT6 – модуль ввода аналоговый для термопар, 6-ти канальный.
2. 1769-IR6 – модуль ввода аналоговый для термометров сопротивления, 6-ти канальный.
3. 1769-OB32 – модуль ввода дискретный, для управления схемой сигнализации, 32 канала.
4. 1769-OF2 – модуль аналогового вывода, 2 канала, сигнал с которого, 4-20 mA идет на электропневмопреобразователь ЭП-3211, с которого пневматический сигнал 20-100 кПА приходит на исполнительный механизм МИМ-250 и регулирующий клапан изменяет свое положение.
4. 1769-РА – блок питания, подключается к промышленной сети переменного тока напряжением 220В - 240В с выходным напряжение 24В постоянного тока, питает контроллер и все его модули.
5. 1769-А4 – шасси (корзина), 4 слота, в ней расположены все модули контроллера, сам контроллер и блок питания для них; вся передача данных происходит по задней шине шасси.
Схема аппаратной и программной реализации представлена на отдельном формате А1. Рассмотрим и опишем программную реализацию.
Рис. 8.2. Программная реализация в CompactLogix, выполненная на релейной логике
Рис. 8.3. Реализация реального дифференцирующего звена, выполненная во встроенной подпрограмме, программы RSLogix 5000
Для начала описания программной реализации ознакомимся с инструкциями, которые будем применять.
Описание применяемых инструкций
MOV – эта инструкция является выходной, значение для перемещения (копирование). Инструкция MOV копирует источник (Source) в назначение (Destination). Источник остается неизменяемым.
Рис. 8.4. Инструкция перемещения MOV
СРТ – инструкция СРТ выполняет арифметические операции, которые определяются в выражении. Когда она разрешена, инструкция СРТ вычисляет выражение и помещает результат в назначении.
Преимущество математической инструкции СРТ над другими инструкциями в том, что она позволяет вам вводить сложные выражения в одну инструкцию, но она медленнее остальных.
Рис. 8.5. Математическая инструкция СРТ
Где: назначение (Destination) – тег для сохранения результата;
выражение (Expression) – выражение состоящее из тегов и/или непосредственных величин, разделенных операторами.
Эту инструкцию я использовал для того чтобы перевести числовые значения технологических параметров в проценты.
Используемая формула:
После преобразования:
%
Где - 0 %;
- максимальное значение, которое может измерить прибор;
- значение измеряемой величины в данный момент;
- 100 %;
- минимальное значение, которое может измерить прибор;
y - переведенное числовое значение в проценты.
JSR – эта инструкция выходная, позволяет переходить к отдельному файлу подпрограммы.
Рис. 8.6. Выходная инструкция JSR
Routine name – имя выполняемой подпрограммы.
В моем случае имя подпрограммы DERV, в ней выполняется расчет реально дифференцирующего звена каскадно-комбинированной АСР.
ADD – инструкция вычисления, производит математические, арифметические операции, используя выражение или специфическую арифметическую инструкцию.
Инструкция ADD является выходной.
Рис. 8.7. Выходная инструкция ADD
назначение (Destination)- тег для сохранения результата.
Инструкция ADD складывает источник В (Source В) с источником А (Source A) и помещает результат в назначении.
PID – закон ПИД регулирования (в нашем случае ПИ – закон регулирования).
Инструкция PID управляет переменной процесса. Инструкция PID получает переменную процесса (PV) из аналогового входного модуля и изменяет выход переменной
управления (CV) в аналоговом выходном модуле с целью поддержания переменной процесса возле желаемой уставки.
Рис. 8.8. Выходная инструкция PID
Где: Переменная процесса (Process variable) – вводится величина, которой хотим управлять;
Задание (Tieback) - выход аппаратной ручной/автоматической станции, который шунтирует выход контроллера; ввести 0, если не нужно использовать этот параметр.
Управляющая переменная (Control variable) – величина которая идет на конечное управляющее устройство (клапан, заслонка. и т.п..); если вы используете зону нечувствительности, то управляющая переменная должна быть REAL или она установится в 0, когда ошибка будет в пределах зоны нечувствительности.
Внешний контур ПИД (PID Master Loop) – PID тег внешнего контура ПИД; если используется подчиненное управление и этот ПИД - подчиненный контур, то ввести имя основного ПИД; ввести 0, если не нужно использовать этот параметр.
Бит установившегося значения (Inhold bit) – текущее состояние бита установившегося значения аналогового выходного канала 1769 для поддержки безударного включения регулятора; ввестие 0, если не нужно использовать этот параметр.
Установившееся значение (Inhold Value) – величина данных считанная из аналогового выходного канала 1769, для поддержки безударного включения регулятора;
ввести 0, если не нужно использовать этот параметр.
Уставка (Setpoint) – только для отображения, текущая величина уставки.
Переменная процесса (Process Variable) – только для отображения; текущая величина промасштабированной переменной процесса.
Выход % (Out put %) – только для отображения; текущее значение выхода в процентах.
В моем дипломном проекте я использую ПИ – закон регулирования.
Описание программной реализации
В инструкции MOV поступают сигналы от модулей ввода. Эта связь образовывается благодаря адресам, прописанным в модулях ввода. В каждой инструкции MOV прописан адрес соответствующего модуля, у модуля ввода для термопар 1769-IT6 адрес Local:3:I, у модуля ввода 1769-IF4:I адрес Local:1. В инструкциях также прописывается и номер канала модуля, на который приходит сигнал от датчиков, сигнал от термопары приходит на 0 – ой канал модуля 1769-IT6:I, сигнал расхода пульпы приходит на 0 – ой канал модуля 1769-IF4:I, сигнал расхода хлора приходит на первый канал модуля 1769-IF4:I.
Дальше инструкции MOV передают полученные данные от модулей в инструкции СРТ, в которых происходит пересчет этих данных в процентное отношение, с помощью формулы, прописанной в этой инструкции.
Инструкция JSR служит для перехода к подпрограмме DERIVATIVE, в которой реализуется реально дифференцирующее звено логикой функциональных блоков, это делается потому, что релейной логикой реально дифференцирующее звено не описывается.
После того как произвели пересчет величин в проценты, инструкция СРТ сохраняет полученные результаты в следующих инструкциях MOV из которых они уже приходят на регуляторы. Настроечные параметры регуляторов заносятся в них также, с помощью инструкции MOV.
Далее данные после регуляторов поступают в инструкцию СРТ, в которой прописывается адрес Local:2:О модуля вывода 1769-OF2.
Описание аппаратной схемы реализации каскадной системы
Температуру расплава в хлораторе буду измерять посредством термоэлектрического преобразователя ТХА (ГОСТ 6616-94), т.к. диапазон температур этого прибора: -40-1200 ˚С. Сигнал от термоэлектрического преобразователя (1а – измерение температуры расплава в хлораторе) приходит на вход 0-го канала термопарного модуля 1769-IT6. В нем происходит преобразование термоэдс в цифровой сигнал, который через внутреннюю шину шасси поступает в процессорный модуль контроллера CompactLogix 1769-L31.
Для того чтобы измерять расход пульпы, подаваемой в хлоратор, будем использовать диафрагму ДКС 0,6-80-А/Б-1, камерная, исполнение 1, условное давление 0,6 МПа, условный диаметр: 80 мм и датчик давления Метран–150 CD, выходной сигнал 4-20 мА.
На входы (канал 0, канал 1) модуля 1769-IF4 приходят унифицированные токовые сигналы (4 – 20 mA): расход хлора и расход пульпы в хлоратор. Далее сигналы через внутреннюю шину шасси поступает в процессорный модуль контроллера CompactLogix 1769-L31.
В контроллере происходит обработка всех сигналов, дальше они из контроллера через внутреннюю шину шасси поступают на вход модуля вывода унифицированных аналоговых сигналов 1769-OF2, где происходит преобразование сигнала из цифрового в аналоговый и через канал 0 унифицированный токовый сигнал в виде управляющего воздействия поступает на вход электропневмопреобразователя ЭП-3211, в котором токовый сигнал преобразуется в пневматический и поступает на исполнительный механизм МИМ-250, который приводит в действие регулирующий клапан подачи хлора в хлоратор.
Питание контроллера и всех модулей ввода – вывода, осуществляется от блока питания Power Supply 1769-РА4 через заднюю шину шасси. Сам блок питания питается от промышленной сети переменного тока напряжением 220-240В, выходное напряжение 24В постоянного тока.
Для того чтобы осуществить передачу данных с контроллера на верхний уровень – ПЭВМ, используется шина RS–232. На третьем уровне находиться компьютер со SCADA - системой, которая осуществляет сбор информации и диспетчерское управление. SCADA - система выполнена на базе программы RS View.
RS View обменивается информацией с контроллерами фирмы Allen-Bradley с помощью собственного драйвера, обеспечивая высокий уровень целостности данных и производительности.
С помощью компонентов программы RS View можно выполнять следующие действия:
- создавать графические объекты и анимировать их;
- производить контроль сигналов тревоги, просматривать отчеты о тревогах;
- регистрировать данные, отслеживать информацию о системе в процессе ее работы;
- отслеживание трендов, визуальное представление значений тегов в реальном времени, это дает операторам возможность непосредственно отслеживать работу установки;
- можно установить защиту, с помощью которой будет ограничен доступ пользователей или групп пользователей к определенным действиям или запретить им изменять определенные значения тегов;
- можно произвести защиту на уровне системы, что позволяет заблокировать пользователей в приложении RS View, так, что они не смогли выйти в операционную систему Windows, это делается для того, что бы оператор не отвлекался от технологического процесса.
Рассмотрим как работать в программе RS View.
Работа в Project Manager (Менеджере проекта)
Project Manager является главным для работы с RSView. Всякий раз, когда создаем проект, появляется Project Manager с именем проекта.
Рис. 8.9. Окно программы
Окно Project Manager разделено на две панели. Когда вновь создаем проект, на левой панели появляется набор папок, а правая панель пустая. По мере создания компонентов проекта они появляются на правой панели.
Project Manager управляет компонентами, а не файлами. Компонент представляет собой ссылку на файл, или, иным словами, путь к физическому файлу. Этот путь может вести к файлу, находящемуся в папке под директорией проекта, к файлу за пределами директории проекта, или к файлу на другом компьютере.
Добавление компонентов к проекту.
Одни и те же файлы могут использоваться более чем в одном проекте, что достигается путем добавления к проекту компонентов с помощью опции Add Existing (добавить существующий). Когда добавляем компонент в Project Manager, мы не перемешаем файл в данный проект. Напротив. Мы создаем ссылку на местоположение этого файла. Когда выделяем компонент на правой панели Project Manager, путь к данному файлу появляется в линейке состояния.
Когда перемешаем файл, ссылка на файл нарушается и имя компонента в Project Manager закрашивается серым, пока не будет обновлена ссылка на этот файл. Для обновления ссылки на файл пользуемся опцией Add Existing.
Добавление компонента к проекту осуществляется следующим образом:
1. Нужно выбрать редактор, который использовался для создания нужного нам компонента. Например, чтобы добавить компонент графики, нужно выделить редактор графических изображений (Graphic Display).
2. Щелкнем правой кнопкой мыши для вывода на экран контекстного меню, и щелкнем на Add Existing.
3. Найдем компонент, который мы хотитим добавить, в диалоговом окне Add Existing Component File (добавить существующий файл-компонент), и щелкнем на Open (открыть). Нужный компонент появится в правой панели Project Manager.
Переименование компонента
Переименование компонента изменяет имя физического файла. Если изменить имя файла, к которому обращается другой проект, этот компонент (ссылка на файл) будет закрашен серым. Для обновления ссылки на такой файл, нужно выбрать Reference (ссылку) в Project Manager, щелкнуть на Rename (переименовать), и напечатать новое имя файла.
Для переименования компонента:
1. Выбрать компонент на правой панели Project Manager.
2. Щелкнуть правой кнопкой мыши, затем щелкнуть на Rename (переименовать).
Рис. 8.10. Окно переименования файла
3. Нужно напечатать новое имя в поле То (куда).
4. Щелкнуть на ОК.
Удаление компонента
Если больше ненужно использовать какой-либо файл в проекте. Можно удалить его из соответствующего проекта этот компонент (ссылку на файл), используя команду Remove (удалить).
При выполнении этой команды компонент (ссылка на файл) удаляется из Project Manager. Это не влияет на физический файл.
Для удаления компонента:
1. Выбрать компонент на правой панели Project Manager.
2. Щелкнуть правой кнопкой мыши, затем щелкните на Remove (удалить).
Подсоединение к устройствам производства Allen-Bradley
Для подсоединения к устройствам производства Allen-Bradley, RSView использует прямое соединение с драйверами RSLinx и WINtelligent LINX.
Осуществление связи с помощью прямых драйверов
Связь посредством прямых драйверов осуществляется с участием:
каналов
- устройств связи программного обеспечения драйверов связи (RSLinx или WINtelligent LINX)
- узлов (устройств управления)
Ниже на рисунке 9.9 показана станция RSView с ее каналами и узлами.
Рис. 8.11. Станция RSView с каналами и узлами
Канал связи
Канал связи представляет собой соединительный элемент между станцией RSView и сетью, к которой присоединены программируемые контроллеры.
Устройство связи - устройство связи соединяет каналы связи с компьютером. Можно использовать внутренние устройства, или внешние устройства, присоединяемые через серийный порт.
Драйвер связи - драйвер связи представляет собой программное средство, обеспечивающее сообщение компьютера с устройством связи. Дня связи с программируемыми контроллерами производства Allen-Bradley нужно пользоваться RSLinx for Windows NT 3.51 или более поздней версии, а также WINtelligent LINX for Windows 95.
Узел (устройства управления) - узел представляет собой программируемый контроллер, присоединенный к магистрали или сети. Когда станция RSView будет создана, она должна периодически обновлять свою таблицу значений. Это делается путем сканирования ее узлов.
Установка связи с продуктами фирмы Allen-Bradley при отсутствии технических или программных средств - в RSView можно установить связь, даже если нет одного или всего из нижеперечисленного:
- инсталлированных драйверов RSLinx или WINtelligent LINX;
- инсталлированных соответствующих технических средств связи.
Краткое описание действий - выполнить нижеприведенные действия для установки прямой драйверной связи с программируемыми контроллерами производства Allen-Bradley.
1. Запустите RSView32 и создайте или откройте проект.
2. В редакторе Channel (канал) выберать канал и присвойте ему соответствующий тип сети.
В поле Primary Communication driver (основной драйвер связи) присвоить каналу драйвер. Если у нет загруженных драйверов, щелкните на None Loaded (ничего не загружено).
3. В редакторе Node (узел) создать узлы для каждого программируемого контроллера, с которым хотим установить связь.
4. Если нужно изменить частоту сканирования узлов по умолчанию, нужно открыть Scan Class (класс сканирования) и отредактировать классы сканирования.
5. В редакторе Tag Database (база тегов) создать теги. Для каждого тега выберать Device (устройство) в качестве источника данных и присвоить узлы и классы сканирования, которые задали.
6. Проконтролировать связь.
9. РАСЧЕТ РЕГУЛИРУЮЩЕГО ОРГАНА
Рис. 9.1. Схема трубопровода
Исходные данные
Регулируемая среда – пульпа.
Qmax = 60 м3/ч - максимальный расход
Qmin = 50 м3/ч - минимальный расход
Т = 210º С - рабочая температура
ρ = 850,43 кг/м3 - плотность пульпы при 150º С
μ = 0,425·10-6 МПа/с - вязкость пульпы при 150º С
Р0 = 0,5 МПа - абсолютное давление в трубопроводе в начале рабочего участка
Рк = 0,3 МПа - абсолютное давление в трубопроводе в конце рабочего участка
Р1 = 5,1 МПа – абсолютное давление перед РО
D = 80 мм
Расчет регулирующего органа:
1) Найдем коэффициент кинематической вязкости:
ν = μ/ρ = 0,425·10-6 /850,43=0,4997· 10-9 м²/с
2) Определим число Рейнольдса при максимальном расходе:
ReD = 0,354 · Qmax / ν · D = 0,354 · 60 / 0,4997 ·10-9 · 80 = 0,53131 · 109
0,53131 · 109 > 2320, значит поток турбулентный
3) Определим условие гидравлической гладкости трубопровода.
Гидравлически гладкими считаются трубопроводы, удовлетворяющие условию:
ReD < 27 · (D / n1)8/7 = 27 · (80 / 0,06)8/7 = 1,006 · 105, где n1 – выбирают по табл.6.9
ReD = 3,537 · 105 > 1,006 · 105
Так как трубопровод в данном случае не является гидравлически гладким, то коэффициент трения λ определяем по Рис. 6.21.
Итак: λ=0,0195
4) Считаем суммарную длину трубопровода:
L = 10 + 25 + 23 + 7 = 55 м
5) Находим среднюю скорость потока при максимальном расходе:
ν = 4 · Qmax / π · D2 = 4 · 60 / 3,14 · 0,01 · 6400 = 1,194 м/с
6) Определим потери давления на прямых участках трубопровода при расчетном максимальном расходе:
∆Рпр = (λ · ρ · L · ν2) / 2 · D = (0,0195 · 850,43 · 55 · 1,194 2) / 2 · 0,08 ·106 = =0,0081 МПа
7) Определим потери давления в местных сопротивлениях трубопровода:
∆Рм = ((ζвх + ζвых + 3 · ζ90°) · ρ · ν2) / 2 =
= ((0,3+1,0+1,0·3) · 850,43 · 1,1942) / 2 ·106 = 0,00261 МПа
ζвх =0,3
ζвых =1,0
ζ90° = 1,0
ζ – коэффициенты местных сопротивлений, которые определяем по табл.6.8 и табл.6.10.
8) Определим потери давления в линии:
∆Рл = ∆Рпр + ∆Рм = 0,0081 + 0,00261 = 0,0107 МПа
9) Определим потери давления в сети:
∆Рсети = ∆Р0 - ∆Р1 ± ∆Рr ,
где ∆Рr – гидростатический напор, соответствующий разности уровней верхней и нижней отметок трубопровода, знак «+» означает, что источник напора находится на верхней отметке.
∆Рr = ∆h · ρ = 13,7 · 850,43 ·10-6 = 0,01165 кгс/м2
∆Рсети = 0,5 – 0,3 - 0,01165 = 0,1883 МПа
10) Определим потерю давления в РО при максимальном расходе:
∆РРОmax = ∆Рсети - ∆Рл = 0,1883 – 0,0107 = 0,1776 МПа
11) Определим максимальную пропускную способность РО по:
12) Определяем условную пропускную способность РО из условия:
Кνy ≥ 1,2 · Кνmax = 1,2 · 41,52 = 49,824 м3/ч
По табл. 6.11 выбираем двухседельный РО с Кνу = 100 м3/ч и диаметром условного прохода РО Dy = 80 мм.
Так как Rey = 5,3131 · 108 > 2000 , то влияние вязкости на расход не учитываем и выбранный РО проверим на возможность возникновения кавитации.
13) Проверим РО на возможность возникновения кавитаций:
ζ у = 25,4 · / К²νy
где ζ у - коэффициент местного сопротивления выбранного РО
FУ - площадь сечения входного патрубка РО
FУ = π · /4 = 3,14 · 8²/4 = 50,24
ζ у = 25,4 · 50,24²/100² = 6,41
Ккав = 0,5 – коэффициент кавитации определим по кривой 1 Рис.6.23
14) Находим перепад давления, при котором возникает кавитация:
∆Ркав = Ккав ( Р0 - Рнщ ) = 0,5 · ( 5,1 – 0,03) = 2,53 кгс/см²
(1 Па = 1,02 ·10-5 кгс/см²)
Перепад давления при максимальном расчётном расходе ∆Рро = 1,4993 кгс/см²
Так как перепад давления в РО ∆РРО ≤ ∆Ркав, т.е. 1,6 ≤ 2,53 , следовательно выбираем РО с ранее найденной условной пропускной способностьюКνy. Выбранный РО обеспечит заданный расход жидкости.
15) Определим отношение перепада давления в линии к перепаду давления на РО при максимальном расходе:
n = ∆Рл / ∆РРОmax = 0,0107/0,1776 = 0,06
Уточним параметр « n » по формуле 6.23:
n' = n · (Кνy / Кνmax · ψ)2 = 0,06 · (100 / 41,52 · 1)2 = 0,35
где ψ = 1 – поправочный коэффициент на влияние вязкости по Рис.6.22.
16) Уточним значение перепада на РО по формуле 6.24:
∆Р'РО = ∆Рсети / (n' +1) = 0,1883/ (0,35+ 1) = 0,254 МПа
17) Определим уточненное значение максимального расхода через РО:
18) Определяем относительные значения расходов:
μmax = Qmax / Q'max = 60 / 172,82 = 0,35
μmin = Qmin / Q'max = 50 / 172,82 = 0,29
19) Определяем диапазон перемещений РО для n' = 0,35
с линейной пропускной характеристикой по Рис.6.15:
0,60 < S < 0,65
с равно-процентной пропускной характеристикой по Рис.6.16:
0,17 < S < 0,54
20) Определяем максимальное и минимальное значения коэффициента передачи для рабочего диапазона нагрузок на РО по Рис.6.19:
a) для линейной пропускной характеристики:
(dμ / dS)max = 0,54
(dμ / dS)min = 0,48
(dμ / dS)min / (dμ / dS)max = 0,48/0,54 = 0,89
б) для равнопроцентной пропускной характеристики:
(dμ / dS)max = 1,09
(dμ / dS)min = 1,04
(dμ / dS)min / (dμ / dS) max = 1,04/1,09 = 0,95
Так как 0,95 > 0,89, то выбираем РО с равнопроцентной пропускной характеристикой.
Вывод: На расхода пульпы выбираем РО с равнопроцентной пропускной характеристикой, с условной пропускной способностью Кνу = 100 м3/ч и диаметром условного прохода Dy = 80 мм. По этим данным из справочников выбираем клапан регулирующий двухседельный 25нж92нж – из нержавеющей стали, для температуры рабочей среды -40 – +200 °С.
|
10. СПЕЦИФИКАЦИЯ ИСПОЛЬЗУЕМЫХ ТЕХНИЧЕСКИХ СРЕДСТВ
Позиция | Наименование и техническая характеристика | Тип, марка, обозначение опросного листа | Код изделия | Завод- изготовитель | Единицы измерения | Количество | Масса,, кг | Примечание |
1 | 2 | 3 | 4 | 5 | 6 | 7 | 8 | 9 |
Температура расплава в хлораторе от 700 до 800 °С | ||||||||
1а | Преобразователь термоэлектрический, диапазон измеряемых температур от -40 до 1200 °С Номинальная статическая характеристика- К Длина монтажной части 2000мм Кварцевый чехол, d нар.=22.5 мм, д=2000 мм | ТХА ГОСТ 6616-94 | цех № 48 | шт | 1 | |||
Температура под сводом хлоратора от 600 до 700 °С | ||||||||
2а | Преобразователь термоэлектрический, диапазон измеряемых температур от -40 до 1200 °С Ном. статическая характеристика- К Длина монтажной части 1600 мм Кварцевый чехол, d нар.=22.5 мм, д=1600 мм | ТХА ГОСТ 6616-94 | цех № 48 | шт | 1 | |||
Температура расплава в пылеосалительной камере №1 от 300 до 360 °С | ||||||||
3а | Преобразователь термоэлектрический, диапазон измеряемых температур от -40 до 600 °С Номинальная статическая характеристика - L Длина монтажной части 1600 мм Кварцевый чехол, d нар.=22.5 мм, д=1600 мм | ТХК ГОСТ 6616-94 | цех № 48 | шт | 1 | |||
Температура над расплавом в пылеосалительной камере №1 от 300 до 400°С | ||||||||
8а | Преобразователь термоэлектрический, диапазон измеряемых температур от -40 до 600 °С Номинальная статическая характеристика - L Длина монтажной части 1600 мм Кварцевый чехол, d нар.=22.5 мм, д=1600 мм | ТХК ГОСТ 6616-94 | цех № 48 | шт | 1 | |||
Температура ПГС после пылеосадительной камеры №1 от 200 до 400 °С | ||||||||
29а | Преобразователь термоэлектрический, диапазон измеряемых температур от -40 до 600°С Номинальная статическая характеристика- К Длина монтажной части 1000мм Кварцевый чехол, d нар.=22.5 мм, д=1000 мм | ТХК ГОСТ 6616-94 | цех № 48 | шт | 1 | |||
Температура ПГС после скрубера оросительного 2 ступени от 70 до 120 °С | ||||||||
23а | Термопреобразователь сопротивления медный. Диапазон измеряемых температур -50 - 180 °С НСХ чувствительного элемента-100М. Длина монтажной части 250 мм, материал защитной арматуры-сталь 12Х18Н10Т, крепление - штуцер М20х1,5 мм, с защитной гильзой L= 250 ммКварцевый чехол, d нар.=22.5 мм, д=1600 мм | ТСМ Метран-204- 02-250-B-3-1- С-Н-У1.1 (-40…75)-ГП ТУ 4211-002-12580824-2002 200.006.00-Н10-250 | г.Челябинск Концерн "Метран" | шт | 1 | |||
Позиция | Наименование и техническая характеристика | Тип, марка, обозначение опросного листа | Код изделия | Завод- изготовитель | Единицы измерения | Количество | Масса,, кг | Примечание |
Температура ПГС после оросительных конденсаторов 1-3 от 0 до 40°С | ||||||||
31а, 32а, 33а | Термопреобразователь сопротивления медный. Диапазон измеряемых температур -50 - 180 °С НСХ чувствительного элемента-100М. Длина монтажной части 250 мм, материал защитной арматуры-сталь 12Х18Н10Т, крепление - штуцер М20х1,5 мм, с защитной гильзой L= 250 мм | ТСМ Метран-204- 02-250-B-3-1- С-Н-У1.1 (-40…75)-ГП ТУ 4211-002-12580824-2002 200.006.00-Н10-250 | г.Челябинск Концерн "Метран" | шт | 3 | |||
Температура пульпы после теплообменников ТТ №1, №2, №3, №4 | ||||||||
18а, 19а, 20а, 21а | Термопреобразователь сопротивления медный. Диапазон измеряемых температур -50 - 180 °С НСХ чувствительного элемента-100М. Длина монтажной части 80 мм, материал защитной арматуры-сталь 12Х18Н10Т, крепление - штуцер М20х1,5 мм, с защитной гильзой L= 80 мм | ТСМ Метран-204- 02-80-B-3-1- С-Н-У1.1 (-40…75)-ГП ТУ 4211-002-12580824-2002 200.006.00-Н10-80 | г.Челябинск Концерн "Метран" | шт | 4 | |||
Температура технического TiCl4 после теплообменников ТТ №5-7 | ||||||||
34а, 35а, 36а | Термопреобразователь сопротивления медный. Диапазон измеряемых температур -50 - 180 °С НСХ чувствительного элемента-100М. Длина монтажной части 80 мм, материал защитной арматуры-сталь 12Х18Н10Т, крепление - штуцер М20х1,5 мм, с защитной гильзой L= 80 мм | ТСМ Метран-204- 02-80-B-3-1- С-Н-У1.1 (-40…75)-ГП ТУ 4211-002-12580824-2002 200.006.00-Н10-80 | г.Челябинск Концерн "Метран | шт | 3 | |||
Температура пульпы TiCl4 в баке - мешалке №2 от 70 до 120 °С | ||||||||
22а | Термопреобразователь сопротивления медный. Диапазон измеряемых температур -50 - 180 °С НСХ чувствительного элемента-100М. Длина монтажной части 800 мм, материал защитной арматуры-сталь 12Х18Н10Т, крепление - штуцер М20х1,5 мм, с защитной гильзой L= 800 мм | ТСМ Метран-204- 02-800-B-3-1- С-Н-У1.1 (-40…75)-ГП ТУ 4211-002-12580824-2002 200.006.00-Н10-800 | г.Челябинск Концерн "Метран | шт | 1 | |||
Уровень пульпы TiCl4 в баке - мешалке №2 от 200 до 1000 мм | ||||||||
29а | Радарный уровнемер для непрерывного измерения уровня жидкости, без взрывозащиты, герметизированная рупорная антенна, температура процесса от -40 до 200 С, присоединение - фланец DN100, PN16, форма С, материал - нерж. сталь 316L,выходной сигнал 4…20 мА , 2-х проводная схема, материал корпуса - пластик, степень защиты IP66/IP67, кабельный ввод М20х1,5 мм. | VEGAPULS 63 PS63. ХX N FE H K М А X /EP | ООО «ВЕГА ИНСТРУМЕНТС», Германия | шт | 1+1 | в т.ч. 1 шт. резерв | ||
Давление-разрежение под сводом хлоратора от -8 до 8 кПа | ||||||||
17а | Датчик давления - разрежения, с индикаторным устройством. Перенастраиваемый предел измерений. Выходной сигнал от 4 до 20 мА Климатическое исполнение УХЛ 3.1 | Метран-150TG 2 3 1 1 L3 АМ5 S5 В4 C1 К04 ТУ 4212-022- 51453097-2006 | г.Челябинск Концерн "Метран | шт | 1 | |||
Позиция | Наименование и техническая характеристика | Тип, марка, обозначение опросного листа | Код изделия | Завод- изготовитель | Единицы измерения | Количество | Массакг | Примечание |
Газоходы после пылеосадительных камер №1, №2 от -4 до 1,5 кПа | ||||||||
37а | Датчик давления - разрежения, с индикаторным устройством. Перенастраиваемый предел измерений. Выходной сигнал от 4 до 20 мА Климатическое исполнение УХЛ 3.1 | Метран-150TG 2 3 1 1 L3 АМ5 S5 В4 C1 К04 ТУ 4212-022- 51453097-2006 | г.Челябинск Концерн "Метран" | шт | 1 | |||
Газоходы после скрубера оросительного 2 ступени от -4 до 1,5 кПа | ||||||||
38а | Датчик давления - разрежения, с индикаторным устройством. Перенастраиваемый предел измерений. Выходной сигнал от 4 до 20 мА. Климатическое исполнение УХЛ 3.1 | Метран-150TG 2 3 1 1 L3 АМ5 S5 В4 C1 К04 ТУ 4212-022-51453097-2006 | г.Челябинск Концерн "Метран" | шт | 1 | |||
Давление анодного хлор-газа (воздуха) 0-250 КПа Трубопроводы подвода хлора (воздуха) к фурмам 1, 2, 3, 4 ХТ | ||||||||
24а,25а, 26а,27а | Датчик давления с индикаторным устройством. Перенастраиваемый предел измерений. Выходной сигнал от 4 до 20 мА Климатическое исполнение УХЛ 3.1 | Метран-150TG 2 3 1 1 L3 АМ5 S5 В4 C1 К04 ТУ 4212-022- 51453097-2006 | г.Челябинск Концерн "Метран" | шт | 4 | |||
Расход анодного хлор-газа от 200 до 600 м 3 /ч Трубопровод подвода хлора к фурмам 1...4 ХТ Диаметр внутренний 100 мм | ||||||||
4а,5а, 6а,7а | Диафрагма камерная, условное давление 1,6 МПа, условный диаметр 100 мм, материал диска 12Х18Н10Т, материал корпуса камеры 12Х18Н10Т | ДКС 1,6-100-Б/Б-1 ГОСТ 8.563.1-97 МИ 2638-2001 | г.Челябинск Концерн "Метран" | шт | 4 | |||
4б,5б, 6б,7б | Датчик разности давлений с индикаторным устройством. Выходной сигнал от 4 до 20 мА с цифровым сигналом на базе протокола HART Климатическое исполнение УХЛ 3.1 Клапанный блок | Метран-150CD 2 2 1 1 L3 А М5S5 В4 K04ТУ 4212-022-51453097-2006 | г.Челябинск Концерн "Метран" | шт | 4 | |||
Расход сжатого воздуха от 80 до 250 м 3 /ч Трубопровод подвода воздуха к фурмам 1...4 ХТ Диаметр внутренний 50 мм | ||||||||
9а,10а, 11а,12а | Диафрагма камерная, условное давление 0,6 МПа, условный диаметр 50 мм, материал диска 12Х18Н10Т, материал корпуса камеры Сталь 20 | ДКС 0,6-50-А/Б-1 ГОСТ 8.563.1-97 МИ 2638-2001 | г.Челябинск Концерн "Метран" | шт | 4 | |||
Расход сжатого воздуха от 80 до 250 м 3 /ч Трубопровод подвода воздуха к фурмам 1...4 ХТ Диаметр внутренний 50 мм | ||||||||
9а,10а, 11а,12а | Диафрагма камерная, условное давление 0,6 МПа, условный диаметр 50 мм, материал диска 12Х18Н10Т, материал корпуса камеры Сталь 20 | ДКС 0,6-50-А/Б-1 ГОСТ 8.563.1-97 МИ 2638-2001 | г.Челябинск Концерн "Метран" | шт | 4 | |||
Позиция | Наименование и техническая характеристика | Тип, марка, обозначение опросного листа | Код изделия | Завод- изготовитель | Единицы измерения | Количество | Массакг | Примечание |
9б, 10б, 11б, 12б | Датчик разности давлений с индикаторным устройством. Выходной сигнал от 4 до 20 мА с цифровым сигналом на базе протокола HART Климатическое исполнение УХЛ 3.1 Клапанный блок | Метран-150CD 2 2 1 1 L3 А М5S5 В4 K04ТУ 4212-022- 51453097-2006 0104 M W 3 2 C 1 1 D9 2 L4 | г.Челябинск Концерн "Метран" | шт | 4 | |||
Расход воздуха на фурмы 1..2 пылеосадительной камеры №1 от 50 до 80 м 3 /ч Трубопровод подвода воздуха к фурмам 1..2 пылеосадительной камеры №1 Диаметр внутренний 50 мм | ||||||||
13а, 14а | Диафрагма камерная, условное давление 0,6 МПа, условный диаметр 50 мм, материал диска 12Х18Н10Т, материал корпуса камеры Сталь 20. | ДКС 0,6-50-А/Б-1 ГОСТ 8.563.1-97 МИ 2638-2001 | г.Челябинск Концерн "Метран" | шт | 2 | |||
13б, 14б | Датчик разности давлений с индикаторным устройством. Выходной сигнал от 4 до 20 мА с цифровым сигналом на базе протокола HART Климатическое исполнение УХЛ 3.1 Клапанный блок | Метран-150CD 2 2 1 1 L3 А М5S5 В4 K04ТУ 4212-022- 51453097-2006 0104 M W 3 2 C 1 1 D9 2 L4 | г.Челябинск Концерн "Метран" | шт | 2 | |||
Регулирование расхода воздуха на фурмы 1..2 пылеосадительной камеры №1 | ||||||||
13в, 14в | Преобразователь электропневматический, Входной сигнал от 4 до 20 мА, Выходной сигнал от 20 до 100 кПа | ЭП-3211 ТУ 25-7304-008-87 | Саранский приборостроительный завод | шт | 2 | |||
13г,д 14г,д | Мембранный исполнительный механизм в комплекте с регулирующим клапаном - 25нж92нж | МИМ - 250 ТУ 26-07-1475-88 | Саранский приборостроительный завод | шт | 2 | |||
Расход анодного хлор-газа от 600 до 2000 м 3 /ч Трубопровод подвода хлора (нитка 1, 2) к ХТ Диаметр внутренний 200 мм | ||||||||
39а, 40а | Диафрагма камерная, условное давление 1,6 МПа, условный диаметр 200 мм, материал диска 12Х18Н10Т,материал корпуса камеры 12Х18Н10Т | ДКС 1,6-200-Б/Б-1 ГОСТ 8.563.1-97 МИ 2638-2001 | г.Челябинск Концерн "Метран" | шт | 2 | |||
39б, 40б | Датчик разности давлений с индикаторным устройством. Выходной сигнал от 4 до 20 мА с цифровым сигналом на базе протокола HART Климатическое исполнение УХЛ 3.1 Клапанный блок | Метран-150CD 2 2 1 1 L3 А М5S5 В4 K04ТУ 4212-022-51453097-2006 0104 M W 3 2 C 1 1 D9 2 L4 | г.Челябинск Концерн "Метран" | шт | 2 | |||
Позиция | Наименование и техническая характеристика | Тип, марка, обозначение опросного листа | Код изделия | Завод- изготовитель | Единицы измерения | Количество | Массакг | Примечание |
Дистанционное управление расходом анодного хлор-газа от 600 до 2000 м 3 /ч | ||||||||
39в 40в | Преобразователь электропневматический, Входной сигнал от 4 до 20 мА, Выходной сигнал от 20 до 100 кПа | ЭП-3211 ТУ 25-7304-008-87 | Саранский приборостроительный завод | шт | 2 | |||
39г,д 40г,д | Мембранный исполнительный механизм в комплекте с регулирующим клапаном - 25нж92нж | МИМ - 250 ТУ 26-07-1475-88 | Саранский приборостроительный завод | шт | 2 | |||
Расход пульпы от 50 до 60 м 3 /ч Трубопровод подвода пульпы в хлоратор Диаметр внутренний 80 мм | ||||||||
30а | Диафрагма камерная, условное давление 0,6 МПа, условный диаметр 80 мм, материал диска и корпуса 12Х18Н10Т | ДКС 0,6-50-А/Б-1 ГОСТ 8.563.1-97 МИ 2638-2001 | г.Челябинск Концерн "Метран" | шт | 1 | |||
30б | Датчик разности давлений с индикаторным устройством. Выходной сигнал от 4 до 20 мА с цифровым сигналом на базе протокола HART Климатическое исполнение УХЛ 3.1 Клапанный блок | Метран-150CD 2 2 1 1 L3 А М5S5 В4 K04ТУ 4212-022- 51453097-20060104 M W 3 2 C 1 1 D9 2 L4 | г.Челябинск Концерн "Метран" | шт | 1 | |||
Регулирование температуры расплава в хлораторе изменением расхода пульпы в хлоратор от 50 до 60 м 3 /ч | ||||||||
1в | Преобразователь электропневматический, Входной сигнал от 4 до 20 мА, Выходной сигнал от 20 до 100 кПа | ЭП-3211 ТУ 25-7304-008-87 | Саранский приборостроительный завод | шт | 1 | |||
1г.д | Мембранный исполнительный механизм в комплекте с регулирующим клапаном - 25нж92нж | МИМ - 250 ТУ 26-07-1475-88 | Саранский приборостроительный завод | шт | 1 | |||
Дистанционное управление температурой парогазовой смеси изменением подачи пульпы на орошение в пылеосадительную камеру №1 | ||||||||
8б | Преобразователь электропневматический, Входной сигнал от 4 до 20 мА, Выходной сигнал от 20 до 100 кПа | ЭП-3211 ТУ 25-7304-008-87 | Саранский приборостроительный завод | шт | 1 | |||
8в,г | Мембранный исполнительный механизм в комплекте с регулирующим клапаном - 25нж92нж | МИМ - 250 ТУ 26-07-1475-88 | Саранский приборостроительный завод | шт | 1 | |||
Позиция | Наименование и техническая характеристика | Тип, марка, обозначение опросного листа | Код изделия | Завод- изготовитель | Единицы измерения | Количество | Массакг | Примечание |
Состояние работы двигателя винтового конвейера №1, 2 Максимальная частота вращения двигателя винтового конвейера 1455 об/мин | ||||||||
15а, 16а | Частотно-регулируемый электропривод переменного тока Uн = 380…460 В, 50 Гц, IP20 | SB19-С110У | НПП «Уралэлектра» г. Екатеринбург | шт | 2 | |||
А1 | Блок питания четырехканальный. Выходное напряжение - 24 В | БП96/24-1/80-DIN ТУ 689400-006- 13282997-96 | г.Челябинск Приборостроительный завод "Элемер" | шт | 1 | |||
А2, A3,А4, A5,А6 | Блок питания четырехканальный. Выходное напряжение - 24 В | БП96/24-4/80-DIN ТУ 689400-006- 13282997-96 | г.Челябинск Приборостроительный завод "Элемер" | шт | 5 | |||
Регулирующий микропроцессорный контроллер в комплекте: | 1769-L31 COMPACTLOGIX SERIAL PROCESSOR, 512K | Allen-Bradley | ||||||
Модуль ввода аналоговый 4 канала | 1769-IF4 | 1 | ||||||
Модуль ввода аналоговый 8 каналов | 1769-IF8 | 2 | ||||||
Модуль ввода для термопар 6 каналов | 1769-IT6 | 1 | ||||||
Модуль вывода аналоговый 2 канала | 1769-OF2 | 1 | ||||||
Модуль вывода дискретный 32 канала | 1769-OB32 | 1 | ||||||
Блок питания,~220/-24 В | 1769-PA4 POWER SUPPLEY | 1 | ||||||
Блок питания для модуля вывода дискретных сигналов, ~220/-24 В | 1606-PB2 POWER SUPPLEY | 1 | ||||||
Шасси 7 слотов | 1769-А7 COMPACTLOGIX CHASSIS | 1 | ||||||
Клеммная колодка | 492-AIFM4-3 | 2 | ||||||
Кабель | 1492-ACAB050AB69 | 2 | ||||||
Кабельные изделия | ||||||||
Кабель силовой с медными жилами, изоляция и оболочка из поливинилхлоридного пластика, сечение 4 • 2,5 мм | ВВГ ГОСТ 16422-80 | м | 16 | |||||
Позиция | Наименование и техническая характеристика | Тип, марка, обозначение опросного листа | Код изделия | Завод- изготовитель | Единицы измерения | Количество | Массакг | Примечание |
Кабели контрольные | ||||||||
Кабель контрольный с медными жилами, изоляция и оболочка из поливинилхлоридного пластика, сечение 4 • 0,75 мм | КВВГ ГОСТ 1508-78 | м | 2622 | |||||
Кабели управления | ||||||||
Кабель управления парной скрутки экранированный с медными жилами Изоляция из полиэтилена в общем экране. Оболочка из поливинилхлоридного пластика, в панцирной оплетке из стальных оцинкованных проволочек сечением 2•2•0,5 мм | КУПЭВ ТУ 16-705.096-79 | м | 6 | |||||
Кабель монтажный | ||||||||
Кабель монтажный с медными жилами, изоляция и оболочка из поливинилхлоридного пластика, сечение 4 • 0,75 мм | МКЭШ ГОСТ 10348-80 | м | 300 | |||||
Провода термоэлектродные | ||||||||
Провод термоэлектродный сечением 2 • 0,75 мм | ПТВВ-ха ПТВВ-хк | м | 190 300 | |||||
Провода установочные | ||||||||
Провод установочный с медными жилами, с изоляцией из поливинилхлоридного пластика, сечением 1 • 0,75 мм | ПВ1 ГОСТ 6323-79 | м | 1182 | |||||
Трубы | ||||||||
Трубы защитные для электропроводок | ||||||||
Труба стальная водогазопроводная с резьбой под накатку, с муфтой | М-н-20•2,5 ГОСТ 3262-75 | м | 78 | |||||
Трубы для трубных проводок | ||||||||
Труба безшовная. Сталь 12Х18Н10Т | 14 • 2,0 22 • 3,0 ГОСТ 8734-75 | м | 253 152 | |||||
Труба поливинилхлоридная высокого давления, диаметр 8 • 1,6 | ПВХ ТУ 4218-001- 01395851-2000 | м | 18 | |||||
Трубы защитные для электропроводок | ||||||||
Рукав металлический гибкий цилиндрический негерметичный, из стальной оцинкованной ленты простого профиля в замке с хлопчатобумажным уплотнением с условным проходом 15 мм | РЗ-Ц-Х-15 ТУ 22-5570-83 | м | 17 | |||||
Трубопроводная арматура | ||||||||
Клапан запорный Ру 16 МПа, Ду 15 мм | 15с54бк тип 5 Ту 26-07-1418-86 | м | 45 | |||||
Позиция | Наименование и техническая характеристика | Тип, марка, обозначение опросного листа | Код изделия | Завод- изготовитель | Единицы измерения | Количество | Массакг | Примечание |
Кран шаровой Ру 1,6 МПа, Ду 15 мм | ФБ 39.011.015.700.01 | шт | 20 | |||||
Монтажные материалы и изделия | ||||||||
Соединение | СМТ15•20-G3/4 У3 ТУ 36-1125-84 | шт | 17 | |||||
Соединение ниппельное вварное | НСВ14-R1/2УХЛ4 Ту 36-1101-82 | шт | 76 | |||||
Соединение навертное | НСН14•М20 УХЛ4 ТУ 36-1101-82 | шт | 1 | |||||
Соединение тройниковое проходное | СТ14У1 СТ22У1 ТУ 36.22.21.00.019-91 | шт | 8 4 | |||||
Профиль Z - образный L = 150 мм L = 270 мм L = 450 мм | ZП25•25У1 ТУ 36.22.21.00.021-91 | шт | 12 10 2 | |||||
Рама стенда датчиков | РПП1 | шт | 1 | |||||
Стойка датчиков | СД | шт | 13 | |||||
Стойка - статив с панелью | ССП | шт | 6 | |||||
Оконцеватель проводов | ОП У3 ТУ 36-1145-84 | шт | 1050 | |||||
Бирка маркировочная | У 136 У 3,5 ТУ 36.22.19.06.001-87 | шт | 500 |
Дата добавления: 2018-06-27; просмотров: 2429; Мы поможем в написании вашей работы! |
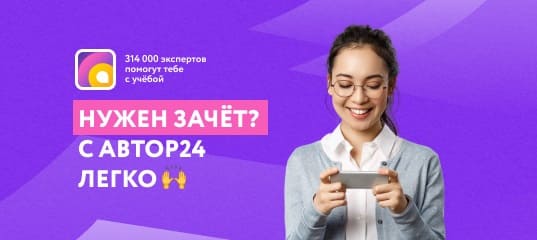
Мы поможем в написании ваших работ!