Требования к системе автоматизации турбокомпрессорной станции.
Cодержание
Реферат. 5
Введение 6
1.Система пневмоснабжения шахты как объект автоматизации. 7
2. Требования к системе автоматизации турбокомпрессорной станции. 10
3. Требования продуктивности компрессорных установок 12
3.1. Функциональная схема автоматического регулирования
продуктивности компрессорной установки. 16
4. Автоматический контроль и защиты компрессорных установок. 18
5. Аппаратура автоматизации компрессорных установок УКАС-М. 23
5.1. Функциональна схема и работа комплектного устройства
УКАС-М. 26
6. Техническое обслуживание компрессорных установок. 28
7. ПБ при эксплуатации компрессорных установок. 34
8. Эффективность и перспективы автоматизации компрессорных
установок. 36
|
|
9. Сетевой график монтажа аппаратуры автоматизации УКАС-М. 37
10. Наладка и обслуживание аппаратуры автоматизации управления компрессорными установками УКАС-М. 38
11. Правила безопасности и охраны труда во время монтажа и технического обслуживания. 39
Вывод.
Список использованной литературы.
Введение
Компрессорные машины - важные виды продукции машиностроения. Они применяются во многих отраслях народного хозяйства: химической, нефтяной, газовой и машиностроительной, на транспорте, в металлургии, геологии, строительстве, агропромышленном комплексе, а также - в новых перспективных направлениях техники и технологии, в частности, в космонавтике, робототехнике, производстве искусственного топлива и др. Сердцем любой холодильной и криогенной установки является компрессор. От эффективности и надежности его работы зависят КПД и долговечность комплекса в целом.
|
|
В основном, компрессорные установки являются неотъемлемой составной частью большинства промышленных и общественных комплексов (химических, нефтеперерабатывающих, газовых, автомобильных, научно-исследовательских). Основная задача КУ – бесперебойное обеспечение объекта газовой смесью с заранее установленными параметрами. Следовательно отказ КУ приводит к простою всего комплекса или, как минимум, его большую часть, а это колоссальные убытки. Снижение расходов на обслуживание и продление межремонтного срока, а также упрощение диагностики неполадок в совокупности с повышением надежности, позволяет говорить о значительной выгоде связанной с применением новой системы управления вместо традиционной при модернизации существующих станций.
Система пневмоснабжения шахты как объект автоматизации.
Система пневмоснабжения шахт и рудников состоит из компрессорной станции, вырабатывающей энергию сжатого воздуха, и пневмосети (трубопроводов с регулирующими органами), осущестляющей его передачу и распределение между такими потребителями, как отбойные молотки, буровые машины и станки, погрузочные машины, насосы, вентиляторы и др.
|
|
Основнойпараметр, характеризующий работу компрессоров и присоединенныхкнимпотребителей — это давление сжатого воздуха. При снижении давления в пневмосети примерно пропорционально уменьшается производительность рабочего оборудования; при повышении давления производительность пневмомашин возрастает, но одновременно увеличиваются непроизводительные затраты, обусловленные ростом потерь в компрессорах, утечек воздуха в неплотностях трубопроводов, износа инструмента, а также снижением к. п. д. пневмодвигателей и т. д. Поэтому необходимо управлять давлением в системе пневмоснабжения таким образом, чтобы обеспечить максимальную производительность потребителей сжатого воздуха при минимальных затратах на его производство и транспортирование. Для поддержания давления на заданном уровне в условиях неравномерного потребления пневмоэнергии, вследствие неодновременного включения потребителей и разной их загрузки (расхода воздуха) требуется регулировать производительность компрессорной станции в широких пределах.
К автоматизации системы пневмоснабжения предъявляются следующие требования:
1.Обеспечить экономичность и безопасность работы компрессорных агрегатов;
2.Предотвратить аварийные режимы, нарушения работы или выход из строя отдельных элементов, узлов и компрессорных, агрегатов в целом;
|
|
3.Повысить эффективность использования пневмоэнергии потребителями;
4.Высвободить частично или полностью обслуживающий персонал.
Выполнение этих требований обеспечивается системой автоматизации процессов пневмоснабжения, состоящей из трех подсистем:
1.Автоматического (дистанционного) управления пуском и остановом двигателей компрессоров и вспомогательных механизмов компрессорных агрегатов;
2.Автоматического регулирования режимов работы компрессорных агрегатов, станции и потребителей сжатого воздуха;
3.Автоматического контроля и защиты основных узлов и систем компрессорных агрегатов и пневмосети.
Автоматизация процессов пневмоснабжения может быть:
1.Частичной;
2.Комплексной;
3.Полной;
При частичной автоматизации контроль и защита компрессорных агрегатов автоматизируются полностью, а управление ими — частично. Некоторые операции управления агрегатами (подготовка к пуску, пуск и др.) осуществляются обслуживающим персоналом вручную.
При комплексной автоматизации управление пуском и остановом, регулирование режимов работы (поддержание заданных значений давления сжатого воздуха, температуры воды и смазки и т. п.), контроль и защита компрессорных агрегатов осуществляются автоматическими системами. Выбор программы и очередности работы агрегатов, введение задания регуляторам выполняются вручную. Компрессоры могут управляться дистанционно по командам горного диспетчера или оператора компрессорной станции.
Полная автоматизация предполагает передачу управляющей
вычислительной машине функций анализа работы системы пневмоснабжения и выбора оптимальных программ функционирования ее элементов,
реализуемых автоматическими системами компрессорной станции и
пневмосети с подключенными к ней потребителями.
Выбор рационального уровня автоматизации процессов
пневмоснабжения обусловливается:
- Технико-экономическими показателями;
- Требованиями охраны труда;
- Техники безопасности;
- Подготовленностью к автоматизации производства.
Требования к системе автоматизации турбокомпрессорной станции.
В компрессорах происходит преобразование энергии, подводимой двигателем к валу, в энергию проходящих через них газов.
В динамических или турбокомпрессорных машинах передача энергии к газу происходит непрерывно во вращающемся рабочем колесе, снабженном лопатками. При обтекании потоком газа решетки из профилей лопаток вращающегося колеса возникает подъемная сила, вызывающая ускорение потока, увеличение его скорости и давления. В дальнейшем в неподвижных элементах происходит добавочное увеличение давления за счет
преобразования кинетической энергии газа.
К динамическим компрессорам относятся:
- Центробежные;
- Диагональные;
- Осевые;
- Вихревые машины.
Рисунок 1 - Технологическая схема турбокомпрессорного агрегата
На рисунке 1 представлена технологическая схема турбокомпрессорного агрегата.
После каждой ступени воздух поступает в воздухоохладители, охлаждаемые водой, и затем в следующую ступень или воздухосборник. Сам турбокомпрессор охлаждению не подвергается. Нагретая вода охлаждается в градирне и насосом снова подается в водопровод охлаждения. Охлаждается водой также и воздух, поступающий на охлаждение электродвигателя.
Шестеренчатый рабочий маслонасос, сидящий на валу редуктора, засасывает через фильтры масло из маслобака и нагнетает его в маслосистему под давлением 500 кПа (5 кгс/см2). Масло проходит через охлаждаемые водой маслоохладители, после которых часть его, поступающая на смазку подшипников, пропускается через редукционный клапан, снижающий давление до 50-90 кПа (0,5-0,9 кг/см2). Масло под высоким давлением используется для работы реле осевого сдвига
опорноупорного подшипника и регуляторов производительности и
противопомпажного, если они гидравлические.
3. Регулирование производительности компрессорных установок.
Производительность компрессора контролируется датчиками расхода воздуха, установленными на всасывающем и нагнетательном воздухопроводах. Они представляют собой дифференциальные манометры с электрическими сигналами на выходе вторичного прибора, измеряющие перепад давления на диафрагмах, смонтированных в воздухопроводах. Датчик расхода всасывающего воздухопровода измеряет полную производительность, и поэтому его показания используются для работы противопомпажного регулятора. Датчик расхода нагнетательного воздухопровода измеряет количество сжатого воздуха, поступающего в воздухосборник и далее в пневмосеть, которое может отличаться от полной производительности, например, при работе противопомпажной защиты, когда часть сжатого воздуха выбрасывается в атмосферу.
Давление воздуха, воды и масла измеряется датчиками, представляющими собой манометры различных типов, обычно бесшкальные с аналоговыми или дискретными сигналами на выходе, которые используются для целей автоматического контроля, защиты, управления.
Температура воздуха, охлаждающей воды, масла, подшипников, обмоток электродвигателя измеряется термометрами сопротивления, в качестве вторичных приборов для которых используются логометры и автоматические мосты.
Для распределения охлаждающей воды по объектам охлаждения предусмотрены регулировочные вентили. Такие же вентили и в системе маслоснабжения. В водопроводной сети устанавливаются датчики контроля потока воды. В нагнетательном трубопроводе устанавливаются управляемые задвижки с электроприводом. Одна задвижка при необходимости отделяет
компрессор от пневмосети, вторая управляется регулятором
противопомпажной защиты и соединяет компрессор с атмосферой.
Рисунок 2 - Рабочие характеристики турбокомпрессора
На рисунке 2 изображены рабочие характеристики турбокомпрессора. Рабочая точка компрессора определяется точкой пересечения А характеристики компрессора 1 и характеристики воздухопровода 2. Точка К соответствует критической производительности Qк компрессора, при которой он развивает максимальное давление Рк. Если расход воздуха в пневмосети станет меньше Qк, то давление, развиваемое компрессором, окажется меньше Рк и, следовательно, меньше, чем в пненмосети, из которой воздух устремится к компрессору и захлопнет обратный клапан в воздухопроводе. Рабочий режим компрессора переместится в точку Б, соответствующую холостому ходу. По мере расходования воздуха, из пневмосети его давление снизится до величины, соответствующей точке А, обратный клапан откроется и компрессор начнет подавать в пневмосеть воздух в количестве, определяемом точкой В. Если расход воздуха останется меньше Qк, все повторяется в том же порядке. Это явление известно под названием помпажа и происходит при эксплуатации компрессора на участке рабочей характеристики, расположенной левее критической точки К.
Устойчивая работа компрессора возможна на участке характеристики, расположенном правее точки К. Для обеспечения нормальной работы компрессора, при меняющемся расходе воздуха в пневмосети, его снабжают противопомпажной защитой, которая обеспечивается специальным регулятором, соединяющим противопомпажной заслонкой нагнетательный воздухопровод компрессора с атмосферой, когда потребление воздуха пневмосетью становится ниже Qк и, таким образом, удерживает режим работы компрессора на устойчивой ветви рабочей характеристики. Степень открытия противопомпажной заслонки определяется разностью между Qк и действительным потреблением воздуха пневмосетью.
Регулирование производительности турбокомпрессора для поддержания постоянного давления независимо от расхода воздуха может осуществятся двумя способами: изменение частоты вращения рабочих колес и дросселирование воздуха во всасывающем трубопроводе с помощью дроссельной заслонки. В точке А компрессор развивает нормальное давление Рн. При снижении потребления воздуха из пневмосети, характеристика которой будет определяться теперь кривой 3, а рабочий режим компрессора точкой Г, давление превысит нормальное. Чтобы довести давление до нормального, можно снизить частоту вращения компрессора: его характеристика изобразится кривой 4, а рабочая точка переместится в точку Д. Тот же результат может быть получен при неизменной частоте вращения компрессора прикрытием дроссельной заслонки во всасывающем трубопроводе. Характеристика компрессора в этом случае изобразится кривой 5, а рабочий режим - той же точкой Д.
Система автоматизации турбокомпрессорной станции должна обеспечивать:
1. Следующие режимы управления турбокомпрессорной станцией:
1.1.Автоматическое программное управление, при котором первичный импульс на пуск и останов отдельных агрегатов и всей станции подается или от ЭВМ или оператором (диспетчером) из пульта, установленного вне машинного зала компрессорной станции, или из машинного зала;
1.2.Местное управление всеми механизмами во время наладочных и ремонтных работ.
При автоматическом управлении должна осуществляться заданная технологическая последовательность управления основным и вспомогательным оборудованиям станции.
Возможность одновременной работы агрегатов в двух режимах должна быть исключена.
2. Контроль работы, сигнализацию о нормальном и аварийном
режимах работы, а также необходимые автоматические блокировки и защиты, в частности от помпажа.
3. Автоматическая поддержка заданного давления сжатого воздуха в коллекторе компрессорной станции путем регулирования режима работы отдельных агрегатов.
Кроме того, система автоматизации должна отвечать следующим требованиям:
1.Схемные решения должны быть универсальными для возможности применения аппаратур на компрессорной станции при возможной их модернизации;
2.Комплект аппаратур должен быть построен на базе блочных элементов и модулей с максимальным использованием стандартных унифицированных узлов, бесконтактных микропроцессорных элементах;
3.Конструктивное оформление комплекта аппаратур должно обеспечивать высокую ремонтопригодность, т.е. быстрый поиск неисправных функциональных блоков в аппаратуре, возможность доступа к ним и быструю замену.
Дата добавления: 2018-06-27; просмотров: 1067; Мы поможем в написании вашей работы! |
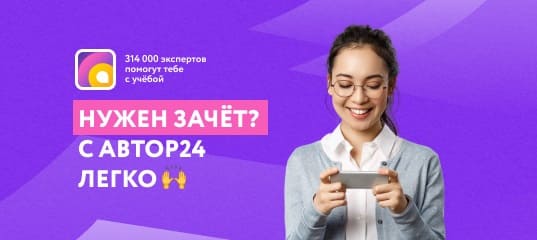
Мы поможем в написании ваших работ!