В ходе прохождения производственной практики я выполнял демонтаж и монтаж запорной арматуры.Задвижка стальная типа 3КЛ2-16.
Демонтаж:
· Убрал пыль и загрязнения с оборудования при помощи щетки и ветоши.
· Отметил взаимное положение фланцев задвижки маркеромприл чертеж
· Поставил поддон под задвижку для исключения пролива остатков воды на пол
· Ослабить усилие затяжки на всех болтах и гайках фланцев при помощи рожкового гаечного ключа.Гайки окрашены, имеют заваленные грани код ключ и не отвинчиваются.Я принял решениесбить лакокрасочное покрытие при помощи зубила и молотка. При помощи ручной шлифовальной машины восстановить размер гаек под ключ. Далее ослабил уже обточенные гайки гаечным ключом
· Разборку болтовых соединений начинал снизу, оставив сверху по 2 болта на каждом фланце, для исключения опрокидывания задвижки.
· Придерживая задвижку отвинтил гаечным ключом и разобрал оставшийся крепеж.
· Отсоединил трубопроводы от фланцев при помощи малого монтажного лома, упирая один конец лома в пол, давил на корпус задвижки и небольшими рывками вывел задвижку из трубопровода
· Очистилфланцы трубопроводов от ржавчины при помощи мелкозернистой наждачной шкурки и протёр их ветошью.
ДАЛЬШЕ ТО ЧТО?
Монтаж:
· Установилновую задвижку на штатное место.В корпусе задвижки не должно быть загрязнений и посторонних предметов.
· Установил прокладки между фланцами трубопровода и задвижки.Проверил положение уплотнительной прокладки между фланцами.Прокладка должна находиться строго по центру между уплотнительными поверхностями, сдвиги более 2 мм не допускаются.
|
|
· Установил плоские и пружинные шайбы на все шпильки.
· Смазал резьбовые поверхности всех болтов.(смазка ЦИАТИМ-201 ГОСТ 6267-74)
· Навинтил гайки на шпильки.
· Затянул гайки при помощи набора головок и динамометрического ключа в соответствии со схемой затяжки (см. приложение 4).Усилие затяжки Мзат. =16 кгсм.
· Неравномерность раскрытия стыка между фланцем трубопровода и задвижки по периферии допускается не более 0,3 мм.
· После затяжки гаек стык между фланцем трубопровода и задвижкираскрыт неравномерно (более 0,3 мм),значит прокладка сдвинута более 2 мм.
· Ослабил затяжку на всех гайках, при помощи тонкой отвёртки поправил прокладку и повторил затяжку, каждый раз измеряя штангенциркулем зазор между корпусом и крышкой. В ходе затяжкистык между фланцем трубопровода и задвижки раскрыт в пределах допустимых параметров(менее 0,3 мм)
· Произвёл проверку работоспособности и герметичности задвижки на рабочих параметрах на отсутствие протечек, каплеобразований между фланцевыми соединениями.Заклинивание или незакрытие задвижки не допускаются.
· В ходе проверки не обнаружились ранее перечисленные деффекы.
|
|
В ходе обслуживания и ремонта данной задвижки я руководствовался: «СБОРНИКОМ КАРТЫ ТЕХНИЧЕКОГО ОБСЛУЖИВАНИЯ, ТЕКУЩЕГО И КАПИТАЛЬНОГО РЕМОНТОВ ЗАПОРНОЙ АРМАТУРЫ»
В приложение!
ЗАКЛЮЧЕНИЕ
В ходе освоения программы былиизучены:функции предприятия его технологические процессы, работа электрического и электромеханического оборудования, освоеныпрофессиональные компетенции:
ПК.1.1 Руководить работами, связанными с применением грузоподъемных механизмов, при монтаже и ремонте промышленного оборудования.
ПК 1.2 Проводить контроль работ по монтажу и ремонт
Промышленного оборудования с использованием контрольно - измерительных приборов.
ПК1.3. Участвовать в пусконаладочных работах и испытаниях промышленного оборудования после ремонта и монтажа
ПК 1. 4. Выбирать методы восстановления деталей и участвовать в процессе их изготовления.
ПК 1.5. Составлять документацию для проведения работ по монтажу и ремонту промышленного оборудования.
Дописать пк
Приобретен практический опыт: руководства работами, связанными с применением грузоподъёмных механизмов, при монтаже и ремонте промышленного оборудования
|
|
- выбора методов восстановления деталей и участвовать в процессе их изготовления;
- составления документации для проведения работ по монтажу и ремонту промышленного оборудования;
новые знания: классификацию технологического оборудования;
устройство и назначение технологического оборудования;
сложность ремонта оборудования;
классификацию грузоподъемных и грузозахватных механизмов;
основные параметры грузоподъемных машин;
методы ремонта деталей, механизмов и узлов промышленного оборудования;
виды заготовок и способы их получения;
виды механической обработки деталей;
классификацию и назначение режущего и измерительного инструментов;
методы контроля точности и шероховатости поверхностей;
правила техники безопасности при выполнении монтажных и ремонтных работ;
средства коллективной и индивидуальной защиты
и умения: выбирать технологическое оборудование;
пользоваться грузоподъёмными механизмами;
рассчитывать предельные нагрузки грузоподъемных устройств;
определять виды и способы получения
заготовок;
выбирать технологическую оснастку;
пользоваться измерительным инструментом;
|
|
определять методы восстановления деталей;
пользоваться нормативной и справочной литературой;
Результатом учебной практики является первичное комплексное освоение вида профессиональной деятельности: организация и проведение монтажа и ремонта промышленного оборудования, оформление отчета по результатам учебной практики.
ЛИТЕРАТУРА
· Пособие слесаря-ремонтника 1973 год. В.А. Дубровский
· Насосы и насосные станции. Карелин В. Я. Минаев А.В.
· Справочник слесаря-монтажника технологического оборудования Владимир Голованов , Виктор Калугин, П. Алексеенко.
ПРИЛОЖЕНИЕ к отчету
Дата добавления: 2018-05-13; просмотров: 765; Мы поможем в написании вашей работы! |
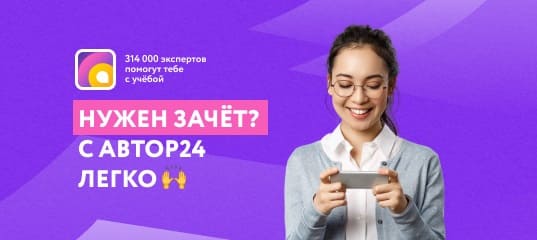
Мы поможем в написании ваших работ!