Замена задних тормозных колодок
Требования безопасности при выполнении работ.
Каждый работник должен соблюдать безопасные приёмы труда. При обнаружении какой-либо опасности для себя и другого работника необходимо, соблюдая меры предосторожности, устранить эту опасность и доложить об этом своему непосредственному руководителю.
Работники, занятые ведением технологического процесса, должны:
- знать процесс производства, схему его контроля, расположение, назначение и принцип работы оборудования, арматуры, коммуникаций, приборов, автоматики и уметь их эксплуатировать;
- соблюдать установленные инструкциями и документацией на оборудование нормы и режимы безопасного ведения технологического процесса.
Для защиты работников от воздействия вредных производственных факторов выдаётся спецодежда и специальную обувь. Если при выполнении работы возможно попадание в глаза отдельных частиц металла, пыли, брызг, агрессивных веществ, искр, работники должны пользоваться защитными очками или щитками.
К работам на электроустановках допускается специально обученный персонал, имеющий соответствующую квалификацию и группу по электробезопасности. При работе на электроустановках необходимо использовать диэлектрические перчатки, боты, резиновые коврики и другие средства, предусмотренные правилами электробезопасности.
Для подъёма и перемещения грузов, монтажа и демонтажа технологического оборудования, арматуры, а также при их ремонте, необходимо применять подъёмно-транспортные механизмы.
|
|
Работникам запрещается:
- производить работы, которые им не поручены;
- пускать или останавливать оборудование и механизмы, если это не входит в их обязанности;
- загромождать или уменьшать подходы к средствам пожаротушения. Использовать средства пожаротушения не по назначению.
Производство работ в местах, где имеется или может возникнуть повышенная производственная опасность, допускается проводить только после обязательного оформления в установленном порядке наряда-допуска на выполнение работ повышенной опасности, в строгом соответствии со специальной инструкцией.
Каждое производственное помещение должно быть оснащено аптечкой с набором медикаментов в соответствии с действующими нормами.
Курение на территории и в производственных помещениях предприятия запрещается, за исключением специально отведённых для этого мест (по согласованию с пожарной охраной), где вывешиваются надписи «Место для курения».
Замена масла в двигателе
Правильная замена масла в двигателе начинается с прогрева системы двигателя.
Затем необходимо подождать пока оно остынет. В это время подбираем ёмкость для слива отработанной смазки.
|
|
После откручивается заглушка на картере, находящаяся в нижней части поддона. Сначала заглушка откручивается ключом, потом руками. Аккуратнее – моторная смазка сразу польется сильной струёй.
Слив происходит быстро, приблизительно за пять минут.
А затем заливаем новое масло в двигатель. Полная замена моторного масла невозможна, всегда остаётся 3-4% старой отработки, не влияющие на работоспособность движка.
При замене масла в двигателе оценивается состояние слитой моторной жидкости на наличие загрязнений и нежелательных примесей. Иногда стоит промыть систему – это отдельная тема.
Замена масла через щуп обязательна – необходимо выставить правильный уровень масла в двигателе. Сначала заливается 80% и понемногу добавляется до нужного количества.
Замена передних тормозных колодок
Для замены передних тормозных колодок авто нужно установить на ровную площадку, поставить его на стояночный тормоз и кинуть противооткатные башмаки под колеса. Затем авто поддомкрачивается с той стороны, где будет производиться замена передних тормозных колодок, предварительно ослабляются болты крепления колеса.
|
|
После поддомкрачивания колесо полностью снимается со ступицы. На данном этапе можно визуально оценить состояние колодок, если замечен сильный их износ – они меняются. Для этого нужно выкрутить один из крепежных болтов суппорта. Далее суппорт снимается с диска путем проворачивания его вокруг оси второго болта крепления. После чего изношенные колодки извлекаются из суппорта.
Перед тем, как заменить передние тормозные колодки, нужно будет утопить поршень в тормозной цилиндр, иначе установить на место суппорт будет невозможно. Вдавливать его нужно с усилием, но аккуратно, поскольку суппорт сделан из алюминия и повредить его несложно.
После того как поршень будет вдавлен, в суппорт устанавливаются колодки, он ставится на место и закрепляется обратно болтом крепления. После чего устанавливается на место колесо и авто снимается с домкрата.
Замена задних тормозных колодок, если они дисковые, производится таким же путем, как и спереди.
Замена задних тормозных колодок
А вот если сзади установлен барабанный механизм, замена задних тормозных колодок более трудоемкая, тем дисковых.
Опять же колесо там, где будет производиться замена тормозных колодок, поддомкрачивается и снимается с авто. Чтобы снять барабан, нужно будет расстопорить гайку крепления барабана и саму гайку выкрутить. Далее аккуратно поддевая барабан с разных сторон, он снимается с оси ступицы. При снятии важно проследить за подшипником, который установлен в барабан. Если имеется механизм стояночного тормоза, то он снимается.
|
|
Далее нужно аккуратно снять стяжные пружины, следует учитывать , что усилие этих пружин значительное. После снятия пружин снимаются пластинчатые пружины фиксаторов колодок и колодки снимаются.
Перед заменой задних тормозных колодок, нужно будет утопить в рабочем цилиндре поршни. После чего колодки ставятся на место. После чего фиксируются фиксаторами, на них устанавливаются стяжные пружины и механизм стояночного тормоза. Затем на место устанавливается барабан с подшипником и затягивается он гайкой, сама гайка стопорится. После устанавливается колесо. Замена задних тормозных колодок барабанного механизма произведена.
Важно учитывать, что замена колодок производится как минимум парно, то есть, если заменены колодки на одном переднем колесе, то менять их нужно и на втором. А лучше производить замену колодок сразу на всех колесах.
Замена ремня грм.
Главное правило, которое важно соблюдать во время замены ремня — не нарушить фазы газораспределения, что достигается совмещением меток на шестернях, маховике коленвала и корпусе двигателя. В процессе ведения работ нужно контролировать, чтобы метки не сдвинулись. Процедура делится выполняется по такой схеме:
· Разборка узла и снятие старого ремня.
· Визуальный осмотр деталей механизма и очистка внутренней полости от грязи.
· Установка нового ремня с роликом, его натяжение.
· Сборка и проверка работоспособности.
Ремонт шин
Чтобы выполнить ремонт шины, используя специальный ремонтный жгут, необходимо иметь специальный набор для выполнения такого рода ремонта. В набор входит: два шила (для подготовки и установки жгута), клей, набор жгутов. В принципе этот набор может и отличаться в зависимости от фирмы производителя этого набора.
Первое, что необходимо сделать — это снять колесо и найти место прокола. Если место прокола видно и к нему есть доступ, то колесо можно не снимать. Если же прокол не удается найти, можно воспользоваться старым "дедовским" методом: опускаем колесо вводу и смотрим откуда идут пузырьки воздуха. Или на крайний случай берем бутылку с водой и поливаем шину, наблюдая не появляются ли пузырьки.
Далее, место для удобства обозначается маркером или мелом, и очищается от загрязнений. Если в месте прокола есть инородный предмет его следует извлечь.
После этого специальным шилом производится зачистка отверстия, то есть подготовка для установки жгута.
Когда место зачищено и подготовлено, в шило с ушком устанавливается ремонтный жгут, промазывается клеем, аккуратно вводится в место прокола.
Шило достается после того как вы убедитесь, что жгут прошел насквозь и место прокола заклеено.
Если отверстие большое и установленный жгут не полностью заделал отверстие, шаги "4" и "5" следует повторить.
После завершения процедуры хвостики, торчащие из отверстия, аккуратно подрезаются.
Качаем колесо, проверяем давление в шинах и продолжаем движение.
Такой способ при правильном подходе и надлежащем выполнении позволяет надежно заклеить бескамерку, которая еще долго прослужит.
Замена охлаждающей жидкости
Процесс замены следует проводить в два этапа, сначала жидкость сливается с радиатора, далее с охлаждающей рубашки двигателя. Стоит помнить, что эта процедура проводиться только на холодный двигатель, чтоб избежать ожогов и прочих повреждений. Для слива нам понадобится емкость объемом 8?10 литров.
Поочередность действий по сливу старой охлаждающей жидкости:
Сливаем воду с радиатора, снимаем защиту с двигателя если такая есть, если печка в салоне регулируется механическим путем, то переводим рычаг в крайнее положение на тепло.
Далее снимаем крышку расширительного бачка, чтоб не создавался вакуум в системе.
Под радиатор ставим емкость и откручиваем сливную пробку аккуратно, чтоб не повредить сам радиатор, так как соты и он сам сделаны с алюминия зачастую. Повредить несложно, а вот заварить его можно только аргоновой сваркой.
После слива жидкости, даем постоять минут пять, чтоб окончательно слилась вся жидкость. На двигателе, так же находим сливную пробку, открутив, сливаем в емкость.
После слива, даем минут десять постоять до полного слива жидкости. Ни в коем случае не промывайте водой проточной, так как может образоваться коррозия внутри водяной рубашки. Некоторые автолюбители откручивают еще патрубок от радиатора, чтоб не образовалась пробка.
После слива старой жидкости и сбора деталей в обратном порядке, приступаем к заливу свежей жидкости (понадобится порядка 8?10 литров). На дроссельной заслонке откручиваем шланг с охладительной системы. Заливаем жидкость в расширительный бачок или в радиатор, если есть пробка сверху, до тех пор, пока не потечет из шланга. Доливаем жидкость в расширительный бачек до отметки максимум.
Теперь заводим автомобиль и запускаем печку на отопление, прогрев агрегат до температуры 50?60 градусов глушим его и проверяем уровень в расширительном бачке, при надобности доливаем тосола.
Балансировка колес
Балансировку колес автомобиля проводят на специальных станках для балансировки, которые могут отследить центр тяжести. Основой такого станка может быть как примитивный компьютер, так и целая система, с лазерными датчиками и множеством измерительных механизмов. Такой станок автоматически определяет место отклонения и указывает где нужно установить балансировочный грузик.
В зависимости от типа диска будет меняться и вид грузика для балансировки колес, для стальных дисков со специальной скобой-крепежом, для легкосплавных дисков специальные грузики с посадкой на внутреннюю часть обода. Сами грузики выполнены с цинка или чаще свинца, но в меру развития технологий появились и стальные грузики. Масса устанавливаемого грузика зависит от меры дисбаланса, для литых дисков выпускаются грузики от 5 до 60 грамм с шагом в 5 грамм. Для стальных дисков эти рамки от 5 до 100 грамм, так же с шагом 5 грамм. Такие грузики в любом случае устанавливаются в случае балансировки колес автомобиля.
Чем большей массы требуется установить грузик, тем вероятней становится показатель, что нужно проверить геометрию диска или правильность его сборки, правильно ли направлен протектор. На штампованные диски или по-другому стальные устанавливают набивные грузики, они крепятся на ребро диска за счет набивки между диском и покрышкой, с типа установки во время балансировки и пошло их название.
Для легкосплавных дисков такие грузики для балансировки не подойдут, во-первых, испортит весь внешний вид, а во-вторых, можно легко повредить диск. Обычно для такой балансировки используют специальные грузики, они устанавливаются на внутреннюю сторону диска, они так же одеваются на ребро диска, такие грузики относят к классу набивных, но по внешней структуре они отличаются. Чаще ставят самоклеющиеся грузики, на клейкой основе, отсюда и пошло название – липучка. Удобство липучек в том, что их легко ставить, практически незаметны после балансировки. Внешний вид липучек если и заметен, то в разы привлекательней набивных грузиков. Но для таких грузиков поверхность должна быть идеально ровной, без сколов и слоения покрасочного материала.
Так с чего же начинается процесс балансировки колес автомобиля. В любом случае, независимо от марки, модели автомобиля или характеристик дисков, их нужно демонтировать с автомобиля. Зачастую рекомендуют снимать шины поштучно: по технологии снял, отбалансировал, поставил, снял следующее колесо - проходят по кругу автомобиля.
Далее весь процесс зависит от квалификации специалиста, который занимается балансировкой колес и от самого оборудования, на котором будет проводиться процедура, но 90% от специалиста. Если СТО работает на современном оборудовании, то специалист сам проверит на наличие неисправностей шины и промоет её от грязи на специальном станке. Чтоб имитировать ступицу автомобиля во время балансировки, есть специальная металлическая пластина. В зависимости от количества отверстий в диске, соответственно подбирается пластина.
Надев металлическую пластину на диск, и тщательно закрутив гайки, специалист отправляется к станку для начала процесса балансировки колес автомобиля. В зависимости от станка, процесс определения неровности может отличаться. Самый обычный балансировочный станок определит точки дисбаланса и покажет, с какой стороны и какого веса нужно установить грузик. Если же используется балансировочный станок с лазерными датчиками, то система покажет все недочеты, в том числе и геометрию диска, по отдельности диск и шину, но естественно и цена балансировки колес автомобиля будет больше.
Определив место дисбаланса, специалист начинает устанавливать грузики, набивая или наклеивая на диск. После набивки грузиков, процедура проверки наличия дисбаланса снова проверяется и в случае надобности грузики заменяются или добавляют новые. В таком цикле процедуру балансировки колес автомобиля, определения дисбаланса и установку грузиков повторяют, пока дисбаланс не станет равен нулю или близок к нулю.
Не исключен вариант, что диск может потерять свою геометрию и его придется прокатывать, только тогда переходить к балансировке колес автомобиля. По завершению всех необходимый этапов балансировки, шина снимается с оси станка, далее специалист снимает металлическую пластину с диска и отдает шину для установки на автомобиль. По советам опытных водителей, балансировку колес стоит проводить парами. Если решили балансировать одно из передних колес, то обязательно проведите балансировку второго переднего, даже если нет на то причин.
Диагностика
Диагностика.
Порядок проведения диагностики
Диагностика неисправностей в электронных системах управления автомобиля проводится обычно в такой последовательности.
Шаг 1. Подтверждение факта наличия неисправности
Требуется убедиться, что неисправность реально существует. Если водитель неверно интерпретирует нормальные реакции автомобиля в каких-то обстоятельствах, ему следует это объяснить. Полезным источником информации является сам водитель (владелец) у которого надо уточнить условия возникновения неисправности:
— какова была за бортом температура;
— прогрет ли двигатель;
— проявляется ли неисправность при трогании с места, ускорении или при постоянной скорости движения;
— какие предупреждающие индикаторы на панели приборов при этом включаются;
— какие и когда выполнялись на автомобиле сервисные или ремонтные работы;
— пользовался ли автомобилем кто-либо другой.
Шаг 2. Внешний осмотр и проверка узлов, блоков и систем автомобиля
Проведение осмотра и предварительной проверки при диагностике необходимо. По оценкам экспертов, 10-30% неисправностей на автомобиле выявляются таким путем. До проведения диагностики неисправностей в системе управления двигателем важно устранить очевидные неисправности, такие как:
— утечка топлива, масла, охлаждающей жидкости;
— трещины или не подключенные вакуумные шланги;
— коррозия контактов аккумуляторной батареи;
— нарушение электрических соединений в контактных разъемах;
— необычные звуки, запахи, дым;
— засорение воздушного фильтра и воздуховода (при длительном простое автомобиля грызуны могут делать там гнезда или запасы корма).
Необходимо также провести предварительную проверку всех функциональных устройств. На этом этапе следует определить, что исправно и что неисправно, для чего поочередно включаются и выключаются все подсистемы.
При этом следует обратить внимание на признаки предыдущих ремонтов — всегда есть риск, что при ремонте что-то забыли подключить или неправильно соединили.
Шаг 3. Проверка технического состояния подсистем
Проверка уровня и качества моторного масла.
1. Уровень масла должен быть в пределах нормы.
2. Если масло на щупе вспыхивает или горит, то в масле присутствует бензин и его пары через систему вентиляции картера излишне обогащают топливовоздушную смесь (ТВ-смесь).
3. Если на разогретой поверхности (например, на выпускном коллекторе) масло кипит или пузырится, в нем содержится влага.
4. Разотрите каплю масла в пальцах, убедитесь, что в нем нет абразивных частиц.
Уровень охлаждающей жидкости и ее качество.
Правильное функционирование системы охлаждения двигателя очень важно для его нормальной работы. При перегреве неизбежно возникают проблемы.
1. Уровень охлаждающей жидкости должен быть в пределах нормы. Проверяется он при холодном двигателе. В рабочем режиме при попытке снять крышку радиатора горячая (температура выше 100 °С) охлаждающая жидкость под давлением выплескивается наружу и может причинить ожоги.
2. Перед зимней эксплуатацией с помощью гидрометра определяются точки кипения и замерзания охлаждающей жидкости, т. е. правильность концентрации антифриза.
3. При работе под давлением неисправная система охлаждения двигателя дает утечку охладителя. В местах протечек обычно видны потеки: серо-белые, ржавые, зеленоватые от антифриза.
4. Если в радиаторе оказываются холодные секции, значит, они засорены.
5. Проверяется работа реле вентилятора, двигателя электровентилятора, натяжение приводного ремня водяного насоса.
Уровень топлива в баке.
Убедитесь, что бак заполнен бензином не менее чем на четверть, в противном случае грязь и вода со дна могут быть закачены в топливную систему.
Напряжение аккумуляторной батареи.
Напряжение должно быть не менее 12,4 В и в пределах
13,5 — 15,0 В при работе генератора.
Понижение напряжения на аккумуляторной батарее вызывает:
— увеличение расхода топлива, т. к. ЭБУ двигателя компенсирует снижение напряжения питания увеличением продолжительности открытого состояния форсунок;
— увеличение оборотов холостого хода. ЭБУ таким образом ускоряет заряд аккумулятора.
Исправность электроискрового зажигания.
Исправность системы зажигания проверяют с помощью высоковольтного разрядника (тестера зажигания), который подключают к высоковольтному проводу на свече и при этом прокручивают двигатель. Проверка искрообразования на стандартной свече при атмосферном давлении не показательна. В цилиндре двигателя искровой пробой на свече происходит под давлением, что при атмосферном давлении в тестере имитируется увеличением длины искрового промежутка до 19 мм. Для пробоя система зажигания должна выдать напряжение 25-30 кВ.
Шаг 4. Работа с сервисной документацией. Считывание диагностических кодов
По оценкам производителей, до 30% случаев неисправностей автомобилей обнаруживается и исправляется на основе информации в виде указаний, предположений, диагностических карт в руководствах по техническому обслуживанию и ремонту. Перед использованием документации следует точно знать: модель, год выпуска, тип двигателя и трансмиссии, постоянная или непостоянная это неисправность. Современное диагностическое оборудование уже содержит карты поиска неисправностей, например DIS (диагностическая информационная система, которая входит в состав оборудования BMW GT1, OPS, BMW STD OBD и других).
В памяти компьютера ЭБУ (в регистраторе неисправностей) сохраняются как коды постоянных (текущих) неисправностей, так и тех, которые были обнаружены ЭБУ, но в данный момент не проявляются — это непостоянные (однократные, исторические) коды. Коды и постоянных и непостоянных неисправностей, которые по сути дела являются диагностическими кодами, называются кодами ошибок или кодами неисправностей. Но строго говоря, это не одно и тоже. Если при возникновении какой-либо неисправности (постоянной или непостоянной) врегистратор неисправности записывается строго однозначный код, то такой диагностический код может быть назван «кодом неисправности». Такой код возникает под прямым непосредственным воздействием конкретной неисправности и присущ только ей. Но некоторые неисправности воздействуют на систему самодиагностики не прямо, а опосредованно, через изменения параметров в ЭБУ. Такие неисправности не имеют своего прямого кода для фиксации в регистраторе, но как и любые другие неисправности, вызывают нарушение штатного (стандартного) режима работы контролируемой системы. Как следствие врегистратор неисправностей записывается код сбоя в системе, который и называется «кодом ошибки». Как правило, код ошибки указывает на несколько возможных неисправностей и в разных подсистемах (или устройствах) управления. В современных электронных системах автоматического управления причинно-следственные связи между непостоянными неисправностями и диагностическими кодами не всегда однозначны, и поэтому, коды фиксируемые в ЭБУ на непродолжительное время (на несколько циклов «пуск-останов ДВС») более полно соответствуют кодам ошибок. Однако, следует отметить, что общепринятой (стандартной) терминологии для обозначения типов диагностических кодов пока не разработано.
Шаг 5. Просмотр параметров с помощью сканера
Сканер — это миниатюрный переносной прибор, обычно с дисплеем на жидких кристаллах.
Все автомобили GeneralMotors и Chrysler с 1981 г. позволяют просматривать параметры режима двигателя с помощью сканера, подключенного к диагностическому разъему.
Параметров много, и просматривать их все подряд бессмысленно, сообщения типа «это значение неверно сканер все равно не выдаст. Нужно или следовать какому-то плану, например диагностической карте, или просмотреть наиболее информативные о работе двигателя параметры:
— убедиться, что для холодного двигателя температура охлаждающей жидкости и воздуха во впускном коллекторе одинаковая;
— клапан регулятора оборотов холостого хода должен быть открыт на допустимое число шагов (или %);
— сигнал с датчика кислорода должен опускаться ниже уровня 200 мВ, подниматься выше 700 мВ, фронты непологие, частота не менее 4 Гц.
Шаг 6. Локализация неисправности на уровне подсистемы или цилиндра
Это наиболее трудоемкая часть диагностирования, т. к. необходимо выполнить следующие процедуры:
— разобраться с диагностическими картами и технической документацией;
— применить рекомендованную аппаратуру и методику диагностики;
— просмотреть изменение коэффициентов коррекции подачи топлива, сделанные ЭБУ при разных режимах работы двигателя;
— произвести тест баланса мощности по цилиндрам.
Шаг 7. Ремонт
Ремонт или замена каких-либо деталей и систем производится согласно инструкциям производителя. Если после замены неисправность сохраняется, приходится повторить все процедуры еще раз. В конце концов, должен быть получен детальный ответ на вопрос, почему же произошла эта неисправность.
Шаг 8. Проверка после ремонта и стирание кодов ошибок из памяти ЭБУ
1. В испытательной поездке следует убедиться, что неисправность устранена и не возникли новые из-за ремонта.
2. Согласно процедуре, рекомендованной производителем, стираются коды ошибок в ЭБУ, в противном случае компьютер может ложно учитывать их при управлении двигателем.
3. Настройки в памяти радиоприемника, маршрутного компьютера и т. д. должны быть сохранены или восстановлены.
Дата добавления: 2018-05-13; просмотров: 256; Мы поможем в написании вашей работы! |
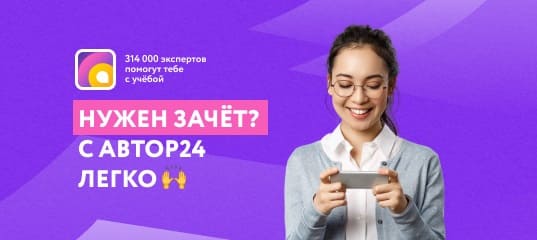
Мы поможем в написании ваших работ!