Анализ на содержание твердых примесей
Анализ на содержание твердых примесей используется для определения содержания:
· Песка.
· Всей твердой фазы.
· Жидкой фазы.
· Нефтепродуктов.
· Воды.
Наличие твердых примесей влияет на большинство свойств бурового раствора, включая плотность, вязкость, прочность геля, потери жидкой фазы и термическую стабильность. Содержание твердых примесей определяет также методы обработки раствора и состав
оборудования, необходимого для эффективного проведения буровых работ.
Определение катионообменной ёмкости (CEC), в том числе метиленовой синькой (MBT)
Этот анализ позволяет получить данные о текущей концентрации глинистых частиц в буровом растворе. Результаты анализа обычно выражаются в бентонитовом эквиваленте (фунт/баррель) или в миллиэквиваленте на миллилитр раствора (мэк/мл).
Обзор способов контроля содержания твердых примесей
Контроль содержания твердых примесей состоит в отслеживании накопления в растворе вредных твердых частиц и их отрицательного воздействия на систему. Повышение содержания твердой фазы оказывает нежелательное воздействие на
эксплуатационные характеристики бурового раствора и на процесс бурения. В тех случаях, когда концентрация твердой фазы малой плотности становится чрезмерной, могут возникнуть трудности при контролировании реологических и фильтрационных свойств раствора. При этом снижается скорость бурения, сокращается срок службы долота (коронки бура), возникают серьезные проблемы, связанные с высокой концентрацией твердых частиц в скважине. При буровых работах оборудование для контроля твердой фазы должно действовать в режиме технологической установки.
|
|
Цель применения оборудования для отделения твердых примесей состоит в том, чтобы отсортировать выбуренные твердые частицы. Приемлемый уровень удаления выбуренных твердых частиц составляет 90 %. Вторая задача применения этого оборудования состоит в том, чтобы удалить из обломков выбуренной породы как можно больше воды, нефти и синтетических материалов. Когда эта задача решена, разбавление водой может стать экономически выгодным. В утяжеленных буровых растворах приемлемый уровень объемного содержания твердой фазы малой плотности составляет от 3 до 6 %. В легких буровых растворах допустимая концентрация твердой фазы малой плотности – 5–7 %.
Источники появления и размеры твердых частиц
Существует два основных источника появления в растворе твердых частиц – это химические добавки и выбуренные обломки пород пласта. Химические добавки – это материалы, добавляемые в буровой раствор для сохранения его свойств. Обломки пластовых пород попадают в систему раствора, когда буровое долото врезается в породу при бурении новой скважины; эти обломки являются загрязняющим фактором, который снижает эксплуатационные характеристики бурового раствора. Если эти обломки не удалить, они будут
|
|
дробиться на все более и более мелкие частицы, которые будет еще труднее удалить из раствора. Большая часть породы пласта может быть удалена из раствора на поверхности механическими
методами. Мелкие частицы удалить труднее, и они сильнее влияют на свойства бурового раствора, чем крупные частицы. Размер выбуренных твердых частиц, находящихся в буровом растворе, может составлять от 1 до 250 микрон (1 микрон равен 1/25 400 дюйма или 1/1000 мм).
В следующей таблице приведены примерные размеры твердых частиц, загрязняющих буровой раствор.
Материал | Диаметр частиц, мкм | Номер сита | Диаметр частиц, дюймы |
Глина, коллоиды | 1 | 0,0004 | |
5 | 0,0002 | ||
Бентонит Мелкая соль Бариты Тонкая цементная пыль | 10 | 1470 | 0,0004 |
Крупнозернистый алеврит | 44 | 325 | 0,0018 |
53 | 270 | 0,002 | |
74 | 200 | 0,003 | |
Песок (по стандарту АНИ) | 105 | 140 | 0,004 |
149 | 100 | 0,006 | |
Крупный песок | 500 | 35 | 0,020 |
1000 | 18 | 0,040 |
|
|
Методы контроля содержания твердых частиц
Существует два основных метода контроля:
· Использование механических средств для отделения твердых частиц.
· Разбавление бурового раствора.
Механические средства для отделения твердых частиц
Механические средства для отделения твердых частиц можно разделить на две основные группы:
· Механические сита.
· Центробежные сепараторы.
Кроме того, центробежные сепараторы могут быть двух типов – осадительные центрифуги и гидроциклоны. В таблице 11-2 приведены типы оборудования и размеры частиц (в микронах), которые могут удаляться с их помощью.
Оборудование для отделения твердых частиц | Могут удаляться… |
Механические сита | Частицы размером 74 мкм при сите номер 200 |
Центробежные сепараторы: осадительные центрифуги, гидроциклоны | Коллоидные частицы размером до 5 мкм, твердые частицы размером 20‑70 мкм – в зависимости от размеров керна |
Механические сита
Механическое сито, называемое также вибрационным ситом, содержит одно или больше вибрирующих сит, через которые пропускается буровой раствор, поступающий из скважины в процессе циркуляции. Вибросита для бурового раствора подразделяются по типу движения.
|
|
Существуют вибросита с круговым/эллиптическим и прямолинейным движением.
Эти типы вибросит описаны ниже:
· Вибросита с круговым/эллиптическим движением.В этих виброситах применяются ролики эллиптического сечения для того, чтобы придать ситам круговые качательные движения, что обеспечивает лучшее удаление твердых частиц при пропускании раствора через сита
· Вибросита с прямолинейным движением.В этих системах используется
прямолинейное качательное (возвратно-поступательное) движение сит, что способствует прохождению раствора сквозь сита
Сита
Эффективность сита определяется рядом характеристик, включая размеры отверстий (номер сита) и конструкцию сетки.
Сетки с квадратными ячейками | ||||
Число отверстий на дюйм | Диаметр проволоки | Ширина просвета | Площадь проходного сечения (в %) | |
Дюймы | Дюймы | Микроны | ||
20 x 20 | 0,016 | 0,0340 | 863 | 46,2 |
30 x 30 | 0,013 | 0,0203 | 515 | 37,1 |
40 x 40 | 0,010 | 0,0150 | 381 | 36,0 |
50 x 50 | 0,009 | 0,0110 | 279 | 30,3 |
60 x 60 | 0,0075 | 0,0092 | 234 | 30,5 |
80 x 80 | 0,0055 | 0,0070 | 178 | 31,4 |
100 x 100 | 0,0045 | 0,0055 | 140 | 30,3 |
120 x120 | 0,0037 | 0,0046 | 117 | 30,7 |
Размер ячеек. Размер отверстий в сите (размер ячеек) определяет размер частиц, которые могут быть удалены при помощи вибросита. Размер ячеек определяется номером сита – количеством отверстий на линейный дюйм, при измерении от середины диаметра проволоки. Так, например, сито 70 x 30 с ячейками продолговатой (прямоугольной) формы имеет 70 отверстий на дюйм в одном направлении и 30 отверстий на дюйм в перпендикулярном направлении. Фактические размеры отделяемых ситом частиц зависят от таких факторов, как форма частиц, вязкость раствора, скорость подачи раствора и когезионная способность частиц. Кроме того, размер отделяемых частиц может определяться и гидравлическими процессами, которые могут происходить в растворах. Некоторые растворы могут образовывать пленки с большим поверхностным натяжением на сеточной проволоке, что приводит к уменьшению размеров эффективного проходного сечения сита. В следующих таблицах приведены технические характеристики и обозначения для различных номеров сит и форм ячеек.
Сита с продолговатыми ячейками | ||||
Число отверстий на дюйм | Диаметр проволоки | Ширина просвета | Площадь проходного сечения (в %) | |
Дюймы | Дюймы | Микроны | ||
20 x 30 | 0,014 | 0,036/0,0193 | 914/490 | 41,8 |
20 x 40 | 0,013 | 0,0371/0,012 | 940/305 | 35,6 |
20 x 60 | 0,009 | 0,041/0,0076 | 1041/193 | 34,0 |
40 x 60 | 0,009 | 0,016/0,0076 | 406/193 | 29,4 |
40 x 80 | 0,0075 | 0,0181/0,0055 | 457/140 | 35,6 |
Конструкция сит
Сита бывают двухмерной и трехмерной конструкции. Двухмерные (плоские) сита могут подразделяться на:
· Панельные сита, имеющие два или три слоя, скрепленных по каждой стороне с помощью сплошной двухслойной профилированной ленты
· Сита с перфорированной пластиной, имеющие два или три слоя, прикрепленных к перфорированной металлической пластине, что обеспечивает жесткость сборки и простоту ремонта
· Трехмерные сита представляют собой перфорированные плоские сита, которые имеют гофрированную поверхность, расположенную параллельно потоку жидкости. Такая конфигурация обеспечивает большую площадь сита по сравнению с двухмерной. Трехмерные сита могут быть различных типов:
· Пирамидальные
· Платообразные
Обозначения сит
АНИ (стандарт RP13E) рекомендует, чтобы все сита имели этикетки с обозначением названия сита, потенциала разделения и пропускной способности. Потенциал разделения представляет собой проектную величину (в процентном выражении) твердых примесей, которые могут быть удалены с помощью этого сита.
Пропусканная способность сита определяется скоростью потока раствора, допустимой при использовании данного сита.
Могут использоваться и дополнительные обозначения: номер сита по американскому стандарту, аспектное отношение и коэффициент пропускания.
Название сита | Номер сита по стандарту США | Потенциал разделения, микроны | Пропускная способность | Аспектное отношение | Коэффициент пропускания | |||
d50 | d16 | d84 | Усл, (Cond) | Площадь | ||||
Derrick PMD DX 50 | 48 | 318 | 231 | 389 | 6,10 | 7,42 | 1,45 | 45,3 |
Brandt BHX 50 | 47 | 327 | 231 | 349 | 8,85 | 7,28 | 1,43 | 64,4 |
Sweco DX 50 | 47 | 324 | 234 | 390 | 6,77 | 7,7 | 1,45 | 52,09 |
Центробежные сепараторы
Применяются два типа центробежных сепараторов:
· Осадительные центрифуги
· Гидроциклоны
Осадительные центрифуги
Осадительная центрифуга имеет в своем составе конический горизонтально расположенный стальной ротор, вращающийся с большой скоростью, и двойной подающий шнек. Этот шнек вращается в том же направлении, что и вмещающий его ротор, но скорость его вращения
немного меньше. Важной особенностью работы центрифуги является разбавление глинистого бурового раствора, который в нее подается. Разбавление раствора снижает вязкость подаваемого материала и обеспечивает сепарационную эффективность агрегата. Чем выше вязкость базового раствора, тем сильнее надо его разбавлять (обычно подается от 2 до 4 галлонов воды в минуту). Вязкость фильтрата (жидкого материала, выходящего из центрифуги) должна составлять для эффективной сепарации 35-37 секунд на кварту. Если значение вязкости падает заметно ниже 35 секунд на кварту, значит, было добавлено слишком много воды. В этом случае внутри ротора возникает турбулентность и эффективность процесса снижается.
Примечание:
Необходимо соблюдать рекомендации изготовителей относительно скорости подачи раствора и скорости вращения ротора.
Если для отделения твердых примесей используется одна центрифуга, то через нее следует пропускать системы растворов малой плотности. Последовательное использование двух центрифуг рекомендуется для обработки следующих систем:
· Эмульсионных систем «вода в нефти» (т. е. систем на основе нефтепродуктов и синтетических веществ)
· Высокоплотных систем на водной основе
· Систем на водной основе, для которых замена основы требует больших затрат (например, солевых растворов)
Первая центрифуга используется для сепарации барита и возвращения его в систему бурового раствора. Второй агрегат проводит обработку верхнего продукта, поступающего из первого агрегата, удаляя все твердые частицы, после чего полученная жидкая фаза возвращается в систему бурового раствора.
Примечание:
Эффективность действия центрифуги зависит от плотности и вязкости бурового раствора. Во время работы центрифуги следует регулярно проводить анализ нижнего продукта, чтобы определять объем твердой фазы малой плотности и барита, которые удаляются из раствора и сохраняются.
Гидроциклоны
В то время как центрифуга может обрабатывать только отдельные составляющие систем бурового раствора, гидроциклоны рассчитаны на обработку всего потока раствора. В состав гидроциклона входит конический резервуар (конус), в котором сила давления передается на тангенциально расположенные входные отверстия загрузочной камеры. Возникающие при этом центробежные силы многократно увеличивают скорость осаждения материалов тяжелой фазы (твердых частиц и более плотной жидкости), заставляя их двигаться по направлению к стенкам конуса. Более легкие частицы движутся к оси конуса и вверх в виде спирального завихрения по
направлению к сливному отверстию в верхней части конуса. Выпускаемая в нижней части резервуара масса называется нижним продуктом; из верхней части резервуара выходит сток, или верхний продукт. Нижний продукт должен выходить из сливного отверстия в виде мелкодисперсной струи с небольшой зоной всасывания (подсоса) в центре. Если продукт выходит в виде сплошной струи без подсоса воздуха, следует провести регулировку агрегата.
Размеры конуса и давление нагнетающего насоса определяют состав получаемых фракций. Использование более низких давлений приводит к более грубой сепарации и снижению производительности. Рекомендуется использовать конусы диаметром 6 дюймов или более.
Дата добавления: 2018-05-12; просмотров: 659; Мы поможем в написании вашей работы! |
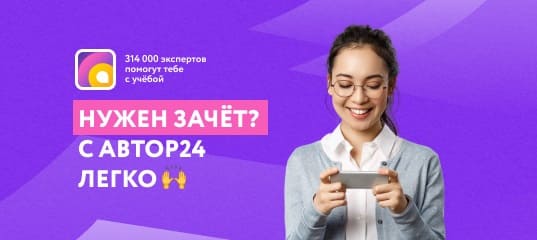
Мы поможем в написании ваших работ!