Основные технологические операции ковки.
ЛЕКЦИИ № 3 - 6. ПРОИЗВОДСТВО ЗАГОТОВОК ПЛАСТИЧЕСКИМ ДЕФОРМИРОВАНИЕМ
Производство заготовок из проката.
Прессование и волочение металлов.
Производство заготовок ковкой.
Общая характеристика штамповочного производства
Специализированные процессы кузнечно-штамповочного производства
Введение
На предприятиях машиностроительной и металлургической промышленности применяются различные методы обработки металлов давлением. Так, например, на машиностроительных предприятиях широко применяется свободная ковка, объемная и листовая штамповка, на металлургических заводах — прокатка, волочение и прессование (выдавливание).
Свободная ковка осуществляется на молотах, либо прессах. Разнообразие форм поковок, получаемых в результате свободной ковки, достигается использованием одного и того же универсального инструмента — бойков, прошивней, раскаток и других. В процессе свободной ковки под действием усилия развиваемого молотом или прессом, происходит осаживание металла по высоте с увеличением его размеров в длину и ширину. Таким образом, форма изделия образуется за счет обжатия заготовки и неодинаковой деформации в различных направлениях.
Электрошлаковая сварка дает возможность широкого применения сварно-литых, сварно-кованых конструкций и крупных деталей, полученных гибкой толстого листа с последующей приваркой кованых или литых частей.
|
|
Объемная штамповка является разновидностью ковки и представляет собой технологический процесс, при котором штампованная поковка получается путем принудительного заполнения металлом полости штампа.
Деформация металла при объемной штамповке осуществляется посредством специального инструмента — штампа, рабочая полость которого представляет собой оттиск формы изделия, которое необходимо получить. Поэтому форма и размеры полости штампа должны соответствовать виду требуемого изделия.
Для объемной горячей штамповки используются штамповочные молоты, горизонтально-ковочные машины, механические и гидравлические ковочные прессы и другое кузнечно-прессовое оборудование.
Исходным материалом для объемной горячей штамповки служат различные профили сортового и периодического проката.
Применяя методы точной объемной, преимущественно холодной штамповки, можно получить детали машин, которые не требуют выполнения последующей механической обработки резанием.
Прокатка является одним из распространенных методов обработки металлов давлением. В начале прокатывали олово для изготовления посуды, золото и серебро для чеканки монет, свинцовые листы для труб. В настоящее время методы прокатки металла получили широкое практическое применение в производстве различных видов изделий.
|
|
В зависимости от расположения валков и их относительного движения методы прокатки бывают: продольная, поперечная и винтовая (геликоидальная).
Машиностроение является основным потребителем прокатного металла, используемого для различных деталей машин и механизмов. Особое внимание уделяется применению экономически выгодных профилей переменного сечения — периодического проката, обеспечивающего рациональное использование их в конструкции машин.
Все процессы обработки металлов давлением основаны на способности металлических материалов в твердом состоянии изменять форму и размеры под действием приложенных внешних сил, т.е. пластически деформироваться.
Несмотря на большое многообразие процессов обработки давлением, их можно объединить в две основные группы — процессы металлургического и машиностроительного производства.
К первой группе относятся: прокатка, прессование и волочение, т. е. процессы, в основе которых лежит принцип непрерывности технологического процесса. Продукцию металлургического производства (листы, полосы, ленты, периодический и профильный прокат, трубы, профили, проволоку и т.п.) используют как заготовку в кузнечно-штамповочных и механических цехах и как готовую продукцию для создания различного рода конструкций.
|
|
Во вторую группу входят такие процессы, как ковка, объемная штамповка (горячая и холодная), листовая штамповка. Эти процессы обеспечивают получение заготовок изделий (деталей) и готовых деталей, не требующих последующей механической обработки.
Кованые и штампованные заготовки (поковки) отличаются высокими механическими свойствами, что обеспечивает высокую надежность и долговечность выпускаемой продукции, поэтому наиболее ответственные, тяжело нагруженные детали машин изготавливают из заготовок, полученных ковкой или штамповкой.
Обработке давлением могут подвергаться те металлы и сплавы, которые обладают необходимым запасом пластичности, обеспечивающим деформирование без нарушения сплошности материала, т.е. без его разрушения. Пластичность не является неизменным, наперед заданным свойством материала - на нее оказывает влияние ряд факторов: химический состав материала, температура и скорость деформации, форма очага деформации и т.п. Создавая соответствующие условия деформирования, можно получить требуемую технологическую пластичность.
|
|
К зависимости от температуры и скорости деформации различают холодную и горячую деформации.
Холодная деформация происходит при таких температурно-скоростных условиях, когда в материале протекает только один процесс — упрочнение (или наклеп) металла.
Горячая деформация осуществляется при таких температурно-скоростных условиях обработки, когда в материале протекают одновременно два процесса: наклеп и рекристаллизация (упрочнение и разупрочнение), причем скорость разупрочнения равна или выше скорости упрочнения. При горячей деформации улучшаются все механические свойства материала: и прочностные, и пластические, особенно повышается ударная вязкость. После горячей деформации, как правило, микроструктура, мелкозернистая, макроструктура волокнистая. Образование волокнистой макроструктуры при горячей деформации — полезное явление, особенно при изготовлении ответственных деталей (турбинных дисков, валов, роторов и т.п.).
При выборе технологического процесса обработки металлов давлением следует учитывать технологические свойства сплавов. Чем ниже пластичность материала, тем сложнее получить качественную заготовку, тем сложнее технологический процесс и выше себестоимость детали.
ПРОКАТКА
Во многих случаях, когда требуются высокие прочность и пластичность, применяют заготовки из сортового и специального проката. В процессе прокатки нагретые до температуры деформирования литые заготовки подвергают многократному обжатию в валках прокатных станов, в результате чего значительно повышается плотность материала за счет «залечивания» литейных дефектов — пористости, микротрещин и т.п. Это придает заготовкам из проката высокую прочность и герметичность даже при небольшой их толщине.
Прокаткой называют вид обработки давлением, при котором металл пластически деформируется вращающимися гладкими или имеющими соответствующие канавки (ручьи) валками. Взаимное расположение валков и заготовки, форма и число валков могут быть различными. При этом получают прокат – готовые изделия или заготовки для последующей обработки ковкой, штамповкой, прессованием, волочением, резанием. В прокат перерабатывают до 80% всей выплавляемой стали и большую часть цветных металлов и сплавов. Его используют в машиностроении, строительстве и других отраслях промышленности.
Виды прокатки. Существуют три основных вида прокатки: продольная, поперечная и поперечно-винтовая (косая). При продольной прокатке (рис. 3.1, I) заготовка 2 деформируется между гладкими или имеющими калибры валками 1, вращающимися в противоположные стороны, и перемещается перпендикулярно к осям валков.
При поперечой прокатке (рис. 3.1, II) валки 1 вращаются в одном направлении, оси их параллельны, а заготовка 2 деформируется ими, вращаясь вокруг своей оси.
При поперечно-винтовой (косой) прокатке (рис. 3.1, III) валки 1 вращаются в одном направлении, оси их расположены под некоторым углом, благодаря чему заготовка 2 деформируется валками и при этом не только вращается, но и перемещается поступательно вдоль своей оси.
В винтовых калибрах непрерывное формообразование осуществляется путем перемещения обрабатываемого тела между вращающимися валками, на поверхности которых по винтовой линии нарезаны ручьи (шары).
Рис. 3.1.Основные виды прокатки:
I – продольная прокатка (а – в гладких валках; б – в калибрах); II – поперечная прокатка; III – поперечно-винтовая прокатка ( а – в гладких валках; б – в спиральных валках; в – винтовая (косая) прокатка труб)
ОБОРУДОВАНИЕ ПРОКАТНОГО ПРОИЗВОДСТВА
Прокатным станом называется технологический комплекс последовательно расположенных машин и агрегатов, предназначенных для пластической деформации металла в валках, дальнейшей его обработки, отделки и транспортировки. Высокая производительность прокатных станов определяется тем, что в них совмещены рабочие и транспортные операции и процесс обработки можно вести непрерывно. Использование полученного со станов фасонного и листового проката в качестве заготовок под штамповку резко повышает производительность штамповочного оборудования, снижает отходы металла.
Различают станы продольной, поперечной и поперечно-винтовой прокатки.
На станах продольной прокатки получают листовой и сортовой прокат. Профиль сортового проката: простой геометрической формы (круг диаметром 5-200мм, квадрат или прямоугольник 6х250, шестигранник, длина 2,4,6,9,12 и т.д. м). Листовой прокат: толстолистая (4-160 мм), тонколистая(0,2 – 4 мм), фольга (менее 0,2 мм).
Станы поперечной прокатки служат для получения заготовок в форме тел вращения. На станах поперечной прокатки получают заготовки зубчатых колес, шаров и других деталей.
Станы поперечно-винтовой прокатки используются для производства заготовок осей, шпинделей зубчатых колес, труб и других деталей. Трубы стальные: бесшовные (диаметром 30-650 мм) и сварные (диаметром 10-1420мм).
Комплект прокатных валков со станиной называется рабочей клетью.
На рис. 3.2. представлена кинематическая схема оборудования для деформации прокатываемого металла в валках.
Рис. 3.2. Кинематическая схема прокатного стана:
1 – рабочая клеть, 2 – валки, 3 – шпиндели, 4 – шестеренная клеть,
5 – муфты, 6 – редуктор, 7 – электродвигатель
В рабочей клети 1 в подушках с подшипниками расположены валки 2, вращательное движение не которые передается от главного электродвигателя 7 через редуктор 6, муфты 5, шестеренную клеть 4 и шпиндели 3.
В зависимости от конструкции и расположения валков рабочие клети прокатных станов подразделяются на шесть групп: дуо; трио; кварто;многовалковые; универсальные и специальной конструкции (рис. 3.3).
Клети дуо (двухвалковые) бывают реверсивные (прокатка ведется в две стороны) и нереверсивные (прокатка ведется в одну сторону).
Клети трио чаще нереверсивные. Прокатка на таких станах ведется вперед между нижним и средним валком и назад между верхним и средним. Различают клети трио сортовые – все валки приводные, имеющие одинаковый диаметр, и листовые – средний валок у которых меньшего диаметра и является холостым; при прокатке он прижимается то к верхнему, то к нижнему валку, за счет чего получает вращение.
Клети кварто имеют четыре валка, расположенные друг над другом, и из них два рабочих валка меньшего диаметра и два опорных – большего диаметра. Различают листовые клети кварто, применяемые для прокатки толстых листов, полос и броневых плит, и клети кварто для прокатки рулонов. Последние применяются в станах холодной и горячей прокатки тонких листов, полос, лент, причем перед клетью может устанавливаться разматыватель рулонов, а сзади моталка, создающая натяжение полосы.
Многовалковые клети имеют пять и более валков. Благодаря жесткости и относительно малому прогибу опорных валков на этих клетях производится холодная прокатка тонких полос и узких лент с малым допуском по толщине.
Рис. 3.3. Классификация рабочих клетей:
а – дуо; б – трио сортовые; в – трио листовые; г – кварто листовые; д – кварто для прокатки рулонов; е – многовалковая (шестивалковая); ж – многовалковая (двадцативалковая); з – универсальная; и – специальная (колесопрокатная);
1 – разматыватель рулонов; 2 – моталка, создающая натяжение
Универсальные клети имеют горизонтальные и вертикальные валки: последние обеспечивают обжатие металла в поперечном направлении. Вертикальные валки располагаются, как правило, с передней стороны.
К клетям специальной конструкции относятся клети прокатных станов узкого назначения: колеснопрокатных, кольцепрокатных, шаропрокатных, станов для прокатки профилей переменного сечения. Специальные виды проката: колесо, кольцо, зубчатые колеса, периодические профили и т.п.
В зависимости от назначения прокатные станы можно подразделить на следующие группы: заготовочные, рельсовые, толстолистовые, среднелистовые, тонколистовые, непрерывные листовые (широкополосные) и штрипсовые (производящие штрипс-заготовку для труб в виде полосы шириной до 300 мм).
Основным параметром обжимных и сортовых станов продольной прокатки обычно является диаметр валков. Основным параметром листовых станов является длина бочек валка, которая определяет максимальную ширину прокатываемых листов и полос. Основным параметром трубных и специальных станов является максимальный размер прокатываемого на стане изделия.
ПРОИЗВОДСТВО БЛЮМОВ, СЛЯБОВ, ЛИСТОВОГО И СОРТОВОГО ПРОКАТА
Исходными заготовками при производстве сортового проката или листов являются слитки. Перед прокаткой слитки подогревают до температуры 1300оС.
На рис. 3.4. приведена схема производства сортового проката.
Исходные заготовки – стальные слитки массой до 60 т – нагревают в нагревательных колодцах 1 и подают на слитковоз, который привозит и укладывает слиток 2 на приемный рольганг блюминга 3, после прокатки на котором получают полупродукт квадратного сечения (от140х140 до 400х400 мм), называемый блюмом4. Блюм, двигаясь по рольгангу, проходит машину огневой зачистки, где производится зачистка поверхностных дефектов, и подается к ножницам, где режется на мерные заготовки. Далее блюм поступает, иногда после дополнительного нагрева, на заготовочный стан 5, где производится прокатка на блюмы сечением от 50х50 до 150х150 мм и затем непосредственно на сортопрокатный стан. Для получения требуемого профиля заготовка проходит ряд клетей.
На рис. 3.4. представлено полунепрерывное расположение клетей сортопрокатного стана. В первой группе (7, 8 ,9) заготовка прокатывается непрерывно, т.е. находится в них одновременно, а во второй группе (10, 11) осуществляется последовательная прокатка.
Рис. 3.4. Схема прокатного производства сортового проката:
1 – нагревательный колодец; 2 – слиток; 3 – блюминг; 4 – блюм;
5 – заготовочный стан; 6 – блюм меньшего сечения; 7, 8, 9, 10, 11 – клети сортопрокатного стана
Полученный прокат требуемого профиля разрезают на заданную длину, охлаждают, правят в холодном состоянии, обрабатывают термически и удаляют поверхностные дефекты.
На рис. 3.5 приведена схема прокатки листов.
Рис. 3.5. Схема прокатного производства листового проката:
1 – слиток; 2 – слябинг; 3 – слябы; 4 – рабочая черновая клеть;
5 – рабочая чистовая клеть
Нагретый слиток 1 массой до 50 т подается на обжимной универсальный стан – слябинг2 для прокатки в слябы3, которые имеют прямоугольное сечение размером от 90х1000 до 250х1800 мм и длиной 1,5…5,5 м. Процесс прокатки на слябинге в основном аналогичен процессу прокатки на блюминге. После 15…21 проходов металл поступает в машину огневой очистки для зачистки поверхностных дефектов, затем его транспортируют к ножницам и далее – на листовые станы. Листовые станы состоят из двух рабочих клетей – черновой 4 и листовой 5, расположенных друг за другом. По выходе из чистовой клети толщина листа достигает 4 мм, затем листы подвергают охлаждению, правке в листоправильных машинах, обрезке боковых кромок и резке на мерные длины или сматывают в рулон.
ПРОИЗВОДСТВО БЕСШОВНЫХ ТРУБ
На рис. 3.6. представлена схема производства бесшовных труб на установке с пилигримовым станом.
Рис. 3.6. Схема прокатки бесшовных труб на трубопрокатной установке с пилигримовым станом:
а – прошивной стан; б – пилигримовый стан; в – калибровочный стан;
1 – заготовка; 2 – валки; 3 – игла; 4 – рабочие валки пилигримового стана;
5 – заготовка; 6 – заготовка с оправкой; 7 – калибровочные валки
В качестве заготовок для производства бесшовных труб используют слитки, а также катанные заготовки. Процесс прокатки состоит из двух основных операций: прошивки отверстия в заготовке и прокатки прошитой заготовки. Прошивку выполняют на прошивном стане поперечно-винтовой прокатки двумя конусообразными рабочими валками 2, оси которых пересекаются под углом 6…120. В валках такого стана заготовка 1 получает одновременно вращательное и поступательное движение. При этом в заготовке возникают радиальные растягивающие напряжения, вызывающие течение металла от ее центра и периферии, в результате чего металл в центре заготовки доводится до состояния разрыхления, и заготовка сравнительно легко прошивается прошивнем (иглой) 3 с образованием трубной заготовки – гильзы, которая передается к пилигримовым станам.
Рабочие валки 4пилигримового стана вращаются в разные стороны с одинаковой скоростью. При этом направление вращения валков противоположно направлению подачи заготовки 5. Валки имеют переменный профиль, вследствие чего сечение калибра непрерывно изменяется при каждом обороте валков. При максимальном размере калибра заготовка с оправкой 6 продвигается в валки на величину подачи. После того, как валки сделают полный оборот и возвратятся в исходное положение, оправку с заготовкой поворачивают на 900 и снова подают в валки для обжатия. Этот цикл повторяется до получения трубы требуемых размеров.
В современных условиях применяется многовалковый калибровочный стан для одновременной калибровки и правки труб. Трубы после калибровки поступают на оборудование для отделки и контроля качества. На установках с пилигримовым станом получают трубы различного назначения: бурильные, насосно-компрессорные, нефте-, газо- и паропроводные из углеродистых и низколегированных сталей.
На рис 3.7. представлена схема установки с автоматическим станом.
Рис. 3.7. Схема прокатки бесшовных труб на трубопрокатной установке с автоматическим станом: а – прошивной стан; б – автомтический стан; в – обкатной стан; г – калибровочный стан; 1 – заготовка; 2 – валки; 3 – игла; 4 – труба;
5 – круглые калибры; 6 – оправка; 7 – обкатные валки; 8 - калибровочные валки
Прокатку заготовки 1, прошитой на прошивном стане, производят на неподвижной оправке в круглых калибрах 5. Толщина стенки трубы 4 зависит от просвета между калибром и оправкой 6. При получении требуемой толщины стенки наружный диаметр трубы уменьшается. Прокатку выполняют за два прохода с поворотом трубы на 900 после первого прохода. Для устранения неровностей, рисок, овальности и неравномерной толщины стенок полученную трубу обкатывают в обкатном стане и для получения заданных размеров пропускают через калибровочный стан. На этой установке получают трубы диаметром 60…426 мм с толщиной стенки 4…13 мм.
ПРОИЗВОДСТВО СВАРНЫХ ТРУБ
Сварные трубы из низколегированных и низкоуглеродистых сталей прокатывают из прокатных полос, называемых штрипсами, ширина которых равна длине окружности трубы. Процесс производства сварных труб включает в себя формовку плоской заготовки в трубу, сварку (печную, электрическую, газовую, высокочастотную и др.), правку, калибровку (рис. 3.8).
Рис. 3.8. Схема производства труб непрерывной печной сваркой:
1 – щтрипс в рулонах; 2 – тянущие ролики; 3 – нагревательная печь;
4 – формовочно-сварочный стан; 5 – клети редукционного стана;
6 – клети калибровочного стана
Для получения сварных труб заготовкой служит горячекатаныйштрипс в рулонах 1, который своим передним концом сваривается с задним концом штрипса предыдущего рулона. Подача концов штрипсов к месту сварки производится при помощи тянущих роликов листоправильной машины 2. Непрерывныйштрипс проходит через нагревательную печь тоннельного типа 3, где нагревается до температуры 1320…1400оС.
При выходе из печи штрипс обдувается сжатым воздухом, что повышает температуру кромок на 60…100оС и сбивает окалину. Непосредственно за печью устанавливается многоклетьевой формовочно-сварочный стан 4, в клетях которого штрипс сворачивается в полный круг, кромки сжимаются и свариваются. В последующих клетях происходит обжатие трубы. Для получения трубы требуемого размера и качества поверхности она прокатывается в клетях редукционного 5 и калибровочного 6 станов. Процесс осуществляется со скоростью 200 м/мин.
Область применения прокатного материала: непосредственно в конструкциях (мостах, зданиях и т.д.), в качестве заготовки для изготовления деталей в механических цехах и заготовки для последующей ковки и штамповки.
Прессование металла
Процесс прессования представляет собой выдавливание металла, помещенного в замкнутую полость контейнера, через отверстие матрицы. Этот способ пластической обработки находит широкое применение при деформировании как в горячем, так и в холодном состоянии.
Прессованием изготовляют прутки диаметром 3.. .250 мм, трубы диаметрам20...400мм при толщине стенки 1,5...12 мм, полые профили с несколькими каналами сложного сечения, с наружными и внутренними ребрами, разнообразные профили с постоянным и изменяющимся (плавно или ступенчато) сечением по длине. Профили для изготовления деталей машин, несущих конструкций и других изделий, получаемые прессованием, часто оказываются более экономичными, чем изготовляемые прокаткой, штамповкой или отливкой с последующей механической обработкой. Кроме того, прессованием получают изделия весьма сложной конфигурации, что исключается при других способах пластической обработки.
К основным преимуществам прессования металла относятся:
возможность успешной пластической обработки в том числе мало пластичных металлов и сплавов; возможность получения практически любого поперечного сечения изделия, что при обработке металла другими способами не всегда удается; получение широкого сортамента изделий на одном и том же прессовом оборудовании с заменой только матрицы; производство изделий с высокими качеством поверхности и точностью размеров поперечного сечения, что во многих случаях превышает принятую точность при пластической обработке металла другими способами (например, при прокатке). К недостаткам получения изделий прессованием следует отнести:
повышенный расход металла на единицу изделия из-за существенных потерь в виде прессостатка; появление в некоторых случаях заметной неравномерности механических идругих свойств по длине и поперечному сечению изделия; сравнительно высокую стоимость прессового инструмента.
Волочение металла
Обработка металла волочением, т. е. протягивание прутка через отверстие, выходные размеры которого меньше, чем исходное сечение прутка, находит широкое применение в металлургической, кабельной и машиностроительной промышленностях. Волочением получают проволоку с минимальным диаметром 0,002 мм, прутки диаметром до 100 мм различного сечения, трубы небольшого диаметра и с тонкой стенкой. Применяются стали разнообразного химического состава, прецизионные сплавы, а также практически все цветные металлы (золото, серебро, медь, алюминий и др.) и их сплавы. Изделия, полученные волочением, обладают высоким качеством поверхности и высокой точностью размеров поперечного сечения. Если изделию требуется придать в основном эти характеристики, то такой вид обработки называют калибровкой.
Волочение чаще всего выполняют при комнатной температуре, когда пластическую деформацию большинства металлов сопровождает наклеп. Это свойство в совокупности с термической обработкой используют для повышения некоторых механических характеристик металла. Так, например, арматурная проволока диаметром 3... 12 мм из углеродистой конструкционной стали (0,70...0,90 ХС) при производстве ее волочением обеспечивает предел прочности 1400... 1900 МПа и предел текучести 1200...1500 МПа.
Волочение выгодно отличается от механической обработки металла резанием (строганием), фрезерованием, обточкой и пр., так как при этом отсутствуют отходы металла в виде стружки, а сам процесс заметно производительнее и менее трудоемок.
Волочением можно изготовлять полые и сплошные изделия часто сложного поперечного сечения, производство которых другими способами не всегда представляется возможным (например, тонкие изделия, прутки значительной длины).
Назначение ковки и штамповки
Пластическая обработка металлов прерывистым воздействием универсального инструмента или соответствующей рабочей частью специального инструмента (штампа) для придания телу заданной формы и размеров называется в первом случае ковкой, а во втором — штамповкой.
Данными способами получают весьма разнообразные по форме и размерам изделия из металла, пластмасс и других материалов с различными степенью точности размеров, механическими и другими характеристиками и качеством поверхности. Поэтому ковочно-штамповочное производство находит широкое применение в машиностроении и приборостроении, в производстве предметов народного потребления и других отраслях народного хозяйства. Получение изделий ковкой и штамповкой позволяет максимально приблизить исходную форму заготовки к форме и размерам готовой детали и тем самым уменьшить или полностью исключить дорогостоящие операции с потерей металла в стружку. При изготовлении изделий из прокатных заготовок на машиностроительных заводах с использованием только металлорежущих станков теряется в виде стружки до 30...40% металла. Предварительная же обработка этих заготовок методами ковочно-штамповочного производства снижает отходы металла в 4..5 раз, уменьшает необходимые парк металлорежущих станков и в целом дает значительную экономию средств. Кроме того, ковка и штамповка улучшают свойства металла, вследствие чего наиболее ответственные детали многих машин и приборов часто изготовляют только из поковок.
Прогресс современного машиностроения в значительной мере определяется состоянием ковочно-штамповочного производства. Поэтому развитию этих видов обработки металла давлением уделяется серьезное внимание.
Характеристика исходных материалов и основные технологические операции
Дня процессов ковки исходными материалами являются слитки, масса которых может составлять от нескольких килограммов до 250...350 т, и прокатные заготовки. Для горячей штамповки используют кованую, прокатанную, прессованную заготовки и заготовки, получаемые волочением, а также жидкий металл. При листовой штамповке исходный материал — это горяче- и холоднокатаные листы и ленты из различных сталей, сплавов на основе алюминия, меди, никеля, титана, благородных металлов и другие материалы.
Подготовка исходного материала (слиток, прутковый или листовой металл) к ковке и штамповке включает такие операции, как сортировка, разрезка на мерные длины, удаление поверхностных дефектов, термическая обработка, если это необходимо, и др. Если деформирование выполняется в горячем состоянии, возникает необходимость нагрева металла.
Разнообразие существующих технологических операций в ковочно-штамповочном производстве требует соблюдения при выборе технологического процесса следующих основных положений:
принятый технологический процесс должен обеспечить производство изделий с определенными; точностью их геометрической формы и размеров, механическими свойствами, структурой и отсутствием поверхностных и внутренних дефектов. При проектировании технологического процесса предусматривается периодический контроль качества изделий, который должен не только выявлять, но и предупреждать появление брака.
Отделочные операции включают такие виды обработки, как обрезка облоя (заусенца) или других отходов, калибровка для повышения точности размеров и формы изделия и улучшения качества поверхности, термическая обработка, правка, очистка и травление, гальванические и лакокрасочные покрытия, оксидирование, анодирование и пр.
Ковка
С развитием металлургии бронзы и железа ковка получила очень широкое распространение. В настоящее время область применения ковки сокращается, но в ряде случаев ковка по-прежнему остается наиболее экономичным способом получения деформированных заготовок, т.е. поковок.
При ковке формоизменение происходит вследствие течения металла в стороны, перпендикулярные к движению деформирующего инструмента-бойка.
Применение ковки для получения заготовок объясняется рядом ее преимуществ по сравнению с другими видами обработки:
1) возможностью изготовления крупногабаритных поковок массой несколько сотен тонн, получение которых другими способами невозможно, причем при обработке таких поковок используется сравнительно маломощное оборудование, так как обработка ведется деформированием отдельных участков заготовки;
2) применение универсального оборудования и универсальной оснастки позволяют получать поковки широкого ассортимента;
3) в процессе ковки значительно улучшается качество металла, повышаются его механические свойства, особенно пластичность и ударная вязкость.
Основные недостатки ковки следующие: низкая производительность, значительная трудоемкость изготовления поковок, особенно на прессах; большие напуски, припуски и допускаемые отклонения размеров поковки, что приводит к увеличению объема механической обработки и расхода металла.
Ковка является рациональным и экономически выгодным процессом получения качественных заготовок с высокими механическими свойствами в условиях мелкосерийного и единичного производств. Ковкой изготавливают самые разнообразные поковки, масса которых находится в пределах от нескольких десятков граммов до сотен тонн. Наиболее ответственные детали, такие, как валы и диски турбин, роторы, коленчатые валы судовых двигателей, барабаны котлов высокого давления и т.п., к которым предъявляются высокие требования по качеству металла и механическим свойствам, изготавливают из поковок.
Ковка осуществляется при температурах горячей деформации, поэтому для такого вида обработки применяют все стали и сплавы, используемые при обработке металлов давлением. Шероховатость поверхности поковок, полученных ковкой, не превышает Rz=320-80мкм. При использовании подкладных штампов шероховатость поверхности поковок может быть доведена до Rz = 80 - 40 мкм.
Основные технологические операции ковки.
При получении изделий ковкой исходный продукт обрабатывают многократным прерывистым воздействием универсального инструмента молота или пресса. Смещаемый объем деформируемого тела по высоте свободно перемещается по контактной поверхности инструмента. Ковка находит применение при единичном и мелкосерийном производстве и выполнении ремонтных работ. Данным способом изготовляют тяжелые поковки (до 250 т и более — валы гидротурбин, цельнокованые паровые котлы и др.), поковки средней массы (50.. .400 кг— коленчатые валы крупных дизелей, маховики, диски и др.) и мелкие поковки массой до 50 кг самого разнообразного назначения.
Технологические процессы ковки представляют собой различные сочетания и последовательность основных и вспомогательных операций, таких, как биллетировка, осадка, протяжка, разгонка, прошивка, гибка, скручивание, рубка, кузнечная сварка и др., а также операции отделки и термической обработки, если это необходимо.
Ковку выполняют с применением кузнечного инструмента, который можно подразделить на основной, обеспечивающий деформирование металла (рис. 175), и вспомогательный, используемый для удержания и манипулирования поковкой в процессе обработки, — это всевозможные патроны, вилки, клещи с различной формой губок.
Рассмотрим основные операции ковки.
Биллетировка слитка представляет собой операцию обжатия ребер заготовки для придания ей формы тела вращения. При этом одновременно со снятием конусности слитка разрушается литая дендритная структура, происходит заварка пузырей и других дефектов литого металла.
Осадка - процесс уменьшения высоты заготовки с одновременным увеличением площади ее поперечного сечения. Осадку производят для устранения литой структуры, получения поковок с относительно малой высотой (для производства зубчатых колес, дисков ипр.) и как предварительную операцию перед прошивкой при изготовлении барабанов, колец и др. Для предотвращения продольного изгиба при осадке высоту заготовки принимают не более 2/5 ее диаметра. Этот процесс выполняют между плоскими или вогнутыми (вырезными) бойками. Высадка — это осадка части заготовки. При этом происходит увеличение площади поперечного сечения части заготовки с одновременным уменьшением ее продольных размеров. Эта операция может производиться различным образом, например, осаживанием заготовки, имеющей местный нагрев, или ограничением деформирования на определенном участке заготовки с помощью колец.
Протяжка — это удлинение заготовки или ее части за счет уменьшения площади поперечного сечения. Протяжку и ее разнообразные варианты используют при производстве гладких, ступенчатых, коленчатых валов и других изделии; она занимает до 70% всего времени обработки. Протяжку выполняют последовательной подачей и обжатием заготовки при ее повороте вокруг своей оси на определенном этапе обработки.
Разгонка используется для увеличения ширины части заготовки за счет уменьшения ее толщины. Разгонку чаще всего выполняют подкладным инструментом (круглым, овальным, плоским).
Прошивка представляет собой операцию получения полостей в заготовке за счет вытеснения металла. Она может выполняться сплошным прошивнем на монетах или прессах, при этом прошиваемая поковка поворачивается на 180*. При сравнительно низкой высоте заготовки прошивку выполняют на подкладных кольцах. При получении отверстии значительного диаметра (более 400 мм) прошивни делают полыми, что уменьшает усилие прошивки. Придание точных размеров отверстию по диаметру производят продавливанием калибра. Прошитая заготовка в дальнейшем может подвергаться обработке (раскатке).
Раскатка — операция, заключающаяся в увеличении диаметра кольцевой заготовки при вращении за счет уменьшения ее толщины с помощью бойка, оправки или роликов. Раскатка используется при изготовлении поковок, имеющих незначительную толщину стенки по сравнению с диаметром отверстия (кольца, бандажи, венцы, различные обечайки). Операция раскатки аналогична протяжке заготовки, концы которой соединены между собой.
Гибка — образование или изменение углов между частями заготовки или придание eй криволинейной формы. Гибку чаще всего выполняют между подкладными опорами. При операции гибки имеется тенденция к образованию складки по внутреннему контуру заготовки и трещины — по наружному.
Закручивание — поворот части заготовки вокруг продольной оси. Эту операцию применяют при производстве поковок некоторых типов коленчатых валов, крупных спиральных сверл и др. Закручивание выполняют вручную или с помощью крана, дня чего используют воротки, вилки и другой инструмент.
Отрубка — полное отделение части заготовки по незамкнутому контуру путем внедрения в заготовку деформирующего инструмента. При этом если от заготовки отделяют часть металла по незамкнутому (наружному) контуру, то такую операцию называют разрубкой, а по замкнутому (внутреннему) контуру — вырубкой. Почти каждый технологический процесс ковки включает операцию отрубки, которая выполняется топорами различной формы — двусторонними, односторонними, угловыми и др. Разрубку и вырубку можно выполнять и в специальных штампах.
Передача металла — смещение одной части заготовки относительно другой при сохранении параллельности осей или плоскостей частей заготовки. Подобные операции применяют при ковке коленчатых валов. Заготовка деформируется на ограниченном участке, когда возникает необходимость выполнить ось заготовки ступенчатой.
Помимо рассмотренных при ковке имеют место и другие операции:
кузнечная сварка, которая утрачивает свое значение в связи с развитием электро- и газосварки, растяжка (местное уменьшение площади поперечного сечения заготовки путем растяжения), прожимка (местное уменьшение площади поперечного сечения заготовки путем обжатия), обкатка (придание заготовке формы тела вращения путем повторных ударов или нажатий), подкатка (обкатка части заготовки), засечка (выделение части объема заготовки путем нанесения углубления по ее границам), проглаживание (устранение неровностей поверхности заготовки путем пластического деформирования) и др.
Ковку выполняют на молотах и прессах. Первые представляют собой машины динамического воздействия на обрабатываемую заготовку, вторые — статического.
Молоты чаще всего характеризуются массой падающих частей. При этом в одних молотах деформирование металла обеспечивается только действием массы свободно падающих частей (молоты простого действия), в других молотах происходит принудительное ускорение падающих частей (молоты двойного действия).
Дня ковки наибольшее распространение получили паровоздушные и пневматические молоты двойного действия.
Ковку слитков более 2...3 т производят на гидравлических прессах с усилием прессования от 5 до 150 МПа и более. Гидравлические прессы деформируют поковку не ударным воздействием, а постепенным продвижением инструмента. При этом в процессе рабочего хода бойков непрерывно подводится энергия, для чего используется вода или масло под высоким давлением. Гидравлические прессы в зависимости от направления перемещения инструмента бывают вертикальными или горизонтальными.
При работе пресса давление жидкости чаще всего создается с помощью плунжерных насосов.
Наряду с применением гидравлических прессов с нагнетательным насосом получили распространение прессы с мультипликатором. Специальный аппарат — мультипликатор — позволяет повышать давление в рабочей сети до 40...60 МПа.
Горячая объемная штамповка
Этот способ наиболее широко распространен для получения качественных заготовок. Горячей объемной штамповкой получают заготовки для ответственных деталей автомобилей, тракторов, сельскохозяйственных машин, железнодорожных вагонов, самолетов, металлообрабатывающих станков, швейных машин и т.д.
Этот способ штамповки наиболее эффективен при массовом, крупносерийном и серийном производствах деталей массой от нескольких граммов до нескольких тонн. Наиболее целесообразно изготовление штамповкой поковок массой не более 50 —100 кг.
По сравнению с ковкой горячая объемная штамповка имеет следующие преимущества:
-поковки, изготавливаемые штамповкой, имеют более сложную форму и лучшее качество поверхности; шероховатость поверхности Rа = 20 – 6,3 мкм, а при применении холодной калибровки Rа = 3,2 -1,6 мкм;
-поковки можно получать со значительно меньшими допусками, чем при ковке, а при точной штамповке допуски можно довести до долей миллиметра и. подвести под классы точности, получаемые при обработке резанием; припуски снижаются в два-три раза (как правило, механической обработке подвергаются только сопрягаемые поверхности);
-значительно повышается производительность труда (десятки и сотни поковок в час).
К недостаткам горячей объемной штамповки относятся:
-ограничения по массе получаемых поковок;
-дополнительный отход металла в заусенец, масса которого составляет от 10 до 30 % от массы поковки;
-для горячей объемной штамповки требуются большие усилия деформирования, чем для ковки;
-инструмент (штамп) является более сложным и дорогим, чем универсальный инструмент для ковки.
Горячая объемная штамповка подразделяется на различные виды в зависимости от типов штампа, оборудования исходной заготовки, способа установки заготовки в штампе и т.п.
Штамповку выполняют с использованием специального инструмента — штампа, который состоит из двух частей или более. Полости штампа называются ручьями. Заготовка, деформируясь в ручьях, заполняет полости и принимает форму поковки. Течение металла при штамповке принудительно ограничивается поверхностями инструмента, что вызывает перераспределение объема заготовки.
Распространение штамповки связывают с развитием машиностроения, особенно автомобильной промышленности, когда возникла необходимость организации массового производства однотипных поковок. Хотя штамповый инструмент отличается высокой стоимостью и чаще всего используется для узкоспециализированных целей, а деформирование металла при этом требует значительно большей мощности по сравнению с ковкой, штамповка при массовом производстве однотипных поковок имеет ряд существенных преимуществ. Помимо высокой производительности штамповка обеспечивает получение поковок с высокой точностью размеров, что уменьшает расход металла на изготовление детали и снижает трудоемкость при последующей обработке металла резанием. Кроме того, штамповка обеспечивает получение высокого качества поверхности поковок, при этом исключается необходимость последующей обработки резанием всей поковки — обрабатывается лишь та ее часть, которая будет соприкасаться с другими деталями. Последующие за горячей штамповкой отделочные операции, например калибровка в холодном состоянии, повышают качество поверхности поковок, а допуски размеров при этом снижаются до ±0,1, а иногда до ±0,05 мм. Поэтому все повышенные расходы на штамповку и изготовление инструмента окупаются экономней металла ирасходами на механическую обработку поковок.
Вместе с тем следует отметить, что штамповка обеспечивает получение изделий сложной формы, во многих случаях невыполнимых ковкой без напусков.
Исходным материалом для горячей штамповки являются сортовой прокат, прессованные прутки, калиброванный металл, литая заготовка и жидкий металл. В крупносерийном производстве деталей находят большое применение заготовки из проката периодического профиля, что обеспечивает в процессе штамповки сокращение подготовительных операций. Исходный материал в заготовительном отделении цеха разрезают на мерные длины. Эту операцию выполняют на хладноломах, кривошипных прессах, механических пилах или производят газовой и электрической резкой. Перед штамповкой заготовки нагревают до температур, определяемых условиями деформирования.
Технологический процесс горячей штамповки отличается значительным разнообразием и определяется видом самого изделия и применяемым оборудованием. Штамповку производят на молотах, прессах, горизонтально-ковочных машинах, гибкой на бульдозерах, вальцовкой и такими способами, как раскатка, ротационная ковка и пр.
Горячую штамповку выполняют двумя методами: облойным (с заусенцем) в открытых штампах и беэоблойкым (при отсутствии заусенца) в закрытых штампах. По типу штампа она бывает: открытая, закрытая.
А) штамповка в открытых штампах.
Сущность облойного метода заключается в том, что поковка по месту разъема штампа вследствие избытка металла получается с заусенцем (облоем). Наличие облоя способствует хорошему заполнению полостей штампа, ибо сам заусенец начинает образовываться раньше заполнения ручьев. При последующем смыкании штампа сопротивление металла истечению в зазор с образованием обпоя резко увеличивается. Это создает подпор по контуру изделия, который способствует заполнению углов штампа, т. е. облой выполняет определенную технологическую функцию.
Штамп в процессе деформирования остается открытым. Зазор между подвижной и неподвижной частями штампа переменный, в него затекает (выдавливается) металл при деформировании, образуя заусенец, т.е. технологический припуск размеры которого зависят от размеров поковки. Назначение заусенца – компенсация колебаний исходных заготовок по массе. На наличие заусенца увеличивает расход металла и для обрезки заусенцев необходимы специальные приспособления.
При безоблойном методе заготовку помещают в полости одной части штампа (в матрице) и процесс деформирования выполняют другой частью (пуансоном). При этом облой в изделии не предусматривается. Незначительный заусенец, который может иметь место по плоскости разъема, не оказывает влияния на процесс штамповки и является результатом неточности размеров заготовки. Для облегчения свободного удаления поковки из штампа его стенки изготовляют с уклоном или применяют выталкиватели. Пониженный расход металла при штамповке данным способом является существенным преимуществом, однако формы поковок при этом менее разнообразны, чем при изготовлении в открытых штампах с облоем.
Уместно отметить, что штамповки выдавливанием и прошивкой (закрытая прошивка) являются разновидностями процесса штамповки в закрытых штампах.
Штамп в процессе деформирования остается закрытым. Зазор между подвижной и неподвижной частями штампа остается постоянным и незначительным по размеру. Он только предохраняет штамп от заклинивания. Отсутствие заусенца сокращает расход металла, вызывает необходимость использовать точные заготовки из калиброванного проката или предварительно механически обработанные
Как при открытой, так и при закрытой штамповках обработка заготовки может выполняться в одном или нескольких ручьях В условиях многоручьевой штамповки заготовка постепенно изменяется при переходе от одного ручья к другому и в чистовом ручье ей придается окончательная форма и размеры. В зависимости от вида поковки, программы производства, имеющегося оборудования ручьи при многоручьевой штамповке могут размещаться в одном общем или нескольких штампах, установленных на однотипных или разнотипных ковочных машинах.
Наибольшее распространение получила штамповка на молотах (паровоздушных, фрикционных, бесшаботных), прессах (кривошипных, винтовых гидравлических) и горизонтально-ковочных машинах
Штамповка на молотах.
Широкое использование молотов при штамповке поковок массой до1000 кг определяется рядом достоинств этого вида оборудования и методов обработки. При штамповке на молотах можно быстро и многократно деформировать заготовку в каждом ручье, осуществлять чрезвычайно энергоемкие операции и большие суммарные деформации. По этим причинам парк штамповочных молотов занимает ведущее положение. Номинальное усилие молотов от 0,6 до 25 тонн. Применяют паровоздушные, фрикционные и гидравлические молоты.
Хотя КПД фрикционных молотов выше паровоздушных, все же они получили меньшее распространение, так как производительность их более низкая из-за пониженного числа ударов в минуту. Кроме того, при работе на таких молотах затруднена возможность регулирования энергии удара, что особенно важно при обработке изделий сложной формы в заготовительных ручьях, где обычно требуется меньшая сила удара.
По принципу действия инструмента на деформируемую заготовку в процессе пластической обработки к молотам близки винтовые (фрикционные) прессы. Здесь сочетается ударное действие и статическое давление. При этом также, как и на молотах, можно деформировать металл в каждом ручье штампа за несколько ударов. Винтовые прессы являются машинами-орудиями, в которых энергия привода преобразуется в полезную работу посредством винтового механизма, т. е. деформирование металла осуществляется кинетической энергией вращательного движения винта с маховиком или без маховика и поступательного движения ползуна с верхним штампом. Штампуют мелкие поковки массой до 20 кг из алюминиевых и медных сплавов типа колпачков, стаканчиков, винты, болты и т.д., шестерни с точным профилем зуба. Ra до 6,3мкм.
При штамповке на молотах используют не только открытые, но и закрытые штампы.
В условиях мелкосерийного производства поковок для уменьшения от ходов металла и повышения точности получаемых изделий применяют подкладные штампы, которые представляют собой инструмент с полостью поковки или отдельного участка поковки.
Штамповка на прессах
Для горячей штамповки помимо молотов широко применяют кривошипные и гидравлические прессы. Штамповка на кривошипных прессах получила значительное распространение лишь к середине XX в. я в результате заметного экономического эффекта во многих случаях вытесняет штамповку на молотах.
Преимущества штамповки на механических прессах:
-Высокая точность поковок (допуски 0,2 – 0,5 мм)
-Экономия металла,
Производительность механических прессов на 30....50% выше производительности молотов, так как изделие выполняется: за один ход ползуна, при этом упрощается возможность применения автоматизации, улучшаются условия труда рабочих.
Горячую штамповку на кривошипных прессах выполняют в открытых (с образованием облоя в полости разъема) и закрытых штампах. Вместе с этим на механических прессах выполняют штамповку выдавливанием, штамповку прошивкой и различные комбинированные операции. Процесс выдавливания применяют в тех случаях, когда необходимо получать поковки, имеющие длинные отростки и, следовательно, значительную разницу поперечных сечении. Этот процесс аналогичен прессованию металла.
Штамповка прошивкой представляет собой процесс вдавливания пуансона в заготовку круглого, квадратного или другого сечения.
Штамповка на гидравлических прессах получила распространение при производстве различных рычагов, зубчатых колес, полых корпусов, коленчатых валов, сферических днищ сосудов, лопастей самолетных винтов и других изделии из прокатной сортовой и листовой заготовок и из кованых заготовок с массой в несколько сотен килограммов и более (до5т). Штамповку на гидравлических прессах выполняют в открытых и закрытых штампах. Эта штамповка значительно тихоходнее и дороже штамповки на молотах. Обычно применяется, если нельзя применить молоты, т.е. наиболее крупные детали. Точность размеров до 12 квалитета.
По окончании горячей штамповки возникает необходимость применения ряда отделочных операции. К ним в первую очередь относится удаление облоя и заусенца, что выполняют в обрезных штампах, обычно устанавливаемых на кривошипных прессах, в холодном состоянии (облой поковок, получаемых на молотах с массой падающих частей выше 1...1.5 т, удаляют в горячем состоянии). После удаления облоя в некоторых случаях требуется правка поковок, которая может быть выполнена в специальном правочном или чистовом ручье. Правку мелких изделии производят в холодном состоянии, крупных — в горячем.
К отделочным операциям относят также и калибровку, которая придает поковке точные размеры и форму и повышает качество поверхности. Калибровку выполняют как в горячем, так и в холодном состоянии. Кроме того, для улучшения качества поверхности изделии и удаления окалины применяют дополнительную обработку: травление, пескоструйную и дробеструйную очистку и обработку. Большое внимание уделяется термической обработке поковок (замедленное охлаждение, нормализация, отжиг и др.).
Дата добавления: 2018-05-12; просмотров: 2241; Мы поможем в написании вашей работы! |
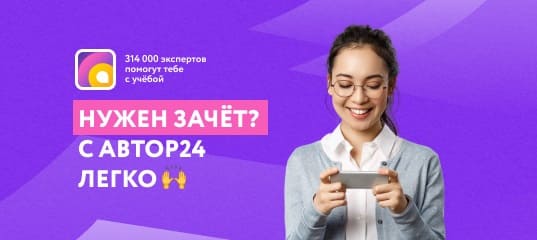
Мы поможем в написании ваших работ!