Расчет основных параметров режима ручной электродуговой
Л а б о р а т о р н а я р а б о т а № 3
Определение параметров режима ручной
Электродуговой сварки
Цель работы:
1. Изучить типы сварных соединений и швов.
2. Освоить расчет основных параметров режима ручной дуговой сварки стыкового соединения.
3. Научиться правильно выбирать необходимое оборудование и материалы.
Классификация сварных соединений и швов
Сварным соединением, как конструктивным элементом, называют участок конструкции, в котором отдельные ее элементы соединены с помощью сварки. В сварное соединение входят: сварной шов, прилегающие к нему зоны термического влияния и участки основного металла. Сварной шов представляет собой закристаллизовавшийся металл, который в процессе сварки находился в расплавленном состоянии.
При изготовлении сварных конструкций применяют различные типы сварных соединений. Наиболее распространенными из них являются: стыковые (а), внахлестку (б), тавровые (в), угловые (г) и торцовые (д) (рис. 17).
На практике широкое применение получили стыковые соединения. Они являются наиболее прочными, экономически выгодными и имеют следующие преимущества перед остальными:
1. Неограниченная толщина свариваемых элементов.
2. Более равномерное распределение напряжений при передаче усилия от одного элемента к другому.
3. Минимальный расход металла на образование сварного соединения.
4. Надежность и удобство контроля качества соединения рентгеновскими лучами.
|
|
а б
|
|
|
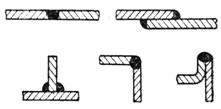
Рис. 17. Типы сварных соединений
Чтобы при сварке обеспечить полное проплавление основного металла и хорошее качество шва, необходимо подготовить кромки свариваемых заготовок. Подготовка кромок заключается: во-первых, в очистке места сварки от окисных пленок, ржавчины, жира и прочих загрязнений, и вовторых, в скосе кромок, величины притупления и зазора между кромками. Раскрытие кромок и зазор необходимы для обеспечения провара всего сечения (без разделки кромок при нормальных режимах ручной сварки можно обеспечить провар до 3–4 мм), а притупление предотвращает прожог.
Конструктивные элементы подготовки кромок и выполненных швов при ручной дуговой сварке углеродистых и низколегированных сталей регламентируются стандартом ГОСТ5264 – 80.
Вид подготовки кромок зависит от толщины свариваемых деталей (S), способа сварки, а также технологических и конструктивных особенностей свариваемого изделия. Наиболее распространенные виды подготовки кромок при ручной дуговой сварке для стыкового соединения следующие:
|
|
1. С отбортовкой кромок при S = до 3 мм.
2. Без подготовки кромок: при односторонней сварке S = 1–6 мм, при двусторонней сварке S = 3 – 8 мм.
3. С V-образной подготовкой со скосом одной или двух кромок S = 3 – 26 мм.
4. С U-образной подготовкой или с криволинейным скосом одной кромки S = 20 – 60 мм.
5. С K-образной подготовкой S = 12 – 40 мм.
6. С X-образной подготовкой S =12 – 60 мм.
7. С двойной U-образной разделкой S = 30 – 100 мм.
Ручная сварка позволяет выполнить швы в различных пространственных положениях. Условно их разделяют на нижние (а), вертикальные (б), горизонтальные (в) и потолочные (г) (рис. 18). Горизонтальные швы – это швы, выполняемые на вертикальной плоскости в горизонтальном положении.
а б в г
Рис. 18. Расположение швов в пространстве
Расчет основных параметров режима ручной электродуговой
Сварки стыкового соединения
Режимом сварки называют совокупность основных контролируемых параметров, определяющих условия сварки. При ручной электродуговой сварке такими параметрами являются: диаметр электрода (dэ), сила сварочного тока (Iсв), напряжение на дуге, скорость перемещения электрода вдоль шва (V), род тока, полярность и др.
|
|
Диаметр электрода выбирается в зависимости от толщины свариваемого изделия, и рекомендуются следующие соотношения между ними:
Толщина свариваемого изделия s, мм | 1−2 | 3 | 4−8 | 9−12 | 13−15 | 16−20 |
Диаметр электрода dэ, мм | 1,5−2,0 | 3 | 4 | 4,0−5,0 | 5 | 5−6 |
При сварке толстостенных материалов, где толщина металла 10–12 мм и более, сварку осуществляют многослойными швами. При этом сварку всех проходов стремятся выполнять на одних и тех же режимах, кроме первого. Первый проход выполняется электродами диаметром 3–4 мм, так как применение электродов большого диаметра не позволяет в необходимой степени проникнуть в глубину разделки для провара корня шва.
Общее число проходов при многослойной сварке можно определить по формуле
, (1)
где F1, Fn, Fш – площади поперечных сечений сварного шва первого, каждого последующего и общая соответственно, мм2.
Для нахождения площади поперечного сечения общего сварного шва Fш, его разбивают на элементарные геометрические фигуры и определяют сумму этих площадей. Например, площадь поперечного сечения стыковочного шва с V-образной разделкой (рис. 19) определяется как сумма площадей геометрических фигур:
|
|
Fш= S1+S2+2S3, (2)
где S1 – площадь сегмента, которую упрощенно можно считать по формуле
S1 = 0,75eq, (3)
S2 – площадь прямоугольника:
S2 = sb, (4)
S3 – площадь прямоугольного треугольника, ее определяют по формуле
S3 = hх/2,
где х = htgα, тогда
S3 = h2tgα/2, (5)
но рассматриваемая нами площадь V-образного шва состоит из двух прямоугольных треугольников, поэтому
2S3 = h2tgα.
Подставляя значение элементарных площадей в формулу (1), получим
Fш =0,75eq+ sb+ h2tgα. (6)
По указанной методике могут быть рассчитаны площади сечения любого шва. В табл. 5 приведены формулы определения площадей некоторых геометрических фигур.
Рис. 19. Геометрические элементы площади сечения стыкового шва
Площадь поперечного сечения первого прохода шва может быть определена по формуле
,
при этом F1 не должно превышать 30−35 мм2.
Площадь сечения каждого из последующих проходов шва находят по формуле
.
Величина сварочного тока зависит от толщины свариваемого металла, типа соединения, скорости сварки, положения шва в пространстве, вида покрытия электрода и т.д. Практически величина сварочного тока Iсв определяется в соответствии с выбранным диаметром электрода по эмпирической формуле:
Iсв = Kdэ,
где K – опытный коэффициент, значение которого равно 40–60, А/мм.
Величина коэффициента К зависит от диаметра электрода, и рекомендуется следующее соотношение между ними:
dэ, мм | 1–2 | 3–4 | 5–6 |
K, А/мм | 25–30 | 30–45 | 45–60 |
Если толщина металла менее 1,5dэ при сварке в нижнем положении, то Iсв уменьшают на 10–15% по сравнению с расчетным. Если толщина металла более 3dэ, то Iсв увеличивают на 10–15% по сравнению с расчетным.
Если сварной шов многопроходный, то расчет параметров сварки осуществляется для первого и последующих проходов отдельно. Например, сила сварочного тока при многопроходной сварке определяется следующим образом:
для первого прохода
Iсв.1 = Kdэ.1;
для последующих проходов,
Iсв.п = Kdэ.п.
где Iсв.1,·dэ.1и Iсв.п·dэ.п. – сила сварочного тока и диаметр электрода для первого и каждого последующих проходов, соответственно.
Длина дуги оказывает существенное влияние на качество шва; чем короче дуга, тем выше качество наплавленного металла. Длину дуги, мм, определяют по формуле:
lд = 0,5(dэ+2).
Падение напряжения на дуге зависит только от длины дуги и определяется по формуле:
UД = Uа.к.+Ul.l,
где Uа.к – сумма падения напряжения в прикатодной и прианодной области (Uа.к =10 − 18 В); U1 – падение напряжения на 1 мм длины столба дуги (Ul = 2,0 − 2,5 В/мм) – длина столба дуги, мм.
Масса наплавленного металла Gн, г, определяется по формуле
Gн= LFшρ,
где L – длина шва, см; Fш– площадь поперечного сечения шва, см2; – плотность наплавленного металла, г/см3 (для стали ρ = 7,8 г/см3).
Масса электродного металла, наплавленная на заготовку, меньше чем масса расплавленного металла электрода. Поэтому расход электродов Gэ подчитывается с учетом потерь от массы стержня электрода на огарки, угар, разбрызгивание и шлакообразование. В среднем коэффициент потерь ψ для качественных электродов равен 0,33 – 0,60, для стабилизирующих – 0,17 – 0,31. Расход электродов определяется по формуле
Gэ = Gн(1 + ψ).
Основное время горения дуги, ч, можно определить по формуле
,
где Gн – масса наплавленного металла, г; αн – коэффициент наплавки. У электродов для сварки конструкции из углеродистых и низколегированных сталей αн изменяется в пределах от 8 до 14 г/А·ч (см. табл. 3).
Полное время, ч, определяется по следующей формуле:
,
где K – коэффициент загрузки сварщика, равный 0,4–0,8 в зависимости от вида производства и характеристики выполняемых работ.
Скорость сварки, м/ч, можно определить по формуле:
,
где L – длина шва, мм.
Производительность процесса сварки, г/ч, зависит от сварочного тока и коэффициента наплавки применяемого электрода.
.
Расход электроэнергии W, кВт·ч, на производство сварочных работ можно определить по формуле
,
где η – КПД источника питания дуги при нагрузках, близких к номинальным; Рх – мощность, потребляемая источником сварочного тока, при холостом ходе (для сварочного трансформатора Рх = 0,2–0,4 кВт, для сварочного агрегата Рх = 2–3 кВт).
Расход электроэнергии составляет в среднем на 1 кг наплавленного металла на переменном токе 3,5–4,5 кВт·ч, на постоянном токе − 7–8 кВт·ч.
Дата добавления: 2018-05-12; просмотров: 308; Мы поможем в написании вашей работы! |
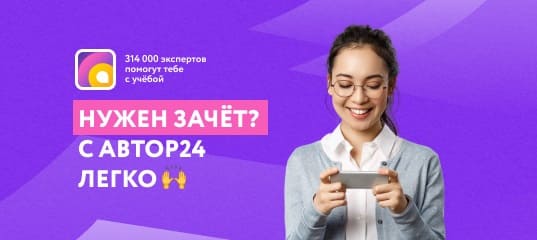
Мы поможем в написании ваших работ!