Цветная капиллярная дефектоскопия
Капиллярный метод контроля проникающими веществами позволяет выявлять внутренние дефекты, выходящие на поверхность. Он заключается в том, что на поверхность изделия наносят индикаторную жидкость-пенетрант, который имеет характерный цветовой фон. Проводится согласно ОСТ.95955-82.
После очистки поверхности от пенетранта наносят проявитель, который вытягивает его из полости дефекта. На поверхности изделия появляется рисунок шириной 0,05-0,3 мм, который виден невооруженным глазом или при помощи лупы с небольшим увеличением.
Для контроля используем цветную дефектоскопию, при которой проникающая жидкость (пенетрант) образует на белом фоне проявителя красный индикаторный рисунок. Красный цвет вследствие особенностей восприятия глазом человека обеспечивает большую вероятность обнаружения индикаторных рисунков, имеет высокую контрастность и легко позволяет отличить микротрещины от рисок и заусенец.
Перед капиллярным контролем необходимо удалить с поверхности изделия лакокрасочные, силикатные и др. покрытия, так как их дефекты могут нести ложную информацию о дефектах сварного соединения. Также обязательно удаляются окисные пленки и жидкие загрязнения, которые заполняют полость дефекта и оказывают разбавляющее действие на индикаторную жидкость, что может изменить и ее свойства.
Технология капиллярной дефектоскопии.
1. Подготовка детали к контролю.
|
|
Сводится к промывке детали. Промывку осуществляют водой. Водой удаляют остатки моющих водных средств, механические нерастворимые загрязнения.
Деталь промывают по несколько раз горячей и холодной водой, затем ее высушивают.
2. Заполнение полости дефектов пенетрантом.
Осуществляют капиллярным способом. Пенетрант наносят на контролируемую поверхность и выдерживают в течение определенного времени. Время проникновения зависит от характера дефекта (сквозной или тупиковый).
Для ускорения процесса пропитки деталь могут подогревать При подогреве уменьшается вязкость и поверхностное натяжение жидкости, улучшается смачиваемость.
3. Удаление пенетранта с поверхности изделия.
Осуществляется промывкой водой или очищающей жидкостью и последующей протиркой или сушкой.
4. Нанесение проявителя.
Оптимальная толщина слоя проявителя составляет 1-15 мм.
Используем механическое распыление проявителя, которое производится струей воздуха или инертного газа. Этот метод обеспечивает высокую чувствительность за счет равномерного слоя проявителя, но связан с большими потерями проявителя до 30-40%.
5. Проявление дефектов.
Осуществляется самым рациональным - тепловым методом. Изделие обдувают струей теплого воздуха с температурой 70-80°С.
|
|
6. Осмотр изделия и анализ индикаторных следов дефектов.
Осмотр изделия производят в 3 этапа:
Визуальный осмотр изделия для оценки качества нанесения проявителя;
Общий осмотр поверхности изделия для обнаружения рисунка дефекта;
Анализ индикаторных рисунков выявляемых дефектов.
Убедившись, что проявитель нанесен качественно, производят общий осмотр поверхности изделия невооруженным глазом или с помощью лупы двукратного увеличения. Эта операция выполняется через 3-5 мин после нанесения проявителя, а через 20-25 мин проявляются следы мелких дефектов и ведется анализ индикаторных рисунков в полной мере.
Полный осмотр предполагает изучение месторасположения рисунка, цвет, яркость, направление рисунка. Необходимо отличать истинные дефекты отложных.
7. Удаление дефектоскопических материалов.
Осуществляется протиркой ветошью с применением воды.
Пенетрант: керосин - 80%, масло трансформаторное -15%, скипидар - 5%, краситель 5С - 10г/л. Очищающая жидкость: ОЖ-3.
Проявитель: каолин 600-700 г на 1 л воды.
Метод проявления - суспензионный.
Класс чувствительности - II.
Цветная капиллярная дефектоскопия применяется в местах удаления временных креплений. При оптимальных условиях с помощью материалов для цветной капиллярной дефектоскопии можно выявлять трещины глубиной 0,01-0,03 мм и более, раскрытием 0,001-0,002 мм и более, протяженностью 0,1-0,3 мм и более. Капиллярные методы предназначены для обнаружения поверхностных и сквозных дефектов в объектах контроля, определения их расположения, протяженности (для протяженных дефектов типа трещин) и ориентации по поверхности. Минимальный размер дефектов -1-10 мкм.
Дата добавления: 2018-05-12; просмотров: 299; Мы поможем в написании вашей работы! |
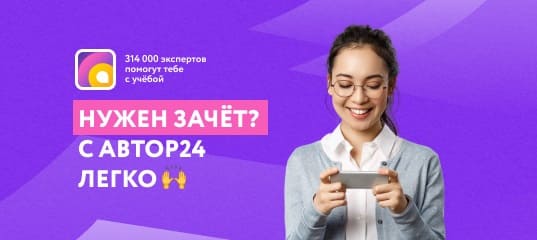
Мы поможем в написании ваших работ!