Общие направления по улучшению условий труда в цехе.
ЛИПЕЦКИЙ ГОСУДАРСТВЕННЫЙ ТЕХНИЧЕСКИЙ УНИВЕРСИТЕТ
Институт машиностроения
Кафедра оборудования и процессов машиностроительных производств
направление: 150400.62 «Металлургия»
программа академическогобакалавриата
профиль: «Технология литейных процессов
ВЫПУСКНАЯ КВАЛИФИКАЦИОННАЯРАБОТА БАКАЛАВРА
Проект чугунолитейного цеха мощностью 30000 тонн годного литья
по номенклатуре ООО «Новолит» с разработкой технологии производства
отливки «Корпус АКШ».
Студент гр. ЛП-12-1_______________________________(Щукин А.М.)
Руководитель проекта______________________________(Суслов А.А.)
Нормоконтроль___________________________________(Суслов А.А.)
Рецензент _____________________________________(Ильин И.А.)
Работа рассмотрена и допущена к защите
«______»_____________2016 г.
Заведующий кафедрой ______________ П.И.Золотухин
Липецк
2016
ЛИПЕЦКИЙ ГОСУДАРСТВЕННЫЙ ТЕХНИЧЕСКИЙ УНИВЕРСИТЕТ
ИНСТИТУТ МАШИНОСТРОЕНИЯ
Кафедра ОПМП
Зав. кафедрой, доцент, к.т.н.
______________П.И.Золотухин
«______»______________2016 г.
ДИПЛОМНОЕ ЗАДАНИЕ
Студенту группы ЛП – 12 - 1 Щукину Алексею Михайловичу
1.Тема: Проект чугунолитейного цеха мощностью 30000 тонн годного литья по номенклатуре ООО «Новолит» с разработкой технологии производства отливки «Корпус АКШ».
2.Исходные данные: Производственная программа и спецификация отливок базового цеха; чертежи и технологическая карта отливки-представителя; материалы, собранные во время преддипломной практики; строительные чертежи; государственные стандарты; требования безопасности; санитарные правила и нормы; научно-техническая, справочная и учебно-методическая литература в области литейного производства и смежных областей металлургии.
|
|
3.Содержание расчетно-пояснительной записки:
Аннотация, оглавление, введение, цель работы.
Расчет производственной программы цеха, выбор и обоснование режима работы проектируемого цеха. Расчет шихты и баланса металла плавильного отделения, обоснование выбора и расчет требуемого количества плавильного и прочего основного и вспомогательного технологического оборудования.Архитектурно-планировочное решение по зданию и сооружениям цеха. Разработка технологического процесса получения отливки-представителя.
Специальная часть: подготовка карьерного пескадля использования в качествеформовочного
Технико-экономическая часть: расчет стоимости тонны металлозавалки, тонны годного литья.
Разработка мероприятий по обеспечению безопасности жизнедеятельности и соблюдению санитарных правил и норм в проектируемом цехе.
Заключение.
4.Перечень графического материала в виде чертежей и плакатов: План и разрез цеха; схема грузопотоков; единица основного производственного оборудования; отливка-представитель; модельная плита в сборе, форма в разрезе; специальная часть.
|
|
5.Срок сдачи проекта руководителю: «20» июня 2016 г.
6.Дата выдачи задания: «22» февраля 2016 г.
7.Руководитель проекта: доцент, к.т.н. ___________________ Суслов А.А.
8.Задание принял к исполнению студент _________________ Щукин А.М..
АННОТАЦИЯ
С. 80, рис. 6, табл23, библиогр. 14 назв., прил. 5.
Разработан проект чугунолитейного цеха мощностью 30000 тонн в год чугунного литья. В проекте разработано архитектурно-планировочное решение цеха, дан расчет основного технологического оборудования. Разработан процесс изготовления типовой отливки«Корпус АКШ». Выявлены опасные и вредные производственные факторы, исходящие от применяемого технологического оборудования и представлены методы их снижения.Для плавки металла предложены современные электрические индукционные печи ИЧТ-6/2,5. Произведен технико-экономический расчет капитальных затрат и амортизационных отчислений, фондов заработной платы, себестоимости одной тонны годных отливок.
В специальной части проекта рассмотрена технология и оборудование для подготовки карьерного песка для использования в качестве формовочного.
|
|
ГРАФИЧЕСКАЯ ЧАСТЬ
План цеха....................................................................................А1
Разрез цеха..................................................................................А1
Схема грузопотоков цеха...........................................................А1
Типовая отливка.........................................................................А1
Модельная оснастка....................................................................А1
Форма в сборе.............................................................................А1
Специальная часть .....................................................................А1
Индукционная печь ИЧТ-6/2,5...................................................А1
_____________________________________________________
Итого 8 листов плакатов и чертежей формата А1.
Оглавление
Введение. 6
1 Исходные данные для проектирования. 8
1.1 Подетальная программа выпуска отливок. 8
2. Режим работы и фонды времени. 10
3. Проектирование плавильного отделения. 11
3.1 Программа отделения. 12
3.2 Выбор плавильного оборудования. 13
3.3 Расчет шихты, материальный баланс плавки. 15
3.4 Система набора и взвешивания шихты, вспомогательные участки. 20
3.5 Планировка плавильного отделения. 21
4 Проектирование формовочно–заливочно-выбивного отделения. 22
4.1 Программа формовочного отделения. 22
|
|
4.2 Выбор и расчет количества формовочного оборудования. 28
4.3 Схема работы формовочного отделения. 32
5 Проектирование стержневого отделения. 33
5.1 Выбор стержневой смеси. 33
5.2 Расчет оборудования для изготовления стержней. 36
5.3 Схема работы стержневого отделения. 38
6 Проектирование смесеприготовительного отделения. 40
6.1 Выбор и расчет оборудования. 41
6.2 Схема работы смесеприготовительного отделения. 43
7 Проектирование термообрубного отделения. 44
7.1 Распределение отливок по операциям.. 44
7.2 Выбор и расчет оборудования. 44
7.3 Планировка и схема работы термообрубного отделения. 46
8 Проектирование складов формовочных и шихтовых материалов. 47
9 Проектирование вспомогательных отделений цеха. 47
9.1 Ремонтно – механическое отделение. 47
9.2 Экспресс – лаборатории. 48
9.3 Цеховые кладовые. 49
9.4 Комнатыы мастеров. 49
10. Объемно – планировочное решение здания цеха. 49
11 Безопасность жизнедеятельности. 51
11.1 Анализ условий труда на проектируемом объекте. 51
11.2 Мероприятия по обеспечению безопасности труда. 53
11.2.1 Общие направления по улучшению условий труда в цехе. 53
12 Экономическая часть. 56
12.1 Себестоимость изготовления 1 тонны годных отливок. 57
12.2 Экономические показатели. 58
13 Технологический процесс изготовления отливки «Корпус АКШ». 59
13.1 Требования, предъявляемые к детали. 59
13.2 Оценка технологичности конструкции детали. 60
13.3 Выбор способа изготовления отливки. 61
13.4 Проектирование технологии формы.. 61
13.5 Проектирование модели. 63
13.6 Выбор типа и расчет размеров литниковой системы.. 64
13.7 Выбор типа модельных плит и опок. 67
13.8 Расчет подъемной силы.. 68
13.9 Параметры и условия заливки формы.. 69
13.10 Охлаждение, обрубка, очистка и контроль отливок. 69
14 Специальная часть. 71
15 Заключение. 74
16 Список использованных источников. 75
17 Приложения. 76
Введение
Задача развития отечественного машиностроения неразрывно связана с разработкой и внедрением новых, совершенствованием существующих конструкционных материалов и созданием прогрессивных технологических процессов получения из них изделий ответственного назначения.
В настоящее время более 45 % (по массе) деталей современных машин и оборудования изготовляют литыми, из них ~75 % из чугуна.
Прогнозы развития техники показывают, что в ближайшем будущем производство и потребление чугунного литья в машиностроении будет преобладающим, так как по экономичности и комплексу свойств отливки из чугуна имеют неоспоримые преимущества в сравнении с отливками из других сплавов.
Повышение качества чугунных отливок имеет первостепенное значение для всех отраслей современного машиностроения, так как позволяет увеличить срок службы изделий, снизить их металлоемкость и в целом сократить потребность в отливках в машиностроении.
Проблема повышения качества отливок из чугуна носит комплексный характер и включает следующие вопросы: выбор и подготовку шихтовых материалов, оптимизацию процессов плавки, разработку способов воздействия на кристаллизацию и структурообразование чугунных отливок.
При этом ориентация промышленности на преимущественное применение электроплавки чугуна позволяет не только поднять на качественно новую ступень развитие отечественного литейного производства, но и существенно улучшить структуру чугунного литья за счет резкого повышения доли легированных и высококачественных чугунов с различной формой графита.
Многочисленные исследования последних лет убедительно показали, что процесс модифицирования жидкого исходного расплава различными добавками является наиболее эффективным средством повышения физико-механических и эксплуатационных свойств чугуна в отливках как вследствие изменения формы и характера распределения графита, так и в результате воздействия на процесс кристаллизации и структурообразование металлической основы.
Модифицирование и микролегирование становятся необходимыми и важными элементами технологии получения высококачественных чугунов при плавке в индукционных и дуговых печах, позволяющих производить предварительную обработку расплава (рафинирование, термовременную обработку и др.) и создавать наиболее благоприятные условия для эффективного протекания этих процессов.
Широкое применение и непрерывное совершенствование методов выплавки, модифицирования, легирования и термообработки чугуна позволяют стабильно удовлетворять широкий комплекс прочностных, эксплуатационных и технологических требований, предъявляемых современной техникой к отливкам из чугуна с различной формой графита.
По комплексу физико-механических и служебных свойств к числу уникальных конструкционных материалов современного машиностроения относится высокопрочный чугун с шаровидным графитом. Дальнейшее значительное расширение его производства в нашей стране, в том числе взамен стали при изготовлении отливок и поковок, является одной из наиболее актуальных задач литейного производства.
Успешное решение проблемы развития литейного производства в целом прямым образом связано с дальнейшим повышением уровня механизации, автоматизации и совершенствованием технологии формообразования отливок, что позволит повысить производительность труда при одновременном улучшении санитарно-гигиенических условий работы в литейных цехах.
Целью данной работы является создание проекта современного чугунолитейного цеха, предназначенного для выпуска 30000 тонн в год мелкого чугунного литья. Технологический процесс литья иллюстрируется на примере отливки-представителя «Корпус АКШ».
1 Исходные данные для проектирования
В качестве исходных данных для расчета производственной программы проектируемого цеха используются чертежи, спецификации и технические условия на отливки, карты технологического процесса и номенклатуру фасонных отливок, выпускаемых в ЧЛЦ ООО ЛТК «Новолит» (таблица 1, 2).
1.1 Подетальная программа выпуска отливок.
Таблица 1 - Номенклатура отливок
№ п/п | Наименование отливки | Марка чугуна | Масса отливки, кг | Годовой выпуск годных отливок | |
шт. | тонн. | ||||
1 | 2 | 3 | 4 | 5 | 6 |
1 технологический поток (фасонные отливки массой менее 20 кг) | |||||
1 | Крышка СО | СЧ-20 | 2,6 | 25000 | 65 |
2 | Корпус СО | СЧ-20 | 2,8 | 30000 | 84 |
3 | Улитка СО | ВЧ-50 | 4,0 | 30000 | 120 |
4 | Фланец СО | СЧ-15 | 4,2 | 30000 | 136 |
5 | Линейка СО | СЧ-20 | 4,8 | 28000 | 134,4 |
6 | Корпус вала шкива | СЧ-20 | 4,9 | 30000 | 147 |
7 | Ступица РПН | ВЧ-50 | 5,0 | 30000 | 150 |
8 | Втулка РПН | СЧ-20 | 6,5 | 26000 | 169 |
9 | Втулка РПА | СЧ-20 | 6,7 | 28000 | 188 |
10 | Крыщкаполуфланца | СЧ-20 | 7,0 | 26000 | 182 |
11 | Полуфланец | СЧ-20 | 7,8 | 30000 | 234 |
12 | Ролик РПА | ВЧ-50 | 8,2 | 15000 | 123 |
13 | Крейцкопф РПА | СЧ-15 | 8,8 | 18000 | 158,4 |
14 | Сопло смесителя | СЧ-20 | 9,4 | 15000 | 141 |
15 | Основное звено | СЧ-20 | 9,5 | 15000 | 143 |
16 | Замыкающее звено | СЧ-15 | 10,0 | 15000 | 150 |
17 | Начальное звено | СЧ-20 | 10,6 | 14000 | 149 |
18 | Маховик СО | СЧ-15 | 11,2 | 15000 | 168 |
19 | Жернов СО | ВЧ-50 | 11,8 | 14000 | 165,2 |
20 | Фиксатор СО | ВЧ-50 | 12,0 | 14800 | 177,6 |
21 | Кронштейн | СЧ-15 | 14,2 | 14000 | 198,8 |
22 | Вкладыш ЛРА | СЧ-20 | 15,8 | 12800 | 202,3 |
23 | Корпус подшипника | СЧ-20 | 16,2 | 15000 | 243 |
24 | Шкив СБР | СЧ-15 | 16,4 | 14500 | 242,2 |
25 | Плита горелочная №1 | СЧ-15 | 16,5 | 15000 | 247,5 |
26 | Плита горелочная №2 | СЧ-15 | 17,4 | 14800 | 257,5 |
1 | 2 | 3 | 4 | 5 | 6 |
27 | Плита горелочная №3 | СЧ-15 | 18,0 | 14000 | 252 |
28 | Ползун | СЧ-20 | 18,4 | 15000 | 276 |
29 | Плита фартука | СЧ-20 | 19,2 | 14800 | 284,2 |
30 | Плита нижняя | СЧ-20 | 19,6 | 15000 | 294 |
31 | Патрубок переходной | СЧ-15 | 19,8 | 14000 | 277,2 |
32 | Крышка люка | СЧ-20 | 20,0 | 15000 | 300 |
33 | Бандаж | ВЧ-50 | 20,0 | 15000 | 300 |
Всего по 1 потоку: | 637705 | 6365,3 | |||
Второй технологический поток (отливки массой от20 до 100 кг) | |||||
1 | Барабан | СЧ-20 | 22,0 | 9600 | 211,2 |
2 | Плита напольная квадрат | СЧ-15 | 25,4 | 250000 | 6350 |
3 | Плита напольн. шестигр. | СЧ-15 | 27,5 | 250000 | 6875 |
4 | Втулка | СЧ-20 | 30,4 | 8800 | 268 |
5 | Венец зубчатый | ВЧ-50 | 32,2 | 9440 | 303,9 |
6 | Шестерня | СЧ-15 | 35,2 | 9220 | 324,5 |
7 | Кольцо сферическое | СЧ-20 | 38,8 | 9800 | 380,3 |
8 | Корпус редуктора | ВЧ-50 | 40,0 | 12000 | 480 |
9 | Опора промежуточная | СЧ-15 | 42,2 | 9600 | 396,7 |
10 | Шпуля | СЧ-20 | 43,6 | 10000 | 436 |
11 | Крышка АПК | СЧ-15 | 44,2 | 10000 | 442 |
12 | Крышка АКШ | СЧ-15 | 46,3 | 9600 | 444,5 |
13 | Корпус подшипника АТГ | СЧ-15 | 46,6 | 9600 | 447,4 |
14 | Колодка | СЧ-15 | 47,1 | 9200 | 433,3 |
15 | Основание АТ | СЧ-20 | 48,2 | 8400 | 404,9 |
16 | Маховик | СЧ-20 | 48,8 | 9600 | 468,5 |
17 | Шкив СБ | СЧ-20 | 48,8 | 8600 | 419,7 |
18 | Ступица РН | СЧ-20 | 50,3 | 10000 | 503,0 |
19 | Венец зубчатый СБР | СЧ-20 | 54,2 | 8700 | 471,5 |
20 | Втулка СРГ | СЧ-20 | 57,8 | 8200 | 473,9 |
21 | Траверса левая | СЧ-15 | 62,1 | 7200 | 447,2 |
22 | Траверса правая | СЧ-20 | 68,5 | 7600 | 520,6 |
23 | Корпус редуктора АТ | СЧ-20 | 78,8 | 5600 | 443 |
24 | Диск секторный | СЧ-20 | 84,6 | 8000 | 676,8 |
25 | Корыто | СЧ-20 | 82,5 | 7600 | 627 |
26 | Щека подвижная | СЧ-20 | 90,0 | 429 | 386,7 |
Итого по 2 потоку: | 706789 | 23635,7 | |||
Всего фасонного литья | 1344449 | 30000 |
В соответствии с данной подетальной производственной программой проектируемый цех следует классифицировать как цех серийного производства мелкого чугунного литья. Годовой выпуск продукции составляет 30000 тонн годного литья. Из них фасонного литья массой до 20 кг- 6365,3 т. (первый технологический поток) и 23635,7 тонн литья массой от20 до 100 кг (второй технологический поток). Отливки изготавливаются из серого чугуна с пластинчатым графитом марок СЧ-15 и СЧ20 и высокопрочного чугуна с шаровидным графитом марки ВЧ-50.
2. Режим работы и фонды времени
В литейных цехах применяется 3 вида режимов работы [1, 2]:
- ступенчатый, с разделением операций по времени, в неизолированных общих помещениях;
- комбинированный, назначаемый с учетом массы отливок и характера их производства в различных отделениях цеха;
- параллельный, характеризуется совмещением по времени основных технологических операций: формовка, заливка и выбивка производятся одновременно, но на разных участках цеха.
В проектируемом чугунолитейном цехе применяем трехсменный параллельный режим работы, т.е. все технологические операции выполняются одновременно на всех производственных участках.
В соответствии с выбранным режимом работы определяем действительный фонд времени работы оборудования и рабочих. Действительный годовой фонд времени (Фд) определяется путем исключения из номинального годового фонда времени неизбежных потерь времени для нормального организованного производства и составит 6210ч.
Действительный фонд времени работы оборудования приведен в таблице 2.
Действительный фонд времени рабочих приведен в таблице 3.
Таблица 2 – Действительный годовой фонд времени работы оборудования
Наименование оборудования | Номинальный годовой фонд времени, час | Потери от номинального фонда, % | Действительный годовой фонд времени, час |
Плавильная печь | 6210 | 6 | 5840 |
Литейное оборудование цехов мелкосерийного и серийного литья | 6210 | 5 | 5900 |
Термическая печь | 6210 | 6 | 5840 |
Вспомогательное оборудование | 6210 | 4 | 5960 |
Таблица 3 - Действительный годовой фонд времени рабочих
Продолжитель-ность рабочей недели, час | Продолжитель- ность отпуска, дней | Номинальный годовой фонд времени, час | Потери от номинального фонда времени,% % | Действительный годовой фонд времени,час |
40 | 24 | 2083 | 14,8% | 1774 |
3. Проектирование плавильного отделения
Плавильное отделение состоит из участков набора и подогрева шихты, собственно плавки чугуна, сушки и подогрева ковшей, ремонта футеровки ковшей, плавильных печей и оборудования[1].
В задачу плавильного отделения, входит бесперебойное обеспечение жидким металлом формовочного-заливочно-выбивного отделения цеха.
Основой при проектировании плавильного отделения, является определение массы выплавляемого чугуна.
3.1 Программа отделения
При расчете программы плавильного отделения за 100% принимается количество перерабатываемой шихты-металлозавалка (А3). Количество жидкого метала (А2) будет составлять разность между металлозавалкой и безвозвратными потерями в виде физического и химического угара (а2), т.е. 100-а2(в процентах от металлозавалки).
Количество потерь в виде всплесков, сливов и ухода со шлаком (а1), образующихся в процессе плавки, при переливе из печи в ковш, транспортировки к месту разливки, определяется на основе данных по базовому цеху с учетом выбранного типа плавильного агрегата, средств транспортировки, способов разливки металла[2, 3].
Таким образом, для составления расчетной программы плавильного отделения принимаем: а2 – угар и безвозвратные потери 5%, а1 – сливы, всплески 3%.Расход металла на ЛПС по заводским данным в среднем составляет 30%.Рассчитаем количество жидкого металла по известной массе отливок с литниками и прибылямис учетом 3% брака.
А1 = Мотл + Млпс. = 30000 + 9000 = 39000 т, с учетом брака
39000×1,03 = 40170
Массу жидкого металла (А2) определяем по формуле:
А2 = А1 · ; (1)
А2 = 40170 · = 41479,88 ≈ 41480т.
Металлозавалка А3 = А2 · ; (2)
А3 = 41480 * 1,052635 = 43663,29 ≈ 43663т.
Угар составляет 43633-41480 = 2153т.
3.2 Выбор плавильного оборудования
При выборе плавильных процессов и агрегатов важнейшим показателем является возможность использования экономичных шихтовых материалов. Современное чугунолитейное производство должно ориентироваться на использование преимущественно легковесного стального лома в виде листовой обрези и высечки, металлизованных окатышей, чугунного лома и передельного доменного чугуна, так как производство литейного чушкового чугуна на металлургических заводах нерентабельно.
В области использования энергетических ресурсов литейного производства следует отметить общую тенденцию перехода на электроплавку чугуна, как более гибкого и экологически чистого процесса.
Дуговые электропечи отличаются высоким КПД (60-70%) в период расплавления металла и высокой эксплуатационной надежностью. Металлургические возможности ДСП позволяют использовать крупногабаритную и тяжеловесную шихту с высоким содержанием окислов железа и неметаллических примесей. Однако локальный перегрев металла в зоне действия электрической дуги и отсутствие перемешивания ванны приводит к повышенному угару шихты, ферросплавов и графитированых электродов, а также к увеличению выброса вредных веществ в атмосферу.
Появившиеся в последние годы дуговые печи постоянного тока (ДППТ) не имеют многих недостатков, присущих ДСП, однако производственный опыт их эксплуатации недостаточен для того, чтобы сделать однозначный вывод о целесообразности применения ДППТ в проектируемом цехе.
Индукционные тигельные печи промышленной частоты обладают следующими технологическими преимуществами [3]:
· позволяют легко достигать высоких температур перегрева благодаря выделению энергии непосредственно в нагреваемом металле;
· обеспечивают более точный химический состав сплава из–за отсутствия соприкосновения металла с топливом или электродами;
· обладают хорошим перемешиванием металла под воздействием электродинамических сил, что повышает коэффициент усвоения ферросплавов и снижает угар шихты.
При переходе на плавку с «болотом» в объеме 30-50% ванны изменяются требования к составу потребляемой шихты. Вместо дорогостоящего литейного доменного чугуна в состав шихты можно вводить более дешевые легковесные материалы (листовая обрезь, чугунная и стальная стружка, легковесный стальной лом и др.). Применение более дешевой шихты дает ощутимый экономический эффект.
С энергетической точки зрения печи типа ИЧТ наиболее сбалансированы, так как имеют среднее значение к.п.д. в период расплавления шихты и высокий к.п.д. в период перегрева металла. Предварительный подогрев шихты до 400-500°С позволяет экономить до 10-15% электроэнергии.
Важным достоинством индукционных печей является резкое сокращение загрязнения воздушного бассейна отходящими газами, особенно в тех случаях, когда промышленные предприятия находятся в непосредственной близости от жилых районов.
Канальные индукционные печи имеют высокий КПД (до 85-90%) и более экономичны, чем тигельные, однако они не могут работать на твердой завалке и чаще всего применяются в виде миксеров, предназначенных для накопления жидкого металла, его выдержки и перегрева до заданной температуры[3].
Учитывая вышесказанное, в качестве основного плавильного агрегата для выплавки серого чугуна марок СЧ15, СЧ20 и высокопрочного чугуна с шаровидным графитом марки ВЧ-50 выбираем индукционную тигельную печь промышленной частоты ИЧТ–6/2,5 с кислой футеровкой на основе кварцита.
Расчетное количество печей определяем по формуле [1]:
(3)
где А – металлозавалка, т,
Кн – коэффициент неравномерности (Кн = 1,1 - 1,5); Кн=1,3,
Фд – действительный годовой фонд времени, ч; Фд=5840час,
qц – производительность агрегата, 2,8 т/ч.
Принимаем 4 единицы оборудования.
Коэффициент загрузки: (4)
.
Таким образом, устанавливаем в плавильном отделении проектируемого цеха 4 индукционные печи ИЧТ – 6/2,5.
Технические характеристики ИЧТ-6/2,5
Параметры | Значение |
Номинальная вместимость, т | 6,0 |
Мощность питающего трансформатора, кВт | 2500 |
Число фаз питающей сети | 3 |
Число фаз контурной цепи | 1 |
Частота тока, Гц | 50 |
Номинальная температура жидкого металла, °С | 1400 |
Максимальная температура жидкого металла, °С | 1500 |
Производительность, т/ч | 2,8 |
Масса электропечи, т | 55,5 |
Количество питающих трансформаторов, шт. | 1 |
3.3 Расчет шихты, материальный баланс плавки
Для расчета шихты необходимо знать химический состав металла, который нужно получить в отливке, состав исходных материалов, из которых составляется шихта. При составлении шихты важно не только получить требуемый химический состав, но и составить ее из наиболее дешевых материалов.
В проектируемом цехе выплавляют три марки чугуна: СЧ-15, СЧ-20 и ВЧ-50.
Таблица 4 – Рекомендуемый химический состав
Марка | Содержание элементов | ||||
C | Si | Mn | P | S | |
СЧ15 ГОСТ 1412-85 | 3,5-3,7 | 2,0-2,4 | 0,5-0,8 | до 0,15 | до 0,15 |
СЧ20 ГОСТ 1412-85 | 3,3-3,5 | 1,4-2,4 | 0,6-0,9 | до 0,15 | до 0,15 |
ВЧ-50 ГОСТ 7293-85 | 3,2-3,7 | 1,9-2,9 | 0,3-0,7 | до 0,1 | до 0,03 |
Учитывая то, что основная доля кремния (0,8-1,0%) вносится в высокопрочный чугун во время операции внепечного модифицирования, следует производить выплавку чугуна базового химического состава на единой шихте, а корректировку до нужной марки производить с помощьюферросплавов. При производстве высокопрочного чугуна с шаровидным графитом предусматриваем обработку чугуна в ковше с помощью модификатора ФСМг4 ( 45% кремния, 4,5% магния, 1,5% редкоземельных металлов, по 1-1,5% алюминия и кальция, остальное-железо) по методу «Сендвич-процесс». В качестве покровного материала используется литой чугунный диск.
Базовый химический состав чугуна принимаем следующий:
C–3,3-3,5; Si–1,7-1,9; Mn–0,5-0,7; S - до 0,015; P- до 0,1.
При наличии организационных возможностей следует разделить во времени выплавку различных марок чугуна путем группировки изготавливаемого литья по маркам в целях последовательного, а не параллельного исполнения заказов на отливки из различных марок чугуна.
За основу принимаем данные состава шихты по базовому цеху.
Чугун передельный…………………………………20%
Чугунный лом……………………………………….25%
Стальной лом………………………………………..14%
Возврат……………………………………………….40%
ФС 45…………………………………………………1%
100%
Расчет производим при помощи программы «Шихта» в виде таблиц 5-7.
Таблица 5 – Базовыйхимсостав
Таблица 6 - Состав базовой шихты
Таблица 7 – Расчет стоимости тонны металлозавалки
Таблица 8 – Материальный баланс плавильного отделения
Статьи прихода в шихтовое отделение | Статьи расхода металлозавалки | ||||
Наименование | % | т/г | Наименование | % | т/г |
Чугун передельный | 32 | 13972 | Годное | 68,7 | 30000 |
Чугун литейный | 5 | 2183 | ЛПС | 20,6 | 9000 |
Стальной лом | 20 | 8733 | Брак | 2,7 | 1170 |
Возврат | 30 | 13098 | Всплески, сливы | 3 | 1310 |
Чугунный лом | 10 | 4367 | Жидкий металл | 95 | 41480 |
Ферросплавы | 3 | 1310 | угар | 5 | 2183 |
Итого: | 100 | 43 663 | Итого: | 100 | 43 663 |
На основе баланса определяем средний выход годного: ∙ 100 = 69 %
3.4 Система набора и взвешивания шихты, вспомогательные участки
Суточный запас шихтовых материалов хранится в расходных контейнерах на участке шихты, куда поступает автомобильным транспортом.
Набор и подача шихты в печи производиться с помощью мостового крана грузоподъемностью 15/5 с электромагнитной шайбой. Загрузка ферросплавов производится плавильщиками вручную.
Кроме основных участков по навеске шихты и плавке чугуна в плавильное отделение входят вспомогательные участки по ремонту оборудования и сушке ковшей, контролю качества выплавляемого сплава.
Для ремонта оборудования и ковшей в плавильном отделении предусмотрены участки приготовления огнеупорной массы, ремонта футеровки ковшей и съемных узлов печей, площадки для ремонта механизмов и оборудования, стенды для сушки и подогрева ковшей.Стенды для сушки ковшей оборудуют местными укрытиями и инжекционными горелками среднего давления[1, 4].
Для контроля качества выплавляемого чугуна в плавильном отделении, в непосредственной близости от плавильных печей, выделен участок для заливки технологических проб. Залитые пробы передаются в экспресс – лабораторию, где производится химический анализ металла.
Подъемно - транспортное оборудование обслуживает технологическое оборудование, размещенное на основных площадях и в отдельных помещениях плавильного отделения. Для этого применяю мостовые краны грузоподъемностью 15/5 т.
3.5 Планировка плавильного отделения
Расчет площади плавильного отделения произвожу исходя из того[1], что плавильное отделение оснащено 4-мя печами ИЧТ-6/2,5, каждый плавильный агрегат имеет собственный трансформатор и конденсаторную батарею, расположенные в отдельном пристроенном помещении площадью 36м2каждое. Участок для футеровки и текущего ремонта ковшей принимаем площадью 36м2, также предусматриваем стенд для сушки ковшей 20м². Кроме того в плавильном отделении располагается стенд для подготовки и хранения резервных индукторов печей. В целях оперативного контроля химического состава чугунапредусматривается наличие экспресс лаборатории площадью 36м2.
Перемещение грузов плавильного участка осуществляется двумя мостовыми кранами грузоподъемностью 15/5 тонн, снабженных электромагнитными шайбами для транспортировки и набора шихты.
Плавильное отделение располагается в 24 метровом пролете.
Комната мастеров плавильного отделения располагается в помещении площадью 36 м2 .
Для обеспечения бесперебойной работы автоматических заливочных установок необходимо иметь достаточное количество ковшей для передачи в них выплавленного чугуна[1, 2]. Расчет парка ковшей сведен в таблицу 9.
Таблица 9 - Ведомость парка ковшей
Емкость ковша | Кол-во металла, подлежащего заливке | Число одновременно работающих ковшей | Число ковшей в ремонте | Запас ковшей | Всего ковшей |
т. | т | шт. | шт. | шт. | шт. |
2 | 41480 | 2 | 2 | 1 | 5 |
4 Проектирование формовочно–заливочно-выбивного отделения
Основные операции, производимые в формовочном отделении[1, 2, 4]:
- изготовление литейных форм;
- постановка стержней;
- сборка форм;
- заливка форм;
-выбивка форм.
4.1 Программа формовочного отделения
Программа формовочного отделения отражена в расчетной ведомости сведенной в таблицу 10.
Формовочное оборудование выбирают в зависимости от технологического процесса и способа уплотнения, по необходимому размеру форм и производительности, в зависимости от массы, объема и серийности производства отливок.
В условиях серийного производства, каким является проектируемый чугунолитейный цех, целесообразно устанавливать автоматические формовочные линии, более подходящие для серийного производства [1]. В соответствии со способом изготовления и группами отливок по массе (см. таблицы 1,2) устанавливаем два групповых технологических потока производства отливок:
· I поток – мелкие отливки массой до 20 кг формуются на автоматических формовочных линиях модели КЛ22821 с размером опок 500×400×200 мм;
· II поток – более крупные отливки массой от 20 до 100 кг формуются на автоматической линии модели Л450 с размером опок 1000×800×400 мм;
Набор групповых потоков и оптимальные размеры форм выбираем с учетом габаритных размеров и массы изготовляемых отливок так, чтобы любая новая заготовка могла бы рационально изготовляться в рамках того или иного принятого потока.
Таблица 10 - Расчетная ведомость формовочного отделения
п/п | Наименование отливки | Марка чугуна | Масса отливки, кг | Кол-во в 1 форме | Годовой выпуск годных отливок | ||
шт. | шт. с учетом брака | форм | |||||
1 | 2 | 3 | 4 | 5 | 6 | 7 | 8 |
1 групповой технологический поток – отливки массой до 20 кг | |||||||
1 | Крышка СО | СЧ-20 | 2,6 | 4 | 25000 | 25750 | 6438 |
2 | Корпус СО | СЧ-20 | 2,8 | 4 | 30000 | 30900 | 7725 |
3 | Улитка СО | ВЧ-50 | 4,0 | 4 | 30000 | 30900 | 7725 |
4 | Фланец СО | СЧ-15 | 4,2 | 4 | 30000 | 30900 | 7725 |
5 | Линейка СО | СЧ-20 | 4,8 | 4 | 28000 | 28840 | 7210 |
6 | Корпус вала шкива | СЧ-20 | 4,9 | 2 | 30000 | 30900 | 15450 |
7 | Ступица РПН | ВЧ-50 | 5,0 | 2 | 30000 | 30900 | 15450 |
8 | Втулка РПН | СЧ-20 | 6,5 | 2 | 26000 | 26780 | 13390 |
9 | Втулка РПА | СЧ-20 | 6,7 | 2 | 28000 | 28840 | 14420 |
10 | Крыщкаполуфланца | СЧ-20 | 7,0 | 2 | 26000 | 26780 | 13390 |
11 | Полуфланец | СЧ-20 | 7,8 | 2 | 30000 | 30900 | 15450 |
12 | Ролик РПА | ВЧ-50 | 8,2 | 2 | 15000 | 15450 | 7725 |
13 | Крейцкопф РПА | СЧ-15 | 8,8 | 2 | 18000 | 18540 | 9270 |
14 | Сопло смесителя | СЧ-20 | 9,4 | 1 | 15000 | 15450 | 15450 |
15 | Основное звено | СЧ-20 | 9,5 | 1 | 15000 | 15450 | 15450 |
16 | Замыкающее звено | СЧ-15 | 10,0 | 1 | 15000 | 15450 | 15450 |
17 | Начальное звено | СЧ-20 | 10,6 | 1 | 14000 | 14420 | 14420 |
18 | Маховик СО | СЧ-15 | 11,2 | 1 | 15000 | 15450 | 15450 |
19 | Жернов СО | ВЧ-50 | 11,8 | 1 | 14000 | 14420 | 14420 |
20 | Фиксатор СО | ВЧ-50 | 12,0 | 1 | 14800 | 15244 | 15244 |
21 | Кронштейн | СЧ-15 | 14,2 | 1 | 14000 | 14420 | 14420 |
22 | Вкладыш ЛРА | СЧ-20 | 15,8 | 1 | 12800 | 13184 | 13184 |
23 | Корпус подшипника | СЧ-20 | 16,2 | 1 | 15000 | 15450 | 15450 |
24 | Шкив СБР | СЧ-15 | 16,4 | 1 | 14500 | 14935 | 14935 |
25 | Плита горелочная №1 | СЧ-15 | 16,5 | 1 | 15000 | 15450 | 15450 |
26 | Плита горелочная №2 | СЧ-15 | 17,4 | 1 | 14800 | 15244 | 15244 |
27 | Плита горелочная №3 | СЧ-15 | 18,0 | 1 | 14000 | 14420 | 14420 |
28 | Ползун | СЧ-20 | 18,4 | 1 | 15000 | 15450 | 15450 |
29 | Плита фартука | СЧ-20 | 19,2 | 1 | 14800 | 15244 | 15244 |
30 | Плита нижняя | СЧ-20 | 19,6 | 1 | 15000 | 15450 | 15450 |
31 | Патрубок переходной | СЧ-15 | 19,8 | 1 | 14000 | 14420 | 14420 |
32 | Крышка люка | СЧ-20 | 20,0 | 1 | 15000 | 15450 | 15450 |
33 | Бандаж | ВЧ-50 | 20,0 | 1 | 15000 | 15450 | 15450 |
Всего по 1 потоку | 637706 | 656838 | 441819 | ||||
2 групповой технологический поток (отливки массой 20-100 кг) | |||||||
34 | Барабан | СЧ-20 | 22,0 | 4 | 9600 | 9888 | 2472 |
35 | Плита напольная квадрат | СЧ-15 | 25,4 | 2 | 250000 | 257500 | 128750 |
36 | Плита напольн. шестигр. | СЧ-20 | 27,5 | 2 | 250000 | 257500 | 128750 |
37 | Втулка | СЧ-20 | 30,4 | 4 | 8800 | 9064 | 2266 |
38 | Венец зубчатый | ВЧ-50 | 32,2 | 2 | 9440 | 9724 | 4862 |
39 | Шестерня | СЧ-15 | 35,2 | 4 | 9220 | 9497 | 2375 |
40 | Кольцо сферическое | СЧ-20 | 38,8 | 2 | 7800 | 8034 | 4017 |
1 | 2 | 3 | 4 | 5 | 6 | 7 | 8 |
41 | Корпус редуктора | ВЧ-50 | 40,0 | 2 | 12000 | 12360 | 6180 |
42 | Опора промежуточная | СЧ-15 | 42,2 | 2 | 9400 | 9682 | 4841 |
43 | Шпуля | СЧ-20 | 43,6 | 2 | 10000 | 10300 | 5150 |
44 | Крышка АПК | СЧ-15 | 44,2 | 2 | 10000 | 10300 | 5150 |
45 | Крышка АКШ | СЧ-15 | 46,3 | 2 | 9600 | 9888 | 4944 |
46 | Корпус подшипника АТГ | СЧ-15 | 46,6 | 2 | 9600 | 9888 | 4944 |
47 | Колодка | СЧ-15 | 47,1 | 1 | 9600 | 9888 | 9888 |
48 | Основание АТ | СЧ-20 | 48,2 | 1 | 8400 | 8652 | 8652 |
49 | Маховик | СЧ-20 | 48,8 | 1 | 9600 | 9888 | 9888 |
50 | Шкив СБ | СЧ-20 | 48,8 | 1 | 8600 | 8858 | 8858 |
51 | Ступица РН | СЧ-20 | 50,3 | 1 | 10000 | 10300 | 10300 |
52 | Венец зубчатый СБР | СЧ-20 | 54,2 | 1 | 8700 | 8961 | 8961 |
53 | Втулка СРГ | СЧ-20 | 57,8 | 1 | 8200 | 8446 | 8446 |
55 | Траверса левая | СЧ-15 | 62,1 | 1 | 7200 | 7416 | 7416 |
56 | Траверса правая | СЧ-20 | 68,5 | 1 | 7600 | 7828 | 7828 |
57 | Корпус редуктора АТ | СЧ-20 | 78,8 | 1 | 5600 | 5768 | 5768 |
58 | Диск секторный | СЧ-20 | 84,6 | 1 | 8000 | 8240 | 8240 |
59 | Корыто | СЧ-20 | 82,5 | 1 | 7600 | 7828 | 7828 |
60 | Щека подвижная | СЧ-20 | 90,0 | 1 | 429 | 442 | 442 |
Всего по 2 потоку | 704989 | 726140 | 407224 |
Зона установки стержней |
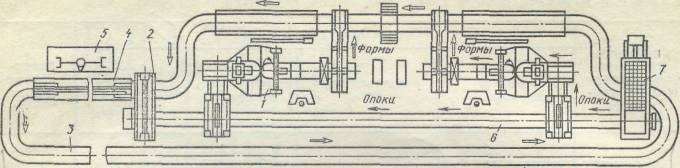
1— автоматический формовочный блок; 2 — перестановщик; 3— пульсирующий литейный конвейер; 4 — нагружатель форм; 5 — заливочная площадка; 6 — конвейер роликовый для возврата опок; 7 — установка выбивки;
Рисунок1 - Типовая планировка линии КЛ22821 (опоки 500*400*200 мм).
1- пульсирующий конвейер; 2-сталкиватель форм; 3;8 -рольганги; 4-механизм выдавливания кома смеси; 5- механизм очистки опок; 6-транспортер дополнительного охлаждения отливок; 7- выбивная решетка; 9- распаровщик опок; 10- машина формовки нижних полуформ; 11-кантователь; 12-установщик полуформ низа на конвейер;13- машина формовки верхних полуформ;14-сборщик форм; 15- грузоукладчик;
I-участок простановки стержней; II- участок заливки форм; III- охладительная ветвь конвейера в вентиляционном коробе.
Рисунок 2 - Типовая планировка линии Л450 (опоки 1000*800*400мм)
-
4.2 Выбор и расчет количества формовочного оборудования
I поток.
Количество форм с мелкими отливками (массой менее 20 кг), согласно расчетной ведомости (см.таблицу 9) составляет367300форм, следовательно,
с учетом6% брака, возникающего при формовке на встряхивающее-прессовых формовочных машинах, должно производится:
441819*1,06 = 468329 форм.
Определяю количество формовочных линий КЛ22821 при 3-х сменном режиме работы оборудования[1, 2]:
Р1= , (3)
гдеn- годовое число форм изготавливаемое в потоке, п/ф,
Фд- действительный фонд времени работы оборудования, 5900 ч,
Nр -производительность оборудования, 120 форм/час,
k-коэффициент неравномерности=1.
Р1= = 0,7
Коэффициент загрузки рассчитываю по формуле (4).
Кз= = 0,70
Следовательно, применяем приизготовления форм для мелких отливок автоматическую формовочную линию 4Л22821.
II поток.
Количество форм с отливками массой 20-100 кг по расчетной ведомости составляет407224 форм, следовательно, учитывая 6% брака на операции формовки на встряхивающее-прессовых машинах автоматической линии Л450 должно производиться:
407224*1,06 = 431657 форм.
Определяю количество линий при 3-х сменном режиме работы оборудования
по формуле (3):
Р1= = 0,74.
Принимаем 1 формовочную линию модели Л450, коэффициент загрузки составляет (4):
Кз= = 0,74
Производство отливок осуществляется в сырых песчано-глинистых формах. Изготовление отливок в сырых песчано-глинистых формах имеет ряд преимуществ над другими видами формовки, а именно:
- низкую стоимость формовочных материалов;
- возможность многократного использования оборотной смеси;
- высокую производительность формовочного оборудования
Характеристика и параметры выбранных автоматических линий.
Технологический цикл изготовления отливок на линии КЛ22821 (рис.1) включает следующие операции: сталкивание комплекта пустых опок с тележек непрерывно движущегося литейного конвейера; разъединение (распаровку) комплекта опок; последовательную формовку верхней и нижней полуформ; вытяжку моделей; установку полуформ на спутниковый конвейер для простановки стержней; сборку форм и передачу собранных форм на литейный конвейер; нагружение форм грузами; заливку, охлаждение, и выбивку форм[2].
Простановку стержней проводят вручную, заливка форм производится при помощи автоматического заливочного устройства. Линии целесообразно использовать комплектно с автоматизированной смесеприготовительной системой производительностью до 40 м3/ч. Применяемая формовочная смесь — единая песчано-глинистая. Метод дозирования смеси — объемный, с помощью шиберного дозатора. Формовочный автомат блока — челночный трехпозиционный, опоки 500*400 мм, высота опок 200мм; с целью экономии формовочной земли при изготовлении форм с неглубоким отпечатком предусматриваем возможность использования опок высотой 100 и 150 мм.
Уплотнение форм встряхиванием с амортизацией ударов и одновременной или последующей подпрессовкой, верхняя вытяжка моделей позволяют получать глубокие полости и «болваны», максимальная высота выступающей части которых над ладом опоки — 80 мм. При формовке верхней опоки в ней при помощи пружинной модели стояка выполняют литниковую воронку диаметром до 75 мм и глубиной до 70 мм, а также стояк. Грузоукладчик — цепной, выбивка форм вибрационная. Цикловая производительность- до 120 полуформ в час на каждом формовочном блоке, т.е. при 2 блоках – до 120 форм в час. Габариты -72000*11000*3000мм.
Комплексная автоматическая линия модели Л453 предназначена для производства отливок в разовых песчано-глинистых формах[2]. Основные агрегаты линии (рис. 2.): литейный пульсирующий конвейер 7, механизм съема форм литейного конвейера 2, рольганги 3, 8, механизм выдавливания кома смеси 4, механизм очистки опок 5, транспортер дополнительного охлаждения 6, встряхивающая решетка7, распаровщик9. трехпозиционные формовочные машины для формовки нижних и верхних полуформ10, 13, кантователь 7, установщик полуформ на конвейер 12, сборщик форм 14, грузоу кладчик 15.
Работа линии происходит следующим образом. Пустые выбитые опоки по рольгангу поступают на позицию механизма очистки опок, где очищаются от остатков смеси и передаются на рольганг, а затем в распаровщик. После распаровки опоки поступают в формовочные машины для изготовления нижних и верхних полуформ. Изготовленныенижние полуформы передаются на кантователь, где кантуются и поступают на позицию установщика нижних полуформ, откуда по конвейеру передаются сборщику форм.
На участке (зона простановки стержней I) литейного конвейера происходит установка стержней в нижние полуформы. Изготовленные полуформы верха передаются в кантователь, кантуются для осмотра, затем снова переворачиваются и поступают на позицию сборщика, где собираются с нижнимиполуформами.
Собранные формы, перемещаясь по литейному конвейеру, нагружаются с помощью грузоукладчика и поступают на участок заливки II. После заливки, постепенно охлаждаясь, формы перемещаются к позиции механизма съема форм. Здесь формы поднимаются над литейным конвейером и по рольгангу перемещают к механизму выдавливания кома смеси, откуда отливки с комом земли попадают на транспортер дополнительного охлаждения. Этот транспортер позволяет резко сократить парк опок и сэкономить производственные площади за счет уменьшения длины зоны охлаждения литейного конвейера.
Далее ком смеси с отливками, перемещаясь по транспортеру, попадает на встряхивающую решетку, где происходит отделение отливок от горелой смеси.
Охлаждение форм на литейном конвейере происходит в охладительном кожухе ІІІ с вытяжной вентиляцией. На линии предусмотрена механизированная заливка форм с помощью заливочных устройств. Заливочное устройство для чугуна имеет индукционный подогрев металла. Доставка металла из плавильного отделения производится ковшами. Система управления линией выполнена на логических элементах. Аппаратура управления расположена в многосекционных шкафах управления. Режимы работы линии полуавтоматический и автоматический. Цикловая производительность – до 100 форм в час. Размер опок в свету 1000*800 мм; высота опок 400 мм; с целью экономии формовочной земли при изготовлении форм с неглубоким отпечатком предусматриваем возможность использования опок высотой 200 и 300 мм. Габариты линии-90000*16800*6300[4].
Для заливки форм предусматриваем на каждой линии автоматическую заливочную установку с индукционным подогревом модели У42 с пневматической подачей расплава[2]. При разливке чугуна, модифицированного магнием, предусматривается возможность применения в виде рабочего газа аргона для снижения угара магния в процессе разливки. Емкость ванны установки составляет 2,5 т, что создает буферный объем расплава, позволяющий менее жестко согласовывать производительность плавильных печей и потребление жидкого чугуна автоматическими линиями. Потребляемая мощность установки-210 кВт.
Внешний вид установки представлен на рисунке 3.
1 – газовое давление, 2 – крышка, 3 – канал в заливочный носок, 4 – заливочный стакан, 5 – заливаемая форма на конвейере, 6 – индукционная единица,
7-заливочный канал, 8 – ковш с металлом.
Рисунок 3 – Автоматическая заливочная установка У-42.
4.3 Схема работы формовочного отделения
Готовая формовочная земля подается из накопительных бункеров в разрыхлитель и в разрыхленном состоянии ленточным транспортером распределяется по эстакадам расходных бункеров над формовочными машинами.
Изготовленные на формовочных машинах полуформы после простановки стержней собираются и устанавливаются на тележечном конвейере, по которому перемещаются к участку заливки. Залитые формы, после выдержки определенного времени на охладительной ветви конвейера, транспортируются к агрегатам выдавливания кома земли с отливками и далее по транспортеру дополнительного охлаждения к выбивным решеткам.
Пустые опоки по конвейерувозврата опок возвращаются к формовочным машинам, выбитые отливки транспортируются по подземному пластинчатому конвейеру в обрубное отделение.
Выбитая на решетках земля просыпается через решетку и попадает на подземный ленточный конвейер с теплостойкой текстильной прорезиненной лентой. Далее отработанная земля проходит через магнитный сепаратор, где происходит отбор из земли металлических частиц; подается на вибросито для отделения спекшихся частиц и поступает в накопительный бункер, расположенный над бегунами, после чего цикл повторяется.
5 Проектирование стержневого отделения
Основой для проектирования стержневого отделения является расчетная ведомость (таблица 10).
5.1 Выбор стержневой смеси
В проектируемом цехе для изготовления стержней применяем холодно- твердеющие смеси (ХТС).
Технология рассчитана на выпуск мелких (до 40 кг)стержней, которые по сложности относятся от 2 до 5 класса, а по конструктивным особенностям – к сплошным и полым. [4]
Для изготовления стержней используются деревянные (окрашиваемые эпоксидными красками) и металлические стержневые ящики. Рабочую поверхность алюминиевых ящиков покрывают уретановой смолой. ХТС приготавливают и сразу же выдают в ящик из смесителей, установленных у рабочего места. Смесь уплотняется вручную или с помощью вибрационного стола, излишки смеси счищаются вручную. Готовые стержни окрашиваются быстросохнущими графитовыми красками.
Тонкостенные стержни сложной формы и тяжелые стержни изготавливают с каркасами.
Холодно-твердеющие стержни широко применяются благодаря высокой точности и прочности, а также обеспечению низкой шероховатости поверхностей отливок. ХТС имеют хорошую выбиваемость из отливок, а также малую трудоемкость стержневых и очистных работ.
Принимаем для приготовления стержневой смеси используемый на базовом заводе ЛПК «Новолит» современный «Альфасет-процесс», обладающий следующими преимуществами:
1) слабый запах при смесеприготовлении
2) малая токсичность на всех стадиях процесса
3) высокая прочность стержней
4) возможность применения песков различной химической природы
5) низкаяприлипаемость к оснастке
6) возможность очистки смесителя и оснастки водой.
Определенным недостатком процесса является необходимость применения формовочных песков с содержанием глинистой составляющей не более 0,5%, иначе возрастает расход дорогостоящей смолы.
Состав и свойства холоднотвердеющих смесей приведены в таблице 11.
Таблица 11 - Состав ХТС по Альфасет-процессу
Связующее – синтетическая смола | Расход |
Фенолоформальдегидная смола ТРА-480 | 1,9 – 2,2 |
Отвердитель | Расход |
Смесь сложных эфиров марки АСЕ | 20-25% от смолы |
Формовочный песок марки не ниже 3К2О403 - 100% (не более 0,5% пылевой фракции)
Свойства смеси:
Живучесть смеси – от 2до30 минут, в зависимости от температуры песка и марки и дозы отвердителя
Прочность на сжатие – от 1 до 3,2 МПа,
Газопроницаемость – до 200 единиц.
Таблица 12.Рассчетная ведомость стержневого отделения
№ п/п | Наименование отливки | Кол-во отливок в год | Кол-во стержней на 1 отливку | Масса стержней на 1 отливку, кг | Годовое количество стержней | |
шт. | тонн. | |||||
1 | 2 | 3 | 4 | 5 | 6 | 7 |
1 | Крышка СО | 25000 | - | - | - | - |
2 | Корпус СО | 30000 | 2 | 0,2 | 30000 | 6 |
3 | Улитка СО | 30000 | 1 | 0,15 | 30000 | 4,5 |
4 | Фланец СО | 30000 | - | - | - | - |
5 | Линейка СО | 28000 | - | - | - | - |
6 | Корпус вала шкива | 30000 | 1 | 1,1 | 30000 | 33 |
7 | Ступица РПН | 30000 | - | - | - | - |
8 | Втулка РПН | 26000 | 1 | 0,7 | 26000 | 18,2 |
9 | Втулка РПА | 28000 | - | - | - | - |
10 | Крыщкаполуфланца | 26000 | - | - | - | - |
11 | Полуфланец | 30000 | - | - | - | - |
12 | Ролик РПА | 15000 | 1 | 2,0 | 15000 | 30 |
13 | Крейцкопф РПА | 18000 | - | - | - | - |
14 | Сопло смесителя | 15000 | 1 | 1,8 | 15000 | 12,6 |
15 | Основное звено | 15000 | - | - | - | - |
16 | Замыкающее звено | 15000 | - | - | - | - |
17 | Начальное звено | 14000 | 2 | 2,2 | 28000 | 30,8 |
18 | Маховик СО | 15000 | - | - | - | - |
19 | Жернов СО | 14000 | 2 | 2,8 | 28000 | 39,2 |
20 | Фиксатор СО | 14800 | - | - | - | - |
21 | Кронштейн | 14000 | - | - | - | - |
22 | Вкладыш ЛРА | 12800 | 2 | 2,2 | 25600 | 28,2 |
23 | Корпус подшипника | 15000 | - | - | - | - |
24 | Шкив СБР | 14500 | - | - | - | - |
25 | Плита горелочная 1 | 15000 | 2 | 2,2 | 30000 | 33 |
26 | Плита горелочная 2 | 14800 | 1 | 2,4 | 14800 | 35,6 |
27 | Плита горелочная 3 | 14000 | 1 | 2,8 | 14000 | 39,2 |
28 | Ползун | 15000 | 1 | 1,2 | 15000 | 18 |
29 | Плита фартука | 14800 | - | - | - | |
30 | Плита нижняя | 15000 | - | - | - | |
31 | Патрубок переходной | 14000 | 1 | 1,2 | 14000 | 16,8 |
32 | Крышка люка | 15000 | - | - | - | - |
33 | Бандаж | 15000 | - | - | - | - |
Всего по 1 потоку с учетом брака 3% | 355,5 | |||||
34 | Барабан | 9600 | 4 | 12,0 | 38400 | 115,2 |
35 | Плита напольная кв. | 250000 | - | - | - | - |
36 | Плита напольная ш/г | 250000 | - | - | - | - |
37 | Втулка | 8800 | 1 | 2,8 | 8800 | 24,6 |
38 | Венец зубчатый | 9440 | - | - | - | - |
39 | Шестерня | 9220 | - | - | - | - |
40 | Кольцо сферическое | 9800 | - | - | - | - |
41 | Обойма | 12000 | - | - | - | - |
42 | Опора промежуточная | 9600 | - | - | - | - |
43 | Шпуля | 10000 | 1 | 2,6 | 10000 | 26 |
44 | Крышка АПК | 10000 | - | - | - | - |
45 | Крышка АКШ | 9600 | - | - | - | - |
46 | Корпус подшипника АТГ | 9600 | 2 | 3,4 | 19200 | 32,6 |
47 | Колодка | 9200 | - | - | - | - |
48 | Основание АТ | 8400 | - | - | - | - |
49 | Маховик | 9600 | - | - | - | - |
50 | Шкив СБ | 8600 | - | - | - | - |
51 | Ступица РН | 10000 | 1 | 1,2 | 10000 | 12 |
52 | Венец зубчатый СБР | 8700 | - | - | - | - |
53 | Втулка СРГ | 8200 | - | - | - | - |
55 | Траверса левая | 7200 | - | - | - | - |
56 | Траверса правая | 7600 | - | - | - | - |
57 | Корпус редуктора АТ | 5600 | 1 | 14,2 | 22400 | 80,6 |
58 | Диск секторный | 8000 | 4 | 6 | 32000 | 48 |
59 | Корыто | 7600 | - | - | - | - |
60 | Щека подвижная | 429 | - | - | - | - |
Всего по 2 потоку с учетом брака 3% | 292,6 | |||||
Итого стержней на программу | 431680 | 664,1 | ||||
Итого стержней на программу с учетом брака 3% | 444631 | 684,1 | ||||
Стержней массой менее 6 кг | 422231 | |||||
Стержней массой более 6 кг | 22400 |
5.2 Расчет оборудования для изготовления стержней
Для приготовленияхолоднотвердеющих смесей для стержней массой более
6 кг (стержень массой более 6 кг имеет только одна отливка из всей номенклатуры) применяем шнековый смеситель периодического действия модели СПД-1.Особенностью смесителя такого типа является наличие программируемого контроллера, позволяющего оператору гибко устанавливать требуемое количество смеси и регулировать её живучесть, варьируя дозу или марку отвердителя. Благодаря высокой частоте вращения смешивающих органов предотвращается налипание смеси и не требуется чистка камеры после каждого замеса. Преимуществом смесителя СПД-1 является возможность приготовления смесей с небольшим циклом твердения, резкое сокращением потерь смеси, особенно при необходимости подачи ее небольшими порциями или при продолжительных остановках смесителя в процессе работы.
Технические характеристики смесителя
периодического действия СПД-1
Масса замеса, кг: 50-150
Число оборотов вала, об/мин. 300
Длительность приготовления порции смеси - не более 50секунд
Подготовленная в смесителе СПД-1 стержневая смесь выдается в стержневые ящики и уплотняется на вибростоле модели 21422.
Для изготовления основного количества стержней (массой менее 6 кг) применяем восьмипозиционный карусельный пескострельный автомат модели 4716А (рис3) с вертикальной плоскостью разъема ящика и массой выстрела до 6 кг. [4]
Требуемое количество стержневых автоматов определяем по формуле:
Р1 = , (3)
гдеВ – количество стержней в год, шт.;
Кн – коэффициент неравномерности потребления стержней,
Кн = 1-1,3; Фд – годовой действительный фонд времени оборудования, ч,
Nр- расчетная производительность оборудования.
Р1 = =0,65
Принимаем 1 автомат модели 4716А.
Коэффициент загрузки рассчитываем по формуле (4).
Кз= = 0,65
Коэффициент загрузки стержневого оборудования = 0,65, что не превышает коэффициент загрузки формовочного оборудования = 0,7. [1]
В качестве вспомогательного оборудования в стержневом отделении используем: поддоны, стеллажи, передвижные и стационарные этажерки для хранения стержней и стержневых каркасов. Предусматриваем рабочее место для сварщика-сборщика каркасов. Количество столов, стеллажей, этажерок выбираем по мере необходимости.
5.3 Схема работы стержневого отделения
Подача свежего песка в стержневое отделение осуществляется по ленточному транспортеру, смола и отвердитель подаются в специальной таре и устанавливаются рядом со смесителем и стержневым автоматом..
Стержневые ящики устанавливаются на карусель с помощью тельфера грузоподъемностью 0,5 т. Мелкие стержневые ящики устанавливаются вручную.
Готовые стержни устанавливаются на этажерки или укладываются на поддоны. Мелкие стержни хранятся на стеллажах. Транспортировка стержней в формовочное отделение на участок простановки стержней производится вручную с помощью передвижных этажерок или на передаточной электротележке.
Возможна транспортировка мостовым краном на специальных поддонах, после использования стержней поддоны возвращаются на стержневой участок.
Стержневой участок располагается в одном пролете вместе с формовочным отделением.
А-А |
|
1- основание карусели; 2- механизм поджима ящика; 3- пескострельный резервуар; 4- смесеприготовительный агрегат; 5- воздушное сопло для очистки ящика сжатым воздухом; 6 – поворотный механизм; 7- стержневые ящики (8 позиций); 8 – карусель.. [3]
Рисунок 4 - Стержневой автомат 4716А
6 Проектирование смесеприготовительного отделения
В чугунолитейном цехе приготавливают формовочные и стержневые смеси. Формовочные и стержневые смеси - это основные компоненты технологического процесса изготовления отливок в разовых песчаных формах.
Применяемые формовочные смеси
В качестве формовочной смеси для производства чугунных отливок по сырому используем единую смесь.
Единая смесь: оборотная смесь (92,5%), свежий песок (6%),бентонит(1%), каменный уголь (0,5%).
Характеристика смеси:
Вид формы – сырая песчано-глинистая форма
Зерновой состав формовочного песка – (3К2О203),
Общее глиносодержание – (6-8%),
Газопроницаемость – (40 – 100),
Прочность на сжатие – (0,30 – 0,70) ∙ 105 Па (кгс/см2),
Влажность – (4,0 – 5,5%).
В случае необходимости изготовления отливок высокой точности, возможно использование облицовочной смеси.
Облицовочная смесь состоит из оборотной смеси (75%), свежих материалов (22%), каменного угля (3%).
При изготовлении песчано – глинистой смеси используется следующая последовательность ввода компонентов в смеситель: песок → вода (перемешивание) → бентонит (перемешивание) → добавки (перемешивание). При такой последовательности формирование глинисто – водной оболочки на зернах песка происходит более интенсивно за счет процесса налипания глинистых частичек на увлажненную поверхность зерен песка, сокращающего период их агрегатирования в комочки[1].
6.1Выбор и расчет оборудования
Общий годовой расход формовочных смесей в мелкосерийном и серийном производстве проектируемого цеха определяется расчетом исходя из размеров и числа изготовляемых форм для всей номенклатуры отливок. Результаты расчетов сводятся в ведомость расхода формовочной смеси (таблица 13).
Имея годовой расход формовочных смесей по размерам форм и их составы, рассчитываем расходы компонентов с учетом потерь при транспортировке и в процессе формообразования (таблица 14).
В расчетах принимаем объемную массу нормально уплотненной формовочной и стержневой смеси равную1,65т/м3, чугуна – 7,2 т/м3. [1]
Основным компонентом формовочной смеси является оборотная смесь. В связи с тем, что все остальные компоненты (песок и бентонит) подаются в смесеприготовительное отделение готовыми к применению, то технологический процесс смесеприготовления начинается с подготовки оборотной смеси.
Оборотная смесь проходит через магнитный сепаратор, вибросито и далее подается в катковые смесители – бегуны.
Впроектируемом цехе целесообразно применить для автоматических линий комплексную систему смесеприготовления.
Таблица 13 – Расчетная ведомость расхода формовочной смеси
Размер формы, мм | Количество форм в год, шт | Объем одной формы, м3 | Расчетный объем, м3/год | Расчет формовочной смеси с учетом потерь, м³/год | |||
Всех форм за год | Металла в формах за год | Стержней в формах за год | Формовочной смеси в формах за год | ||||
500×400×200 | 468329 | 0,08 | 37466 | 910,6 | 215,4 | 36340 | 59961 |
1000×800×400 | 431657 | 0,64 | 276261 | 3381,2 | 177,3 | 272703 | 449960 |
Итого: | 313727 | 4291,8 | 392,7 | 309043 | 509921 |
Таблица 14 – Расчет компонентов смеси на годовую программу
Наименование смеси | Расход компонентов | |||||||
Оборотная смесь | Кварцевый песок | Каменный уголь | Бентонит | |||||
% | Куб.м/год | % | Куб.м/год | % | Куб.м/год | % | Куб.м/год | |
Единая формовочная смесь | 92,5 | 471677 | 7 | 35694 | 0,5 | 2550 | 1 | 5099 |
Требуемую комплексную систему подбираем исходя из её производительности по формуле: [15]
1 = , (3)
гдеВ – годовой объем смеси, м³,
Кн – коэффициент неравномерности потребления, Кн = 1,0 -1,2,
Фд – годовой действительный фонд времени оборудования, ч,
Nр- расчетная производительность оборудования, м³/ч,
Np = 509921*1,0:5900=85, следовательно требуется комплекс производительностью не менее 85 м3/час, принимаем комплекс К100П в составе 4 бегунов модели15328 общей производительностью 100 м3/час.
Коэффициент загрузки рассчитываю по формуле (4).
Кз= = 0,85, что приемлемо.
6.2 Схема работы смесеприготовительного отделения
Свежий подготовленный песок в количестве 140 тонн в сутки завозят автотранспортом и пересыпают в бункера. Бентонит (20 т в сутки) и песок поступают в готовом к использованию виде в герметичных упаковках «биг-бэг» массой 1т. Жидкие вещества–смола и отвердитель хранятся в баках, герметично закрытых.
Из бункеров свежий песок по ленточным транспортерам передается в смесеприготовительное и стержневое отделения.
Для освежения формовочной смеси песок передается по системе ленточных транспортеров и элеватору к бегунам.
Приготовленная формовочная смесь транспортируется в бункера-отстойники, где смесь вылеживается с целью выравнивания свойств. Из бункеров-отстойников системой ленточных транспортеров смесь подается в расходные бункера формовочного оборудования, при этом с помощью специальных установок (лопастных аэраторов-разрыхлителей) она разрыхляется для улучшения ееформуемости.
7 Проектирование термообрубного отделения
Отливки выбитые из литейных форм, проходят определенный по длительности цикл охлаждения (таблица 14), после чего их передают в термообрубное отделение, где путем проведения ряда операций улучшают их физико-механические свойства и придают им товарный вид. [1, 2]
Таблица 14 - Нормы времени охлаждения отливок после выбивки из форм
Масса отливки, кг | Время охлаждения, ч |
До 10 | до 1,0-2,5 |
10-30 | 1,2-1,5 |
31-50 | 1,5-2,2 |
51-100 | 2-3 |
7.1 Распределение отливок по операциям
К операциям относят очистку, обрубку, обточку отливок, их термическую обработку, заварку или заделку шпатлевками поверхностных дефектов..
7.2 Выбор и расчет оборудования
После выбивки отливки подвергают обрубке и очистке. Отливки относящиеся к первой группе (мелкие) очищают от пригоревшей земли и стержней с частичным удалением литников в проходном галтовочном барабане.
Тонкостенные отливки подвергаются ручному удалению литников и стержней с помощью пневматических молотков модели МО 21.
Более крупные отливки подвергаются очистке в дробеметном барабане.
Заточку наплывов, остатков питателей производят для мелких отливок - на стационарных заточных станках, для более крупных – при помощи ручных заточных машинок.
Проходной барабан для линии КЛ22821должен быть один, поэтому подбираем марку барабана по его производительности:
Р1 = , (3)
гдеВ = 6365,3*1,03 т. – годовое количество обрабатываемых мелких отливок (с учетом брака-3%);
Кн – коэффициент неравномерности потребления, Кн = 1,2…1,4;
Фд – годовой действительный фонд времени оборудования, ч;
Nр- расчетная производительность оборудования, т/ч.
Р1 = = 0.68
Коэффициент загрузки рассчитываю по формуле (4).
Кз= = 0, 68
Принимаю 1 проходной галтовочный барабан для мелких отливок, модели 41212 с производительностью 3 т/ч при трехсменном режиме работы.
Объем отливок 2 потока составляет 23635,7т.
Требуемое количество дробеметных барабанов определяем по формуле (3):
Р1 = = 2,6
Коэффициент загрузки рассчитываю по формуле (4).
Кз= = 0, 86.
Принимаем 3 дробеметных барабана модели 42233 с производительностью 2,0 т/ч и наибольшей массой загрузки 800 кг.для отливок 2 технологического потока при трехсменном режиме работы.
Для удаления заливов и остатков литников на отливках массой менее 10 кг применяю стационарные заточные станки модели ЗМ636 в количестве 4 шт. , для более крупных - переносные установки с гибким валом модели 3382.
Удаление заливов, швов и других неровностей на поверхности отливок, а также вырубку дефектов для заварки обычно выполняют пневматическими рубильниками - молотками модели МО21, МО22. Молотки МО21 и МО22имеют специальную виброгасящую насадку и направленный выхлоп воздуха, что обеспечивает минимальное вредное воздействие на человека.
Основными методами исправления дефектов отливок являются декоративная заделка мелких поверхностных раковин пастами, а также заварка.
Проектом предусматривается получение требуемой микроструктуры металла отливок в литом состоянии, однако для исправления брака литья по микроструктуре или для получения специальных свойств металла предусматриваем возможность проведения термической обработки, для чего принимаем 2 термические колпаковые электропечи модели 2145 с производительностью 3,5 т/ч. [1, 3]
7.3 Планировка и схема работы термообрубного отделения
Термообрубное отделение располагается в двух пролетах шириной 24 м. Выбитые отливки транспортируются на термообрубной участок по пластинчатому транспортеру или в унифицированной таре при помощи электротележкигрузоподъемностью10т и мостового крана 15/3. В дальнейшем отливки сортируются по массе и распределяются по видам обрубки.
Для передачи тележек с отливками в термическую печь предусматривается транспортная платформа, на которую отливки загружаются с помощью мостового крана в специальной таре.
Отливки, прошедшие полный цикл обработки в термообрубном отделении, на специально отведенном участке предъявляются контролерам ОТК.
Отливки, прошедшие ОТК передаются на склад годного литья.
8 Проектирование складов формовочных и шихтовых материалов
Все свежие формовочные материалы поступают на цеховой склад в готовом к использованию виде автотранспортом. Свежий песок разгружается в бункера. Бентонит в упаковках по 1т складируется на площадке.
Подготовленные шихтовые материалы завозятся автотранспортом в количестве односменной потребности и хранятся на специальной площадке в непосредственной близости от плавильного отделения в закромах. Из закромов шихта мостовым краном 15/5 с магнитной шайбой набирается в самораскрывающиеся корзины, подогревается газовыми горелками и передается в печи. Для дозирования и навески шихты применяют платформенные весы и крановые динамометры.
9 Проектирование вспомогательных отделений цеха
Вспомогательные службы литейных цехов включают в себя следующие подразделения: ремонтную службу цеха, предназначенную для текущего ремонта и обслуживания оборудования, экспресс-лабораторию для оперативного контроля химического состава жидкого чугуна, цеховые кладовые и подсобные помещения.
9.1 Ремонтно – механическое отделение
В действующей системе планово-предупредительных ремонтов (ППР) предусмотрено централизованное выполнение службами завода капитального, среднего и малого ремонта механического и электротехнического оборудования, КИП и автоматики, а также ремонта инструмента и оснастки. Цеховая служба обеспечивает только межремонтное обслуживание всего перечисленного оборудования и приборов цеха в течение всего времени работы оборудования (во всех сменах), в связи с чем функции и состав этой службы значительно упрощаются и сокращаются.
Проектирование цеховой ремонтной службы включает в себя определение числа дежурных слесарей, электриков, слесарей КИП, газовщиков, сантехников и т.д. В зависимости от количества ремонтного персонала определяется площадь помещений, занимаемых ремонтными службами из расчета 4-5 м2на человека и
10 м2 на каждый станок[1].
Принимаем следующий состав ремонтной службы (для каждой смены):
Слесари – 4 чел.
Электрики - 4 чел.
Слесарь – сантехник – 1 чел.
Слесарь КИП – 1чел.
Станочный парк принимаем в количестве 3-х станков – сверлильный, токарный и фрезерный. Таким образом минимальная площадь мастерской ремонтной службы составит 6 чел * 5 м2 + 3станка * 10 м2 = 60 м2.
Принимаем площадь мастерской 72 м2.
9.2 Экспресс – лаборатории.
Металлургическая экспресс – лаборатория предназначена для систематического оперативного контроля химического состава выплавляемого металла. В целях получения высококачественного расплава чугуна, особенно при его последующем переделе на высокопрочный чугун с шаровидным графитом, следует отбирать не менее 3-х проб от каждой плавки и определять до 12 элементов в каждой пробе, для чего предусматриваем оснащение экспресс-лабораторииквантометром «КВАНТОВАК». Исходя из трудоемкости 1 анализа в 0,4-0,7 человекочаса (в среднем-0,55) [1] и 8-ми плавок в смену необходимое количество лаборантов составляет:
0,55*3*8 = 13,2 чел/час : 8 час. = 1,65 = 2 человека в смену.
Земельная лаборатория предназначена для контроля свойств формовочных и стержневых смесей, для чего оснащается приборами для ситового анализа песка, определения прочности, газопроницаемости, осыпаемости и влажности смесей.
Площадь лаборатории принимаем 36м2.
Для сокращения времени передачи проб лаборатория располагается в непосредственной близости от рабочей площадки печей. Результаты анализов чугунапередаются на монитор, расположенный возле печей.
9.3 Цеховые кладовые
В цеховых кладовых хранят запчасти, вспомогательные материалы, инструменты, ветошь, бумагу и прочие расходные материалы.
Площадь общецеховых кладовых принимается по укрупненному нормативу из расчета 1,3-1,7 м2 на 1000 тонн выпуска литья[1]. Принимаем площадь цеховой кладовой 40 м2, площадь кладовой ремонтной службы– 40 м2 . Число кладовщиков составляет 1 человек в смену.
9.4 Комнатыы мастеров
Комнаты мастеров располагаются в основных отделениях цеха на площадях, не предназначенных для производственных операций. В этом же помещении происходит прием и сдача смены рабочим персоналом, совещания и решения проблем цеха. Принимаем площадь комнат мастеров отделений по 18-20м2.
10. Объемно – планировочное решение здания цеха
Проектируемый цех одноэтажный, двухпролетный, ширина каждого пролета- 24 метра.
Длина цеха составляет по осям колонн 138 м, ширина 48м. Шаг колонн 6м. Высота пролета составляет 9,6 м. Площадь цеха – 6624 м2.
Каркас здания сборный железобетонный, фундамент и фундаментные блоки также железобетонные.
Кровля выполнена без фонарей, на фермах уложены железобетонные перекрытия, полы выполнены из бетона и покрыты чугунными плитками.
Рядом с цехом построена открытая эстакада. Помещение АБК площадью
1300 м2 (по укрупненному нормативу 2,6 м2 *477 человек работающих = 1296 м2) размещено рядом с цехом и соединено с ним отапливаемым переходом.
В качестве теплоносителя для цеха используется перегретая вода, в самом цехе применяются калориферы с подогревом приточного воздуха.
Вентиляцию в цехе применяют естественную, общеобменную и местную. Общеобменная вентиляция поддерживает воздушную среду во всем объеме помещения. Местная вентиляция предусматривает подачу воздуха в некоторые ограниченные места рабочей зоны помещений. Местную вытяжную вентиляцию применяю в виде местных отсосов, укрытий, зонтов. Перед выбросом в атмосферу технологические выбросы и воздух проходят через сухую или водяную фильтрацию.Для нужд цеха предусмотрено снабжение технической и питьевой водой.В цехе предусмотрены системы канализации: хозяйственно-бытовая, ливневая и промышленная.
11 Безопасность жизнедеятельности
11.1 Анализ условий труда на проектируемом объекте.
Основная цель анализа безопасности – выявление причин возникновения потенциальных опасностей и разработка мероприятий, исключающих или существенно понижающих риск возникновения нештатных ситуаций в процессе производственной деятельности. Проектируемый цех оснащен самыми различными видами технологического оборудования. Его использование облегчает труд человека, делает его производительным. Однако в ряде случаев работа этого оборудования связана с возможностью воздействия опасных и вредных производственных факторов. К числу опасных производственных факторов относят те, воздействие которых может привести к травмам или к другим внезапным и резким повреждениям здоровья работающих. Источниками таких факторов являются машины и механизмы, их движущиеся и вращающиеся элементы, электрические машины, транспортные средства, грузоподъемные механизмы, расплавленные материалы, и многое другое.
К вредным факторам относятся такие, воздействия которых наработающих могут привести к заболеванию или снижению их работоспособности. Факторы отрицательно влияющие на санитарно-гигиенические условия труда. Многие из них приводят к ухудшению состояния не только производственной, но и окружающей воздушной среды. К ним относятся: неудовлетворительные метеорологические условия (температура, влажность и другие), ядовитые (токсичные) вещества, производственная пыль, шумы, вибрация, вредные излучения (ионизирующие, тепловые, электромагнитные), плохое освещение, вредные биологические и психофизические факторы[6, 7].
Безопасность труда в механизированном производстве также обусловлена степенью безопасности оборудования и технологических процессов. Производственное оборудование должно обеспечивать безопасность работающих при монтаже (демонтаже), вводе в эксплуатацию и эксплуатации при соблюдении требований по ГОСТ 12.2.003-91[5], предусмотренных эксплуатационной документацией. Анализируя проектируемый цех, представляю перечень опасных и вредных производственных факторов по основным технологическим операциям.
Таблица 15 – Опасные и вредные производственные факторы
Выполняемая работа | Применяемое оборудование, материалы, вещества | Опасный или вредный производственный фактор | Общие мероприятия по защите или нормализации |
1. Смесеприготовительное отделение | |||
Приготовление формовочной и стержневой смеси | Сито барабанное, бегуны, сушило песка и глины, песок, формовочная смесь | Подвижные механизмы, электрический ток, шум, вибрация, загазованность, запыленность | Защитные кожухи, звуковой и световой сигнал, защитное заземление, экранирование шума, естественная и механическая вентиляция |
2. Формовочное отделение | |||
Приготовление стержней и форм, доставка смеси | Краны, формовочные машины, пескомет, бункера, питатели, трамбовки, смеситель, формовочные и стержневые смеси | Опасность механических травм, вибрация, шум, запыленность, поражение электрическим током | Ограждение, звуковые и световые сигналы, виброизолирующий фундамент, средства индивидуальной защиты, местная вытяжная вентиляция, аварийное автоматическое отключение, заземление |
3. Плавильное отделение | |||
Загрузка шихты Плавка металла Выпуск металла из печи | Индукционные печи, мостовой кран, завалочная бадья, шихта, суточные бункера с ферроматериалами Печь, шихта, ферросплавы, жидкий металл Печь ИЧТ – 6, ковши, жидкий металл, шлак | Запылённость, шум, вылет кусков шихты Выделение дыма, газов, повышенная температура, избыточное тепло Избыточное тепловое излучение, выброс металла при сливе | Звуковые сигналы, местная вытяжная вентиляция, средства индивидуальной защиты, комплексная автоматизация Удаление газов от электропечи, механизация процессов, воздушное охлаждение воздуха кондиционером, беруши Периодическое увлажнение пола в зоне облучения в периоды между разливкой стали Индивидуальные средства защиты |
Таким образом, на пректируемом объектена рабочих воздействуют следующие опасные и вредные производственные факторы, классифицируемые в соответствии с ГОСТ12.0.003-74 [6, 7].
Опасные факторы:
· Опасность механическоготравмирования
· Опасность поражения электрическим током
· Опасность отравлений.
Вредные факторы:
· Микроклимат производственных помещений, не соответствующий санитарным нормам.
· Недостаточное освещение.
· Воздействие шума и вибрации.
11.2Мероприятия по обеспечению безопасности труда
Общие направления по улучшению условий труда в цехе.
Основными мероприятиями по улучшению условий труда являются: автоматизация и механизация технологических процессов, применение современных безопасных технологических процессов и исходных материалов, а также оборудования, которое не является источником опасных или вредных факторов. Большое значение имеет рациональное размещение оборудования и организация рабочих мест, обозначение опасных зон, применение быстродействующих средств локализации аварийных ситуаций. Однако полностью исключить действие опасных и вредных факторов на современном этапе развития чугунолитейного производства невозможно, поэтому в проектируемом цехе применяются индивидуальные и коллективные средства защиты работающих.
ГОСТ12.4.011-89 [8] распространяется на средства коллективной и индивидуальной защиты, применяемые для предотвращения или уменьшения воздействия на работающих опасных и вредных производственных факторов, устанавливает их классификацию и общие требования к средствам защиты. Средства защиты предназначены для предотвращения или уменьшения воздействия опасных и вредных факторов.
В целях нормализации воздушной среды производственных помещений впроектируемом цехе предусмотрены устройства для общеобменной и местной вентиляции, очистки и кондиционирования воздуха; отопления.К средствам нормализации освещения производственных помещений и рабочих мест относятся источники естественного света в виде световых проемов и искусственного – в виде осветительных приборов.
Для защиты от повышенного уровня шума применяются звукоизолирующие и звукопоглощающие ограждения.
Средства индивидуальной защиты следует использовать в тех случаях, когда безопасность работ не может быть обеспечена конструкцией оборудования, организацией производственных процессов, архитектурно-планировочными решениями и средствами коллективной защиты.
К средствам индивидуальной защиты, применяемым в проектируемом цехе, относятся: спецодежда, спецобувь, рукавицы, перчатки, респираторы, очки и маски, каски и подшлемники, шумозащитные наушники и вкладыши-беруши.
Технологический процесс изготовления отливок должен соответствовать требованиям ГОСТ 12.3.027-2004 [9] и «Санитарным правилам для литейного производства» [10]
В технологическом процессе литейного производства возможно воздействие многих опасных и вредных факторов по ГОСТ 12.0.003-74 [4].
Вредные вещества по характеру воздействия, по степени опасности и пути проникновения в организм классифицируются по ГОСТ 12.1.007-76 [6, 7].
Защита окружающей среды осуществляется следующими мероприятиями:
- размещение плавильного отделения с подветренной стороны здания;
- эффективная очистка от пыли и вредных составляющих отходящих от печей газов;
- автоматизация и механизация процессов плавки, загрузки шихты;
- местная и обще обменная вентиляция в местах интенсивного теплового излучения.
Пыль литейного цеха в основном мелкая, значительную часть пыли составляет диоксид кремния, выделяющийся при сушке песка, приготовлении формовочных и стержневых смесей, выбивке и очистке отливок.
Механизация и автоматизация этих процессов, а также устройство местной вентиляции нормализует условия труда в заливочно-формовочно-выбивном отделении.
Устройство отсосов предусматривается в местах формовки, заливки, выбивки форм. Для выбивных установок применяются накатные звукопоглощающие камеры, для операторов - шумонепроницаемые кабины с двойным остеклением и приточной вентиляцией.
В стержневом отделении предусматривается местная вытяжная вентиляция и средства индивидуальной защиты.
Участком с вредными условиями труда является термообрубное отделение, характеризующиеся пылевыделением при очистке отливок, шумом, создаваемым галтовочными и дробеметными барабанами, возможностью травм от ударов кусочками обрубаемого металла или разорвавшегося абразивного круга, а также интенсивным тепловым излучением при термообработке отливок.
Для нормализации условий труда предусмотрены следующие меры:
- галтовочный и дробеметный барабаны изолируются в звукопоглощающих укрытиях и снабжаются местными пылеотсосами;
- термическая печь снабжается местной вентиляцией, обеспечивающей отбор газов;
- рабочие отделения обеспечиваются средствами индивидуальной защиты (очки, маски, респираторы, беруши, шумозащитные наушники, брезентовые фартуки и рукавицы)
Курение в цехе разрешено только в специально отведенных местах[6, 7].
12 Экономическая часть
Расчет себестоимости тонны металлазавалки принимаем по данным таблицы 7.
Расчет себестоимость тонны жидкого чугуна представляем в виде таблицы 16.
Статьи расхода | Годовой расход, т. | Цена за 1 т., руб. | Затраты на 1 тонну жидкого металла, руб. |
Металлозавалка | 24583 | ||
Топливо и энергии: 1. Природный газ, тыс./м3 2.Электроэнэргия,. кВт×час | 3979 28592 | 4500 2,80 | 432 1930 |
Транспортные расходы | 1159 | ||
Основная з/пл. производственных рабочих | 243 | ||
Дополнительная з/пл. | 36 | ||
Отчисления на соц. страх 30 % | 73,3 | ||
Расходы на содержание и экспл. оборуд. | 973 | ||
Цеховые расходы | 243 | ||
Цеховая себестоимость | 29639 |
Таблица 16 - Калькуляция себестоимости 1 тонны жидкого чугуна
Примечание:
· транспортные расходы, расход газа и электроэнергии принимаем по данным базового цеха;
· цеховые расходы устанавливаем в размере 100 % к основной заработной плате производственных рабочих по плавильному отделению;
· расходы на оборудование устанавливаем в размере 400 % от основной заработной платы производственных рабочих по плавильному отделению.
12.1 Себестоимость изготовления 1 тонны годных отливок
Таблица 17 – Калькуляция себестоимости изготовления 1 тонны отливок из чугуна при годовом выпуске 30000 тонн
Статьи расхода | Годовой расход, т | Расход на 1 тонну годного литья, руб. |
1. Жидкий металл | 41480 | 29639 |
2. Возвратные отходы (-) | -11480 | -4592 |
3. Годное литье | 30000 | |
4.Вспомогательные материалы | 4000 | |
5. Основная з/пл. произв. рабочих | 824 | |
6. Дополнительная з/пл. | 124 | |
7. Отчисление на соц. страх(30%). | 248 | |
8. Расходы на оборудование | 3295 | |
9. Расходы на передел | 33538 | |
10. Общезаводские расходы | 824 | |
11. Производств.себестоимость | 34362 | |
12. Внепроизв. расходы | 17181 | |
13. Полная себестоимость | 51543 |
Примечание:
· вспомогательные материалы принимаю по заводским данным 4 тыс.руб./т.
· расходы на содержание и эксплуатацию оборудования принимаю в размере 400% от основной заработной платы производственных рабочих;
· общезаводские расходы составляют 100% от основной заработной платы производственных рабочих;
· внепроизводственные расходы принимаем по заводским данным 50 % от производственной себестоимости.
12.2Экономические показатели
Таблица 18 – Экономические показатели
№ п/п | Наименование показателей | Проект |
1. | Годовой выпуск литья, тонн | 30000 |
2. | Стоимость тонны металлозавалки, руб/тонна | 24583 |
3. | Себестоимость тонны жидкого чугуна, тыс.руб. | 29639 |
4. | Себестоимость тонны годного литья | 51543 |
13 Технологический процесс изготовления отливки «КорпусАКШ».
13.1 Требования, предъявляемые к детали
Отливка II группы качества. Точность 10-5-14-9 См 0,8 ГОСТ 26645-85.
«Корпус АКШ.03.603» изготавливается литьем в песчано-глинистую сырую разовую форму из смеси с влажностью от 3,5 до 4,5% и прочностью от 60 до 120 кПа (от 0,6 до 1,2 кг/см2), с уровнем уплотнения до твердости не ниже
70 единиц[12,14].
Класс размера точности – 10;
Степень коробления элементов отливки – 5;
Степень точности поверхностей отливки – 14;
Шероховатость поверхностей отливки Ra, мкм, не более 40;
Класс точности массы отливки – 9;
Ряды припусков на обработку отливки – 8;
Допуски размеров отливки, мм: наибольший ± 4,40
средний ± 3,6
наименьший ± 2,8
Допуск массы отливки – 3,2%;
Припуски на механическую обработку, мм: верх - 5
низ - 3
бок - 4
Отливка изготавливается из высокопрочного чугуна марки ВЧ50. Чугун обладает высокой износостойкостью, малой чувствительностью к концентраторам напряжения. Высокопрочный чугун более технологичный материал, чем сталь, его расплав обладает более высокой жидкотекучестью и меньшей усадкой.
Таблица19 - Химический состав ВЧ-50 (ГОСТ 7293-85)
Марка | Содержание элементов | ||||
C | Si | Mn | P | S | |
ВЧ - 50 | 3,2-3,7 | 1,9-2,9 | 0,3-0,7 | до 0,10 | до 0,02 |
К механическим свойствам относятся прочность, твердость, упругость, пластичность и другие. К физическим и литейным свойствам относятся плотность, теплопроводность, электропроводность, температура плавления.
Таблица 20 – Механические свойства ВЧ -50 (ГОСТ 7293-85)
Марка | σв, МПа | σ0,2, МПа | δ ,% | НВ |
ВЧ - 50 | 500 | 320 | 7 | 153 - 245 |
13.2 Оценка технологичности конструкции детали
Характеристика детали.
Целью технологии литейного производства является получение отливки гарантированного качества: высокий уровень и минимальный разброс по прочности, повышенная точность размера.
Литая деталь должна иметь:
- простые и прямолинейные общие контуры, облегчающие изготовление, как литейной оснастки, так и самой отливки;
- рациональную толщину стенок в различных сечениях, возможность заполнения литейной формы жидким металлом без образования дефектов;
- рациональные формы различных переходов, сопряжения, ребер жесткости и других элементов, способствующих снижению внутренних напряжений и устранению дефектов усадочного характера;
- конструктивные уклоны;
Отливка изготавливается из сплава марки ВЧ - 50
Масса отливки 40 кг.
Габаритные размеры: длина – 240мм
диаметр –280мм
Средняя толщина стенки отливки 10 мм.
13.3 Выбор способа изготовления отливки
Отливка «Корпус АКШ» изготавливается в сырой песчано-глинистой разовой форме. Данный метод наиболее экономичен для мелкосерийного производства. Не требуется площадь для сушильных агрегатов, дополнительный расход топлива. Сокращается цикл изготовления отливки и снижается ее себестоимость.
13.4 Проектирование технологии формы
Выбор положения отливки в форме при формовке и заливке.
Отливка располагается в двух полуформах в горизонтальном положении. Такое расположение облегчает формовку и обеспечивает направленное затвердевание металла, при этом обрабатываемые поверхности расположены вертикально. Отливка имеет внутреннюю полость, которая образуется одним стержнем. Выбранное положение обеспечивает возможность проверки размеров полости формы при сборке, а также надежное крепление стержня[14].
Выбор поверхности разъема модели и формы.
Форма и модель имеет одну поверхность разъема, которая обеспечивает удобное изготовление и сборку литейной формы. Модель легко извлекается из формы. Выбранный разъем обеспечивает простоту изготовления модели, а при формовке в парных опоках - наименьшую суммарную высоту опок.
Определение контура стержня, размера стержня, конструкции его знака, способа фиксации, положения в форме, величины уклонов, зазоров между знаком модели и стержнем.
Стержень (смотри рисунок 4) выполняется целым, что обеспечивает точность полости отливки, имеет надежную опору – знаки. Знаковые части стержня обеспечивают точность установки стержня в форму. Конфигурация стержня выполняется по внутреннему контуру детали с учетом зазоров и припусков на механическую обработку/
Рисунок 4 – Положение отливки в форме
При горизонтальном расположении стержня и его четкой фиксации в осевом направлении знаки имеют торцевые фиксаторы.
Размеры знаков стержня принимаем по ГОСТ 3606 – 92.
Длина горизонтальных знаков 55мм
Высота нижнего знака 35 мм
Формовочные уклоны знаковых частей: верхний 10 о
нижний 7˚
Зазоры между знаковыми поверхностями формы и стержня,
верх 0,5мм
низ 0,6мм
13.5 Проектирование модели
Выбор материала, определение припусков на механическую обработку.
Для изготовления детали в условиях массового производства используется металлический модельный комплект из алюминиевого сплава АК5М2, который обеспечивает точность отпечатка, прочность модели.
При разработке модельного комплекта размеры модели пересчитываются с учетом усадки сплава, точности исполнения и шероховатости поверхности.
Припуски на механическую обработку назначаем по ГОСТ 26645-85, мм:
верх – 5
низ – 3
бок – 4
Выбор величины формовочных уклонов.
Вертикальные стенки модели выполняются с уклоном, чтобы при ее извлечении форма не разрушалась. Формовочные уклоны на обрабатываемых поверхностях выполняются сверх припуска на механическую обработку по ГОСТ 3212-92, в зависимости от высоты формообразующей поверхности. На не обрабатываемых поверхностях отливки, не сопрягаемых по контуру с другими деталями, выполняются за счет увеличения или уменьшения размеров отливки[14].
Припуск на усадку зависит от вида сплава, массы и размеров отливки. Припуск на усадку ВЧШГ принимаем 2 %.
Изготовление модели
Технологический процесс изготовления оснастки заключается в изготовлении деревянной промодели, по которой получаем металлическую модель, обработке модельного комплекта, сборке модельного комплекта и монтаже на плитах, проверки и отладке модельного комплекта. Модели и стержневые ящики – основная оснастка при изготовлении отливок.
Металлические модели и стержневые ящики получаем литьем в песчаные формы по деревянным моделям, которые и называются промоделями. Стержневой ящик изготовлен облегченным с целью экономии металла. Для придания прочности на не рабочих сторонах изготовлены ребра жесткости. Для упрощения технологии ящик изготовлен разборным, но при этом обеспечено жесткое крепление между собой отдельных элементов конструкции, фиксация которых обеспечена контрольными штифтами.
Рисунок 5 – Схема модели
13.6 Выбор типа и расчет размеров литниковой системы
Принимается горизонтальная нормальная литниковая система. Литниковая система состоит из литниковой воронки 1, стояка 2, шлакоуловителя 3, питателей 4.
Рисунок 7 – Схема литниковой системы
Площадь минимального сечения литниковой системы при заливке формы из поворотного ковша рассчитывается по формуле Б.Озанна:
∑ Fмин. = ,(5)
где G= 266 кг-металлоемкость формы (при среднем для высокопрочного чугуна выходе годного 60%), кг;
µ =0,32 - коэффициент расхода литниковой системы;
τ – продолжительность заливки формы, сек;
Нр – средний расчетный напор металла, см.
Расчет продолжительности заливки производим по формуле К.А Соболева,
Г.Н Дубицкого:
τ = , (6)
где S – коэффициент, учитывающий жидкотекучесть сплава и тип литниковой системы, S = 1,5;
δ – толщина стенки отливки, δ = 12 мм;
G – металлоемкостьформы,кг
τ = 1,5 = 21 с.
Расчет среднего гидростатического напора определяется по формуле Диттерта:
Нср = Но – Р2/2С, (7)
где Но – высота от верха стояка до уровня подвода расплава в форму, см;
Р – высота отливки над уровнем подвода расплава в форму, см;
С – общая высота отливки по положению в форме, см;
Нср. = 20 – 142/ 2∙28 = 16,5см.
Площадь минимального сечения литниковой системы при заливке форм из поворотного ковша:
∑ Fмин. = …………………………………………………………………………(8)
где G – масса отливок в форме, кг
∑ F мин. = = 31 см2
Принимаем соотношение площадей сечения элементов литниковой системы:
Fст. : ∑ Fшл. : ∑ Fпит. = 1,0 : 1,1 : 1,2
Fшл =ΣFпит×1,1 = 31×1,1 = 34,1 см²
Fcт = 31×1,2 = 37,2 см²
Fст. = π ∙ d2 / 4, откуда d = 1,13 ∙ = 1,13 ∙
= 6,3 см
Размер литниковой воронки: dв.в = hв = 3 ∙ d = 3 ∙ 63 =190мм;
Размер металлоприемника: hм.п. = 1,2 ∙ d = 1,2 ∙ 63 = 76мм
Радиус зумпфа r = 0,625 ∙ 63 = 69 мм;
Размеры шлакоуловителя: Fшл =ΣFшл. /2 = 34 : 2 = 17 см²
Принимаем: ширина основания – 43 мм
Верхнее основание- 35 мм
Высота - 43 мм
Размеры питателя: Fпит =ΣFпит. / 4 =31 : 4 = 8 см² (9)
Принимаем: ширина основания – 40мм
Верхнее основание- 34 мм
Высота - 20мм
Определяем размеры прибылей:
1) Dпр =2,25 dуз , (10)
dуз – диаметр узла питания,мм; в данном случае равен диаметру окружности, вписанной в наибольшую толщину стенки отливки = (210-108) : 2 = 51мм
Dпр=2,25 ×51 = 112мм
Н пр =1,6 Dпр = 112×1,6= 180 мм
2) Dпр =2,25×( ) = 45мм, что меньше минимально рекомендуемого 80мм, следовательно принимаем 80мм.
Н пр = 1,6× 80 =128 мм
Рисунок 6 – Сечение элементов литниковой системы
13.7 Выбор типа модельных плит и опок
Основными элементами металлического комплекта являются модельная плита и стержневые ящики, а вспомогательными элементами являются кондукторы для зачистки и сборки стержней.
Изготавливается модельная плита составной, модель делается отдельно, а затем монтируется вместе с моделями элементов литниковой системы на модельную плиту. Это позволяет устранить некоторые ручные операции при формовке.
Модельная плита имеет повышенную прочность, изготовленная из стали марки 25Л.
Модельная плита тонкостенная, усиленная ребрами жесткости.
Учитывая, что использование больших опок влечет за собой увеличение затрат труда на уплотнение формовочной смеси, нецелесообразный расход смеси, а использование очень маленьких опок может вызвать брак отливок вследствие продавливания металлом низа формы или уход металла по разъему.
Для отливок массой от 26 до 50 кг рекомендуются следующие минимальные толщины слоя смеси:
- от верха модели до верха опоки – 70 мм
- от модели до стенки опоки - 50 мм
- от низа модели до низа опоки - 90 мм
- между моделями - 60 мм
- между моделью и шлаковиком - 40 мм
Минимальная высота опоки верхней - 175 + 70 = 245 мм
Минимальная высота опоки нижней - 175 + 90 = 265 мм
Минимальная длина опоки – 50 +340 + 60 + 69 + 60 + 340 + 50 = 969 мм
Минимальная ширина опоки – 50 + 140 + 60 + 112 + 60 + 140 + 50 = 612 мм
Исходя из формообразующего оборудования и минимально допустимых размеров опок принимаем по ГОСТ 2133 – 75 размер опок в свету:
1000 × 800 × 300 (мм) – нижняя
1000 × 800 × 300 (мм) – верхняя
13.8 Расчет подъемной силы
Для предотвращения подъемаверхнейполуформы под действием статического давления метала, форму нагружают грузом. Массу груза определяют как разность между подъемной силой и массой верхней полуформы.
P = к ∙ [ Н ∙ ( Fотл. + Fл.с. ) ∙ ρ + Vст. ∙ ( ρ – ρст. ) ]– m; (11)
где P – подъемная сила , испытываемая верхней полуформой от давления жидкого металла, кгс;
к – коэффициент запаса, учитывающий гидравлический удар, к = 2…4;
Н – высота от верха отливки до верхнего края опоки, дм;
Fотл. – площадь горизонтальной проекции отливки в плоскости разъема, дм2;
Fл.с. – площадь литниковой системы в разъеме формы, дм2;
ρ и ρст. – плотность жидкого металла и плотность стержня, кг/дм3;
Vст. – объем стержня без знаков, дм3;
m – масса верхнейполуформы, кг.
Н = 1,6дм
К = 2
Fотл= 2,8 × 2,4 × 4 = 27 дм²
Fл.с= 2 × (3,14× 1,12² : 4 + 3,14 × 0,80² : 4) + 4,5 × 0,045 = 3,16 дм²
ρ ме= 7 кг/ дм³
ρ ст = 1,9 кг/ дм³
Vст= 3,14 × 0,85² × 2,4 = 5,44 дм³
m = 1650 × (0,1000 × 0,800 × 0,300 ) + 200 = 596 кг
P = 2 ∙ [ 1,6 ∙ ( 27 + 3,16 ) ∙ 7 + 5,44 ∙ ( 7 – 1,9 ) ] – 596 = 732-596 = 136 кг
Так как давление жидкого металла (732 кг) больше, чем масса верхнейполуформы (596кг), то необходим груз не менее 136 кг.
13.9 Параметры и условия заливки формы
Для заливки жидкого металла в форму используется автоматическая установка У42. Для обеспечения хорошей заполняемости формы и получения качественной отливки необходимо выдерживать определенную температуру заливаемого чугуна. [2]
Таблица 21 – Рекомендуемая температура заливки форм
Сплав | Характеристика отливки | Температура расплава, °С | |
При выпуске из печи | При заливке в форму | ||
ВЧ50 | Отливка мелкая тонкостенная | 1400 | 1350 |
13.10 Охлаждение, обрубка, очистка и контроль отливок
Охлаждение отливки.
После затвердевания отливки она охлаждается вместе с формой, как единая система. Длительность охлаждения отливки в форме в десятки раз превосходит длительность затвердевания. Наличие стержня резко замедляет охлаждение.
Продолжительность выдержки чугунной отливки массой до 20кг в форме принимаем по рекомендациям не менее 0,26-0,34 часа.
Очистка и контроль отливки.
Очистку отливки от пригара производят в дробеметном барабане.
Зачистку отливок от остатков литников, выпоров и других неровностей, производят ручными шлифовальными машинками или с помощью подвесных точил. Если отливка подверглась воздушно – дуговой резке в районе обрабатываемой поверхности, то необходимо провести отжиг, для улучшения структуры и улучшения механических свойств материала.
Контроль качества готовой отливки заключается в установлении ее соответствия требованиям действующего ГОСТа, техническими условиями и чертежами. Визуально контролируется внешний вид и качество поверхности. Для выявления скрытых дефектов проводится выборочно механическая обработка отливки. Контролируется размерная и массовая точность отливки, а также химический состав металла, микроструктура, механические свойства.
Незначительные дефекты на поверхности отливки можно устранить. Для устранения дефектов применяется: электросварка, исправление замазками. При выявлении брака: трещин, глубоких газовых раковин, неметаллических включений, отливка бракуется и отправляется на переплав. Годные отливки поступают на склад готовой продукции.
14 Специальная часть.
Дата добавления: 2018-05-12; просмотров: 316; Мы поможем в написании вашей работы! |
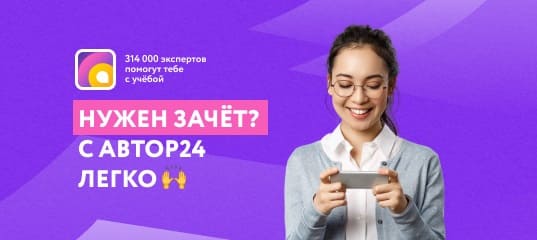
Мы поможем в написании ваших работ!