Особенности сверления глубоких отверстий
Министерство образования Российской Федерации
Камский государственный политехнический институт
ТЕХНОЛОГИЯ
МАШИНОСТРОЕНИЯ
Методические указания к лабораторным работам для
студентов машиностроительных специальностей
дневной и заочной формы обучения.
Набережные Челны
2004
УДК 621.9.
"Технология машиностроения" Методические указания к лабораторным работам для студентов машиностроительных специальностей дневной и заочной формы обучения. / Составители: Г.А.Паутов, А.П.Абызов, О.И.Тарабарин, А.В.Передерий, С.М.Петров, Д.Т.Сафаров.
Под общей редакцией Г.А.Паутова. – г. Набережные Челны. Из-во КамПИ, 2004г. 252 с.
Изложены основные теоретические положения из технологии формирования точности и качества по тематике лабораторных работ. Определены: состав технологического оборудования; измерительные средства; последовательность выполнения работ.
Методические указания предназначены для студентов специальности 1201 «Технология машиностроения», а также для студентов других специальностей, изучающих технологию производства машин.
Рецензенты:
заместитель генерального директора
АО «Камаз-Дизель» А.К. Буцалан.
главный технолог АО «Камаз-Дизель» В.М. Баринов
Печатается по решению научно-методического совета Камского государственного политехнического института от 23.06.2003г.
© Камский государственный политехнический
|
|
институт 2004г.
Введение
Технология производства машин – отрасль науки, занимающаяся изучением закономерностей, средств, методов превращения первичного материала в детали и сборки из них машин.
Лабораторный практикум позволяет закрепить теоретические знания в области технологии производства посредством выполнения различных этапов изготовления: формообразования, обеспечения качества, сборки, контроля. При этом приобретаются навыки, как при разработке отдельных этапов технологических процессов, так и в практическом использовании технологических установок, оснастки, режущего и измерительного инструментов.
Все лабораторные работы проводятся в лаборатории технологии машиностроения.
Студенты перед началом проведения занятий должны изучить правила техники безопасности при работе в лаборатории и расписаться в ведомости проведения инструктажа.
Практическая работа на станке, с оснасткой, средствами измерений и инструментом допускается только после изучения методического руководства к лабораторной работе в присутствии учебного мастера.
Работа считается выполненной после сдачи результатов и проверки теоретических знаний студента и подписи преподавателем отчёта.
|
|
Содержание
1. | Особенности сверления глубоких отверстий (Паутов Г.А.)… | 5 |
2. | Отделочно-упрочняющая обработка методом выглаживания (Паутов Г.А.)……………………………………………………. | 19 |
3. | Исследование методов затяжки резьбовых соединений (Паутов Г.А.)…………………………………………………………. | 34 |
4. | Разработка и анализ точности технологического процесса сборки гидромуфты привода вентилятора автомобиля КамАЗ (Абызов А.П.)……………………………………………... | 41 |
5. | Анализ точности изготовления зубчатых колёс до зубонаре-зания (Абызов А.П.) …………………………………................ | 52 |
6. | Технологическое и техническое нормирование операций обработки деталей на станке с ЧПУ (Абызов А.П.)………….. | 75 |
7. | Определение погрешности базирования при фрезеровании (Тарабарин О.И.)………………………………………………... | 89 |
8. | Определение жесткости технологической системы и изучение её влияния на погрешность формы детали (Тарабарин О.И.)…………………………………………………………….. | 100 |
9. | Определение точности настройки станка (Тарабарин О.И.)… | 112 |
10. | Проектирование технологического процесса сборки гидромотора типа Г15-2 (Петров С.М.)……………………………... | 120 |
11. | Проектирование технологической операции механической обработки, практическое освоение её выполнения и анализ точности качества (Петров С.М.)……………………………… | 129 |
12. | Выбор средств контроля и проектирование операции контроля (Петров С.М.)……………………………………………. | 139 |
13. | Разработка технологического процесса изготовления детали типа валика и освоение черновой токарной обработки (Передерий А.В.)…………………………………………………… | 148 |
14. | Анализ точности сверления отверстий по разметке (Передерий А.В.)………………………………………………………… | 168 |
15. | Анализ точности обработки деталей вероятностно-статистическим методом (Сафаров Д.Т.)……………………... | 193 |
16. | Технологическая подготовка и анализ эффективности обработки на токарном станке с ЧПУ (Паутов Г.А.)……………… | 223 |
17. | Определение влияния температурных деформаций на точность детали (Сафаров Д.Т.)…………………………………… | 236 |
|
|
Лабораторная работа №1
Особенности сверления глубоких отверстий
1. Теоретические положения.
Сверление – распространённый способ обработки глухих сквозных отверстий в конструкционном материале с точностью Н11,Н12 и шероховатостью Rz 40-20мкм
|
|
Отверстия диаметром свыше 35…40мм сверлят за два перехода - сначала сверлом меньшего диаметра, а затем требуемого. Отверстия диаметром свыше 60…70мм целесообразно обрабатывать кольцевым сверлом, т.к. остающийся металл в виде сердечника пригоден к дальнейшему использованию.
Сверление производят обычно с использованием кондукторов с направляющими втулками на сверлильных и расточных станках.
Для повышения производительности применяют многошпиндельные головки или специальные (агрегатные) станки.
Для повышения качества обработанной поверхности и уменьшения погрешности обработки после сверления отверстия при необходимости зенкеруют и развёртывают, используя для этого кондукторы со сменными втулками и быстросменные патроны для закрепления инструмента в шпинделе станка.
Глубокое сверление при L ≥ 10d значительно сложнее обычного: возрастает опасность отклонений оси отверстия от оси детали, затруднено охлаждение сверла в зоне резания и извлечение стружки из отверстия во время работы.
Увод оси отверстия вызывают следующие явления:
- продольный изгиб сверла;
- неодинаковая заточка режущих лезвий сверла.
При неодинаковой длине режущих лезвий (рис.1) срезается стружка различной ширины. Силы резания, возникающие на лезвиях, неодинаковые по величине, что создаёт неуравновешенную радиальную силу, отклоняющую сверло от оси. При этом сверло деформируется и вращается подобно гибкому валу.
|
|
|

Рис.1. Геометрия режущей части сверла.
Неблагоприятные условия резания в начальный момент обработки, когда сверло работает только перемычкой.
Для уменьшения увода оси отверстия необходимо: применять направляющие (кондукторные) втулки для сверла, ограничивающие его деформацию; обеспечивать симметричную геометрию режущих лезвий инструмента при заточке; выполнять предварительную зацентровку отверстия жестким (коротким) сверлом с углом при вершине 90°. Это исключает перемычку сверла из работы в начальный момент обработки. Сверление начинается непосредственно режущими лезвиями инструмента, а кромки зацентрованного отверстия заготовки направляют сверло (рис.2)
Рис.2. Зацентровка жестким сверлом.
Кроме этого необходимо использовать "ручные сверла", имеющие специальную конструкцию.
Глубокие отверстия можно сверлить тремя основными методами:
· вращение и движение подачи сообщается инструменту;
· вращение сообщается детали, а движение подачи инструменту;
· вращение сообщается детали и инструменту в противоположные стороны, а подача – инструменту.
Вращение сверла позволяет вести обработку на высоких скоростях резания, ограничиваемых только стойкостью материала сверла, что особенно важно при сверлении отверстий, диаметр которых значительно меньше размеров обрабатываемой детали. Этим методом обрабатывают глубокие отверстия на агрегатных, вертикально и радиально-сверлильных станках.
Основным недостатком этого метода является опасность увода оси отверстия. В этом случае отверстие обрабатывается, в основном, спиральными сверлами, что при значительной глубине отверстия вызывает спрессовывание стружки в канавках сверла. Во избежание поломки сверла приходится периодически его выводить из отверстия, а это снижает производительность труда. При сверлении этим методом затруднён также подвод охлаждающей жидкости в зону резания.
Сверление глубоких отверстий на горизонтально-сверлильных станках при вращении детали и при осуществлении подачи сверлом обеспечивает существенное уменьшение увода оси обрабатываемого отверстия. Так как в этом случае процесс сверления становится подобным расточке отверстия резцом: при отклонении резца в радиальном направлении ось отверстия остаётся прямолинейной, совпадающей с осью шпинделя, но размер отверстия (диаметр) изменится. Аналогично при сверлении: увод сверла не вызывает искривления оси отверстия, но порождает погрешность формы отверстия (рис.3)
Рис. 3. Схема образования погрешности формы.
Основным недостатком данного метода является трудность обеспечения высоких скоростей резания, особенно при обработке крупногабаритных деталей. Такие детали обычно вращаются с малой частотой и обработка их ведется быстрорежущим инструментом. Поэтому метод глубокого сверления с вращением только детали для крупногабаритных изделий малопроизводителен.
Наиболее производительным является метод сверления при одновремённом вращении инструмента и детали в противоположных направлениях. Сверло вращается с большой частотой, чем обеспечивается высокая скорость резания. Обработка осуществляется на горизонтально- сверлильных станках, имеющих устройства для вращения режущего инструмента. (станки роторного типа).
При глубоком сверлении важен правильный выбор конструкции сверла. Для размельчения стружки при глубоком сверлении с целью надёжного ее удаления из отверстия, большое значение имеет расположение режущих кромок инструмента. В зависимости от этого различают сверла, работающие методом деления стружки по ширине и толщине.
Сверла, работающие по первому методу, называются сверлами одностороннего резания. Независимо от количества резцов их режущие кромки образуют как бы единую режущую поверхность. При этом нет необходимости в точной установке резцов по торцу сверла.
Сверла, работающие делением стружки по толщине, называются сверлами двустороннего резания или с двусторонним расположением резцов; длина режущей кромки каждого резца равна глубине резания. В этом случае подача на один оборот сверла распределяется между обоими резцами. Точная установка резцов по торцу инструмента затруднена. Сверла двустороннего резания дают больший увод оси отверстия, чем сверла одностороннего резания.
Для глубокого сверления большое значение имеют форма и размеры отходящей стружки. Стружка лучше удаляется из отверстия когда она имеет форму мелких завитков или кусочков. Такая форма стружки достигается особой заточкой режущих частей сверла-образованием на его передней поверхности порожков строго определенной формы и размеров. (рис.4 а,б).
|
|
|

Рис.4. Сверла для сплошного и кольцевого глубокого
сверления отверстий:
а) – трубчато-лопаточное сверло с наружным отводом стружки (Ø6…20мм);
б) – однорезцовое кольцевое сверло с внутренним отводом стружки (Ø60…130мм);
в) – однокромочное мверло с внутренним отводом стружки (Ø18…35мм).
Сверление осуществляется с применением смазочно-охлаждающих жидкостей: сульфата фрезола, содержащего 1,5…25% серы и минеральных масел, подаваемых под давлением 100…500кПа (10…50 ). Реже применяется жирная эмульсия.
Режимы резания при работе сверл одностороннего резания: подача 0,01…0,1 мм/об, скорость до 100…200м/мин и более. Сверла двустороннего резания из быстрорежущей стали работают при подаче 0,15…0,5мм/об и скорости резания 15…40 м/мин. Режимы резания, применяемые при кольцевом сверлении отверстий диаметром 60…200 мм в заготовках из сталей = 0.75…1 ГПа (75…100
): подача 0,1…0,3 мм/об, скорость резания 140…120 м/мин.
Повышение точности диаметра и уменьшение шероховатости достигается последующей обработкой зенкерованием, растачиванием, развёртыванием или протягиванием. Зенкеруют и развертывают глубокие отверстия с применением обратной подачи. Инструмент не проталкивается в отверстие, а протягивается через него, чтобы тонкая державка работала на растяжение, а не на сжатие.
Для глубоких отверстий в труднообрабатываемых материалах применяются физико-химические процессы: электоэрозионный, анодно-механический, ультрозвуковой и др. Данные методы позволяют получать отверстия и некруглого профиля.
- Цель выполнения работы.
Целью работы является изучение особенностей получения глубоких отверстий и ознакомление с возможностями технологических способов сверления, а также освоение методики контроля точности расположения отверстий.
- Технологическое оснащение.
· Образцы для сверления и контроля – 4 шт.
· Центра – 1 комплект.
· Стойка индикаторная – 1шт.
· Индикатор НЧ 0-10 ГОСТ 577-68.
· Чертилка, 1 шт.
- Содержание работы.
Произвести сверление отверстий в цилиндрических заготовках на вертикально-сверлильном и токарно-винторезном станках согласно требованиям технологического процесса (приложение).
Определить величину увода осей отверстия посредством измерения наружного диаметра деталей на контрольно-измерительном приспособлении.
Для измерения необходимо установить деталь кромками просверленного отверстия в центре приспособления. После этого подвести измерительный наконечник /индуктивного датчика, индикаторных часов и т.д./ к наружной цилиндрической поверхности, расположив его в диаметральной плоскости на расстоянии 2-3 мм от одного из торцов, например, левого. Поворачивая деталь осуществляют замер радиуса – вектора наибольшего. Отмечают данную точку карандашом, риской и т. д. и определяют радиус – вектор в диаметрально противоположной точке
(рис.5). После этого установить точку
под измерительный наконечник и установить индикаторную стрелку на нуль шкалы. Затем повернуть деталь на 180º и снять показание индикатора Δ
в точке
. Условимся считать, что отклонение имеет отрицательный знак, если наконечник индикатора перемещается к центру детали.
Измерение производится таким образом, что за базу принимается отверстие и относительно него определяется положение оси наружной цилиндрической поверхности. Поэтому поместив в т. О систему координат /см. рис. 5/, можно найти координату т. О.
Рис.5. Расчетная схема левого торца.
где Δ – алгебраическое значение отклонения стрелки показывающего прибора от нулевого значения шкалы в фиксированной точке.
т.к.
Далее определяется отношение расположения центра наружной цилиндрической поверхности (т.О) и центра отверстия /т. / на другом торце детали – правом (рис.???)
Рис.6. Расчетная схема правого торца.
Через точки и
провести образующие цилиндра и в пересечении их с правым торцом поместить т.
и
, а также т.
и
, лежащие в плоскости, перпендикулярной прямой
. Повернуть деталь так, чтобы одна из фиксированных точек расположилась под наконечником и установить стрелку на нулевое показание. Снять показания во всех отмеченных точках с учетом знаков отклонений. Вычислить координаты точки О в системе координат
Теперь определим величину увода оси отверстия Δув. Для этого необходимо спроектировать рассмотренные точки на обоих торцах на плоскость перпендикулярную оси наружной цилиндрической поверхности. (рис.???)
Рис.7. Схема расчета увода оси отверстия.
Величина увода равна.
Замеры повторить на следующих деталях.
Сопоставить величины увода осей отверстий, полученных различными методами /на токарном и вертикально-сверлильном станках/, сделать выводы по работе.
- Отчёт по выполненной работе.
Отчёт составить по схеме:
· эскизы образцов;
· схемы обработки образцов на токарном и сверлильном станках;
· схема измерения для контроля прямолинейности;
· схемы расчёта увода оси отверстий, с обозначением фактических значений измерений;
· расчёт величин увода;
· выводы и рекомендации.
Лабораторная работа №2
Дата добавления: 2018-05-12; просмотров: 1953; Мы поможем в написании вашей работы! |
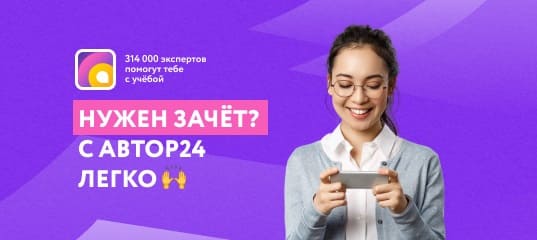
Мы поможем в написании ваших работ!