Расчет ожидаемой производительности синхронной АЛ.
Министерство образования и науки РФ ФГБОУ ВПО «Тульский государственный университет» Политехнический институт Механико-технологический факультет Кафедра «Технология машиностроения» «автоматизация производственных процессов»
РАСЧЕТ ОЖИДАЕМОЙ ПРОИЗВОДИТЕЛЬНОСТИ СИНХРОННОЙ автоматическОЙ линиИ
АЛС - 104
Курсовая работа
Пояснительная записка
КАПП.ПЗ
Выполнил студент гр. 630191 Соколова Н.А.
Проверил проф. кафедры ТМС Федин Е.И.
Тула, 2013
Аннотация.
Автоматизация является одним из эффективных средств повышения
производительности труда в крупносерийном и массовом производствах. Одновременно внедрение отработанных и современных средств автоматизации способствует стабилизации технологического процесса, его количественных и качественных показателей, в конечном итоге повышению потребительских и эксплуатационных свойств выпускаемых изделий.
Содержание.
Введение…………………………………………………………………….4
Основные понятия и определения теории надежности…………………..5
Расчет ожидаемой производительности синхронной АЛ……..…………6
Заключение…………………………………………………………………10
Список использованных источников……………………………………..11
Введение.
|
|
при автоматизации крупносерийного и массового производств важнейшее значение имеет решение проблемы повышения надежности используемых средств автоматизации и автоматизированного оборудования, образующих в совокупности автоматические линии.
Принципиально эта проблема может быть решена двумя путями:
1) Максимальным упрощением конструкций и использованием минимального количества средств автоматизации в автоматической линии (АЛ). Такое решение характерно для синхронных автоматических линий *), в которых перемещение предметов производства между станками-автоматами производится одновременно (синхронно) по завершению лимитирующего перехода,
выполняемого на одной из технологических машин.
2) Разделением АЛ на участки с автоматическим накоплением межучастковых заделов предметов производства с целью компенсации (частичной или
полной) простоя всей АЛ при вынужденном простое отдельного станка-
автомата или средства автоматизации вследствие какой-либо технической или
организационной причины. Такие АЛ получили название несинхронных или автоматических линий с гибкой транспортной связью.
При проектировании АЛ из типовых агрегатных узлов одним из основных количественных показателей, определяющих структуру линии, типы и количества станков-автоматов и средств автоматизации является производительность (П) или ее обратная величина - такт выпуска (tа) продукции. Таким образом, конструкторы, занимающиеся компоновкой автоматической линии с заданной производительностью, должны четко представлять баланс времени работы и простоев всей системы машин, обладая исходной информацией о показателях надежности входящих в эту систему элементов: технологических машин
|
|
(станков-автоматов), средств автоматизации, вспомогательных устройств, технологической оснастки и инструментов.
Основные понятия и определения теории надежности.
Надежность АЛ- комплексное свойство технической системы, характеризующееся целым рядом частных свойств, важнейшими из которых являются:
безотказность, ремонтопригодность, долговечность.
Безотказность- свойство АЛ непрерывно сохранять работоспособность
в течение некоторого времени.
Безотказность количественно может быть оценена следующими показателями:
· вероятностью безотказной работы Pр (τ) в течение промежутка времени τ;
· интенсивностью отказов λ(τ);
· наработкой до отказа tр(τ) или средней наработкой до отказа Мр(τ), которая является математическим ожиданием наработки АЛ от включения до первого отказа за принятый промежуток времени ее эксплуатации.
|
|
Ремонтопригодность- свойство АЛ, заключающееся в приспособленности к предупреждению и обнаружению причин возникновения отказов, поддержанию и восстановлению работоспособного состояния путем проведения технических обслуживаний и ремонтов.
Важнейшими количественными критериями ремонтопригодности являются:
· вероятность восстановления работоспособности за определенный
промежуток времени РВ(τ);
· интенсивность восстановления μ(τ);
· время восстановления tВ(τ) или среднее время восстановления МВ (τ).
Долговечность- свойство АЛ сохранять работоспособность в течение
некоторого времени с необходимыми перерывами для технических обслуживаний и ремонтов до наступления предельного состояния.
Под предельным состоянием понимается такое функционирование АЛ, которое характеризуется неустранимым снижением производительности, экономической неэффективностью ее дальнейшей эксплуатации или же сопряжен-
ной с этим опасностью производственной деятельности (биологической, экологической и т.п.). Иногда критерием предельного состояния может служить снижение средней наработки до отказа за относительно небольшой промежуток
|
|
времени (месяц, квартал) до предельно допустимого значения
Мр(τ) < Мр min (1)
Долговечность АЛ связана с долговечностью отдельных станков-
автоматов и средств автоматизации этой линии. Определяющими факторами,
влияющими на долговечность, являются процессы изнашивания, старения, потери прочности (усталости) при действии переменных напряжений в деталях
машин.
Расчет ожидаемой производительности синхронной АЛ.
1. Расчет технологической производительности
tМ – машинное время (мин)
tВ – вспомогательное время – все действия внутри цикла тех. машины, направленное на подготовку процесса обработки (мин)
tц= tМ +tВ= tОП = tа – такт линии
tа=2,3+0,4=2,7 мин.
Технологическая производительность ПТЛ=1/ tМ (шт/мин)
ПТЛ= 60/2,3=26,08 шт/час.
2. Расчет цикловой производительности и коэффициента производительности
;
(шт/час)
;
В реальном производстве помимо цикловой потери времени (tВ) имеет место внецикловые потери времени (ВПВ), снижающие производительность.
3. Расчет коэффициента готовности
Для определения коэффициента готовности принимают следующие допущения:
a. (мин/отказ)
(мин/восст.)
в теории надежности принимают обратные величины
b. (отказов в мин) – интенсивность отказов
(восст. в мин) – интенсивность восстановлений
c. В АЛ встречаются как дискретные так и непрерывные механизмы
Мр, λ, МВ – непрерывные элементы
Мрц, λц – цикловые/дискретные элементы
d. Удельные ВПВ рассчитываются по формуле
(мин на 1 мин)
e. В последовательной системе (синхронной АЛС) удельные ВПВ по любым причинам равны сумме Вi удельных ВПВ по тем же причинам
f. Коэффициент готовности определяется по формуле
Согласно пункту 3 заполняем таблицу 1, исходные данные для которой определяем по справочным данным [1].
таким образом имеем:
Позиция 1
оборудование поз.1
Наименование | Модель (тип) | шт | λ | μ | Внт*103 |
Бабка фрезерная | УХ4131.01 | 2 | 0,12 | 0,10 | 2,4 |
1.1.1
1.1.2
Наименование | Модель | шт | Мв, Мин/восст | λц*103 отк/цикл | λ*103, отк/мин | μ, восст/мин | Внт*103 |
Стол крестовый | УЕ4315.05 | 2 | 30 | 0,18 | 0,067 | 4 |
Инструмент поз.1
1.2.1
Наименование | Модель | шт | Мрц, Цикл./отк | Мр, Мин/отк. | МВ, Мин/восст | Внт*103 |
Фреза торцовая со вставными ножками | Т14К8 | 2 | 3756,5 | 10142,6 | 6 | 0,00118 |
;
Аналогичным образом заполняется вся таблица.
Суммируем все полученные ВПВ на каждой операции и получаем:
(мин/мин), таким образом имеем
4. Определение удельных собственных ВПВ и технической производительности
, где Вс удельные собственные ВПВ
, где МВПО и МВПС среднее время восстановление работоспособности в течение одной рабочей смены фактически соответствуют нормам времени на техническое обслуживание и организационную подготовку АЛ, которые рассчитываются по приложениям 10 и 11.
, где Fсм – сменный фонд времени работы (8,2 часа).
мин
=45 мин
мин
Расчет удельных потерь времени на плановую смену инструментов ВПН производится по таблице 2.
№ | Инструмент | Кол-во | Показатели надежности | ||||
Т | Мрц | Мр | Мв | Впн | |||
1 | Фреза торцовая Т14К8 | 2 | 180 | 78,26 | 211,3 | 5 | 0,153 |
2 | Сверло спиральное Ø6 Р6М5 | 2 | 90 | 39,13 | 105,6 | 0,8 | 0,04 |
3 | Сверло спиральное Ø8,2 Р6М5 | 1 | 90 | 39,13 | 105,6 | 0,8 | 0,02 |
4 | Сверло спиральное Ø14 Р6М5 | 1 | 90 | 39,13 | 105,6 | 0,8 | 0,02 |
5 | Зенкер Ø18 Т5К6 | 1 | 180 | 78,26 | 211,3 | 0,8 | 0,01 |
6 | Сверло спиральное Ø8,2 Р9 | 1 | 90 | 39,13 | 105,6 | 0,8 | 0,02 |
7 | Сверло спиральное Ø18 Р9 | 2 | 90 | 39,13 | 105,6 | 0,8 | 0,04 |
8 | Зенкер Ø16 Т15К6 | 1 | 180 | 78,26 | 211,3 | 0,8 | 0,01 |
9 | Развертка Ø9 Р9 | 1 | 120 | 53,17 | 143,5 | 0,2 | 0,004 |
мин
мин
Техническая производительность равна дет/час
5. Расчет коэффициента загрузки оборудования и фактической производительности.
ηз отражает долю рабочего времени, течение которого АЛ обеспечивает всем необходимым для работы . Теоретически не определяется, выполняется статистически.
Для массового производства принимаем ηз=0,85
дет/час
Заключение
В ходе данной работы был произведен расчет производительности синхронной АЛ: технологической, цикловой, технической и фактической. Для увеличения производительности на предприятии следует учитывать человеческий фактор и наличие экстренных ситуаций, а именно: опоздания, неявку на работу, отключение электроэнергии, тепло- и водоснабжения, недостаточность освящения и проветривания рабочего места. Это можно проконтролировать имея в штате сотрудников широкого профиля и резервных рабочих. Также необходимо учитывать возможность подключения аварийных источников электроэнергии и тепло- и водоснабжения.
Дата добавления: 2018-05-12; просмотров: 128; Мы поможем в написании вашей работы! |
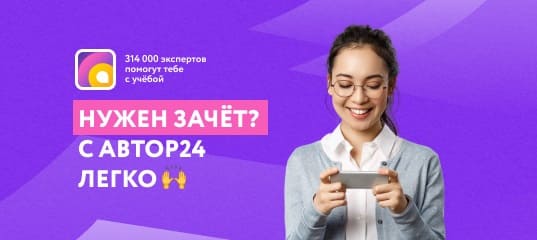
Мы поможем в написании ваших работ!