Розглянемо послідовність проектування пристосування і зміст його окремих етапів.
Вибір групи пристосуваннязалежно від типу виробництва здійснюється перед початком його конструювання. В умовах масового і великосерійного виробництва застосовують спеціальні пристосування, в середнє - і дрібносерійному, а також в одиничному — переналажуємі—УЗП, УНП, ЗРП, ЗНП. Вибір найекономічнішої доцільної групи повинен вироблятися на основі відповідних економічних розрахунків .
Вибір способуустановки пристосування на верстатітакож повинен предшевствувати початку його конструювання, оскільки від цього в деякій мірі залежать схема закріплення заготівки і конструкція затискних пристроїв, а також загальна компоновка пристосування .
Вибір баз і способу базування заготівки. Бази можуть бути вказані технологом, наприклад, на операційному ескізі або вибираються конструктором. Для вибраних баз конструктор розробляє спосіб базування заготівки, керуючись правилом орієнтування заготівок групою баз
Вибір точки додатку і напряму затискного зусиллявиробляється звичайно разом з вибором способу базування. Необхідність узгодження схеми закріплення і способу базування заготівки обумовлена стремлінням врахувати багато чинників, що впливають на точність обробки, надійність закріплення, компактність пристосування, зручність зняття і установки заготівки і т.д.
Вибір конструкції опорних елементівздійснюється з урахуванням вибраного способу базування по рекомендаціях, приведених в довідниках по пристосуваннях, ГОСТах і галузевих нормалях. Як правило, слід використовувати стандартні і нормалізовані опорні елементи.
|
|
Вибір контактного елементу, силового механізму і приводу здійснюється з урахуванням конкретних умов виконання даної операції по рекомендаціях. Крім того, необхідно враховувати і правила техніки безпеки, передбачені ГОСТ. Зокрема, сумарні розрахункові зусилля затискних елементів пристосувань повинні перевищувати максимальні сили різання не менше ніж в 2,5 рази; ексцентрикові швидкодійні пристрої, що самогальмуютьсядопускається застосовувати при розрахунковому зусиллі затиску, що розвивається, не перевищуючому 230 Н (220 кгс), а гайки при зусиллі затиску не більш 100 Н (10 кгс).
При виборі конструктивної схеми силового механізму і всього затискного пристрою рекомендується користуватися довідникамиі іншою літературою по пристосуваннях, де приведена велика кількість опробуваних конструкцій, що володіють надійністю; високою продуктивністю і зручністю експлуатації. Багато хто з них нормалізований і включений в галузеві нормалі. Використовування нормалізованої конструкції затискного пристрою дасть можливість скоротити терміни проектування пристосування, підвищити його надійність і продуктивність.
|
|
Вибір направляючих елементів для інструментуздійснюється залежно від конкретних умов виконання операції по рекомендаціях.
Розробка компоновки пристосуванняздійснюється на рівні технічного проекту. В більшості випадків виконана досвідченим конструктором компоновка після відповідних узгоджень і деякого коректування оформляється як складальне креслення пристосування. У зв'язку з цим при її розробці враховуються вимоги ГОСТ 2.109—73 «Правила виконання креслень деталей складальних, загальних видів, габаритних і монтажних» і рекомендації по оформленню складальних креслень пристосувань.
Розрахунок затискних пристроївдля забезпечення надійного закріплення заготівки виробляється по методиці.
Розрахунок точності сконструйованогопристосування здійснюється по методиці.
Розрахунки міцності деталей і вузлів пристосування.Кінематичні розрахунки. Ці розрахунки необхідні при обробці заготівок із значними зусиллями різання, при розробці механізованих і автоматизованих швидкодійних пристосувань і в деяких інших випадках. Всі вони виконуються по методиках, висловлених в підручниках по таких загальноінженерних дисциплінах, як опір матеріалів, теорія машин і механізмів, деталі машин і ін.
|
|
Розрахунки економічної доцільності застосування сконструйованого пристосуваннявиробляються по методиці, Цими розрахунками практично закінчується розробка технічного проекту пристосування. Якщо вони підтвердили правильність ухвалених конструкторських рішень, то технічний проект передається на узгодження керівнику і технологу. Після його узгодження і твердження приступають до розробки робочої документації — оформленню складального креслення і робочих креслень деталей.
Контрольні запитання
1 Розробка схеми базування
2 Розрахунок похибки базування
3 Що таке установчі елементи пристосування, вибір
4 Які розраховуються похибки?
5 Вибір ріжучого інструмента
6 Розрахунок режимів різання
7 Що потрібно для розрахунку зусилля затиску?
8 Розрахунок на міцність
ЗАНЯТТЯ № 29-30( 4 години)
Вид заняття: ЛАБОРАТОРНА РОБОТА №1
ТЕМА :Розбір зразків пристосувань з затискувачами різного типу.
Конструкції, принцип дії, визначення зусиль затиску, які діють на заготовку.
1 Зміст лабораторної роботи:
1 Вивчення і аналіз верстатного пристрою середньої складності, яке задане у вигляді натурального зразка.
|
|
2 Придбання практичних навичок по вибору технологічних баз, базуванню заготовки в пристосуванні.
3 Визначення і розрахунок сил, які діють на заготовку в процесі обробки.
4 Виконання заданої операції на верстаті.
5 Виконання ескізу пристосування.
6 Виконання розрахунку сили затиску по завданню згідно варіанту.
7 Відповісти на контрольні запитання, звіт.
Заняття 31-32(4години)
Продовження теми 7
Тема :Складальні пристроїдля верстатів з ЧПК та автоматичних ліній
План :1 Призначення та особливості
2 Пристрої дня установки, закріплення та направлення ріжучого інструменту
3Основні типи допоміжного інструменту і вимоги до нього
4 Засоби суміщення часу зміни заготовок з часом роботи верстата
/2, с. 234-248; 3, с.41-43; 57-61/
Механізація і автоматизація є основними напрямами в проектуванні пристосувань. Механізація і автоматизація верстатних пристосувань дозволяють звільнити робочої від важкого ручної праці, підвищують продуктивність, полегшують працю, вивільняють значне число робітників. Залежно від масштабу виробництва проводиться часткова або повна автоматизація пристосувань.
Частково автоматизують наступні прийоми роботи; завантаження заготівок в робочу зону пристосування; базування заготівок, тобто доведення їх базових поверхонь до повного контакту з настановними елементами пристосування; закріплення і відкріплення заготівок; обертання, фіксацію і кріплення поворотних (або пересувних) частин пристосувань; знімання і виштовхування заготівок після обробки; вимірювання деталей в процесі обробки; очищення від стружки.
У автоматичних пристосуваннях всі прийоми, починаючи від завантаження і базування і кінчаючи зніманням оброблених деталей, виробляються без участі робітника. У напівавтоматичних автоматизується тільки частина прийомів.
Автоматизація пристосувань в більшості випадків заснована на застосуванні пневматичних, пневмогідравлічних, механічних, електричних або гідравлічних приводів, керованих через кінцеві вимикачі, робочими органами верстата, що переміщаються (шпінделем свердлувального верстата, супортом токарного верстата, столом фрезерного верстата і т. д.).
Автоматизація циклу роботи верстата, доповнена автоматизацією циклу роботи пристосування, дозволяє перетворити звичні універсальні верстати на напівавтомати і автомати, а це, у свою чергу, забезпечує значне підвищення продуктивності праці і можливість багатоверстатного обслуговування. Наприклад, якщо токарні напівавтомати або безцентрово-шліфувальні верстати оснастити завантажувально-розвантажувальними пристосуваннями, то вони стануть автоматами, а універсальні круглошліфувальні верстати при установці на них вимірювальних пристроїв для автоматичного контролю розмірів в процесі обробки — напівавтоматами. Тому механізація і автоматизація парку верстатів, що є на заводах, є могутнім резервом підвищення продуктивності праці.
У автоматизованих пристосуваннях повинна бути повністю виключена можливість неправильної установки заготівки. Для цього застосовують блокувальні і запобіжні пристрої, контрольні упори (у автоматичних лініях), які при неправильному положенні заготівки зупиняють верстат.
На автоматичних лініях використовують пристосування стаціонарні іпристосування-супутники.
Стаціонарні пристосування автоматичних ліній виконують ті ж функції, що і звичні пристосування. Їх вмонтовують на окремі агрегати автоматичної лінії. У них подають, встановлюють, закріплюють, обробляють, відкріпляють і передають на транспортуючий пристрій заготівки.
Відмінною рисою цих пристосувань, є те, що вони повинні забезпечувати правильну установку заготівок при простих рухах транспортуючих пристроїв. Для цього опорні пластинки, як правило, є продовженням направляючих планок транспортуючого пристрою, а установчі пальці виконують висувними. Якщо установчі елементи нерухомі, то правильне положення заготівки забезпечується додатковими затискачами, забезпечуючими щільний контакт базових поверхонь - з установчими елементами.
Пристосування автоматичних ліній повинні бути надійними і безвідмовними в роботі. Тому в них часто передбачають автоматичний контроль правильного положення заготівки за допомогою пневматичних, електричних і інших датчиків. Велику увагу надають автоматичному очищенню пристосування від стружки. Затискний пристрій повинен бути надійним і самогальмуючий.
Більшість автоматичних ліній працює при базуванні деталі по площині і двом циліндровим отворам; так обробляють корпусні деталі. Якщо заготівка не має таких баз і її обробляють при установці в пристосуванні-супутнику, то саме пристосування-супутник базують по площині і двом отворам. При такому базуванні висувні установчі елементи (пальці і фіксатори) викликають збільшення погрішності установки заготівки. Тому до точності пристосувань для автоматичних ліній пред'являють підвищені вимоги.Для підвищення точності обробки слід надавати велику увагу збільшенню жорсткості пристосування і відсутності або зменшенню деформації заготівки під дією сил затиску.
Пристосування-супутники застосовують для обробки заготівок складної конфігурації. Всі стадії обробки виконують при одному закріпленні заготівки, чим забезпечується принцип постійності установчих баз. На початку лінії на супутник встановлюють і закріплюють заготівку, в кінці лінії її відкріплюють і знімають, а супутник повертають в початкове положення.
Переміщення пристосувань-супутників або оброблюваних заготівок по всіх агрегатах автоматичної лінії здійснюється за допомогою крокового або ланцюгового (рідше) конвеєра.
Механізація і автоматизація особливо необхідні при виконанні складальних робіт.
Одним з важливих етапів автоматичної збірки є орієнтування поверхонь однієї деталі, що сполучаються, відносно іншої з точністю, що забезпечує збираємість на базуючих пристроях складальних пристосувань. Деталі необхідно орієнтувати так, щоб при заданих допусках на розміри і відносні повороти. поверхонь, що сполучаються, можна було легко здійснити їх сполучення.
Тому до точності складальних пристосувань пред'являють жорсткі вимоги, особливо при автоматичній збірці деталей, сполучення поверхонь яких відбувається з дуже малими величинами гарантованого зазору і фаски.
Спеціалізовані налагоджувальні пристосування застосовують на фрезерно-свердлувальних і багатоцільових верстатах з ЧПУ в серійному і великосерійному виробництві для установки споріднених по конфігурації деталей. Спеціалізоване налагоджувальне пристосування складається з базової частини — комбінованого трьохкулачкового патрона (рисунок 1а) і комплекту змінних наладок, кулачків, опор і тяги, призначеної для установки заготівок деталей типу фланців, втулок, кілець при обробці отворів на свердлувальних верстатах з ЧПУ. У корпус 5 патрона вбудований гідроциліндр 7 двосторонньої дії, поршень 4який сполучений за допомогою трьох важелів 3з підставами 2 кулачків. Патрон базується відносно паза столу верстата штирями 6.Масло в гідроциліндр від джерела тиску поступає через швидкозмінні муфти 8 і 9.Змінні наладки-кулачки встановлюються по зубчастійоснові2кулачків, а опори — Т-образним пазам. Для закріплення заготівок зверху швидкозмінною шайбою за допомогою тяги остання вгвинчується в вкладиш, який встановлюється у виточку отвору штока 4 поршнягідроциліндра. Точна відстань торців полиць 1 від патрона дозволяє встановлювати на верстаті два патрони впритул для обробки за програмою двох заготівок.
Приклади компоновок спеціалізованих налагоджувальних пристосувань показані на рисунку 1б—д. Заготівка 2встановлюється на опорні планки, центрується і закріплюється трьома кулачками3(рисунок 1б) (на бічній проекції кулачки умовно повернені). Заготівка 1 центрується по внутрішній циліндровій поверхні змінними наладками — кулачками 2(рисунок 1в). Заготівка 1 встановлюється по торцю і отвору на втулку 2.Затиск заготівки зверху здійснюється через відкидну шайбу3тягою 4,вгвинчуваної у вкладиш 5 штока6 гідроциліндра(рисунок 1г). Якщозаготівка 1 встановлюється на цангу 2, тозатиск її здійснюється через шайбу 3 тягою4, вгвинчуваноїу вкладиш 6 штока7 гідроциліндра.При переміщенні штока головка тяги 4 натискаєна цангу 2, переміщаючиїї відносно конусної вставки 5. При цьому цанга, розтиснувшись, центрує, а потім закріплює заготівку (рисунок 1д).
|
|
|
|
|
Рисунок 1 - Спеціалізовані налагоджувальні пристосування для установки заготівок деталей типу фланців
У серійному виробництві при обробці на верстатах з ЧПУ заготівок невеликих розмірів декількома інструментами ефективно використовувати багатомісні спеціалізовані налагоджувальні пристосування з послідовною обробкою заготівок одним з декількох інструментів. Спочатку одним з інструментів послідовно обробляються однакові поверхні у всіх заготівках, потім здійснюється зміна інструмента і обробка ним цих же або інших поверхонь і т.д. Такий спосіб обробки різко скорочує час, що витрачається на додаткові переміщення (позиціонування) столу верстата. Проте цей час буде значно менше, ніж час, що витрачається назміну інструменту. При цьому збільшується точність обробки, оскільки точність позиціонування столу вища точності повторної установки інструменту. Зменшується також знос хвостовиків інструменту і корпусного отвору шпінделя верстата. Так, наприклад, при обробці трьох отворів у фланцях трьома інструментами в одномісному пристосуванні необхідно 9 разів здійснити зміну інструменту. При обробці цих отворів в 10-місному пристосуванні кожного отвору послідовно одним інструментом вимагається міняти інструмент замість 9 разів всього лише 3 рази.
Точність обробки на верстатах значною мірою залежить від точності і жорсткості допоміжного інструменту. Найважливішою умовою підвищення ефективності верстатів є їх комплектація високоякісним стандартним допоміжним інструментом централізованого виготовлення.
Допоміжний інструмент для токарних верстатів повинен забезпечувати достатню жорсткість, високу точність і стабільність установки (базування і кріплення) ріжучого інструменту, виконання всіх технологічних переходів, передбачених технічною характеристикою верстата, швидкозмінністьінструментів, міжрозмірну уніфікацію, настройку інструменту поза верстатом.
На центрових і патронно-центрових верстатахрекомендується застосовувати револьверні головки з кріпленням блоків ріжучого інструменту в пазах головок, на патронно-центрових і патронних — різцетримачі з циліндровим хвостовиком і нарізною лискою або з базуючою призмою.
Приєднувальні поверхні револьверних головок і різцетримачів уніфіковані по ГОСТ 24900.
Допоміжний інструмент з циліндровим хвостовиком діаметром 30, 40, 50, 60, 80 мм, з циліндровим хвостовиком і нарізною лискою, а також з базуючою призмою регламентований галузевими нормалями.
Розроблені три підсистеми допоміжного інструменту: інструмент для кріплення на свердлувально-розточувальних і фрезерних верстатах, інструмент з циліндровим базуючим хвостовиком для кріплення на токарних верстатах, інструмент з базуючою призмою для кріплення на токарних верстатах.
Система допоміжного інструменту припускає закріплення широкої номенклатури токарних різців (зокрема прохідних контурних, розточувальних прохідних і розточувальних контурних, різців для проточування канавок і ін.), свердел центрових, перових, спіральних, а також іншого осьового інструменту.
Підсистема допоміжного інструменту з базуючим циліндром включає праві і ліві різцетримачідля кріплення різців з квадратним або прямокутним перетином.
Підсистема допоміжного інструменту з базуючою призмою включає 4 різцетримачі для кріплення різців з квадратним або прямокутним перетином, а також,різцетримачі на яких можливо закріплювати оснащення, що має циліндровий хвостовик діаметром 25, 30, 40, 50 і 60 мм.
Для центрових або нескладних патронних робіт на токарно-гвинторізному верстаті застосовується інструментальна головка
Застосування інструментального шпінделя дозволяє здійснити на токарному верстаті фрезерування пазів, свердлення, зенкує отворів за програмою. При оснащенні верстата системою повороту шпінделя за програмою і відповідною системою ЧПУ можлива обробка не центральних отворів і фрезерування лисок. Револьверна головка встановлюється на хрестовому супорті токарного верстата з ЧПУ. У базових отворах планшайби револьверної головки закріплюються різцетримачі з інструментом. У будь-яке з базових отворів - діаметром 36 мм може бути встановлено інструментальний привід. При повороті планшайби револьверної головки інструментальний привід переміщається в робочу позицію, де він автоматично з'єднується з приводом, який повідомляє йому необхідну частоту обертання.
Частота обертання (від 63 до 1250 об/мин) інструментального приводу, що вимагається за програмою, з інструментом забезпечується блоком регулювання частоти обертання, який складається з восьми дроселів. Відключення кожного з дроселів або поєднання їх змінює витрату рідини, що поступає в гідродвигун від гідростанції верстата, частоту обертання гідродвигуна і відповідно шпінделя.
При невеликій номенклатурі виробів кількість інструментів, необхідних для обробки заготівок типу тіл обертання, не перевищує, як правило, 12. Вказані інструменти можуть бути встановлені в одній або двох револьверних головках. Проте при значній номенклатурі заготівок, що характерне для дрібносерійного виробництва, часто потрібна більша кількість інструментів, що викликає необхідність застосування магазина інструментів і автоматичної їх зміни. Розроблено декілька систем зміни інструменту. Принцип дії цих систем полягає у тому, що корпус інструменту залишається на верстаті, а заміні підлягають лише інструментальні державки з непереточуваними багатогранними пластинами, державки з осьовим інструментом, державки з щупами і ін. Змінні інструментальні державки (головки) мають невеликі габаритні розміри і масу (до декількох стільників грам), що дозволяє мати достатньо великий комплект інструментів без значного збільшення розмірів інструментального магазина.
Допоміжний інструмент для верстатів фрезерно-свердлувально-розточувальної групи повинен забезпечувати високу точність, мінімальну погрішність установки, високу жорсткість на всіх напрямках становлячих сил різання, вібростійку, швидкозмінність, надійність, легку і швидку настройку інструменту на необхідний розмір; універсальність, простоту конструкції і технологічність, мінімальну номенклатуру.
Для верстатів фрезерно-свердлувально-розточувальної групи і оброблювальних центріврозроблена система уніфікованого збірного допоміжного інструменту, призначена для компоновки інструментальних блоків, кожний з яких може бути використаний для конкретного технологічного переходу.
Уніфікація допоміжного інструменту ґрунтується на принципі взаємозамінності (елементи повинні компонуватися в блоках без додаткового пригону), раціонального розділення конструкцій інструментальних блоків на агрегати. Кожен агрегат виконує певну функцію і може багато разів використовуватися при створенні різних інструментальних блоків з необхідною точністю і жорсткістю з'єднання.
Здійснюється типова, розмірна і модифікаційна уніфікація: інструментів, що мають схожі розмірні параметри, але не відмінних конструктивним виконанням; однотипних інструментів, які мають різні основні розмірні параметри; конструктивних модифікацій, виконаних на основі типових рішень.
Перевагою збірного інструменту, як напрями уніфікації, є зменшення кількості окремих типів допоміжного інструменту; можливість переналагодження розмірів інструменту і регулювання довжини допоміжного інструменту; зменшення витрати металу.
Збірний інструмент дозволяє скоротити номенклатуру ріжучого і допоміжного інструменту.
Застосування інструментальних блоків з уніфікованого допоміжного інструменту забезпечує зниження вартості інструменту завдяки збільшенню серійності його випуску при скороченні номенклатури, раціональна витрата металу при виготовленні інструменту ступінчастої форми, зменшення витрати інструменту, попередню настройку осьових розмірів інструменту. Розроблена ВНІІ система уніфікованого допоміжного інструменту, а також стандартизація його приєднувальних поверхонь створюють сприятливі передумови для централізованого випуску інструментального оснащення, поліпшення забезпечення інструментами верстатів з ЧПУ.
У сучасних верстатах з ЧПУ, зокрема з автоматичною зміною інструменту, з'єднання ріжучого тдопоміжного інструменту здійснюється за допомогою циліндрових і конічних хвостовіков.
Передача моменту, що крутить, тертям застосовується при використовуванні циліндрових хвостовіков або хвостовіков з конусами Морзе. Проте з'єднання з конусами Морзе у верстатах з автоматичною зміною інструменту не можуть одержати широкого застосування через нестабільність установки інструментів по довжині я необхідності великих зусиль для видалення інструменту з кожного кубла.
Найбільше поширення на багатоінструментальних верстатах з ЧПУ набули з'єднання допоміжного інструменту з шпінделем, в якому установка хвостовика інструменту здійснюється по конусній поверхні з конусністю 7:24, а передача моменту, що крутить, забезпечується з'єднанням шпони.
З метою уніфікації хвостовіков допоміжного т ріжучого інструментів розроблено галузевий стандарт. З урахуванням особливостейверстатів з ЧПУ, призначених для обробки корпусних деталей, хвостовики інструменту для них містять елементи, що забезпечують закріплення інструменту в шпінделі, а для верстатів з автоматичною зміною інструменту — елементи, що забезпечують захоплення пристрою для транспортування інструменту з магазина в шпіндель верстата і назад.
Для забезпечення взаємозамінності прийнятий конічний хвостовик інструменту конусністю 7 : 24 з основними розмірами, задовольняючий вимоги ІСО. З великого числа типорозмірів хвостовіков стандарт передбачає застосування двох типорозмірів(40 і 50) одного виконання (з V-образною канавкою на зовнішньому діаметрі фланця).
З урахуванням необхідності забезпечення точності, жорсткості, вібростійкій і експлуатаційній надійності кріплення ріжучого інструменту вибрані два методи його кріплення:
- нерегульоване в осьовому напрямі кріплення ріжучого інструменту з базуванням по призматичних, конічних, а також по циліндрових поверхнях перехідних втулок і облямовувань, закріплених в шпінделі верстата;
- регульоване в осьовому напрямі кріплення ріжучого інструменту з базуванням по циліндрових поверхнях патронів, закріплених в шпінделі верстата.
Допоміжний інструмент для свердлувальних верстатів.
До допоміжних інструментів для свердлувальних верстатів відносяться:
розрізні і звичні перехідні втулки для кріплення ріжучих інструментів, що вставляються в патрони або безпосередньо в кубло шпінделя верстата;
швидкозмінні патрони кулькові, кулачкові і інші з наборами змінних втулок;
патрони, що самовстановлюються, для розгорток;
патрони для закріплення мітчиків;
самоцентруючи патрони для дрібних інструментів (ГОСТ8522);
розточувальні, підрізні і канавочні скалки і головки,
Багато хто з допоміжних інструментів нормалізований. Проте продовжується розробка нових, досконаліших конструкцій. Нижче розглядаються основні різновиди допоміжних інструментів.
Перехідні втулки
Закріплення інструментів на свердлувальних верстатах звичайно виробляється за допомогою конуса Морзе. Залежно від розмірів верстатів їх шпінделі мають внутрішні конуси Морзе від № 1 до 5. У більшості настільних свердлувальних верстатів шпіндель має не внутрішній конус, а хвостовік з конусом для закріплення патронів.
Перехідні втулки застосовуються для кріплення інструменту, конус Морзе якого менше, ніж конус в шпінделі.
На заміну інструменту, закріплюваного в конусі шпінделя безпосередньо або через перехідні втулки, потрібні значні витрати часу. Скорочення часу на видалення інструменту з конуса шпінделя досягається застосуванням виштовхуючого кільця.
Швидкозмінні патрони
При обробці точних отворів або отворі з фасками, кільцевими канавками і т.п. доводиться послідовно виробляти свердлення, зенкерування, розгортання і т.д. Якщо інструменти з конусним хвостовиком закріплювати безпосередньо в шпінделі верстата і кожного разу вибивати клином, то на це витрачатиметься дуже багато допоміжного часу.
Дляпідвищенняпродуктивності застосовуютьшвидкозмінні патрони,
що дозволяють в короткий час замінювати ріжучий інструмент. Деякі конструкції патронів дозволяють виробляти заміну без зупинки шпінделя верстата.
Для легких робіт використовуються швидкозмінні патрони з провідними кульками. Вони прості по конструкції і допускають зміну інструменту без зупинки шпінделя верстата.
|
Рисунок 1 - Швидкозмінні патрони: а) з провідними кульками, б) з шпилькою
Більшість інструментів, забезпечених конусними, циліндровими і квадратними хвостовиками, закладаються в патрон за допомогою змінних втулок.
На фіг. 3 представлений набір втулок до швидкозмінних патронів; перед роботою всі інструменти, вживані для даної операції, наперед закріплюються в своїх змінних втулках.
Рисунок 2 - Втулки до швидкозмінних патронів
На рисунку 2 показані: а і б — втулки для інструментів з конічним хвостовиком; віг — втулки гойдаються з кульовим поясочком К для розгорток з конічним хвостовиком; д і е— втулки з цанговим затиском для свердел і інших інструментів з циліндровим хвостовиком; ж і з — втулки гойдаються з кульовим поясочком і цанговим затиском для розгорток і мітчиків з циліндровим хвостовиком; і — втулка гойдається для мітчиків з квадратом. Кулькові швидкозмінні патрони застосовуються для легких робіт. На крупних свердлувальних верстатах для важких робіт рекомендується застосовувати швидкозмінні двохкулачкові патрони, які звичайно виготовляються з хвостовиками конус Морзе № 4 і 5. До кожного такого патрона виготовляється комплект змінних втулок з внутрішніми конусами Морзе № 1, 2, 3 і 4, що дозволяє закріплювати різний інструмент.
У випадках, коли на свердлувальних верстатах інструменту задається подвійний напрям для його зв'язку з шпінделем верстата, можна використовувати патрон з штиковим замком (рисунок 3), Цей патрон дозволяє швидко замінювати інструмент і в той же час не заважає йому самовстанавлюватися в кондукторних втулках, оскільки в сполученні патрона з циліндровою посадочною частиною інструменту передбачається великий зазор. Хвостовики інструментів і розточувальних качалок забезпечуються в цьому випадкуповодковими штифтами, що легко заводяться в прорізі патрона.
Рисунок 3 - Патрон з штиковим замком
Дата добавления: 2018-05-09; просмотров: 391; Мы поможем в написании вашей работы! |
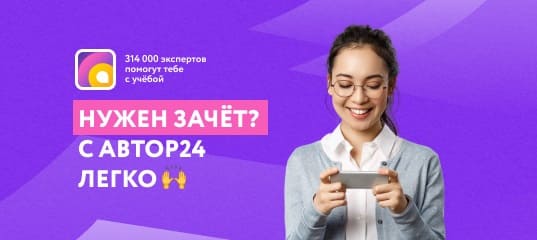
Мы поможем в написании ваших работ!