Автоматы и полуавтоматы параллельного, последовательного и параллельно-последовательного действия.
Простейшим структурным вариантом любой рабочей машины является однопозиционная машина, на которой осуществляется полностью или частично весь технологический процесс обработки, сборки или контроля изделий. Такие машины для выполнения заданного технологического процесса должны иметь минимально необходимый комплект механизмов рабочих и холостых ходов, привода, комплект инструмента и т. д. Так токарный одношпиндельный автомат должен иметь один шпиндель, один механизм зажима и подачи прутка, поперечные суппорты и т. д. (токарно-револьверные автоматы, автоматы фасонно-продольного точения). Отличительной чертой таких автоматов является последовательное использование всех инструментов технологического комплекта (возможно совмещение некоторых операций).
![]() |
Если технологический процесс дифференцирован, то есть каждая машина выполняет одну составную операцию, то она должна иметь полный комплект механизмов и устройств и инструментов из технологического комплекта.
В многопозиционных машинах, выполняющих весь дифференцированный и концентрированный технологический процесс, количество механизмов неизбежно увеличивается по сравнению с однопозиционной машиной. Так, многошпиндельные токарные автоматы и полуавтоматы, обрабатывающие те же детали, что и на т/р. автомате, должны иметь столько механизмов зажима и подачи прутка, сколько шпинделей имеет станок и идентичный технологический комплект инструмента.
|
|
![]() |
Таким образом, если в однопозиционных машинах общее время рабочего цикла определяется суммарной длительностью всех не совмещенных операций, то в многопозиционных интервал выпуска изделий равен длительности одной составной операции плюс время холостых ходов на загрузку и зажим деталей, подвод и отвод инструмента и т.д., что приводит к повышению производительности.
Дальнейший рост требований к производительности приводит к тому, что одна технологическая цепочка машин с дифференцированным технологическим процессом уже не в состоянии обеспечивать производственную программу. Отсюда появление многопоточных технологических машин.
![]() |
Исходя из изложенного различают машины последовательного, параллельного и последовательно-параллельного (смешанного) действия.
На машинах последовательного действиявсе операции выполняются последовательно на одном изделии по рабочим позициям в порядке, заданном технологическим маршрутом обработки детали. При этом весь технологический комплект инструмента рассредоточен по позициям обработки. Обработка на всех позициях происходит одновременно, после завершения которой производятся холостые ходы (перемещение деталей в следующую позицию, зажим и разжим заготовок, передача новой заготовки в I-ю позицию, подвод и отвод суппортов и т.д.). При этом каждая деталь последовательно проходит через все рабочие позиции, а длительность рабочего цикла машин (автоматов и полуавтоматов) равна интервалу выпуска одной детали.
|
|
По такому циклу работает большинство автоматов и полуавтоматов одношпиндельных и многошпиндельных, вертикальных и горизонтальных.
В машинах параллельного действия, как правило, в нескольких позициях одновременно выполняется одна и совмещенные с ней операции технологического процесса, а, следовательно, такие машины имеют один механизм рабочего хода (суппорт, инструментальный блок и др.). За каждый цикл работы таких автоматов со станка сходит одновременно столько деталей, сколько позиций имеется на станке. Длительность же рабочего цикла определяется временем срабатывания основных механизмов (суппортов, инструментальных блоков и др.).
Машины параллельно-последовательного или смешанного действия концентрируют как одноименные, так и разноименные операции. Такие машины применяются при сложных технологических процессах обработки и большой производственной программе.
|
|
Компоновка автоматов и полуавтоматов. В зависимости от технологических возможностей и назначения автоматы и полуавтоматы могут быть различного конструктивного исполнения.
Автоматы фасонно-продольного точения выполняются одношпиндельными для пруткового материала диаметром обычно до 12-16 мм и применяются для обработки детали большой длины и малых диаметров со сложным контуром с точностью по 5-8 квалитету, шероховатостью Ra=1,25 мкм. Они получили широкое распространение в часовой и приборостроительной промышленности, где используются для изготовления различные валы и оси. Повышенные требования к точности обработки и небольшая жесткость обрабатываемых деталей привели к необходимости применения люнетов, которые размещаются в кронштейне близко к месту обработки. В процессе обработки детали пруток, зажатый во вращающемся шпинделе, постепенно перемещается в осевом направлении на заданные величины, а инструменты поочередно подходят к прутку и производят обработку. Инструмент закрепляется в 4-5 поперечных суппорта. Помимо продольного и поперечного точения на таких автоматах можно осуществлять фасонную обработку, точение конусов, обработку отверстий, нарезание резьб и т.д.
|
|
Фасонно-отрезные автоматы, работающие из проволки, применяются для выполнения различных фасонно-отрезных работ из материала, диаметром до 8 мм. Чаще всего это обработка шпилек, винтов и других простейших по конструкции деталей. Обработанный материал при обработке деталей не вращается и остается зажатым между двумя зажимными механизмами, один из которых расположен спереди шпинделя, а другой позади него. Вращение получают суппортные головки. Кроме того, в процессе обработки инструменты получают поперечное перемещение. По окончании обработки детали и ее отрезки инструменты возвращаются в исходное положение, зажимные механизмы освобождают пруток и происходит подача новой порции материала, после чего цикл повторяется. Другой характерной особенностью станков этой системы является наличие механизма правки, который осуществляют с помощью роликов, между которыми пропускается проволока.
Одношпиндельные фасонно-отрезные автоматы применяются для обработки коротких деталей из прутка (прутковые) и штучных заготовок (магазинные, бункерные)с точностью по 8..13 квалитету и шероховатостью Ra=2мкм. Наибольшее распространение получили прутковые автоматы для прутков диаметром от 3 до 25 мм. Пруток или штучная заготовка зажимаются во вращающемся шпинделе, а резцы получают поперечную подачу. По окончании обработки детали в зону обработки либо подается новая заготовка, либо выдвигается пруток до упора. При обработке деталей на таких автоматах, как правило, используются фасонные инструменты.
Одношпиндельные токарно-револьверные автоматы применяются для обработки деталей сложной формы из прутков диаметром до 70мм. с точностью по 8..13 квалитету и шероховатостью Ra=2мкм. Автоматы имеют револьверную головку и 2-4 поперечных суппорта. Пруток подается из шпинделя на определенную величину и зажимается, после чего производится последовательная обработка инструментами, закрепленными в револьверной головке и в суппортах. После отрезки готовой детали пруток снова подается до упора на определенную величину и цикл повторяется.
Многошпиндельные автоматы последовательного действия проектируются, как правило, для обработки деталей из пруткового материала диаметром до 100мм, реже для обработки штучных заготовок с магазинным питанием и могут быть 4, 6, 8 и 12 шпиндельными. Автоматы имеют продольный суппорт и поперечные на каждую позицию, а также оснащаются разного рода приспособлениями, расширяющими технологические возможности автомата (резьбонарезное устройство, быстросверлильное, для фрезерования пазов, шлиц и др.). По окончании одного цикла шпиндельный блок поворачивается на одну или несколько позиций и цикл повторяется. За каждый цикл со станка сходит готовая деталь.
Многошпиндельные автоматы непрерывного действия применяются в основном для обработки штучных заготовок с бункерным или магазинным питанием. В процессе непрерывного карусельного вращения шпиндельного блока вокруг неподвижной колонны осуществляется обработка деталей либо путем перемещения заготовок относительно неподвижных инструментов, либо перемещением инструментов относительно заготовок. Полный поворот стола вокруг колонны соответствует времени обработки заготовки и удаления готовых деталей со станка. Как правило, такие автоматы применяются для обработки сравнительно несложных деталей.
Многошпиндельные фасонно-отрезные автоматы являются результатом развития одношпиндельных фасонно-отрезных автоматов и представляют собой, по существу, несколько соединенных в одном корпусе отдельных одношпиндельных автоматов, каждый из которых осуществляет полную обработку детали (автоматы параллельного действия). Они строятся обычно 2, 4, 6 и 8 шпиндельные.
Патронные и центровые многорезцовые одношпиндельные полуавтоматы широко применяются в крупносерийном и массовом производстве тяжелых и сложных работ. Весь процесс обработки производится автоматически, за исключением установки и закрепления заготовок, т.к. конфигурация заготовок в большинстве случаев требует сложных механизмов для автоматического зажима заготовок.
Такие полуавтоматы предназначены для выполнения различных операций, а поэтому кроме поперечных суппортов они снабжаются продольным суппортом. Детали большой длины можно обрабатывать в центрах одновременно несколькими продольными и поперечными суппортами, расположенными по ее длине на круглых скалках (направляющих). Применяя ряд специальных приспособлений, можно осуществлять обработку фасонных поверхностей.
Патронные и центровые полуавтоматы чаще строятся с горизонтальной осью и реже имеют вертикальную компоновку.
Револьверные полуавтоматы предназначены для сложных патронных и центровых работ, требующих большого количества последовательно работающих инструментов. Полуавтоматы этого типа получают все большее применение ввиду их мобильности и широких технологических возможностей в серийном и мелкосерийном производстве деталей длиной до 1750мм, а также деталей типа фланцев, дисков, шкивов, зубчатых колес и др. за один или несколько проходов. Станки могут оснащаться и устройствами для смены инструментов по программе, число которых может достигать 16.
Многошпиндельные полуавтоматы последовательного действия. По принципу действия не отличаются от многошпиндельных автоматов и предназначены для обработки штучных заготовок из различных материалов (втулки, кольца, гильзы, зубчатые колеса и др.). Отличием многошпиндельных горизонтальных полуавтоматов от аналогичных автоматов является отсутствие блока направляющих труб для поддержания вращающихся прутков и наличие зажимных, обычно пневматических патронов. Процесс смены готовой детали на заготовку осуществляется на специально для этого отведенной позиции и производится во время обработки на других позициях. Шпиндель в позиции загрузки не вращается. После установки заготовки оператор включает шпиндель и тем самым снимает блокировку от поворота шпиндельного блока.
Такие полуавтоматы получают широкое применение в крупносерийном и массовом производстве. На них можно выполнять самые разнообразные операции. При оснащении их специальными загрузочными устройствами они могут работать полностью по автоматическому циклу. По специальному заказу они могут выполняться с двойной индексацией шпиндельного блока, то есть могут работать как сдвоенные полуавтоматы с загрузкой в двух позициях, что позволяет обрабатывать одновременно две несложные детали. Производительность при этом значительно возрастает.
Вертикальные многошпиндельные полуавтоматы предназначены для обработки, в основном, крупногабаритных деталей большого диаметра и небольшой длины. Шпиндель в загрузочной позиции не вращается. В остальных позициях шпиндель вращается с частотой, необходимой по характеру обработки в данной позиции. Шпиндельный блок по окончании обработки во всех позициях по команде оператора поворачивается на одно деление вокруг неподвижной колонны, на гранях которой установлены суппорты. Все суппорты имеют независимый привод. Они могут осуществлять продольную и поперечную обработку, точение конусов и фасонных поверхностей.
Существуют полуавтоматы непрерывного действия с фасонно-продольной обработкой, многошпиндельные полуавтоматы непрерывного действия с невращающейся заготовкой, многошпиндельные полуавтоматы последовательного действия для обработки деталей неправильной формы (рычаги, автотракторные детали и т. д.) в основном для осевой обработки.
Ретроспектива развития ЧПУ.
Дальнейшее усовершенствование и развитие любой отрасли машиностроения немыслимо без широкой и комплексной автоматизации производственных процессов.
Известно, что на обработку резанием при изготовлении детали в настоящее время приходится 40-45% от общей трудоемкости, обработку давлением - 7-8%, сварочные процессы - 5-6% и т.д. на заготовительные операции, транспортирование, складирование деталей. Такое разделение сохранится как минимум до 2000 года, т.к. основная масса деталей изготовляются, и будут изготовляться из сталей и чугунов и только незначительная их часть из различных полимерных материалов. Кроме того, на обработку металлов резанием затрачивается значительно меньше энергии, чем на другие технологические процессы при лучшем качестве обрабатываемых поверхностей. Так при эл. физических методах обработки энергии требуется в 10 раз больше, чем при обработке резанием, а при обработке лучом лазера - в сто тысяч раз. Поэтому металлорежущие станки были, есть и будут основным технологическим оборудованием, но с ним произойдут радикальные изменения, что повлечет радикальные изменения и во всем машиностроении. Типаж металлорежущих станков весьма велик и разнообразен (9 групп,9 подгрупп, плюс целая масса станков специальных и специализированных). Большая часть этих станков приходится на долю единичного, мелкосерийного и серийного производства (около 75%). А это значит, что на каждом таком станке должен быть оператор. Возникает 1-я ПРОБЛЕММА - нехватка станочников. Так, в настоящее время, на 3 млн. станков приходится 2 млн. станочников. Кроме того, тяжело повышать производительность. При замене морально устаревшей модели станка новой, производительность может быть повышена, но в общем балансе времени она незначительна. В результате затраты времени на обработку с использованием станков общего назначения и специализированных в условиях мелкосерийного и серийного производства значительно превышают их для крупносерийного и массового производства. Применение же станков специальных, станков-автоматов и автоматических линий в условиях мелкосерийного и серийного производства крайне нежелательно. Это 2-я ПРОБЛЕММА.
Далее, доля затрат на складирование и транспортирование в условиях мелкосерийного и серийного производства значительно перекрывает по площадям долю затрат на заготовительные операции и размерную обработку деталей.
1.Затраты на заготовительные операции.
2.Затраты на размерную обработку на станках.
3.Затраты на транспортирование деталей.
4.Затраты на складирование деталей.
5.Затраты на различные финишные операции (отделочные работы, смазка, упаковка и т.д.).
Ликвидация затрат на транспортирование и складирование деталей является очередной ПРОБЛЕММОЙ в машиностроении. Необходимо решать вопросы, чтобы деталь со станка сходила в уже готовом виде и по каналам связи (транспортеры, конвейеры) передавалась на сборочные посты, минуя складские помещения.
С развитием автотракторостроения, авиастроения, ракетной техники, новейшей научно-исследовательской аппаратуры к металлообрабатывающему оборудованию предъявляется все больше и больше требований. Для новых отраслей характерно усложнение объектов производства. Так, в самом сложном современном автомобиле насчитывается более 4 тыс. наименований деталей, а самолет типа АН-22 - один из крупнейших в мире транспортных кораблей, содержит уже около 400 тыс. наименований деталей, нормалей и узлов. Пассажирский самолет средних размеров включает примерно 60 тыс. деталей. В конструкциях растет число совершенно оригинальных, не встречающихся ранее узлов и деталей. Решить задачу выпуска таких новых объектов в кратчайшие сроки, даже с использованием станков-автоматов и полуавтоматов практически невозможно. Для этого необходимо спроектировать и изготовить около 2000 копиров, 3-5 тыс. различных штампов, около 1000 кулачков, 15-20 тыс. шаблонов для измерения заготовок, деталей и узлов. Изготовление такого количества оснастки требует колоссальных затрат труда рабочих, что ведет к низким темпам изготовления машин, которые зачастую устаревают еще до того, как выйдут на испытания.
Можно констатировать, что в станках-автоматах и полуавтоматах высокая производительность достигнута за счет узкой специализации, приведшей к потере маневренности, гибкости и плохой адаптации станка к меняющимся объектам производства. Автоматизация движений в таких станках, их последовательность и продолжительность осуществляется применением различного рода кулачков, копиров, упоров и других кинематических элементов, которые в процессе работы быстро изнашивались, в результате чего точность обработки на таких станках снижалась и не превышала обычно третьего класса. Переналадка таких станков на обработку другой детали приводила к необходимости длительной регулировки многочисленных упоров и изготовлению новых кулачков высококвалифицированными лекальщиками.
Именно поэтому станки-автоматы и полуавтоматы эффективны лишь в условиях крупносерийного и массового производства с устойчивой номенклатурой изделий.
Однако такой тип производства дает в настоящее время менее 30% всей продукции машиностроения и приборостроения, а свыше 70% - производится в отраслях единичного, мелкосерийного и серийного производства с быстрой сменяемостью номенклатуры. Доля этих типов производства под влиянием воздействия НТР будет еще выше.
Таким образом, быстрые темпы обновления продукции машиностроения и приборостроения поставили на повестку дня ЗАДАЧУ создания универсального станка-автомата, обладающего и высокой производительностью, и достаточной гибкостью, и маневренностью в условиях современного динамического производства.
Для решения этих проблем призваны станки с ЧПУ, создание которых стало возможным благодаря бурному развитию электроники и вычислительной техники. Первое устройство ЧПУ было изобретено в 1949 году советскими специалистами А.Е.Кобринским, М.Г. Брейдо и В.К.Бесстрашновым. В 1955 г. был изготовлен макетный образец станка с ЧПУ, а в 1957 г. советский станок с ЧПУ демонстрировался на Всемирной выставке в Брюсселе, где он завоевал первую премию "Гран-при". В этом станке дозировка размерных перемещений осуществлялась с помощью механического шагового привода с анкерным механизмом.
С 1959 г. начинается все расширяющийся промышленный выпуск станков с ЧПУ. С этого времени начался 1-й ЭТАП в развитии станков с ЧПУ.
Для устройств ЧПУ первого поколения характерно применение полупроводниковых приборов и электронных машин. Широкое применение в этот период получил фрезерный станок модели 6Н13ГЭ-2 с шаговым эл.гидравлическим приводом. Программа записывалась в унитарном коде на магнитную ленту, что позволило значительно упростить электронную часть устройства и повысить ее надежность.
Простота устройств ЧПУ позволила быстро освоить их выпуск и эксплуатацию. Станки с этими устройствами ЧПУ оправдали себя, несмотря на ограниченные технологические возможности (отсутствие коррекции и др.) и трудоемкость подготовки программы на магнитной ленте.
Вскоре выяснилось, что ручной расчет и изготовление программ, особенно для обработки детали со сложными криволинейными поверхностями, крайне трудоемкая работа. При расчете требуется оперировать без округления многозначными цифрами, что приводит к появлению многочисленных ошибок и проведению многократных перепроверок и перерасчетов. Потребовалась организация больших служб инженеров и технологов программистов для выполнения таких расчетов.
В начале освоения станков с ЧПУ считалось, что основной областью применения ЧПУ станками станет единичное производство. Однако уже первые результаты промышленной эксплуатации показали, что трудности подготовки программы обусловили наиболее эффективное применение ЧПУ в мелкосерийном и серийном производстве, где партии деталей достаточно велики. В опытном производстве станки с ЧПУ нашли применение главным образом при обработке крупногабаритных деталей со сложной конфигурацией.
В России первый этап на большинстве предприятий завершился в 1960 - 62 гг. Опыт эксплуатации станков на этом этапе выявил следующие преимущества ЧПУ станками:
1. Снижение квалификации станочников;
2. Сокращение и упрощение технологической оснастки;
3. Повышение производительности за счет снижения машинного и вспомогательного времени.
ВТОРОЙ ЭТАП характеризуется резким увеличением внедрения станков с ЧПУ различных групп в различные отрасли промышленности. Совершенствуются конструкции и технические показатели отдельных узлов станков и систем ЧПУ. В станках применяют быстродействующий привод подач, высокоточные датчики, поворотные резцедержатели, револьверные головки и т.д.
Все больше находит применение контрольные автоматы с ЧПУ, промышленные роботы на сборочных и упаковочных операциях, основанные на принципах ЧПУ. Широкие возможности для внедрения роботов открываются в литейных, термических, гальванических цехах и кузнечно-штамповочном производстве.
Особую группу составляют станки с ЧПУ, получившие название "обрабатывающий центр" (много инструментальный, многооперационный). Эти станки могут выполнять полную обработку всех сторон детали, закрепленной на столе станка, за одну установку, производя разнородные операции: точение, сверление, фрезерование, нарезание резьбы и др. Такие станки имеют инструментальные магазины, в которых может устанавливаться до 138 различных инструментов и "автоматические руки" для смены инструмента в шпинделе станка. Кроме этого с помощью ЧПУ на этих станках осуществляются автоматические перемещения заготовки вдоль трех координатных осей и ее вращение вокруг вертикальной оси поворотного стола, а иногда и вокруг горизонтальной оси, что дает возможность осуществлять обработку сложных корпусных деталей при одном их закреплении. ПУ станка обеспечивает необходимое изменение скорости вращения шпинделя, величины рабочей подачи и скоростей холостых перемещений, а также включение и выключение других устройств станка.
Режущий инструмент помещается в револьверных головках или специальных инструментальных магазинах большой емкости, что делает возможным в соответствии с принятой программой автоматически устанавливать в шпинделе станка практически любой инструмент, необходимый для обработки соответствующей поверхности детали. Смена инструмента производится в течение 3-5 сек.
ЧПУ всеми движениями станка и поворотным столом, а также автоматическая смена большого числа режущих инструментов обеспечивает в некоторых моделях многооперационных станков получение до 500000 различных положений инструмента относительно обрабатываемой детали.
В отличие от обычных многошпиндельных станков – автоматов и автоматических линий, применяемых в массовом производстве повышение производительности на многооперационных станках достигается не за счет совмещения технологических переходов и параллельной много инструментальной обработки многих поверхностей, а вследствие резкого сокращения затрат вспомогательного и подготовительно-заключительного времени и интенсификации режимов резания. Так в условиях серийного и мелкосерийного производства доля машинного времени на прецизионных станках не превышает 18-20%, на станках с ЧПУ она увеличивается до 50-60%, а на многооперационных она достигает 80- 90%. Простой станка под наладкой сокращается в среднем на 80%. В результате этого производительность изготовления деталей на таких станках в 4-10 раз превышает производительность обработки на универсальных станках.
Важнейшим преимуществом многооперационных станков перед другими автоматизированными станками является простота их наладки и переналадки и отсутствие необходимости создания сложной технологической оснастки (шаблонов, копиров, приспособлений и т.д.). Это создает большую гибкость и мобильность производства, позволяющие применить многооперационные станки в условиях мелкосерийного и опытного производства. И, несмотря на высокую стоимость этих станков при правильной их эксплуатации с полной загрузкой в 2-3 смены окупаются в течение 1-2 лет.
Второй этап характеризуется и созданием систем автоматического расчета управляющих программ на ЭВМ. Разработка методов автоматического программирования и математического обеспечения оказал решающее значение на темпы развития ЧПУ станками в целом. Для ускорения решения вопросов программирования были созданы специальные системы автоматического программирования и машинного языка, рассчитанные на определенный тип станков и осуществляющие связь оператора с машиной (САП-2, САП-3, САПС-М32 и др.). В РОССИИ значительную роль в ускорении систем автоматического программирования и улучшении вопросов подготовки программ сыграли заводские бюро и созданные в 1973 г. кустовые территориальные центры по программированию. В последнее время начали внедряться способы задания информации голосом.
Использование принципов ЧПУ с широким привлечением ЭВМ позволяет автоматизировать инженерный труд. Созданы координатографы, графопостроители, которые работают в 25-30 раз быстрее человека и могут по сигналам управления выполнить многие сечения деталей, перевести цифровую модель детали в графическую форму, изменить масштаб построения, выполнить аксонометрическую проекцию изделия и т.д.
Появились и устройства, выполняющие противоположные функции - программаторы. Программаторы на основании чертежа или модели изделия создают его цифровую модель, а затем - управляющую программу для станка с ЧПУ.
С развитием электроники и вычислительной техники построен, изготовлен и находится в эксплуатации дисплей. Это устройство позволяет осуществлять визуальный диалог человека и машины в графических образах. Дисплей представляет весьма существенные возможности для автоматизации конструирования, выполнении конструкторских работ человеком в апре с ЭВМ и используется для ускорения отладки и внедрения УП станкам с ЧПУ непосредственно в цехе, возле станка. Оператор, с помощью специального светового луча может непосредственно у станка вносить изменения в чертеж детали на экране дисплея, которые сразу запоминаются машиной.
На основании устройств автоматизирующих конструкторскую и технологическую подготовку производство изделий, а также их непосредственного изготовления, контроль и сборку технические прогнозы обещают создание в 2000 году комплексов СЧД (система чертеж-деталь), в которой на протяжении всего цикла производства - от возникновения замысла до изготовления детали - рука и мозг человека не будут участвовать в производственных процессах.
Широкое использование ЭВМ при подготовке УП для станков с ЧПУ показало, что такие станки могут эффективно использоваться не только в мелкосерийном и единичном производстве, но и успешно решать задачи серийного и крупносерийного производства.
Однако даже такие станки, как обрабатывающие центры не всегда обеспечивают полную обработку детали, т.к. многие из них требуют дополнительных операций - термообработка, шлифование, доводка и т.д. Кроме того, на каждом станке с ЧПУ должен быть оператор и только иногда допускается многостаночное обслуживание. Эти обстоятельства привели к 3-му ЭТАПУ в развитии станков с ЧПУ.
Стремление распространить автоматизацию, достигаемую на автоматических линиях, на мелкие и средние партии обрабатываемых деталей привело к объединению нескольких обрабатывающих центров и станков с ЧПУ в участок (автоматическую станочную систему АС) с единым транспортным устройством и универсальным управлением. Создание автоматизированных участков и цехов, управляемых от одной линии ЭВМ, сопровождается разработкой станков с новыми конструктивными компоновками, учитывающими возможность работы в составе автоматизированного участка, промышленных роботов для загрузочно-разгрузочных операций, контрольных автоматов с ЧПУ, а также адаптивные системы к станкам.
Таким образом, получаются системы, обеспечивающие быструю переналадку на другое изделие и обладающие высокой гибкостью в противоположность жестким автоматическим линиям.
Первый гибкий комплекс "Rota-F-125М" (ГДР) в мировой практике демонстрировался в 1971 г. на Лейпцигской выставке. В комплекс входит семь станков с ЧПУ: 1-токарный, 3-токарноревольверных, 2-вертикальнофрезерных, 1-круглошлифовальный.
В РОССИИ в настоящее время эксплуатируется более 100 автоматических станочных систем типа АСК - для обработки корпусных деталей и АСВ - для обработки деталей типа тел вращения.
3-й ЭТАП в развитии станков с ЧПУ характеризуется и разработкой и оснащением станков с ЧПУ адаптивными системами и системами диагностики, позволяющими в любой момент времени быстро определить ту или иную неисправность станка, или определить приближение того или иного узла к критическому состоянию.
Понятие о ЧПУ станками.
Почти всякий автоматизированный станок можно рассматривать как станок с ПУ. Программоноситель в таких станках: кулачок, копир, шаблон, расположенные в определенных местах упоры и конечные выключатели являются программой формообразования детали. Он кинематически связан определенным образом с исполнительными узлами либо непосредственно (автоматы с РВ), либо через систему усиления и управления. При таком управлении для изменения величины перемещения исполнительного узла требуется смена параметров кинематической цепи (замена кулачков и копиров, переустановка упоров и т. д.).
В станках с ЧПУ программа формообразования и осуществления вспомогательных движений рабочих органов не связана со структурой и конструкцией станка. Эти станки характеризуются управлением, обеспечивающим быструю их переналадку без смены и перестановки механических элементов, т.е. бескопирным дистанционным управлением. Величины перемещения исполнительных узлов, определяющие форму и размеры детали задаются числами или какими-либо другими символами, отражающими форму траектории, величину, направление и скорость этого перемещения.
Программа для станков с ЧПУ обычно составляется заранее. Суть ее обычно состоит в следующем. По заданному технологическому процессу изготовления детали и ее чертежу разрабатывают программу перемещений режущего инструмента относительно заготовки, а также направления и величины подач этих перемещений. Эту программу кодируют, т.е. либо заменяют принятой условно системой чисел или знаков, которые затем фиксируют посредством пробивки отверстий на программоносителе- перфокарте или перфоленте, либо запоминаются каким-либо иным способом (магнитная запись на ленте, запись на киноленте и т.д.). В таком виде программа вводится в "считывающее" устройство станка, в котором "прочитанные" данные преобразуются в соответствующие командные импульсы, а последние с помощью управляющих механизмов подают сигналы на приводы исполнительных органов.
Таким образом, станками с ЧПУ называются станки, в систему автоматического управления которых вводятся числа или символы, отражающие величины перемещений исполнительных органов, участвующих в формообразовании изготовляемой детали или позиционировании заготовки и инструмента.
Классификация ЧПУ станками.
В СЧПУ программа работы станка задается в виде определенного комплекса чисел или знаков, записанных на программоносителе (перфоленте, магнитной ленте, перфокарте, ОЗУ и т.д.). Системами с программированием цикла и режимов работы оснащаются станки автоматы и полуавтоматы, а также станки с автоматической сменой режимов работы.
2. По принципу управления движениями: позиционные и контурные. Позиционные системы управления, в свою, очередь делятся на:
а) системы с установкой координат без определенного линейного перемещения между отдельными точками обработки с заданной точностью. При этом все исполнительные узлы могут перемещаться в любом направлении одновременно, но не взаимосвязано. Траектория движения инструмента при этом существенного значения не имеет и определяется в основном конструкцией станка и его кинематической схемой. Например, в станках сверлильно-расточной группы необходимо вначале установить ось сверла над центром будущего отверстия, что может осуществляться одновременным, но несогласованным движением сверла по осям X и Y, т.е. в плоскости, перпендикулярной оси сверла, а затем дать рабочее движение (т.е. подачу) по оси Z, вдоль оси сверла. Перемещения в таких системах задают в абсолютных координатах или приращениях, а работа систем основана на сравнении показаний абсолютных и неабсолютных датчиков перемещения с координатными данными, заданными программой.
б) системы с прямоугольным последовательным перемещением исполнительных органов от пункта к пункту в процессе формообразования детали. Такие системы можно назвать системами с программированием прямых, параллельных направлению движения исполнительных органов. Перемещения в позиционной системе с необходимой точностью, определяемой ее разрешающей способностью, как правило, задают в абсолютной системе координат, имеющей фиксированное начало отсчета, которое может изменяться по программе или вручную.
Рабочее движение в позиционных системах ПУ, т.е. движение подачи, всегда осуществляется по одной координате. Системами с программированием прямых могут считаться токарные, карусельные и фрезерные станки.
Системы контурного (непрерывного) управления являются функциональными. В таких системах производится непрерывное, одновременное и согласованное движение исполнительных органов и заготовки, что обеспечивает обработку криволинейных контуров и поверхностей на станках токарной, фрезерной, строгальной и др. групп. Программа задается в относительных координатах или в приращениях, определение которых на криволинейных участках контура производится автоматически, с помощью специальных устройств - интерполяторов.
Само собой разумеется, что контурные СПУ в принципе можно применять вместо позиционных, т.к. они также обеспечивают приход инструмента в заданную точку с высокой точностью, хотя координаты у них обычно заданны в относительной системе. Однако из-за наличия интерполятора контурные СПУ всегда были намного сложнее и дороже позиционных и в связи с этим их применяли только в станках, предназначенных для обработки деталей с криволинейными образующими взамен копировальных станков, где эффект от применения СПУ был особенно велик.
Появление инструментальных магазинов в среднем на 30-40 инструментов, необходимость в связи с этим автоматически изменять частоту вращения шпинделя в широких пределах, иметь коррекцию размеров инструментов и индикацию положений рабочих органов станка, упрощения программирования за счет введения стандартных циклов, переход на следящий режим позиционирования для обеспечения высокой точности - все это привело к резкому усложнению позиционных СПУ. Добавление в такую СПУ интерполятора не на много увеличивает ее сложность и стоимость, но делает ее универсальной.
В связи с этим большинство современных СПУ выполняют как универсальные. И только простейшие СПУ до некоторой степени сохраняют это разделение.
Подразделение СПУ на позиционные, контурные, универсальные привело к некоторым изменениям в нумерации и обозначении станков с ЧПУ. Так, в обозначении станков с ЧПУ обозначают дополнительным индексом в конце: Ф1 - станки с цифровой индикацией и пред набором координат, Ф2 - с позиционными системами ПУ, Ф3 – с контурными системами ПУ , Ф4 - с универсальными системами для позиционной и контурной обработки, С1, С2, С3 - количество управляемых координат. Например, токарный станок с контурной СПУ и управлением по 2-м координатам обозначают 1А616Ф3С2.
В зависимости от наличия или отсутствия обратной связи СПУ подразделяются на замкнутые и разомкнутые системы управления. Система управления с разомкнутым контуром значительно проще и дешевле в изготовлении, но в ней отсутствует контроль исполнения команды, что снижает ее точностные показатели. В СПУ с замкнутым контуром датчик обратной связи следит за положением исполнительного органа и вносит необходимые коррективы в работу СПУ. Такие системы обладают большей точностью, но они сложнее, менее надежны и соответственно дороже СПУ с разомкнутым контуром.
По характеру информации, выраженной в программе различают системы непрерывные, дискретные и дискретно-непрерывные.
Программа в СПУ с фазовой модуляцией считывается с магнитной ленты в виде синусоидального напряжения, имеющего угол сдвига фазы относительно опорного напряжения, пропорциональный заданному перемещению, а воспроизведенное движение контролируется датчиками перемещения также в угол сдвига фаз синусоидальных напряжений. Фаза напряжений, характеризующее заданное и фактическое перемещения, сравниваются в так называемом фазовом индикаторе, который выдает сигнал следящему приводу в виде выпрямленного напряжения. Фазовая система ПУ по сравнению с другими СПУ имеет минимальный объем электронного оборудования и надежные в работе датчики положения.
Дискретная (импульсная) система - это такие СПУ, в которых информация о перемещении инструмента или изделия выражена соответствующим числом импульсов.
В разомкнутых импульсных системах в качестве исполнительных устройств применяют шаговые двигатели, поэтому их часто называют шагово импульсными. В таких системах каждый импульс преобразуется в поворот вала шагового двигателя на определенный строго фиксированный угол. Число импульсов определяет величину перемещения, а частота их следования - скорость движения рабочего органа станка.
Замкнутые импульсные системы называют счетно-импульсными, т.к. в них использована счетная схема. В счетно-импульсных суммирующих системах величина перемещения рабочего органа задается в виде суммы импульсов. Каждому импульсу соответствует перемещение, например, на 0,01 мм. Заданное число импульсов фиксируется и сравнивается с числом импульсов, поступающих по мере перемещения рабочего органа от датчика обратной связи. Когда число импульсов, поступивших от датчика обратной связи сравняется с заданным числом импульсов, подается команда для прекращения движения рабочих органов.
Однако импульсные СПУ имеют и недостатки:
1. Возможность потери информации (пропадания импульсов программы), что приводит к изменению размеров детали.
2. Задание размеров в приращениях приводит к накопленной ошибке.
3. Введение в систему обратной связи с целью повышенной точности обработки усложняет конструкцию станка, снижает их надежность и долговечность.
Системы же с фазовой модуляцией в значительной мере свободны от этих недостатков благодаря непрерывному характеру управляющей информации, имеющей вид фазомодулированных синусоидальных сигналов переменного тока. Для получения информации в импульсных системах применяют преобразователь унитарного кода в фазовый, что обеспечивает простоту и надежность управления.
Шагово-импульсные системы применяют в станках с точностью обработки не выше +-0.1 мм и шероховатости поверхности 5-6 при максимальном времени обработки деталей в цикле не более 30-40 мин.
Счетно-импульсные системы с обратной связью находят применение в станках для обработки крупногабаритных деталей с циклом обработки до 2-3 часов, точностью до +- 0.1 мм и 5. Станки 6441Пр, ГФ-628, СФП-1, СФП-2 и др.
Дискретно-непрерывные системы подразделяются на аналого потенциометрические (АПСПУ) и импульсно-фазовые.
В АПСПУ происходит непрерывно воспроизведение и обработка текущих значений координатных точек траектории центра фрезы, вычисленных относительно начала координат, принятых для системы. АПСПУ является системой абсолютного отсчета со встроенным линейным интерполятором электромеханического типа. В системе предусмотрен датчик обратной связи потенциометрического типа. Программоносителем является обычно 80-колонковые перфокарты. В таких системах сравнивающие устройство сравнивает число импульсов, заданных программой с числом импульсов системы обратной связи (с числом фактически отработанных импульсов) и выдает аналоговый сигнал, пропорциональный отклонению скорости и величины перемещения рабочих органов станка от заданных программой. Этот сигнал образуется в результате отклонения от нулевого положения реверсивного счетчика, в котором выполняется одновременное сложение импульсов программы и вычитание импульсов обратной связи.
В импульсно-фазовых системах аналоговый сигнал управления образуется в результате сдвига по фазе последовательности импульсов обратной связи по отношению к последовательности импульсов программы.
АПСПУ обеспечивает выполнение следующих функций: работу станка в позиционном и контурном режиме, одновременную продольную и поперечную подачу при включенной вертикальной подаче, линейную интерполяцию контура детали, изменение положения начала координат в системе воспроизведения.
Таким образом АПСПУ характеризуется непрерывным управлением приводами продольной и поперечной подач и позиционным управлением приводом вертикальной подачи станка.
Системы ПУ, в которых помимо основного потока информации на перемещение какого-либо исполнительного узла по определенным направлениям с коррекцией или без коррекции этого перемещения, имеется ряд дополнительных воздействий в зависимости от факторов случайного характера (состояния режущей кромки инструмента, физические свойства обрабатываемого материала, тепловые колебания и другие силовые воздействия на систему СПИД), называются самонастраивающимися или адаптивными системами ПУ. Такие системы можно отнести к системам с программированием цикла и режима обработки.
Преимущества станков с ЧПУ
1. Высокая производительность за счет сокращения вспомогательного, Тп.з. и То. времени.
2. Исключение предварительных разметочных и пригоночных работ.
3. Повышение точности и идентичности деталей и, как следствие сокращение брака и пригоночных работ в процессе сборки.
4. Сокращение количества и упрощение конструкции технологической оснастки, что сокращает сроки технологической подготовки производства.
5. Обеспечивается экономия площадей для хранения деталей в процессе производства, готовых изделий, приспособлений, инструментов.
6. Значительное снижение квалификации оператора.
7. В связи с резким сокращением брака при работе на станках с ЧПУ, автоматической сменой инструмента и его перемещением относительно заготовки по программе значительно уменьшается объем контрольных операций и сокращается штат контролеров.
Благодаря этим преимуществам применение станков с ЧПУ целесообразно в следующих случаях:
1) сложные многочисленные и дорогостоящие операции по настройке и обработке;
2) обработка малыми партиями, особенно для сложных деталей;
3) деталь настолько сложная, что обработка ее в больших количествах приводит к появлению субъективных ошибок;
4) обработка деталей с большим количеством размеров, имеющих жесткие допуски, и детали с индивидуальными отклонениями размеров в партии;
5) обработка деталей подверженных конструктивным изменениям;
6) когда требуется весьма точная и дорогая оснастка;
7)сложность хранения инструментов;
8) расходы на контроль составляют значительную часть общей мости детали.
Дата добавления: 2018-05-02; просмотров: 1314; Мы поможем в написании вашей работы! |
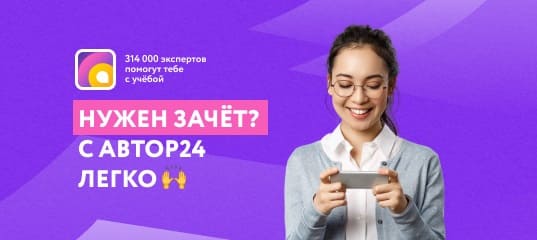
Мы поможем в написании ваших работ!