Значения скорости резания при точении стеклопластика
|
Сверление отверстий
Одной из наиболее часто встречающихся и в то же время наиболее трудоемкой операцией при обработке является операция сверления. Достаточно отметить, что трудоемкость сверлильных операций на некоторых изделиях достигает 70...80 % от общей трудоемкости процесса механической обработки. Естественно, что в этих условиях неправильный выбор режущего инструмента и режимов резания приводит к значительным издержкам.
Отверстия в ПКМ сверлят как в направлении армирующих волокон, так и перпендикулярно им, причем различают сверление отверстий сквозных и глухих. У глухих отверстий торец должен быть перпендикулярен оси. Требования к точности отверстий относительно невелики и не превышают, как правило, 11-й, 12-й квалитеты: параметр шероховатости поверхности должен соответствовать Rz > 20 мкм. При таких требованиях к точности и шероховатости поверхности в большинстве случаев удовлетворительные результаты получают при сверлении твердосплавными сверлами из быстрорежущей стали. Однако появление таких материалов, как боропластики, делает порой невозможным применение традиционных инструментов и приводит к необходимости применения инструментов из сверхтвердых материалов.
Процесс сверления ПКМсверлами из быстрорежущих сталей и твердых сплавов изучен достаточно полно. Что же каса-
280
3. ТЕХНОЛОГИЯ ИЗГОТОВЛЕНИЯ КОНСТРУКЦИЙ ИЗ МКМ И УУКМ
|
|
ется процесса алмазного сверления, то этот процесс изучен менее полно и порой сдерживает применение прогрессивного метода в промышленности.
Повышение производительности и качества сверления ПКМ возможно только за счет применения алмазного сверления. Полимерные ПКМ в отличие от традиционных материалов обладают всеми специфическими свойствами, присущими как армирующим волокнам, так и полимерной матрице. Влияние связующего сказывается в первую очередь на ограничении интенсивности обработки (по температуре) в зоне резания. Поэтому алмаз в данном случае является наилучшим инструментальным материалом. Обладая самой высокой твердостью, алмаз имеет коэффициент трения по пластмассе значительно меньший, а коэффициент теплопроводности больший, чем у твердых сплавов.
Алмазное сверление повышает производительность труда, уменьшает расход режущего инструмента и улучшает качество обработанной поверхности.
Алмазные абразивные сверла состоят из двух частей: алмазоносного слоя и металлической оправки, на которую этот слой наносится.
Проектирование алмазоносного слоя включает в себя назначение марки, зернистости алмазного порошка, связки и выбор способа изготовления алмазоносного слоя. Проведенные исследование позволяют с достаточной надежностью рекомендовать в качестве связки никель, а в качестве метода изготовления — гальваностегию.
|
|
Зернистость алмазного порошка является одной из важнейших характеристик алмазных сверл, так как оказывает значительное влияние практически на все показатели процесса алмазного сверления: качество обработанной поверхности, производительность и срок службы сверл.
Разрезка изделий
Разрезку изделий из композитов применяют для получения требуемых размеров и форм изделий из листовых материалов, плит и оболочек, используя ленточные и дисковые пилы, абразивные и алмазные круги, струи жидкости высокого давления, лазерный луч. При этом ленточные и дисковые пилы,
281
3.5. Механическая обработка композитов
дисковые фрезы (даже твердосплавные) обладают весьма низкой стойкостью, разрезка с их помощью малопроизводительна и не обеспечивает требуемого качества реза. Наиболее эффективный метод - разрезка абразивными и алмазными кругами.
Для разрезки рекомендуется применять абразивные круги из карборунда на вулканитовой и главным образом на бакелитовой связках твердостью от СМ1 до СТ1. Толщина круга составляет 1...4 мм, скорость вращения - 2500...3500 мин~\
|
|
Характерной особенностью процесса разрезки стеклопластиков абразивными кругами является их интенсивное изнашивание, которое заключается в выпадении отдельных зерен из-за сильного абразивного воздействия наполнителя обрабатываемого материала. Кроме того, круг весьма интенсивно засаливается связующим и продуктами деструкции полимера. Интенсивность засаливания падает при обильном охлаждении обычной водой. Однако использование охлаждения в ряде случае недопустимо: это существенно ограничивает область применения для разрезки абразивных кругов. В то же время опыт использования для разрезки пластиков алмазных отрезных кругов показывает, что применение алмазного инструмента по сравнению с абразивным дает увеличение скорости и производительности в полтора-три раза и стойкости в десятки раз при улучшении качества обработки. Кроме того, алмазные отрезные круги позволяют производить резку без охлаждения жидкостью.
В последние годы в нашей стране и за рубежом в промышленном масштабе используют резку ПКМ с применением лазеров. Использование пучка лазера обеспечивает получение точных, чистых резов при скоростях, в несколько раз превышающих скорости механического резания. Важными преимуществами лазерной резки являются: отсутствие силы резания, а значит, и деформаций, напряжений, расслоений и растрескивания разрезаемых стенок объекта производства, чрезвычайно узкий рез (0,2 мм), отсутствие особых требований к рабочей среде, малая зона термической деструкции, высокая точность и скорость резания. В состав лазерной установки для резания ПКМ входят: лазер (генератор излучения), оптическая система, система эвакуации продуктов резки, система подачи технологического газа и устройства для установки и перемещения объекта производства.
|
|
3. ТЕХНОЛОГИЯ ИЗГОТОВЛЕНИЯ КОНСТРУКЦИЙ ИЗ МКМ И УУКМ
Поскольку пучок лазера не передает силу на обрабатываемую стенку объекта производства, то вопросы конструирования технологической оснастки и оборудования существенно упрощаются. При использовании лазерных систем возможны четыре варианта организации технологической операционной системы (т.е. взаимного расположения и перемещения лазера, оптической системы и заготовки).
Лазерная головка неподвижно закреплена, а объект производства перемещается по заданной программе, формируя траекторию реза.
Лазерная головка перемещается над закрепленным объектом производства по заданной траектории.
Лазер и объект производства неподвижны, а пучок перемещается относительно объекта производства по заданной программе с помощью подвижных зеркал.
Комбинированная система: по одной из координат перемещается лазерный пучок, а по другой — объект производства.
Использование лазера на углекислом газе для резки ПКМ позволяет увеличить производительность операции в пять — десять раз и существенно улучшить санитарно-гигиенические условия труда.
Параметры режима лазерной резки приведены в табл. 3.5.
Таблица 3.5 Параметры лазерной резки ПКМ и волокнистых полуфабрикатов
ПКМ или полуфабрикаты | Толщина, мм | Скорость резки, м/с | Ширина резки, мм |
Стеклоткань МКТ | 5 | 0,8 | 0,5 |
Стеклоткань ТСФ | 1,5 | 5,0 | 0,4 |
Кварцевая ткань | 5 | 0,50 | 0,5 |
Стеклопластики на основе | 3 | 0,25 | 0,4 |
ткани МКТ и эпоксидного | 6 | 0,10 | 0,4 |
связующего | 9 | 0,05 | 0,7 |
Стеклотекстолит ПСД-Д | 15 | 0,01 | 0,8 |
Органопластик | 5 | 1,50 | 0,5 |
Боропластик | 3 | 0,30 | 0,4 |
Углепластик | 3 | 0,50 | 0,5 |
Кварцевое стекло | 1 | 0.02 | 0,2 |
282
283
3.5. Механическая обработка композитов |
|
Используется также резки ПКМ водяной струей, истекаю щей из сопла со скоростью 600...800 мм/с (рис. 3.21). Для получения потока с такой скоростью давление в технической системе для подачи воды должно быть равно 294...441 МПа.
Рис. 3.21.Схема гидрорезки: / — водяная струя; 2 — сопло форсунки; 3 - линия разреза; 4 — угол отклонения струи от прямого направления; 5 — разрезаемая деталь; 6 — направление движения сопла |
Для резки ПКМ используют
сопла диаметром 0,1...0,3 мм.
Расход воды составляет
1,04... 1,40 л/мин, скорость резания 100...4000 мм/мин.
Так как при сверхвысоких давлениях температура замерзания воды возрастает, то при давлении свыше 900 МПа можно применять водоглицериновую смесь, имеющую пониженную температуру замерзания.
При таких давлениях и скоростях водяная струя диаметром 0,1...0,3 мм имеет жесткость и твердость, присущую искусственному сапфиру и способна разрезать стенки из ПКМ толщиной до 25 мм.
Ширина реза составляет от 0,15 до 0,35 мм. Операция выполняется без образования пыли и запаха, в связи с чем обеспечивается высокая производительность труда. Разрезаемый материал остается сухим.
К недостаткам операции относят высокий уровень шума при обработке и необходимость тщательной фильтрации жидкости.
Дата добавления: 2018-05-02; просмотров: 839; Мы поможем в написании вашей работы! |
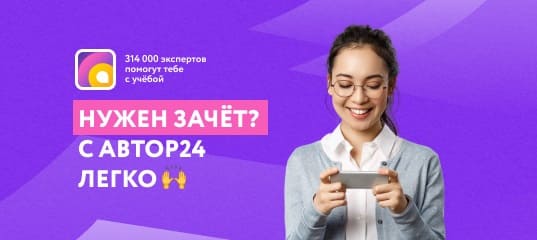
Мы поможем в написании ваших работ!