Производство санитарно-технических и бытовых изделий из тонкой керамики
ГЛАВА 9
ПРЕДПРИЯТИЯ ПО ПРОИЗВОДСТВУ САНИТАРНО-ТЕХНИЧЕСКИХ ИЗДЕЛИЙ
Краткая история развития санитарно-технических изделий. Классификация санитарно-технических изделий
Создание древних городов в долинах рек Нила и Инда, Тигра и Евфрата уже в IV тыс. до н. э. выдвинуло проблему водоснабжения и канализации жилищ. Скопление большого числа жителей при отсутствии самых простейших элементов благоустройства приводило к распространению опустошительных эпидемий. В борьбе с их последствиями возникли и стали развиваться основы гигиены, которые вначале выливались в форму обязательных религиозных ритуалов. Недаром во всех древних религиях есть предписания о чистоте тела, об омовениях и купаниях в священных водах. Согласно историческим данным, родиной гигиены считают Древнюю ведическую Славяно-Арийскую Империю, Индию, Тибет и другие регионы Земли, откуда гигиенические и медицинские знания быстро распространились по всему древнему миру.
Наиболее сложные санитарно-технические устройства прошлого были созданы славянами и ариями на Западных территориях, которые сейчас занимают Греция, Италия, Португалия, Франция, Англия, Германия и другие европейские страны. На Восточных территориях, в частности в Индии и Пакистане, в городах Хараппа и Мохенжо Даро в древности так же ариями были созданы сложные и очень эффективные санитарно-технические устройства и системы. По своим масштабам они нисколько не уступали современным сооружениям, а по качеству работы и по конструктивному оформлению не имели себе равных ни в эпоху феодализма, ни даже в начальный период развития капитализма.
|
|
Даже великолепные фонтаны и водопровод в Версале и Марли, во дворцах и парках Людовика XIV, считавшиеся величайшим достижением техники конца XVII в., не могут служить свидетельством прогресса санитарной техники в жилище. Ее новый расцвет приходится только на XVIII в., когда изобретенные во Франции в 1750 г. ватерклозеты были не только запатентованы в Англии (в 1775 г.), но начали входить в обиход с 1810— 1820 гг. После холерной эпидемии 1832 г., когда погибли тысячи людей, ватерклозеты сделались в Лондоне обязательными. Тогда же начали разрабатывать и изготовлять санитарный фаянс для ванн, раковин, клозета, умывальников.
Первые санитарные изделия, появившиеся во Франции, затем в Англии и Германии, готовили из беложгущейся пластичной глины, каолина, кварца и полевого шпата и обжигали при очень высокой температуре. Во Франции и Англии вместо полевого шпата, который в этих странах в чистом виде встречается реже, чем в Германии, к фаянсовой массе прибавлялся пегматит или корнваллийский камень. Англичане называли эти фаянсовые изделия белым гранитом, а немцы — твердым штейнгутом. Изделия отливали в гипсовых формах на гончарном круге. Покрывались они легкоплавкими глазурями, содержащими свинец.
|
|
Когда санитарные изделия стали массовыми, составы фаянса упростились, а глазурь стали применять с большим содержанием глинозема и добавками окиси олова. В настоящее время, согласно последним отечественным стандартам, керамические санитарно-строительные изделия изготовляются из фарфора, полуфарфора и фаянса.
К ним относятся:
- умывальники полукруглые, угловые, консольные и на постаменте, а также специальные для парикмахерских и хирургических;
- унитазы тарельчатые, с прямым и косым выпуском, козырьковые, детские, вагонные, уриналы (писсуары напольные);
- ванны ангобированные ножные, с плоским дном; бидэ;
- писсуары; бачки смывные; фонтанчики питьевые и т.п.
Унитаз представляет собой фарфоровую, металлическую или фаянсовую раковину в уборных для стока нечистот. На самом деле, унитаз это сложный механизм, превращающий потенциальную энергию воды в кинетическую и выполняющий при этом важную функцию смывания того, что в него попадает. Помимо этого, унитаз выполняет еще и важные санитарно-гигиенические функции.
|
|
Материалы изготовления унитазов. Как правило, унитазы производятся из тех же материалов, что и умывальники или ванны: из полимеров, стали или керамики, которая является самым распространенным материалом для оборудования бытового назначения. Сантехническая керамика имеет несколько разновидностей, среди которых при производстве унитазов активно используются фарфор и фаянс. Разница заключается в том, что в этих материалах имеются различные сырьевые компоненты и технологии обработки, что приводится к различным физическим свойствам у этих двух материалов.
Унитазы из сантехнического фаянса. Сантехнический фаянс покрывается обычно еще слоем глазури сверху, чтобы предохранить унитаз от агрессивных чистящих средств, обеспечить более эффективную очистку при смывании и придать изделию более привлекательный вид. Сантехнический фаянс имеет ряд недостатков, среди которых высокий уровень впитывания воды (9—12%) и значительная пористость.
Рис.9.1 Виды унитазов
Унитазы из сантехнического фарфора. Такой фарфор производят только из лучших сортов глины, что качественно отражается на его механической прочности и химической стойкости. У унитазов из сантехнического фарфора коэффициент впитывания воды гораздо ниже (не более 0,8%), чем у унитазов из других сортов керамики.
|
|
Обилие различных видов унитазов в зависимости от их цвета и формы уже никого не удивляет. Современные модели способны вписаться практически в любой интерьер. Все потому, что сегодня производители изготавливают как однотонные, так и окрашенные под цветной мрамор, а также разрисованные картинными сюжетами или классической росписью модели.
Для особо взыскательных людей новаторы придумали различные приятные функции унитазов. Сделать процесс как можно более комфортным помогут сиденья с подогревом, музыкальное сопровождение, антибактериальное излучение, функции дезодорации воздуха.
Писсуар, или как его еще называют уринал, чаще можно увидеть в общественных зонах, а также он является неотъемлемым сантехническими элементом в любых общественных помещениях (учебных заведениях, ресторанах, аэропортах, офисных помещениях и т.д.). Писсуар позволяет максимально обезопасить пользователей общественных туалетов от заражения инфекционными и вирусными заболеваниями.
Существуют 2 вида писсуаров, писсуары керамические напольные и настенные.
Настенный писсуары применяются, как правило, в общественных туалетах, административных, офисных или общественных зданиях (театры, кинотеатры, кафе и т.д.). Настенные писсуары подразделяются на:
- писсуары с цельно отлитым керамическим сифоном;
- писсуары без цельно отлитым керамическим сифоном;
- писсуары, удлиненные с цельно отлитым керамическим сифоном;
В комплект настенного писсуара входит: писсуарный кран или бачок и разводящие трубопроводы.
Писсуары напольные состоят из одной или нескольких секций-панелей, изготовленных из специального фаянса.
В стандартном проявлении писсуар изготавливается из керамики, однако в последнее время появились и другие материалы: различные полимеры, камень, эмалированный металл и пр.
Писсуары комплектуются встроенной электроникой, в частности датчиками (в основном инфракрасными) для обеспечения автоматического смывания. Данное дополнение одинаково полезно как в общественных уборных, так и в условиях офиса или дома.
Рис.9.2 Различные виды уринал (писсуаров)
По форме и размерам бидемало чем отличается от унитаза, функционально они тоже связаны друг с другом, и устанавливать их принято рядом.
Большинство биде изготавливаются из керамики различных видов. Это может быть керамика без покрытия или покрытая специальным защитным слоем, более устойчивым к повреждениям. Качество и цена в зависимости от использованных материалов тоже отличаются. Самые дешевые биде – из фаянса, значительно дороже – фарфоровые. Поверхность керамики может быть полированной или матовой. Возможно также применение специального покрытия, предотвращающее возникновение осадка или помогающее поддерживать керамику в чистоте.
Смесители для биде точно такие же, как для умывальников – отличаются только перлатором. Он находится на самом краю смесителя, на шаровом сгибе. Благодаря этому струю воды можно направить в любом направлении.
Рис.9.3 Различные виды биде
Смесители для биде могут быть с двумя вентилями (отдельный вентиль для холодной и горячей воды). Но самые популярные модели с одной ручкой, они же, наиболее удобны в использовании. Как вариант, можно купить для биде термостатическую батарею, которая будет поддерживать постоянную температуру воды, установленную пользователем, независимо от той температуры воды, которая подается.
Современные смесители – электронные – включаются и выключаются автоматически. Большинство смесителей для биде имеет одно отверстие, но есть и с тремя - слив в одном, регулировочный рычаг в двух остальных.
Умывальник– незаменимый элемент любой ванной комнаты. Умывальником мы пользуемся регулярно, по нескольку раз каждый день. Потому от правильного выбора этого небольшого, но значимого вида сантехнического оборудования зависит удобство и комфорт ваших ежедневных гигиенических процедур и даже ваше настроение.
На современном рынке сантехники представлен широчайший ассортимент умывальников для ванных комнат, который отвечает запросам самых притязательных покупателей.
Основные виды умывальников.
1. Умывальники для ванных комнат отличаются, прежде всего, по своей конструкции и способу установки.
Рис.9.4 Общий вид умывальников
Подвесные умывальники
– это так называемые раковины-консоль, которые монтируются к стене с помощью кронштейнов или на специальных дюбелях. Благодаря такому креплению, в ванной появляется ощущение пространства. Чтобы сохранить эту легкость, подберите декоративный сифон, причем желательно, чтобы сливные трубы были скрыты в стене непосредственно под умывальником, либо приобретите умывальник с полупъедесталом, который их скроет. Такой подвесной умывальник будет выглядеть гармонично и красиво даже в небольшой ванной комнате.
Настольные умывальники бывают нескольких видов.
Накладные умывальники размещаются в ванной непосредственно на стол, тумбу или шкафчик, могут иметь разнообразную форму, например, глубокой чаши, тазика или почти плоской тарелки. Накладные раковины выглядят очень интересно, даже необычно, они станут одним из самых ярких и привлекательных предметов в Вашей ванной комнате. Однако многим такие умывальники могут показаться неудобными и непрактичными. К тому же к ним особенно тщательно нужно подбирать смеситель – раковина-чаша обычно не имеет отверстия для смесителя, а он, в свою очередь, может потребоваться только с высоким изливом.
Врезные умывальники встраиваются в столешницу, образуя с ней почти ровную поверхность либо частично выступая над ней (полуврезные раковины). Такие раковины еще иногда называют «мебельными», так как чаще всего они являются составной частью гарнитура для ванной комнаты, который может включать большую столешницу, шкафчики, зеркала, полочки и др. Все это создаст Вам максимум комфорта в ванной. Слабым местом врезных умывальников являются соединительные швы с поверхностью стола, они требуют тщательного монтажа и внимательного ухода.
Более надежный и герметичный в этом плане – умывальник-столешница, который представляет собой единую, монолитную систему и позволяет во время умывания иметь под рукой все необходимое.
Напольные умывальники
- устанавливаются на пол с помощью опоры, в качестве которой чаще всего выступает специальная ножка – пьедестал или постамент. Одновременно они выполняют функцию маскировки сливных труб и сантехнической арматуры. Умывальник-«тюльпан» отлично подойдет для просторной ванной, выполненной в классическом стиле с элементами барокко.
2. По месту расположения
различают умывальники стандартные, которые размещаются у стены, угловые (помогут эффективно использовать всю территорию маленькой комнаты) и отдельно стоящие, их можно вмонтировать в столешницу или прямо в пол. Последний вид умывальников особо популярен в связи с использованием его в качестве миниатюрного таза для стирки, зачастую его устанавливают в дополнение к стандартным раковинам.
3. Форма умывальников
Современные умывальники отличаются своим многообразием и оригинальностью: кроме классического умывальника Вы найдете прямоугольные, квадратные, круглые, овальные, в виде ромба, капли и других простых и замысловатых, симметричных и асимметричных форм.
4. Материалы, из которых производят умывальники, весьма разнообразны
Их перечень расширяется, а технологии совершенствуются. Сегодня можно купить умывальник из керамики, стали, натурального камня, композитных материалов, из специального стекла и даже из дерева. У каждого из этих видов умывальников есть свои достоинства и недостатки. Например, стальные умывальники легкие и доступные по ценам, но при использовании издают много шума, могут легко поцарапаться, погнуться, а чтобы они идеально выглядели, за ними нужен тщательный уход. Раковины из мрамора очень эффектные, прочные и устойчивые к различным агрессивным средам, но тяжелые и дорогостоящие, а умывальники на основе камня имеют меньший вес, проще чистятся, но менее прочные. Стеклянные умывальники пленяют своей изысканностью и прозрачностью, они достаточно прочные и уход за ними несложный.
Наиболее популярны умывальники из белой керамики. Делают их из фарфора и фаянса. Предпочтительнее выбрать умывальник из фарфора. Считается, что он более прочный и плотный, меньше поддается загрязнению, но стоимость его выше. Некоторые производители покрывают свою керамическую сантехническую продукцию специально разработанным грязеотталкивающим слоем, что, несомненно, увеличивает их потребительские качества.
Крупногабаритные изделия специального назначения (лечебные ванны и лабораторные раковины) производят из шамотированного фаянса. Разработка санитарно-технических изделий ведется в двух направлениях. Одно заключается в конструировании приборов с минимальными удобствами, предназначенных для массового производства, другое — в создании небольших партий изделий, отвечающих требованиям повышенного комфорта. Для авторов санитарных приборов массового производства и применения характерно стремление к максимальной технологичности, механизации основных производственных операций, сокращающих ручной труд, а это неизбежно влияет на форму изделий, простую и лаконичную.
Ванные.
Поэтому до сих пор выпускаются изделия, очень похожие, например, на приборы начала века; санитарные приборы типа «Компакт» вот уже два десятилетия устанавливаются в наших домах, не претерпевая никаких изменений. В то же время немассовые изделия отличаются более пластичной и скульптурной формой.
Ванны, раковины и другое оборудование санитарно-технических узлов жилых и производственных помещений изготовляют из фаянса, полуфарфора и фарфора. Сырьем для производства этих трех разновидностей керамических материалов, обладающих различной пористостью являются беложгущиеся глины, каолины, кварц и полевой шпат, взятые в различных соотношениях.
Из фаянса преимущественно методом литья изготовляют унитазы, умывальники, смывные бачки и др. Для производства крупных изделии (ванн, моек и пр.) используют шамотный фаянс, в который вместо кварца вводят шамот (10-15%). Водопоглощеиие фаянса 10-12%, предел прочности при сжатии обычно до 100 МПа. Поверхность фаянсовых изделий покрывают глазурью, что придает им водонепроницаемость.
Рис.9.5 Ванная комната
Рис.9.6 Угловая ванна
К сожалению, повышение эстетических качеств отдельных приборов не позволяет рассчитывать на существенное повышение бытового комфорта. Ибо пока и в планировке, и в конструировании, и в оборудовании существующих санкабин отражено лишь основное требование жилищного строительства — экономичность. Это не значит, что не надо работать над улучшением формы и качества санитарных приборов.
Рис.9.7 Акриловая ванна
По сравнению с фаянсом полуфарфор имеет более спекшийся черепок (водопоглощеиие 3-5 %) и его прочность выше (Rсж =150-200 МПа). Фарфор отличается еще большей плотностью (водопоглощеиие 0,2-0,5%) прочностью (до 500 МПа), что позволяет изготовлять из него тонкостенные изделия.
Керамика (греч. Keramike - гончарное искусство, от kéramos - глина) - изделия и материалы, получаемые спеканием глин и их смесей с минеральными добавками, а также окислов и др. неорганических соединений.
Керамика получила широкое распространение во всех областях жизни - в быту (различная посуда), строительстве (кирпич, черепица, трубы, плитки, изразцы, скульптурные детали), в технике, на железнодорожном, водном и воздушном транспорте, в скульптуре и прикладном искусстве.
Рис.9.8 Деревянная ванна для бани
Рис.9.9 Ванна из камня
Рис.9.10 Гидромассажная медицинская ванна
Основными технологическими видами керамики являются терракота, майолика, фаянс, каменная масса и фарфор.
Тонкая керамика - группа материалов с тонкозернистым и однородным по структуре керамическим телом, разделенная по плотности на два класса: плотные спекшиеся и неполностью спекшиеся мелкопористые. К первому классу относят: твердый фарфор (хозяйственный, технический, электротехнический, химический и др.); мягкий фарфор (хозяйственный и художественный); тонкокаменные изделия (кислотоупорные). Ко второму классу относят: полуфарфор (хозяйственный, технический, санитарно-технические изделия, облицовочные плитки и др.); майолика и фаянс (хозяйственная посуда, декоративные изделия и др.).
Изделия тонкой керамики изготовляют на основе трехкомпонентных традиционных сырьевых масс, включающих пластичное сырье, отощающие материалы и плавни в отношении примерно (%-масс.);50:25:25. В качестве пластичного сырья используют каолины и огнеупорные беложгущиеся глины с минимальным содержанием вредных примесей (Fe203 + ТiO2 не более 1%). Для повышения пластичности масс возможно введение 17-30% низкоспекающихся глин с содержанием не более 1,5% Fe203 и 1,25% TiO2. В качестве отощающих в тонкокерамические массы вводят жильный кварц, чистые кварцевые пески или тонкомолотый бой неглазурованных изделий. Плавнями служат полевые шпаты, пегматиты, сиениты, а также материалы, содержащие щелочноземельные элементы (мел, доломит).
Тонкокерамические массы требуют особенно тщательной подготовки. При этом на каждом ее этапе должна быть гарантирована защита керамической массы от загрязнения красящими оксидами. Для измельчения сухих глинистых материалов применяют глинорезки, молотковые дробилки, дезинтеграторы. Тонкий помол непластичных материалов производят в шаровых мельницах периодического или непрерывного действия сухим или мокрым способом с использованием в качестве мелющих тел кремниевой гальки, фарфоровых шаров или шаров из высокоглиноземистых масс типа «Уралит». Длительность помола составляет 6-12 ч. Глинистые материалы после грубого измельчения распускают в воде в лопастных или пропеллерных мешалках.
Формуют тонкокерамические изделия из сухих порошков, пластичных масс и жидких шликеров, но, как правило, во всех случаях первый этап приготовления тонкокерамических масс - получение шликера. Этот способ обеспечивает наилучшее разрушение природной структуры глин и его преимущество высокая однородность исходной шихты.
Для подготовки первичного шликера отдозированные и измельченные непластичные материалы и глинистый шликер смешивают в пропеллерной мешалке 40 - 90 мин и пропускают через вибросито для очистки от крупных включений. Усреднение и хранение массы осуществляется в сборных бассейнах лопастными тихоходными мешалками. Обычно полученный в мешалках шликер имеет влажность 50-65%. Для снижения ее в шликер вводят электролиты (жидкое стекло и др.), позволяющие при сохранении текучести снизить влажность до 32-33%.
Из жидких шликеров методом водного литья можно изготовлять изделия как простой формы (плитка), так и сложной (санитарно-технические изделия). Однако учитывая положительные стороны шликерного способа подготовки масс (высокое качество) и его недостатки (повышенный расход топлива), большую часть шликеров подвергают предварительному обезвоживанию. Для формования пластическим способом его обезвоживают на фильтр-прессах до влажности около 25% (фото.9.11). При производстве высококачественных изделий дополнительно дважды повторяют обработку массы на вакуум-мялках сначала в массозаготовительном, а затем в формовочном цехе. При этом из массы удаляются вредные примеси.
Фото 9.11 Фильтр пресс
Для подготовки масс к полусухому прессованию шликера обезвоживают в распылительных сушилках (рис.9.12). Суспензию распыляют через форсунки, расположенные тангенциально к внутренней проверхности сушильной камеры. Сушка капель суспензии происходит во взвешенном состоянии в течение 15-30 с в противотоке с потоком теплоносителя. Распылительная сушка позволяет механизировать процесс и дает возможность получать пресс-порошки из практически сферических гранул практически одного размера (30-40 мкм), обладающих высокой сыпучестью. Выбор способов подготовки масс и формования определяется видом изделий тонкой керамики.
Сформованный полуфабрикат подвергают сушке. Для изделий тонкой керамики наряду с традиционными способами конвенктивной сушки в сушилках с воздушным или паровоздушным теплоносителем применяют и другие способы сушки. Чаще всего используют радиационный метод, когда сушильным агентом также является воздух, но он служит в основном для отвода влаги от высушиваемых изделий, а нагревание изделий и выделение влаги происходят за счет радиационного нагрева от теплоизлучателей (газовые беспламенные горелки, электролампы инфракрасного излучения и др.).
Рис.9.12 Распылительная сушилка: 1 — камера сушки; 2 — форсунка; 3 — шнек для выгрузки высушенного материала; 4 — циклон; 5 — рукавный фильтр; 6 — вентилятор; 7 — калорифер.
Высокочастотная сушка основана на превращении электрического тока частотой (1-6 МГц) в тепловую энергию при прохождении через влажное тело. В этом случае полуфабрикат сушится не только с поверхности, но и по всему объему, что приводит к существенному сокращению времени сушки.
Специфическая операция в технологии тонкой керамики - глазурование. Глазурь - тонкое (0,1-0,3 мм) стекловидное покрытие, образующееся при обжиге на керамическом изделии в результате плавления ее компонентов, нанесенных на изделие в виде водной суспензии. Глазурование повышает атмосферо и химстойкость изделий, их водо и газонепроницаемость, улучшает эстетические и декоративные свойства. В то же время правильно подобранная глазурь «залечивает» поверхностные трещины полуфабриката и повышает прочность изделий при сжатии на 40-50, при изгибе - на 30-40%.
Сложность подбора глазури состоит в том, что, с одной стороны, температура ее плавления должна строго находиться в пределах интервала спекшегося состояния, так как розлив глазури на пористом изделии приводит к ее впитыванию в подложку, а розлив на плотном изделии - к стеканию. С другой стороны, хотя при обжиге глазурь взаимодействует с подложкой и образуется промежуточный слой, обеспечивающий их сцепление, глазурь и подложка имеют разный температурный коэффициент линейного расширения (ТКЛР) и различие между ними более чем в 20-30% приводит к трещинообразованию (цеку) или отслаиванию глазури. По температуре розлива различают глазури: тугоплавкие, предназначенные для глазурования фарфора, с температурой розлива 1250-1400°С, и легкоплавкие, предназначенные для глазурования фаянса гончарных изделий, с температурой розлива 900-1250°С.
Сырьем для приготовления тугоплавких глазурей служат полевой шпат, кварц, каолин, а также добавки мела и магнезита. Исходные материалы подвергают совместному мокрому помолу в шаровой мельнице и полученную водную суспензию наносят на изделия.
Для снижения температуры розлива легкоплавких глазурей в них дополнительно вводят соли щелочных или щелочноземельных элементов, а также соединения свинца. Поскольку легкоплавкие глазури содержат водорастворимые компоненты, а также оксиды свинца, исходную шихту подвергают фриттованию - сплавлению с частью кварца, входящего в состав глазури. Это необходимо, так как водорастворимые компоненты, переходя в глазурный шликер, вызывают нарушение однородности получаемого покрытия за счет их концентрации в поверхностных слоях, а свинец обуславливает его токсичность. При фриттовании в результате взаимодействия с кремнеземом водорастворимые компоненты шихты становятся нерастворимыми, а свинецсодержащие соединения - нетоксичными. Полученный стеклообразный состав (фритту) гранулируют, выливая в воду, гранулы измельчают мокрым помолом с добавлением недостающих компонентов, и полученный глазурный шликер наносят на изделия. Соответственно такие глазури называют фриттованными, а тугоплавкие, не подвергаемые предварительной обработке, сырыми.
По прозрачности глазури различают на глухие и прозрачные. Цвет и непрозрачность глухих обусловлены введением специальных добавок-глушителей (оксиды олова, циркония, цинка и др.), выделяющихся в глазури в виде микрокристаллов соответствующей твердой фазы. Их наносят на облицовочные плитки и санитарно-технические изделия из фаянса и полуфарфора, изготовленные с использованием окрашенных глин. Окраска цветных прозрачных глазурей также обусловлена введением красителей - оксидов или солей металлов с переменной валентностью (Си, Ni, Со, Сг, Мп). Растворяясь в глазурном слое, красители придают ему соответствующий оттенок вследствие образования окрашенных силикатов.
Нанесению глазури предшествует очистка поверхности от жирных пятен и пыли щетками или сжатым воздухом под высоким давлением. Глазурный шликер наносят на изделия разными способами - окунанием, пульверизацией либо поливом на конвейере.
Глазурование толстостенных изделий проводят после их сушки. Тонкостенные изделия во избежание их размокания в глазурном шликере и последующей деформации сначала подвергают предварительному утельному обжигу, а затем глазурованию.
Производство санитарно-технических и бытовых изделий из тонкой керамики
Санитарно-технические изделия (умывальники, столы, унитазы, ванны и др.) отличаются большими размерами и массой. Поэтому к их прочности и термостойкости предъявляются особо высокие требования, которые должны быть обеспечены тщательной подготовкой сырьевых шихт, а также особыми режимами сушки и обжига.
Изготовляют санитарно-технические изделия из фарфоровых, полуфарфоровых и фаянсовых масс, которые отличаются составом, степенью спекания и пористостью. Фаянсовые изделия имеют мелкозернистую пористую структуру, окраску белую или любую светлую однородную. Фаянс не просвечивает на свету и в неглазурованном виде впитывает и пропускает воду. Фарфоровые изделия имеют плотную спекшуюся структуру, цвет белый. Фарфор в тонком слое просвечивает на свету и не пропускает воду даже в неглазурованном виде. Полуфарфор занимает по свойствам промежуточное положение между фарфором и фаянсом.
Изделия санитарно-технической керамики отличаются сложными формами, поэтому их формуют, в основном, способом литья в пористые (чаще гипсовые) формы, где в течение определенного времени происходит «набор массы», то есть процесс образования на стенках пористой формы уплотненного и до некоторой степени обезвоженного слоя минерального вещества за счет отсоса влаги внутрь пор формы вследствие капиллярного давления.
Различают два варианта шликерного литья (сливной и наливной). При сливном способе после набора на внутренней стороне формы уплотнившегося слоя массы требуемой толщины оставшийся шликер выливают из формы. Его применяют для формования полых тонкостенных изделий с толщиной стенки 3-5 см.
Основным сырьем для производства санитарно-технических изделий служат беложгущиеся огнеупорные глины, каолин, кварц, полевой шпат. За счет разного их соотношения в шихте обеспечивается различная степень спекания изделий.
Рис.9.13 Конвейер по производству керамических умывальников
Рис.9.14 Робот манипулятор по производству унитазов
Сырьевые материалы подвергают тщательной переработке: помолу, отмучиванию, просеиванию с целью получения тонкоизмельченной шихты. Готовят массы, как правило, шликерным способом.
Рис.9.15 Печь для обжига сливных бачков
При наливном способе процесс набора массы продолжается до тех пор, пока ею не будет заполнена вся полость формы. Значительная убыль объема шликера за счет удаления из него воды компенсируется его периодической доливкой или непрерывным поступлением из заранее заполненной воронки, стоящей над формой (рис.). Этот вариант применяют для изготовления массивных сплошных изделий, а также полых толстостенных деталей. Формы при наливном способе должны быть обязательно разъемными для выгрузки сформованного полуфабриката.
Литье — формование изделий сложной конфигурации (унитазы, умывальные столы и т. д.) в гипсовых формах, основанное на способности пористой гипсовой формы отсасывать часть воды из залитой в нее шликерной массы. Вследствие диффузии и испарения воды масса уплотняется (происходит набор черепка), уменьшается в объеме и свободно отделяется от формы. Срок уплотнения всей шликерной массы зависит от литейных свойств самой массы, гипсовых форм, температуры и влажности окружающей среды.
В настоящее время распространены три способа отливки изделий в гипсовых формах: наливной, сливной и комбинированный (рис.9.18). Наливной способ применяется для изготовления смывных бачков, унитазов и других изделий, имеющих большую толщину стенок.
Рис.9.16 Робот по качественному осмотру унитазов
Рис.9.17 Тепловые установки для производства сантехники
Рис.9.18 Способы отливки в гипсовых формах а — наливной; б — сливной; в — комбинированный
Для этого используют разборные формы сложной конструкции, которые собирают в батареи по 16—20 шт. и скрепляют металлическими стяжками. Набор черепка происходит между двумя стенками формы, в которую подается шликер. Излишки шликера через 1—3 ч сливаются через отверстия, расположенные внизу формы. Через 7—16 ч после закрепления черепка изделия освобождают от форм, оправляют и прикрепляют отдельно отлитые части к корпусу изделия.
При сливном способе излишки шликера из формы выливают после того, как на ее внутренней поверхности сформировался уплотненный слой массы толщиной 9—11 мм. Сливным способом отливают тонкостенные изделия, умывальные столы.
Комбинированным способом литья, при котором одни части изделия выполняют наливным, а другие сливным методом и затем соединяют, изготовляют умывальные столы, писсуары и т. д. Литье изделий производят на специальных стендах или на литейно-подвялочных конвейерах СМ-461А и СМ-462А (рис. 5). Отливка изделий на стенде требует больших площадей и затрат ручного труда на очистку форм, сборку, промазку и заливку шликера, разбор формы, освобождение изделий, их оправку и зачистку и не позволяет автоматизировать процесс литья.
Рис.9.19 Схема литейно-подвялочного конвейера СМ-462А 1 — гидротолкатель верхний; 2 — гидроподъемник; 3 — механизм слива шликера; 4 — камера; 5 — механизм заливки шликера; 6 — тележки; 7 — гидротолкатель нижний; 8 — подвялочный конвейер; 9 — пневмоподъемник; 10 - монорельс уборки отходов; 11 — механизм съема изделий; 12 — конвейер возврата воронок и колышков
Формование умывальников и унитазов на литейно-подвялочном конвейере включает следующие операции: подготовка гипсовых форм, заливка шликера, набор и закрепление черепка, слив шликера, разборка форм, оправка, подвялка изделий и сушка форм. Литейно-подвялочные конвейеры представляют собой двухъярусный тележечный конвейер. Тележки с формами проталкиваются и перемещаются с одного яруса на другой гидравлическими толкателями и подъемниками. На первом ярусе готовят формы и заливают шликер. Затем тележки с формами проталкиваются в камеры набора черепка с температурой 35—40 °С, длина которых составляет 2/3 длины конвейера. Эти камеры тележки с формами проходят за 1,5 ч, после чего с помощью автоматического устройства каретка с формой наклоняется, и излишек шликера сливается. В конце нижнего яруса каретки с формами гидроподъемником подаются на второй ярус конвейера и проталкиваются толкателем в камеру закрепления черепка. Продолжительность этого процесса 3 ч, температура 35—50 °С. Затем тележка с формой опускается снова на нижний ярус. На нижнем ярусе рабочие открывают гипсовую форму, извлекают отлитое изделие, устраняют дефекты, подвяливают и снова оправляют его, а затем подают в сушильную камеру. Освобожденные формы перед очередной заливкой шликера высушивают при температуре 55— 60 °С.
Ванны, мойки, радиаторы и другие крупные толстостенные изделия изготовляют способом литья из шамотированных масс. Для получения шликера необходимой текучести при минимальной влажности добавляют электролиты.
Производство акриловых ванн
Если быть точными, то общеупотребительное словосочетание "акриловая ванна" не совсем правильное. Обычно так говорят об изделиях, изготовленных из сантехнического полиметилметакрилата. Это синтетический полимер, который относится к категории термопластов, способных при нагревании до определенной температуры размягчаться и принимать задаваемую им форму, а при охлаждении - сохранять ее. Материал называют еще сантехническим акрилом. Поэтому, чтобы не запутаться в терминах, в дальнейшем изложении мы будем пользоваться привычным выражением акриловая ванна.
Акриловые ванны - европейское увлечение, хотя чаще данный материал используется для душевых поддонов и, в особенности, для гидромассажных ванн. Европа с большим удовольствием перешла на акрил, известный там уже 30 лет. У нас же акриловые ванны широкое распространение получили в последние 10 лет, и сейчас в магазинах сантехники присутствуют как импортные, так и отечественные образцы.
Акрил сам по себе материал прозрачный, но для ванн используется молочно-белый акрил, в которые еще при отливке акрилового листа добавляется специальный порошок, придающий ему характерный цвет и непрозрачность. Поэтому поверхность акриловых изделий глянцевая, свет на ней переливается и играет.
Процесс изготовления ванн состоит из нескольких этапов. Для создания объема нужной формы применяется термопневмоформовка или вакуумная вытяжка. Акриловый лист толщиной 4-5 мм нагревают до 130-160 °C, что делает его податливым и эластичным, а затем формуют в пресс-форме, после чего охлаждают. Второй важный этап производства - армирование заготовки. Для этого ванну с наружной стороны покрывают смесью разогретой эпоксидной (или полиэстеровой) смолы и стекловолокна (резаной капроновой нити). Застывая, смесь придает изделию жесткость и прочность. Для равномерного застывания смеси и снятия внутренних и поверхностных напряжений ванну сушат в термопечи. Из отечественных производителей данную установку в настоящее время используют Akrilan и Doctor Jet. Далее края акриловой чаши обрезают, удаляют облой, тем самым формируя бортики ванны. Чем больше слоев армирования, тем надежнее и прочнее ванна. Поскольку каждый слой требует сушки, весь процесс изготовления качественного изделия может занимать до 24 часов. Соответственно с увеличением количества армирующих слоев растет и цена самой ванны.
Для создания моделей сложной формы требуется более пластичных акрил, а среди акрилов надежными считаются те, что жестче, но они не так-то легко поддаются формовке. Так что здесь - либо причудливый дизайн, либо - высокая износостойкость, что-то одно.
Чистый листовой акрил (его еще называют литьевым акрилом) - материал очень дорогой, и ванны из листов толщиной 4 и 6 мм при равных условиях будут отличаться по цене в два-три раза. Некоторые производители (Teuco, Guzzini, Doctor Jet и др.) наряду с традиционным акрилом используют экструдированные полимерные материалы, например, листы двухслойного сантехнического пластика толщиной от 4 до 8 мм. У такого пластика верхняя (лицевая) сторона акриловая (слой 1-1,5 мм), а нижняя (несущая) - из прочного АБС-пластика (достаточно сказать, что он применяется для изготовления автомобильных бамперов). Однако при формовке ванны слой акрила становится тонким, и случайное механическое повреждение может привести к тому, что вода будет взаимодействовать с АБС-пластиком, который, в свою очередь, не является влагостойким материалом.
Таким образом, стенки изделия представляют собой "сэндвич" из акрила (2-4 мм) и АБС-пластмассы (4-6 мм). С внешней стороны пластиковая чаша покрыта слоем полиэстеровой смолы и мелкоизмельченного стекловолокна (4 мм), далее следует специальный пористый пластик, играющий роль теплоизоляции и звукоизоляции (характеристики материала, что называется, - секрет фирмы). Несущий слой придает ванне ударопрочность и устойчивость, служит дополнительным армирующим слоем и позволяет изготавливать модели с четкими прямоугольными формами или закруглениями с очень малым радиусом (что проблематично, если иметь дело с литьевым акрилом). У качественных изделий дно, углы и бортики в момент нанесения армирующей смеси дополнительно усиливаются листами типа ДСВ (к ним обычно крепятся и ножки ванны). Тем самым обеспечивается равномерность распределения нагрузок на корпус, чтобы ни днище, ни бортики не прогнулись. Модели из композита "АБС + акрил" внешне ничем не отличаются от традиционных акриловых и обладают теми же достоинствами.
У акриловой ванны есть несколько безусловных преимуществ. Первое - небольшой вес (всего 20-45 кг в зависимости от размеров), что заметно облегчает транспортировку и установку ванны. Второе - глухой звук при наполнении, ведь акрил является звукопоглощающим материалом. Кроме того, на акриле плохо размножаются бактерии, что немаловажно для изделия, постоянно находящегося в контакте с водой. И самое главное качество, радующее всех пользователей (любителей садиться на бортик или влезать в сухую ванну, чтобы принять душ) - акриловая чаша теплая на ощупь. Причина этого проста: материал обладает низкой теплопроводностью.
К сожалению, у акрила есть и отрицательные свойства: в такой ванне нельзя замачивать белье, ее поверхность легко поцарапать, а упавшая зажженная сигарета способна оплавить поверхность. А самое неприятное, несмотря на все заверения производителей, в процессе эксплуатации по корпусу ванны может пойти трещина. Такое редко, но случается от давления при переливе воды.
Однако уход за акриловой ванной предполагает практически полное восстановление его первоначального вида даже в случае серьезных повреждений. Ценное качество ванн - возможность удаления царапин (только для образцов из литьевого акрила), неизбежно появляющихся со временем на поверхности, и пятен. Профессионалы используют для этого самую "нежную" наждачную бумагу, осторожно затирая шкуркой выявленный дефект, а после восстанавливают блеск полировочной пастой. Мелкие дефекты можно устранить и самостоятельно, например, с помощью мягкой тряпочки с зубной пастой. Однако это не означает, что в акриловой ванне можно мыть, скажем, собаку: от когтей останутся следы, не поддающиеся затирке. К тому же прибегать к подобной процедуре постоянно не рекомендуется, поскольку от каждой такой операции слой акрила истончается.
Диапазон цен на акриловые ванны очень широк, и на украинском рынке представлено большое количество компаний, выпускающих данный вид продукции, чем тех, что действуют в разряде стальных или чугунных изделий. В Украине акриловые модели сейчас предлагают все крупнейшие мировые производители: Albatros Guzzini, Teuco, Jakuzzi (Италия), Galatea, Bamberger, Duscholux, Hoesch, Villeroy & Boch (Германия), Balteco (Эстония), Pamos (Австрия), Doctor Jet, Akrilan (Россия), Pool-Spa (фабрика принадлежит испанской Roca), а также фирмы Svedbergs, IDO, международный концерн Ideal Standart и др.
Рис.9.20 Вакуум формовочная машина
Лист акрилового пластика превращается в полноценную ванну, последовательно проходя четыре основные технологические операции:
1. Формовка;
2. Усиление;
3. Обрезка;
4. Сборка.
Первая технологическая операция, с которой начинается превращение плоского акрилового листа в ванну или душевую кабину, – это формовка пластиковой заготовки. Именно на этой технологической стадии определяется качество будущей продукции и, в особенности, внешний вид акриловой поверхности.
Основная задача, решаемая при формовке заготовки, – превращение плоского пластикового листа в пространственную деталь-заготовку, в точности повторяющую облик будущей ванны или душевой кабины. Качество формовки определяется равномерной толщиной и гладкостью (технический термин) поверхности получившейся заготовки.
Рис.9.21 Заключительная стадия процесса формовки акриловой заготовки – термостатирование (остывание акрилового листа происходит без выемки формы, во избежание деформации акриловой поверхности)
Операцию формовки обычно выполняют в автоматизированной термовакуумформовочной машине, на специальной матрице, изготовленной из алюминия или высокотемпературного композита. Однако некоторые производители, в основном, в Китае, операцию формования выполняют вручную.
Почему важно получить заготовку будущей ванны или душевой кабины с равномерной толщиной стенки по всей детали?
При формовке лист пластиковой заготовки разогревается и под действием вакуума начинает растягиваться под размер формы, причём в результате неравномерного натяжения толщина листа уменьшается порой на 80%(в углах заготовки). Если ванна была изготовлена из 5-миллиметрового листа чистого акрила, нам будет достаточно 1,8 мм заготовки на весь долгий срок службы ванны.
Вторая технологическая операция производства ванн – усиление.
После этапа формования тонкая акриловая скорлупка со всеми предосторожностями отправляется на усиление. В процессе усиления обратную, не видимую покупателю сторону акриловой заготовки покрывают переменным по толщине композиционным слоем, который принимает все нагрузки от воды и веса человека, передавая их дальше на раму и пол ванной комнаты. Именно толщина и плотность усиления определяют прочность корпуса акриловой ванны. Сегодня в серийном производстве наиболее распространена технология усиления ванн посредством напыления полиэфирного компаунда вперемешку с рубленым стекловолокном (практически в 99% серийных производств).
Рис.9.22 Нанесение композиционного полимерного усиливающего слоя на обратную поверхность ванны.
Акрил и соэкструзия АБС ПММА требуют разные марки полиэфирного компаунда. К АБС, а это обратная сторона соэкструзионного листа, компаунд имеет химическое сродство и поэтому приклеивается «намертво». Для усиления инертного литого акрила требуются специальные компаунды с повышенной адгезией, а также предварительная обработка обратной поверхности полимерной заготовки.
К сожалению, на этом этапе производства соэкструзионные листы подстерегает опасность химического разрушения слоя АБС (из-за химического сходства полиэфирного компаунда), и как следствие – повреждение слоя акрила. Такое разрушение начинается в углах ванн или в месте установки слива и выглядит, как паутинка из тончайших трещинок. Правда химическое разрушение может произойти лишь в том случае, если были допущены нарушения в технологии нанесения усиливающего слоя или неправильно задано соотношение между полиэфирным компаундом и инициатором полимеризации (катализатором).
Еще одна особенность химического разрушения заключается в том, что процесс может занять некоторое время и проявиться уже после установки и начала эксплуатации ванны. Покупателю в этой ситуации очень трудно отстоять свои права на замену некачественной продукции.
Чистому акрилу подобная опасность в принципе не грозит.
В процессе выполнения операций на этапе усиления заготовка акриловой ванны из тонкой, 2-5-миллиметровой «скорлупки» превращается в мощное композиционное многослойное изделие. Она обретает необходимую прочность и стабильность и готова выдержать любые расчетные нагрузки в течение всего периода эксплуатации.
Дата добавления: 2018-05-02; просмотров: 2195; Мы поможем в написании вашей работы! |
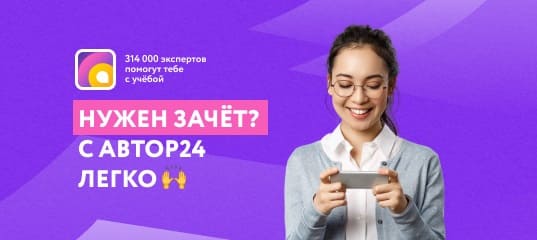
Мы поможем в написании ваших работ!