Приведите современную классификацию и маркировку алюминиевых сплавов, приведите примеры применения этих сплавов в машиностроении
По технологии изготовления полуфабрикатов и изделий все применяемые в промышленности алюминиевые сплавы делят на три группы: деформируемые, литейные и спеченные.
Деформируемые сплавы имеют высокую технологическую пластичность, поэтому используются для изготовления деталей способами холодной и горячей пластической деформации (прокаткой, ковкой, прессованием, экструдированием, штамповкой, волочением и т.д.).
Пластическая деформация этих сплавов не только средство изменения или придания формы, ее используют также и для упрочнения алюминиевых сплавов.
К деформируемым алюминиевым сплавам относятся сплавы Al-Cu-Mg-Mn; Al-Zn-Mg-Cu, это дуралюмины (Д1, Д16, Д18, Д19 и др.), авиали (АВ, АД31, АДЗ3 и др.), высокопрочные алюминиевые сплавы (В95, В96), магналии сплавы алюминия с магнием.
В продовольственном машиностроении алюминиевые сплавы идут на цистерны, различные емкости, детали холодильных агрегатов. Из деформируемых сплавов АД, АД1, Д16, АМц др. В продовольственном машиностроении изготавливают различные сварные конструкции технологического оборудования. Хорошими свойствами обладает алюминиево-марганцовистый сплав АМц и алюминиево-магниевые сплавы АМг и АМгЗ (магналии). Они имеют хорошую пластичность, хорошо свариваются, обладают высокой коррозионной стойкостью и не требуют для упрочнения термической обработки.
Литейные алюминиевые сплавы
Предназначены для изготовления деталей методами фасонного литья (в земляные или металлические формы, под давлением и т.д.), имеют хорошие литейные свойства высокую жидкотекучесть, малую склонность к образованию горячих трещин, малую усадку.
|
|
Широкое распространение для изготовления литых деталей получили силумины - сплавы алюминия с кремнием (ГОСТ 1589-89). Силумины обладают малой удельной массой хорошими литейными свойствами, коррозионной стойкостью.
Свойства ряда силуминов представлены в таблице
Таблица 1. - Состав и свойства силуминов
Марка сплава | Содержание Si, % | sв, МПа | НВ, МПа | d, % |
АК7 | 6…8 | 200…230 | 500…570 | 2…4 |
АК9 | 8…10,5 | 170…290 | 2…4 | |
АК12 | 10…13 | 160…190 | 2…6 |
В продовольственном машиностроении силумины используются для изготовления корпусов насосов, работающих в контакте с пищевыми продуктами.
Для фасонного литья применяют также сплавы на основе Аl-Сu-Mg, Аl-Сu, Al-Zn-Mg. Магналии также относятся к алюминиевым литейным сплавам, они содержат 4...13 % Mg.
Спеченные алюминиевые сплавы (САС) получают брикетированием, спеканием и деформированием порошков алюминия и легирующих элементов или порошков стандартных алюминиевых сплавов. К таким сплавам относятся САС1 (25...30% Si, 5...7% Ni, остальное Al). Их применяют для деталей приборов, работающих в паре со сталью при 20...200°С, где необходимо сочетание низкого коэффициента линейного расширения и малой теплопроводности.
|
|
Для деталей, работающих при высоких температурах (до 500°С), применяют спеченные алюминиевые порошки (CAП1...САП4) сплав алюминия с его окисью (Аl2O3).
Изложите сущность технологии волочения стальной проволки, исходный материал, оборудование, инструмент и область применения
Волочением называют пластическую деформацию при протягивании проволоки, прутка, профиля, трубы через сужающийся канал инструмента (волоки). Усилие растяжения, приложенное к выходящему из волоки концу изделия, расходуется на формоизменение заготовки и преодоление сил трения о канал волоки. Обжатие за проход ограничено прочностью выходящего конца изделия и, как следствие, обрывом металла. Характеристикой процесса служит вытяжка λ.
Волочение относится к холодной пластической обработке. Кроме формоизменения и вытяжки достигается упрочнение (наклеп) материала, улучшается качество поверхности и точность размеров.
Различают волочение на цепных станах (для получения труб, прутков и профилей ограниченной длины) и волочение на станах барабанного типа (для получения длинномерной продукции, например, проволоки).
|
|
Заготовки для волочения – это сплошные (катаные, прессованные) круглые и фасонные профили в бухтах или отрезках, бесшовные или сварные трубы. Готовые изделия волочильных цехов – это проволока диаметром от 0,01 до 6 мм, трубы диаметром до 400 мм, калиброванные прутки и профили, профильные (овальные, прямоугольные и т. п.) трубы.
Производительность процесса волочения определяется скоростью на выходе из волоки (скоростью волочения), вытяжкой за проход, затратами времени на начало процесса и замену инструмента.
Скорость волочения составляет 1–10 м/с для прутков, профилей и труб и до 50 м/с для тонкой проволоки. При таких скоростях скольжения неизбежны проблемы износостойкости волок, обеспечения качества поверхности изделий. Первостепенная роль при волочении принадлежит технологической смазке и управлению процессом трения. Радикальным средством уменьшения износа, повышения скорости и производительности является волочение в режиме гидро- или пластогидродинамического трения.
Перед волочением заготовку термически обрабатывают, удаляют с нее окалину и подготавливают ее поверхность для закрепления смазки. Термическая обработка снимает наклеп и обеспечивает получение оптимальной структуры. Смягчающий отжиг повторяют после 70–85 %-го обжатия для стали и 99 %-го для цветных металлов (меди, латуни). Окалину после термической обработки удаляют механическим, химическим, электрохимическим способами, а также одновременно несколькими способами. Механическая очистка состоит в периодическом изгибании полосы между роликами, обдуве дробью или песком. Такой способ малоэффективен для удаления прочной окалины, поэтому чаще применяют химический способ.
|
|
После травления заготовку промывают, на ее поверхность наносят подсмазочный слой путем желтения, омеднения, фосфатирования, известкования. При желтении на заготовку наносят тонкий слой гидроксида железа Fе(ОН)3, который вместе с нанесенной затем на него известью играет роль наполнителя для смазки. Фосфатирование состоит в нанесении пленки фосфатов марганца, железа и цинка. К пленке фосфатов хорошо прилипает смазка и коэффициент трения снижается до 0,04 – 0,06. Известкование в растворе нейтрализует остатки кислот и образует пленку наполнителя для смазки. Для волочения с большими обжатиями и давлениями рекомендуется омеднение заготовки в растворе купороса; коэффициент трения при этом равен 0,08 – 0,12. После нанесения покрытия заготовку сушат в камере при 300–350 оС.
Для увеличения производительности концы бухт сваривают электроконтактной сваркой. Это снижает потери времени на заправку заготовки в волоки до минимума.
Проволоку изготовляют на машинах многократного волочения с числом волок 5–22. За каждой волокой скорость проволоки увеличивается пропорционально вытяжке λ, достигая на выходе 40–50 м/с (на наиболее современных машинах). Автоматизированный электропривод позволил объединить в один непрерывный агрегат волочильную проволочную машину и установку для отжига проволоки «на проход». При производстве труб и прутков также стремятся объединить в один агрегат волочильную машину, механизмы для правки, резки, острения концов, установки оправок и т. д.
К волочильному инструменту относятся волоки и оправки. Канал волоки (рисунок 1) имеет следующие зоны: входную для облегчения ввода заготовки, смазочную и рабочую для ввода смазки и обжатия заготовки, калибрующий поясок, обратный конус и выходную зону для предохранения изделия от образования рисок и царапин. Основные характеристики волоки – это материал, угол a и ширина калибрующего пояска. Длина пояска составляет 0,4 – 1,0 длины рабочей зоны. Угол α обычно равен 6–15°.
1 – входная зона; 2 – смазочная зона; 3 – калибрующая зона; 4 – обратный конус; 5 – выходная зона
Рисунок 1 – Схема канала волоки
По диаметру изделий, мм, волочение подразделяется на толстое (3,5 – 1,5), среднее (1,6 – 0,25), тонкое (0,4 – 0,1) и тончайшее (0,02 – 0,008). Наибольшей износостойкостью обладают волоки из природных (до 2,4 мм) и синтетических (поликристаллических до 4,6 мм) алмазов, однако они нуждаются в интенсивном охлаждении. Размеры и форма канала стандартизованы. Алмазные волоки вставляют в оправы из латуни или бронзы и заливают легкоплавким сплавом. Для изделий диаметром 1 – 50 мм применяют в основном сборные волоки из обоймы с запрессованной в нее твердосплавной вставкой. Размеры и материалы вставок на основе карбидов вольфрама и кобальта стандартизованы.
Для мелкосерийного производства и производства труб диаметром до 300 мм применяют волоки из сталей У8 – У12, Х12М, ШХ15 и др.
В цепном волочильном стане (рисунок 2) передний конец прутка или трубы 1 проталкивается через волоку 2 и захватывается клещами каретки 3. Каретка сцепляется с пластинчатой цепью 4, перематываемой с помощью привода 5. На входной стороне стана имеется приспособление для подачи и удержания стержня оправки.
Рисунок 2 – Схема цепного волочильного стана
Скорости волочения на современных станах достигают 3–5 м/с, усилие волочения составляет 30–1500 кН, причем одновременно протягивается до трех заготовок. Недостатки цепных станов таковы: ограниченная длина изделий, большие затраты времени на подготовку к волочению очередной заготовки. Разработаны автоматизированные линии волочения прутков, в которых специальные захваты попеременно тянут заготовку через волоку без остановки процесса.
Дата добавления: 2018-05-01; просмотров: 1118; Мы поможем в написании вашей работы! |
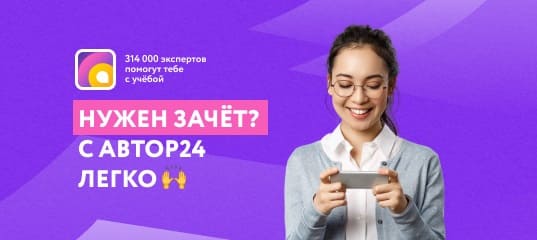
Мы поможем в написании ваших работ!